
Колбасников Н.Г. - Физические основы прочности и пластичности металлов (2004)
.pdf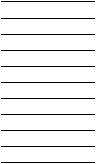


множестве присутствуют в литом материале. Для их устранения было решено использовать кристаллизацию сплава под давлением. Расплавленный металл с температурой 1150÷1180 °С
был залит в закрытую матрицу, нагретую до температуры 750 °С, и после образования поверхностной корочки был сжат пуансоном до давления 400 МПа, которое поддерживалось постоянным в течение в течение 3÷4 минут. Полученные после кристаллизации слитки диа-
метром 36 мм и длиной 100 мм имели размер зерна 1÷3 мм, а видимые литейные дефекты отсутствовали. Из этих слитков были приготовлены плоские образцы 20×32×80 мм, которые прокатывали при указанных выше режимах деформации.
Рис. 9.25. Поверхность разрушения бронзы после прокатки при температурах: а − T = 580°С; б − T = 650°С
|
1800 |
|
|
|
|
|
|
|
|
|
|
|
|
|
|
|
|
1638 |
|
|
|
|
|
|
1600 |
|
|
|
|
|
|
|
|
|
|
|
|
Liquid |
|
|
|
|
|
|
|
|
1455 |
|
1400 |
|
|
|
|
1395 |
|
|
|
|
|
|
|
|
|
|
|
|
|
1385 |
|
||
(C) |
|
|
|
|
|
|
|
|
|
|
|
1200 |
|
|
|
1133 |
AlNi |
|
|
|
|
|
|
Temperature |
|
|
|
|
|
|
|
|
|
||
|
|
|
|
|
|
|
|
|
Ni |
||
|
|
|
|
|
|
|
|
|
|
||
1000 |
|
|
|
|
|
|
|
|
|
|
|
|
|
|
854 |
|
|
|
|
|
|
|
|
800 |
|
|
|
|
|
|
|
|
|
|
|
|
|
|
|
|
|
700 |
|
|
|
||
|
660 |
633,9 |
|
|
|
|
|
|
|
||
|
|
|
|
|
|
|
|
|
|
|
|
|
600 |
|
Ni |
|
2 |
|
|
|
AlNi3 |
|
|
|
Al |
|
|
Ni |
|
|
|
|
|||
|
|
|
|
|
|
|
|
|
|||
|
|
3 |
|
3 |
|
|
|
|
|
|
|
|
400 |
|
Al |
|
Al |
|
|
|
|
|
|
|
|
|
|
|
|
|
|
|
|
|
|
|
0 |
10 |
20 |
30 |
40 |
50 |
60 |
70 |
80 |
90 |
100 |
|
Al |
|
|
|
Atomic Percent Ni |
|
|
|
Ni |
Рис. 9.26. Диаграмма состояния системы Ai-Ni
Применение кристаллизации под давлением не устранило хрупкости металла, а разрушение происходило таким же образом, как и для металла, разлитого в кокили при атмосферном давлении. Исследование структуры деформированного после кристаллизации под давлением металла позволило выявить одну из причин интеркристаллитного разрушения при температурах выше 650 °С: при действии давления во время кристаллизации на границах зе232
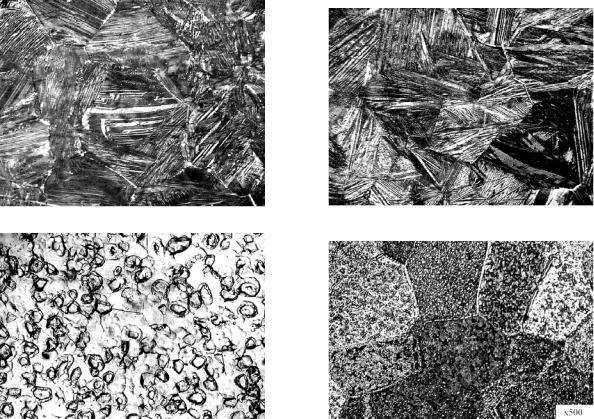
2.Поликристаллическая бронза, полученная прокаткой, при одинаковом составе с монокристаллической имеет значительно более высокие температуры мартенситного превращения, которые зависят от условий пластической деформации и окончательной термообработки. Например, бронза с содержанием алюминия 14 мас.% имеет температуру начала мартенситного превращения Ms≈–80°C в монокристаллическом и Ms≈50°C в поликристаллическом состоянии.
3.Размер зерна исходной аустенитной фазы в зависимости от температуры окончательной термической обработки представлен в табл. 9.3. Видно, что вплоть до температуры перехода в однофазную область (Т>560°C) размер зерна изменяется незначительно.
а) |
б) |
в) |
г) |
Рис. 9.27. Структура поликристаллической бронзы Cu-Al-Ni: а − после прокатки (×200), б − после окончательной закалки при температуре: 750°С (×500) - для состава Cu-14%Al-4%Ni; 4 − 650°С (×1000); 5 − 750°C
(×500) - для состава Cu-14,2%Al-4%Ni после прокатки в чехлах.
4. Мартенсит в поликристаллической бронзе чрезвычайно стабилен термически: нагрев и выдержка в течение 30 минут при температурах 200, 300, 400 °С не приводит к распаду мар-
тенсита. Распад мартенсита становится заметным при температуре выше 500 °С.
5. В горячедеформированных при температуре 600÷640 °С образцах присутствуют час-
тицы второй фазы серого цвета размером 3÷5 мкм. Их размер и количество зависит, в основном, от длительности выдержки при указанных температурах. На фоне этих частиц присут-
ствует мартенсит. При температуре окончательной термической обработки 750 °С и выше
236
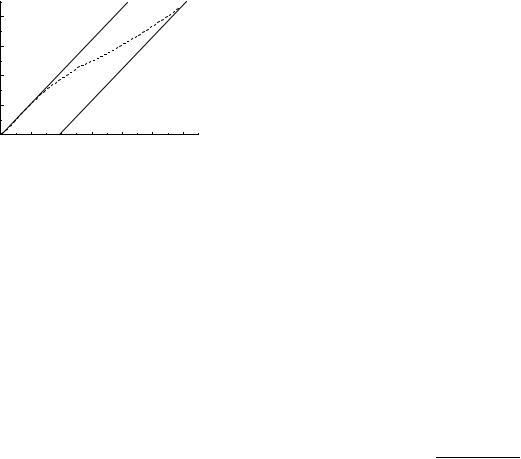
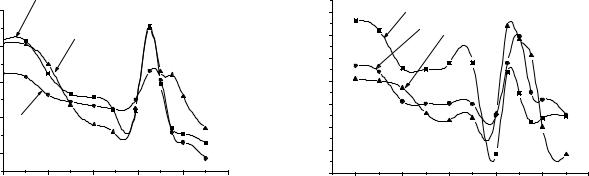