
75 группа 2 вариант / Режимы роботы и эксплуатации ТЭС / ПТ / Книги / Учебное пособие. Режимы работы и эксплуатация паротурбинных установок ТЭС
.pdf23.При снижении температуры выхлопных патрубков ЦНД до 55оС отключают подачу циркуляционной воды через труб- ную систему конденсатора.
24.В некоторых случаях при плановом останове турбины контролируют качество работы системы автоматического регу- лирования по удержанию ею оборотов холостого хода после от- ключения турбогенератора от сети. В этом случае при разгрузке турбоагрегата до максимальной мощности, обеспечиваемой при подаче пара через байпас ГПЗ при условии сохранения номи- нального давления перед стопорным клапаном, открывают пол- ностью регулирующий клапан и электрифицированную задвиж- ку на байпасе ГПЗ, после чего ГПЗ закрывают. Далее воздей- ствуя на синхронизатор турбины, разгружают турбогенератор до нуля (что подтверждается реле обратной мощности) и отключа- ют турбогенератор от сети. В этом случае система автоматиче- ского регулирования турбины должна устойчиво держать обо- роты холостого хода (3000 об/мин). Если частота вращения ро- тора будет возрастать, то турбина должна быть остановлена ав- томатом безопасности. В случае если частота вращения ротора продолжает увеличиваться, немедленный останов турбины осу- ществляют за счёт закрытия регулирующего клапана и запорной арматуры на байпасе ГПЗ. Дальнейшие операции по останову турбины ведут так, как описано выше.
4.4.5.2.Выбег ротора турбоагрегата
Выбег ротора является важным показателем, позволяющим в определённой степени судить об исправности турбоагрегата. Во-первых, выбег ротора характеризуется временем от момента отключения турбогенератора от сети до момента прекращения вращения ротора. Время полного выбега современных турбин составляет в зависимости от мощности от 20 до 45 минут. Уменьшение времени выбега свидетельствует о появлении по- вышенного трения в подшипниках или задеваний в проточной части и уплотнениях. Поэтому в процессе выбега ротора необ- ходимо периодически прослушивать турбину, чтобы обнару- жить возможные задевания. Увеличение времени выбега, как
341

правило, свидетельствует о неплотности стопорных или регули- рующих клапанов или обратных клапанов на линии регенера- тивных отборов [26].
Вторым важным показателем является кривая выбега, выра- жающая зависимость частоты вращения ротора от времени при выбеге ротора. Замедление частоты вращения при выбеге про- исходит из-за трения лопаток и дисков о пар, из-за вентиляции пара лопаточным аппаратом и из-за трения в масляном слое подшипников. Вентиляционные потери очень сильно зависят от частоты вращения. Со снижением частоты вращения они быстро уменьшаются, поэтому начальный участок кривой выбега ока- зывается более крутым (рис. 4.8). С уменьшением частоты вра- щения основную роль начинают играть потери на трение в мас- ляном слое подшипников. Сопротивление трения в подшипни- ках в меньшей степени зависит от частоты вращения, поэтому характер кривой выбега на следующем участке более пологий. Наконец, на последнем участке наблюдается резкое падение ча- стоты вращения, вызванное переходом от жидкостного трения в подшипниках к полусухому трению.
n, об/м ин |
|
|
|
3000 |
|
|
|
0 |
I |
II |
III |
|
|
|
|
|
|
|
В рем я, м ин |
Рис. 4.8. Кривая выбега ротора турбины: I – |
зона влияния вентиля- |
||
ционных потерь; II – |
зона влияния жидкостного трения в подшипни- |
||
ках; III – |
зона полусухого трения в подшипниках |
||
|
|
342 |
|
Для построения кривой выбега сначала отмечают время и момент закрытия стопорного клапана при номинальном числе оборотов турбины, затем через каждую 1 или 2 мин до полной остановки записывают число оборотов ротора, которые должны измеряться ручным контрольным тахометром. По данным изме- рениям строят кривую выбега, которая затем сравнивается с нормативной кривой, снятой при останове спустя первые (после монтажа или капитальных ремонтов) 200–300 часов работы по- сле приработки всех деталей турбины. Как нормативную, так и все текущие кривые выбега снимают при одном и том же посто- янном давлении в конденсаторе турбины.
Для каждой турбины должна быть определена длительность выбега ротора при останове с нормальным давлением отрабо- тавшего пара и при останове со срывом вакуума. При изменении этой длительности должны быть выявлены и устранены причи- ны отклонения. Длительность выбега должна быть проконтро- лирована при всех остановах турбоагрегата [9].
4.4.5.3. Особенности планового останова в резерв турбоагрегатов блочной ТЭС с барабанными котлами без промежуточного перегрева пара
1. В блочной паротурбинной установке ряд технологических систем обеспечиваются паром непосредственно из отборов тур- бин. Поэтому заранее или на определённом этапе разгрузки тур- боагрегата подачу пара на концевые уплотнения турбины, ос- новные эжекторы и деаэраторы питательной воды переводят от парового коллектора собственных нужд.
2. Все подготовительные операции, связанные с обеспечени- ем надёжности и безопасности турбины в период её разгрузки (расхаживание стопорных, регулирующих клапанов и ГПЗ; опробование маслонасосов смазки; отключение теплофикаци- онной установки, регулируемых отборов, ПВД; контроль крите- риев безопасности и т.д.), соответствуют изложенным в разд. 4.4.5.2 требованиям подготовки к останову неблочных турбоагрегатов.
343
3.При разгрузке блока до определённой мощности включают
вработу БРОУ, для того чтобы избыточный пар, вырабатывае- мый котлом, сбрасывать в конденсатор в обвод турбины.
4.Разгрузка энергоблока производится до нагрузки, опреде- ляемой устойчивостью поддержания на номинальном уровне температуры свежего пара при малых расходах топлива на котёл [26]. Дальнейшие остановочные операции проводятся в следу- ющей последовательности.
4.1.При нагрузке турбоагрегата 40–50 % от номинальной прекращают подачу топлива на котёл, который вследствие своей теплоаккумулирующей способности в течение нескольких ми- нут продолжает вырабатывать пар, подаваемый на турбину.
4.2.Для удержания номинального давления свежего пара вначале прикрывают БРОУ, а затем разгружают турбину.
4.3.При нагрузке 15–20 % от номинальной следует отключе- ние турбины и котла воздействием на соответствующие ключи останова (или от действия защиты по понижению давления в камере регулирующей ступени).
4.4.Осуществляют контроль отключения турбогенератора под воздействием реле обратной мощности. В случае отказа срабатывания реле турбогенератор отключают с БЩУ, для чего необходимо:
– просле дить по показаниям ваттметра за отсутствием нагрузки на турбине;
– убедиться , что давление в регулирующей ступени турбины снизилось до нуля;
– убедиться , что ГПЗ идет на закрытие (байпас ГПЗ должен быть отключён);
– откл ючить генератор, не допуская работу турбины в беспа- ровом режиме более 4 мин.
4.5.Отключить БРОУ (при его автоматическом открытии) и прекратить подачу воды на ее охлаждающее устройство.
4.6.При частоте вращения ротора 2800 об/мин включить ре- зервный электронасос смазки и следить, чтобы давление и тем- пература масла в системе смазки были нормативными.
344
4.7. Дальнейшие действия персонала соответствуют изло- женным в п. 4.4.5.2 требованиям по останову неблочных турбо- агрегатов.
4.4.5.4. Плановый останов турбоагрегатов в ремонт
Ранее было отмечено (см. разд. 4.3 настоящего пособия), что в зависимости от объема выполняемых ремонтных работ плано- вые ремонты разделяют на текущие, средние и капитальные.
Начало остановочных операций по выводу паротурбинной установки в любой вид ремонта осуществляется по команде начальника смены электростанции на основании разрешенной диспетчерской заявки. Заявку на вывод турбоагрегата в ремонт подает администрация цеха. Плановым остановам в ремонт все- гда предшествуют подготовительные работы.
На практике текущие ремонты выполняются по мере накоп- ления дефектов в работе вспомогательного турбинного обору- дования, препятствующих обеспечению экономичной и надёж- ной работы паротурбинной установки при её дальнейшей экс- плуатации. Как правило, это многочисленные дефекты, вклю- чающие течи рабочей среды через неплотности фланцевых со- единений трубопроводов, сальниковых уплотнений запорно- регулирующей арматуры или концевых уплотнений насосов; неплотности трубных систем регенеративных подогревателей; свищи в паропроводах и т.п. Устранение этих дефектов не свя- зано с тепловым состоянием собственно турбины. В таких слу- чаях останов паротурбинной установки осуществляют так же, как при выводе турбоагрегата в оперативное состояние «Резерв».
Плановый останов паротурбинной установки в капитальный и средний ремонты производится по программе, утвержденной главным инженером (техническим руководителем) ТЭС, кото- рая предусматривает в том числе (см. разд. 4.3 настоящего по- собия) и порядок вывода ПТУ из работы. При проведении капи- тальных и средних ремонтов осуществляют вскрытие цилиндров для проведения ревизии и устранения дефектов в элементах проточной части турбины (роторах, диафрагмах, концевых уплотнениях и т.д.). Прекращение вращения ротора турбины
345
валоповоротным устройством, а также прекращение подачи масла к подшипникам и снятие изоляции допускается как по техническим причинам, так и по соображениям техники без- опасности при температуре металла турбины ниже 150оС. Необ- ходимость в полном остывании турбины возникает и при ча- стичных ремонтах системы маслоснабжения (например, главных маслонасосов), подшипников, паровпускных частей турбины. Известно, что современные турбины остывают со скоростью 60–70 оС в сутки. Поэтому если производить останов турбины описанным ранее способом (как в резерв), то потребовалось бы 6–7 суток для естественного остывания турбины до допустимой температуры, позволяющей приступить к выполнению ремонт- ных работ. Для сокращения времени простоя турбоагрегатов в капитальном и среднем ремонтах останов может проводиться с предварительным расхолаживанием металла турбины.
Существуют различные способы принудительного расхола- живания: воздушный низкопотенциальным паром, разгружени- ем турбины при скользящих параметрах пара и комбинирован- ный. При использовании любого из этих способов соблюдаются обязательные требования: скорость охлаждения металла турби- ны, разность температур по ширине корпусных деталей, относи- тельное укорочение роторов, температура металла выхлопных патрубков ЦНД не должны превышать предельных допустимых значений. При этом температура свежего пара, подаваемого на турбину, должна быть всегда выше температуры насыщения при данном давлении не менее чем на 50оС. Расхолаживание влаж- ным паром недопустимо из-за резкого, скачкообразного увели- чения коэффициента теплоотдачи, что может служить причиной появления обратного теплового удара, то есть резкого захола- живания цилиндров турбины [1].
Расхолаживание турбоагрегатов блочных ТЭС с барабанны- ми котлами без промежуточного перегрева пара проводится при открытых регулирующих клапанах на скользящем давлении при плавном снижении температуры пара до 260–280°C. Дальней- шее расхолаживание достигается за счет прикрытия регулиру- ющих клапанов со снижением нагрузки до величины техниче-
346
ского минимума при постоянном давлении свежего пара около 2–3 МПа , поддерживаемом подключением пуско-сбросного устройства (БРОУ) на паровой коллектор собственных нужд. Для упрощения операций технология ориентирована на измене- ние на каждом этапе расхолаживания лишь одного из регулиру- емых параметров (нагрузки, давления, температуры свежего па- ра, положения регулирующих клапанов) [47]. При этом все рас- сматриваемые выше предварительные операции по останову турбоагрегатов блочной ТЭС остаются прежними.
Для турбоагрегатов неблочных ТЭС, работающих во всём диапазоне нагрузок на номинальных параметрах свежего пара, расхолаживание турбин осуществляется низкопотенциальным паром от коллектора собственных нужд давлением 1,0–1,5 МПа. Соответствующая схема расхолаживания представлена на рис. 4.9.
Расхолаживание турбины производится следующим образом [26]. После предварительной разгрузки турбоагрегата до 5–20 % от номинальной мощности (уточняется программой и графиком расхолаживания) подачу пара на турбину организуют через сме- ситель 4, установленный на байпасе главной паровой задвижки 1, после чего ГПЗ закрывают. Далее расхолаживают турбину за счёт увеличивающегося количества пара, подаваемого из кол- лектора промышленного отбора 7 в смеситель 4. После полного открытия задвижек на подаче пара промышленного отбора 7 в смеситель 4 дальнейшее снижение температуры охлаждающего пара осуществляется путём снижения подачи свежего пара в смеситель 4. На следующем этапе пар промышленного отбора, поступающий в турбину, охлаждается впрыском конденсата, поступающего с напора конденсатных насосов 5 в пароохлади- тель 6. Для удержания относительного сокращения ротора ЦВД в допустимых пределах в первую камеру концевого уплотнения ЦВД через задвижки 14 организуется подача свежего пара, а задвижка 15 закрывается. Представленная схема позволяет рас- холодить турбину до температуры 200 оС за 8 часов вместо 90 часов при естественном остывании.
347
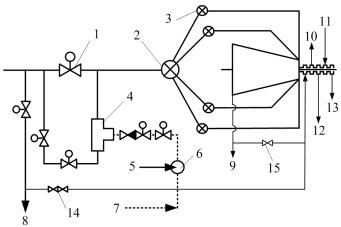
Рис. 4.9. Схема расхолаживания турбин неблочных ТЭС: 1 – глав-
ная паровая задвижка; 2, 3 – стопорный и регулирующие клапаны; 4 – смеситель; 5 – ввод конденсата с напора КЭН; 6 - пароохладитель; 7 – подача пара с коллектора давлением 1,0–15,0 кгс/см2; 8 – подвод све- жего пара к эжекторам конденсационной установки; 9, 10 – отводы пара в I регенеративный отбор; 11 – пар от парового коллектора соб- ственных нужд; 12, 13 – соответственно пар на подогреватель сальни- ковый и отсос паровоздушной смеси на охладитель концевых уплот- нений ротора турбины; 14 – задвижки подачи свежего пара на перед- нюю шейку ротора ЦВД; 15 – задвижка (при расхолаживании турбины закрывается)
Учитывая требования ПТЭ [9] к выполнению сложных пере- ключений в тепловых схемах, расхолаживание турбоагрегата должно осуществляться по заранее разработанной и утвержден- ной техническим руководителем программе, в которой должны быть предусмотрены ответственные лица, последовательность выполнения операций, очередность снятия защит и блокировок, возможные типовые аварийные ситуации, способы выхода из них и т.д.
348
4.4.5.5. Аварийный останов турбоагрегатов
Аварийный останов турбоагрегата может быть осуществлен от действия автоматической системы защиты или от воздей- ствия оперативного персонала на соответствующие органы управления (кнопку ручного останова, установленную непо- средственно на турбине; ключ дистанционного отключения тур- бины, установленный на ЦТЩУПТ и воздействующий на элек- тромагнитный выключатель).
В первом случае аварийный останов турбоагрегата осуществ- ляется системой автоматической защиты турбины при недопу- стимых отклонениях контролируемых параметров. При этом защита может срабатывать на отключение турбоагрегата мгно- венно или с некоторой задержкой времени, что сопровождается звуковой и световой технологической и аварийной сигнализаци- ей. Аварийных отключений турбоагрегата от действия системы автоматической защиты может быть столько, сколько задей- ствовано защит на конкретном турбоагрегате. Перечень сигна- лизаций, защит и блокировок, задействованных на турбоагрега- те, регламентируется «картой уставок срабатывания технологи- ческих защит и блокировок турбоагрегата». Такие карты согла- совываются с технологическим (турбинным) цехом, производ- ственно-техническим отделом, цехом ТАИ и утверждаются тех- ническим руководителем ТЭС. Технологические защиты, вве- денные в постоянную эксплуатацию, должны быть включены в течение всего времени работы оборудования, на котором они установлены. Вывод из работы исправных технологических за- щит не допускается. Защиты должны быть выведены из работы
вследующих случаях [9]:
–при работе оборудования в переходных режимах, когда необходимость отключения защиты определена инструкцией по эксплуатации основного оборудования;
–при очевидной неисправности защиты; отключение произ- водится по распоряжению начальника смены электростанции с обязательным уведомлением технического руководителя ТЭС и оформляется записью в оперативной документации; кроме того, отключение неисправных защит необходимо зафиксировать за-
349
писями в оперативных журналах цеха ТАИ и начальника смены турбинного цеха с указанием времени и причины отключения; такой жесткий порядок вывода технологических защит с обяза- тельным уведомлением технического руководителя ТЭС установ- лен для обеспечения быстрейшего устранения неисправностей;
–для периодического опробования, если оно производится на действующем оборудовании.
Во втором случае аварийное отключение турбоагрегата осу- ществляет непосредственно оперативный персонал. Причинами отключения могут быть:
–отказ в работе защит турбоагрегата при явном отклонении контролируемых параметров от предельных допустимых значений;
–при возникновении неисправностей на оборудовании паро- турбинной установки, угрожающих распространению аварии (разрывы маслопроводов и паропроводов; появление металличе- ских звуков и необычных шумов внутри турбины или турбоге- нератора; появление искр или дыма из подшипников и концевых уплотнений турбины или турбогенератора; возникновение круго- вого огня на контактных кольцах ротора турбогенератора и т.п.);
–при возникновении пожаров, угрожающих безопасности персонала и оборудования, и пожаров, которые нельзя ликвиди- ровать без останова турбоагрегата;
–во всех случаях, когда работа турбоагрегата угрожает жиз- ни персонала.
Аварийный останов турбоагрегата может осуществляться двумя способами: со срывом вакуума и без срыва вакуума.
Останов со срывом вакуума нежелателен по двум причинам: во-первых, из-за возникновения больших динамических нагру- зок на лопаточный аппарат ротора; во-вторых, из-за резкого охлаждения воздухом концевых уплотнений и шеек ротора. Ча- стое использование останова турбины со срывом вакуума при- водит к появлению микротрещин на рабочих лопатках роторов, втулках под концевые уплотнения роторов и т.п. Необходимость срыва вакуума при отключении турбины должна быть опреде- лена местной инструкцией в соответствии с указаниями завода- изготовителя. Выбор способа останова осуществляет оператив-
350