
Пинч / Смит Р.,Клемеш Й.,Товажнянский Л.Л.,Капустенко П.А.,Ульев Л.М.-- Основы интеграции тепловых процессов (2000)
.pdf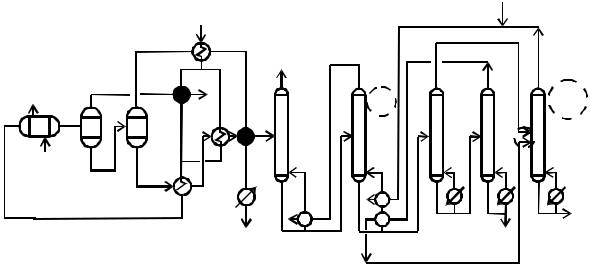
30 |
Глава 1 |
мых утилит. В итоге из проекта было полностью исключено использование охлаждающей воды, потребление энергии снижено на 38%, число теп- лообменных аппаратов сократилось вдвое, а их общая площадь поверхно- сти теплообмена уменьшена на 15%.
Сырьё и |
Пар |
|
|
Рециклы |
|
Пар |
1.05 |
|
|
4.2 |
кг/см2 |
|
|
кг/см2 |
|
1 |
2 |
3 |
4 |
5 |
Реактор
Остаток
Отпарная
колонна
Рис. 1.12. Процесс после реконструкции
Вкачестве следующего примера рассмотрим реконструкцию тепло- обменной системы и процесса, который состоит из реактора, вакуумной перегонки и более сложной, чем в предыдущем процессе системы очистки
(рис. 1.11).
Данный процесс уже высоко интегрирован с хорошо установленны- ми связями между технологическими потоками. Система теплообмена со- держит 13 теплообменников. Основным заданием при реконструкции рас-
сматриваемой ХТС является снижение энергопотребления процессом с помощью модификации теплообменной сети. Технологическая схема ре- конструкции процесса выполненная с помощью методов пинч-анализа, по- казана на рис. 1.12. Модификация процесса включает изменения давления
вколонне №2 от 0,14 Мпа до 0,105 МПа, а в колонне №5 от 0,49 МПа до 0,42 МПа. В теплообменную сеть необходимо установить два новых теп- лообменника вместо трех теплообменников,. которые нельзя использовать
вмодернизированной сети из-за их несоответствия новым технологиче- ским условиям, но их стоимость равна стоимости вновь устанавливаемым теплообменникам, и поэтому дополнительных капиталовложений в модер- низацию ХТС можно избежать.
Врезультате указанных мероприятий нагрузка на внешние энергоно- сители снижается на 27%, а срок окупаемости выполненного проекта со- ставит 6 месяцев.

Структура и иерархия проектирования ХТС |
31 |
В заключение проведенного нами краткого рассмотрения методоло- гии проектирования отметим, какие улучшения позволяет сделать инте- грация процесса:
1)качественное улучшение процесса проектирования;
2)снижение затрат на энергоносители;
3)уменьшение выбросов вредных веществ в окружающую среду;
4)лучшее использование капитальных вложений;
5)повышение производительности после реконструкции.
Укажем кратко на применимость методов пинч-анализа:
1)прикладные разработки;
2)энергосбережение;
3)уменьшение вредных выбросов;
4)экономия капитальных вложений;
5)использование как для новых проектов, так и для реконструкций;
6)применимость для непрерывных и для периодических процессов;
7)применимость для всех производственных процессов.
Реактор
Пар
70
Рецикл
Цели
1
1652 |
Пар |
|
|
|
|
|
Подвод тепла |
62% |
|
|
|
|
||
|
3 |
2 |
поверхности теплообмена |
85% |
|
|
|
||
|
654 |
|
Число теплообменников |
67% |
|
|
|
|
|
Сырьё |
Охлаждающая |
|
Продукт |
|
вода |
|
|
||
|
|
|
|
Рис. 1.13. Пинч – анализ позволяет устанавливать цели перед проектированием
Отметим еще два очень важных свойства, являющихся неотъемле- мой частью пинч-анализа. Первое – это возможность установления целей проектирования перед началом самого проектирования. Если вернуться к
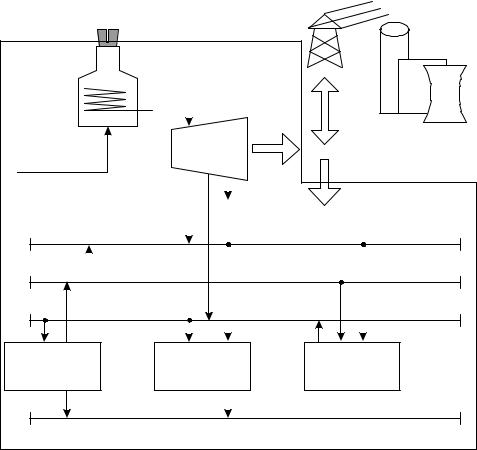
32 |
Глава 1 |
примеру 1 (рис. 1.13), мы видим значения тех величин, которые должны быть достигнуты в процессе выполнения проекта.
Вторым важным свойством является возможность интегрирования процессов в пределах большого производственно-территориального ком- плекса (рис. 1.14).
Процессы в большом производственно-территориальном комплексе функционируют независимо друг от друга, и порой трудно сделать выбор для вложения денежных средств с целью улучшения экономических пока- зателей. С помощью методов пинч-анализа мы можем получить информа- цию о энергетических требованиях для всего комплекса, рассматривая один процесс эквивалентный всему комплексу. В итоге мы можем полу- чить инвестиционные планы, определить энергетические цели и цели для
Потребляемое |
|
Электростанция |
топливо |
|
|
|
Конденсат |
|
Процесс А |
Процесс B |
Процесс C |
|
|
Охлаждающая вода |
Рис. 1.14. Интеграция производственно-территориального комплекса
снижения эмиссии вредных веществ как для существующих процессов, так и для проектируемых.
За последнее десятилетие университетом “UMIST” и членами научно- исследовательского консорциума UMIST-а [www.cpi.umist.fc.uk] выполне- но более 2600 проектов создания новых и модернизации действующих производств в различных отраслях промышленности и различных странах.
Структура и иерархия проектирования ХТС |
33 |
Некоторые результаты воплощения этих проектов приведены в табли-
цах 1.1-1.3 ниже.
Таблица 1.1. Результаты применения Пинч-технологии в “Union Carbide”
|
Тип |
Экономия за |
Кап. |
Время оку- |
Процесс |
проекта |
счет снижения |
вложе- |
памости, |
|
|
энергетических |
ния, $ |
мес |
|
|
затрат, $/год |
|
|
Нефтехимический |
Модиф. |
1 050 000 |
500 000 |
6 |
Специальной хи- |
Модиф. |
139 000 |
57 000 |
5 |
мии |
|
|
|
|
––– // ––– |
Модиф. |
82 000 |
6 000 |
1 |
Лицензионная ус- |
новый |
1 300 000 |
экономия |
– |
тановка |
|
|
|
|
Органической |
Модиф. |
1 000 000 |
600 000 |
7 |
объемной химии |
|
|
|
|
––– // ––– |
Модиф. |
1 243 000 |
1 835 000 |
18 |
––– // ––– |
Модиф. |
2 000 000 |
800 000 |
5 |
Спец. Химия |
Модиф. |
570 000 |
200 000 |
4 |
Таблица 1.2. Результаты применения Пинч-технологии в “ICI”
|
Тип |
Экономия за счет сни- |
Кап. вложения, |
Процесс |
проекта |
жения энергетических |
$ |
|
|
затрат, $/год |
|
Объемной орг. |
Новый |
800 000 |
800 000 |
химии |
|
|
|
Спец. химии |
–– // –– |
1 600 000 |
экономия |
Грубой перера- |
Модиф. |
1 200 000 |
–– // –– |
ботки |
|
|
|
Неорг. объемн. |
Новый |
320 000 |
–– // –– |
химии |
|
|
|
Спец. химии |
Модиф. |
200 000 |
160 000 |
Новый завод |
Новый |
30 – 40 % |
30 % экономии |
Не профильный |
Модиф. |
300 000 |
800 000 |
Нефтехимия |
–– // –– |
фаза I 2 000 000 |
600 000 |
|
|
фаза II 200 000 |
1 200 000 |
34 |
Глава 1 |
Таблица 1.3. Анализ применения Пинч-технологии в различных отраслях
промышленности
Отрасль |
Экономия |
Окупаемость проекта |
Нефтехимия |
40% от потребляемого топ- |
10-24 месяца |
|
лива |
|
Неорг. химия |
30% общей энергии |
9-16 месяцев |
Химия |
30% общей энергии |
15 месяцев |
Фармаколо- |
20-40% общей энергии |
2-2,5 года |
гия |
|
|
Полимерная |
25% + увеличение произво- |
до 2,5 лет |
|
дительности |
|
Красители |
15% общей энергии |
15 месяцев |
Металлургия |
50% увеличение мощности |
2 года |
Пищевая |
35% общей энергии |
1 – 2 года |
Выводы
·Иерархия проектирования процесса может быть представлена кон- центрической (²луковичной²) диаграммой;
·Цели обеспечивают:
-стимул к поиску лучших решений;
-уверенность, что при их достижении ничего не упущено; · Пинч-анализ имеет широкий диапазон применения.

Введение в пинч–принципы |
35 |
|
|
|
|
Глава 2
ВВЕДЕНИЕ В ПИНЧ-ПРИНЦИПЫ
Согласно рассмотренной в предыдущем разделе иерархии проекти- рования, выполнение проекта начинается с построения проекта реакторной системы – первый слой луковичной диаграммы, а затем переходит ко вто- рому слою, в котором совместно рассматриваются системы разделения и рециклы. Результатом выполнения этих двух внутренних этапов должны стать материальный и энергетический балансы ХТС.
Таким образом, нам становится известной тепловая нагрузка и на- грузка на хладагенты для двух внешних слоев луковичной диаграммы (т. е. для теплообменной системы и системы энергоносителей). В большинстве
применяющихся в настоящие время методов проектирования для полной оценки проекта необходимо выполнить все четыре этапа проектирования, заключенные в луковичную диаграмму, независимо от того, выполняется
проект вручную проектировщиком или с помощью автоматизированных систем.
В пинч-анализе, как мы уже упоминали, целевые значения, которые должен достигнуть проектировщик в результате выполнения проекта, мож- но получить после выполнения двух внутренних этапов луковичной диа- граммы, т. е. мы можем сделать экономическую оценку всего проекта, ре- ально не выполняя проекты для двух внешних слоев диаграммы. Более то- го, установление целей проектирования позволяет проектировщику вно- сить улучшения во внутренние слои луковичной диаграммы (реактор, сис- темы разделения и рецикла), что в свою очередь дает возможность коррек- тировать энергетические и инвестиционные данные (цели) для внешних слоев и т. д.
Такой подход позволяет быстро и эффективно проанализировать большое количество альтернативных проектов, такое количество, которое при полном проектировании и расчете ХТС трудно было бы проанализиро- вать за обозримое время даже большому количеству хороших профессио- налов.
Для того, чтобы освоить технику пинч-анализа нам предстоит разо- браться и понять, что лежит в основе этого метода.
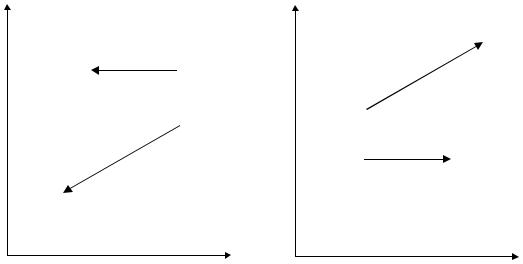
36 |
Глава 2 |
|
|
2.1. Построение составных кривых технологических потоков и определение энергетических целей
Все технологические потоки ХТС можно разделить на две группы. В одну из них войдут те потоки, которые требуют охлаждения перед даль- нейшей их обработкой. Мы будем называть такие потоки – горячими пото- ками. Во вторую группу потоков войдут те потоки, которые необходимо нагреть – холодные потоки.
T |
T |
1 |
1 |
2 |
|
2 |
а |
|
б |
0 |
H 0 |
H |
Рис. 2. 1. Представление технологических потоков на температурно–энтальпийной плоскости: а) – представление горячих потоков: 1 – конденсация, 2 – охлаждение; б) – холодные потоки: 1 – нагревание; 2 – испарение
Изменение теплосодержания технологических потоков удобно анали- зировать на температурно–энтальпийной диаграмме (рис. 2.1).
Горячие технологические потоки принято обозначать вектором, на- правленным справа налево в температурно–энтальпийных координатах. Это связано с тем, что у горячих тепловых потоков происходит уменьше- ние их теплосодержания – энтальпии как при охлаждении, так и при изме- нении их фазового состояния (рис. 2.1.А).
Аналогично у холодных технологических потоков ХТС при нагревании или изменении их фазового состояния теплосодержание возрастает, и по- этому в координатной плоскости температура – энтальпия такие потоки будут изображаться векторной линией, направленной слева направо.
Заметим, что представление изменения энтальпии технологического
потока в зависимости от изменения его температуры отобразить прямой линией возможно только для потоков, теплоемкость которых в пределах изменения температуры потока можно считать постоянной величиной.
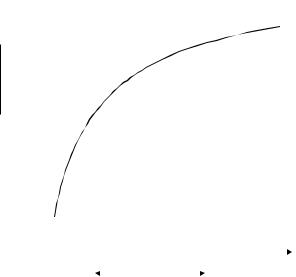
Введение в пинч–принципы |
37 |
|
|
|
|
Т
T2
Т
T1
0 |
Н |
|
Н |
|
|
Рис. 2.2. Функциональная зависимость между изменением температуры и изменением
энтальпии потока
Действительно, связь между изменением температуры потока и уменьшением его теплосодержания – энтальпии в общем случае будет вы- ражаться нелинейной функцией (рис. 2.2) приращения энтальпии потока при изменении температуры и определяться следующим образом :
dH = cp MdT |
(2.1) |
где ср- удельная теплоемкость вещества технологического потока при по- стоянном давлении, Дж/кг×К; М – массовый расход вещества потока, кг/с; Т – температура, К; Н – теплосодержание потока, Вт.
Следовательно, общее изменение теплосодержания технологическо-
го потока в пределах изменения его температуры может быть вычислено с помощью выражения:
T2 |
|
DH = òcp MdT . |
(2.2) |
T1 |
|
Если теплоемкость вещества потока в пределах изменения температуры [Т1, Т2] остается постоянной, то (2.2) примет вид:
H = cp M(T2 − T1 ) |
(2.3) |
Произведение удельной теплоемкости ср и расхода М принято называть те- плоемкостью потока или потоковой теплоемкостью и обозначать иденти- фикатором СР:
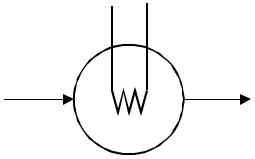
38 |
Глава 2 |
|
|
CP = cp M . |
(2.4) |
Размерность потоковой теплоемкости определяется как [CP] = Дж/К×с. Заметим, что необходимо при работе с методами пинч-анализа очень
четко представлять различие между удельными величинами и потоковыми величинами. Потоковая теплоемкость СР определяет количество энер-
Q
T1 |
T2 |
|
|
H=Q |
|
|
|
T=T2-T1 |
CP(T) = lim |
H |
|
T |
|||
|
T→0 |
Рис. 2.3. Определение потоковой теплоемкости СР
гии, которое необходимо подвести к потоку, чтобы повысить темпера- туру вещества, проходящего через поперечное сечение потока за одну се-
кунду на один градус. Формально определить потоковую теплоемкость можно рассмотрев поток, нагреваемый в теплообменном устройстве (рис. 2.3.).
Потоковую теплоемкость можно также определять как отношение мощности, потребляемой технологическим потоком к разности его конеч- ной и начальной температур, CP=DH/(T2-T1), что бывает полезно при быст- рой оценке потенциала энергосбережения действующих предприятий.
Из (2.3.), (2.4.) следует, что изменение энтальпии потока DH опреде- ляет количество энергии, которое необходимо подвести к потоку, чтобы изменить температуру вещества, проходящего в течении 1 секунды через поперечное сечение потока от значения Т1 до значения Т2 (2.3.). Отсюда следует, что фактически DH представляет энергетическую мощность, кото- рую необходимо подводить к потоку, чтобы удовлетворить проектным тре- бованиям. В дальнейшем изложении, исключительно с целью большей на- глядности, мы будем при использовании терминов теплота, энергия, эн- тальпия, теплосодержание, относящихся к технологическим потокам, под- разумевать, что это потоковые величины, а случаи, в которых это может привести к искажению смысла, мы будем специально оговаривать.
Следующим основополагающим понятием, которым оперирует пинч- анализ, является наименьший тепловой напор в теплообменной ХТС или
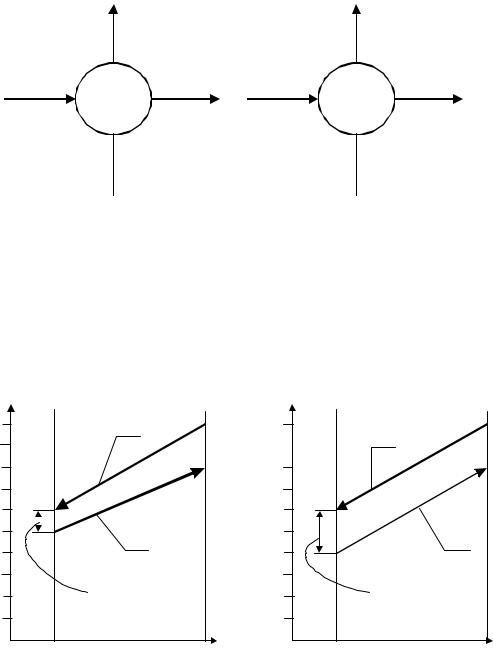
|
Введение в пинч–принципы |
39 |
||
|
|
|
||
минимальная разность температур |
Тmin между технологическими потока- |
|||
ми в теплообменном оборудовании. |
|
|
|
|
|
80 °C |
|
70 °C |
|
100 °C |
60 °C |
100 °C |
60 °C |
|
|
1 |
|
2 |
|
50 °C |
40 °C |
Рис. 2.4. К определению минимальной разности температур между теплоносителями в
теплообменных аппаратах
Рассмотрим два теплообменника (рис. 2.4.) и определим Тmin для каждого из них. Представим потоки теплоносителей на температурно- эн- тальпийной диаграмме, и поскольку изменение теплосодержания по абсо- лютной величине одинаковое у холодного и горячего потока, мы легко оп- ределяем Тmin. Первый теплообменник имеет минимальную температур-
|
T |
1 |
|
T |
|
|
|
|
|
|
1 |
|
|
|
|
|
|
|
|
|
|
80 |
|
|
80 |
|
|
|
60 |
|
|
60 |
|
|
|
40 |
2 |
|
40 |
|
2 |
|
|
|
|
|
||
|
20 |
Tmin=10 °C |
20 |
Tmin=20 °C |
||
|
|
а |
|
|
б |
|
|
0 |
|
H |
0 |
|
H |
Рис. 2.5. Определение |
Тmin с |
помощью |
температурно-энтальпийной диаграммы: |
|||
а – изменение теплосодержания потоков в |
теплообменнике – 1; б – 2; |
1 – горячий по- |
||||
ток; |
2 – холодный поток |
|
|
|
|
ную разность между теплоносителями 10 °С, а второй – 20 °С (рис. 2.5). Рассмотрим технологическую схему простого химического процесса,
имеющего два химических реактора, систему разделения и рецикл (рис. 2.6.). Система теплообмена имеет четыре теплообменных аппарата, два ре- куперативных теплообменника, один теплообменник, подогревающий по-