
техника транспорта обслуживание и ремонт
.pdf
Мкр=Ртrк ;
изгибающий момент от тяговой силы Рт
Мрт=Ртb ;
изгибающий момент от нормальной реакции дороги Rz
Mz=Rzb ;
изгибающий момент от поперечной реакции дороги Ry
My=Ryrк ;
где b – плечо изгиба; rк – радиус ведущего колеса.
Изгибающий момент Мрт действует в горизонтальной плоскости, а изгибающие моменты Мz и My – в вертикальной плоскости.
При прямолинейном движении автомобиля результирующий изгибающий момент в вертикальной и горизонтальной плоскостях
Мизг=b
R |
2 |
|
z |
||
|
P2 т
.
Сложные напряжения от изгиба и скручивания
ζΣ=
М |
2 |
М |
2 |
|
R |
2 |
b |
2 |
P |
b |
2 |
Р |
2 |
r |
2 |
||
изг |
кр |
|
|||||||||||||||
|
|
|
|
|
|
|
z |
|
|
т |
|
|
|
|
т к |
||
|
|
|
|
|
|
|
|
|
|
|
|
|
|||||
|
0,1d |
3 |
|
|
|
|
|
|
0,1d |
3 |
|
|
|
|
|
||
|
|
|
|
|
|
|
|
|
|
|
|
|
|
,
где d – диаметр полуоси в опасном сечении;
Рт=Rzθx ; θх=0,8 – коэффициент продольного сцепления.
Расчѐт разгруженной полуоси на прочность выполняется только для случая прямолинейного движения автомобиля. При этом полуось рассчитывается на кручение и жѐсткость. Крутящий момент, передаваемый разгруженной полуосью
равен: Мкр=Ртrк . Напряжения кручения
ηкр= Рт rк3 .
0,2d
7.11.Рулевое управление
Крулевому управлению предъявляются специальные требования, в соответствии с которыми рулевое управление должно обеспечивать:
- минимальный радиус поворота для высокого маневренного автомобиля; - лѐгкость управления автомобилем;
- пропорциональность между усилием на рулевом колесе и сопротивлением повороту управляемых колѐс;
- соответствие между углами поворота рулевого колеса и управляемых колѐс; - минимальную передачу толчков и ударов на рулевое колесо от дорожных
неровностей; - предотвращение автоколебаний управляемых колѐс вокруг осей поворота;
- минимальное влияние на стабилизацию управляемых колѐс; - травмобезопасность, исключающую травмирование водителя при любых
столкновениях автомобиля.
141

Минимальный радиус поворота – это расстояние от центра поворота до оси колеи переднего наружного управляемого колеса при максимальном угле поворота колеса.
Минимальный радиус поворота автомобиля можно определить по следующей формуле:
Rпmin=
R |
э |
0,5В |
|
|
||
|
|
|
1 |
|
|
|
cos( |
max |
|
1 |
) |
||
|
|
|
|
|
,
где
Rэ=
|
L |
|
|
|
tg ( |
max |
|
1 |
) |
|
|
|
- радиус поворота автомобиля;
θmax – максимальный угол поворота управляемых колѐс; δ1, δ2 – углы увода передних и задних колѐс;
L – база автомобиля.
Центр поворота автомобиля О находится внутри его базы на некотором расстоянии С от оси задних колѐс:
С =Rэ tgδ2.
Угловым передаточным числом рулевого управления называется отношение
угла поворота рулевого колеса αр.к. |
к углу поворота управляемых колѐс θ: |
|||||||
|
uω= |
|
р.к. |
, |
|
|
||
|
|
|
|
|||||
|
|
|
|
|
||||
|
|
|
|
|
|
|
||
где |
θ=(θн+θв)/2; θн, |
|
θв |
– углы поворота |
наружного |
и внутреннего |
||
управляемых колѐс. |
|
|
|
|
|
|
|
|
Это |
передаточное число |
является переменным, |
зависит от |
передаточных |
чисел рулевого механизма uр.м. и рулевого привода uр.п. и равна их произведению:
uω=uр.м.uр.п..
Угловое передаточное число называют также передаточным числом рулевого механизма, которое равно отношению угла поворота рулевого колеса αр.к. к углу поворота вала сошки αр.с..
Рулевые механизмы большинства автомобилей имеют постоянное передаточное число uр.м.=13…22 для легковых автомобилей uр.м.=20…25 для грузовых автомобилей.
Передаточным числом рулевого привода называется отношение угла поворота вала рулевой сошки αр.с. к углу поворота управляемых колѐс θ. Передаточное число рулевого привода при повороте рулевого колеса не остаѐтся постоянным, а изменяется, так как изменяется положение рычага и сошки. Его значение находится в пределах 0,85…1.10.
Рулевым называется механизм, преобразующий вращение рулевого колеса в поступательное перемещение рулевого привода, вызывающее поворот управляемых колѐс автомобиля. Рулевые механизмы должны обеспечивать:
-высокий КПД при передаче усилия от рулевого колеса к управляемым колѐсам для лѐгкости управления автомобилем и несколько меньший КПД в обратном направлении для уменьшения толчков и ударов на рулевом колесе от дорожных неровностей;
-обратимость механизма, исключающую снижение стабилизации управляемых колѐс автомобиля;
142

-минимальный зазор в зацеплении механизма при нейтральном положении управляемых колѐс и возможность регулирования этого зазора в процессе эксплуатации;
-заданный характер изменения передаточного числа механизма.
На современных автомобилях имеют применение три типа рулевых механизмов: червячные (червячно-роликовые и червячно-секторные), винтовые (винторычажные и винтореечные) и зубчатые (шестерѐнные и реечные).
Червячные рулевые механизмы применяются на легковых, грузовых автомобилях и автобусах.
Винтовые рулевые механизмы используются на тяжѐлых грузовых автомобилях. Наибольшее распространение получили винтореечные механизмы. Винторычажные применяются редко, так как имеют низкий КПД и значительное изнашивание.
Зубчатые рулевые механизмы применяются в основном на легковых автомобилях малого и среднего классов.
Рулевой привод служит для передачи усилия от рулевого механизма к управляемым колѐсам и для обеспечения правильного поворота колѐс. В соответствии с предъявляемыми требованиями рулевой привод должен обеспечивать:
-правильное соотношение углов поворота управляемых колѐс, исключающее боковое скольжение колѐс автомобиля;
-отсутствие автоколебаний управляемых колѐс вокруг шкворней;
-отсутствие самопроизвольного поворота управляемых колѐс при колебаниях автомобиля на упругих устройствах подвески. Рулевые приводы различаются по типу рулевой трапеции(с неразрезанной рулевой трапецией и с разрезанной рулевой трапецией) и по расположению рулевой трапеции (с передней рулевой трапецией и с задней рулевой трапецией).
В рулевом управлении рассчитывают на прочность:
-детали рулевого механизма;
-детали рулевого привода.
При расчѐте на прочность определяют нагрузки, действующие на детали рулевого управления, и напряжения, возникающие в деталях.
При расчѐте максимального усилия на рулевом колесе по максимальному сопротивлению повороту управляемых колѐс на месте момент сопротивления повороту определяется по формуле:
М = |
2 |
|
|
Gk3 |
, |
|
у |
|
|||
с |
3 |
|
pш |
|
|
|
|
|
|
где θу = 0,9…1,0 – коэффициент сцепления при повороте управляемого колеса на месте;
Gk – нагрузка на колесо;
Рш – давление воздуха в шине.
Усилие на рулевом колесе для поворота на месте
Рр.к.= |
|
|
М с |
|
, |
|
u |
|
R |
|
|
||
|
|
|
р.к. |
р. у. |
||
|
|
|
|
|
143 |
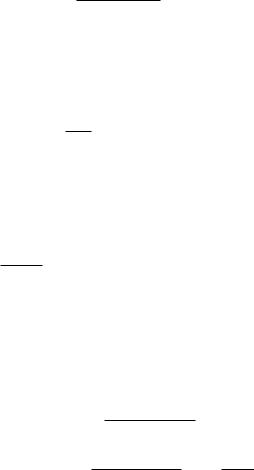
где uω – угловое передаточное число рулевого управления; Rр.к. – радиус рулевого колеса;
ηр.у – КПД рулевого управления.
Рулевой вал (обычно трубчатый) работает на кручение, нагружаясь моментом
Мр.к.Рр.к..
Напряжения кручения трубчатого вала
ηкр=
М |
р.к. |
d |
н |
|
|
|||
|
|
|
|
|||||
0,2(d |
4 |
d |
4 |
) |
||||
н |
в |
|||||||
|
|
|
|
|
|
,
где dн и dв – наружный и внутренний диаметры вала.
В червячно-роликовой рулевой передаче глобоидный червяк и ролик рассчитывают на сжатие, при котором определяют контактные напряжения в зацеплении:
ζсж=
Q Fk n
,
где Q – осевая сила, действующая на червяк;
Fk – площадь контакта одного гребня ролика, равная сумме площадей двух сегментов;
n – число гребней роликов.
Осевая сила Q=
М |
кр |
|
|
|
|
r tg |
ч |
|
0 |
|
,
где r0 – начальный радиус червяка в наименьшем сечении; βч – угол подъѐма винтовой линии червяка.
В рулевом приводе рассчитывают вал рулевой сошки, рулевую сошку, палец рулевой сошки, продольную и поперечную тяги и рычаги поворотных цапф.
Вал рулевой сошки рассчитывают на кручение.
При отсутствии усилителя ηкр=
при наличии усилителя ηкр= |
М |
|
М |
р.к. |
u |
|
|
р.м. |
|||
|
|
р.м. |
||||||
|
|
0,2d |
3 |
|
|
|||
|
|
с |
|
|
||||
|
|
|
|
|
|
|
|
|
р.к. |
u |
|
|
|
р.м. |
|
||
|
р.м. |
|
||||||
0,2d |
3 |
|
|
|||||
|
|
|
||||||
c |
|
|
|
|||||
|
|
|
|
|
|
|
|
;
|
|
D |
2 |
|
|
|
|
р |
|
|
гц |
ж |
4 |
|
|
|
|
||
|
|
|
,
где dc – диаметр вала рулевой сошки.
Расчѐт сошки проводят на изгиб и кручение от максимальной силы Рсош , действующей на шаровой палец от продольной рулевой тяги.
При отсутствии усилителя Рсош= |
М р.к.u р.м. р.м. |
, |
|
||
|
l1 |
где l1 – расстояние между центрами головок рулевой сошки.
|
М |
|
u |
|
|
D2 |
||
При наличии гидроусилителя Р = |
|
р.к. |
|
р.м. р.м. |
р |
|
гц |
. |
|
|
|
|
ж |
|
|||
сош |
|
|
l |
4l |
||||
|
|
|
|
1 |
|
|
1 |
|
7.12. Тормозное управление
Как уже упоминалось ранее, современные автомобили оборудуются различными тормозными системами.
144

Рабочая тормозная система предназначена для снижения скорости автомобиля вплоть до полной его остановки. Она является наиболее эффективной из всех тормозных систем, действует на все колѐса автомобиля и используется для служебного и экстренного торможения.
Стояночная тормозная система служит для удержания на месте неподвижного автомобиля. Она воздействует только на задние колѐса автомобиля или на вал трансмиссии.
Запасная тормозная система является резервной, она предназначена для остановки автомобиля при выходе из строя рабочей тормозной системы. При отсутствии на автомобиле отдельной запасной тормозной системы еѐ функции может выполнять исправная часть рабочей тормозной системы или стояночная тормозная система.
Вспомогательная тормозная система служит для ограничения скорости движения автомобиля на длинных и затяжных спусках. Она выполняется независимой от других тормозных систем и представляет собой тормоз – замедлитель, который обычно действует на вал трансмиссии.
Прицепная тормозная система предназначена для снижения скорости движения, остановки и удержания на месте прицепа, а также автоматической его остановки при отрыве от автомобиля – тягача.
Рабочей, стояночной и запасной тормозными системами оборудуются все автомобили, а вспомогательной – только грузовые автомобили большой грузоподъѐмности полной массой свыше 12 т и автобусы полной массой более 5 т. Прицепной тормозной системой оборудуются прицепы, работающие в составе автопоездов.
Тормозные системы должны обеспечивать:
-минимальный тормозной путь или максимальное замедление при торможении;
-сохранение устойчивости автомобиля при торможении;
-стабильность тормозных свойств при неоднократных торможениях;
-минимальное время срабатывания при торможении;
-пропорциональность между усилием на тормозной педали и тормозными силами на колѐсах автомобиля;
-лѐгкость управления.
Необходимыми условиями получения минимального тормозного пути являются минимальное время срабатывания тормозного привода, одновременное торможение всех колѐс автомобиля, возможность доведения тормозных сил на колѐсах автомобиля до максимального значения по сцеплению и обеспечение необходимого распределения тормозных сил между колѐсами автомобиля в соответствии с нагрузками на колѐса.
Для выполнения требования устойчивости при торможении необходимо, чтобы тормозные силы на левых и правых колѐсах автомобиля при торможении были одинаковыми (разница не более 15 %) и распределялись между передними и задними колѐсами в соответствии с приходящимися на них нагрузками или пропорционально нормальными реакциями на колѐсах:
145

Ртор1 |
|
R |
z1 |
|
|
|
|
|
|
Р |
тор2 |
|
R |
z 2 |
|
|
|
.
Стабильность тормозных свойств при неоднократных торможениях автомобиля может быть обеспечена, если тормозные накладки будут иметь коэффициент трения, равный 0,3…0,35, мало зависящий от скорости скольжения, нагрева и попадания на них воды.
Время срабатывания тормозной системы зависит главным образом от типа тормозного привода. Оно должно составлять 0.2…0,5 с при гидравлическом приводе, 0.6…0,8 при пневматическом приводе и 1…2 с для автопоезда с пневматическим тормозным приводом.
Тормозные механизмы могут осуществлять принудительное замедление автомобиля различными способами – механическим (фрикционным), гидравлическим, электрическим и внеколѐсным торможением.
Фрикционные тормозные системы (дисковые и барабанные) получили наиболее широкое распространение. Дисковые тормозные механизмы применяются для передних и задних колѐс легковых автомобилей малого и среднего классов. Барабанные тормозные механизмы используют на грузовых автомобилях, независимо от их грузоподъѐмности, в качестве колѐсных и трансмиссионных и на легковых автомобилях малого и среднего классов для задних колѐс.
Дисковые тормозные механизмы по сравнению с барабанными имеют меньшую массу, более компактны, более стабильны и лучше охлаждаются. Однако они менее эффективны, имеют более быстрое изнашивание фрикционных накладок и хуже защищены от грязи.
Гидравлические, электрические, компрессорные и аэродинамические тормозные механизмы используются на автомобилях в качестве тормозовзамедлителей.
Гидравлические тормоза-замедлители имеют большую массу и мало эффективны при небольших скоростях движения автомобиля.
Электрические тормоза-замедлители высокоэффективны и обеспечивают плавность торможения автомобиля. Однако они имеют большую массу, дорогостоящи в изготовлении и расходуют дополнительную энергию аккумуляторных батарей.
Компрессорный тормоз-замедлитель прост по конструкции и не требует больших затрат. Однако он малоэффективен при торможении автомобиля, движущегося на высших передачах. Кроме того, для него необходимо специальное устройство, предотвращающее выбрасывание масла из воздушного фильтра двигателя.
Аэродинамические тормозные механизмы увеличивают сопротивление воздуха и используются для экстренного внеколѐсного торможения автомобилей.
Эффективностью тормозного механизма служит коэффициент, который представляет собой отношение тормозного момента Мтор, создаваемого механизмом, к моменту от приводной силы, называемый коэффициентом эффективности:
146

Кэ=
М |
тор |
|
|
|
|
Р |
|
r |
|
п.с. п |
,
где Рп.с. – суммарная приводная сила тормозных колодок; rп – радиус приложения результирующей силы трения.
В барабанном тормозном механизме коэффициент эффективности рассчитывается не только для механизма в целом, но и отдельно для каждой тормозной колодки:
Кэ1=
М |
тор1 |
|
|
||
Р u |
б |
|
1 |
- для первичной колодки;
Кэ2= |
М |
тор2 |
- для вторичной колодки, |
||
|
|||||
Р r |
|||||
|
|
||||
|
|
2 |
б |
|
где Мтор1, Мтор2 – тормозные элементы, создаваемые колодками; Р1, Р2 – приводные силы колодок.
Тормозной момент дискового механизма
Мтор=2Рμrср,
где μ – коэффициент трения. Коэффициент эффективности механизма
Кэ= |
М тор |
. |
|
||
|
2Рr |
|
|
ср |
Дисковые тормозные механизмы обеспечивают плавное торможение всех колѐс при любой начальной скорости автомобиля. Однако они очень чувствительны к загрязнению и их сложно использовать в качестве стояночных тормозных механизмов.
Широко распространѐнные барабанные тормозные механизмы отличаются силовым воздействием колодок с разжимным устройством и барабаном, а также расположением опор тормозных колодок.
Приводные силы Р1 и Р2 прижимающие колодки 1 и 2 к барабану равны, так как площади поршней тормозного цилиндра одинаковы. Колодка 1 называется первичной (активной, самоприжимной), а колодка 2 – вторичной (пассивной, самоотжимной). Первичная колодка нагружается больше, чем вторичная. При вращении колеса в противоположную сторону (движение автомобиля задним ходом) функции колодок изменяются и колодка 2 работает как первичная, а колодка 1 – как вторичная.
В связи с тем, что реакции барабана на колодки и силы трения не равны между собой, подшипники ступицы колеса нагружаются дополнительной силой. Такой механизм является неуравновешенным. Тормозная колодка первичной накладки изнашивается интенсивнее, чем вторичной. Для уравновешивания изнашивания фрикционная накладка первичной накладки делается длиннее, чем у вторичной колодки.
Такого типа тормозные механизмы применяются на грузовых автомобилях средней грузоподъѐмности и в качестве задних тормозных механизмов на легковых автомобилях.
147

Управление тормозными механизмами осуществляется тормозными приводами.
Механический тормозной привод представляет систему тяг, рычагов, тросов
спомощью которых усилие водителя от рычага или педали управление передаѐтся к тормозным механизмам. Механический привод применяется в качестве обязательного привода в стояночной тормозной системе. На легковых автомобилях механический привод действует на тормозные механизмы задних колѐс, а на грузовых – на трансмиссионный тормоз, устанавливаемый обычно на вторичном валу коробки передач. Механический привод имеет низкий КПД, равный 0,4, и требует частых регулировок.
Гидравлический тормозной привод является гидростатическим, в котором передача энергии осуществляется давлением несжимаемой жидкости (до 220 МПа). Гидравлический привод применяется на легковых и грузовых автомобилях малой и средней грузоподъѐмности. На легковых автомобилях в зависимости от их класса могут применяться тормозные гидравлические приводы без усилителя или с вакуумным усилителем, который облегчает управление автомобилем. На грузовых автомобилях применяются вакуумные, гидровакуумные и пневматические усилители, при которых усилие на тормозной педали не превышает 250…300 Н, тогда как без усилителя усилие на тормозной педали достигает 800…1000 Н.
Пневматический тормозной привод применяется на грузовых автомобилях средней и большой грузоподъѐмности, автопоездах и автобусах. Он более эффективен по сравнению с другими приводами, однако, менее компактен, сложен по конструкции и в обслуживании, более дорогостоящий и имеет большее время срабатывания (в 5…10 раз больше, чем у гидропривода).
Комбинированные тормозные приводы применяются на грузовых автомобилях средней и большой грузоподъѐмности, а также на автопоездах. К ним относятся приводы пневмогидравлические, электропневматические и др. На длиннобазовых грузовых автомобилях и многозвенных автопоездах применяются электропневматический тормозной привод, имеющий электрическую часть и пневматическое оборудование.
Антиблокировочная система служит для устранения блокировки колѐс автомобиля при торможении. Система автоматически регулирует тормозной момент и обеспечивает одновременное торможение всех колѐс автомобиля. она также обеспечивает оптимальную эффективность торможения и повышает устойчивость автомобиля.
При расчѐте тормозных систем определяют:
-удельные давления для фрикционных накладок тормозных колодок;
-работу трения при торможении;
-нагрев тормозного барабана или тормозного диска;
-нагрузки и параметры гидравлического тормозного привода без усилителя и
сусилителем;
-нагрузки и параметры пневматического тормозного привода.
148

Удельные давления для накладок тормозных колодок рассчитывают по величине нормальных реакций, действующих со стороны тормозного барабана.
Удельные давления для первичной колодки
руд1= |
N1 |
; |
r b |
||
|
1 б 1 |
|
для вторичной колодки
руд2= |
N 2 |
|
, |
r b |
2 |
||
|
2 б |
|
где N1, N2 – нормальные реакции для первичных и вторичных колодок; β1, β2 – углы охвата колодок;
rб – радиус тормозного барабана; b1, b2 – ширина колодок.
Удельные давления не должны превышать 100…200 Н/см2 для первичной колодки и 50…70 Н/см2 для вторичной колодки. Для уравновешенного тормозного механизма руд=80…90 Н/см2.
Удельная работа трения qуд зависит от начальной скорости торможения, при которой вся кинетическая энергия автомобиля поглощается работой трения в тормозных механизмах:
qуд=
A
Fнак
,
где A=mav2/2 – кинетическая энергия автомобиля массой ma при максимальной скорости v начала торможения;
Fнак – суммарная площадь поверхности накладок тормозных механизмов всех колѐс автомобиля.
Средние значения удельной работы трения составляют 1…2 кДж/см2 для легковых автомобилей и 0,6…0,8 кДж/см2 для грузовых автомобилей и автобусов.
Нагрев tб тормозного барабана (или диска) за одно торможение определяется по формуле:
tб=
m |
k |
|
|
|
|
2m |
с |
|
|
б |
|
,
где mk – масса автомобиля, приходящаяся на тормозящее колесо; mб – масса тромозного барабана;
с=500 Дж/(кг·К) – удельная теплоѐмкость чугуна или стали.
Нагрев тормозного барабана или диска недолжен превышать за одно торможение 20 0С.
7.13.Подвеска
Всоответствии с предъявляемыми требованиями подвеска должна: - обеспечивать высокую плавность хода автомобиля; - обладать высокой динамической энергоѐмкостью;
- эффективно гасить колебания кузова и колѐс автомобиля при движении; - обеспечивать правильную кинематику управляемых колѐс автомобиля; - иметь минимальную массу неподрессоренных частей.
149

Плавность хода автомобиля можно оценивать по упругой характеристики подвески и по амплитудно – частотной характеристике автомобиля.
Упругой характеристикой подвески называют зависимость между вертикальной нагрузкой и прогибом подвески, измеренным по перемещению колеса.
По упругой характеристике подвески можно определить следующие параметры: статический прогиб подвески fст, динамический прогиб подвески при ходе колеса вверх fд.в, и вниз fд.н, жѐсткость подвески сп, коэффициент динамичности кд и статическую силу сухого трения Fст в подвеске.
Статический прогиб подвески fст определяется путѐм проведения касательной линии к упругой характеристике в точке, соответствующей статической нагрузке Gст. Желательно, чтобы статический прогиб подвески составлял 200…250 мм для легковых автомобилей, 80…140 мм для грузовых автомобилей и 110…200 мм для автобусов.
Динамический прогиб подвески при ходе колеса вверх fд.в, включая прогиб резинового буфера, ограничивающего ход колеса, должен составлять: 0,5fст для легковых автомобилей; 1fст для грузовых автомобилей и 0,75fст для автобусов.
Динамический прогиб подвески при ходе колеса вниз fд.н должен быть приблизительно равен динамическому прогибу при ходе колеса вверх (fд.н=fд.в).
Жѐсткость подвески определяется как тангенс угла наклона касательной к средней линии упругой характеристики подвески:
Сп=tgα= Gст .
fст
При снижении жѐсткости подвески уменьшается частота колебаний подрессоренной подвески и повышается плавность хода автомобиля. Это достигается применением независимой подвески, жѐсткость которой меньше, чем у зависимой подвески.
Статическая сила трения Fст в подвеске определяется как половина разности ординаты, заключѐнной между кривыми нагружения и разгружения подвески. Эту силу называют силой сухого трения. Динамическая сила сухого трения в подвеске меньше, чем статическая, и еѐ значение приблизительно составляет Fд=(0,5…0,7)Fст.
Амплитудно-частотной характеристикой автомобиля называется зависимость перемещений кузова и колѐс и ускорений кузова автомобиля от частоты возмущающей силы. Периодически действующая на автомобиль возмущающая сила, обусловленная волнистой поверхностью дороги, вызывает вынужденные колебания автомобиля. Эти колебания зависят от частоты возмущающей силы (чередование дорожных неровностей), с-1:
ν= 2v ,
3,6lд
где v – скорость автомобиля, км/ч; lд – длина неровностей, км/ч. Энергоѐмкость подвески характеризуется коэффициентом динамичности.
150