
ПОЛИКОНДЕНСАЦИОННЫЕ 2
.pdf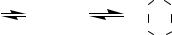
греванием его выше 140 – 1600 С. Деполимеризация проходит без плавления с образованием газообразного мономерного формальдегида. γ-Полиоксиметилен, являясь простым эфиром, де-
полимеризуется только при нагревании с разбавленными кислотами, гидролизующими эфир-
ные группы.
Образование полиоксиметиленгликолей – лишь одна из схем полимеризации альдегидов -
полимолекулярная. Другая – тримолекулярная схема. В соответствии с нею, нагревание кон-
центрированного водного раствора формальдегида в присутствии кислот (или кислых катализа-
торов) приводит к образованию циклического триоксиметилена - триоксана – одного из про-
дуктов, используемого для получения высокомолекулярного полиформальдегида.
|
O |
|
|
|
|
|
|
|
|
|
О |
||
3 |
|
|
|
|
|
|
|
|
|
|
Н2С |
СН2 + H O |
|
H-C |
-H + H O |
|
|
|
HO(CH ) H |
||||||||
|
|
|
|||||||||||
|
|
|
|
|
|||||||||
|
2 |
2 3 |
|
|
|
|
|
2 |
О О
СН2
Аналогично ацетальдегид, полимеризуясь по тримолекулярной схеме, образует парааце-
тальдегид (паральдегид).
Циклические олигомеры, получаемые по тримолекулярной схеме, являются индивидуаль-
ными веществами, характеризующимися определёнными физическими постоянными (темпера-
турами плавления, кипения). В этом их принципиальное отличие от полимеров, полученных по полимолекулярной схеме, состоящих из смеси полимергомологов с разной степенью полиме-
ризации.
Для отрасли пластмасс рассмотренные полиоксиметилены самостоятельного значения не имеют. Они используются как исходные продукты для синтеза многих химических соединений,
в том числе и для получения высокомолекулярного полиформальдегида.
2.1.2. Получение высокомолекулярного полиметиленоксида В промышленности высокомолекулярный полиметиленоксид (полиформальдегид) получа-
ется двумя способами: полимеризацией безводного мономера (формальдегида) и его цикличе-
ского тримера — триоксана.
2.1.2.1. Полимеризация безводного формальдегида Формальдегид, как отмечалось выше, способен к самопроизвольной полимеризации под
действием как электрофильных, так и нуклеофильных агентов, а также в присутствии даже не-
значительных количеств (следов) воды. Но для получения высокомолекулярного полиформаль-
дегида необходимо, чтобы содержание примесей в мономере (воды, метанола, муравьиной кис-
лоты и других) не превышало 0,05 – 0,1%. Недостаточно чистый и сухой формальдегид не об-
разует полимеров с молекулярной массой более 1000, пригодных для изготовления технических изделий. Это обязывает включать в технологию получения полиформальдегида в качестве обя-
зательной стадии процесса стадию подготовки формальдегида к полимеризации. Подготовка заключается в удалении влаги, метанола, муравьиной кислоты и прочих примесей.
209
Начинается подготовка с выделения формальдегида из транспортных растворов формали-
на. Для этого концентрированный формалин нагревается в аппарате-испарителе. Выделяющий-
ся при нагревании раствора формальдегид проходит холодильники, газоотделители, где осво-
бождается от основного количества унесённой из испарителя влаги, и поступает в выморажи-
ватель – секционированный кожухотрубный теплообменник, нижняя часть трубчатки которого охлаждается рассолом, а верхняя – обогревается паром. Газообразный формальдегид, проходя через нижнюю часть вымораживателя, частично полимеризуется, химически связывая воду в гидраты. Образующийся параформ оседает на стенках трубчатки, адсорбирует другие примеси и по мере своего накопления счищается специальным инструментом. В дальнейшем он рас-
творяется в воде, раствор концентрируется в ректификационной колонне и регенерированный формалин возвращается в процесс. Прошедший через вымораживающую зону газообразный сухой формальдегид подогревается в верхней части аппарата для предупреждения прежде-
временной полимеризации и поступает на стадию превращения в полимер.
Полимеризация проводится в жидкой инертной среде – бензине, толуоле, циклогексане и других. Наиболее распространенной средой служит уайт-спирит.
Уайт-спирит (английское white spirit, от white - белый, бесцветный и spirit -
спирт, бензин) - смесь жидких углеводородов, выкипающая в пределах 160—200°С.
Содержит до 16% ароматических углеводородов. Полностью свободен от кислот,
щелочей, воды, непредельных углеводородов. Мало токсичен. Получается при пря-
мой перегонке нефти. Основное применение – растворитель в лакокрасочной про-
мышленности.
Полимеризатор – цилиндрический аппарат, охлаждаемый через рубашку водой. Имеет пропеллерную мешалку и снабжён обратным холодильником. В этот аппарат подаются из мер-
ников уайт-спирит и раствор катализатора полимеризации (стеарата кальция) в уайт-спирите.
Формальдегид подводится к реактору по обогреваемому трубопроводу и барботируется через перемешиваемую жидкость. Полимеризация проводится при 30 – 600С.
Барботирование - продавливание газа или пара через слой жидкости. Устройст-
вами для проведения этого процесса служат барботеры — трубы с мелкими отвер-
стиями (3 – 6 мм), ситчатые или колпачковые тарелки абсорберов и ректификацион-
ных колонн. При движении пузырьков газа (пара) через жидкость создаётся большая межфазная поверхность, что способствует тепло- и массообменным процессам, бы-
строму растворению газа, а также перемешиванию и химическому взаимодействию газов с жидкостями. Барботирование применяют для прогрева жидкости острым па-
ром, а также для перемешивания агрессивных жидкостей.
Для регулирования молекулярной массы образующегося полимера в газообразный фор-
мальдегид или непосредственно в жидкую среду реактора добавляются в требуемых количест-
210
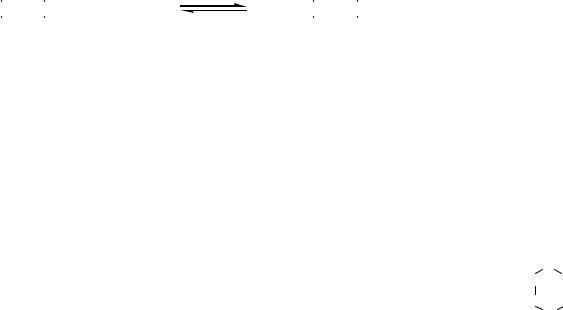
вах регуляторы роста цепей – спирты, вода, кислоты.
Гомополимер, который нерастворим в реакционной среде, выпадает по мере образования в виде мелкодисперсного порошка. Суспензия полимера в уайт-спирите далее разделяется на центрифуге и растворитель направляется на регенерацию. Полученный полиметиленоксид не-
однороден по химическому составу. Большинство его макромолекул содержит концевые сво-
бодные гидроксильные группы из-за протекания при полимеризации реакций передачи цепи на воду. Такие макромолекулы имеют малую термическую стойкость, деполимеризуются при на-
гревании подобно параформальдегиду, α- и β- полиоксиметиленам, выделяя формальдегид.
Поэтому выделенный полиформальдегид на второй стадии производства подвергается стаби-
лизации. В её основе - «блокировании» концевых гидроксильных групп, т.е. превращение их в химически устойчивые фрагменты. Таковыми могут быть структуры простых и сложных эфи-
ров. Наиболее технически удобным решением служит обработка полученного полиформальде-
гида уксусным ангидридом, в ходе которой гидроксильные группы превращаются в ацетаты.
HO |
|
|
CH2O |
|
|
|
H + 2 (CH CO) O |
|
|
|
CH COO |
|
|
CH2O |
|
|
|
COCH |
+ 2 CH COOH |
|
|
|
|
|
|
|
|
|
|
|
|
||||||||
|
|
|
|
|
|
|
|
|
|
|
|
|
|||||||
|
|
|
|
|
n |
3 2 |
3 |
|
|
|
|
n |
3 |
3 |
Ацетилирование проводится в аналогичном аппарате в среде уайт-спирита добавлением уксусного ангидрида, пиридина и ацетата натрия. Температура массы при ацетилировании 135
– 1400С; продолжительность операции около 4-х часов. После охлаждения реакционная смесь разделяется на центрифуге, полиформальдегид многократно промывается водой и высушивает-
ся до влажности не более 0,2%. Сухой порошкообразный продукт в специальном смесителе смешивается с добавками, способствующими повышению его термостабильности (смесь дифе-
ниламина, полиамида и диоксида титана), и гранулируется.
2.1.2.2. Полимеризация триоксана |
|
|
|
Триоксан или триоксиметилен (мета-формальдегид) – стойкий цик- |
|
О |
|
лический тример формальдегида, обладающий свойствами циклическо- |
Н2С |
|
СН2 |
|
|||
О |
О |
||
0 |
|
СН2 |
|
го простого эфира или ацеталя. Тпл = 62 С. Удовлетворительно раство- |
|
|
|
рим в воде (21,1 г в 100 см3 воды при 250С); хорошо растворяется в спирте и во мно-
гих других органических растворителях, в том числе – в лёгких бензиновых углево-
дородах. Сравнительно устойчив в нейтральных и щелочных средах, медленно гид-
ролизуется в растворах сильных кислот. При нагревании в присутствии серной,
фосфорной кислот, некоторых хлористых солей превращается в формальдегид. Этим свойством пользуются в технике для получения безводного формальдегида. Чистый триоксан при нагревании выше 2000С испаряется без деполимеризации. Получают триоксан перегонкой водного раствора формальдегида, содержащего около 2% сер-
ной кислоты. Образовавшийся тример экстрагируют из раствора органическим рас-
творителем.
211
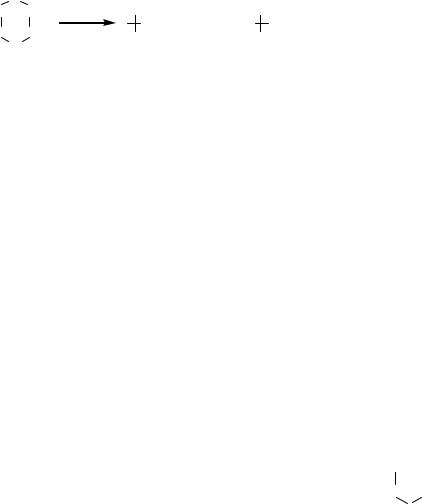
Триоксан, в отличие от формальдегида, - твёрдый устойчивый продукт, который очищается от примесей ещё в процессе своего производства и в дополнительной очистке не нуждается.
Полимеризация его может проводиться в газовой (выше 1150С), жидкой, твёрдой фазах или в растворе в присутствии катализаторов. Полимеризация триоксана в полиформальдегид проис-
ходит с раскрытием цикла под влиянием катионных катализаторов.
О |
|
n Н2С СН2 |
CH2O - CH2O - CH2O n |
О О |
СН2
Образующийся продукт по химическому строению и свойствам идентичен, получаемому из
формальдегида. Но особенности кристаллического строения его частиц не позволяют прово-
дить гетерогенное ацетилирование, необходимое для стабилизации. Поэтому для ацетилирова-
ния полимер необходимо полностью растворять в чистом уксусном ангидриде или в его смеси с растворителем при 1500С, а затем высаживать. Дальнейшая обработка аналогична выше опи-
санной.
Громоздкость подобного способа стабилизации гомополимера очевидна. В связи с этим в
промышленности предпочтительно получение из триоксана не гомополимера, а сополимера с другими сомономерами или сополимерами, содержащих связи С – С, например, с оксидом эти-
лена, ацеталями, 1,3-диоксоланом и др. При статическом распределении сомономеров в макро-
молекулах полиформальдегида разрыв ацетальных связей под действием температуры, кисло-
рода, кислот приводит к деполимеризации не всей макромолекулы, как в случае гомополимера,
а только участка цепи, заключённого между двумя С – С связями. |
В промышленности из сомо- |
||||
номеров чаще всего используется 1,3-диоксолан |
|
|
|
|
|
1,3-Диоксолан (этиленформаль, гликольформаль) |
- жидкость с |
Н2С |
|
|
СН2 |
|
|
||||
Ткип = 75-760С. Смешивается с водой в любых соотношениях, является |
|
|
|||
O |
|
|
|
||
|
O |
||||
хорошим растворителем для многих органических веществ, в том числе |
|
СН2 |
и для полимеров. Устойчив в нейтральной и слабощелочной средах, кислотами гид-
ролизуется. Полимеризуется и сополимеризуется с эфирами непредельных кислот.
Получается нагреванием этиленгликоля с формальдегидом
Сополимер триоксана с диоксоланом при содержании последнего 2 – 5% принципиально не отличается по физико-механическим свойствам от гомополимера, но по устойчивости к ще-
лочным реагентам и действию высоких температур значительно превосходит гомополимер,
стабилизированный с помощью уксусной кислоты. Последнее особенно важно при переработ-
ке поликарбонатов в изделия.
По одной из технологий получение сополимера триоксана с 1,3-диоксоланом проводится в среде бензина или уайт-спирита. В реакторе вначале готовится смесь растворов триоксана, ди-
оксолана и катионного катализатора (бутилового эфира фторида бора – BF3·O(C4H9)2). Количе-
212

ство диоксолана 2 – 6% от триоксана. Далее масса перемешивается при 65 – 700С и давлении
0,05 - 0,06 МПа до конверсии 95 – 98%. Реакция сополимеризации описывается уравнением:
|
О |
Н2С |
|
|
|
|
СН2 |
|
|
|
|
|
|
|
|
|
|
|
|
|
|
|
Н2С |
|
СН2 |
|
|
|
|
|
|
|
|
|
|
|
|
|
|
|
|
|
|
||
|
|
|
|
|
|
|
|
|
|
|
|
|
|
|
|
|
|
|||||
n |
|
+ |
m |
|
|
|
|
|
|
CH2 |
- O |
|
|
|
CH2 |
- CH2 |
- O - CH2 |
- O |
|
|
|
|
О |
О |
O |
|
O |
|
|
|
n |
m |
|||||||||||||
|
|
|
|
|
|
|
|
|
|
|
||||||||||||
|
СН2 |
|
|
СН2 |
|
|
|
|
|
|
|
|
|
|
|
|
|
|
Образовавшийся в виде порошка сополимер отделяется от жидкой среды центрифугирова-
нием, промывается горячей водой, вакуумируется при нагревании для отделения от захваченно-
го бензина, высушивается, смешивается со стабилизирующими добавками и гранулируется.
Полученный сополимер содержит 5 – 10% (по массе) концевых нестабильных полуаце-
тальных блоков - СН2О -. Удаление этих блоков и получение сополимера, стойкого до 260 –
2700С, может производиться двумя способами. Один – способ термической деструкции. Он сводится к нагреванию сополимера в вакууме при температурах выше температуры его плав-
ления (190 – 2200С). В ходе такой термообработки происходит деполимеризация концевых по-
луацетальных групп, которая прекращается, когда концевыми группами сополимера стано-
вятся оксиэтиленовые.
CH2 - O |
|
|
|
|
|
|
CH2 - CH2 - O - CH2 - O |
|
|
|
|
|
|
|
|
|
|
|
|
||||||||
|
n |
|
|
|
|
|
|
m |
|
|
|
|
|
|
|||||||||||||
|
|
|
|
|
|
|
|
|
|
|
|
|
|
|
|
|
|
|
|
|
|
||||||
|
|
|
|
|
|
|
|
|
CH2 - O |
|
|
|
|
|
OCH2 |
- O - CH2 - CH2 |
- O |
|
|
|
+ mH C = O |
||||||
|
|
|
|
|
|
|
|
|
|
|
|
|
|
|
|
|
|||||||||||
|
|
|
|
|
|
|
|
|
|
n |
|
|
|||||||||||||||
|
|
|
|
|
|
|
|
|
|
|
|
||||||||||||||||
|
|
|
|
|
|
|
|
|
|
|
|
|
|
|
|
|
|
|
|
|
|
|
m |
2 |
Процесс термостабилизации может, в принципе, совмещаться с гранулированием, но в этом случае необходимо предусматривать наличие у экструдера активно работающих вакуум-
отсосов для своевременного удаления выделяющегося формальдегида, блок оборудования для его улавливания и регенерации.
Второй способ стабилизации – химический. В процессе получения порошок сополимера после водной промывки и удаления бензина обрабатывается в автоклаве при температуре 130 –
1400С раствором аммиака. При этом происходит отщепление полуацетальных группировок и их взаимодействие с аммиаком с образованием уротропина. Затем сополимер отмывается горя-
чей водой от избытка аммиака и хорошо растворимого в воде уротропина, высушивается,
смешивается с термо- и светостабилизаторами и гранулируется.
2.1.3. Свойства и применение полиметиленоксида Полиметиленоксид - линейный полимер формальдегида - белое рогоподобное кристалли-
ческое вещество с молекулярной массой 30000—120000. Степень кристалличности 70 - 100% в
зависимости от условий получения. Плотность 1,41 - 1,43 г/см3 (20 °С).
Полиформальдегид - один из наиболее жёстких конструкционных термопластов с высоки-
ми механической прочностью, усталостной выносливостью, износостойкостью, влагостойко-
стью, низким коэффициентом трения, стабильностью размеров у изготовленных из него дета-
лей. Ниже 600С незначительно (менее 3%) набухает практически во всех нейтральных органи-
213
ческих растворителях. Растворяется же при этих температурах только в гексафторацетонгидра-
те. Выше 1000С ограниченно растворим в феноле, ароматических аминах, бензиловом спирте.
Химически устойчив к действию практически всех нейтральных органических растворителей,
причём даже по сравнению с полиэтиленом более стоек к алифатическим, ароматическим и га-
лоидсодержащим углеводородам. Стоек к разбавленным водным растворам щелочей, но разла-
гается концентрированными растворами сильных оснований и минеральных кислот. Водопо-
глощение за 24 часа при комнатной температуре 0,2%.
Физиологически безвреден. Горюч, сгорает без остатка.
.Исключительно низка проницаемость полиформальдегида для органических жидкостей и газообразных углеводородов. Воздухопроницаемость плёнок из полиформальдегида примерно в 100 раз меньше, чем у полиэтиленовых.
Рабочая температура от -40 до +900С, но короткое время может использоваться до 1500С.
Нестабилизированный полиформальдегид деполимеризуется при нагревании выше 100 0С, а
выше 200 °С полностью разлагается до формальдегида. Ацетилированный продукт устойчив в инертной среде или в вакууме примерно до 250 0С, однако в присутствии кислорода воздуха разлагается с заметной скоростью начиная со 160 0С. Для замедления термоокислительной де-
струкции в полимер вводятся добавки (дифениламин и другие ароматические амины, замещён-
ные фенолы и др.), связывающие кислород и позволяющие увеличить индукционный период разложения в условиях переработки. Гомополимер со стабилизирующими добавками выдер-
живает нагрев в присутствии воздуха при 220 0С в течение 30 – 40 минут, что вполне достаточ-
но для переработки полимера в изделия.
В стабилизированном сополимеризаций полиформальдегиде доля «термостабильного» по-
лимера составляет обычно 85 -95%. Такой полимер выдерживает в среде инертного газа или в вакууме нагревание до 2700С в течение 6 – 8 часов без существенных изменений молекулярной массы и других показателей. Разложение за счёт гомолитического разрыва связей С – О в мо-
лекулах наступает при 290 – 3000С. Сополимеризация обеспечивает и долговременную ста-
бильность продуктов на воздухе при более низких температурах.
Введение сомономеров оказывает и отрицательное влияние: несколько нарушается кри-
сталлическая структура, снижается температура плавления, жёсткость, твёрдость, возрастает эластичность. Последнее, однако, влечёт рост прочности к ударным нагрузкам. Варьировани-
ем количествами сомономеров можно получать продукты с широким диапазоном свойств. Так,
введение сомономеров в количестве не более 2,5 - 3% мало влияет на температурные показате-
ли и прочностные свойства, но существенно увеличивает термостабильность. Подобные сопо-
лимеры полиформальдегида получили наименование «ацетальные смолы», в США – «дельри-
ны», в Германии «хостаформы».
Одной из особенностей полиформальдегида с его сополимеров является малая вязкость
214

(высокая текучесть) расплава. Поэтому при изготовлении деталей литьём под давлением при-
ходится применять самозапирающиеся сопла малых сечений, подобные тем, которые исполь-
зуются при переработке полиамидов.
Показатели основных свойств полиформальдегида приведены в таблице 1.
Комплекс свойства полиформальдегида позволяет использовать его в качестве конструкци-
онного материала в самых разных отраслях. Гомополимер и сополимеры находят применение в машино- и приборостроении главным образом для изготовления различных силовых деталей машин: арматуры, зубчатых колёс, втулок, корпусов, пружин, рукояток и т.п. В этих деталях полимер успешно заменяет цветные металлы и сплавы и проявляет лучшие эксплуатационные свойства, чем полиамиды, фенопласты и другие конструкционные пластмассы. В небольших количествах полиформальдегид перерабатывается в плёнки и волокна технического назначе-
ния, трубы, контейнеры для аэрозолей. При температурах до 700С может использоваться для изделий, контактирующих с пищевыми продуктами и фармацевтическими препаратами.
2.2. Полиэтиленоксиды Полиэтиленоксиды общей формулы ~ СН2 – СН2 – О – СН2 – СН2 –О ~ в зависимости от
условий получения и молекулярной массы принято подразделять на две группы: низкомолеку-
лярные полиэтиленгликоли и высокомолекулярные полимеры этиленоксида. Первые имеют молекулярную массу до 40000, получаются при полимеризации оксида этилена в присутствии щелочных катализаторов с добавкой воды и используются в качестве пластификаторов, компо-
нентов косметических препаратов, как исходное сырьё в производстве полиуретанов и т.п. Вы-
сокомолекулярные полимеры, и называемые собственно полиэтиленоксидами (ПЭО), произво-
дятся под торговыми наименованиями «полиокс» (США), «алкокс» (Япония) и перерабатыва-
ются в различного рода изделия общепринятыми для полимеров методами. Для использования в качестве конструкционных материалов они не пригодны из-за своих свойств, но широко ис-
пользуются в различных отраслях промышленности как материалы специального назначения.
Сырьём для них тоже служит оксид этилена, но его полимеризация проводится в присутствии металлорганических катализаторов.
Оксид или окись этилена (этиленоксид, 1,2-эпоксиэтан, оксиран). Химическая
формула |
H |
C |
|
C |
H |
|
H |
O |
|||
|
|
|
H |
Этиленоксид - бесцветная подвижная жидкость со сладковатым эфирным запа-
хом. Ткип = 10,730С; Тпл = - 111,70. Хорошо растворим в воде, спиртах углеводородах и многих других растворителях. Устойчив при нагревании до 3000С. Для него харак-
терны реакции присоединения, сопровождающиеся размыканием цикла. Так, при на-
гревании с водой в присутствии серной или фосфорной кислот образуется этилен-
гликоль.
215
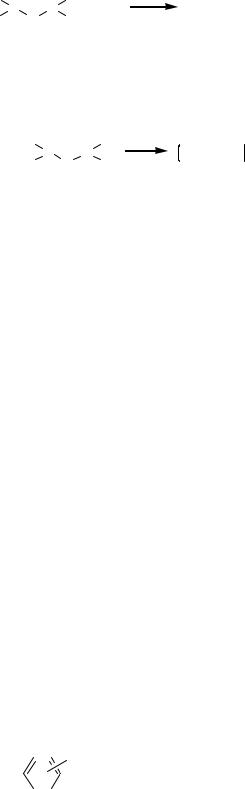
H |
C |
|
C |
H + H O |
|
HOCH |
-CH OH |
|
H |
|
O |
|
H |
2 |
2 |
2 |
|
|
|
|
|
|
|
Получается в промышленности окислением этилена воздухом на катализаторах.
Оксид этилена под действием многих каталитических систем способен к полимеризации с образованием линейных полимеров класса простых эфиров. Полимеризация проходит с рас-
крытием оксиранового цикла.
n H |
C |
|
C |
H |
|
- CH2-CH2-O |
- |
|
|
||||||
H |
|
O |
|
H |
|
|
n |
Степень полимеризации может быть различной от 102 до 107. Низкомолекулярные полиме-
ры с концевыми гидроксильными группами, названные полиэтиленгликолями, в большинстве своём жидкие или воскообразные продукты. Используются они в качестве связующих в фарма-
цевтике и косметике, как компоненты моющих средств, в качестве антистатических и смачи-
вающих агентов в текстильной промышленности, как пластификаторы.
Высокомолекулярные полимеры с молекулярной массой от 500 тыс. до 10 млн. – твёрдые термопластичные материалы со степенью кристалличности до 95%. Они слабо растворимы в воде, растворяются во многих органических растворителях, нерастворимы в парафиновых угле-
водородах.
Применяются ПЭО в качестве загустителя красящих составов и латексов, для шлихтования волокон, связующих в производстве керамических изделий. Низкая токсичности позволяет использовать их в фармацевтической и пищевой промышленностях, косметике. Используются для изготовления упаковочных плёнок и нитей с высокими прочностью и эластичностью, изго-
товления различных деталей экструзией, литьём под давлением, прессованием. Изделия из ПЭО хорошо работают в сухой среде (относительной влажности воздуха не более 80 – 90%). В
более влажной среде из-за гигроскопичности материал увлажняется, резко уменьшая показате-
ли механических свойств.
2.3. Полифениленоксиды Полифениленоксиды – незамещённые и замещённые в ароматическое кольцо простые по-
лиэфиры общей формулы
H |
|
|
|
|
|
|
|
|
Rx |
|
|
|||
|
|
|
|
|
|
|
|
|||||||
|
|
|
|
|
|
|
|
|
O |
|
|
|
n |
|
|
|
|
|
|
|
|
|
|
|
|
|
|||
|
|
|
|
|
|
|
|
|
|
|
|
|
|
|
|
|
|
|
|
|
|
|
|
|
|
|
|
|
|
|
|
|
|
|
|
|
|
|
|
|
|
|
|
|
|
|
|
|
|
|
|
|
|
|
|
|
|
|
|
R – алкил, галоген, фенил, аллил; |
х = 0, 1, 2. |
Всё это термопластичные бесцветные полимеры преимущественно линейного строения, за исключением галоген- и монометилзамещённых, имеющих разветвлённое строение. Молеку-
лярная масса может достигать от нескольких десятков тысяч до нескольких сотен тысяч. Неза-
мещенный в кольце поли-р-фениленоксид имеет высокую степень кристалличности. Наличие в бензольных ядрах заместителей уменьшает способность к кристаллизации. Температура стек-
216
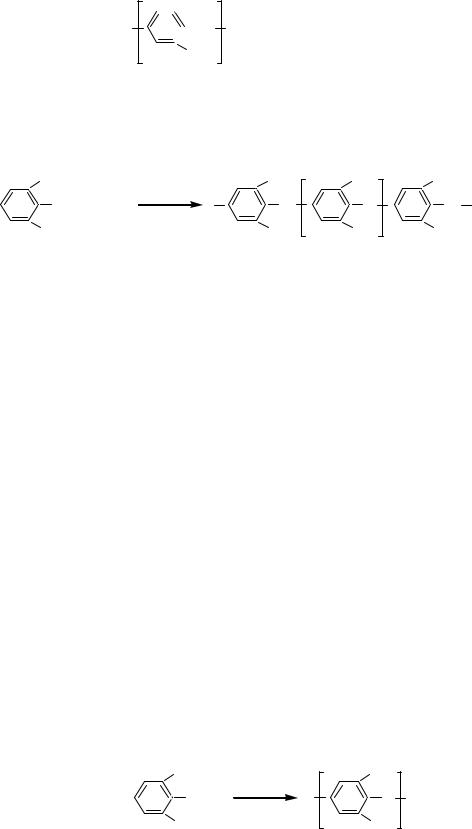
лования различных представителей класса 100 – 2700С. Термическая деструкция замещённых полифениленоксидов начинается на воздухе при 200 – 3000С, незамещённых при 3500С. Крат-
ковременный нагрев на воздухе до температуры начала окислительной деструкции полифени-
леноксидов, содержащих алкильные группы, превращает их в сетчатые полимеры, имеющие к термоокислительной деструкции повышенную стабильность и начинающие разлагаться лишь при 350 - 4000С. Наибольшее распространение получил поли-2,6-диметил-р-фениленоксид,
CH3
O
CH3 n
Поли-2,6-диметил-р-фениленоксид (ПФО) выпускается под двумя наименованиями: поли-
фениленоксид (РРО) и полифениленэфир (РРЕ). Он получается в промышленности двумя ме-
тодами. Одним из них является окислительная поликонденсация 2,6 - диметилфенола.
CH3 |
CH3 |
CH3 |
CH3 |
|
OH + 1/2 O2 |
O |
O |
O |
+ H2O |
CH3 |
CH3 |
CH3 n |
CH3 |
|
2,6- диметилфенол (2,6-ксиленол) – кристаллическое вещество с Тпл=490С, мало растворимо в воде. Растворим в большинстве органических растворителей. В водных растворах щелочей образует соли, на воздухе медленно окисляется. Получается из смол, образующихся при термической обработке твёрдых топлив.
Окислительная поликонденсации или дегидрополиконденсация может проводиться в инертном растворителе (бензоле, толуоле, дихлорбезоле) или в смеси ароматических углеводо-
родов с осадителем (изопропиловым спиртом). В первом случае среда гомогенна и образую-
щийся полимер приходится выделять из раствора высаживанием метиловым спиртом; во вто-
ром случае полимер выделяется в виде порошка по мере образования. Реакция проводится при
28 – 320С. Катализаторами служат комплексы или соли металлов переменой валентности (од-
новалентной меди, марганца, свинца) в комплексе с алифатическими аминами, пиридином, ди-
метилформамидом. Осаждённый полимер отфильтровывается, отмывается от растворителей,
высушивается в вакууме и гранулируется. При необходимости в него вводятся пигменты, на-
полнители.
Известен и реализован в промышленности метод синтеза поли-2,6-диметил-p-фениленок-
сида дегидрополиконденсацией p-хлор-2,6-диметилфенола в присутствии двухлористой меди и окислителя в пиридине. Окислителем может быть кислород, ферроцианид калия (жёлтая кро-
вяная соль, K4[Fe(CN)6]), персульфат калия (K2S2O8).
|
CH3 |
CH3 |
Cl |
OH |
пиридин |
O |
||
|
|
CuCl2 |
|
CH3 |
CH3 n |
217
Полифениленоксид (ПФО) – твёрдый термопласт, обладающий способностью к самозату-
ханию. В зависимости от способа и условий получения молекулярная масса сможет составлять
30 – 700 тыс. Продукт, полученный из диметилфенола, аморфен, но дополнительной обработ-
кой (нагреванием в хлористом метилене, циклогексане, ацетоне) его можно перевести в кри-
сталлический вид.
ПФО стоек к действию кипящей воды, перегретого пара, разбавленных и концентрирован-
ных растворов щелочей. Растворим в ароматических и хлорированных углеводородах, а также в некоторых органических растворителях (тетрагидрофуран, диметилформамид), что позволяет формовать плёнки поливом. Заметно набухает в ацетоне.
При нагревании на воздухе потеря массы начинается с 2000С. Одновременно изменяется растворимость, что свидетельствует о кристаллизации и сшивании. Сшивание обусловлено час-
тичным окислением метильных групп, в результате чего они превращаются в альдегидные и карбоксильные, которые и реагируют с ароматическими ядрами. Повторное нагревание подоб-
ных изменений уже не вызывает и свойства материала стабилизируются до температуры 250 –
3000С. Показатели основных свойства ПФО приведены в таблице 1.
Перерабатывается литьём под давлением при температуре расплава 320 – 3400С и экструзи-
ей при 250 – 3000С. Полученные детали отличаются прочностью, стабильностью размеров и используются в электротехнике, электронике, химической промышленности, изготовлении час-
тей бытовой техники. Некоторая доля ПФО расходуется на изготовление изоляционных и за-
щитных покрытий. Плёнки получают как поливом, так и каландрованием.
Высокая температура стеклования ПФО (230 – 2500С) затрудняет формование из него изде-
лий, так как требуется сильный обогрев рабочих цилиндров формующих машин. С целью по-
нижения этой температуры создан ряд модифицированных полифениленоксидов. Такие про-
дукты представляют собой сплавы ПФО с различными полярными полимерами (ударопрочным полистиролом, полиамидом и др.). Модифицированные ПФО несколько уступают гомополи-
меру по теплостойкости, имеют температуру стеклования около 2000С, но существенно пре-
восходят его по ударной вязкости и легче перерабатываются.
В СССР (Уралхимпласт) ПФО был известен под торговой маркой «Арилокс», в США - «Noril». Причём арилокс производился двух марок «арилокс 1» и «арилокс II», различающихся почти на два десятичных порядка ударной вязкостью.
218