
Tema_5_ofsetnaya_pechat
.pdfРис. 2.1-16 Печатный аппарат листовой офсетной машины: расположение цилиндров (а), контрольные колбца, шестереночный механизм привода и управление захватами на листовой офсетной машине (Heidelberg) (б)
Для обеспечения безупречного переноса изображения с печатной формы на бумагу необходимо, чтобы все три цилиндра вращались с идеально одинаковыми окружными скоростями без проскальзывания. Поскольку по окружностям цилиндров имеются технологические выемки, невозможно, чтобы в течение печати всего тиража выдерживалось требуемое относительное вращение только за счѐт сил трения между контактирующими поверхностями. По этой причине все цилиндры имеют шестерѐнчатый привод, связанный с приводом машины. Кроме того, через печатный аппарат осуществляется также привод красочного аппарата.
Проблемы печати, вытекающие из конструкции шестерѐнчатого привода (в особенности появление «полошения» дефекта, связанного с неточным изготовлением шестерен), можно разрешить за счѐт оптимального допуска на боковой зазор шестерѐн привода, а также путем совершенствования и повышения качества сборки узлов.
Кроме того, при сборке необходимо уделять внимание тому, чтобы межосевое расстояние между цилиндрами печатного аппарата изменялось таким образом, чтобы обеспечить отключение и включение натиска. При этом следует принимать во внимание межосевое расстояние между офсетным и печатным цилиндрами при разной толщине бумаги и изменения межосевого расстояния при перемещении офсетного цилиндра. Межосевое расстояние регулируется при применении эвольвентного зацепления с соответствующей коррекцией профилей зубьев.
При минимальном межосевом расстоянии необходимо гарантировать наличие зазора между зубьями, а при увеличении межосевого расстояния обеспечение надѐжного контакта. Поэтому в печатных машинах применяются зубья увеличенной высоты. Синхронность вращения цилиндров достигается за счѐт косозубой передачи, так как она увеличивает коэффициент перекрытия зацепления. Кроме одинаковой угловой скорости, для переноса печатной краски необходимо, чтобы между формным и офсетным цилиндрами, а также между офсетным цилиндром и бумагой было обеспечено достаточно высокое давление. Между формным и офсетным цилиндрами, которые вращаются с жѐстко установленным межосевым расстоянием, давление устанавливается за счѐт поддекельной покрышки на офсетном цилиндре, которая обеспечивает радиальную деформацию офсетной резины в диапазоне 0,05-0,15 мм. Между офсетным и печатным цилиндрами устанавливают давление, зависящее от свойств запечатываемых материалов.
При вращении цилиндров с шестеренчатой передачей возникает явление проскальзывания. Оно приводит к тому, что к радиальной деформации
21
офсетной резины в зоне контакта цилиндров добавляется еще тангенциальная составляющая. Силовое нагружение цилиндров печатного аппарата соответствует периоду взаимодействия их рабочих поверхностей, после чего в момент прохождения выемок происходит их разгрузка. Подобное циклическое нарушение силового контакта приводит к возникновению вибраций в печатном аппарате, влияющих на качество печати.
Чтобы свести к минимуму последствия вибрации, на торцевые стороны формного и офсетного цилиндров устанавливают контактные кольца из закалѐнной стали с высокой поверхностной прочностью. Диаметры этих колец равны диаметрам начальной окружности шестерѐн, и они обкатываются друг относительно друга с натягом. На машинах формата печати 70 x 100 см усилие натяга составляет около 15 000 Н. Контактные кольца препятствуют крутильным колебаниям, которые могут возникнуть в механической системе (цилиндр зубчатое колесо). Кроме того, контактные кольца увеличивают жѐсткость на изгиб пары цилиндров. Это сдвигает резонансную частоту системы в некритическую область и уменьшает вибрацию, вызываемую прохождением выемок на цилиндрах.
Для обеспечения необходимого взаимодействия формного, офсетного и печатного цилиндров в процессе печати необходимо, чтобы не возникали их относительные перемещения в окружном и радиальном направлениях. Существенными являются конструктивные особенности установки цилиндров в печатном аппарате. Для всех трѐх цилиндров опоры должны быть выбраны с учетом больших нагрузок. К тому же, исходя из требований точного переноса необходимого количества краски, должны быть обеспечены высокая жесткость конструкций и отсутствие люфтов.
К формному цилиндру предъявляется дополнительное требование, связанное с его юстировкой (необходимость его поворота при диагональной приводке (раздел 2.1.2.3) на определенный угол). При установке офсетного цилиндра необходимо учесть работу механизма натиска. Вследствие учета этих разносторонних требований в качестве опор валов цилиндров применяются беззазорные игольчатые или конические роликовые подшипники, которые поставляются изготовителями с уже гарантированным предварительным натягом.
Цилиндры с их опорами монтируются между двумя вертикальными боковыми стенками (рис. 2.1-16,б). Они изготавливаются преимущественно из высококачественного литья. Учитывая высокие требования к параллельности цилиндров, установочные отверстия должны выполняться совместно в обеих стенках. Печатный аппарат сохраняет требуемую жесткость к вибрациям и кручениям благодаря тому, что вертикальные стойки привинчиваются в нижней части к жесткой станине. В некоторых конструкциях станина выполняет функцию фундамента. Кроме станины для повышения жѐсткости печатного аппарата используют поперечные связи.
22

Монтаж машины требует не только установки цилиндров, но также соблюдения определѐнных условий и правил сборки других узлов. Например, при установке системы захватов на печатном цилиндре и механизма управления открытием и закрытием захватов.
Для обеспечения длительного функционирования и долговечной службы печатного аппарата и вращающихся деталей необходимо достаточное количество качественной смазки. Подшипники и зубчатые передачи предъявляют особенно высокие требования к качеству смазочных веществ. Смазка машин большей частью осуществляется с помощью специальных приспособлений. В узлах возможна утечка масла. Поэтому для машин малого и среднего формата применяют пастообразные смазки. При выборе масел обращают внимание на возможное их взаимодействие с различными растворителями, с окрашенными металлическими и полимерными поверхностями, цветными металлами, резиновыми и другими материалами. Учитывают также воздействие смазочных материалов на процесс старения отдельных деталей печатных машин.
Качество оттисков
Вразделах 1.4, а также 2.1.4 и 3.2.2 подробно изложены методы контроля качества оттисков и применяемая измерительная техника. В настоящем разделе дается только обзор определѐнных параметров качества. Показатели качества приведены в одном из следующих разделов. В зависимости от заказа и оригинала возможны различные, первоначально устанавливаемые критерии качества, К важнейшим из них относятся:
Равномерность оптической плотности растровых изображений Если изображение, получаемое на оттиске, имеет относительно большие
участки, отличающиеся равномерностью тона, то даже небольшие различия в оптической плотности могут оказаться заметными для глаза человека. Значения минимальных (пороговых) различий составляют порядка 0,02 единицы оптической плотности AD (раздел 1.4.1). Если в процессе печати тиража возникают колебания градации тона, то на оттисках они проявляются
ввиде пятен или полос, которые являются дефектами. При колебаниях оптической плотности от оттиска к оттиску и последующем сравнении репродукций они становятся сразу заметными.
Равномерность оптической плотности плашки На таких участках колебания оптических плотностей от оттиска к
оттиску также очень хорошо заметны человеческому глазу. Градационная передача растрового изображения
Вкопировальном, а также в печатном процессе могут обнаруживаться существенные изменения размеров растровых точек. От этого страдает
качество печати. На помощь приходит стандартизация процесса
23
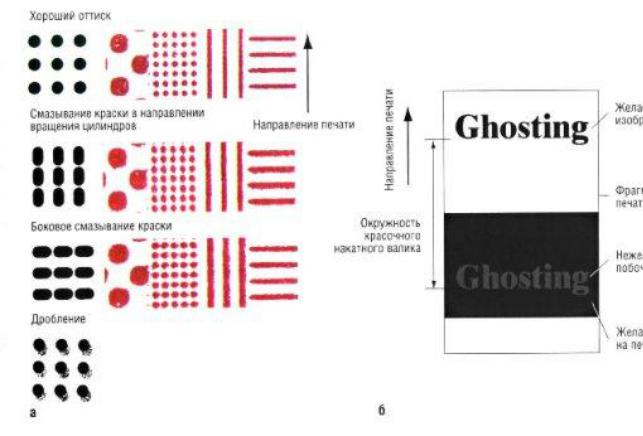
изготовления офсетной репродукции (раздел 2.1.2). Соответствующая документация регламентирует условия стабильности передачи растровой структуры в формном и печатном процессах. Основное влияние на точность воспроизведения в печатном процессе оказывают офсетное резиновое полотно и настройка печатной машины. Отклонения в усилии прижима между формным и офсетным цилиндрами приводят к существенным изменениям в градационной передаче. Неправильно выбранная величина давления между офсетным и печатным цилиндрами вызывает значительные цветовые искажения на оттиске.
На изображении может обнаруживаться деформация растровых точек в виде увеличения их размеров и, следовательно, появляются отклонения в цветопередаче. Растискивание и дробление растровых точек два важнейших параметра, определяющих качество печати (рис. 2.1.17,а).
Рис. 2.1-17 Примеры нарушения качества печати: деформация растровой точки вследствие смазивания и дробления (а), эффект шаблонирования на печатном изображении (б)
В процессе растискивания происходит сдвиг контуров растровых точек. Причиной этого являются относительные перемещения между поверхностями печатной формы и офсетного цилиндра или между офсетным цилиндром и запечатываемым материалом. При этом поверхности неточно прокатываются одна по другой. Смещения в направлении печати называются смещением по окружности, а смещение в поперечном направлении боковым смещением. Причина растискивания состоит, главным образом, в
24
повышенном давлении между двумя соприкасающимися цилиндрами. Так как деформация офсетного резинового полотна по ширине едва ли сказывается на величине растискивания, то деформация растровых точек происходит преимущественно в направлении печати. При этом, например, круглая точка превращается в эллиптическую. Часто недостаточно натянутое офсетное полотно или слишком большая подача краски также являются причинами таких изменений площадей и форм растровых точек. Однако растискивание возможно также и в боковом направлении. Отклонения в различных направлениях заметны на полях контрольных шкал, состоящих из штриховых элементов (рис. 2.1-17,а). Штрихи, перпендикулярные направлению печати, расширяются в направлении вращения цилиндров, что приводит к потемнению данного поля, тогда как ширина штрихов, расположенных в направлении печати, остаѐтся неизменной.
Дробление это увеличение растровых точек, при котором вокруг них образуется двойной или многократный тенеобразный контур. Это смещение красочных изображений приводит к увеличению оптической плотности. Дробление происходит за счѐт колебаний приводки во время печати (обусловленных машиной или бумагой). В многокрасочных машинах печатные листы со свежей краской запечатываются, например, после первой печатной секции последующей второй краской во второй секции. На офсетном резиновом полотне за счѐт расщепления красочного слоя возникает цветной отпечаток растровой структуры, который снова переносится на следующий печатный лист (раздел о рулонных машинах). Таким образом, изображение с формного цилиндра должно точно накладываться на предыдущее свежесформированное изображение на офсетном цилиндре, в противном случае печатающие элементы увеличатся за счѐт их дробления. Увеличение размеров растровых точек за счѐт дублирования происходит при уменьшенной толщине красочного слоя, получаемого на оттиске.
Смещение на величину 10 мкм уже приводит к изменениям градационной передачи.
Шаблонирование Шаблонирование это наложение печатающих элементов в направлении
печати на последующие участки изображения (рис. 2.1-17,б). Вообще, в традиционном красочном аппарате накатные валики меньше формного цилиндра. Однако после нанесения краски на печатную форму из-за расщепления слоя на накатных валиках остаѐтся красочный слой, который после их одного оборота может стать причиной образования на оттиске вторичного «паразитного» изображения. В принципе красочный слой на печатной форме становится достаточно равномерным за счѐт применения нескольких накатных, красочных валиков различных диаметров (в листовых офсетных машинах их чаще всего 4) и, соответственно нескольких участков контакта, а также за счѐт положительного влияния осевого раската краски. При неблагоприятной подаче краски на печатную форму и соответствующем
25
построении красочного аппарата также возможно появление заметного шаблонирования.
Микронеоднородность (англ. mottling)
Под микронеоднородностью понимают пятнистость, облачность красочного слоя на запечатанном материале. Это происходит из-за неравномерности впитывания красочного слоя в запечатываемый материал при его прохождении между печатными секциями многокрасочной печатной машины. Неравномерность впитывания приводит к неравномерному распределению красочного слоя, что особенно усиливает эффект при последовательном наложении красок, делая его заметным. Чем быстрее и равномернее впитывается первая краска, тем лучше и ровнее передача следующей краски. Неравномерность можно устранить, в частности, путем соответствующего изменения впитывающей способности красок, изменением последовательности их наложения или применением другой бумаги. На неравномерность влияюттакие свойства бумаги, как однородность ее структуры и поверхностного слоя.
Восприятие слоем предыдущей печатной краски слоя последующей краски ( trapping )
Треппинг параметр, характеризующий переход второй краски на первую при их последовательном наложении в многокрасочной печати («сырое по сырому»). Расщепление краски зависит, главным образом, от еѐ реологических свойств (например, липкости). Чтобы последующая отпечатанная краска хорошо воспринималась уже отпечатанной ранее нанесенной краской, она должна иметь меньшую липкость.
Абсолютное значение оптической плотности и координаты цветности Абсолютное значение оптических плотностей определяется по
колориметрическим стандартам, а также координатам цветности. При многокрасочной печати с наложением красок применяется колориметрия, основанная на спектральных измерениях.
Средства, пригодные для применения в измерительных системах и устройствах регулировок, должны обеспечивать соответствующую точность определения оптических плотностей и координат цветности. Это относится как к растровым изображениям, так и к плашкам. При печати тиража измерение оптических плотностей часто оказывается достаточным для приладки, а для оценки наложения красок необходимо проводить спектрофотометрические измерения.
Приводка и совмещение Приводка точное совпадение оттисков при последовательном
наложении красок, называемое также термином «совмещение красок», в значительной степени определяет качество изображения на оттиске. Для четырех красочного оттиска от приводки зависит достигаемое впечатление четкости, являющейся одним из самых существенных критериев оценки качества печати. Приводка или совмещение это формально точное
26
расположение изображения на листах запечатываемого материала или на бумажном полотне относительно краев обрезаемого листа или полотна, Но в большинстве случаев, имея в виду совмещение красок, говорят о точном наложении однокрасочных изображений в процессе многокрасочной печати, как уже об этом говорилось раньше.
Глянец Глянец оттисков и также его равномерность оказывают субъективное
влияние на качество печати. Однако «читаемость» печатных изображений с высоким глянцем уменьшается, хотя часто высокий глянец визуально отождествляют с высоким качеством печати.
Вид растрирования Чем более высоколиниатурный растр, тем выше разрешающая
способность печати, но тем больше также растискивание растровых точек. Для того чтобы избежать образования муара и розеток при многокрасочной печати, часто используют нерегулярные растры. Они позволяют воспроизводить очень мелкие детали оригинала, а отклонения в приводке не столь сильно влияют на отклонения в цветопередаче. При применении совмещенных растровых изображений различной структуры (комбинация периодических и непериодических), при прочих равных условиях, обеспечивается повышение качества печати.
Белизна и равномерность белизны запечатываемого материала
Белизна запечатываемого материала оказывает существенное влияние на воспроизводимый цветовой охват в четырехкрасочной печати. Мелованные бумаги имеют поверхностные слои, придающие им высокую степень белизны. Собственно при печати используются относительно прозрачные краски. В таких условиях цветовой тон незапечатанной бумаги является решающим фактором, определяющим воспроизведение цвета.
Методы измерения Для измерения вышеуказанных параметров качества имеются
соответствующие методы и средства измерений. В числе важнейших, используемых для определения соответствия требованиям качества, можно указать следующие:
- |
|
|
|
|
денситометрию; |
- |
колориметрические |
измерения |
(спектрофотометр); |
||
- |
|
измерения |
|
глянца; |
|
- |
измерения |
точности |
совмещения |
красок |
(приводки); |
- |
измерения степени белизны (прибор для измерения белизны и |
|||
спектрофотометр); |
|
|
|
|
- |
определение |
частоты |
растровой |
структуры; |
• определение резкости (измерительныймикроскоп).
Имеется большое количество контрольных элементов, которые могут быть интегрированы в печатное изображение. Анализ контрольных шкал предполагает применение соответствующей измерительной техники. Однако
27

контрольные элементы служат также для визуальной оценки изменений, влияющих на качество печатной продукции. Методы измерения подробно описываются в разделах 1.4.1,1.4.4 и 2.1.4.
Листовая офсетная печать
Листовая офсетная печать по сравнению с другими способами обладает преимуществами с экономической точки зрения и с позиции качества продукции. К ним, прежде всего, надо отнести возможность печати широкого ассортимента продукции и сравнительно низкую ее стоимость при высочайшем качестве и широком спектре тиражей. Цветовые возможности в офсетной печати укладываются в интервал от одной, включая четырехкрасочную печать, до двенадцати красок. Листовым офсетом могут запечатываться материалы самых различных форматов и плотностей. Короткое время занимает подготовка к печати.
Таким образом, важным оказывается, что наряду со свободным выбором формата может быть решена проблема применения запечатываемых материалов с различными свойствами. Многообразие видов материалов, используемых в листовом офсете, предъявляет особые требования к организации их хранения поставщиками и потребителями. Операции отделки продукции, такие, как лакирование, впечатывание информации, нумерация, перфорирование и штанцевание, выполняемые непосредственно в печатных машинах или вне их, широко используются в технологии листового офсета. Важным является и множество вариантов обработки продукции.
Листовые офсетные машины позволяют:
осуществлять высокоточную проводку бумажного листа с высокой скоростью с учетом динамики и специфики нагрузок для данного способа печати;
контролировать и надѐжно осуществлять сложный технологический процесс печати с большим числом участвующих в нем расходных материалов (увлажняющий раствор, краска, бумага, воздух и др.).
28
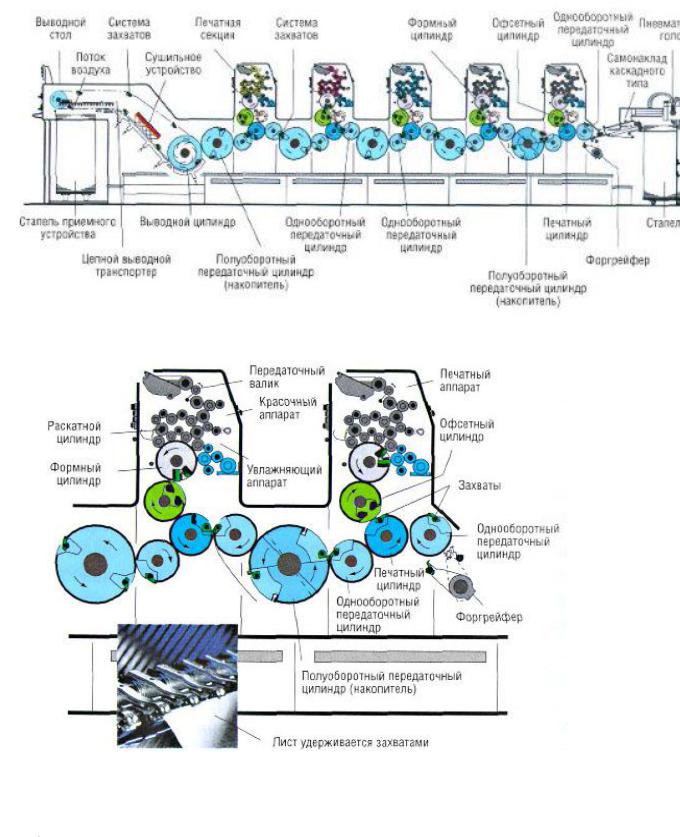
Рис. 2.1-18 Транспортировка листа в листовой офсетной машине секционного построения (Speedmaster SM 74-5-P, H, Heidelberg)
Рис. 2.1-19 Транспортировка листа в печатной секции (Heidelberg)
Проводка бумаги
29
Движение листа от стапеля через самонаклад к печатной секции должно быть обеспечено высокоточной транспортирующей системой, контрольными и блокирующими элементами, вплоть до нанесения на него краски и вывода на приѐмный стол (рис. 2.1-18). В самонакладе транспортировка листа осуществляется исключительно посредством вакуума или сил трения. Процесс подачи сводится к отделению верхнего листа от стопы с помощью вакуума пневматической головкой и транспортированию его по накладному столу, где он проводится между роликами, лентами и щѐтками. Каждый лист подводится к печатному аппарату с высокой скоростью. Перед этим он притормаживается, останавливается и выравнивается по передним и боковым упорам. Выравненные листы захватываются захватами форгрейфера, разгоняются до скорости печати и передаются в печатный аппарат. В машинах, производительность которых достигает 15 000 листов/ч, формата 70 см х 100 см, осуществляется проводка бумаги со скоростью около 3,5 м/с. При выходе из зоны равнения для плавного ускорения запечатываемого материала до скорости печати предусматривается соответствующий ускоряющий механизм в виде форгрейфера и передаточного цилиндра.
В печатных аппаратах (рис. 2.1-18) лист подается к печатному цилиндру. Система захватов (рис. 2.1-19) принимает его и во время рабочего цикла вводит в контакт с офсетным цилиндром, где он запечатывается краской, а затем с помощью передаточных цилиндров передаѐтся транспортной системой к следующему печатному аппарату, после чего - на выводной стол. Процесс печати предполагает наличие определѐнного давления для перехода краски на запечатываемый материал между формным и офсетным цилиндрами, а также между офсетным и печатным цилиндрами. В зависимости от структуры поверхности запечатываемого материала и его толщины давление между последней парой цилиндров регулируется путѐм изменения расстояния между поверхностями в зоне контакта на требуемую величину. При этом давление между формным и офсетным цилиндрами не изменяется.
Офсетные краски представляют собой пастообразное, высоковязкое и, следовательно, липкое вещество. Благодаря этим их свойствам бумага прилипает к печатающим участкам резинотканевого полотна, а при выходе из контакта она отрывается со значительным усилием от него с помощью захватов. Таким образом, для вывода листа требуется определенное усилие фиксации его захватами. Однако следует учитывать, что усилие фиксации захватов не должно деформировать поверхность листа, а сами они должны быть износоустойчивы.
Рабочие детали захватов изготавливаются из специально выбираемых материалов, например полиуретана, керамики, и имеют особую поверхностную структуру. Обрабатывается и опорная поверхность, к которой прижимаются захваты. Однако, несмотря на это, определѐнное
30