
Базирование и базы в машиностроении
.pdf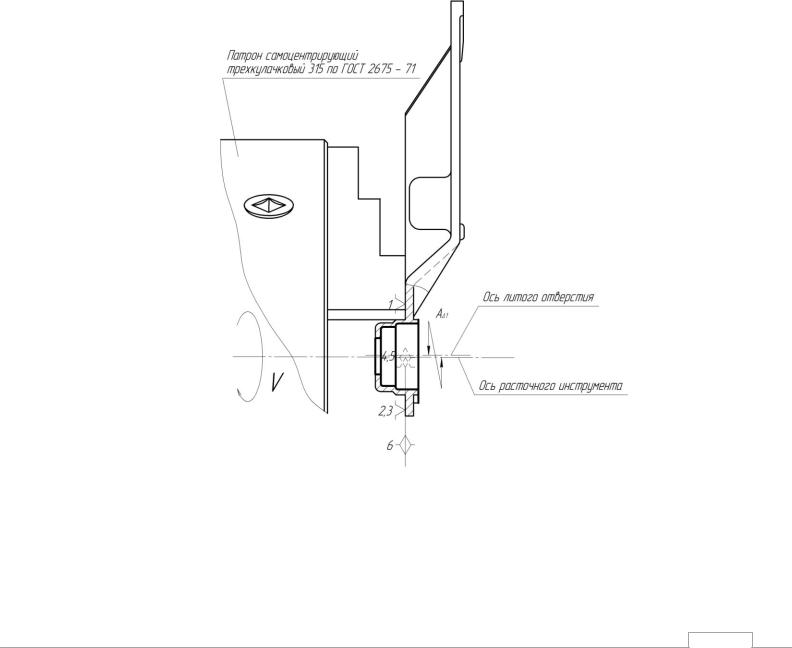
расточного инструмента - А∆). Смещение в данном случае обусловлено неточностью расположения стержня к наружной поверхности (базовой поверхности) и регламентируется допуском на размер от базовой поверхности до внутренней поверхности литого отверстия - А∆ = 800 мкм.
Кроме того, весьма затруднительно выполнить подрезку торца главного отверстия. Это обусловлено тем, что при обработке резец, двигаясь в радиальном направлении, будет работать на удар, а также близость ребер жесткости делает подвод инструмента весьма затруднительным. Следствием этого будет, снижение стойкости инструмента и ухудшения качества обрабатываемой поверхности. Решая эту задачу, потребуется уменьшить режимы резания, что приведет к увеличению основного технологического время, а также использовать нестандартный режущий инструмент.
Поэтому, обработку поверхности соединения рычага и крышки целесообразно выделить в отдельную операцию (фрезерную), а для первой операции необходимо рассмотреть такую схему базирования, где вместе с комплектом основных технологических баз для большинства операций будет обеспечен равномерный припуск при растачивании главного отверстия.
Рисунок 49 – Первый вариант базирования рычага на первой операции При втором варианте базирования рычаг также устанавливается и
фиксируется в самоцентрирующем трехкулачковом патроне с сырыми кулачками с выточкой под необработанное литое отверстие (рисунок 50).
91
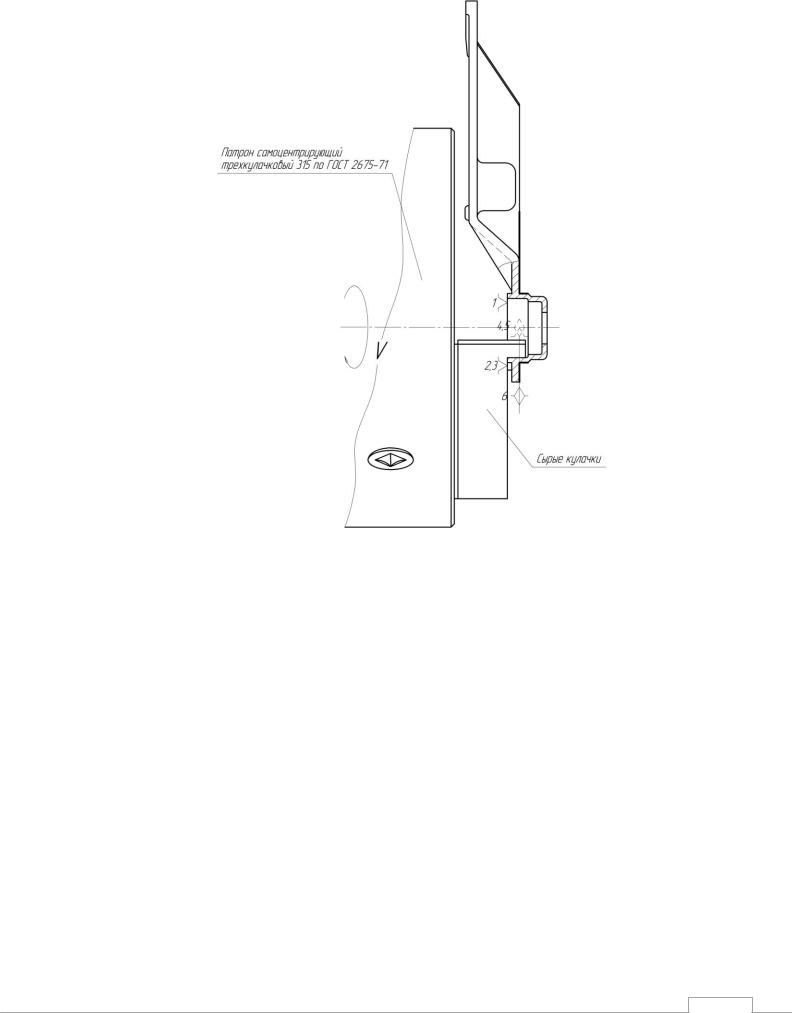
Рисунок 50 – Второй (базовый) вариант базирования рычага на первой операции
При такой установке в качестве установочной базы используется необработанный торец главного отверстия, в качестве двойной центрирующей необработанная внутренняя поверхность литого отверстия, опорная база является скрытой и мысленно приложена к одной из осей.
При такой установке вполне можно выполнить с заданной точностью обработку наружной поверхности рычага, при которой ось литого отверстия (базовой поверхности) совпадает с осью режущего инструмента, а также торцовую поверхность соединения рычага и донышка, что обеспечит комплект основных технологических баз для большинства последующих операций. Кроме того, обработав наружную цилиндрическую поверхность относительно литого отверстия обеспечивается, равномерность распределения припуска при последующей операции растачивания главного отверстия. В этом случае А∆ - смещение оси литого отверстия относительно оси расточного инструмента будет не более 80 мкм в пределах допустимого биения кулачков и погрешности установки рычага в самоцентрирующем патрон /11, с.41/.
92

Рассмотренные выше варианты базирования и закрепления рычага в самоцентрирующий патрон имеют существенный недостаток, а именно: при установке рычага в патрон за обозначенные технологические базы центр масс рычага значительно смешен от оси вращения, что приведет к значительным колебаниям всей технологической системы в процессе обработки и не позволит вести обработку на оптимальных режимах резания. Кроме того, под действием режущих сил возможен вырыв заготовки из патрона, что недопустимо.
Решением данной проблемы может быть – использование планшайбы с балансиром. Поэтому, для надежного базирования и закрепления рычага на токарных операциях целесообразно использовать планшайбы с и рассмотреть такой вариант базирования на первой операции.
При третьем варианте базирования рычаг базируется на разжимной оправке планшайбы, в качестве установочной базы используется необработанный торец главного отверстия, в качестве двойной центрирующей необработанная внутренняя поверхность литого отверстия, опорная база приложена к наружной поверхности консольной части рычага.
При таком варианте базирования неравномерность распределения припуска при растачивании главного отверстия на последующей токарной операции составит:
А е |
Smax |
|
190 190 |
190 мкм |
|
|
|||
|
2 |
2 |
|
|
|
|
где Smax – максимальный зазор в сопряжении 56H11 (при установке рычага в
56h11
базирующее отверстие планшайбы при обработке внутренней полости). Эскиз базирования представлен на рисунке 51.
93
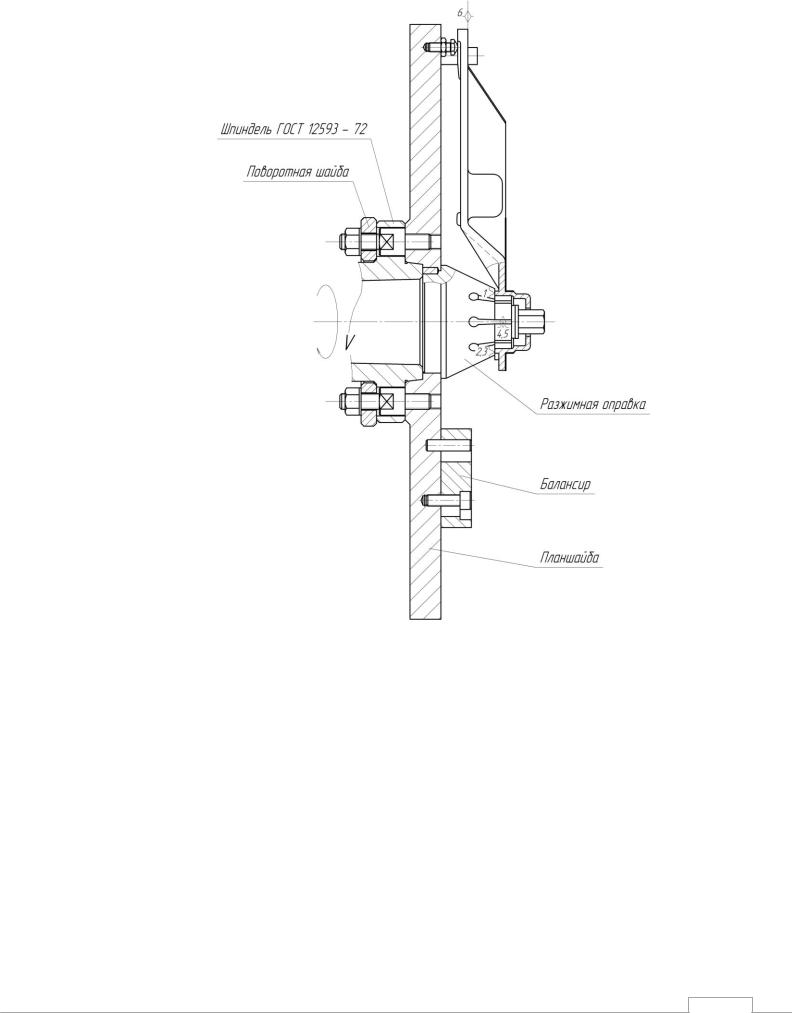
Рисунок 51 – Третий вариант базирования
Проведя сравнительный анализ трех вариантов базирования рычага на первой операции принимаем третий вариант, обеспечивающий:
надежное базирование и закрепление детали
уравновешивание колебаний технологической системы
безопасное ведение технологического процесса
комплект технологических баз для последующих операций
обработку на оптимальных режимах резания
Затраты на изготовления данного приспособления вполне окупятся в условиях серийного производства.
94

ПРАКТИЧЕСКИЕ ЗАНЯТИЯ ПО ВЫБОРУ ТЕХНОЛОГИЧЕСКИХ БАЗ
Первые этапы проектирования технологического процесса изготовления детали, включая выбор технологических баз, выполняются в следующем порядке:
1.Анализ служебного назначения изделия (сборочной единицы). Обоснование технических условий на изготовление изделия.
2.Размерный анализ изделия. Переход от служебного назначения изделия и технических условий на его изготовление к техническим условиям на отдельные детали.
3.Анализ служебного назначения детали.
Определение функций ее поверхностей и связей между ними.
4.Выбор комплекта постоянных технологических баз (КПТБ) для большинства операций технологического процесса.
5.Выбор баз на первой (первых) операциях технологического процесса для обработки поверхностей, входящих в КПТБ.
6.Разработка общей последовательности изготовления детали.
ПРАКТИЧЕСКОЕ ЗАНЯТИЕ № 1
Служебное назначение изделия, определение точностных требований и построение конструкторских размерных цепей.
Приведенный на рис.43 узел предназначен для передачи вращения и изменения его направления.
При монтаже узла в изделие он участвует своими размерами в решении следующих задач:
совмещении вершин делительных конусов зубчатых колес (замыкающие звенья А∆, Б∆);
обеспечении угла β∆ между осями делительных конусов колес.
Для выполнения узлом служебного назначения при сборке его должны быть обеспечены дополнительно следующие точностные требования:
натяг в подшипниках Г∆ соосность ввинчиваемых в корпус болтов с осью отверстий в крышках
подшипников Е∆.
В работе необходимо:
1. Определить численные значения перечисленных выше точностных требований (А∆, Б∆, β∆, Е∆).
2.Выявить размерные связи узла, обеспечивающие выполнение точностных требований и построить соответствующие конструкторские размерные цепи.
3.Выбрать метод достижения точности для каждой размерной цепи и соответствующего точностного требования.
95
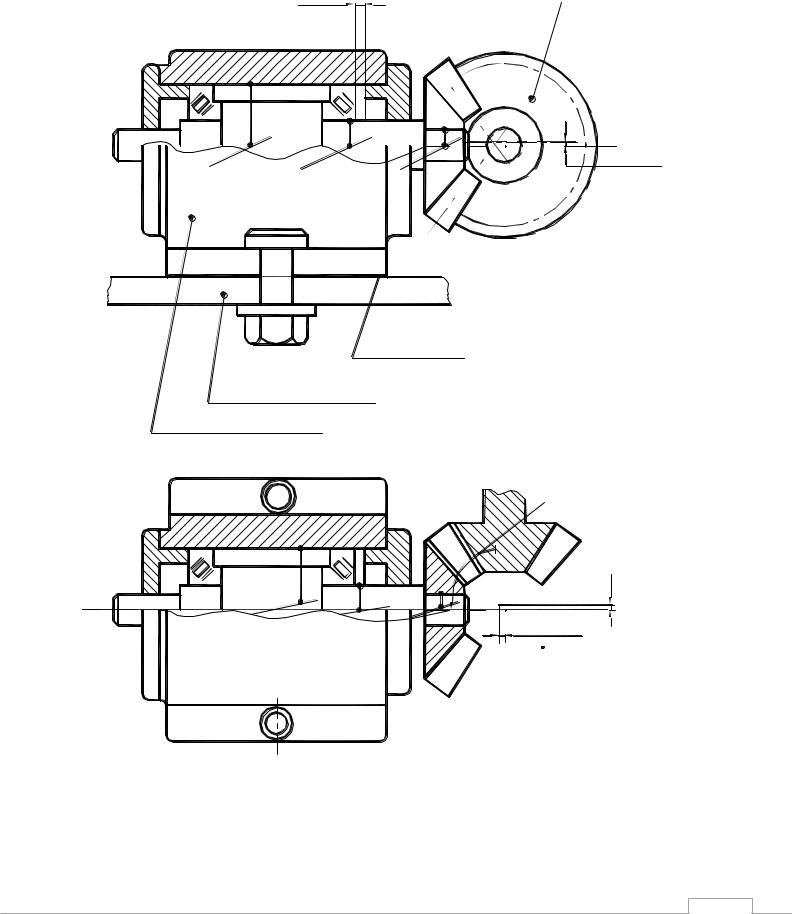
r =0+0,07+0,15 |
|
Узел привода №2 |
|
|
|
=0 |
+ |
|
|
- 0,02 |
|
|
Прокладка |
|
|
Основание привода |
|
|
|
Узел привода №1 |
|
|
|
|
|
|
|
|
|
|
|
|
|
|
+ |
|
|
|
- |
|
|
Б =0 0,06 |
|
|
|
+ |
|
|
|
- |
|
|
А =0 0,06 |
|
|
|
|
|
|
|
|
+ |
|
|
=90- 0,06/ 150 |
|
Рис.52.Узел привода №1
96

Методические указания
В рассмотренном примере изделием является привод, смонтированный на общей плите (рис.52).
Узлы N1 и N2 привода, несущие конические шестерни смонтированы, на общей плите – основании привода.
Регулирование положения узла N1 в вертикальной плоскости (при обеспечении точности замыкающего звена В∆ ) осуществляется с помощью прокладки, устанавливаемой между корпусом и общей плитой привода.
Переход от служебного назначения изделия (привода) к техническим условиям на изготовление детали (корпуса) можно осуществить в два этапа.
На первом этапе осуществляется переход от технических требований на изделие (А∆, Б∆, В∆, β∆) к точностным требованиям на узлы N1 и N2.
Эта задача решается размерной цепью (В∆, В1, В2, В3), приведенной на рис.53,а.
Точность в размерной цепи (В∆, В1, В2, В3) может быть обеспечена методом регулирования. Результатом расчета являются точностные требования к размерам В1 и В2 и параметры компенсатора (звено В2).
На втором этапе осуществляется переход от точностных требований к узлу N1 к техническим требованиям на отдельные детали узла (корпус).
Эта задача решается размерной цепью
/ , 1/ , 2/ , 3/ , 4/ , 5/ (рис.53,б).
Расчетом размерной цепи В/ устанавливается допуск на размер В/5 корпуса, которым он участвует в выполнении изделием его служебного назначения.
Аналогичный анализ приводится по всем размерным цепям, определяющим точностные требования к изделию (А∆, Б∆, β∆ ).
Примеры расчета подобных размерных цепей приведены в [7].
97

|
|
|
|
Ось делит ельного |
|
В4 |
|
|
|
|
|
|
|
|
|
|
|
|
|
|
|
|
||||||||||||
|
|
|
|
|
|
|
|
|
|
|
|
|
|
|
|
|
|
|
|
|
||||||||||||||
|
В1 |
|
|
конуса узла №1 |
|
|
|
Ось делит ельного |
||||||||||||||||||||||||||
|
|
|
|
|
||||||||||||||||||||||||||||||
|
|
|
|
|
|
|
|
|
|
|
|
|
|
|
|
|
|
|||||||||||||||||
|
|
|
Основание корпуса |
|
|
|
конуса узла №2 |
|
В3 |
|||||||||||||||||||||||||
|
|
|
|
|
|
|
||||||||||||||||||||||||||||
|
|
|
|
|
|
|
|
|
|
|
|
|
|
|
|
|
|
|
|
|||||||||||||||
|
|
|
|
|
|
|
|
|
|
|
|
|
|
|
|
|
|
|
|
|||||||||||||||
|
|
|
|
|
|
|
|
|
|
|
|
|
|
|
|
|
||||||||||||||||||
|
|
|
|
|
|
|
|
|
|
|
|
|
|
|
|
|
|
|
|
|
|
|
|
|
|
|
|
|
|
|
|
|||
|
Прокладка |
|
|
|
|
|
|
|
|
|
|
|
|
|
|
|
|
|
|
|
|
|
|
|
|
|
|
|
||||||
|
|
|
|
|
|
|
|
|
|
|
|
|
|
|
|
|
|
|
|
|
|
|
|
|
|
|
|
|||||||
|
|
|
|
|
|
|
|
|
|
|
|
|
|
|
|
|
||||||||||||||||||
|
В2 |
|
|
|
|
Поверхност ь общей плит ы- основания привода |
||||||||||||||||||||||||||||
|
|
|
|
|
|
|
|
|
|
|
|
|
|
|
|
|
|
|
|
|
|
|
|
|
|
|
|
|
||||||
|
|
|
|
а) |
|
|
|
|
|
|
|
|
|
|
|
|
|
|
|
|
|
|
|
|
|
|
|
|
|
|
|
|||
|
|
|
|
|
|
|
|
|
|
|
|
|
|
|
|
|
|
|
|
|
|
|
|
|
|
|
|
|||||||
Ось делит ельного конуса узла №1 |
|
|
|
В'1 |
|
|
|
|
|
|
|
|
|
|
|
|
|
|
|
|
||||||||||||||
|
|
|
|
|
|
|
|
|
|
|
|
|
|
|
|
|
|
|||||||||||||||||
|
|
|
|
|
|
|
|
|
|
|
|
|
|
|
|
|
|
|
|
|
|
|
|
|
|
|
|
|
|
|
|
|
||
|
|
|
|
|
|
|
|
|
|
|
|
|
|
|
|
|
|
|
|
|
|
|
|
|
|
|
|
|
|
|
|
|||
|
|
|
|
Ось от верст ия в шест ерне |
|
|
|
|
В'2 |
|
|
|
|
|
|
|
|
|||||||||||||||||
|
|
|
|
|
|
|
|
|
|
|
|
|
|
|
|
|
|
|
|
|||||||||||||||
|
|
|
|
|
|
|
|
|
|
|
|
|
|
|
|
|
|
|
|
|
|
|
|
|
|
|
|
|
|
|
|
|
||
|
|
|
|
|
|
|
|
|
|
|
|
|
|
|
|
|
|
|
|
|
|
|||||||||||||
|
Ось цент рирующей шейки вала |
|
|
|
|
|
В3 |
|||||||||||||||||||||||||||
|
|
|
||||||||||||||||||||||||||||||||
|
|
|
|
|
|
|
|
|
|
|
|
|
|
|
|
|
|
|
|
|
|
|
|
|
|
|
' |
|
|
|
|
|
|
|
|
|
|
|
|
|
|
|
|
|
|
|
|
|
|
|
|
|
|
|
|
|
|
|
|
|
|
||||||||
' |
|
|
Ось опорной шейки вала |
|
|
|
|
|
В4 |
|||||||||||||||||||||||||
|
|
|
|
|
||||||||||||||||||||||||||||||
|
|
|
|
|
|
|||||||||||||||||||||||||||||
|
|
|
|
|
|
|
|
|
|
|
|
|
|
|
|
|
|
|
|
|
|
' |
|
|
|
|
||||||||
|
В1=В |
|
|
|
|
|
|
|
|
|
|
|
|
|
|
|
|
|
|
|
|
|
|
|
||||||||||
|
|
Ось от верст ия в корпусе |
|
|
|
|
|
|
|
|
||||||||||||||||||||||||
|
|
|
|
|
|
|
|
|
|
|
|
|
|
|
|
|
||||||||||||||||||
|
|
|
|
|
|
|
|
|
|
|
|
|
|
|
|
|
|
|
|
|
|
|
|
|
|
|
|
|
|
|
|
|
|
|
В'5
Основание корпуса
б)
Рис.53.Размерный анализ узла привода: а – размерная цепь В; б – размерная цепь В/
98
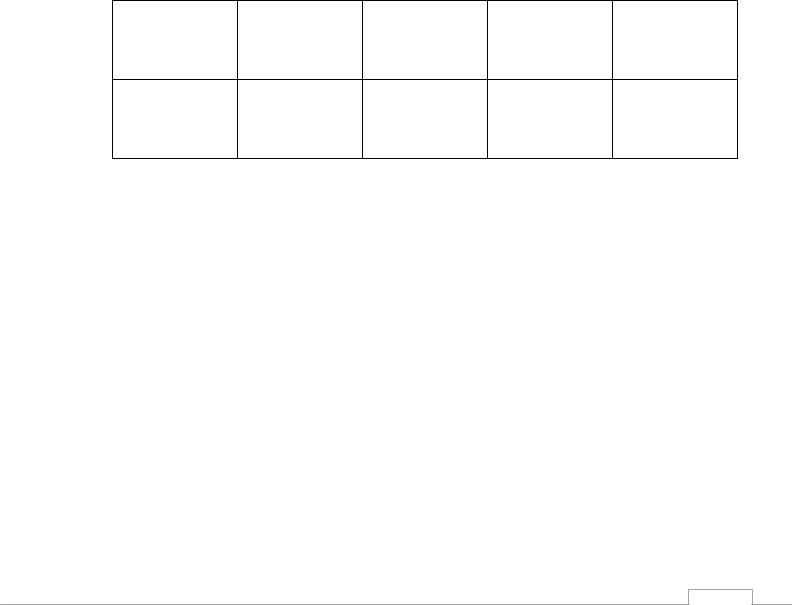
ПРАКТИЧЕСКОЕ ЗАНЯТИЕ № 2
Точностные требования к детали и выбор комплекта постоянных технологических баз (КПТБ).
Целью работы является обоснование комплекта постоянных технологических баз, используемых на большинстве операций технологического процесса изготовления корпусной детали сборочной единицы, приведенной на рис.54.
Порядок выполнения
1. Выявить, какими размерами корпус участвует в достижении точностных требований к узлу, и записать эти размеры в таблицу.
Таблица 2
ТТ №
Размер
2.На основе расчета размерных цепей установить допуски на выявленные в п.1 размеры корпуса.
3.Сформулировать служебное назначение корпуса с точки зрения его участия в достижении точностных требований к узлу.
4.Составить граф размерных связей между поверхностями корпуса по трем координатным осям.
Размерные связи и обозначение поверхностей корпуса приведены на рис.45.
5.На основе анализа размерных связей по каждой координатной оси выявить комплект из трех поверхностей (баз), по отношению к которым ориентированно большинство поверхностей в направлении данной оси.
6.Разработать теоретические схемы базирования корпуса.
Выбрать КПТБ, в наибольшей степени соответствующий всем его размерным связям и приемлемый для большинства операций технологического процесса изготовления корпуса.
7. Привести схему приспособления, материализирующего предложенный вариант КПТБ.
99

С целью выбора КПТБ размерные связи корпуса (рис.54) целесообразно представить в виде графа связей поверхностей (рис.55).
Граф в данном случае служит для наглядного представления связей и удобства их анализа.
Граф позволяет установить:
1.Угловые и линейные связи между поверхностями.
2.С какой поверхностью (поверхностями) связано большинство других поверхностей.
3.Приоритетность связей (т.е. степень их жесткости).
4.Возможность (физическая ) использования поверхностей в качестве баз.
Из графа следует, что большинство поверхностей корпуса связано с поверхностями основных конструкторских баз корпуса – основанием 6 и осями крепежных отверстий 30 и 120, которые целесообразно использовать в качестве КПТБ на большинстве операций технологического процесса.
После выбора КПТБ устанавливаются точностные требования к базам (в данном случае – точности расстояния между осями отверстий 30 и 120, см. прил.4).
100