
методички / 4012 ЭИ
.pdf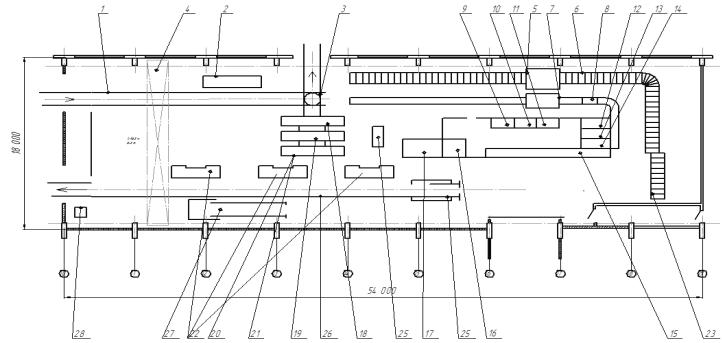
Комплектовочный участок размещен в изолированном помещении, имеет смежные помещения с участком по ремонту подшипников и отделения монтажа колесных пар. Монтажное отделение предназначено для монтажа букс с роликовыми подшипниками на шейку оси колесной пары, подбора парных подшипников, для контроля радиального зазора и подбора парных подшипников, укладки подшипников в буксу, смазывания специализированным модификатором внутренних колец на шейке оси и в блоке подшипников, для нанесения смазки Л3 ЦНИИ на лабиринтные кольца и в блок подшипников, монтажа букс в комплекте с блоком подшипников на шейку оси, для крепления гайки или болтов торцевой шайбы, обвязки проволокой болтов М12, крепления стопорной планки, клеймения оси, монтажа крепительной и смотровой крышек, проверки легкости проворачивания буксы [1,2,5].
Рис. 7. Схема колесно-роликового участка депо по ремонту грузовых вагонов: 1 – наклонный путь; 2 – стенд демонтажа букс с колесных пар; 3 – поворотное устройство; 4 – кран – балка; 5 – моечная машина корпусов букс; 6 – транспортер деталей буксового узла; 7 – машина для мойки и сушки роликовых подшипников; 8 – транспортер подшипников; 9 – приспособление шлифовки торцов роликов; 10 – приспособление шлифовки наружных колец; 11 – установка зачистки наружных колец; 12 – дефектоскопная установка контроля колец подшипников; 13 – вихретоковый дефектоскоп для контроля сепараторов; 14 – ультразвуковой дефектоскоп; 15 – стенд демонтажа букс; 16сверлильный станок; 17 – индукционный нагреватель; 18 – моечная машина колесных пар; 19 – стенд обмера колесных пар; 20 – магнитный дефектоскоп для контроля средней части оси; 21 – магнитный дефектоскоп для контроля шеек осей; 22 – колесотокарные станки; 23 – накопитель колесных пар;
24 – стеллаж отремонтированных деталей; 25 – стенд монтажа буксового узла; 26 – транспортер для отремонтированных деталей буксового узла; 27 – позиция для промежуточной ревизии буксового узла; 28 – АРМ АСУ ВЧДР
21
Предмонтажное отделение примыкает с одной стороны к колесно-токарному отделению, а с другой стороны – к монтажному отделению. Предназначено для осмотра букс, осмотра гаек, стопорных планок, осмотра, зачистки и замера шеек колесных пар, демонтажа лабиринтных и внутренних колец (если необходимо), окраски средней части оси, дисков, нанесения контрольных полос, отстоя колесных пар перед монтажом и после ремонта. Колесно-токарное отделение предназначено для предварительного осмотра и определения необходимого ремонта, обмера, оформления приходного листа ВУ-51, демонтажа букс с роликовыми подшипниками, обмывки колесных пар в моечной машине, обмывки корпусов букс, обмывки роликовых подшипников в автоматической установке, обмывки деталей букс, обточки поверхности катания колесных пар, дефектоскопии колесных пар, промежуточной ревизии букс (пасс. депо) или текущего ремонта (груз. депо) колесным парам, выкаченных из-под вагонов деповского ремонта (пригодных для подкатки под вагоны текущего ремонта), окраски.
Порядок выполнения работы
1.Ознакомиться со схемами колесно-роликовых участков пассажирского и грузового ремонтных депо, а также основными выполняемыми технологическими операциями.
2.Выполнить выданное преподавателем индивидуальное задание, приведенное в практическом занятии, в таблице 7.
3.Ответить на контрольные вопросы.
4.Оформить отчет.
Содержание отчета
По результатам проведенной работы составляется отчет в письменной форме или в машинописном тексте. Отчет должен содержать: название работы, цель работы, выполненное индивидуальное задание, ответы на контрольные вопросы
Контрольные вопросы
1.Каково назначение колесно-роликового участка?
2.С какими участками взаимодействует колесно-роликовый участок?
3.Какие виды работ выполняет колесно-роликовый участок?
4.На какие отделения и участки включает колесно-роликовый участок?
5.Каково назначение колёсного парка?
6.Из каких участков состоит отделение роликовых подшипников?
7.Каково назначение комплектовочного участка?
8.Каково назначение предмонтажного отделения?
22
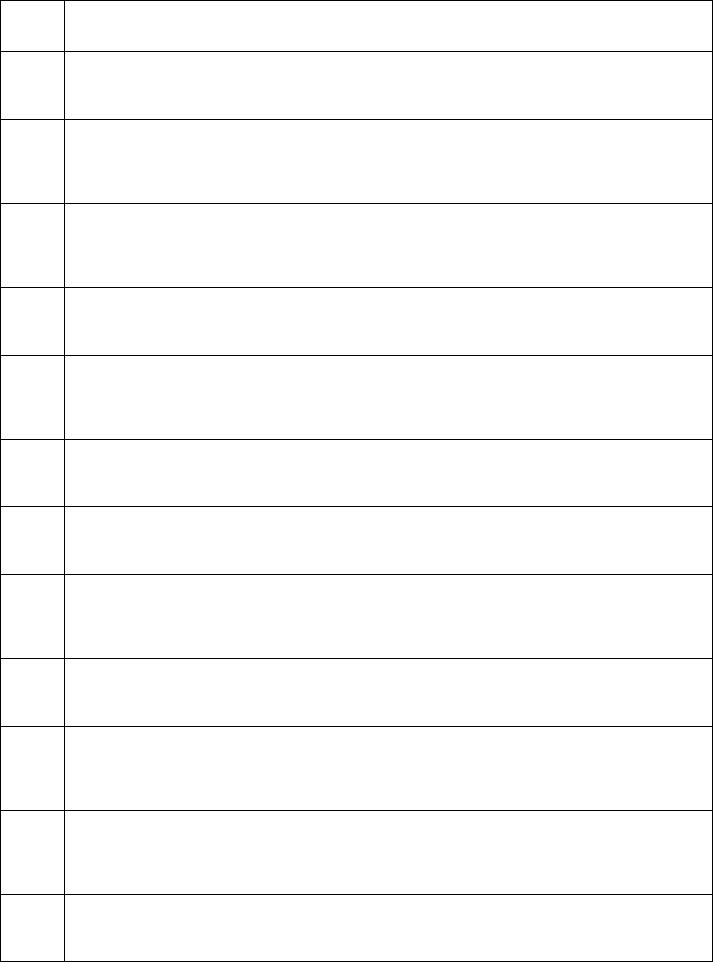
Таблица 7
Исходные данные для выполнения индивидуального задания
№
вариИндивидуальные задания анта
1Изобразите схему колесно-роликового участка депо по ремонту пассажирских вагонов. Укажите
размещение колесно-токарного отделения. Укажите схематично очередность прохождения колесной парой технологических операций этого отделения. Выпишите технологические операции, проводимые в колесно-роликовом участке депо по ремонту пассажирских вагонов
2Изобразите схему колесно-роликового участка депо по ремонту пассажирских вагонов. Укажите
размещение участка для дефектоскопии осей колесных пар. Укажите схематично очередность прохождения колесной парой технологических операций данного участка. Выпишите технологические операции, проводимые в колесно-роликовом участке депо по ремонту пассажирских вагонов
3Изобразите схему колесно-роликового участка депо по ремонту пассажирских вагонов. Укажите
размещение отделения по ремонту роликовых подшипников. Укажите схематично очередность прохождения колесной парой технологических операций этого отделения. Выпишите технологические операции, проводимые в колесно-роликовом участке депо по ремонту пассажирских вагонов
4Изобразите схему колесно-роликового участка депо по ремонту пассажирских вагонов. Укажите
размещение предмонтажного отделения. Укажите схематично очередность прохождения колесной парой технологических операций этого отделения. Выпишите технологические операции, проводимые в колесно-роликовом участке депо по ремонту пассажирских вагонов
5Изобразите схему колесно-роликового участка депо по ремонту пассажирских вагонов. Укажите
размещение монтажного отделения роликовых букс. Укажите схематично очередность прохождения колесной парой технологических операций этого отделения. Выпишите технологические операции, проводимые в колесно-роликовом участке депо по ремонту пассажирских вагонов
6Изобразите схему колесно-роликового участка депо по ремонту пассажирских вагонов. Укажите
размещение колесного парка. Укажите схематично очередность прохождения колесной парой технологических операций. Выпишите технологические операции, проводимые в колеснороликовом участке депо по ремонту пассажирских вагонов
7Изобразите схему колесно-роликового участка депо по ремонту грузовых вагонов. Укажите
размещение колесного парка. Укажите схематично очередность прохождения колесной парой технологических операций. Выпишите технологические операции, проводимые в колеснороликовом участке депо по ремонту пассажирских вагонов
8Изобразите схему колесно-роликового участка депо по ремонту грузовых вагонов. Укажите
размещение монтажного отделения роликовых букс. Укажите схематично очередность прохождения колесной парой технологических операций этого отделения. Выпишите технологические операции, проводимые в колесно-роликовом участке депо по ремонту пассажирских вагонов
9Изобразите схему колесно-роликового участка депо по ремонту грузовых вагонов. Укажите
размещение предмонтажного отделения. Укажите схематично очередность прохождения колесной парой технологических операций этого отделения. Выпишите технологические операции, проводимые в колесно-роликовом участке депо по ремонту пассажирских вагонов
10Изобразите схему колесно-роликового участка депо по ремонту грузовых вагонов. Укажите
размещение отделения по ремонту роликовых подшипников. Укажите схематично очередность прохождения колесной парой технологических операций этого отделения. Выпишите технологические операции, проводимые в колесно-роликовом участке депо по ремонту пассажирских вагонов
11Изобразите схему колесно-роликового участка депо по ремонту грузовых вагонов. Укажите
размещение участка для дефектоскопии осей колесных пар. Укажите схематично очередность прохождения колесной парой технологических операций данного участка. Выпишите технологические операции, проводимые в колесно-роликовом участке депо по ремонту пассажирских вагонов
12Изобразите схему колесно-роликового участка депо по ремонту грузовых вагонов. Укажите
размещение колесно-токарного отделения. Укажите схематично очередность прохождения колесной парой технологических операций этого отделения. Выпишите технологические операции, проводимые в колесно-роликовом участке депо по ремонту пассажирских вагонов
23

ПРАКТИЧЕСКАЯ РАБОТА № 5
СТРУКТУРА ТЕЛЕЖЕЧНЫХ УЧАСТКОВ ГРУЗОВОГО И ПАССАЖИРСКОГО ВАГОНОРЕМОНТНЫХ ДЕПО (4 часа)
Цель работы: ознакомиться с размещением оборудования в тележечном участке грузового вагонного депо и тележечном участке пассажирского вагонного депо с автоматизированной поточно-конвейерной линией.
Краткие теоретические сведения
Ремонт грузовой тележки осуществляется на пяти основных и одной подготовительной позициях поточно-конвейерной линии – см. рис. 8.
На подготовительной позиции тележки подаются в моечную машину на трансбордерной тележке Если буксы с роликовыми подшипниками не подлежат разборке, то перед подачей колесной пары в моечную машину на них устанавливаются предохранительные устройства, защищающие полости букс от воды. Тележка подается в моечную машину с помощью толкателя. Из моечной машины тележка с помощью толкателя выкатывается на позицию I.
Рис. 8. Схема поточной линии ремонта грузовой тележки:
1 – моечная машина; 2, 9 – подъемно-поворотное устройство; 3, 10 – устройства для дефектоскопирования; 4, 8 – подъемник с поворотник для снятия и постановки триангелей; 5, 7 – подъемник с поворотником для снятия и постановки пружинных комплектов;
6 – кантователь надрессорной балки
Подъемник 4 опускает раму на каретку поворотника, который поворачивает раму на 900 для снятия подвесок тормозных башмаков и триангеля с одной стороны, затем поворачивает раму на 1800 для снятия подвесок тормозных башмаков и триангеля с другой стороны, после чего поворачивает раму на 900 и опускает на ленту транспортера для ее транспортировки на II позицию. Кроме того, на I позиции производится дефектоскопирование боковых рам и надрессорной балки тележки в сборе.
На II позиции производится снятие пружин рессорных комплектов с одной стороны рамы, затем рама поднимается с помощью подъемно-поворотного устройства 5 и поворачивается на 1800 для снятия пружин с другой стороны рамы.
24
На III позиции специальное устройство раздвигает боковые рамы, они снимаются с надрессорной балки и оказываются на кантователях. Надрессорная балка с помощью кантователя поворачивается для осмотра, выявления трещин и обмера рабочих поверхностей (опорные поверхности, подпятник). На этой позиции разбираются боковые скользуны. В боковых рамах проверяют наличие трещин, проверяют прочность крепления фрикционных планок, замеряют величину износа отверстий в кронштейнах для валиков подвесок тормозных башмаков. Если надрессорная балка и боковые рамы нуждаются в сварочно-наплавочных работах, то их краном подают на участок сварки, а оттуда подают уже готовые, ранее отремонтированные. Производится дефектоскопирование боковых рам и надрессорных балок в отдельности.
На IV позиции производится сборка боковых рам, надрессорной балки, пружинных комплектов. Места под рессоры предварительно окрашиваются.
На V позиции устанавливаются триангели и подвешиваются тормозные башмаки, причем, поворотник 8 поворачивает раму для установки триангелей с одной стороны, а затем поворачивает ее на 1800 для установки триангелей с другой стороны. После постановки триангелей рама снимается с конвейера и поднимается для подкатки колесных пар. Колесные пары подаются через поворотное устройство 9 из колесного цеха. Затем колесные пары подкатываются на позицию V, где фиксируются на расстоянии, равном базе тележки. Рама опускается на колесные пары. Собранную тележку обмеряют и сдают приемщику вагонов. Готовая тележка подается в вагоносборочный участок.
Для осуществления технологического процесса ремонта тележек грузовых вагонов применяется оборудование: стенд для контроля внешнего вида и размеров тележки, дефектоскоп феррозондовый ДФ-205; вихретоковые дефектоскопы ВД-12ФМ, ВД-201, приспособление для раздвижки боковин, кантователь, злектродомкраты, сварочный агрегат ПДГО-5010, ВДУ-505, станок фрезерный, вертикально-фрезерный станок, консольно-фрезерный станок, стенд разборки, сборки и испытания триангелей, контейнер, электропечь нагревательная, наковальня, молот пневматический, машина шлифовальная ИП 2002 ГОСТ 12634-80, дефектоскоп поясный, сварочный полуавтомат ГОСТ 11396-65, стол сварщика ГОСТ 20741-81Е, вертикально-сверлильный станок испытательный стенд СИП, токарный станок, строгальный станок, толщиномер, кондуктор для вырезки окна, трансформатор сварочный, специализированная оснастка для наплавки, воздуховод, воздушно-дуговой резак ВДР-400, станок Ф008, , станок токарный винторезный, установка для автоматической наплавки, станок сверлильный, печь для разогрева заклепок, резак ГОСТ 5191-79Е, машина шлифовальная ГОСТ 1263480 [4].
Размещение оборудования в тележечном участке пассажирского депо. Поточно-
конвейерная линия для ремонта тележек пассажирских вагонов имеет 6 позиций – см. рис. 9.
25
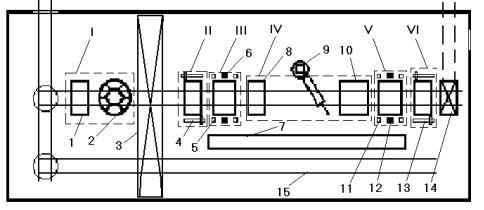
После выкатки из под вагона тележки накатывают на трансбордерную тележку и отправляют в тележечный участок. Первая тележка вагона (без генератора) подается сразу же в моечную машину. Вторая тележка ставится на подготовительную позицию для демонтажа генератора и постановки защитных устройств на роликовые буксы, не подлежащие полной разборке. Затем тележка поступает в моечную машину.
Рис. 9. Схема поточной линии ремонта пассажирской тележки:
1 – подготовительная позиция для снятия генераторов; 2 – моечная машина; 3 – мостовой кран; 4, 13 – электрогайковерты; 5, 11 – подставки под буксы; 6, 12 – пресс для сжатия пружин;
7 – транспортеры; 8 – кантователь для надрессорной балки; 9 – консольный кран локтевого типа; 14 – подземный тоннель 15 – второй путь (позиция ожидания)
После мойки тележки подаются во вторую позицию (первую разборочную), где электрогайковертами ослабляются гайки шпинтонов, отворачиваются гайки валиков центрального подвешивания, при помощи гидравлических домкратов снимаются гидравлические гасители. Здесь же краном-укосиной снимаются тормозная рычажная передача и снимаются тормозные башмаки с подвесками и продольные поводки, которые подвергаются дефектоскопированию.
На третьей позиции (вторая разборочная) полностью разбирается центральное рессорное подвешивание, снимается рама, надрессорная балка и убираются колесные пары. Рама тележки дефектоскопируется с помощью вихретокового дефектоскопа ВД-113. На раму устанавливаются отремонтированные башмаки, рычажная передача, траверсы, производят ремонтно-сварочные работы рамы тележки.
На позиции имеется следующее оборудование:
-пресс для сжатия пружин центрального рессорного подвешивания;
-подставки для букс;
-консольный кран локтевого типа с переменной стрелой (грузоподъемность 250 кг);
-кантователь надрессорной балки тележки;
-кантователь рамы тележки;
-подъемник колес с поворотным устройством;
-газосварочный комплект.
26
Разборка центрального рессорного подвешивания осуществляется в следующей последовательности:
1)устанавливается шкворень, удерживающий тележку;
2)пресс сжимает рессорное подвешивание;
3)снимаются гасители колебаний и продольный поводок;
4)разбирается центральное рессорное подвешивание;
5)снимается и убирается шкворень.
Сжатие прессом рессорного подвешивания необходимо для ослабления подвесок, так как пружины рессорного подвешивания имеют начальное поджатие. После ослабления валики подвесок вынимаются и надрессорная балка поднимается, освобождая пружины. После поднятия рамы с надресорной балкой колесные пары выкатываются и удаляются мостовым краном с помощью специального захвата на пути, ведущие в колесно-роликовый цех. Тяжелые детали (рычажная передача, детали рессорного подвешивания, гасители колебаний) укладываются в кассеты и отправляются в подсобный цех для ремонта. Поддоны, пружины центрального рессорного подвешивания, детали буксового рессорного подвешивания с помощью локтевого крана размещаются на конвейере для подачи на V позицию. С помощью мостового крана рама и надрессорная балка устанавливаются на кантователи IV позиции.
На IV позиции (первая сборочная) проверяются и ремонтируются рама тележки и надрессорная балка, собирается тормозная рычажная передача.
На V позиции (вторая сборочная) производится сборка тележки в следующей последовательности:
1)из колесного цеха подаются отремонтированные колесные пары;
2)осматриваются и обмеряются пружины рессорного подвешивания;
3)на поддонах собираются комплекты центрального рессорного подвешивания, на них устанавливается надрессорная балка;
4)собираются фрикционные гасители колебаний и надбуксовые пружины;
5)рама тележки устанавливается на колесные пары;
6)устанавливаются продольный поводок и гидравлические гасители колебаний.
На VI позиции электрогайковертом заворачиваются гайки шпинтонов и валиков
центрального подвешивания. Устанавливаются тормозные башмаки с подвесками и рычажная передача. Тележки с помощью мостового крана перемещаются на второй путь (позицию ожидания), где на вторую тележку вагона устанавливается электрогенератор.
Отремонтированные колесные пары поступают из колесного цеха по подземному тоннелю и с помощью мостового крана и специального захвата подаются на V позицию [1,2,5].
Порядок работы
1.Ознакомиться со схемами поточной линии ремонта грузовой тележки и пассажирской тележки, а также с основными выполняемыми технологическими операциями.
2.Ответить на контрольные вопросы.
3.Оформить отчет.
27
Содержание отчета
По результатам проведенной работы составляется отчет в письменной форме или в машинописном тексте. Отчет должен содержать: название работы, цель работы, ответы на контрольные вопросы.
Контрольные вопросы
1.Привести схему поточной линии тележечного участка пассажирского депо и перечислить оборудование на каждой позиции.
2.Перечислить части и элементы тележки пассажирского вагона, которые подвергаются осмотру и обмеру перед ремонтом (напряженные узлы, рабочие поверхности).
3.Описать последовательность выполнения операций на поточной линии по ремонту тележки пассажирского вагона.
4.Перечислить оборудование для ремонта пассажирских тележек.
5.Привести схему поточной линии тележечного участка грузового депо и перечислить оборудование на каждой позиции.
6.Перечислить части и элементы тележки грузового вагона, которые подвергаются осмотру и обмеру перед ремонтом (напряженные узлы, рабочие поверхности).
7.Описать последовательность выполнения операций на поточной линии.
8.Перечислить оборудование, применяемое при ремонте грузовых тележек.
ПРАКТИЧЕСКАЯ РАБОТА № 6
СТРУКТУРА АВТОТОРМОЗНОГО КОНТРОЛЬНОГО ПУНКТА
ИКОНТРОЛЬНОГО ПУНКТА АВТОСЦЕПКИ ГРУЗОВОГО
ИПАССАЖИРСКОГО ВАГОННЫХ ДЕПО (2 часа)
Цель работы: ознакомиться с планировкой автоконтрольного пункта и контрольного пункта автосцепки ремонтного депо, размещением оборудования, организаций операций при выполнении технологического процесса ремонта соответствующих узлов.
Краткие теоретические сведения
Контрольный пункт автосцепки вагонного депо предназначен для полного осмотра и ремонта узлов автосцепного устройства, снятых с вагонов в вагоносборочном участке, а также поступивших с текущего ремонта и единой технической ревизии. Производственная структура и состав отделения КПА определяется масштабом производства и принятым методом ремонта и контроля корпусов автосцепок и поглощающих аппаратов. В состав отделения входят: участок правки корпусов и деталей
28
автосцепки; сварочная кабина (для выполнения сварочных и наплавочных работ); специальная площадка для ремонта поглощающих аппаратов и тяговых хомутов.
В контрольном пункте автосцепки используется несколько видов организации производства, определяющих план помещения, выбор и размещения производственного оборудования:
1)стационарный метод ремонта с применением кассет для корпусов;
2)метод с применением подвижных кассет для корпусов;
3)поточный метод с транспортировкой корпусов по подвесному монорельсу;
4)поточно-конвейерная линия кольцевого типа (тележки, перемещающиеся по рельсам);
5)стенды карусельного типа для ремонта корпусов и тяговых хомутов.
На рис. 10 приведена схема контрольного пункта автосцепки пассажирского ремонтного депо. В данном случае принят стационарный метод ремонта с использованием стендов карусельного типа. Это объясняется тем, что поточный метод ремонта применять при небольшой программе ремонта экономически невыгодно. Также в процессе работы трущиеся детали автосцепок имеют неодинаковый износ. Транспортировка деталей и узлов автосцепного устройства осуществляется с помощью кран-балки и консольного крана.
Автосцепки, поступившие для полного осмотра на специальных кассетах, обеспечивающих возможность их перемещения, подаются для очистки в моечную машину с помощью кран-балки. Затем их сушат. После этого автосцепки вместе с кассетой подаются в зону действия крана-укосины и устанавливаются на поворотный стенд карусельного типа, где автосцепку разбирают, осматривают и проверяют корпус шаблонами. Хвостовик автосцепки подвергают магнитному контролю на стенде, дефектоскопом. Детали автосцепки проверяют на столе. Детали, требующие выправления изгибов, направляются на участок правки, где имеются нагревательная печь, пресс для правки корпуса и деталей автосцепки, а так же и приспособление для правки предохранителя. Детали, имеющие чрезмерные износы, а также трещины, допускаемые к заварке, подаются по транспортерам-накопителям в сварочную кабину для наплавки. Исправные корпуса устанавливают на сборочный стенд, по конструкции аналогичный стенду. Дефектоскопом проверяют также корпуса, поступающие на сварочные работы после выправления изгибов.
Наплавляют изношенные места корпусов автосцепок, а также детали механизма сцепления (при помощи специальных приспособлений) на манипуляторе. При необходимости используют сварочный стол. Хвостовик автосцепки наплавляют на установки. Нагрев деталей осуществляется индукционно-металлургическим способом, с помощью специального комплекса устройств.
29
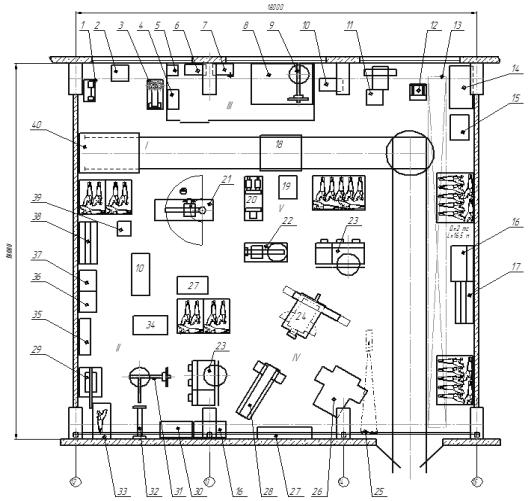
Рис. 10. Схема контрольного пункта автосцепки: I – участок наружной очистки; II – участок для разборки, дефектоскопирования и сборки автосцепки; III – участок сварочных и наплавочных работ;
IV – участок механической обработки; V – участок ремонта поглощающих аппаратов, тяговых хомутов, упорных плит и других деталей; 1 – пневмопресс правки предохранителя замка; 2 – печь для
нагрева автосцепки; 3 – стенд правки хвостовика автосцепки (корпуса); 4 – аппарат сварочный для наплавки порошковой проволокой; 5 – электродуговая строжка; 6 – сварочное оборудование; 7 – стол для наплавки деталей автосцепки; 8 –установка для наплавки тяговых и ударных поверхностей контура зацепления автосцепки порошковой проволокой с последующей обработкой; 9 – манипулятор корпуса автосцепки (при наплавке); 10 – стол для дефектоскопистов; 11 – стенд для обработки (фрезеровки) корпуса автосцепки после наплавки (шипа, торца, отв.под валик); 12 – пресс для клеймения корпуса и деталей автосцепки; 13 – кран-балка Q=2 т; 14 – накопитель хомута; 15 – изолятор брака; 16 – стол проверки деталей автосцепки; 17 – стеллажи для хранения деталей автосцепного устройства (годные детали); 18 – бескабельная передаточная тележка; 19 – станок вертикально-сверлильный; 20 – стенд разборки и сборки поглощающего аппарата; 21 – станок радиально-сверлильный; 22 – стенд испытания поглощающих аппаратов; 23 – стенд разборки и сборки автосцепки; 24 – вертикально-фрезерный станок; 25 – кран консольный передвижной; 26 – станок сгоризонтально-фрезерный; 27 – шкафы для хранения шаблонов и инструментов; 28 – горизонтально-строгальный станок для обработки зева автосцепок; 29 – стенд дефектоскопии хомута; 30 – стенд дефектоскопии корпуса автосцепки (дефектоскоп и намагничивающие устройства); 31 – стол для проверки прогиба хвостовика автосцепки; 32 – стенд дефектоскопии маятниковой подвески, маятника и клина; 33 – эталон корпуса автосцепки (трещины) для проверки (настройки) дефектоскопа; 34 – изолятор брака; 35 – эталон хомута (трещины) для проверки (настройки) дефектоскопа; 36 – стол проверки плиты упорной, балочки, маятника и клина, хранение дефектоскопа; 37 – стол для проведения дефектоскопии деталей автосцепки; 38 – стеллажи для хранения деталей (годные детали); 39 – станок обдирочно-шлифовальный; 40 – машина для мойки корпуса автосцепки
30