
Базирование и базы в машиностроении
.pdf
базы для выполнения первой или первых операций технологического процесса. На этих операциях обрабатывают поверхности, которые затем используют в качестве технологических баз на большинстве последующих операций технологического процесса. При выборе технологических баз на первой операции необходимо исходить из решения следующих задач:
1.Установление связей, определяющих расстояния и повороты поверхностей, получаемых в результате обработки, относительно свободных необрабатываемых поверхностей.
2.Обеспечение равномерного распределения фактического
припуска на поверхностях, подлежащих обработке.
Первая задача определяется техническими условиями, вытекающими из служебного назначения детали. Вторая задача определяется требованиями технологии. При решении второй задачи при выборе баз на первой операции руководствуются двумя основными положениями:
необходимостью сохранения наиболее качественного слоя материала на поверхностях детали, подвергающихся при ее работе в машине интенсивному износу:
необходимостью обеспечения равномерного распределения припуска на обработку поверхностей (прежде всего, отверстий). При обработке плоскостей равномерный припуск позволяет снять минимально необходимый слой материала и сохранить наиболее качественную зону поверхностного слоя материала.
При обработке отверстий равномерный припуск (рис.39.) позволяет устранить колебания упругих отжатий инструмента и вызываемые ими погрешности геометрической формы и за счет этого уменьшить необходимое количество технологические переходов, необходимых для достижения заданной точности геометрической формы.
Таким образом, в качестве количественных критериев для сравнения вариантов базирования на первой или первых операциях принимают точность связи между обрабатываемыми и необрабатываемыми поверхностями и равномерность припуска на обработку.
Для выбора наиболее предпочтительного варианта базирования необходимо проанализировать возможные их схемы путем
71
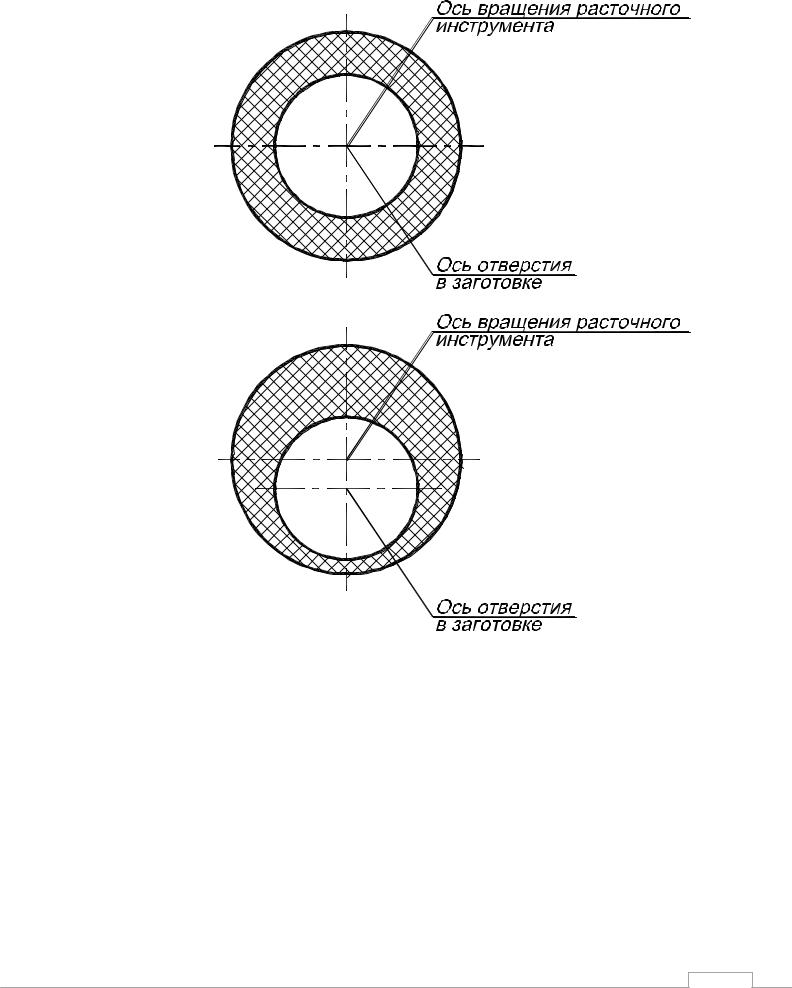
Рис.39. Распределение припуска на обработку отверстия а) равномерный припуск;
б) неравномерный припуск, вызванный несовпадением оси литого отверстия и оси вращения расточного инструмента
72

выявления и расчета возникающих технологических размерных связей. Для этого в первую очередь надо определять то место в технологическом процессе, где поставлен гая задача находит свое окончательное решение. Так, если стоит задача обеспечения требуемой точности положения обрабатываемой поверхности относительно свободных необрабатываемых поверхностей, то ее решение следует искать на операции окончательной обработки этой поверхности. Если же стоит задача обеспечения равномерного припуска при обработке определенной поверхности заготовки» то ее решение проявляется на операций обработки этой поверхности.
Определив операцию, на которой решается поставленная задача, т.е. место получения замыкавшего звана, необходимо выявить все составляющие звенья этой технологической размерной цепи. Для этого следует найти те межпереходные размеры, полученные на данной и предшествующих операциях, и те размеры заготовки» которые влияют на точность замыкающего звена.
Пример. Обеспечить в процессе изготовления корпуса статора электродвигателя симметричность отверстия относительно необрабатываемых наружных поверхностей в горизонтальной плоскости (рис.40. ).
Несимметричность А∆ обнаружится при выполнении расточной операций и через составляющее звено А1 будет зависеть от принятой схемы базирования детали на первой операций, в которой обрабатываются плоскость основания и установочные отверстия. На (рис.40,б, в) приведены два варианта базирования детали на первой операции, отличающиеся только тем, что в первом варианте опорная база (точка 6) создана на боковой поверхности корпуса, а во втором варианте в качестве опорной базы принята плоскость симметрии наружных поверхностей корпуса. Скрытая опорная база во втором варианте может быть создана с помощью самоцентрирующего приспособления, губки которого условно показаны стрелками, обеспечивающего точность расположения обрабатываемых установочных отверстий относительно плоскости симметрии.
73
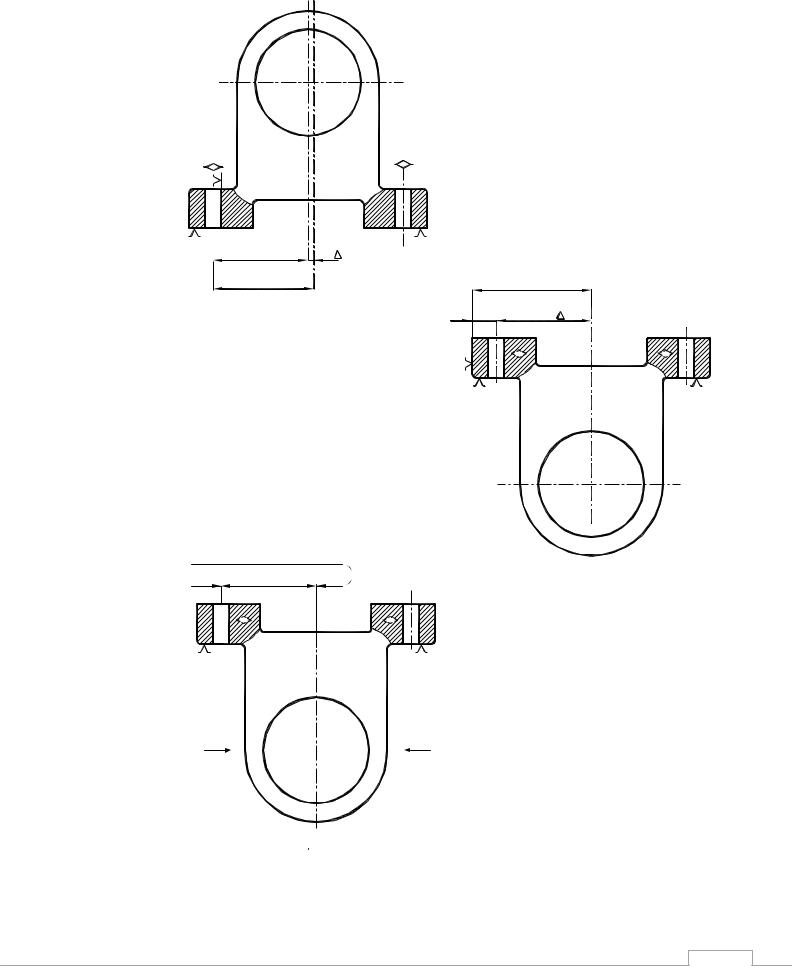
4 |
|
|
6 |
|
|
5 |
|
|
|
1 |
A2 |
A |
2,3 |
|
|
|
|
||
|
A1 |
|
|
Б2 |
|
a) |
|
Б1 |
А1=Б |
|
|
|
|
|
|
|
|
|
4 |
|
|
|
6 |
|
|
|
|
|
1 |
А1=В
4 |
1
б)
5 |
2,3 |
5 |
2,3 |
в) 6
Рис 40. Анализ вариантов базирования при обработке корпуса
74

статора электродвигателя
Анализируя технологические размерные цепи и оценивая возможные погрешности их составляющих звеньев, получит:
в первом варианте
ωА∆=ωА1 + ωА2 = ωБ1 + ωБ2 + ωА2=0,1+2,4+0,1=2,6мм;
во втором варианте
ωА∆=ωА1 + ωА2 = ωВ∆+ ωА2=0,3+0,1=0,4мм
Пример . При обработке корпуса (рис. 41 ) необходимо обеспечить равномерность припуска в отверстии D.
Неравномерность припуска обнаружится на операции растачивания отверстия. Для большинства операций обработки корпуса в качества технологических баз используется основание и два технологически отверстия. При избранной схеме базирования детали на расточной операции неравномерность припуска проявится как относительное смещение оси отверстия в заготовке и оси вращения борштанги с резцом (рис. 41,а ). Рассматривая решение этой задачи в вертикальной плоскости, такое смещение можно представить замыкающим звеном А∆ размерной цепи А, составляющими звеньями которой будут: A1 - расстояние между осью отверстия в заготовке и установочной технологической базой детали и А2 - расстояние между осью обработанного отверстия (осью вращения борштанги с резцом) и той же базой детали. Точность расстояния А2 зависит только от расточной операции. Расстояние А1 установится при обработке основания К на первой операции технологического процесса. Точность расстояния A1 будет зависеть от схемы базирования на первой операции. При обработке поверхности К могут быть использованы различные варианты базирования детали.
По первому варианту (рис.41,б) в качестве установочной базы можно использовать поверхность полок (т. 1, 2,-3), а в качестве направляющей и опорной технологических баз – боковые поверхности основания детали.
75
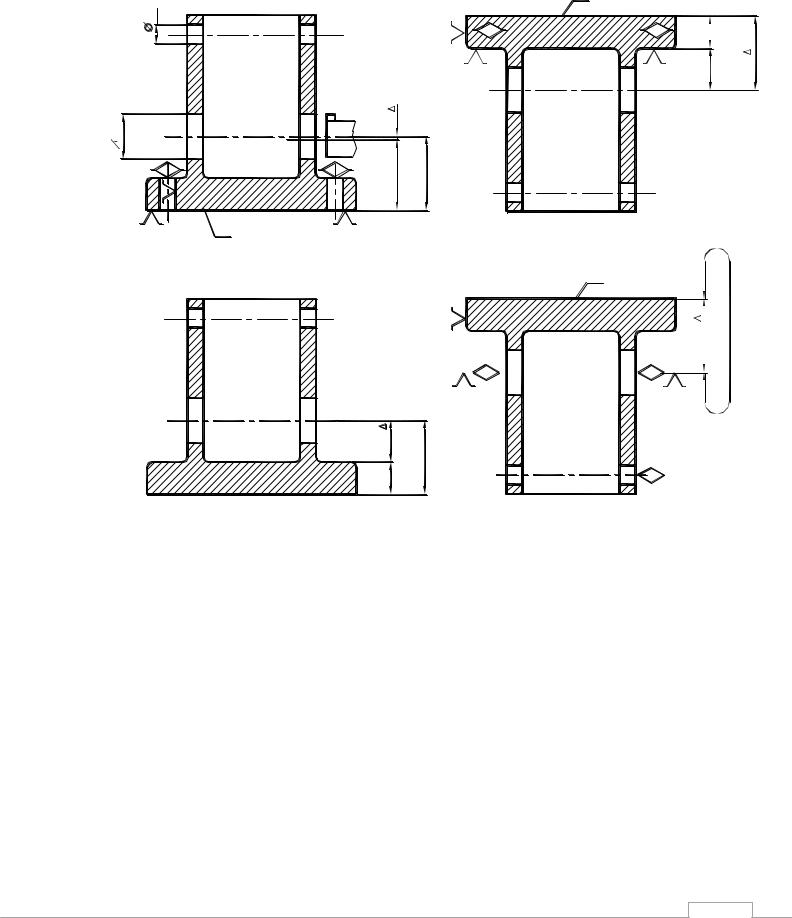
|
|
|
|
|
|
K |
d |
|
|
|
|
4 |
|
|
|
|
|
6 |
5 |
|
|
|
|
|
|
||
|
|
|
|
|
1,2 |
3 |
|
|
|
|
|
|
|
|
|
|
А |
|
|
|
D |
|
|
|
|
|
|
5 |
|
6 |
А1 |
А2 |
|
|
|
4 |
|
|
|
|
|
1,2 |
K |
3 |
|
|
|
|
а) |
|
|
|
|
б) |
|
|
|
|
|
|
|
K |
|
|
|
|
6 |
|
|
|
|
|
|
|
3 |
4 |
|
|
|
|
|
1 |
2 |
|
|
|
Б1=В |
В1 |
|
|
|
|
|
В2 |
|
|
5 |
в) |
|
|
|
|
|
г) |
Б2 |
|
|
Б1 |
|
А1=Б |
|
||
|
|
А1=Г
Рис.41. Анализ вариантов базирования при обработке отверстий в корпусной детали
76

При такой схеме базирования детали на первой операции расстояние А1 получается как замыкающее звено Б∆ трехзвенной размерной цепи Б:
ωА1=ωБ∆=ωБ1+ ωБ2.
Составляющее звено Б2 – это выдерживаемый размер при обработке детали на настроенном станке, а звено Б1 – размер, принадлежащий заготовке. Его точность достигается в процессе получения заготовки и зависит от простановки размеров на чертеже заготовки. Если размеры заготовки будут проставлены и выдержаны в процессе ее получения так, как показано на рис.42в, то размер Б1 будет
формироваться как замыкающее звено В∆ размерной цепи В и его погрешность ωБ1
будет равна погрешности ωВ∆, представляющей сумму погрешности составляющих звеньев В1 и В2:
ωБ1 =ωВ∆= ωВ1+ ωВ2.
В соответствии с выявленной схемой образования погрешности ωА∆ в первом варианте базирования детали на первой операции
ωА∆=ωА2 + ωА1 = ωА2 + ωБ2 + ωБ1=ωА2 + ωБ2 + ωВ1 + ωВ2
Численные значения возможных погрешностей: ωА2, ωБ2, ωВ1, ωВ2, - могут бать определены с помощью нормативов средне экономической точности используемых методов обработки и допусков на размеры заготовки. В соответствии с этими нормативами и при условии, что в рассматриваемом примере габаритные размеры корпусной детали находятся в пределах 280 – 500мм, расстояние В1 – в пределах 120 – 280мм, расстояние В2 будет менее 50мм, а отливка будет выполнена по второму классу точности.
ωА∆=0,1+0,3+2,4+1,6=4,4мм
77

Во втором варианте может быть выбрана схема базирования на первой операции, приведенная на рис.41, г: отверстие в заготовке большего диаметра использовано в качестве двойной направляющей технологической базы, роль опорных баз выполняют отверстие меньшего диаметра и боковая поверхность основания. В этом случае расстояние А1 будет получено как замыкающее звено Г∆ размерной цепи технологической системы, на которой выполняется первая операция:
ωА∆= ωА2+ ωА1= ωА2+ ωГ∆=0,6мм
Так как второй вариант дает более короткий путь достижения точности А∆ и полностью исключает влияние погрешностей заготовки на величину неравномерности припуска при обработке отверстия ØD, его можно считать более удачным решением поставленной задачи.
Пример. Обеспечить при обработке направляющих поверхностей станины токарного станка с сохранение наиболее качественной и износостойкой зоны поверхностного слоя материала.
Станины отливают направляющими вниз, чтобы получить на них наиболее плотный и однородный слой материала. Следовательно, для сохранения износостойкости направляющих с них необходимо снять при обработке равномерный и минимальный слой материала.
Эта задача решается путем выбора рациональной последовательности обработки станины, в частности, построением первой операции – ее содержанием и схемой базирования. На первой операции следует обрабатывать поверхности основания, используя в качестве технологических баз направляющие поверхности станины.
78
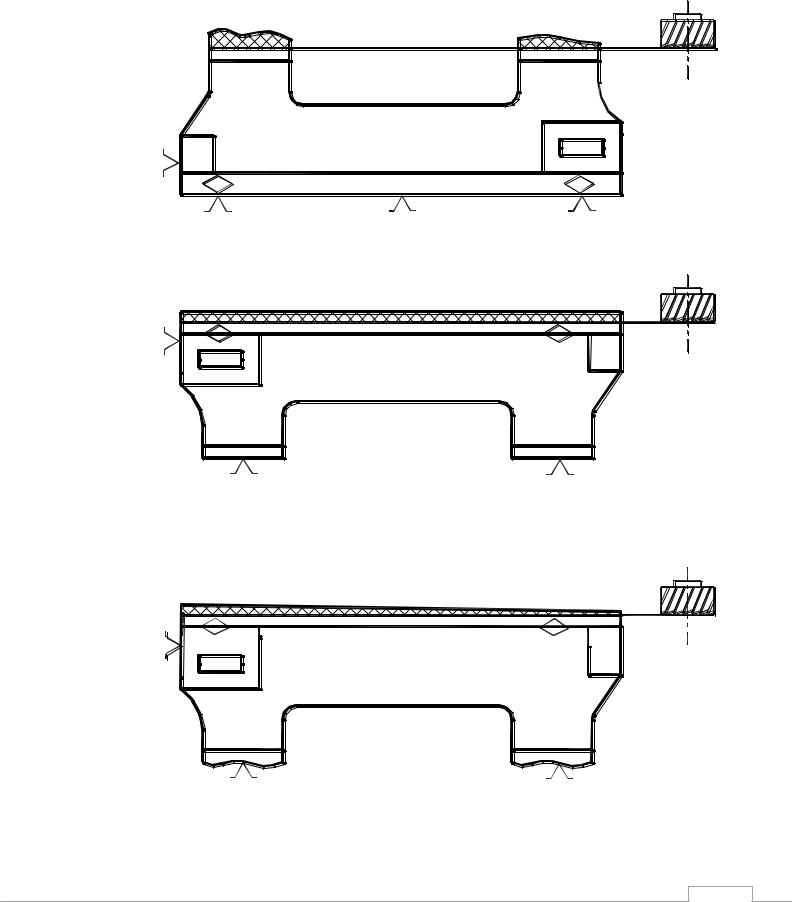
6 |
|
4 |
5 |
1 |
2 |
3 |
а) |
|
|
6 |
4 |
5 |
|
|
1,2
б)
6 |
4 |
|
1,2
в)
3
5
3
Рис.42. Анализ вариантов базирования на первой операции обработки станины
79

При этом погрешности литой заготовки будут удалены в виде неравномерного слоя металла, снимаемого с поверхностей ножек (рис.42, а). На следующей операции обработки направляющих поверхностей обработанные поверхности ножек используются в качестве технологических баз. Это позволит снять с направляющих равномерный слой металла (рис.42, б).
Если обработку станины начать с фрезерования направляющих поверхностей с установкой на необработанные поверхности ножек, то наиболее качественный слой металла может быть удален путем снятия неравномерного припуска.
Неравномерность припуска возникает из – за установки на необработанные поверхности ножек (рис.42,в).
80