
[SHipinsky_V.G.]_Oborudovanie_i_osnastka_upakovoch(z-lib.org)
.pdf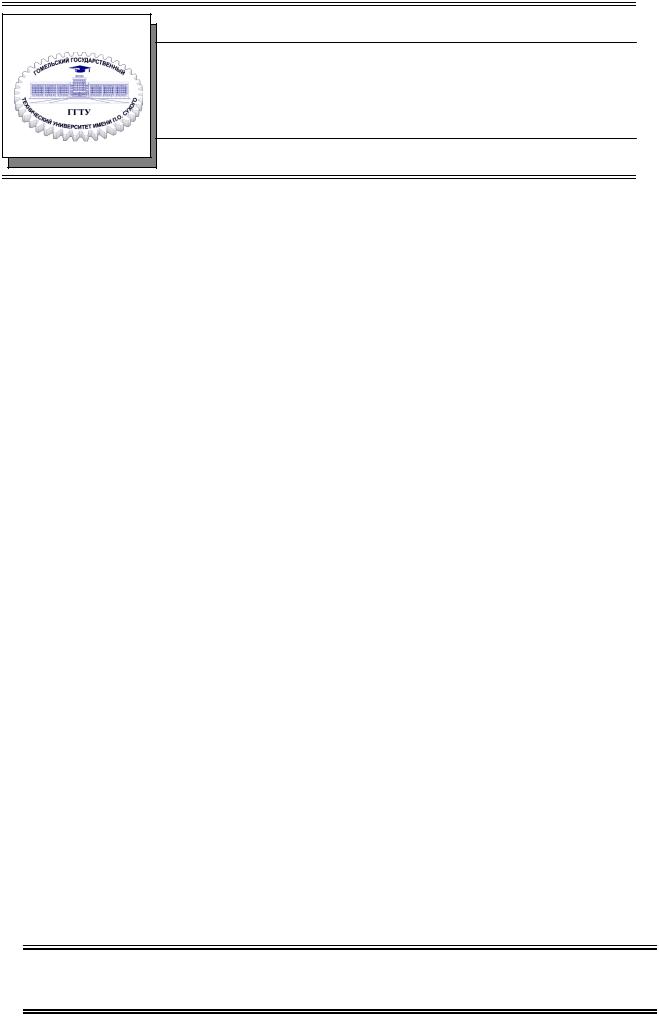
Министерство образования Республики Беларусь
Учреждение образования «Гомельский государственный технический университет имени П.О. Сухого»
Кафедра «Обработка материалов давлением»
В. Г. Шипинский
ОБОРУДОВАНИЕ И ОСНАСТКА УПАКОВОЧНОГО ПРОИЗВОДСТВА
Часть III .
Средства технологического оснащения (Продолжение)
УЧЕБНОЕ ПОСОБИЕ
для студентов специальности I-36 20 02-03 «Упаковочное производство (технологии и оборудование упаковочного производства)»
Гомель 2013
УДК 621. 798.06(075.8)
ББК 30.61я73
Ш65
Шипинский В. Г.
Ш65 Оборудование и оснастка упаковочного производства.
Часть III. . Средства технологического оснащения (Продолжение)/
В. Г. Шипинский. – Гомель: ГГТУ им. П.О. Сухого, 2013. 178 с.: ил.
Рассматриваются технологии, оборудование и оснастка, применяемые для упаковывания продукции в тубы и картонную тару, а также для транспортного пакетирования продукции, утилизации использованной упаковки и переработки во вторичное сырье. Содержатся основные конструктивные исполнения этого оборудования и применяемой оснастки, а также необходимые методики их проектировочных расчетов.
Книга предназначена для студентов высших учебных заведений, обучающихся по специальности «Упаковочное производство». Будет полезна для инженерно-технических работников, занимающихся упаковочным технологическим оборудованием, комплексной автоматизацией производственных процессов, технологиями и оснасткой тароупаковочного производства, созданием и производством самой упаковки, а также товарообращением.
УДК 621.798.06(075.8) ББК 30.61я73
Учреждение образования “Гомельский государственный технический университет имени П.О. Сухого”, 2013
2
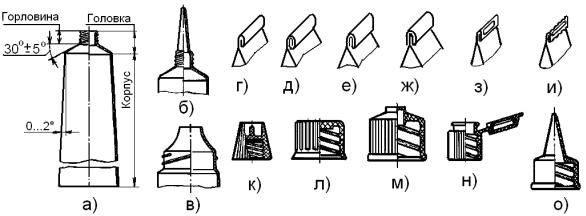
17.УПАКОВЫВАНИЕ В ТУБЫ
17.1.Конструктивные исполнения туб
Тубой называется разовая потребительская тара с корпусом, обеспечивающим выдавливание содержимого, с узкой горловиной укупориваемой бушоном (колпачком), и дном, закрываемым после наполнения продукцией.
В тубы упаковываются в большом ассортименте пастообразная пищевая, косметическая, и фармацевтическая продукция, товары бытовой химии, а также краски, смазочные материалы и многие другие товары. Пожалуй, не существует такого пастообразного продукта, который невозможно было бы упаковать в тубы для продажи потребителям. Причем тубы являются не только удобной и экономичной одноразовой потребительской тарой, но одновременно и самым простым дозировочным устройством. Ни в одном другом средстве упаковки пока не удалось совместить эти функции проще и эффективнее.
Туба (рис.17.1а) состоит из головки, узкая горловина которой переходит в плечо в форме усеченного конуса, и корпуса в виде тонкостенной трубки, один конец которой соединяется по периметру с плечом головки, а второй – открыт. Горловины туб выполняются с цилиндрической или конической наружной поверхностью, содержащей стандартную метрическую резьбу или резьбу с мелким шагом. Особенностью конической горловины является то, что колпачок (бушон) закручивается на нее вполоборота (рис.17.1в). Отверстие в горловине обычно имеет круглую форму. Однако чтобы придать выдавливаемому продукту другую форму выполняются и фигурные отверстия в виде овала, эллипса, щели, звездочки и т. д. Отверстие горловины, при необходимости, герметично закрывается тонкой мембраной приклеенной к ее торцу или выполненной при изготовлении тубы.
Рис.17.1. Исполнения туб и их конструктивных элементов
Тубы с фармацевтической и некоторой другой продукцией часто содержат на горловинах специальные конструктивные элементы, например, в виде удлиненного носика – канюли (рис.17.1б), шприца для инъекций, намазывателя, натирателя, массирующего и других функциональных приспособлений, повышающих эффективность использования содержимого.
Горловина головки тубы переходит в плечо, имеющее форму усеченного конуса с наклоном образующей в пределах от 25о до 35о. Плечо в свою очередь соединяется по периметру с концом тонкостенного корпуса. Корпус тубы
3
имеет цилиндрическую форму или образует расширяющуюся к низу под углом 1 – 2о коническую поверхность. Конические корпуса позволяют задвигать пустые тубы друг в друга, образуя из них стопы высотой около 750 мм. В результате этого при транспортировке и хранении пустых туб экономится занимаемое ими пространство, тубы лучше защищаются от загрязнений (пыли и других) и механических повреждений, а их поштучная выдача в тубонаполнительных автоматах осуществляется более компактными и простыми магазинными питателями.
Материал корпуса тубы должен обладать хорошими барьерными свойствами, быть инертным к упакованной продукции, обеспечивать требуемую прочность и герметичность корпуса, хорошо обрабатываться, надежно удерживать покрытия и декоративное полиграфическое оформление и, главное, легко деформироваться от малого усилия сжатия, создаваемого без значительного напряжения пальцами человека. Широко применяются тубы металлические, пластмассовые и изготовленные из комбинированных многослойных материалов (ламинатов) с объемом наполнения от 4 до 500 см3, с наружным диаметром корпуса в пределах от 10 до 60 мм и длиной в пределах от 35 до 300 мм.
Металлические тубы на начальном этапе применения изготовлялись из пластичных сплавов на основе олова и свинца. Первый же патент на металлические тубы, изготовляемые из олова, свинца или алюминия, был выдан в 1841 г Джону Ренду (США). Начиная с 1920-х годов и по настоящее время их изготовляют только из легкого, безвредного и дешевого высокопластичного алюминия технической чистоты, содержащего примесей не более 0,3%. Достоинства алюминиевых туб заключаются в прочном и герметичном цельноштампованном корпусе, идеальных барьерных характеристиках материала, эффективном процессе производства, а также в высокоэластичном корпусе, практически не имеющем остаточной упругости, приводящей к самопроизвольному восстановлению его формы после снятия сжимающего усилия. Этим в процессе длительного потребления упакованной продукции исключается попадание внутрь тубы воздуха через горловину и его взаимодействие с содержимым, а также обеспечивается использование продукта практически без остатка.
Пластмассовые тубы появились на рынке упаковки в 1980-х годах и к настоящему времени получили достаточно широкое распространение. Они дешевле алюминиевых, обладают исключительными возможностями для привлекательного декоративного оформления, их упругий корпус после сжатия всегда восстанавливает свою первоначальную форму, сохраняя тем самым на всем протяжении использования содержимого привлекательный внешний вид. Изготовляются пластмассовые тубы в основном из полиэтилена высокой и низкой плотности, а также из смеси этих материалов с толщиной стенки корпуса 0,4 – 0,5 мм. Полиэтилен хорошо окрашивается в массе и предоставляет широкие возможности для декоративного многокрасочного оформления туб сухим офсетным способом, тиснением фольгой, трафаретной печатью и другими методами. Для улучшения сцепления красочного слоя поверхность заготовок туб подвергается предварительной обработке электрическими коронными разрядами или пламенем газовой горелки. После
4
сушки печатных красок полиэтиленовые тубы покрываются бесцветным лаком, который защищает красочное оформление и делает поверхность блестящей и еще более привлекательной. Ввиду того, что полиэтилен не обладает высокой диффузионной плотностью, печатные краски и лаки, используемые для оформления таких туб, должны быть устойчивы не только к свету и другим факторам внешней среды, но и к содержимому туб. Применяются пластмассовые тубы в основном для упаковывания косметической продукции, не содержащей окислительных веществ и быстроулетучивающихся ароматических масел, а также для упаковывания смазочных материалов, дисперсных красок, пищевых продуктов, например, таких как повидло, сливки для кофе, ореховый и шоколадный кремы, глазури для пирожных и других паст. Дальнейшее совершенствование этого вида тары привело к созданию и широкому применению ламинатных туб.
Ламинатные тубы изготавливаются из гибких многослойных материалов, получаемых в результате соединения исходных материалов в многослойные ламинированием и кашированием. Изготавливают тубы из ламинатов, содержащих в основе как алюминиевую фольгу толщиной 20 – 40 мкм, так и специальную полимерную пленку с высокой диффузионной плотностью. Наиболее широко для этих целей применяются, например, пятислойные ламинаты толщиной 0,3 – 0,4 мм, у которых средний слой из алюминиевой фольги или специального полимера соединяется с наружными слоями из полиэтилена через промежуточные слои из соответствующего сополимера, например, такого, как нукрел, созданного фирмой «Du Pont». Нукрел – это кислотная сополимерная смола, применяемая в ламинатах в качестве связующего слоя благодаря отличной сцепляемости с фольгой, полиэтиленом и другими самыми разнообразными материалами, а также обеспечивающая экономическую выгодность такой упаковки. Ламинатные тубы сочетают в себе прочность, эластичность и высокую диффузионную плотность, присущую алюминиевым тубам, с привлекательным внешним видом и другими достоинствами пластмассовых туб.
На горловину головки туб вначале обычно навинчивают колпачки (бушоны), а затем их в тубонаполнительных автоматах заполняют продукцией через открытый конец корпуса, после чего он герметично закрывается плоским фальцевым или сварочным соединением. При закрытии металлической тубы конец ее корпуса сжимается в плоское положение, несколько раз перегибается, а затем обжимается губками фальцевального механизма. В зависимости от требуемой прочности применяют двойное (рис.17.1г), тройное (рис.17.1д), четверное (рис.17.1е) и седлообразное (рис.17.1ж) укупоривающее загибание концов тубы. После обжатия гладкого (рис.17.1з) или с рифлением (рис.17.1и) закрывающее тубу фальцевое соединение становится плотным, герметичным и стабильным. При обжатии или после обжатия фальцевого соединения на нем клеймом наносится маркировка, содержащая, например, такую информацию, как месяц и год изготовления продукта, номер партии и другие данные.
Пластмассовые и ламинатные тубы после наполнения закрывают сварочным соединительным швом. При закрытии конец наполненной тубы вначале нагревается до стадии размягчения материала, например, горячим воздухом, а затем сжимается холодными плоскими губками прессового
5
механизма. Материал при этом охлаждается и на конце тубы образуется герметичное сварное соединение шириной 6 – 8 мм. Одновременно на поверхности сварного шва, установленным в одной из губок клише, отпечатывается маркировка. Обычно пластмассовые (полиэтиленовые) тубы имеют на поверхности сварного шва рифления, а ламинатные тубы закрываются гладким сварным швом. Для придания таре эстетичного вида на заключительном этапе на тубах подрезается неровный край закрывающего сварного шва, и готовые упаковочные единицы выводятся из тубонаполнительного автомата.
Укупоривающие тубы колпачки (бушоны), содержат конструктивные элементы для закрепления их на горловине, закрытия и герметизации отверстия, облегчения откупоривания тары, декоративного оформления упаковки, а также способствующие полному и эффективному использованию содержимого. По внешней форме наиболее часто применяемые колпачки можно разделить на конические (рис.17.1к) и цилиндрические (рис.17.1л) с гладкой и рифленой боковой поверхностью, а также фигурные, имеющие более сложную конфигурацию (рис.17.1м, о). Закрепление колпачков на горловине туб обеспечивается, как правило, резьбовым соединением. Для этого применяется метрическая резьба, а также коническая и многозаходные резьбы, обеспечивающие быстрое закрепление колпачков за четверть и вполоборота. Для герметичного закрытия отверстия на горловине тубы, в колпачках сопрягающаяся с ним поверхность выполняется в виде плоского, сферического и конического уплотнителя или для этого на дно колпачка укладывается упругая (резиновая или полимерная) прокладка. Для укупоривания пластмассовых и ламинатных туб широко применяются колпачки по наружному диаметру равные диаметру корпуса тубы, так как в процессе эксплуатации их рекомендуется ставить на плоскую поверхность этого колпачка горловиной вниз. В таком положении содержимое тубы стекает в нижнюю часть корпуса, заполняет горловину и после снятия колпачка легко и полностью выдавливается из нее. Главным достоинством популярных колпачков (рис.17.1н), содержащих откидывающуюся на упругом шарнире крышку («Флип-Офф») является то, что они позволяют быстро открывать и закрывать тубу, не снимая с ее горловины колпачка. Тубы, отверстие в горловине которых герметично закрыто защитной мембраной, укупориваются, как правило, колпачками, оснащенными с наружной стороны штырем (рис.17.1к), обеспечивающим ее прокалывание при первом использовании содержимого. Выполняются также колпачки с прозрачным экраном (рис.17.1м), позволяющим визуально определить цвет содержимого тубы, а также носиками (рис.17.1о) и многими другими функциональными приспособлениями, способствующими более эффективному использованию содержимого. Для нанесения на выдавливаемую пасту цветных полос в горловину тубы встраивается специальная пластмассовая вставка (инсерт), представляющая собой полимерную трубку, внутри которой имеются продольные канавки, соединяющиеся наклонными отверстиями с полостью тубы в зоне сопряжения горловины с плечом. В процессе упаковывания продукции такая туба вначале заполняется цветной пастой до уровня нижнего торца трубки, а затем – основной пастой до полного объема и закрывается. При
6
выдавливании же из нее содержимого основная паста поступает в горловину по осевому отверстию трубки, а цветная паста подается при этом в трубку через наклонные боковые отверстия и наносится в канавках продольными цветными полосами на поверхность основной пасты, придавая ей привлекательный внешний вид.
К новым разновидностям относятся сдвоенные тубы, у которых внутри одной размещена вторая туба с меньшими размерами. Они оснащаются сложными дозаторами или смесителями, встраиваемыми в горловину, и применяются для упаковывания продукции, два компонента которой должны храниться отдельно и смешиваться только в процессе применения, например, красителей для волос. Созданы также полутубы – это упаковка, в которой конструктивные элементы тубы сочетаются с флаконом. За рубежом их называют «tottle» (от английских слов «tube» (туба) и bottle (флакон)). Их солидный внешний вид, а также оригинальность в сочетании с функциональной универсальностью позволяют использовать эту упаковку с одинаковым успехом для средств по уходу за волосами и телом, для солнцезащитной косметики и т. д. Каждый же новый этап в развитии тубы улучшает как ее внешний вид, так и функциональные характеристики. Так, например, закрывающий шов и подрезка конца тубы может выполняться овальной или волнообразной, на нем может содержаться отверстие для подвешивания тубы или закрепления в нем различных функциональных или декоративных элементов, а в ее укупоривающий колпачок может встраиваться жидкокристаллический экран с таймером и т. д. Европейские фирмы уже предлагают тубы кубической формы, и с рифленым корпусом. Еще одна новинка – туба с прозрачной полоской во всю длину корпуса, позволяющей следить за расходованием содержимого.
17.2. Изготовление металлических туб
Для изготовления металлических туб используются полосы или листы из алюминия марки АД00 толщиной 4 – 5 мм. Маршрутный же технологический процесс изготовления металлических туб включает в себя следующие операции:
1.Вырубка круглых или шестигранных заготовок на пресс-автомате из полос или листов алюминия.
2.Галтовка заготовок во вращающемся галтовочном барабане для снятия с них заусенцев.
3.Отжиг заготовок в электропечи при температуре 520 – 560 оС в течение 90
–120 минут, для снятия наклепа и повышения пластичности материала.
4.Мойка заготовок в ванне с 2-процентным водным раствором
кальцинированной соды, с последующим их ополаскиванием в ванне с чистой водой и высушиванием при температуре около 100 оС в сушильной камере.
5.Зажиривание заготовок гидрированным кашалотовым жиром (или заменяющими смазками) в пропорции 1 г жира на 1 кг заготовок в галтовочном барабане, для облегчения последующего процесса выдавливания туб.
6.Формование из заготовок холодным выдавливанием (экстрюдингом) бесшовных туб с толщиной стенок корпуса около 0,1 мм на пресс-автомате с усилием 2,5 МН.
7
7.Подрезка корпуса тубы на заданную длину, торцовка горловины и накатка на ней резьбы на специальном автомате.
8.Отжиг туб в проходной печи для снятия наклепа, повышения пластичности материала и удаления жировой технологической смазки путем ее выжигания.
9.Лакирование внутренней поверхности тубы 2 – 3-х кратным напылением на нее лака с частичной промежуточной и полной окончательной сушкой покрытия в поточной сушилке.
10.Внешнее художественно-декоративное оформление тубы, включающее окраску поверхности обкатывающимся роликом, нанесение печатного полиграфического изображения, лакирование и сушку.
11.Промазка внутренней хвостовой поверхности корпуса водно-аммиачной пастой с последующим ее высушиванием, для обеспечения герметизации закрывающего тубу плоского фальцевого соединения.
12.Навинчивание колпачка на горловину тубы в соответствующем автомате.
13.Растяжка корпуса тубы на 1 – 2о в конусообразную форму на специальном конусообразующем автомате и автоматическая укладка их в стопы длиной около 750 мм путем задвигания друг в друга; корпуса при этом упрочняются и укорачиваются по длине на 3 – 5 мм.
14.Укладка туб стопами в транспортную или технологическую тару и доставка на тубонаполнительные автоматы.
Из приведенного технологического процесса следует, что для изготовления металлических туб требуются производственные мощности, содержащие большую номенклатуру различных средств технологического оснащения, которые включают в себя как универсальное оборудование, используемое многими промышленными предприятиями, так и специализированное, то есть применяемое только в производстве металлических туб. Из первой группы применяются:
кривошипные ножницы, обеспечивающие резку листового материала на полосы;
пресс-автомат, штампующий из полосового материала круглые или шестигранные заготовки;
галтовочные барабаны, в которых производится снятие с заготовок заусенцев и их зажиривание соответствующими смазками;
электропечь отжига заготовок при температуре 520 – 560 оС для снятия наклепа и повышения пластичности материала;
двухванновая моечная установка, в первой ванне которой заготовки после отжига очищаются в 2-процентном водном растворе кальцинированной соды, а затем в ее второй ванне ополаскиваются чистой водой;
установка конвективной сушки заготовок после мойки при температуре около 100 оС;
транспортирующие устройства и механизмы, обеспечивающие доставку объектов обработки к технологическому оборудованию, располагающемуся в последовательности выполняемых операций технологического процесса;
Кспециализированному же относится следующее технологическое оборудование:
8
пресс гидравлический усилием 2,5 МН для холодного выдавливания из заготовок бесшовных туб с толщиной стенок корпуса около 0,1 мм (производительность – 50 туб в минуту; диаметр формуемых туб – от 11 до 25 мм, длина – до 150 мм; мощность привода – 4 кВт; с автоматической загрузкой заготовок и удалением туб);
автомат модели YGR12, осуществляющий торцовку горловины тубы и накатку на ней резьбы, а также подрезку корпуса на заданную длину (производительность – 60 туб в минуту; диаметр обрабатываемых туб – от 13 до 38 мм; мощность привода – 2,2 кВт);
печь отжига трехвалковая модели YGR13D, обеспечивающая снятие наклепа, повышение пластичности материала и удаление жировой технологической смазки с туб путем ее выжигания (производительность – 90
туб в минуту; диаметр обрабатываемых туб – от 13 до 38 мм; максимальная температура – 550 оС; потребляемая мощность: приводом – 2,2 кВт, нагревательными элементами – 48 кВт);
автомат модели WP603, лакирующий внутреннюю поверхность туб 2 – 3-
хкратным напылением на нее лака с частичной промежуточной сушкой (производительность – 60 туб в минуту; диаметр обрабатываемых туб – от 13 до 38 мм, длина – до 200 мм; мощность привода – 3 кВт);
автомат, наносящий на внутреннюю хвостовую поверхность корпуса тубы водно-аммиачную пасту, для обеспечения герметизации закрывающего ее плоского фальцевого соединения;
вулканизационная печь модели YGR23D, обеспечивающая окончательную сушку внутреннего лакового покрытия туб с герметизирующей прокладкой (производительность – 120 туб в минуту; диаметр обрабатываемых
туб: 13 – 30 мм и 22 – 38 мм, длина – до 220 мм; максимальная температура – 400 оС; потребляемая мощность: приводом – 1,1 кВт, нагревательными элементами – 52 кВт);
печатная машина модели ZD07B, осуществляющая грунтование наружной поверхности туб (производительность – 60 туб в минуту; диаметр обрабатываемых туб – от 16 до 35 мм; мощность привода – 3 кВт);
четырехцветная печатная машина модели ZY08 планетарного типа, осуществляющая внешнее художественно-декоративное оформление корпуса туб (производительность – 60 туб в минуту; диаметр обрабатываемых туб – от 16 до 35 мм; мощность привода – 5,5 кВт); работает в едином комплексе с печатной машиной модели ZD07B;
автомат модели YGR17, навинчивающий колпачки (бушоны) на горловины туб (производительность – 60 туб в минуту; диаметр обрабатываемых туб – от 13 до 38 мм, длина – до 120 мм; диаметр колпачков – от 12 до 16 мм, высота – от 10 до 18 мм; мощность привода – 1,1 кВт);
автомат, обеспечивающий растяжку корпуса тубы на 1 – 2о в конусообразную форму и их укладку в стопы длиной около 750 мм путем задвигания друг в друга;
оснастка для приведенного технологического оборудования на все типоразмеры изготовляемых туб.
9
Таким образом, для организации производства металлических туб необходимо не менее 16-ти единиц приведенного технологического оборудования и оснастка к нему на все типоразмеры изготовляемых туб, а также транспортирующие устройства и механизмы, обеспечивающие доставку объектов обработки к технологическому оборудованию, располагающемуся на производственных площадях в последовательности выполняемых операций технологического процесса.
17.3. Изготовление пластмассовых и ламинатных туб
Пластмассовые тубы изготавливаются бесшовными, например, экструзией с раздувкой, и собранными из отдельно изготовленных составных частей (сборными). В сборных тубах присоединение корпуса к головке может осуществляться как в процессе непосредственного изготовления головки, например, методами литья под давлением или термоформования, так и на последующей сварочной операции.
Производство бесшовных пластмассовых туб характеризуется низкой производительностью, и они из-за этого применяются относительно редко. В тоже время постоянно и устойчиво увеличиваются объемы производства на высокопроизводительном автоматическом оборудовании пластмассовых и особенно ламинатных сборных туб. Головки для этих туб изготавливают в основном из полиэтилена методами литья под давлением и термоформования в многоместных формах. Корпуса сборных туб бывают бесшовными и с продольным сварным швом. Бесшовные цилиндрические корпуса получают путем разрезки на куски требуемой длины соответствующей пластмассовой бесшовной длинномерной трубки, изготовленной методом экструзии. При этом декоративное многокрасочное оформление полученных заготовок выполняется на последующих операциях производственного процесса. Корпуса с продольным сварным швом изготовляют из предварительно декорированного ленточного материала свернутого в рулон. В процессе изготовления корпусов эта лента разматывается с рулона и сворачивается в трубку с точным совмещением и сваркой внахлестку ее краев. Затем полученная трубка разрезается на заготовки заданной длины. Точная отрезка обеспечивается фотоэлементом, воспринимающим специальные метки на декорированной поверхности ленты. Полученная из ленты трубка перед разрезкой на мерные заготовки может дополнительно покрываться внешним слоем полиэтилена путем переэкструзии. При этом повышается прочность корпуса, и продольный сварочный шов на поверхности трубки становится едва заметным. Бесшовные цилиндрические корпуса изготовляются в основном из однородной пластмассы, в то время как корпуса с продольным сварным швом делаются обычно из многослойных рулонных материалов (ламинатов). Ламинатные корпуса с дополнительным внешним полиэтиленовым покрытием стоят дороже обычных и поэтому применяются только для особой продукции.
Герметичное соединение корпуса с плечом головки в сборных тубах выполняется обычно сваркой. В ламинатных тубах на головку в области плеча дополнительно приваривают штампованные из того же ламината внешние или внутренние кольцевые вставки (рондели), повышающие диффузионную плотность тубы в этой зоне. Для образования сварных соединений может
10