
Все лаборатарные работы
.pdfВ сварочном производстве одним из видов сварки и пайки чугуна, цветных металлов и некоторых специальных сталей является сварка под флюсом. Применение флюсов помогает удалить оксидную пленку. Нанесенный на соединяемые поверхности флюс в процессе нагрева плавится, растекается, смачивает поверхность и вступает в химическое взаимодействие, в результате которого образуются легкоплавкие шлаки. Сварочные шлаки или флюсы, представляющие собой сплав различных оксидов и солей, имеют пониженный по сравнению с жидким металлом удельный вес и поэтому располагаются в основном на поверхности металлической ванны.
Сварочные флюсы - шлаки существенно отличаются от металлургических по химическому составу и по условиям взаимодействия с металлом. Однако некоторые наиболее общие принципы и представления об их составе имеют несомненное сходство. Так, для флюсования основных оксидов, например FeO, во флюсы вводят оксиды кислотного характера, такие как: SiO2, B2O3, TiO2 и др. Для флюсования оксидов кислотного характера применяются соединения, дающие основные оксиды, например, сода Na2CO3, поташ K2CO3. Для флюсов растворителей применяются галоидные соли щелочных и щелочно-земельных металлов: NaCl, KCl, LiCl, CaCl2, NaF, CaF2 и др. Добавление этих веществ необходимо для борьбы с пористостью шва, вызываемой образованием оксида углерода, водорода и паров воды. Вводимые вещества должны подавить реакции образования этих соединений в момент кристаллизации металла. Например, добавка CaF2 приводит к реакции
2 CaF2 + 3 SiO2 2 CaSiO3 + SiF4, |
(3.7) |
а затем |
|
SiF4 + 3 H SiF + 3 HF , |
(3.8) |
CaF2 + H CaF + HF, |
(3.9) |
SiF4 + 2 H2O SiO2 + 4 HF. |
(3.10) |
В результате этих процессов уменьшается содержание водорода и паров воды и образуется нерастворимый в металле фтористый водород. Для обеспечения соответствующей вязкости вводятся специальные добавки в виде хлоридов марганца, титана, оксидов натрия, калия и др. Некоторые оксиды нерастворимые в жидком металле, образуют отдельную фазу и сравнительно легко переходят в шлак. К их числу относятся оксиды титана, кремния, марганца, алюминия и др.
Как было показано выше, сера и фосфор являются вредными примесями в металлах и сплавах. Наличие кремния и алюминия в металле значительно ускоряет процесс его десульфурации путем включения серы в состав образующихся шлаковых частиц. Удаление фосфора из сварочной ванны основано на его окислении и последующем связывании фосфорного ангидрида P2O5 в прочное легко отшлаковываемое комплексное соединение:
180
CaO + FeS + C CaS + Fe + CO, |
(3.11) |
2 CaO + 4 Fe3F + 5 O2 2 Ca(PO3)2 + 12 Fe. |
(3.12) |
Важные функции сварочных флюсов – шлаков следующие:
1)защита жидкого металла от непосредственного контакта с воздухом;
2)проведение в той или иной степени процессов раскисления, легирования и рафинирования металла;
3)улучшение теплового режима сварки путем снижения скорости охлаждения металла;
4)поддержание устойчивого процесса сварки;
5)обеспечение правильного формирования металла шва.
Процесс сварки под флюсом связан со значительным выделением пыли при засыпке флюса в бункер и при сборе остатков флюса после сварки, а также образованием значительного количества отходов продуктов взаимодействия флюса с химическими веществами на поверхности металлических изделий.
Газовая и плазменная резка металлов также сопровождается выделением пыли и вредных газов. Пыль представляет собой конденсат оксидов металлов, размер частиц которого не превышает 2 мкм. Химический состав пыли определяется маркой разрезаемого материала, обычно это токсичные соединения хрома и никеля, титана, железа, марганца, вредные
газы CO, NxOy.
В цехах механической обработки образуются стружка, пыль, туманы масел и эмульсий. В процессах шлифования и полирования выделяется большое количество тонкодисперсной пыли. Пыль, образующаяся в процессе абразивной обработки, на 30-40 % состоит из материала абразивного круга, на 60-70 % - из материала обрабатываемого изделия. Вредные выбросы цехов механической обработки древесины состоят в основном из опилок, стружки и древесной пыли.
Таким образом, при использовании различных методов сварки, литья, проката и механической обработки металлов образуется большое количество отходов в виде остатков флюса, шлаков, металлической стружки и т.д. и поэтому возникает проблема сбора, переработки и дальнейшего их использования.
3.3.2. Возможные пути утилизации твердых отходов машиностроения
Твердые отходы в машиностроении образуются в процессе производства продукции в виде амортизационного лома (модернизация оборудования, оснастки, инструмента), стружки и опилок (металлов, древесины, пластмасс и т. п.); шлаков и золы; шламов, осадков и пыли (отходы систем очистки воздуха) и др. Отходы машиностроительных
181
предприятий, в основном, образуются от производства проката (концов, обрезков, обдирочной стружки, опилок, отрезков слитков на ножницах и пилах и др.); производства литья (литников, шлаков, съемов и др.) и механической обработки. Основными источниками образования отходов легированных сталей являются металлообработка – 84 % и амортизационный лом – 16 %.
Стружки, металлические опилки, окалина могут найти применение при коагуляционной очистке сточных вод от активных красителей. Отходы древесины широко используются для изготовления товаров культурнобытового назначения и хозяйственного обихода, изготовляемых, главным образом, методом прессования.
До 98 % сильно токсичного металла, каким является кадмий, можно удалить из сточных вод с помощью обычных древесных опилок, предварительно обработанных щелочью. Возможна переработка промышленных отходов, содержащих органические вещества (опилки, стружки, обрезки и др.) наряду с другими естественными и искусственными органическими материалами в сырье для получения пористых углеродных адсорбентов - активных углей, широко используемых в промышленности для очистки жидких и газообразных сред и производства катализаторов.
Вмашиностроительном комплексе используется более 20 % пластмасс
исинтетических смол, выпускаемых в нашей стране. Утилизация, безопасное хранение и переработка огромного количества полимерных материалов, входящих в состав пришедших в негодность машин, - важная составляющая современных природоохранных проблем машиностроения. Наиболее рациональным методом ликвидации пластмассовых отходов служит высокотемпературный нагрев без доступа воздуха (пиролиз), в результате которого из отходов пластмасс в смеси с другими отходами (дерево, резина и др.) получаются ценные продукты: пирогаз, горючий газ и пиролизная смола.
Некоторые способы утилизации различных видов шлаков были рассмотрены выше. Шламы из отстойников очистных сооружений и цехов химической и электрохимической обработки металлов содержат большое количество твердых частиц, от 20 до 300 г/л. После нейтрализации и сушки шламы используют для извлечения соответствующих металлов в качестве добавки к агломерационной шихте, в строительной индустрии и др.
3.3.3.Утилизация шламов
Вряде отраслей машиностроения широкое распространение получает электрохимическая обработка (ЭХО). Большим достоинством этого метода является возможность обработки специальных сплавов, обладающих повышенной жаропрочностью, вязкостью и твердостью. Однако ЭХО неразрывно связана с многократным использованием рабочей жидкости – электролита.
182
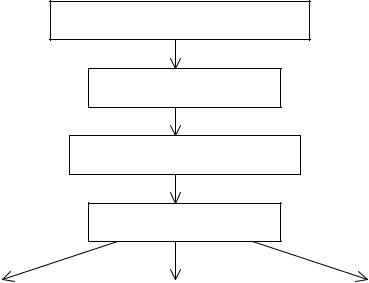
Для осуществления этого процесса необходима высококачественная очистка рабочей жидкости от продуктов анодного растворения (шламов), поскольку наличие их приводит к ухудшению качества поверхности, снижению точности обработки и уменьшению производительности процесса. Обычно шлам состоит из оксидов или гидроксидов металлов, нерастворимых в электролите и образующих суспензии или коллоидный раствор. С целью сохранения первоначальной электропроводности, вязкости и других физикохимических свойств электролита примеси необходимо устранять. Установлено, что шламы после электрохимической обработки представляют собой смесь, меняющуюся по составу, содержащую гидроксиды и основные соли металлов - железа, никеля, кобальта, алюминия, титана и др. Представляет интерес извлечение из шламов всех или основных дорогостоящих компонентов (Ni, Co, Mo, W, Cr и др.) в виде чистых элементов или их солей.
Схему утилизации шламов вне зависимости от их состава можно представить, как показано на рис. 3.1.
Как было показано выше, суть пирометаллургического способа связана с восстановлением металлов при высоких температурах. Процессы восстановления металлов из водных растворов их солей различными методами относятся к области гидрометаллургии. Основными стадиями при гидрометаллургической переработке являются перевод металла в раствор выщелачиванием и выделение металла из раствора известными методами, такими как: кристаллизация, адсорбция, ионное осаждение, флотация, экстракция, электролиз и др.
Шламосодержащий
Отделение шлама
Промывка, сушка шлама
Утилизация шлама
Регенерация |
|
Производство |
|
Производство |
ката- |
металлов пиро- и |
|
строительных |
|
лизаторов, флюсов, |
|
гидрометаллургиче- |
|
материалов |
|
электродных |
обма- |
ской переработкой |
|
|
|
зок, красок и пиг- |
|
|
|
||||
|
|
|
|
ментов |
|
|
|
|
|
|
|
183
Рис. 3.1. Схема утилизации шламов
Промышленный пирометаллургический передел до сих пор известен лишь для переработки никелевых шламов, при котором получают никелькобальтовый концентрат. Остальные металлы остаются в шламах. Шламы после обработки титановых сплавов и низколегированных сталей не перерабатываются и вывозятся на свалки.
Переплавка шламов ЭХО не может обеспечить получение исходного сплава в силу различных свойств входящих в его состав металлов. Однако плавка позволяет получить вторичный сплав, который может использоваться
вкачестве легирующего материала в производстве соответствующих сплавов.
Одним из направлений применения шламов является их использование
вкачестве катализаторов для некоторых нефтехимических производств. Известно, что многие нефтехимические процессы происходят в присутствии гетерогенных катализаторов, представляющих собой смесь оксидов, хлоридов или гидроксидов различных металлов.
Возможен вариант использования шламов вместо титановых концентратов. Схема использования шламов, полученных при размерной электрохимической обработке заготовок из сплавов на титановой основе, включает отмывку электролита из шламов водой, сушку и использование полученного продукта в составе шихты для изготовления сварочных электродных обмазок и флюсов вместо титановых концентратов (ильменита
ирутила) и оксида титана (IV). Титан в шламе находится в виде оксидов и гидроксидов. Гидроксиды при сушке перейдут в оксиды, их целесообразнее использовать после соответствующей переработки в качестве сырья для получения лаков, красок, пигментов.
Для снижения экологических последствий влияния ионов тяжелых металлов, содержащихся в шламе, можно связать ионы металлов в нерастворимые соединения, что достигается термической обработкой. В дальнейшем получают композиты с глиной, которые можно использовать в строительной индустрии, в производстве керамики, черепицы, красителей, стекла.
3.4.ЭКОЛОГИЧЕСКИЕ ПРОБЛЕМЫ ПРОИЗВОДСТВА ПОЛУПРОВОДНИКОВЫХ ПРИБОРОВ И МИКРОЭЛЕКТРОНИКИ
Микроэлектроника представляет собой одну из наиболее развитых отраслей производства и позволяет реализовать, например в одном кристалле кремния размером 5 мм2, более полумиллиона электронных компонентов. Особый интерес представляют программируемые БИС - микропроцессоры - схемы универсального применения. Использование микропроцессоров позволяет повысить «интеллект» производственного оборудования, создать
184
роботы нового типа, увеличить надежность, безопасность и эффективность устройств, автоматизировать сложные технологические процессы.
Применение комплекса электронных приборов для космических систем, полупроводниковых приборов для аппаратуры связи, индикаторных
идругих устройств имеет огромный экономический эффект.
Впроизводстве микроэлектронных схем и полупроводниковых приборов используется широкий комплекс материалов. К ним относятся металлы и сплавы, различные растворы, в состав которых входят вещества органической и неорганической природы, полимерные материалы, керамика, фарфор, стекла и полупроводниковые материалы. Полупроводниковые материалы могут использоваться в виде поликристаллов, аморфных спеченных порошков, монокристаллов и эпитаксиальных пленок. В эпитаксиальных пленках структура решетки полученного слоя является точной копией структуры кристалла подложки.
Полупроводниковые материалы делятся на элементарные и сложные. К элементарным относятся: кремний, германий, некоторые модификации бора, углерода, фосфора, мышьяка, сурьмы, висмута, серы, селена, теллура, йода; к
сложным - оксиды (Cu2O, Mn3O4, Al2O3, ZnO, CdO), сульфиды (PbS, CdS, ZnS, Bi2S3), селениды и теллуриды (CdSe, PbSe, HgSe, CdTe, PbTe, Bi2Te3),
арсениды (GaAs, InAs), фосфиды (GaP, InP), стеклообразные |
сплавы |
||
As2S3, As2Se3, |
сложные |
твердые растворы Cd - HgTe, PbTe - SnTe и др. |
|
Многие |
из этих |
веществ являются вредными, что |
необходимо |
учитывать как при синтезе полупроводниковых материалов, так и выращивании монокристаллов и эпитаксиальных пленок, создании p-n переходов, оксидных слоев, травлении поверхности, проведении различных операций при изготовлении полупроводниковых устройств. Например, соединения германия - слабые яды, оксид германия GeO2 является уже токсичным веществом. Токсичными свойствами обладают также мышьяк, кадмий, свинец и их соединения, арсениды, теллуриды, селениды и др.
При получении монокристаллических образцов и пленок полупроводниковых веществ и соединений применяются различные методы: выращивание монокристаллов вытягиванием из расплава, из раствора в расплаве, из газовой фазы, методы зонной плавки и др.
Для получения полупроводниковых веществ в виде монокристаллов определенной кристаллографической ориентации, которая обеспечивает требуемые электрофизические свойства, процесс осуществляется с применением затравки. При использовании, например, газофазного метода одновременно образуется большое число кристаллов на стенках кварцевого реактора, которые не отвечают требованиям по размерам, ориентации и свойствам. Выделяющиеся на выходе из реактора газообразные вещества загрязнены примесями. Сам реактор после однократного или многократного использования становится непригодным для дальнейшего применения. Таким образом возникают твердые, жидкие и газообразные отходы и проблемы их очистки и утилизации.
185
При использовании метода вытягивания монокристаллов на затравку из расплава (метод Чохральского), после получения кристаллов, например, в виде булей кремния и германия, остается расплав, который более обогащен примесями, что требует повторной очистки и регенерации.
На всех стадиях создания приборов образуются растворы, газы и твердые отходы, требующие нейтрализации и переработки. К ним относятся клей БФ для наклейки слитка на специальный столик при определении кристаллографической ориентации, абразивная суспензия для резки кристалла на алмазных дисках, в состав которой входят оксид алюминия с примесью кварца и алмазный порошок, карбиды кремния и бора, графит и др. Как при резке металлов, так и при дальнейшей шлифовке и сортировке пластин образуются сколы или дефектные пластины, которые идут в отходы.
Экологические проблемы связаны также с наличием сточных вод, образующихся при химическом травлении полупроводниковых кристаллов, которое применяется для выявления кристаллической структуры, дефектов и других неоднородностей. Используются растворы с целью предварительной очистки поверхности и получения кристаллов требуемой толщины и окончательной очистки поверхности кристалла.
Для травления германия и кремния широко используются растворы, содержащие перекись водорода Н2О2 с добавлением HF и HCl, увеличивающих скорость реакции, и электролиты на основе HNO3-HF.
3.5. СПОСОБЫ ОТДЕЛЕНИЯ ТВЕРДОЙ ФАЗЫ Для отделения твердой фазы используются процессы седиментации,
коагуляции и флокуляции, микро- и макрофильтрации, сорбции и адсорбции, химические и электрохимические.
При проведении вышеперечисленных процессов используются методы гравитационного, центробежного, мембранного и электрохимического разделения фаз. Условная классификация методов представлена на рис.3.2.
К гравитационным методам относятся седиментация в отсутствии и присутствии флокулянтов и коагулянтов, фильтрация. Под седиментацией понимают осаждение частиц под действием гравитационного поля.
Центробежное отделение твердой фазы под действием центробежных и центростремительных сил происходит в таких аппаратах, как центрифуги, открытых, напорных или многоярусных гидроциклонах.
Методы мембранного разделения условно делятся на микро- и ультрафильтрацию, обратный осмос, испарение через мембраны, диализ. Наибольшие успехи, с точки зрения эффективности и технологичности разделения (отделения твердых примесей), достигнуты с помощью обратного осмоса и ультрафильтрации.
Разделение частиц дисперсной системы под действием электрического поля можно отнести к электрохимическим методам.
3.5.1. Центрифугирование (к опыту 3.2)
186
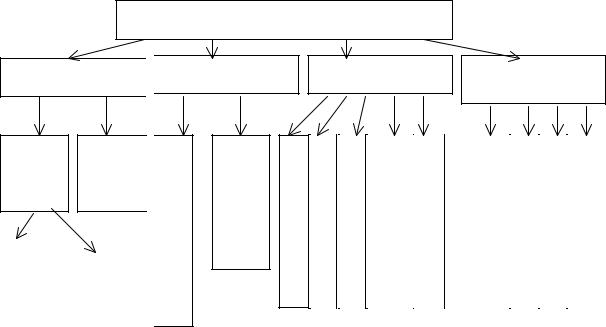
Разделение твердых и жидких фаз суспензий в поле центробежных сил осуществляется в аппаратах двух типов: центрифугах и гидроциклонах. При центробежном разделении ускорение оседающей твердой частицы по
сравнению с гравитационным ускорением возрастает на величину Kp = ω2r/g, где ω - угловая скорость вращения жидкости, r - радиус вращения; g - ускорение свободного падения. Эту величину называют фактором разделения. Она характеризует эффективность процесса.
Методы отделения твердой фазы
Гравитационные
Седиментация
Без коагулянтов и |
|
|
|
В присутствии |
|
|
|
|
Центрифугирован
Разделение в циклонах
Микрофильтра |
Ультрафильтра |
Обратный |
Испарение через мембрану |
Диализ |
Электрофлотац |
Электродиализ |
Электрофорез |
Электроосмос |
|
|
|
|
Рис. 3.2. Классификация методов отделения твердой фазы
Существует ряд центрифуг и центробежных аппаратов различного типа. Однако движение частиц в гравитационном поле одинаково независимо от аппарата. Скорость движения частиц зависит, в первую очередь, от центробежного эффекта, который прямо пропорционален радиусу центрифуги, квадрату угловой скорости и диаметру частиц. Установлено, что скорость центрифугирования суспензий с размером частиц 5 мкм в 25 раз выше, чем с размером частиц 1 мкм. Эффект размера частиц можно усилить путем агрегации или флокуляции, в результате которых образуются крупные частицы, что облегчает их выделение.
После центрифугирования для выделения конечного продукта, так же как после фильтрации, необходимы операции промывки и сушки осадка.
3.5.2. Седиментация (к опыту 3.3)
187
Седиментация – осаждение частиц под действием гравитационного поля. Для улучшения отделения твердой фазы дисперсных систем седиментацией необходимо применение специальных веществ - флокулянтов, способствующих агрегации или флокуляции частиц и увеличению скорости осаждения взвесей. Флокулянты - это водорастворимые полимеры с полярными концевыми функциональными группами. Их действие основано на том, что концы цепеобразных полимерных макромолекул сорбируют взвешенные частицы и связывают их в рыхлые сетчатые трехмерные агрегаты.
Наибольшее распространение в нашей стране получило использование в качестве флокулянта полиакриламида.
Методы осаждения конструктивно просты, бесшумны и обладают малой энергоемкостью. Хотя из-за большой влажности отделенного осадка данные методы не применяют непосредственно для очистки от твердых примесей, но они получили распространение для сгущения очищаемой среды и первичного выделения осадков.
Метод осаждения находит применение для выделения твердой фазы и дает положительный эффект в комбинации с другими методами, например, при наложении электрических и магнитных полей.
3.5.3. Фильтрация (к опыту 3.4)
Фильтрами называют устройства, в которых очистка жидкостей от частиц твердой фазы осуществляется в процессе их протекания через перегородку, имеющую сквозные микроканалы (поры). Фильтрующая перегородка, являющаяся важнейшей частью любого фильтра, может задерживать твердые частицы либо своей поверхностью с образованием осадка, либо внутренней извилистой поверхностью микроканалов. Движущей силой процесса фильтрования является разность значений давления по обе стороны фильтровальной перегородки.
Применение фильтрования для выделения осадка зависит от размера частиц и характера их агрегации. Существуют сетчатые, волокнистые и зернистые фильтры. Сетчатые фильтры служат для задержания сравнительно грубых частиц. Их изготовляют из одного или нескольких слоев ткани или металлической сетки. Действие этих фильтров основано на механическом задерживании больших частиц, не проходящих через ячейки сетки, а также на инерционном осаждении частиц. Эффективность сетчатых фильтров заметно увеличивается по мере забивания их отфильтрованной дисперсной фазой, поскольку в результате образования на поверхности фильтра так называемого намывного слоя уменьшается диаметр отверстий. Поэтому иногда на тканевые фильтры перед их использованием наносят асбестовую пыль, особенно эффективную при фильтрации.
Волокнистые фильтры делают из фильтровальной бумаги, специального картона и некоторых других волокнистых материалов. Вследствие значительного гидравлического сопротивления эти фильтры
188
применяют лишь при небольших скоростях течения фильтрующегося раствора (суспензии). С целью повышения производительности волокнистых фильтров их часто изготавливают с «развернутой» (увеличенной) поверхностью.
Взернистых фильтрах широко используют в качестве фильтрматериалов кварцевый песок, дробленый шлак, гравий, антрацит и т.п. Зернистые фильтры изготавливают однослойными и многослойными. Регенерация зернистых фильтров предусматривает промывку обратным потоком чистой воды или сжатым воздухом.
Фильтрование под вакуумом применяется для очистки маловязких жидкостей. Степень очистки в вакуум-фильтрах не превышает, как правило, 80 %, но удельная производительность очистки наиболее высокая. Тонкость очистки в вакуум-фильтре определяется фильтрующими свойствами пористого элемента (ткани, бумаги и др.). Конструктивных разновидностей вакуум-фильтров много, однако наиболее распространенными являются барабанные, дисковые и ленточные фильтры.
Характер сырья и конечная цель применения полученного осадка обусловливают тщательность промывки осадка. Если использовался водный раствор, то достаточно промывки простой водой. Однако если вещества не растворимы в воде, например при использовании алканов или других углеводородов, то требуется промывка растворителем. Часто, чтобы избежать дополнительного выделения, промывку осадка проводят на фильтре.
Восадке после фильтрации содержится определенное количество влаги. Поэтому полученный продукт высушивают так, чтобы содержание влаги было минимальным. Остаточная влага связана с компонентами продукта. Способ сушки выбирается в зависимости от требований к качеству
иконечной форме продукта.
3.5.4. Обратный осмос и ультрафильтрация (к опыту 3.4)
Осмос - процесс широко распространенный в природе. Суть его сводится к односторонней диффузии растворителя через полупроницаемую перегородку между растворами разной концентрации. Осмос служит для отделения твердых частиц при незначительных объемах жидкости из отходов гальванических, химических, фармацевтических производств, содержащих пригодные к повторному использованию металлы, мономеры, димеры, лекарственные препараты и пр.
Устройства для обратного осмоса и ультрафильтрации делятся по способу укладки мембран в объеме.
В настоящее время наиболее распространены аппараты типа «фильтрпресс» с плоскими мембранами. Такие аппараты состоят из плотно сжатых между двумя фланцами плоских фильтрующих элементов (рис.3.3) прямоугольной или круглой формы, разделенных тонкими (например, паронитовыми) прокладками. Последние образуют периферийные стенки ка-
189