
Tema_5_ofsetnaya_pechat
.pdf
Тема 5 История офсетной печати
Первая печатающая литографская пресс-машина со смещением была создана в Англия в 1875 и конструирована для печати на металле. Смещенный цилиндр был покрыт специально обработанным картоном, который переносил напечатанное изображение от камня litho к поверхности металла.
Но после ( примерно в 1880 году) заволакивание картоном смещенного цилиндра было изменено к резине, которая стала самым используемым материалом.
Первым человеком, кто реализовал идею использования смешанного давления печати на бумаге, была американка Ira Washington Rubel в 1903 году. Первое давление офсетной печати Она получила идею совершенно случайно. Ira Washington Rubel заметила, что когда лист бумаги не был подан в литографское давление во время деятельности, камень напечатал свое изображение к резиненному цилиндру изображение, и следующее изображение было с двух сторон: сразу litho на фронте и изображение от rubber одеяла на задней части. Rubel после этого заметила, что изображение на задней части листа было гораздо острее и гораздо чѐтче, чем сразу изображение litho. Так как мягкая резина могла отжать изображение на бумаге лучшее чем трудный камень. Ira Washington Rubel вскоре решила построить давление таким образом, чтобы печаталось каждое изображение от плиты к одеялу и после этого к бумаге.
Братья Charles и Albert Harris независимо наблюдали за этим процессом приблизительно в тоже самое время и разработали смещенное давление. Harris конструировали смещенное давление вокруг роторной машины letterpress. Они использовали плиту металла согнутую вокруг цилиндра, а с верху находится машина против роликов чернил и воды. Печатающий ( Blanket) цилиндр был расположен сразу ниже, и соединенный с (in contact with) цилиндром плиты.
Пока этот основной процесс, который все еще используется и сегодня,
но уточнения |
включаются постепенно в разработку печатного стержня |
|||||
(используя |
крены |
бумаги, |
которые |
больше |
чем |
листы). |
Сегодня, большинство печати, включая газеты, произвозводиться с помощью технологии со смещенным процессом.
Офсетная печать, офсет
Офсетный способ печати является классическим и практически основным, благодаря экономичности и отличному качеству выпускаемой
продукции. |
Печать |
офсетным |
способом |
способна |
воссоздать |
|
|
|
|
|
1 |
высококлассную полиграфическую продукцию. С ее помощью возможно отличное воспроизведение мелких деталей и хорошая передача полутонов.
Говоря об офсетном способе печати, можно отметить, что сегодня офсетная печать наиболее популярна и часто используется в полиграфическом производстве для печати книг, журналов, газет и другой продукции.
История офсета в современном его виде насчитывает практически век. В начале 20 века американский печатник Айра В. Рюбель изобрел способ офсетной печати. В процессе печати он неожиданно обнаружил что изображение, оказавшееся на резиновом полотне печатного цилиндра по качеству превосходит оттиски на бумаге и годится для печати. На основе этого принципа Рюбель сконструировали свою первую в в истории трехцилиндровую печатную машину.
Сегодня на офсетных печатных машинах, листовых и рулонных, производят следующие виды печатной продукции:
глянцевые журналы, иллюстрированную журнальную продукцию на мелованной бумаге или бумаге с полупокрытием.
полноцветные газеты, которые обычно печатаются на рулонных ротационных машинах. Качество продукции напрямую зависит от запечатываемого материала — это обязательно должна быть бумага для офсетного способа печати.
рекламная продукция, изготавливается на малоформатных листовых офсетных машинах.
представительская продукция - печать буклетов, брошюр, каталогов, плакатов, постеров, календарей, открыток, папок, блокнотов, а также многого другого.
Печать офсетным способом характеризуется первоначальным созданием
печатных форм. Множество факторов влияют на качество отпечатков при офсетной печати. Среди них, такие наиболее важные, как:
жесткость воды, загрязнение воды,
влияние запечатываемого материала
влияние печатной машины (на качество печати и стабильность процесса)
Офсетные печатные машины: устройство и виды
Воснове принципа действия офсетных машин лежит нанесение изображения на, специальным образом обработанную, пластинку, а потом с помощью вспомогательного офсетного цилиндра - на непосредственный носитель. Полноцветное изображение при таком способе складывается из четырех основных цветов: голубого, желтого, пурпурного и черного. Подготовительный этап при офсетном способе включает в себя несколько процессов:
Монтаж макета
Вывод фотоформ
2

Засветка фотоформ
Наладка оборудования под изготовленную форму
Офсетные машины делятся по принципу построения на 2 вида: рулонные и листовые офсетные машины. Печать на каждой из них имеет свои преимущества и недостатки. Изготовление печатной продукции с помощью рулонных офсетных машин позволяет быстро и качественно распечатать недорогую в производстве полиграфическую продукцию.
Печать на листовой печатной машине отличается тем, что с помощью данного оборудования можно очень быстро осуществлять высокоточную проводку бумажного листа. При проводке становится возможным учитывать динамику и специфику нагрузок для офсетной печати, а также контролировать и надѐжно осуществлять сложный технологический процесс печати с большим числом участвующих в нем расходных материалов (увлажняющий раствор, краска, бумага, воздух и др.).
Для печати газет, в основном, используются офсетные печатные машины планетарного построения. Ярусное же построение печатной машины для офсета преимущественно подходит для печати наиболее мелкоформатной полиграфической продукции.
Сухой офсет
Для классического процесса печати офсетным способом требуется увлажненный раствор и особенные печатные краски.
Но кроме вышеупомянутого приема существует метод «сухого» офсета или типоофсет, где печатный процесс происходит без увлажнения. Хотя этот способ печати имеет большой потенциал, сегодня его использование в полиграфической промышленности не превышает 5%.
Офсет без увлажнения базируется на том же принципе, что и классический способ офсетной печати, но поверхности материалов совершенно другие. Пробельные участки печатной формы для типоофсета покрыты силиконом, поэтому отталкивают краску. Краска воспринимается лишь на тех участках печатной формы, с которых силикон удален.
Печатные краски для типоофсета используются вязкие, поэтому при ее растире в красочном аппарате валики могут нагреваться до 50 градусов С, охлаждающего увлажняющего раст
Печатные формы, печатные краски, увлажняющий раствор
Печатные формы
Печатные формы для офсетной печати представляют собой тонкие (до 0,3 мм), хорошо натягивающиеся на формный цилиндр, преимущественно монометаллические или, реже, полиметаллические пластины. Используются также формы на полимерной или бумажной основе. Среди материалов для печатных форм на металлической основе значительное распространение
3
получил алюминий (по сравнению с цинком и сталью). Необходимое зернение поверхности пластины выполняется механическим путем при помощи пескоструйной машины или на зернильных установках с шарами и абразивным материалом, а также с применением мокрой или сухой обработки щетками. В настоящее время формные пластины зернятся почти исключительно электрохимическим путем и на заключительном этапе оксидируются (рис. 2.1-3). На металлическую основу наносится копировальный слой, на котором формируется изображение, несущее краску. Это в основном полимер. На полиметаллических (биметаллических) формных пластинах олеофильным слоем служит медь. В настоящее время в типографиях применяются преимущественно светочувствительные алюминиевые формные пластины с предварительно нанесенной фотополимеризующейся композицией на основе диазосоединений. Формирование изображения осуществляется благодаря различным свойствам поверхности пластин после их экспонирования и проявления. Печатные формы вследствие воздействия света и обработки образуют воспринимающие или отталкивающие краску элементы.
Оксид алюминия, который при особой обработке основы представляет собой тонкий слой, образует стабильную гидрофильную поверхность. Задача при обработке предварительно очувствленной офсетной формной пластины заключается в том, чтобы на этапах экспозиции и проявления добиться дифференциации поверхностных свойств.
Актиничный свет (содержащий УФ-излучение), воздействующий на поверхность светочувствительного материала на формной пластине, вызывает его химические изменения. В зависимости от вида и структуры слой реагирует на экспонирующее излучение по-разному. Различают следующие две фотохимические реакции при обработке формной пластины:
• задубливание копировального слоя светом (негативное копирование),
• разрушение копировального слоя светом (позитивное копирование).
При фотохимическом задубливании копировальный слой на засвеченных участках становится нерастворимым для проявителя. Если, напротив, копировальный слой фотохимически разрушается, то проявитель растворяет засвеченный слой, удаляя его с подложки (например, алюминия). Таким образом, возможны два различных способа копирования: позитивное и негативное. Они требуют различной засветки для образования изображения, т.е. различных предварительно изготовленных фотоформ (рис.
2.1-4).
При позитивном копировании в качестве копируемого оригинала используется позитивная фотоформа, т.е. непрозрачные для света зачерненные участки на ней соответствуют участкам, воспринимающим краску на печатной форме. Как следует из рис. 2.1-4,а, при копировании свет проходит через прозрачные участки в позитивной фотоформе. При этом светочувствительный копировальный слой на пластине «разлагается».
4
Следствием этого является очищение от копировального слоя в процессе проявления участков поверхности формной пластины, в данном случае тех, на которых нет изображения. Недостаток этого способа заключается в том, что на формной пластине в отличие от прозрачных участков пленочного оригинала могут частично воспроизводиться в виде печатающих элементов края пленки, пыль, монтажные полосы и пр., т.е. темные частицы на пленке. При негативном копировании с применением «негативных формных пластин» в качестве копируемых оригиналов используется негативная фотоформа, на которой участки изображения (печатающие элементы) соответствуют прозрачным светлым участкам. Как следует из рис. 2.1-4,б свет отверждает копировальный слой на формной пластине, который после проявления остается на участках ее поверхности, в то время как с незасвеченных участков (пробельных) он удаляется. Независимо от того, идет ли речь о позитивном или негативном копировании, готовые печатные формы идентичны относительно своего информационного содержания – различаются лишь наносимые слои, используемые для изготовления печатающих элементов. Решение о работе с тем или иным видом форм, изготавливаемых позитивным или негативным копированием, принимает полиграфическое предприятие. Многие типы металлических печатных форм для повышения их тиражестойкости после проявления подвергаются термической обработке (путем обжига).
Печатные формы на лавсановой основе применяют для выполнения работ среднего качества. Они используются для печати однокрасочных и многокрасочных работ малого формата. Для обеспечения контроля качества в процессе изготовления печатных форм совместно с основным изображением копируют контрольные элементы. Для этого имеются стандартные шкалы FOGRA с соответствующими клиньями, подобными тестовому клину PMS-Offset-Testkeil или UGRA-Offset-Testkeil.
Печатные формы для термической записи изображения.
Наряду с печатными формами, описанными выше, для цифровой записи изображения созданы термочувствительные формные пластины. Запись изображения осуществляется путем воздействия лазерного излучения. В качестве примера на рис. 2.1.5 представлена печатная форма для офсета без увлажнения на лавсановой основе. В разделе 4.3.9 подробно рассмотрена технология ее изготовления.
Печатная краска
Применяемые в офсетной печати краски представляют системы высокой вязкости. Они состоят из цветных пигментов, связующего вещества, добавок и растворителя (раздел 1.5.2). Цветные пигменты имеют органическую или неорганическую природу. Они определяют цветовой тон печатной краски. Пигменты состоят из твердых частиц неправильной формы размерами от 0,1 до 2 мкм. Связующие вещества необходимы, чтобы пигмент, находящийся в виде порошка, мог закрепляться на запечатываемом материале. Кроме того,
5
связующие вещества образуют защитную пленку, препятствующую механическому истиранию красочного слоя на оттиске. В зависимости от технологических особенностей печатного процесса и свойств запечатываемого материала связующее вещество изготавливается по определенным рецептурам из соответствующего сырья. Используемые для изготовления печатных красок связующие вещества называются «фирнисами». В самой рецептуре, подготовке и комбинации отдельных видов сырья и состоит собственное ноу-хау изготовителей печатных красок. Добавки вводятся в печатные краски, чтобы целенаправленно влиять на их особые свойства. Называемые также «вспомогательными средствами» добавки применяются главным образом тогда, когда обнаруживаются особые трудности в печатном процессе. Роль растворителя в офсетных красках выполняют минеральные масла. Они формируют условия для переноса краски и удаляются в процессе сушки (испарением, впитыванием). Часть печатных красок закрепляется также за счет окисления. Наряду с этими красками, применяющимися чаще всего, имеются также краски, которые затвердевают посредством воздействия излучения (УФ- и электронного). Структура их совершенно иная, чем обычных красок. Различают УФ-краски как для обычной офсетной печати (с увлажнением форм) и для офсета без увлажнения.
Увлажняющий раствор
В традиционной офсетной печати увлажняющий раствор служит для разделения печатающих и пробельных участков на печатной форме, т.е. для того, чтобы избежать попадания краски на непечатающие участки. Увлажняющий раствор состоит в основном из воды. Опыт показывает, что увлажняющий раствор должен иметь значение рН между 4,8 и 5,5. Степень жесткости воды от 8 до 12 DH. Увлажняющий раствор обычно содержит также защитный коллоид для пластин, вещества для увеличения смачивания
– изопропиловый спирт, буферные вещества и антимикробные добавки. В качестве защитного коллоида для печатных форм служит гуммиарабик. Добавки для увеличения смачивания вводятся для снижения поверхностного натяжения. На рис. 2.1-6 показано действие добавок на величину поверхностного натяжения. Введение буферного средства стабилизирует значение рН. Антимикробные добавки особенно требуются в тех случаях, когда увлажняющий раствор подготавливается централизованно в специальном устройстве для нескольких офсетных машин. Существует опасность, что без этих добавок его подача может прекратиться из-за появления и роста в резервуарах водорослей. Так называемые «безалкогольные увлажняющие растворы» вместо изопропилового спирта содержат вещества, заменяющие его, например гликоли.
вора просто нет. Для хорошего печатного процесса температура валиков должна быть не более 30 градусов С.
6

Для избежания тенения, в красочном аппарате необходимо поддерживать определенную температуру посредством применения раскатных цилиндров с водяным или воздушным охлаждением.
Посредством типоофсета изготавливают высоколиниатурные растровые изображения.
В печатное оборудование для сухого офсета отличается простой конструкцией красочного аппарата. Благодаря этому можно быстро достичь высокого качества полиграфической продукции.
Один из главных недостатков сухого офсета – отсутствие очищающего действия увлажняющего аппарата: на офсетном полотне и поверхности печатной формы легко осаждаются капли краски и бумажная пыль.
Красочный аппарат, увлажняющий аппарат, печатный аппарат
Красочные аппараты Во время печатного процесса краска с печатающих элементов формы
передается через офсетный цилиндр на запечатываемый материал. Задача красочного аппарата заключается в том, чтобы постоянно подавать на печатающие элементы новые порции краски с тем, чтобы печатный процесс не прекращался. Определенное количество печатной краски должно непрерывно подаваться в печатную систему. Баланс между количеством подачи краски и ее отдачей печатной форме должен быть отрегулирован так, чтобы исключить колебания плотности краски на оттиске.
Наряду с соблюдением баланса, решающее значение для качества печати имеет постоянство толщины красочного слоя на печатающих элементах формы и на запечатываемых участках материала. Теоретически повсюду на печатном листе должен находиться красочный слой одинаковой толщины этим допущением в репродукционной технике обосновывается изготовление цветоделенных фотоформ.
7
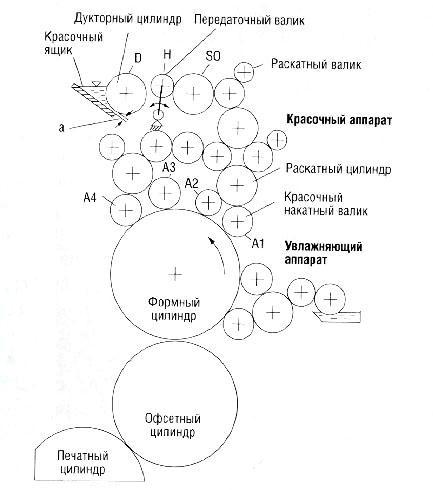
Рис. 2.1-7 Схема красочного и увлажняющего аппаратов офсетной машины
Критериями, определяющими качество, таким образом, являются:
- крайне малые колебания средней толщины красочного слоя; - постоянство толщины красочного слоя на печатающих элементах и на запечатанных участках материала (бумаги) в пределах всей поверхности.
Эти величины зависят от конструктивных особенностей красочного аппарата, шероховатости печатного материала, микрогеометрии печатной формы и резинового офсетного полотна. Реологические свойства печатной краски определяют равномерное покрытие ею плашек и отдельных растровых точек на печатном материале.
В красочном аппарате (рис. 2.1-7) осуществляется периодическая (прерывистая) подача краски посредством качающегося передаточного валика Н. Последний принимает от дукторного цилиндра сравнительно толстый слой печатной краски и передает часть его благодаря своему вращению на первый валик SO красочного аппарата. Выбор зазора между дуктором и ножом, продолжительность вращательного движения дукторного цилиндра D (преимущественно прерывистого), время контакта передаточного валика и скорость вращения валиков являются определяющими факторами для дозирования подаваемого количества краски.
8
Наряду с системами прерывистой подачи краски имеются также системы для
еенепрерывной подачи (так называемые «красочные аппараты пленочного типа»).
Все валики красочного аппарата (кроме валиков D и Н) имеют одинаковую окружную скорость, так же как формный и офсетный цилиндры. Система работает почти без проскальзывания, если не считать его малую величину, обусловленную деформацией сжатия (раздел 2.1-2) между жесткими и эластичными валиками. Нанесенная полоса краски многократно расщепляется и раскатывается. Количество краски, находящейся в красочном аппарате, зависит от числа красочных валиков и от площади их поверхностей. При оптимальном конструктивном исполнении красочного аппарата можно исходить из того, что накатные красочные валики от А1 до А4 создают на печатающих элементах формного цилиндра относительно постоянный красочный слой, т.е. после последнего накатного валика А4 обеспечивается получение красочного слоя примерно постоянной толщины независимо от распределения печатного изображения на форме. В печатной зоне (между офсетным и печатным цилиндрами) часть красочного слоя переносится на запечатываемый материал.
Как известно, офсетные печатные формы отличаются тем, что печатающие и пробельные элементы находятся в одной плоскости. «Необходимые» количества краски и увлажняющего раствора на форме (при сбалансированном их количестве) должны соответствовать задачам оптимального процесса печати. Если баланс нарушается, то происходят изменения толщины красочного слоя на оттиске.
Как прерывистая подача печатной краски в системе передаточный валик и дукторный цилиндр, так и неравномерная ее подача на форму (пробельные и печатающие элементы) является причиной того, что реально нельзя говорить о точном, постоянном процессе. Следует обращать внимание на расщепление краски на отдельных участках контакта при печати, а также при
еепрохождении в красочном аппарате.
Вупрощенной модели нанесения краски посредством одного накатного валика можно пояснить возникновение «паразитных» эффектов обратного действия (рис. 2.1-8). Для упрощения модели не будем принимать во внимание слой увлажняющего раствора. Перед нанесением краски на накатном валике находится ее слой толщиной S 1 . На печатающих элементах формы имеется остаточный красочный слой толщиной S 2 . После нанесения краски печатающий элемент на форме будет иметь новый красочный слой S 4 , а на соответствующем участке накатного валика останется красочный слой толщиной S 3. Толщины красочного слоя S 3 и S 4 выводятся с учетом коэффициента расщепления (предполагая, что имеются замкнутые красочные слои, а не сегментообразные, как показано на рис. 2.1-8):
S 4 = a ( S 1 + S 2 ), S 3 = (1a )( S 1 + S 2 ).
9

Рис. 2.1-8 Перенос краски в красочном аппарате: с красочного накатного валика на формный целиндр (а), с печатной формы на запечатываеый материал (б)
В соответствии с рис. 2.1-8, а непосредственно перед участком с толщиной S 3 и после него накатной валик имеет толщину слоя S 1 .Таким образом, появляется участок резкого изменения в толщине слоя с разницей As = S 1 S 3 . Правда, эта разница уменьшается при дальнейших прокатываниях расположенным выше раскатным валиком, а также при подаче новой краски из красочного аппарата.
Однако она не устраняется полностью. Эта разница сказывается на слоях краски на печатающих элементах и на запечатываемом материале. На печатающих элементах в этом случае не будет создаваться красочный слой постоянной толщины. Это ухудшает качество печати. На печатный процесс влияет схема построения красочного аппарата (возможность возникновения эффекта шаблонирования).
На рис. 2.1.8,б представлены основные процессы расщепления краски и параметры толщин слоев, начиная от формного цилиндра до печатного листа. В идеальном случае следует исходить из постоянного коэффициента расщепления a = 0,5 и постоянной толщины слоя S 4 на печатной форме.
10