
Measurement and Control Basics 3rd Edition (complete book)
.pdf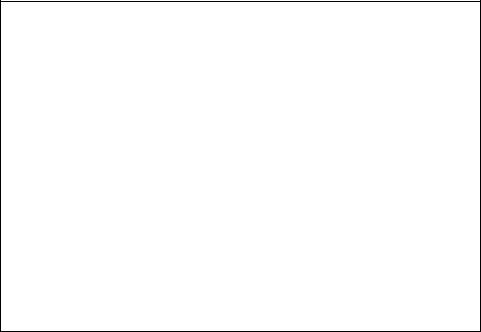
Chapter 8 – Analytical Measurement and Control |
225 |
EXAMPLE 8-7
Problem: Find the intensity of a 100-w point source at 1 meter and 2 meters from the source.
Solution: The intensity at 1 meter from the source is as follows:
|
I = |
|
P |
|
|
4π r 2 |
|||
|
|
|||
I = |
100w |
|
= 7.96w / m2 |
|
|
|
|||
4π (1m)2 |
|
|
The intensity at 2 meters from the source is
I = |
100w |
=1.989w / m2 |
|
4π (2m)2 |
|||
|
|
Photoconductive Sensor
A common type of photodetector is based on the change in conductivity that occurs in a semiconductor material with radiation intensity. Since resistance is the inverse of conductivity, these devices are also called photoresistive cells.
A semiconductor is a material in which there is an energy gap between conduction electrons and valence electrons. In the semiconductor-based photoconductive sensor, a photon is absorbed and in turn excites an electron from the valence to the conduction band. When a large number of electrons are excited into the conduction band, the semiconductor resistance decreases, which makes the resistance an inverse function of radiation intensity. For the photon to make such an excitation it must carry at least as much energy as the gap. From Equation 8-17, this implies a maximum wavelength as follows:
Ep = |
hc |
|
= ∆ |
(8-20) |
|
λ |
|
Eg |
|||
λ max = |
|
hc |
|
(8-21) |
|
|
|
|
|||
|
∆ Eg |
where
λ max = the maximum detectable radiation wavelength in meters

226 |
Measurement and Control Basics |
||
|
∆ Eg |
= the semiconductor energy gap in joules |
|
|
h |
= |
Planck’s constant in joule-s |
|
c |
= |
the speed of light in m/s |
It is important to note that any radiation with a wavelength greater than that predicated by Equation 8-21 cannot cause any resistance change in the semiconductor.
Example 8-8 shows how to find the maximum wavelength for resistance change by photon absorption for a semiconductor.
EXAMPLE 8-8
Problem: The semiconductor material germanium has a band gap of
1.072 x 10–19 joules. Find the maximum wavelength for resistance change by photon absorption.
Solution: Using Equation 8-21, we find the maximum wavelength as follows:
λ max = |
hc |
∆ Eg |
λ max = (6.63x10−34 J − s)(3x108 m / s)
λ max =1.86µ m
The two most common photoconductive semiconductor materials are cadmium sulfide (CdS), which has an energy band gap of 2.42 eV, and cadmium selenide (CdSe), which has a 1.74 eV band gap. Note that one electron volt (eV) is equal to 1.6 x 10-19 joules of energy. Because of the large gap energy for both semiconductors, they have a very high resistivity at room temperatures. This gives bulk samples of these semiconductors a resistance much too high for practical applications. To compensate for this, a special construction is used, as shown in Figure 8-14, that minimizes resistance while providing maximum surface area for the detector. This photodetector construction is based the equation for resistance discussed earlier:
R = |
ρ l |
(8-22) |
|
A

Chapter 8 – Analytical Measurement and Control |
227 |
where
R |
= the resistance in ohms |
ρ= resistivity in ohm-m
l |
= |
length in meters |
A |
= |
the cross-sectional area in meters squared. |
A side view of the photoconductive cell is shown in Figure 8-14a. This arrangement produces a minimum length, l, and a maximum area, A, to produce a low resistance value according to Equation 8-22. The area of photoconductive material is the length of the material times its thickness. By using a thin narrow strip of material and by winding the material back and forth as in the front view shown in Figure 8-14b, we obtain the maximum surface area to detect photons.
A = length x thickness
Conductors
l
Photoconductive
Material
a) Side view of photoconductive cell
Photoconductive
Material
b) Top view of photoconductive cell
Figure 8-14. Photoconductive cell
A photoconductive cell resistance decreases nonlinearly with increases in radiation intensity, like a thermistor. Generally, this change in resistance is several hundred orders of magnitude from dark to normal daylight.
If you need an accurate measurement of intensity, you can use calibration methods that have a standard resistance-measuring circuit. You can obtain sensitive control about ambient radiation intensity by using the photoconductive cell in a Wheatstone bridge circuit that has been adjusted for null

228 Measurement and Control Basics
current at the ambient radiation level. You would use operational amplifier circuits to convert the resistance change of the cell into a current of voltage change in measurement applications.
Photovoltaic Sensors
An important type of photodetector is the photovoltaic cell, which generates a voltage that is proportional to the incident EM radiation intensity. These sensors are called photovoltaic cells because of their voltage-gener- ating capacity, but the cells actually convert EM energy into electrical energy. Photovoltaic cells are very important in instrumentation and control applications because they are used both as light detectors and in power sources that convert solar radiation into electrical power for remote-measuring systems. Our emphasis here is on their use in analytical instruments.
The operating principle of the photovoltaic cell is illustrated in Figure 8-15. The cell is a large exposed diode that is constructed using a pn junction between appropriately doped semiconductors. Photons hitting the cell pass through the thin p-doped upper and are absorbed by electrons in the n-doped layer. This causes conduction electrons and holes to be created.
Incident radiation
Top conductor plate |
p-doped |
semiconductor
pn junction
n-doped
semiconductor
Vout
Bottom conductor plate
Figure 8-15. Photovoltaic cell
The upper terminal is positive and the lower negative. In general, the open-circuit voltage V that is developed on a photovoltaic cell varies logarithmically with the incident radiation intensity according to the following equation:
V= Voln(IR) |
(8-23) |
Chapter 8 – Analytical Measurement and Control |
229 |
where |
|
|
I |
= the radiation intensity in W/m2 |
|
R |
|
|
Vo |
= |
the calibration voltage in volts |
V |
= |
the unloaded output voltage in volts |
Photovoltaic cells have a low internal resistance, so when they are connected to a measurement circuit that has some load resistance, the cell voltage is reduced from the value indicated by Equation 8-23. Since the internal resistance, Ri, is in series with the load resistance, RL, the actual current, I, that is delivered to a load is given by the following:
I = |
|
V |
(8-24) |
|
Ri |
+ RL |
|||
|
|
The cell calibration voltage Vo is a function of the cell material only, and this indicates that the voltage produced is independent of the cell geometry. The current that is produced by a photovoltaic depends on the radiation intensity and also the cell surface area. Cells are generally arranged in series and parallel combinations to obtain the desired voltage and current output.
Example 8-9 illustrates how to calculate the internal resistance and the open-circuit voltage for a typical photovoltaic cell.
Photomultiplier Tube
The photomultiplier tube is one of the most sensitive photodetectors available for use in analytical instruments. Figure 8-16 shows the basic structure of the photomultiplier tube. It consists of a photoemissive cathode and an anode separated by electrodes called dynodes.
The cathode is maintained at a high negative voltage and is coated with a photoemissive material. Numerous dynodes maintained at successively more positive voltages follow the cathode. The final electrode is the anode, which is grounded through a resistor R. When a light photon strikes the photoemissive cathode with sufficient energy, several electrons are ejected from the surface, and the voltage potential difference accelerates them to the first dynode. Each electron from the cathode that strikes the first dynode ejects several electrons. All of these electrons are accelerated to the second dynode where each one strikes the surface with sufficient energy to again eject several electrons. This process is repeated for each dynode until the electrons that reach the anode have greatly multiplied and they produce a large current flow through the output resistor. The voltage pro-

230 Measurement and Control Basics
EXAMPLE 8-9
Problem: A photovoltaic cell generates 0.4 volts open-circuit when exposed to 20 W/m2 of radiation intensity. A current of 2 mA is delivered into a 100 Ω at that intensity. Calculate (a) the internal resistance of the cell and (b) the opencircuit voltage at 50 W/m2.
Solution:
a. Using Equation 8-24, we can calculate the internal cell resistance as follows:
I = |
|
V |
|
Ri |
+ RL |
||
|
Solving for internal resistance, we obtain
Ri = V − IRL
I
Ri = 0.4V − (2mA)(100Ω ) =100Ω 2mA
b. To find the open-circuit voltage at 50 W/m2, we use Equation 8-23 to first calculate Vo, as follows:
Vo = V ln(I R )
Vo = 0.4volts = 0.134volts
ln 20
So that at 50 W/m2, we obtain
V = (0.134 volts)ln(50)
V = 0.524 volts
duced across the output resistor R is directly proportional to the light striking the cathode.
The number of dynodes and material from which they are constructed determines the gain of the photomultiplier tube detector. Typical gains are in the range of 105 to 107 for photoelectrons from the cathode to electrons

Chapter 8 – Analytical Measurement and Control |
231 |
Dynodes (typical) |
|
|
|
|
Glass tube |
|
|
Incident Light |
Anode |
|
|
Vout |
-V |
Photo |
|
cathode |
|
R |
|
|
|
|
Figure 8-16. Photomultiplier tube
at the anode. The spectral response of a phototube is determined by two factors: the spectral response of the cathode photoemissive coating material and the transparency of the window through which the light must pass. By using various materials it is possible to construct different types of photomultipliers, which span wavelengths from 0.12 m to 0.95 m.
Turbidity Analyzer
A typical application for photodetectors in analytical measurement is as a turbidity analyzer. The cloudiness of a liquid, called turbidity, is caused by the presence of finely divided suspended material. Turbidimetric methods involve measuring the light transmitted through a medium.
Turbidity can be caused by a single substance or by a combination of several chemical components. For example, the amount of silica in a liquid may be determined in approximate concentrations of 0.1 to 150 ppm of SiO2. Sometimes composite material turbidities are expressed as being equivalent to silica.
In the typical application shown in Figure 8-17, a turbidity value is developed from a test sample under controlled conditions. In this application, a laser beam is split and passed through two mediums to matched photodetectors. One medium is a carefully selected standard sample of fixed turbidity. The other medium is an in-line process liquid. If the in-line process liquid attenuates the laser beam more than the standard or reference sample, the electronic circuit triggers an alarm or takes some appropriate control action to reduce turbidity.


Chapter 8 – Analytical Measurement and Control |
233 |
Light
Source
Signal Out
Proportional to
Particle Density
Light
Detector
Process stack
Air Flow
Figure 8-18. Particulate stack monitor
tion signals. Ranges are typically from 0 to 10 percent and 0 to 30 percent. Air is used as a reference, and oxygen standards are used for calibration.
Some oxygen analyzers exhibit thermal sensitivity and are usually operated at elevated temperatures for stability. It is advantageous to have sample extraction versions when stack temperatures are low because the cells can be installed in ovens outside the stacks.
Paramagnetic gas sensors were among the earliest oxygen detectors. Analyzers can be specified for ranges from 0 to 1 percent and 0 to 100 percent. The instruments respond to the magnetic susceptibility of the sample. The susceptibility of oxygen is two orders of magnitude greater than that of most other stack constituents, so the accuracy of these sensors is high.
Combustibles
Combustible gases and vapors are detected by measuring the thermal properties of samples. Catalytic bead devices, the most common form of measuring equipment, have both active and inactive filaments arranged in bridge circuits. As gas contacts the catalytically treated filaments, combustible materials diffuse into the surfaces and are oxidized. The heat of reaction raises the temperature, inducing resistance differences. You can also detect flammable gases or vapors by mixing samples with hydrogen and burning the product. The concentration of combustibles in the sample is inferred from flame temperature. Combustibles are usually monitored for explosion hazards, so outputs are calibrated to read in terms of percent of lower explosive limit (LEL).
234 Measurement and Control Basics
Hydrocarbon Analyzers
Analyzers that determine the total number of hydrocarbons are used for pollution monitoring and control programs, particularly for automobile exhausts and fossil-fueled stationary combustion facilities. They are also used to detect leaks in refrigerant systems and aerosol packaging as well as to detect breakthroughs from carbon adsorption beds.
Flame ionization detectors (FIDs) are often employed to measure total hydrocarbon concentrations in ranges from 0 to 1 ppm and 0 to 12,000 ppm. The samples are mixed with hydrogen and burned. Electrodes around the flames sense the carbon ions released during the combustion. FIDs typically have response times of less than 10 s. FIDs also have good sensitivity, with concentrations as low as 0.01 ppm. Infrared analyzers can be used for selected hydrocarbons, but they cannot measure total hydrocarbon concentrations.
Carbon Monoxide Analyzers
Carbon monoxide (CO) is measured in chemical, gas processing, metallurgical, and many other types of manufacturing facilities. CO analyzers, the measuring instruments for this application, can also be found in sewers, mines, bus terminals, and garages. Likewise, CO monitors are used to control ventilating equipment in vehicular tunnels. The standard threshold limit for CO is 50 ppm. CO monitors will normally trigger audible and visible alarms at 50 ppm or higher.
Many instruments are available for sensing carbon dioxide. One CO detector cell operates on the principle of catalytic oxidation. In the cell, the gas sample passes through an inactive chemical bed and then through an active catalytic bed. This catalytic bed, which consists of a mixture of oxides of copper, cobalt, manganese, and silver, is used to convert carbon monoxide to carbon dioxide. Each bed has a thermistor that is connected to a Wheatstone bridge circuit. Any CO gas present is immediately oxidized in the catalytic half of the sensor. This raises the temperature of the catalytic thermistor and changes its electrical resistance. This in turn causes a resistance imbalance in the bridge circuit and thus a signal that is proportional to the CO gas concentration in the sample.
In another type of CO measurement system, the sensor has an electronic interface circuit and an electrochemical polarographic cell that contains a sulfuric acid electrolyte. Air samples diffuse through a gas-porous membrane and a sintered metal disk and enter a sample area within the cell.
The cell electro-oxidizes CO gas to carbon dioxide (CO2) gas in proportion to the partial pressure of CO in the sample. The oxidation generates an