
- •Общие сведения
- •Основы конструирования редукторов
- •1. Этапы компоновки зубчатых и червячных редукторов.
- •Последовательность конструирования механических передач.
- •1.1 Первый этап эскизной компоновки редуктора
- •Расстояние между деталями
- •1.2.Второй этап эскизной компоновки редукторов
- •1.2.1. Проектный расчет валов
- •1.2.2.Выбор типа подшипников.
- •2. Конструирование узлов редуктора
- •2.1. Конструирование валов
- •2.1.1. Цилиндрические редукторы
- •2.1.2. Конические редукторы
- •2.1.3.Червячные редукторы
- •2.2.Конструирование корпусов
- •2.3.Конструирование элементов корпус
- •2.3.2.Фланцы крепление крышки редуктора к корпусу.
- •2.3.3.Установочные штифты (рис.2.28).
- •2.3.4.Фланецы для крышки смотрового окна (рис.2.30).
- •2.4.Смазывание, смазочные устройства и уплотнения
- •2.4.1.Смазывание зубчатого (червячного) зацепления.
- •2.4.2. Смазывание подшипников
- •2.4.3. Уплотнительные устройства
- •2.4.4. Регулировка подшипников
- •2.4.5. Монтаж и демонтаж подшипников.
- •3. Рабочие чертежи деталей
- •Общие сведения
- •3.1. Рабочий чертеж вала
- •3.2.Рабочие чертежи зубчатых и червячных колес.
- •3.4.Рабочие чертежи шкивов и звездочек.
- •4. Оформление сборочных чертежей и деталей редуктора
- •4.1. Шероховатость поверхностей.
- •4.2. Допуски и посадки деталей передач
- •4.3. Пример определения допусков формы и расположения посадочных поверхностей
- •4.4. Требования к оформлению чертежа.
- •Заключение
- •Библиографический список
- •Приложения
- •Приложение 2 Сборочные чертежи редукторов
- •Приложение 3 Рабочие чертежи деталей

|
До 3 |
Св. 3 до |
Св.6 до |
|
Св. 30 до |
Св.120 до |
Св. 315 |
|
|
|
6 |
30 |
|
120 |
315 |
|
до 1000 |
|
|
|
|
|
|
|
|
|
Точный t1 |
0,1 |
0,1 |
0,2 |
|
0,3 |
0,4 |
|
0,5 |
Средний t2 |
0,2 |
0,2 |
0,4 |
|
0,6 |
1,0 |
|
1,6 |
Грубый t3 |
0,3 |
0,4 |
1,0 |
|
1,6 |
2,4 |
|
4,0 |
Очень грубый t4 |
0,3 |
1,0 |
2,0 |
|
3,0 |
4,0 |
|
6,0 |
Рабочий чертеж вала приведен в |
приложении 3 |
(рис.П3.1 и |
||||||
рис.П3.2) |
|
|
|
|
|
|
|
|
3.2.Рабочие чертежи зубчатых и червячных колес.
Оформление рабочих чертежей зубчатых и червячных колес имеет ряд особенностей Помимо графического изображения, выполняемого как правило, в одной проекции с дополнительным видом на посадочное отверстие, чертежи обязательно сопровождаются данными, необходимыми для нарезки зубьев и их контроля, в виде таблицы и техническими требованиями к точности заготовки. Положение таблицы параметров на поле чертежа строго определено стандартом, (рис.3.3). В верхнем правом углу чертежа, отступив от верхней обрамляющей линии на 20 мм проводят верхнюю линию таблицы. Правая линия таблицы совпадает с обрамляющей линией чертежа.
Рис.3.3 |
Рис.3.4 |
При обработке венца зубчатого колеса в собранном виде сведения, необходимые для его изготовления и контроля, помещают на сборочном чертеже.
67
–в первой части таблицы (рис.3.3) вносятся параметры для изготовления зубчатого венца (модуль т. число зубьев z, угол наклона β, направление зуба – правое, левое, шевронное, нормальный исходный контур со ссылкой на ГОСТ 13755 – 81, коэффициент смещения х, степень точности, вид сопряжения и обозначение стандарта норм точности – ГОСТ 1643 – 81;
–во второй части таблицы одну-две строки оставляют свободной;
в третьей части таблицы приводят делительный диаметр d и обозначение чертежа сопряженного колеса.
Если зубчатое колесо имеет два или более венца одного вида (например, цилиндрические), то значения параметров указывают в таблице в отдельных графах (колонках) для каждого венца (рис.3.4) Венец и соответствующие колонки обозначают одной прописной буквой русского алфавита.
Для венцов разного вида (например, цилиндрической и конической) приводят отдельные таблицы, которые располагают рядом или одна под другой. Каждый венец и таблицу в этом случае обозначают одной прописной буквой русского алфавита.
Цилиндрические колеса. Нормализованные или улучшенные колеса при твердости 350 НВ обычно имеют конструкцию, показанную на рис.3.5. Заготовка – штампованная или поковка. Тихоходные колеса обычно не балансируют, форма их заготовки сохраняется (рис.3.5,а). Быстроходные колеса обтачивают кругом, что позволяет обходиться без специальной балансировки (рис.3.5,б).
При высокой твердости 350 НВ зубьев конструкция колес должна быть жесткой. Колеса изготавливают из штамповочной или кованой заготовки.
68

Рис.3.5. Цилиндрические колеса
Основные размеры колес вычисляют по следующим формулам:
диаметр ступицы колеса |
dСТ (1,6 1,7)dв ; |
длина ступицы |
lСТ (0,8 1,5) dв; |
толщина обода |
0 (2,5 3,0) m; |
толщина диска |
C (0,2 0,3) b; |
штамповочный радиус |
R (2 4) mn ; |
где dв диаметр посадочного отверстия колеса b ширина колеса
m модуль зацепления
В чертежах колес, обточенных кругом, галтелей указывать не следует.
69

Конструкция шевронного колеса (рис.3.6) с твердостью 350 НВ
предусматривает для выхода зуборезной фрезы |
канавку а, |
|||||||||
определяемую в зависимости от mn: |
|
|
|
|
|
|||||
mn |
2 |
2,5 |
3 |
3,5 |
4 |
5 |
6 |
7 |
8 |
10 |
а |
32 |
37 |
42 |
47 |
52 |
58 |
67 |
75 |
82 |
100 |
Основные размеры вычисляют по выше приведенным формулам, но толщина диска С должна быть не менее b/3.
Рис.3.6. Шевронное цилиндрическое колесо
Размеры и предельные отклонения колес показаны на рис.3.7:
Ц (Г) – цепочный (габаритный размер); b – ширина зубчатого венца, S –
толщина диска, полученная в заготовительной операции (штамповке); С
– размер, связывающий систему размеров для заготовительной и механической операции (между обработанной и необработанной поверхностями детали).
70

Рис.3.7. Зубчатые колеса
Кроме того, на чертежах зубчатых колес кроме прочих размеров указывают диаметры: da – вершин зубьев, d – отверстия, dст - ступицы. На чертеже колеса с цилиндрическим отверстием и шпоночным пазом задают размер d + t2 (рис.3.8 а), где t2 определяют по размерам шпоночного паза из таблиц П1.1 приложения 1. На рис.3.8,б показан вал конической формы. На ширину шпоночного паза чаще всего задают поле допуска JS9.
Рис.3.8. Посадочные отверстия в ступицах колес
Допуски формы и допуски расположения поверхностей.
Назначение каждого из допусков (рис.3.9):
допуск цилиндричности посадочной поверхности (поз.1) назначают, чтобы ограничить концентрацию контактных давлений;
71

допуск перпендикулярности торца ступицы (поз.2) задают чтобы создать точную базу для подшипника качения, уменьшить перекос его колец и искажение геометрической формы дорожки качения внутреннего кольца;
допуск параллельности торцов ступицы узких колец (поз.3) задают по тем же соображениям, как и допуск перпендикулярности торца ступицы (поз.2). Если у колес нет выточки и, следовательно, нет размера dст, допуск параллельности относят к условному диаметру d1 = (1.5…2) d. На рис.3.9,а-г показаны несколько зубчатых колес и условные обозначения баз и допусков формы и расположения поверхностей. В табл.3.8 даны указания по определению допусков.
Рис.3.9.Допуски формы и поверхностей
Если торцы ступиц не участвуют в базировании подшипников, то допуски по поз.2 и 3 не назначают.
Таблица на изготовление и контроль зубчатых колес заполняется в такой последовательности:
|
|
Таблица 3.8 |
|
|
Допуски на размеры цилиндрического колеса |
||
|
|
|
|
Позиция |
|
Допуск |
|
на рис.3.9 |
|
|
|
1 |
Т 0,5 t, где t – допуск размера поверхности |
|
|
2 |
Т на диаметре dст при |
l/d 0,7 по табл.3.5. Степень точности |
|
допуска при базировании подшипников: шариковых – 8, роликовых |
|
||
|
– 7. |
|
|
3 |
Т на диаметре dст при l/d 0,7по табл.3.5. Степень точности допуска |
|
|
при базировании подшипников: шариковых – 7, роликовых – 6. |
|
||
4 |
Т 0,5 tцил; Т 2 tцил где |
tцил – допуск ширины шпоночного паза, |
|
|
табл.3.9 |
|
|
72

Таблица 3.9
Допуски на размеры
Интервал |
|
|
|
|
|
|
|
Квалитет |
|
|
|
|
|
||
размеров, |
3 |
4 |
5 |
6 |
7 |
8 |
9 |
10 |
11 |
12 |
13 |
14 |
15 |
16 |
17 |
мм |
|
|
|
|
|
|
|
|
|
|
|
|
|
|
|
Св.3 до 6 |
2,5 |
4 |
5 |
8 |
12 |
18 |
30 |
48 |
75 |
120 |
180 |
300 |
480 |
750 |
1200 |
« 6 « 10 |
2,5 |
4 |
6 |
9 |
15 |
22 |
36 |
58 |
90 |
150 |
220 |
360 |
580 |
900 |
1500 |
«10 « 18 |
3 |
5 |
8 |
11 |
18 |
27 |
43 |
70 |
110 |
180 |
270 |
430 |
700 |
1100 |
1800 |
«18 « 30 |
4 |
6 |
9 |
13 |
21 |
33 |
52 |
84 |
130 |
210 |
330 |
520 |
840 |
1300 |
2100 |
«30 « 50 |
4 |
7 |
11 |
16 |
25 |
39 |
62 |
100 |
160 |
250 |
390 |
620 |
1000 |
1600 |
2500 |
« 50 « 80 |
5 |
8 |
13 |
19 |
30 |
46 |
74 |
120 |
190 |
300 |
460 |
740 |
1200 |
1900 |
3000 |
«80 « 120 |
6 |
10 |
15 |
22 |
35 |
54 |
87 |
140 |
220 |
350 |
540 |
870 |
1400 |
2200 |
3500 |
«120 «180 |
8 |
12 |
18 |
25 |
40 |
63 |
100 |
160 |
250 |
400 |
630 |
1000 |
1600 |
2500 |
4000 |
«180 «250 |
10 |
14 |
20 |
29 |
46 |
72 |
115 |
185 |
290 |
460 |
720 |
1150 |
1850 |
2900 |
4600 |
«250 «315 |
12 |
16 |
23 |
32 |
52 |
81 |
130 |
210 |
320 |
520 |
810 |
1300 |
2100 |
3200 |
5200 |
«315 «400 |
13 |
18 |
25 |
36 |
57 |
89 |
140 |
230 |
360 |
570 |
890 |
1400 |
2300 |
3600 |
5700 |
«400 «500 |
15 |
20 |
27 |
40 |
63 |
97 |
155 |
250 |
400 |
630 |
970 |
1550 |
2500 |
4000 |
6300 |
В приложении 3 (рис.П3.36 П3.5) дан рабочий чертеж цилиндрических колес.
Конические колеса. Геометрические параметры конических колес определяют по ГОСТ 19624 – 74 для прямозубых конических колес и по ГОСТ 19326 – 73 для колес с круговыми зубьями. При проектном расчете конической зубчатой пары определяют основные параметры колес: числа зубьев колес, внешний окружной модуль и т. д.
Размеры и предельные отклонения.
Конструктивные формы конических колес с внешним диаметром dае 120 мм показаны рис.3.10 Такие колеса выполняют в основном при крупносерийном производстве.
Рис.3.10. Конические колеса
73
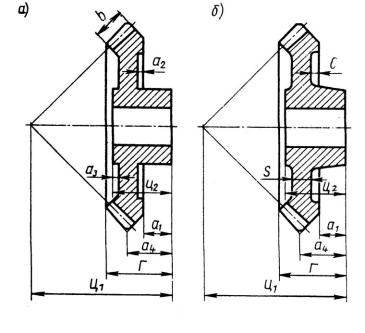
Широкое применение имеют конические колеса с круговыми зубьями, которые нарезают резцовыми головками, закрепляя заготовку на оправке. При этом необходимо предусмотреть свободный выход инструмента размер а 0,5 mte, где mte внешний окружной модуль.
На рис.3.11 показаны основные размеры, которые проставляют на чертеже конического колеса.
Рис.3.11. Размеры конических колес
Ц1 цепочный размер, определяющий положение вершины делительного конуса колеса;
Ц2 цепочный, определяющий величину осевого зазора в комплекте вала с подшипниками;
b ширина зубчатого венца; а1 размер, координирующий положение венца относительно ступицы; а2, а3 размеры углублений; Г габаритный размер;
Простановка размеров также зависит от способа получения заготовки колеса. Например, для штампованного колеса ставят осевые размеры по рис. 3.11,б. В отличие от предыдущего указывают размер S, полученный на заготовительной операции, а вместо а2 связующий размер С.
На чертежах конических зубчатых колес кроме размеров, определяющих форму и габариты детали, приводят размеры венца (рис.3.12)., которые определяются расчетом конической передачи.
74

Рис.3.12. Венцы конических колес
Звездочкой обозначены размеры для справок.
Допуски формы и допуски расположения поверхностей конических колес определяют так же, как и для цилиндрических (см. рис.3.9, табл.3.8)
Заполнение таблицы на изготовление и контроль см. в приложении
3 (рис.П3.4)
Червячные колеса. Червячные колеса чаще изготавливают составными: центр из серого чугуна или стали, зубчатый венец из бронзы. Основные геометрические размеры червячного колеса определяют расчетом. Соединение венца с центром должно обеспечивать передачу большого вращающего момента и сравнительно небольшой осевой силы.
Конструкция червячного колеса и способ соединения венца с центром зависит от объема выпуска. Например, при единичном и мелкосерийном производстве, когда годовой объем выпуска менее 50 шт., и небольших размерах колес (dам2 300 мм) зубчатые венцы соединяют с центром посадкой с натягом. Конструкции червячных колес представлены на рис.3.13.Толщина обода δ ≈ 2 m +0,05 b2; δ1 ≈ 1,25 δ; Ширина колеса b = b2 принимается из расчета передачи. Размеры ступицы принимают также как для цилиндрических коле
75

Рис.3.13. Червячные колеса
Конструирование основных элементов червячного колеса выполняют также как и для цилиндрических колес. Другие конструкции колес приведены в литературе 4
Заполнение таблицы и рабочий чертеж червячного колеса приведены в приложении 3 (рис.П3.6)
3.3. Рабочие чертежи стаканов и крышек подшипниковых
узлов
Стаканы применяются для самостоятельного сборочного комплекта с фиксирующими опорами (рис. 3.14). Наиболее часто стаканы используют в конических передачах, где требуется точная установка и регулирование относительного положения зубчатых колес. Кроме того, установка стаканов необходима в подшипниковых узлах быстроходных валов червячных редукторов и цилиндрических вертикальных редукторов с неразъемным корпусом в случае, если диаметр выступов червяка или шестерни окажется больше диаметра наружного кольца подшипника da1 D. Стаканы изготавливают обычно из чугуна СЧ15-32, реже из стали.
Толщину стенок с литых стаканов из чугуна марки СЧ15-32 выбирают в зависимости от диаметра наружного кольца подшипника D в соответствии с данными, приведенными ниже:
D |
< 50 |
50-62 |
63–95 |
100 -145 |
150-220 |
, мм |
4…5 |
5…7 |
7…9 |
9 …11 |
11…13 |
d, мм |
6 |
6 |
8 |
10 |
12 |
z |
4 |
4 |
4 |
6 |
6 |
|
|
|
76 |
|
|

Наружный диаметр стакана Dа D + 2 округляют до ближайшего стандартного числа по ГОСТ 6636–69 из ряда Rz 40. Толщину упорного буртика 1 принимают равной толщине стенок, толщину фланца 2 ≈
1,2
Высоту t упорного буртика назначают в соответствии с размером подшипника качения. Если осевая сила направлена в сторону, противоположную бурту, то можно использовать более технологичную конструкцию стакана с пружинным кольцом, заменяющим бурт.
Диаметр d и количество винтов z для крепления стаканов принимают в зависимости от диаметра стакана или крышки. Диаметр фланца выполняют минимальным (рис.3.14)
Dф Dа 4,2 4., 4 d,
где d – диаметр винта.
а |
|
б |
|
|
|
|
|
|
|
|
в |
|
|
г |
|
|
|
Рис. 3.14. Конструкция стаканов |
||||
|
Для снижения массы |
корпуса допускается свисание стакана |
||||
b |
(1,5–2,0) . Проточка, |
выполненная на наружной поверхности |
стакана, облегчает сборку и уменьшает длину шлифуемой поверхности. Если стакан в процессе сборки неоднократно перемещают вдоль оси отверстия, то предусматривают посадку H7h6 или H7j6. Более
77

надежной является посадка H7k6, которая может быть применена в том случае, если регулирование осевого положения стакана не требуется.
На чертежах стаканов (рис.3.15, а, б) задают осевые линейные размеры: габаритные, цепочные и свободные. Предельные отклонения задают на размеры: свободные среднего класса точности; цепочные по общему правилу (см. выше).
Допуски формы и допуски расположения поверхностей приведены в табл. 2.2.
Таблица 3.10
Позиция |
Допуск |
|
на рис. 3.15 |
|
|
|
|
|
1 |
Т 0,5t, где t – допуск размера поверхности |
|
2 |
Т 0,6 t, где t – допуск размера поверхности |
|
3 |
Т по табл. 3.2 в зависимости от типа подшипника |
|
|
||
4 |
Т – на диаметре D по табл. 3.5. Степень точности допуска для |
|
|
||
|
подшипников: шариковых – 8, роликовых – 7 |
|
5 |
Т на диаметре Dф по табл. 3.5.Степень точности допуска для |
|
|
||
6 |
подшипников качения: шариковых – 8, роликовых – 7 |
|
Т 0,4(dотв – dв), где dотв – диаметр отверстия, dв – диаметр |
||
|
||
|
винта |
|
|
|
Рис. 3.15.Примеры чертежей стаканов
78
Основной базой является поверхность С фланцев стакана. Точность положения базовых торцов стакана для упора подшипников обеспечивает их параллельность торцу С стакана.
Назначение каждого из допусков (рис. 3.15):
допуск цилиндричности (поз. 1) задают, чтобы ограничить отклонение геометрической формы посадочных поверхностей и связанных с ними дорожек качения наружных колец подшипников;
допуск соосности посадочных поверхностей стакана назначают, чтобы ограничить отклонение межосевого расстояния в конической передаче (поз. 2) и перекос колец подшипников качения (поз. 3);
допуск перпендикулярности (поз. 4) и допуск параллельности (поз. 5) задают, чтобы ограничить перекос колец подшипников;
позиционный допуск (поз. 6) задают, чтобы ограничить отклонение в расположении центров крепежных отверстий и обеспечить так называемую «собираемость» резьбового соединения. Этот допуск задают только в том случае, когда отверстия для винтов в стакане и в корпусной детали сверлят независимо друг от друга в приспособлениях или на станках с ЧПУ. В остальных случаях позиционный допуск не приводят.
Пример рабочего чертежа стакана приведен в приложении. 3 (рис.П3.8).
Крышки подшипниковых узлов. Привертные крышки применяются в неразъемных корпусах для подшипниковых узлов, а также в редукторах с разъемными корпусами. Крышки подшипников изготовляют из чугуна марок СЧ15, СЧ20. Конструкции привертных крышек приведены на рис. 3.16. Они могут быть глухими рис. 3.16, а, б, г и с отверстием под выходной вал (рис. 3.16, в). Выбор конструкции крышки зависит:
-от уплотнения выходных валов (см. уплотнения валов);
-крепления подшипников на валу (если вал не выходит за пределы подшипника, то крышку выполняют с плоской внешней поверхностью
(рис. 3.16, а, б)
-если торец вала выступает за пределы подшипника, то крышку выполняют по рис.3.16, г);
-регулировки зазора подшипника, которая производится установкой набора прокладок под фланец крышки (см. рис. 3.16) или воздействием винтами с резьбовыми крышками (см. рис.2.43);
-размещения комплекта деталей подшипникового узла.
При размещении комплекта в корпусе редуктора крышка выбирается по диаметру наружного кольца подшипника D, если комплект деталей собирается в стакане, то размеры крышки определяют по его наружному диаметру.
79

Ниже приведены рекомендации по выбору толщины стенки, диаметра d и числа z винтов крепления крышки к корпусу в зависимости от наружного диаметра подшипник D:
D |
50…62 |
63…95 |
100…145 |
150…220 |
|
5 |
6 |
7 |
8 |
d |
6 |
8 |
10 |
12 |
z |
4 |
4 |
6 |
6 |
|
|
б |
|
в |
|
г |
а |
|
|||||
|
|
|
|
|
|
|
|
|
|
|
|
|
|
|
Рис. 3.16. Крышки подшипниковых узлов |
|
||||
|
|
В варианте по рис. 3.16, б крышку крепят винтами с цилиндрическими головками и шестигранным углублением под ключ. В этом случае толщину крышки принимают
3 = Н + 0,8 ,
где Н – высота головки винта.
Опорные поверхности под головки крепежных болтов или гаек чаще всего необходимо обрабатывать. Обрабатывают или непосредственно те места, на которые опираются головки винтов (рис. 3.16, а, б), или весь поясок на торце в зоне расположения головок винтов
(рис. 3.16, в, г). Размеры других конструктивных элементов крышки: 1 = 1,2 ; 2 = (0,9–1) ; Dф = D + (4… 4,4) d; С d.
Закладные крышки. На рис. 3.17 показаны основные конструкции закладных крышек: глухих – рис. 3.17, а, б; с отверстием для выходного конца вала рис.3.17,в; с резьбовым отверстием под нажимной винт – рис. 3.17,г. Закладные крышки широко применяют в редукторах, имеющих плоскость разъема по осям валов. Эти крышки не требуют крепление к корпусу резьбовыми деталями: их удерживает кольцевой выступ, для которого в корпусе протачивают канавку. Чтобы обеспечивать сопряжения торцов выступа крышки и канавки корпуса по плоскости, на наружной цилиндрической поверхности крышки перед
80

торцом выступа желательно выполнять канавку шириной b. Размер
канавки на диаметре вала d принимают: |
|
||
d |
10…50 |
50…100 |
≥ 100 |
b |
3 |
5 |
8 |
Наружный диаметр крышки выполняют с такими отклонениями, при которых в сопряжении с корпусом образуется малый зазор, препятствующий вытеканию масла из корпуса. Толщину стенки принимают в зависимости от диаметра D отверстия под подшипник (см. выше). Размеры других элементов крышки: 1 = (0,9–1) ; S = (0,9–1) ; С0,5S; l b.
Рис. 3.17.Закладные крышки подшипниковых гнезд
На чертежах крышек подшипников осевые размеры проставляют по рис.3.18. Во всех конструкциях размер S получен при отливке крышки на заготовительной операции. Размер h обычно входит составляющим размером размерной цепи, определяющей осевой зазор в комплекте вала с подшипниками качения. Размер Н везде габаритный.
81

Размер С связывает необработанные и обработанные поверхности, С0 – глубина гнезда для манжетного уплотнения.
Рис. 3.18.Предельные отклонения размеров
Рис. 3.19. Допуски расположения поверхностей
82