
- •Textbook Series
- •Contents
- •1 Overview and Definitions
- •Overview
- •General Definitions
- •Glossary
- •List of Symbols
- •Greek Symbols
- •Others
- •Self-assessment Questions
- •Answers
- •2 The Atmosphere
- •Introduction
- •The Physical Properties of Air
- •Static Pressure
- •Temperature
- •Air Density
- •International Standard Atmosphere (ISA)
- •Dynamic Pressure
- •Key Facts
- •Measuring Dynamic Pressure
- •Relationships between Airspeeds
- •Airspeed
- •Errors and Corrections
- •V Speeds
- •Summary
- •Questions
- •Answers
- •3 Basic Aerodynamic Theory
- •The Principle of Continuity
- •Bernoulli’s Theorem
- •Streamlines and the Streamtube
- •Summary
- •Questions
- •Answers
- •4 Subsonic Airflow
- •Aerofoil Terminology
- •Basics about Airflow
- •Two Dimensional Airflow
- •Summary
- •Questions
- •Answers
- •5 Lift
- •Aerodynamic Force Coefficient
- •The Basic Lift Equation
- •Review:
- •The Lift Curve
- •Interpretation of the Lift Curve
- •Density Altitude
- •Aerofoil Section Lift Characteristics
- •Introduction to Drag Characteristics
- •Lift/Drag Ratio
- •Effect of Aircraft Weight on Minimum Flight Speed
- •Condition of the Surface
- •Flight at High Lift Conditions
- •Three Dimensional Airflow
- •Wing Terminology
- •Wing Tip Vortices
- •Wake Turbulence: (Ref: AIC P 072/2010)
- •Ground Effect
- •Conclusion
- •Summary
- •Answers from page 77
- •Answers from page 78
- •Questions
- •Answers
- •6 Drag
- •Introduction
- •Parasite Drag
- •Induced Drag
- •Methods of Reducing Induced Drag
- •Effect of Lift on Parasite Drag
- •Aeroplane Total Drag
- •The Effect of Aircraft Gross Weight on Total Drag
- •The Effect of Altitude on Total Drag
- •The Effect of Configuration on Total Drag
- •Speed Stability
- •Power Required (Introduction)
- •Summary
- •Questions
- •Annex C
- •Answers
- •7 Stalling
- •Introduction
- •Cause of the Stall
- •The Lift Curve
- •Stall Recovery
- •Aircraft Behaviour Close to the Stall
- •Use of Flight Controls Close to the Stall
- •Stall Recognition
- •Stall Speed
- •Stall Warning
- •Artificial Stall Warning Devices
- •Basic Stall Requirements (EASA and FAR)
- •Wing Design Characteristics
- •The Effect of Aerofoil Section
- •The Effect of Wing Planform
- •Key Facts 1
- •Super Stall (Deep Stall)
- •Factors that Affect Stall Speed
- •1g Stall Speed
- •Effect of Weight Change on Stall Speed
- •Composition and Resolution of Forces
- •Using Trigonometry to Resolve Forces
- •Lift Increase in a Level Turn
- •Effect of Load Factor on Stall Speed
- •Effect of High Lift Devices on Stall Speed
- •Effect of CG Position on Stall Speed
- •Effect of Landing Gear on the Stall Speed
- •Effect of Engine Power on Stall Speed
- •Effect of Mach Number (Compressibility) on Stall Speed
- •Effect of Wing Contamination on Stall Speed
- •Warning to the Pilot of Icing-induced Stalls
- •Stabilizer Stall Due to Ice
- •Effect of Heavy Rain on Stall Speed
- •Stall and Recovery Characteristics of Canards
- •Spinning
- •Primary Causes of a Spin
- •Phases of a Spin
- •The Effect of Mass and Balance on Spins
- •Spin Recovery
- •Special Phenomena of Stall
- •High Speed Buffet (Shock Stall)
- •Answers to Questions on Page 173
- •Key Facts 2
- •Questions
- •Key Facts 1 (Completed)
- •Key Facts 2 (Completed)
- •Answers
- •8 High Lift Devices
- •Purpose of High Lift Devices
- •Take-off and Landing Speeds
- •Augmentation
- •Flaps
- •Trailing Edge Flaps
- •Plain Flap
- •Split Flap
- •Slotted and Multiple Slotted Flaps
- •The Fowler Flap
- •Comparison of Trailing Edge Flaps
- •and Stalling Angle
- •Drag
- •Lift / Drag Ratio
- •Pitching Moment
- •Centre of Pressure Movement
- •Change of Downwash
- •Overall Pitch Change
- •Aircraft Attitude with Flaps Lowered
- •Leading Edge High Lift Devices
- •Leading Edge Flaps
- •Effect of Leading Edge Flaps on Lift
- •Leading Edge Slots
- •Leading Edge Slat
- •Automatic Slots
- •Disadvantages of the Slot
- •Drag and Pitching Moment of Leading Edge Devices
- •Trailing Edge Plus Leading Edge Devices
- •Sequence of Operation
- •Asymmetry of High Lift Devices
- •Flap Load Relief System
- •Choice of Flap Setting for Take-off, Climb and Landing
- •Management of High Lift Devices
- •Flap Extension Prior to Landing
- •Questions
- •Annexes
- •Answers
- •9 Airframe Contamination
- •Introduction
- •Types of Contamination
- •Effect of Frost and Ice on the Aircraft
- •Effect on Instruments
- •Effect on Controls
- •Water Contamination
- •Airframe Aging
- •Questions
- •Answers
- •10 Stability and Control
- •Introduction
- •Static Stability
- •Aeroplane Reference Axes
- •Static Longitudinal Stability
- •Neutral Point
- •Static Margin
- •Trim and Controllability
- •Key Facts 1
- •Graphic Presentation of Static Longitudinal Stability
- •Contribution of the Component Surfaces
- •Power-off Stability
- •Effect of CG Position
- •Power Effects
- •High Lift Devices
- •Control Force Stability
- •Manoeuvre Stability
- •Stick Force Per ‘g’
- •Tailoring Control Forces
- •Longitudinal Control
- •Manoeuvring Control Requirement
- •Take-off Control Requirement
- •Landing Control Requirement
- •Dynamic Stability
- •Longitudinal Dynamic Stability
- •Long Period Oscillation (Phugoid)
- •Short Period Oscillation
- •Directional Stability and Control
- •Sideslip Angle
- •Static Directional Stability
- •Contribution of the Aeroplane Components.
- •Lateral Stability and Control
- •Static Lateral Stability
- •Contribution of the Aeroplane Components
- •Lateral Dynamic Effects
- •Spiral Divergence
- •Dutch Roll
- •Pilot Induced Oscillation (PIO)
- •High Mach Numbers
- •Mach Trim
- •Key Facts 2
- •Summary
- •Questions
- •Key Facts 1 (Completed)
- •Key Facts 2 (Completed)
- •Answers
- •11 Controls
- •Introduction
- •Hinge Moments
- •Control Balancing
- •Mass Balance
- •Longitudinal Control
- •Lateral Control
- •Speed Brakes
- •Directional Control
- •Secondary Effects of Controls
- •Trimming
- •Questions
- •Answers
- •12 Flight Mechanics
- •Introduction
- •Straight Horizontal Steady Flight
- •Tailplane and Elevator
- •Balance of Forces
- •Straight Steady Climb
- •Climb Angle
- •Effect of Weight, Altitude and Temperature.
- •Power-on Descent
- •Emergency Descent
- •Glide
- •Rate of Descent in the Glide
- •Turning
- •Flight with Asymmetric Thrust
- •Summary of Minimum Control Speeds
- •Questions
- •Answers
- •13 High Speed Flight
- •Introduction
- •Speed of Sound
- •Mach Number
- •Effect on Mach Number of Climbing at a Constant IAS
- •Variation of TAS with Altitude at a Constant Mach Number
- •Influence of Temperature on Mach Number at a Constant Flight Level and IAS
- •Subdivisions of Aerodynamic Flow
- •Propagation of Pressure Waves
- •Normal Shock Waves
- •Critical Mach Number
- •Pressure Distribution at Transonic Mach Numbers
- •Properties of a Normal Shock Wave
- •Oblique Shock Waves
- •Effects of Shock Wave Formation
- •Buffet
- •Factors Which Affect the Buffet Boundaries
- •The Buffet Margin
- •Use of the Buffet Onset Chart
- •Delaying or Reducing the Effects of Compressibility
- •Aerodynamic Heating
- •Mach Angle
- •Mach Cone
- •Area (Zone) of Influence
- •Bow Wave
- •Expansion Waves
- •Sonic Bang
- •Methods of Improving Control at Transonic Speeds
- •Questions
- •Answers
- •14 Limitations
- •Operating Limit Speeds
- •Loads and Safety Factors
- •Loads on the Structure
- •Load Factor
- •Boundary
- •Design Manoeuvring Speed, V
- •Effect of Altitude on V
- •Effect of Aircraft Weight on V
- •Design Cruising Speed V
- •Design Dive Speed V
- •Negative Load Factors
- •The Negative Stall
- •Manoeuvre Boundaries
- •Operational Speed Limits
- •Gust Loads
- •Effect of a Vertical Gust on the Load Factor
- •Effect of the Gust on Stalling
- •Operational Rough-air Speed (V
- •Landing Gear Speed Limitations
- •Flap Speed Limit
- •Aeroelasticity (Aeroelastic Coupling)
- •Flutter
- •Control Surface Flutter
- •Aileron Reversal
- •Questions
- •Answers
- •15 Windshear
- •Introduction (Ref: AIC 84/2008)
- •Microburst
- •Windshear Encounter during Approach
- •Effects of Windshear
- •“Typical” Recovery from Windshear
- •Windshear Reporting
- •Visual Clues
- •Conclusions
- •Questions
- •Answers
- •16 Propellers
- •Introduction
- •Definitions
- •Aerodynamic Forces on the Propeller
- •Thrust
- •Centrifugal Twisting Moment (CTM)
- •Propeller Efficiency
- •Variable Pitch Propellers
- •Power Absorption
- •Moments and Forces Generated by a Propeller
- •Effect of Atmospheric Conditions
- •Questions
- •Answers
- •17 Revision Questions
- •Questions
- •Answers
- •Explanations to Specimen Questions
- •Specimen Examination Paper
- •Answers to Specimen Exam Paper
- •Explanations to Specimen Exam Paper
- •18 Index

Controls 11
Control Balancing
The aerodynamic force on the controls will depend on the area of the control surface, its angular displacement and the IAS. For large and fast aircraft the resulting aerodynamic force can give hinge moments / stick forces which are too high for easy operation of the controls.
The pilot will require assistance to move the controls in these conditions, and this can be done either by using (hydraulic) powered flying controls or by using some form of aerodynamic balance.
Aerodynamic Balance
Aerodynamic balance involves using the aerodynamic forces on the control surface to reduce the hinge moment / stick force and may be done in several ways:
HINGE SET - BACK |
|
INTO SURFACE |
F2 |
|
|
d |
|
Figure 11.5 Inset hinge
Inset Hinge
If the distance (d) is reduced, the hinge moment will be reduced. The smaller the hinge moment, the smaller the stick force and the easier it will be for the pilot to move the controls. Setting the hinge back does not reduce the effectiveness of the control, only the hinge moment.
If the aerodynamic force (F2) were to move forward of the hinge, a condition known as “overbalance” would exist. As the force moved forward, a reduction then a reversal of the stick force would occur. This would be very dangerous and the designer must ensure the aerodynamic force can never move forward of the hinge.
AEROFOIL |
HINGE |
LINE |
|
|
CONTROL |
HORN |
SURFACE |
|
Figure 11.6 Horn balance
Horn Balance
The principle of the horn balance is similar to that of the inset hinge, in that part of the surface is forward of the hinge line, and forces on this part of the surface give hinge moments which are in the opposite direction to the moments on the main part of the surface. The overall moment is therefore reduced, but the control effectiveness is not.
Controls 11
335
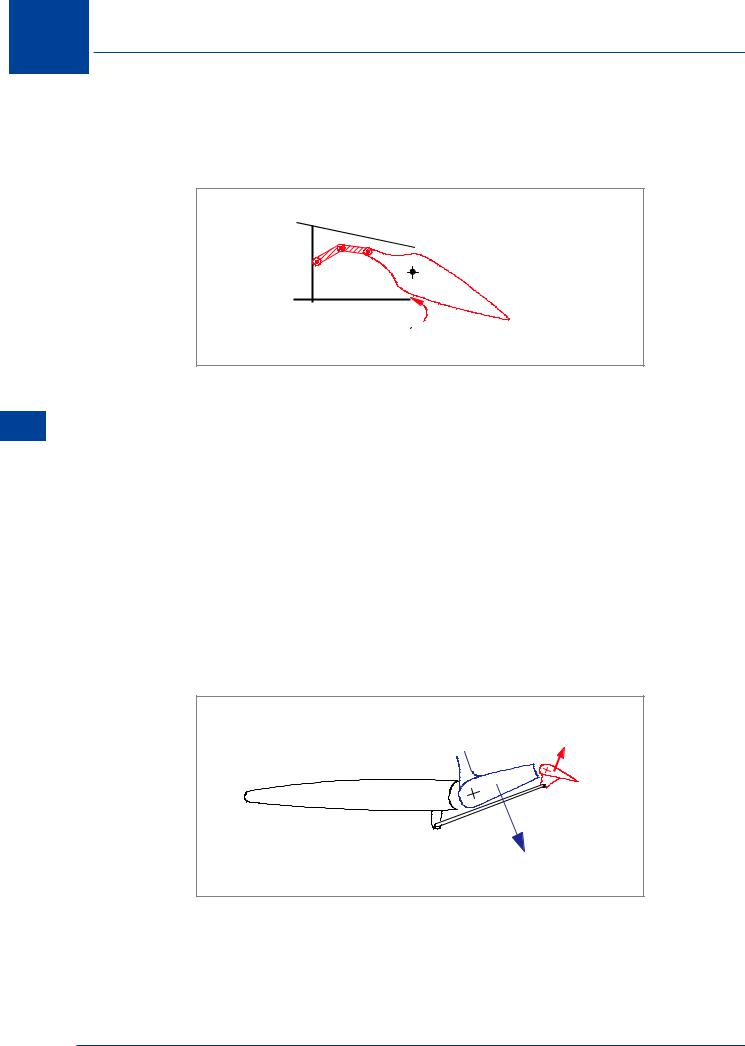
11 Controls
Internal Balance
Controls 11
This balance works on the same principle as the inset hinge, but the aerodynamic balance area is inside the wing.
LOW PRESSURE
HIGH
PRESSURE
Figure 11.7 Internal balance
Movement of the control causes pressure changes on the aerofoil, and these pressure changes are felt on the balance area. For example, if the control surface is moved down, pressure above the aerofoil is reduced and pressure below it is increased. The reduced pressure is felt on the upper surface of the balance ‘panel’, and the increased pressure on the lower surface. The pressure difference on the balance therefore gives a hinge moment which is the opposite to the hinge moment on the main control surface, and the overall hinge moment is reduced.
See page 354 for a Tab Quick Reference Guide.
Balance Tab
The preceding types of aerodynamic balance work by causing some of the dynamic pressure on the control surface to act forward of the hinge line. The balance tab provides a force acting on the control surface trailing edge opposite to the force on the main control surface. The balance tab moves in the opposite direction to the control surface. The pilot moves the surface, the surface moves the tab.
TAB
FORCE
PILOT INPUT
CONTROL
FORCE
Figure 11.8 Balance tab
Unlike the previous types of balance, the balance tab will give some reduction in control effectiveness, as the tab force is opposite to the control force.
336

Controls 11
Anti-balance Tab
The anti-balance tab moves in the same direction as the control surface and increases control effectiveness, but it will increase the hinge moment and give heavier stick forces. The pilot moves the surface, the surface moves the tab.
PILOT INPUT
TAB
FORCE
CONTROL
FORCE
Figure 11.9 Anti-balance tab
Servo Tab
Pilot control input deflects the servo tab only; the aerodynamic force on the tab then moves the control surface until an equilibrium position is reached. If external control locks are fitted to the control surface on the ground, the cockpit control will still be free to move; therefore, you must physically check any central locks have been removed before flight. Older types of high speed jet transport aircraft (B707) successfully used servo tab controls. The disadvantage of the servo tab is reduced control effectiveness at low IAS.
PILOT INPUT |
CONTROL "HORN" FREE TO |
|
PIVOT ON HINGE AXIS |
Figure 11.10 Servo tab
Spring Tab
The spring tab is a modification of the servo tab, such that tab movement is proportional to the applied stick force. Maximum tab assistance is obtained at high speed when the stick forces are greatest. High dynamic pressure will prevent the surface from moving, so the spring is compressed by the pilot input and the tab moves the surface. The spring is not compressed at low IAS, so the pilot input deflects the control surface and the tab, increasing the surface area and control effectiveness at low speed.
HORN FREE TO |
PIVOT ON HINGE AXIS |
PILOT INPUT |
SPRING |
Figure 11.11 Spring tab
Controls 11
337

11 Controls
Controls 11
(Hydraulic) Powered Flying Controls
If the required assistance for the pilot to move the controls cannot be provided by the preceding types of aerodynamic balance, then power assisted or fully powered controls have to be used.
POWER FLYING
CONTROL UNIT (PFCU)
SERVO
VALVE
Figure 11.12 Power assisted flying control
Power Assisted Controls
With a power assisted flying control, Figure 11.12, only a certain proportion of the force required to oppose the hinge moment is provided by the pilot; the hydraulic system provides most of the force. Although the pilot does not have to provide all the force required, the natural ‘feel’ of the controls is retained and the stick force increases as the square of the IAS, just as in a completely manual control.
POWER FLYING
CONTROL UNIT (PFCU)
SERVO
VALVE
Figure 11.13 Fully powered flying control
338

Controls 11
Fully Powered Controls
For bigger and/or faster aircraft, hinge moments are so large that fully powered controls must be used. In a fully powered control system, none of the force to move the control surface is supplied by the pilot. The only force the pilot supplies is that required to overcome system friction and to move the servo valve; all the necessary power to move the control surface is supplied by the aircraft’s hydraulic system.
Figure 11.13 shows that movement of the servo valve to the left allows hydraulic fluid to enter the left chamber of the PFCU. The body of the unit will move to the left, its movement being transferred to the control surface. As soon as the PFCU body reaches the position into which the pilot placed the servo valve, the PFCU body, and hence the control surface, stops moving. The unit is now locked in its new position by “incompressible” liquid trapped on both sides of the piston and will remain in that position until the servo valve is again moved by the pilot. Aerodynamic loads on the control surface are unable to move the cockpit controls, so powered flying controls are known as “irreversible” controls.
Artificial Feel (‘Q’ Feel)
POWER FLYING
CONTROL UNIT (PFCU)
STATIC |
|
PITOT |
SERVO |
|
|
|
VALVE |
ARTIFICIAL FEEL UNIT ( 'Q ' FEEL )
Figure 11.14 Artificial feel (‘Q’ feel)
With a fully powered flying control the pilot is unaware of the aerodynamic force on the controls, so it is necessary to incorporate “artificial” feel to prevent the aircraft from being overstressed. As shown schematically in Figure 11.14, a device sensitive to dynamic pressure (½ ρ V2) or ‘Q’ is used.
Pitot pressure is fed to one side of a chamber and static pressure to the other, which moves a diaphragm under the influence of changing dynamic pressure with airspeed and causes “regulated” hydraulic pressure to provide a resistance or ‘feel’ on the pilot’s input controls proportional to IAS2, just as in a manual control. In addition, stick force should increase as stick displacement increases.
Controls 11
339