
Все лаборатарные работы
.pdf
2.3. ЭКСПЕРИМЕНТАЛЬНАЯ ЧАСТЬ
Опыт 2.1. Нейтрализация щелочных сточных вод углекислым газом
Цель работы: проведение процесса нейтрализации щелочной воды углекислым газом, определение степени нейтрализации, времени обработки воды и количества углекислого газа.
Выполнение опыта
Для определения начальной концентрации исследуемой щелочной воды в коническую колбу для титрования налейте 5 мл щелочной воды, добавьте 1 каплю фенолфталеина. Оттитруйте пробу 0,1 н раствором HCl до обесцвечивания, рассчитайте концентрацию гидроокиси в растворе по формуле
В[OH- ] =VHCl 0,1,
Vпробы
где VHCl - объем 0,1 н раствора HCl, израсходованной на титрование,мл; Vпробы - объем пробы, взятой на титрование, мл.
При помощи индикаторной бумаги определите рН.
Затем в стакан налейте 200 мл щелочной воды и барботируйте СО2 из аппарата Киппа, где происходит реакция
2 HCl + СаСО3 → CaCl2 + H2O + CO2.
Углекислый газ можно получать в колбе Вюрца, добавляя к мелу соляную кислоту 1: 4.
Через 3, 5, 7, 10, 15 мин отберите с помощью пипетки с грушей по 5 мл воды, определите рН универсальным индикатором и ВОН-
титрованием раствором HCl (аналогично исходной). Данные занесите в табл. 2.4.
|
|
|
|
|
|
Таблица 2.4 |
|
№ опыта |
τ, мин |
рН |
VHCl , мл |
BOH- |
η, % |
|
MCO2 |
|
|
|
|
|
|
|
|
Количество углекислого газа, поглощенного щелочным раствором, рассчитать по уравнению
MCO2 =(B[OH- ]нач −B[OH- ]τ ) Vводы τ,
где Vводы = 200 – Vна титрование; τ – время.
170

Степень нейтрализации вычислите по уравнению
η= В[OH- ]нач −В[OH- ]τ 100 %. B[OH- ]нач
Постройте следующие зависимости: η = f (τ); η = f ( МСО2 ) . Напишите уравнение реакции нейтрализации.
Опыт 2..2. Сульфитная очистка хромовых сточных вод
Цель работы: определение оптимального значения величины рН реакционной среды для полного восстановления шестивалентного хрома.
Выполнение опыта
В 6 стаканчиков налейте по 25 мл K2Cr2O7. Для создания определенного значения рН добавьте по каплям с помощью пипетки 2 н раствор H2SO4, контролируя рН универсальной индикаторной бумагой (табл.2.5). Затем в хроматные растворы с различным значением рН прилейте по 0,5 мл раствора Na2SO3. Определите концентрацию Cr (VI) в растворах. Для этого в 5 мерных колб на 25 мл поместите по 0,5 мл исследуемых растворов, добавьте 1 мл ДФК (дифенилкарбазида), доведите до метки
дистиллированной водой и определите оптическую плотность растворов (Аi) на фотоколориметре (λ = 535 нм). Для сравнения таким же способом найдите оптическую плотность начального раствора (Анач). По калибровочной кривой определите концентрацию Cr (VI).
Степень восстановления хрома (η) рассчитайте по формуле (2.33) для каждого раствора:
|
Снач6+ - |
Сi |
6+ |
|
|
η= |
Cr |
Cr |
|
100 %. |
(2.33) |
Снач6+ |
|
||||
|
|
|
|
||
|
Cr |
|
|
|
|
Постройте график зависимости степени восстановления Cr (VI) от величины рН реакционной среды: η = f (pH).
Напишите уравнение реакции K2Cr2O7 с Na2SO3.
171
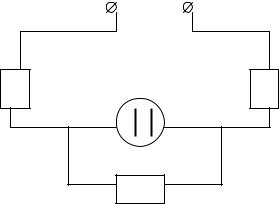
|
|
|
|
|
|
|
Таблица 2.5 |
|
|
|
|
|
|
|
|
|
|
№ раствора |
рН |
VH SO |
4 |
,мл |
А |
СCr(VI) , мг/л |
|
η, % |
|
|
2 |
|
|
|
|
|
|
1 |
1 |
1 |
|
|
|
|
|
|
2 |
2 |
0,5 |
|
|
|
|
|
|
3 |
3 |
0,3 |
|
|
|
|
|
|
4 |
4 |
0,2 |
|
|
|
|
|
|
5 |
5 |
0,1 |
|
|
|
|
|
|
Исх.р-р |
6 |
0 |
|
|
|
|
|
Опыт 2.3. Изучение процессов очистки сточных вод электролизом Цель опыта: изучение влияния условий электролиза на электрохимическое восстановление шестивалентного хрома.
|
Выполнение опыта |
Для проведения электролиза соберите электрическую схему, |
|
изображенную на рис. 2.3. |
|
+ |
– |
R |
Я |
A |
|
|
|
|
V |
|
Рис. 2.3. Электрическая схема: R – реостат, Я – электрохимическая ячейка, V – вольтметр, А – амперметр
В химический стакан налейте 50 мл раствора, содержащего Cr (VI), установите с помощью амперметра ток 0,2 А и проведите электролиз в течение 2 мин. Раствор отфильтруйте через складчатый фильтр и определите концентрацию Cr (VI). Для этого в мерную колбу на 25 мл поместите 5 мл исследуемого раствора, добавьте 1 мл ДФК (дифенилкарбазида), доведите объем до метки дистиллированной водой и определите оптическую плотность раствора (Аi) на фотоколориметре (λ = 535 нм). Для сравнения так же определите оптическую плотность исходного раствора (Аисх).
172
По калибровочной кривой определите концентрацию Cr (VI). Опыт повторите, увеличивая время электролиза до 5, 7, 10, 15 мин.
Степень восстановления хрома (η) рассчитайте по формуле (2.33) для каждого раствора.
Экспериментальные данные занесите в табл. 2.6.
|
|
|
|
Таблица 2.6 |
|
|
|
|
|
|
|
№ р-ра |
τ, мин |
А |
СCr(VI) , мг/л |
|
η, % |
1 |
2 |
|
|
|
|
2 |
5 |
|
|
|
|
3 |
7 |
|
|
|
|
4 |
10 |
|
|
|
|
5 |
15 |
|
|
|
|
Исходный |
- |
|
|
|
|
раствор |
|
|
|
|
|
Постройте график зависимости степени восстановления Cr (VI) от времени электролиза: η = f(τ).
173
3. ОТДЕЛЕНИЕ И УТИЛИЗАЦИЯ ТВЕРДЫХ ОТХОДОВ
В состав твердых отходов машиностроительной и других отраслей промышленности входят: черные и цветные металлы, шлаки, окалина, зола, шламы, флюсы, отходы деревообработки - древесная стружка и опилки, пластмассы, а также значительное количество разнообразной пыли, задерживаемой пылеулавливающими установками.
3.1. ЦЕЛЬ РАБОТЫ
Ознакомление с твердыми отходами металлургии, машиностроения и приборостроения, а также сопутствующих производств и возможными путями их отделения и утилизации. Овладение навыками экспериментального отделения твердой фазы различными методами.
3.2. УТИЛИЗАЦИЯ ТВЕРДЫХ ОТХОДОВ МЕТАЛЛУРГИЧЕСКИХ ПРОИЗВОДСТВ И ЭНЕРГЕТИЧЕСКИХ УСТАНОВОК
Получение металлов из руд, представляющих собой различные оксиды, сульфиды, карбонаты металлов, проводят их восстановлением углеродом, оксидом углерода (II), водородом, магнием, алюминием, например, по реакциям:
FeO + CO Fe + CO2 ; |
(3.1) |
TiCl4 + 2 Mg Ti + 2 MgCl2 ; |
(3.2) |
2 Fe2O3 + 3 C 4 Fe + 3 CO2 ; |
(3.3) |
CrO3 + 2 Al Cr + Al2O3 . |
(3.4) |
При плавке руды добавляют флюсы, например CaCO3 и SiO2, которые, превращаясь в шлак, позволяют извлекать из металла серу и фосфор, являющихся вредными примесями:
FeS + CaO + C = CaS + Fe + CO. |
(3.5) |
Шлаки предохраняют поверхность расплавленного металла от |
|
окисления: |
|
2 FeO + Si SiO2 + 2 Fe . |
(3.6) |
Ежегодно при производстве чугуна и стали в нашей стране образуется свыше 70 млн. т металлургических шлаков. Помимо этого при работе таких производств, как агломерационное, доменное, сталеплавильное, горячего проката, травления металлов образуются значительные массы шламопылевых отходов. Например, объем шламов, содержащих примерно 50 % железа, составляет около 20 млн. т, что при возвращении в производство может заменить примерно десятую часть железорудного сырья. Выход шлака в цветной металлургии достигает 10-200 т на 1 т получаемого металла.
174
В результате взаимодействия золы топлива, компонентов пустой породы и флюсов образуются металлургические шлаки, представляющие собой силикатные системы с различным содержанием железа, обладающие определенными физическими свойствами и химическим составом. Так, в зависимости от химического состава различают основные, в которых преобладают оксиды кальция и магния (CaO и MgO); кислые, отличающиеся повышенным содержанием оксидов кремния и алюминия (SiO2 и Al2O3), и нейтральные, с одинаковым содержанием перечисленных оксидов - доменные шлаки. В табл. 3.1 приведен состав шлаков ряда металлургических предприятий.
Таблица 3.1
Химический состав металлургических шлаков
Вид шлака |
|
|
|
Состав, % масс. |
|
|
||||
|
|
|
SiO2 |
Al2O3 |
CaO |
MgO |
Fe2O3 |
FeO |
MnO |
SO3 |
Доменные |
|
|
|
|
|
|
|
|
||
шлаки заводов |
|
|
|
|
|
|
|
|
||
юга |
|
|
33-38 |
5-9 |
45-50 |
2-4 |
0,5-15 |
1-3 |
2-3 |
2-4 |
То |
же |
за- |
|
|
|
|
|
|
|
|
водов центра |
37-40 |
7-9 |
44-48 |
1-3 |
0,1-0,3 |
0,3-0,5 |
0,5-15 |
2-4 |
||
То |
же |
заво- |
|
|
|
|
|
|
|
|
дов |
Урала и |
|
|
|
|
|
|
|
|
|
Сибири |
|
35-37 |
12-16 |
30-38 |
4-7 |
0,1-0,3 |
0,1-0,4 |
0,5-20 |
0,5-15 |
|
Сталеплавиль- |
|
|
|
|
|
|
|
|
||
ные шлаки: |
|
|
|
|
|
|
|
|
||
а) |
мартенов- |
|
|
|
|
|
|
|
|
|
ские |
|
|
22-25 |
2-6 |
38-40 |
9-14 |
2-4 |
5-12 |
6-9 |
0,2-0,6 |
б) |
ваграноч- |
|
|
|
|
|
|
|
|
|
ные |
|
|
38-46 |
9-13 |
20-32 |
5-20 |
0,5-15 |
5-13 |
5-8 |
0,2-0,4 |
Шлаки |
цвет- |
|
|
|
|
|
|
|
|
|
ной металлур- |
|
|
|
|
|
|
|
|
||
гии |
(никеле- |
|
|
|
|
|
|
|
|
|
вые, медные и |
35-40 |
6-10 |
16-18 |
2-7 |
1-2 |
20-35 |
0,1- |
0,5-20 |
||
др.) |
|
|
|
0,4 |
||||||
|
|
|
|
|
|
|
|
|
|
|
Как видно из табл. 3.1, шлаки содержат богатый спектр химических соединений, поэтому они являются ценным сырьем для получения строительных материалов и изделий, являющихся более качественными и дешевыми, чем получаемые из природного сырья. Переработку доменных шлаков можно проводить разными способами. Основным способом в настоящее время является их грануляция. Гранулированные доменные шлаки являются хорошим материалом для дорожного строительства, пригодны для
175
производства цемента, шлакового щебня, пемзы, минераловатных и других изделий.
Масштабы образования сталеплавильных шлаков примерно вдвое меньше, чем доменных. Так, в 1975 г. их выход составил несколько более 22,3 млн т, в том числе 66,5 % мартеновских, 29,4 % конверторных и 3,7 % электросталеплавильных. Основная их масса (87,6 %) была направлена в отвалы.
Сталеплавильные шлаки содержат железо (до 24 % в виде оксидов и до 20 % в металлической форме), MnO до 11 %, различные оксиды (SiO2, Al2O3, MgO, Cr2O3, P2O5) и сульфиды (FeS, MnS и др.). Они характеризуются большой плотностью (до 3,2 т/м3) и имеют неоднородную структуру (включения корольков металла, кусков извести).
Состав и свойства сталеплавильных шлаков определяют возможные направления их переработки и использования. В настоящее время около половины перерабатываемой массы этих шлаков идет на изготовление щебня, около 30 % используется в качестве оборотного продукта (в виде флюса в доменной шихте и вагранках), примерно пятая часть перерабатывается в удобрения для сельского хозяйства, весьма незначительное количество идет на изготовление минераловатных изделий. При переработке сталеплавильных шлаков с помощью электромагнитных сепараторов из них извлекается металл.
Отвальные шлаки цветной металлургии содержат значительное количество ценных компонентов. Например в отвалах шлаков на медных заводах бывшего СССР находится примерно 27 млн. т Fe, 335 тыс. т Cu и 2 млн т Zn, а шлаковые отвалы свинцовых заводов включают около 3 млн т Fe, более 900 тыс. т Zn, 150 тыс. т Pb и 70 тыс. т Cu. Содержание отдельных металлов в ряде шлаков выше, чем в добываемых рудах, поэтому такие шлаки должны перерабатываться с целью извлечения из них ценных составляющих.
Согласно химическому составу шлаки цветной металлургии могут быть условно объединены в три группы. В одну из них можно объединить шлаки никелевых заводов и часть шлаков медных заводов, отличающихся малым содержанием цветных металлов и железа. Извлечение ценных компонентов из таких шлаков экономически нецелесообразно, поэтому наиболее приемлемым путем утилизации этих отходов является переработка в различные строительные материалы и изделия.
Вторую группу могут составить медные шлаки, отличающиеся значительным содержанием железа, малым содержанием меди и наличием ≤5 % Zn и Pb. Такие шлаки целесообразно перерабатывать лишь при комплексном извлечении Fe, Zn и Pb с одновременной утилизацией силикатной части.
В третью группу входят оловянные, свинцовые и часть медных шлаков, отличающихся значительным содержанием Zn, Pb и Sn. Высокое содержание этих компонентов делает экономически выгодным их извлечение даже без
176
комплексной переработки шлаков.
Технологическая схема переработки шлаков выбирается в зависимости от их состава и физико-химических свойств и может включать как гидрометаллургические, так и пирометаллургические способы извлечения металлов. При пирометаллургическом способе осуществляют восстановление металлов из их безводных соединений в условиях высоких температур. Гидрометаллургический метод связан с восстановлением металлов из водных растворов их соединений различными методами. Как и шлаки черной металлургии, шлаки производства цветных металлов служат сырьем для получения строительных материалов и изделий различного назначения. Технологии соответствующих производств в обоих случаях примерно одинаковы.
Энергетические установки. Основными компонентами,
выбрасываемыми в атмосферу при сжигании различных видов топлива в энергоустановках, являются CO2 и H2O, продукты неполного сгорания топлива - оксид углерода, сажа, углеводороды, несгоревшие частицы твердого топлива, зола, шлаки и прочие механические примеси. Современная ТЭЦ мощностью 2,4 млн кВт расходует до 20 тыс. т угля в сутки и выбрасывает 120-140 т твердых частиц (зола, пыль, сажа) при эффективности системы пылеулавливания 94-98 %. По объему образования (70 млн т/год) и составу твердые отходы сжигания топлив-золы и шлаки - близки к металлургическим шлакам. На 80-90 % химический состав золошлаковых отходов представлен оксидами Si, Al, Fe, Ca и Mg, находящимися в различных соотношениях; помимо этого в них присутствуют соединения Ti, V, Ge, Ga, S, а также несгоревшие частицы топлив (0,5-20 % масс.). Степень использования золошлаковых отходов не превышает 1,5-2,0 %. Значительное число ТЭС снабжено мокрыми золоуловителями или имеет системы гидрозолоудаления, что приводит к гидратации оксидов металлов, смешению зол с шлаками, их цементации, разнородности физико-химических характеристик отходов в отвалах, и таким образом затрудняет их использование, направления и масштабы которого определяются химическим составом и свойствами золошлаковых отходов. Большая часть используемой массы этих отходов служит сырьем для производства строительных материалов и изделий.
Золы и шлаки от сжигания углей, сланцев и торфа могут широко использоваться в качестве вяжущего для производства силикатного кирпича при содержании в них не менее 20 % CaO или в виде кремнеземистого заполнителя, если содержат до 5 % CaO; содержание частиц несгоревшего топлива при этом не должно превышать 5 %. Золы с высоким содержанием частиц угля используются в качестве отощающей и топливной добавки к глине в количестве 15-50 % по весу (иногда до 80 %) при производстве красного (глиняного) кирпича.
Золы ТЭС используются для получения искусственных пористых заполнителей - аглопоритового (с содержанием ≤ 5-10 % горючих) и зольного гравия (с содержанием ≤ 3 % горючих).
177
Как кислые золошлаковые отходы, так и основные, с содержанием свободной извести до 10 % и до 5 % горючих, используют в качестве активной минеральной добавки при производстве цемента; их же можно применять в качестве гидравлической добавки (10-15 %) к цементу. Золошлаковые отходы широко используют в дорожном строительстве, для производства минераловатных изделий. Использование золошлаковых отходов по перечисленным направлениям является не только экономически выгодным, но и позволяет повысить качество соответствующих изделий.
Золы сланцев и торфа содержат значительные количества CaO и используются для известкования кислых почв вследствие содержания значительных количеств K и P, а также микроэлементов, необходимых ряду сельскохозяйственных культур, они применяются практически без какойлибо дополнительной обработки в качестве удобрений. Некоторые виды золошлаковых отходов используют в качестве агентов очистки промстоков.
Золы углей и нефтей содержат многие металлы, причем в ряде случаев их концентрация в золе такова, что извлечение становится экономически выгодным; так, максимальные концентрации Sr, V, Zn, Ge в золе углей могут достигать 10 кг/т. В золе нефтей содержание V2O5 в отдельных случаях достигает по массе 65 %, кроме того, в ней в значительных количествах содержатся Mo и Ni. Зола торфа содержит значительные количества U, Co, Cu, Ni, Zn, V, Pb. Поэтому извлечение металлов становится еще одним направлением переработки этих отходов; из золы некоторых углей извлекают редкие и рассеянные элементы (в частности Ge и Ga), из золы мазутов - V, Ni и другие металлы.
Предприятия цветной металлургии также оказывают очень сильное воздействие на окружающую среду. Поэтому необходимо:
-комплексное использование руд цветных металлов, которые обычно полиметалличны, а перерабатываются нередко только как сырье для получения одного продукта;
-улавливание и переработка газообразных выбросов, содержащих вредные для природы, но в то же время необходимые для промышленности продукты;
-разработка технологий переработки твердых отходов с целью снижения их токсического воздействия и одновременного получения дополнительных сырьевых источников примесных металлов;
-использование многотоннажных отходов обогащения и выплавки металлов в технологии строительных материалов;
-повторное вовлечение в технологический процесс сточных вод после предварительного максимального извлечения примесей и их переработки на целевые продукты.
Выполнение всех этих рекомендаций обещает не только экологический эффект, но и заметную экономическую выгоду, так как отходы цветной металлургии обычно содержат весьма ценные продукты.
Экологическое совершенствование теплоэнергетики идет, как видим,
178
по различным взаимодополняющим направлениям.
Во-первых, улавливание, обезвреживание и целевая переработка газообразных выбросов, использование твердых отходов в других производствах и минимизация водопотребления.
Во-вторых, «улучшение» топлива путем предварительного удаления из него вредных примесей или переработки твердого горючего на жидкие продукты.
Третьим направлением является использование принципиально отличных от реакции горения источников энергии.
3.3. ТВЕРДЫЕ ОТХОДЫ МАШИНОСТРОЕНИЯ
ИИХ УТИЛИЗАЦИЯ
3.3.1.Твердые отходы некоторых производств машиностроения
Основными производствами любого машиностроительного комплекса являются литейное, сварочное, прокатное, кузнечно-прессовое, электрохимическая и механическая обработка металлов.
Литейное производство в качестве плавильных агрегатов оснащено вагранками, электродуговыми и индукционными печами. Они являются наиболее крупными источниками пылегазовыделения на машиностроительных предприятиях. При производстве тонны чугунных отливок выделяется 150-330 кг CO, около 1,5 кг SO2, 25-60 кг пыли, оксиды азота, фенол, аммиак и другие вредные вещества. Состав пыли зависит от сорта выплавляемой стали. Примерный химический состав пыли, выделяющейся при работе электродуговых печей, %: Fe2O3 - 56,8; Mn2O3 - 10,0; Al2O3 - 5,0; SiO2 - 6,9; CaO - 6,9; MgO - 5,8; остальное - хлориды, оксиды хрома и фосфора. Размер частиц пыли 0...20 мкм, однако основную ее массу (около 75%) составляют частицы 0,4 мкм.
Наибольшее количество пыли и газов выделяется при плавке металла в вагранках. Химический состав ваграночной пыли зависит от состава металлозавалки, шихты, состояния футеровки, вида топлива, условий работы вагранки. Типичный пример химического состава ваграночной пыли приведен ниже, %: SiO2 - 10...45; CaO - 2...18; Al2O3 - 0,5...25; MgO -0,5-5; Fe2O3 - 5...26; MnO - 0,5...9; C-10...64; PbO - до 8; P2O5 - 0,4; Na2O -1,5; K2O - 1,0. Ваграночная пыль отличается широким интервалом дисперсности (1-150 мкм), но основу составляют высокодисперсные частицы (до 70 %, выше 60 мкм).
Основным составляющим твердых отходов прокатных и кузнечнопрессовых цехов является окалина, до 2 – 4 % от массы прокатываемого металла. При этом масса частиц размером более 1 мм составляет до 90 % от всей массы окалины. Кроме того, в процессе обработки металла в этих цехах выделяется много пыли, туманов кислот и масел. В среднем общий выброс пыли из цеха составляет 200 г на 1 т товарного проката.
179