
ПОЛИКОНДЕНСАЦИОННЫЕ 2
.pdfрах (до 1800С) даже в присутствии влаги. Они легко металлизируются многими металлами
(алюминием, цинком, оловом), армируются волокном и сетками, матируются, окрашиваются,
прекрасно удерживают на себе слои липких полимерных композиций. Из металлизированных плёнок изготавливаются конденсаторы для радиопромышленности, декоративные нетускнею-
щие золотистые и серебристые нити, используемые в производстве трикотажных изделий и иг-
рушек. Применяются плёнки также для изготовления мембран диафрагмовых насосов, шлан-
гов, упаковочного материала.
Основное применение плёнок из АПЭТ – производство термоформованной упаковки для пищевых продуктов и медикаментов. Тому способствуют: хорошая пластичность, высокие ударопрочность и морозостойкость, полная безвредность для организма ввиду отсутствия в ПЭТ токсичных веществ, способных мигрировать в пищу при хранении. Наиболее широкое распространение плёнки получили при изготовлении коррексов для конфет, контейнеров (бли-
стеров) для кондитерских изделий (тортов, пирожных), лотков для упаковки продуктов дли-
тельного хранения.
Коррекс – это ложемент из термопластичной плёнки, предназначенный для фик-
сации штучных пищевых продуктов в заданном положении при транспортировке.
Такими продуктами могут быть конфеты, мармелад, рулеты и т.п. Коррексы из жё-
сткой полимерной плёнки - неотъемлемая часть современной кондитерской упаков-
ки, особенно шоколадных конфет. Изготавливаться они могут из плёнок АПЭТ тол-
щиной 150 – 600 мкм и ценятся за красивый и эстетичный блеск, высокое качество металлизации или окрашивания. Современные красители могут придавать плёнкам из АПЭТ эффект окраса под серебро или золото даже без металлизации.
Блистерные упаковки состоят из полимерного листа с фланцем, к которому с помощью клея, скоб или сварки присоединена соответствующая подложка. Блисте-
ры могут изготавливаться с несколькими полостями, что ценно при желании пока-
зать комплект товара. Как правило, упаковка повторяет объёмную форму изделия, а
на картоне подложки размещается информация о товаре. Блистерная упаковка даёт возможность потребителю увидеть товар со всех сторон, что делает её наиболее рас-
пространённым видом упаковок. При блистерной упаковке лекарств сам блистер приваривается к фольге.
Прозрачные контейнеры для индивидуальной или групповой упаковки тортов,
пирожных и прочей выпечки иногда называют пирожницами. Для их изготовления используются толстые плёнки толщиной около 300 мкм. Из АПЭТ изготавливаются микроконтейнеры различного назначения (упаковка салатов, орешков, сладких паст,
мёда и т.п.). На лотки для мясной и рыбной продукции используется АПЭТ плёнка,
ламинированная полиэтиленовой плёнкой толщиной 30 – 40 мкм. Тонкий полиэти-
229
леновый слой, с которым и контактирует продукт, необходим для увеличения барь-
ерных свойств упаковки.
На основе ПЭТ изготавливаются клеи для машиностроительной, кожевенной, обувной промышленностей. Растворы в метиленхлориде служат основой многих рецептур лаков.
Помимо полиэтилентерефталата производятся и используются его аналоги – эфиры тереф-
талевой кислоты с другими гликолями (полибутилентерефталат, например), эфиры других аро-
матических диосновных кислот, такие как полиэтиленнафталинат-2,6 и т.п. Их применение несравненно меньше, чем ПЭТ.
Постоянный рост потребления изделий из ПЭТ делает весьма актуальной задачу вторич-
ного использования материала. До настоящего времени тысячи тонн использованных бутылок выбрасывались и выбрасываются на свалку, сжигаются или закапываются в землю. И это не-
смотря на то, что возврат (рециклинг) ПЭТ значительно проще, чем других полимеров. Этот материал не испытывает превращений с образованием токсичных веществ ни в процессе экс-
плуатации изделий из него, ни при переработке. С 2004 в России начал формироваться специа-
лизированный сегмент рынка по рециклингу полиэтилентерефталата. Несколько компаний ор-
ганизуют сбор использованной посуды, её сортировку, дробление, многостадийную мойку,
сушку и реализацию вторичного сырья. При желании потребителя полученные ПЭТ-хлопья
(флексы) гранулируются. Вторичный ПЭТФ может использоваться как добавка к первичному сырью при изготовления различных изделий. Изготовление тары и упаковок для пищевой промышленности из вторичного сырья не допускается. Поэтому распространение приобретают трёхслойные плёнки ПЭТФ. Два внешних слоя в них делаются из первичного сырья, середин-
ный слой – из вторичного. Такие плёнки, обозначаемые как «плёнки А-В-А» допущены для упаковки пищевых продуктов. Их недостаток – меньшая прозрачность. Поэтому плёнки «А-В-
А» используются, в основном для изготовления непрозрачных коррексов и молочно белых ста-
канов, в материалы которых добавляются пигменты и минеральные наполнители.
230
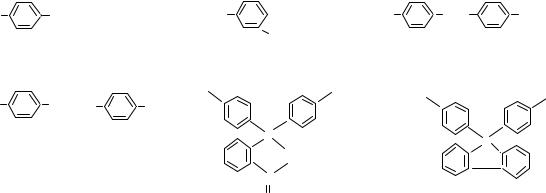
3.2. Полиарилаты Полиарилатами называют сложные эфиры двухатомных фенолов и различных дикарбоно-
вых кислот. К этой группе полимеров по химическому строению относятся и рассматриваемые ниже поликарбонаты, но термин «полиарилаты» относят обычно к производным более высо-
комолекулярных чем угольная кислот. В качестве спиртовой компоненты при синтезе поли-
арилатов чаще всего используются диан, фенолфталеин, диоксидифенилфлуорен, гидрохинон,
резорцин, диоксидифенилметан, и некоторые другие. Химические формулы некоторых при-
меняемых в производстве полиарилатов бифункциональных ароматических спиртов приводят-
ся ниже.
НО |
ОН |
|
НО |
ОН |
НО |
СН2 |
ОН |
||
|
|
|
=1700С |
|
4,4'-Диоксидифенилметан. Т =1630С |
||||
Гидрохинон. Т |
пл |
Резорцин. Т |
пл |
= 110,80С |
|||||
|
|
|
|
|
|
|
пл |
||
НО |
С(СН3)2 |
НО |
|
|
ОН |
НО |
ОН |
||
ОН |
|
|
|
||||||
|
|
|
|
|
|||||
4,4'-диоксидифенил-2,2-пропан, |
С |
|
|
С |
|
||||
диан. Тпл = 156 - 1570С |
|
|
О |
|
|
||||
|
|
|
|
|
|||||
|
|
|
|
|
С |
|
4,4'-диоксидифенилфлуорен. |
||
|
|
|
|
|
О |
|
|||
|
|
|
|
|
|
Тпл = 224 - 2250С |
|
||
|
|
|
|
4,4'-диоксифталофенон, |
|
|
фенолфталеин. Тпл 2360С
Второй составляющей полиарилатов – дикарбоновой кислотой – могут служить представи-
тели как алифатического, так и ароматического ряда. Производные алифатических дикарбоно-
вых кислот (янтарной, адипиновой, себациновой и др.) в большинстве своём не находят широ-
кого практического применения. Причины этого: сравнительно низкие температуры размягче-
ния (100 – 1600С) образующихся полимеров, ограниченная сырьевая база, наличие полимеров других классов со сравнимыми физико - механическими показателями, но значительно более доступных. Наибольший практический интерес имеют полиарилаты на основе ароматических дикарбоновых кислот, из которых преимущественно используются фталевые. Такие продукты обладают высокими тепло- и термостойкостью, имеют хорошие эксплуатационные показате-
ли. Особое место среди термостойких полиарилатов занимает продукт, получаемый поликон-
денсацией пара-оксибензойной кислоты НО-С6Н4-СООН и известный под названием «эконол»
(США). Этот полностью ароматический высококристаллический гомополимер имеет термо-
стойкость 380 - 4000С и способен длительно работать на воздухе при температурах до 3150С.
В наибольших количествах производятся полиарилаты марок:
Д– 1 – полиэфир диана и изофталевой кислоты с молекулярной массой более 80000;
Д- 2 – полиэфир диана и терефталевой кислоты;
Д-3, Д-3Э, Д-4, Д-4С – продукты поликонденсации диана со смесью изо- и терефталевой
231
кислот, взятых в разных соотношениях (молекулярная масса таких
полиэфиров около 35000)
Д-9 –полиэфир диоксидифенилфлуорена и терефталевой кислоты;
Ф-1, Ф-2 – продукты поликонденсации фенолфталеина и изо- и терефталевых кислот соот-
ветственно.
3.2.1. Свойства и применение
Полиарилаты – термопластичные материалы. Их характерной особенностью являются вы-
сокие значения температур плавления и начала разложения. Комплекс свойств полиарилатов зависит от химического строения исходных мономеров и, в частности, от расположения в них функциональных групп. Так, наиболее высокие температуры плавления имеют полиарилаты,
полученные из мономеров, не имеющих алифатических звеньев и содержащих заместители бензольного кольца в пара-положении. Примерами таких соединений являются гомополимер
п-оксибензойной кислоты – поли(п-оксибензоат) или эконол и полигидрохинонтерефталат. Оба соединения не плавятся до 5000С в то время как полигидрохинонизофталат размягчается уже при 3200С. Наличие алкильных заместителей в орто-положениях к гидроксильным группам,
снижая температуру размягчения, способствует росту сопротивления ударным нагрузкам,
уменьшает вязкость расплавов и тем облегчает переработку материала в изделия.
В таблице 2 приведены некоторые температурные показатели полиарилатов марок Д и Ф
Таблица 2. Температурные показатели некоторых полиарилатов
Показатели |
|
Марки полиарилатов |
|
|
|
Д-3 |
Д-4 |
Ф-1 |
Ф-2 |
Температура, 0С |
|
|
|
|
плавления |
270 – 285 |
255 – 275 |
300 – 310 |
320 – 340 |
начала окисления |
270 |
270 |
280 |
290 |
разложения |
450 |
450 |
500 |
500 |
Верхний предел рабочих температур, 0С |
155 - 180 |
155 - 175 |
200 - 220 |
250 |
Теплостойкость по Вика,0С |
210 |
210 |
270 |
280 |
Морозостойкость, 0С |
-100 |
-100 |
-100 |
-100 |
Наличие в исходных мономерах функциональных групп в орто- и мета-положениях и нали-
чие у двухатомных фенолов боковых заместителей влекут уменьшение плотности упаковки полимерных цепей и способствуют образованию аморфных полиарилатов. На степень кристал-
личности в наибольшей мере влияет структура спиртового компонента и, в частности, объём-
ность заместителей у центрального углеродного атома бисфенолов. Полиарилаты на основе диана и фталевых кислот (заместители – метильные группы) ещё сохраняют способность к кри-
сталлизации и способность растворяться в некоторых растворителях. Замена метильных групп на более объмные заместители (фенильные, например) влечёт потерю способности к кристал-
лизации и резко увеличивает растворимость полиарилатов. Степень кристалличности может регулироваться и условиями синтеза. Она несколько возрастает при снижение температуры процесса.
232
Химическое строение полиарилатов определяет и их растворимость. Полиарилаты ароматических кислот, таких как изо- и терефталевой, и таких бисфенов, как резорцин,
гидрохинон, практически нерастворимы в органических растворителях. Наличие боковых заместителей в бисфеноле несколько увеличивает растворимость. Достаточно хорошо растворяются так называемые кардовые полиарилаты, т.е.полиарилаты бисфенолов или ароматических дикарбоновых кислот с объёмными заместителями у центрального углеродного атома, замкнутыми в цикл. Таковы полиарилаты фенолфталеина, диоксидифенилфлуорена. Они растворимы в алифатических хлоруглеводородах, циклогексаноне, тетрагидрофуране.
Высока устойчивость всех полиарилатов к длительному воздействию большинства органи-
ческих растворителей, нефтепродуктов, минеральных и органических кислот (кроме концен-
трированной серной), окислителей, разбавленных щелочных растворов. Концентрированные растворы щелочей и даже аммиак приводят к гидролитическим процессам. Химическая устой-
чивость эконола близка к устойчивости фторопластов.
Физико-механические показатели (таблица 3) полиарилатов сравнимы с аналогичными по-
казателями полиэтилентерефталата и поликарбоната.
Одной из особенностей полиарилатов являются их высокие диэлектрические показатели, не изменяющиеся в широком интервале температур (от -60 до 2000С, а для некоторых представи-
телей класса и выше).
Высокие теплостойкость, прочностные и диэлектрические показатели определяют области применения полиарилатов. Они используются как конструкционные материалы, применяются в радиотехнической, электротехнической, электронной отраслях. Наполненные, в том числе и ан-
тифрикционными добавками, успешно применяются для изготовления пар трения, которые ра-
ботают без смазки в условиях высоких (до 2500С) температур и вакуума.
Растворимые полиарилаты перерабатываются в теплостойкие волокна и плёнки. Плёнки выпускаются двух типов: электротехнические и конденсаторные. Первые имеют толщину 20 – 100 мкм, неориентированы и производятся поливом из раствора. Конденсаторные плёнки суще-
ственно тоньше (6 – 20 мкм) и получаются экструзией с последующей ориентацией. Основной материал для конденсаторных плёнок – полиарилат Д-3Э. Волокна изготавливаются как из рас-
творов, так и экструзией через фильеру с последующей вытяжкой. Фильтрующие материалы из таких волокон используются для улавливания аэрозолей и способны работать при температурах до 3000С. Одним из ценных качеств волокон и плёнок является способность сохранять хорошие механические показатели при повышенных температурах и после длительного нагревания.
Ценными качествами облают полиарилатные лаки. Это растворы полиарилатов в разнооб-
разных растворителях. Например, лак Д-4ЛК представляет собой раствор полиарилата Д-4 в
смеси тетрахлорэтана и фенола. Покрытия из таких лаков, нанесенные на металлы, стойки к действию концентрированных и разбавленных кислот при температурах до 1000С.
233
Способы переработки полиарилатов определяются их свойствами. Изделия из практически неплавкого поли-(п-оксибензоата) формуют спеканием порошкообразного полимера при 425 –
4500С и давлении 50 – 150 Мпа. Возможна даже горячая ковка такого материала. Для этого от-
прессованную заготовку нагревают до 1500С и проковывают в течение 6 – 10 секунд с общим расходом механической энергии 1400 – 14000 кгм. Менее теплостойкие полиарилаты перераба-
тывают литьём под давлением, литьевым и компрессионным прессованием. Наличие жёстко-
цепных макромолекул и переход в вязкотекучее состояние при температурах, граничащих с температурами деструкции, а также высокая вязкость расплавов создают определённые трудно-
сти при переработке. В производственном процессе переработки обязательна стадии подсушки материала до остаточной влажности не более 0,1 – 0,2%, так как остатки воды могут при высо-
ких температурах активизировать гидролизные процессы.
3.2.2. Получение Получаются полиарилаты поликонденсацией фенолов (или их ацетатов) с кислотами или их
хлорангидридами. Использование вместо кислот более реакционноспособных хлорангидридов даёт возможность проводить поликонденсацию в растворе при несколько пониженных темпе-
ратурах. Это особенно важно для высокоплавких полиарилатов, так как в этом случае можно довести реакцию до высокой степени завершённости без термораспада образующегося поли-
мера.
Реализуются, в основном, две технологии синтеза полиарилатов. Одна – поликонденсация компонентов в инертной среде при повышенных температурах в высококипящих растворите-
лях, другая – межфазная поликонденсация мономеров при комнатной температуре. В первом случае реакция проводится при температурах 180 – 2200С в растворителях, растворяющих ис-
ходные компоненты, но не растворяющих или при этой температуре слабо растворяющих обра-
зующийся полимер. Необходимо отметить, что свойства растворителя влияют на молекуляр-
ную массу и структуру образующегося полимера. От окисления кислородом воздуха реакцион-
ная масса защищается током инертного газа. Выделяются конечные продукты из реакционной массы после её охлаждения фильтрованием. У технологии синтеза при высоких температурах имеются свои положительные черты. Так, здесь мал расход растворителей, реакция протекает в гомогенной среде, достаточно просты операции по выделению полимера, образуется продукт с фибриллярной (а не глобулярной) структурой с лучшими механическими показателями.
Межфазная поликонденсация протекает на границе раздела фаз, образующихся при смеше-
нии раствора дихлорангидрида дикарбоновой кислоты в органическом растворителе с водно-
щелочным раствором бисфенола. Реакция проводится при температурах 20 – 250С. Образую-
щийся полимер выделяется в виде порошка. Этим способом удаётся получить более высокомо-
лекулярные продукты с молекулярной массой до 160000. Но отходы производства (водные растворы) требуют дополнительных расходов на обезвреживание.
234

3.3. Поликарбонаты
Поликарбонаты – гетероцепные сложные полиэфиры угольной кислоты НО-СО-ОН и диолов (диоксисоединений). Спиртовой компонентой могут служить, в принципе, любые ди-
и полиолы. Тогда общая формула поликарбонатов будет [- O - R - O – CO - ]n. В зависимости от природы R поликарбонаты могут быть алифатическими, жирно-ароматическими и ароматиче-
скими, а в зависимости от функциональности R (соответственно и физической структуры мак-
ромолекулы) – линейными, разветвлёнными и трёхмерными. Наибольший практический инте-
рес представляют сейчас поликарбонаты на основе двухатомных фенолов (бисфенолов) - аро-
матических диоксисоединений общей формулы НО-Ar- R -Ar-OH. Ароматические ядра таких бисфенолов могут содержать заместители (галоиды, алкильные группы, одновалентные радика-
лы ненасыщенных углеводородов), а мостиком - R- между ядрами могут служить свободная и замещенные метиленовые группы (–СН2-; -СН(СН3)- ; -С(СН3)- ; -СН(С6Н5) -), кислород, ди-
фенильный радикал - С6Н5 - С6Н5 - и другие.
Основными промышленными способами получения поликарбонатов являются
-фосгенирование бисфенолов (реакция с дихлорангидридом угольной кислоты – фосгеном)
ворганических растворителях в присутствии третичных органических оснований, связываю-
щих хлористый водород и являющихся катализатором поликонденсации (пиридин);
- способ межфазной поликонденсации: фосгенирование растворенных в водных растворах
щелочей бисфенолов на поверхности раздела фаз в присутствии в качестве катализаторов тре-
тичных аминов – триэтиламина, например;
- переэтерификация в расплаве ароматических эфиров угольной кислоты (диарилкарбона-
тов) бисфенолом.
Перечисленные способы неравноценны, так как позволяют получать продукты с разной
молекулярной массой. В первом способе – с мол. массой 60 – 80 тыс., во втором – до 200 тыс., в
третьем – 20 – 50 тыс.
Наибольше применение получил сложный эфир угольной кислоты и дифенилолпропана,
названный в СССР «дифлоном». Широко известно в России и немецкое наименование этого полимера – «макролон», и американское «мерлон». В торговых сетях этот полимер обычно на-
зывают «поликарбонат».
Дифенилолпропан (4,4'-дигидроксидифенилдиметилметан, ди- |
|
|
|
|
|
|
CH3 |
|
|
||
|
|
|
|
|
|||||||
ан, бисфенол-А) - бесцветные кристаллы с Тпл 156 – 1570С, Ткип. = |
|
|
|
|
|
|
|
|
|
|
|
OH |
|
|
|
C |
|
|
|
OH |
|||
|
|
|
|
||||||||
|
|
|
|
|
|
|
|
|
|
|
|
|
|
|
|
|
|
|
|
|
|
|
|
|
|
|
|
|
|
|
|
|
|
|
|
250 – 2520С (при 13 мм. рт. ст.). Наименование «диан» присвоено CH3
дифенилолпропану по имени его первооткрывателя Александра Павловича Дианина
(1851 - 1918 г.г.) - русского химика-органика. Ученик А. П. Бородина и его преемник по кафедре химии Медико-хирургической академии в Петербурге (1887—1916)
А.П.Дианин установил, что при окислении одноатомных фенолов образуются двух-
235

атомные фенолы. Это открытие послужило развитию промышленного производства соединений различных классов. В 1891 году А.П.Дианиным был впервые получен ди-
фенилолпропан.
Диан растворим в низших спиртах, ацетоне, уксусной кислоте. Растворимость в воде и углеводородах незначительна. Со щелочами реагирует с образованием солей
(фенолятов). Натриевые и калиевые соли дифенилолпропана хорошо растворяются в воде. В промышленности дифенилолпропан получается конденсацией фенола с аце-
тоном в присутствии серной или соляной кислот:
+ НСl
2 OH |
|
|
|
+ СН3СОСН3 |
|
|
|
|
|
OH
СН3 |
|
|
|||||
|
|
|
|
|
|
OH + Н2О |
|
С |
|
|
|
||||
|
|
||||||
|
|
|
СН3 |
|
|
||
|
|
|
|
|
Дифенилолпропан широко используется в химической промышленности в каче-
стве исходного продукта для синтеза эпоксидных смол, антиоксидантов, гербицидов.
Превращение дифенилолпропана в дифлон (поликарбонат) может проводиться разными методами. Наибольшее признание в технике имеют его прямое взаимодействие с хлорангидри-
дом угольной кислоты и переэтерификация диэфиров угольной кислоты.
Хлорангидрид угольной кислоты (фосген) – бесцветный газ с запахом прелого сена. Ткип = +8,20С, Тпл = -1180С. Ограниченно растворяется в воде, но хорошо рас-
творим в большинстве органических растворителей. В жидкой фазе фосген быстро гидролизуется. Эта реакция сильно ускоряется в присутствии едких щелочей. Фос-
ген – типичный представитель боевых отравляющих веществ первого поколения.
Надёжной защитой от него является противогаз.
По первому методу реакция протекает по схеме:
n NaO - Ar - ONa + n Cl - CO - Cl |
|
|
|
|
O - Ar - O - CO |
|
n + 2n NaCl |
|
|
|
|
Осуществляться процесс может как в среде растворителя, так и без него.
Синтез поликарбоната при прямом фосгенировании без растворителя проводится пропус-
канием газообразного фосгена через водный щелочной раствор бисфенола при 27 – 300С. Для связывания образующегося хлористого водорода в водный раствор вводятся четвертичные ам-
мониевые основания, триметиламин или другие третичные амины. Поликарбонат выделяется по мере образования в виде тонкого порошка. Для промышленного получения дифлона данный метод не используется.
Другими технологическими вариантами прямого фосгенирования являются поликонденса-
ция в среде пиридина, смеси пиридина с более дешёвыми растворителями и межфазный про-
цесс. Реакция описывается уравнением:
n HO - Ar - OH + n Cl - CO - Cl |
|
|
|
|
O - Ar - O - CO |
|
|
n + 2n HCl |
|
|
|
|
|
||||
|
|
|
|
|
|
|
Поликонденсация в среде пиридина является примером фосгенирования в растворе. Она
236

проводится в отсутствии воды. Растворитель - пиридин, который, являясь сильным основанием,
одновременно служит катализатором поликонденсации и акцептором выделяющегося при ре-
акции хлористого водорода. |
|
Пиридин – бесцветная жидкость с сильным специфическим запахом. |
|
Ткип = 115,60С. Смешивается во всех соотношениях с водой и |
N |
большинством органических растворителей. Является хорошим растворителем для многих органических веществ, в том числе и для поликарбоната. Сильное основание. С
кислотами образует соли. Типичное ароматическое соединение, но реакции электро-
фильного замещения протекают в пиридине несравненно труднее, чем в бензоле. Ши-
роко используется в химической промышленности при синтезе красителей, лекарст-
венных препаратов, инсектицидов и пр. Основным источником пиридина является ка-
менноугольная смола.
В результате поликонденсации в среде пиридина образуется вязкий раствор дифлона, со-
держащий хлоргидрат пиридина. Для снижения вязкости в реакционную массу может добав-
ляться инертный растворитель (бензол, толуол, метиленхлорид) в таком количестве, чтобы по-
сле промывки раствора водой для удаления пиридина и его соли поликарбонат оставался рас-
творённым в таком комбинированном растворителе. Выделяют поликарбонат из промытого раствора высаживанием петролейным эфиром или гексаном. Данным методом можно полу-
чать и другие поликарбонаты, растворимые в инертных растворителях. Поликонденсация про-
ходит в гомогенной жидкой среде при сравнительно низких температурах (10 – 250С). Молеку-
лярная масса получаемого поликарбоната варьируется изменением температуры процесса, кон-
центрации исходного бисфенола, скоростью подачи фосгена и другими факторами. Недостаток метода - необходимость регенерации пиридина и других растворителей.
Наиболее экономичным и более широко применяемым способом синтеза дифлона являет способ межфазной поликонденсации. Здесь газообразный фосген пропускается через эмульсию водного щелочного раствора бисфенола в органическом растворителе, хорошо растворяющем фосген и образующийся поликарбонат. Одним из таких растворителей является метиленхлорид.
Метиленхлорид (дихлорметан) Cl-CH2-Cl – жидкость с Ткип = 40,10С. Раствори-
мость в воде составляет около 2%. Хорошо смешивается со многими органическими растворителями, является растворителем для многих органических соединений, в том числе для ацетатов целлюлозы. Обладает слабым наркотическим действием. Получает-
ся хлорированием метана.
Катализаторами реакции могут служить третичные амины (триэтиламин), ацетат натрия,
четвертичные аммониевые основания (соединения типа (CH3)4NOH) и др. Технология получе-
ния дифлона данным способом складывается из стадий фосгенирования диана, водной про-
мывки раствора полученного полимера в органическом растворителе, обезвоживания органиче-
237

ской фазы, высаживания полимера из раствора и его отделения от смеси растворителей, сушки полимера и регенерации растворителя и высадителя. Схема производства дифлона периодиче-
ским способом приведена на рис. 2. В реактор 1 загружаются заранее приготовленный при-
мерно 10%-ый раствор дифенилолпропана в водном растворе едкого натрия, метиленхлорид
(дихлорметан), катализатор и при интенсивном перемешивании при температуре 20 – 250С на-
чинают барбатировать газообразный фосген, который хорошо растворим в метиленхлориде.
Поликонденсация проводится в атмосфере азота, так как феноляты легко окисляются кислоро-
дом воздуха. Реактор охлаждается холодной водой. Часть реакционного тепла расходуется на испарение метиленхлорида, который возвращается в реактор из обратного холодильника 8.
Раствор диана |
8 |
10 |
12 |
Фосген |
11 |
|
|
Метиленхлорид |
|
|
|
Катализатор
Азот
1
2
Конденсат
HСl |
Вода |
Вода
9
Пар
3
Метанол
Ацетон
5
4 регенерацию На
6
7
Дифлон
Рис. 2. Схемапроизводствадифлонапериодическимметодом:1- реактор, 2 -промыватель, 3- аппарат
обезвоживания, 4- высадитель, 5- фильтр, 6- сушильный аппарат, 7- гранулятор, 8,10холодильники- - конденсаторы, 9- насадочнаяколонна, 11- сборник-сепаратор азеотропнойсмеси, 12мерник.
Образующийся полимер растворяется в метиленхлориде, образуя вязкий раствор. Этот рас-
твор вместе с водной фазой по окончании реакции сливается в промыватель 2, куда подаются свежая вода и раствор соляной кислоты для нейтрализации реакционной массы. После интен-
сивного перемешивания эмульсия отстаивается, водная фаза отделяется декантацией от орга-
нического слоя и сливается в очистную систему. Такая промывка повторяется несколько раз.
Промытая органическая фаза передаётся в аппарат 3 для обезвоживания. Там раствор дифлона в метиленхлориде нагревается через рубашку. Пары метиленхлорида (Ткип= 40,10С) и воды в виде азеотропной смеси (98,5% хлористого метилена, Ткип = 38,10С) поступают в насадочную колонну 9, холодильник 10, конденсируются и собираются в сепараторе. После разделения сло-
ёв метиленхлорид возвращается в аппарат, а водяной конденсат отводится на очистные соору-
жения. Обезвоженный раствор поликарбоната переливается в высадитель 4. Там к нему из мерника 5 прибавляется метанол (или ацетон) для высаживания дифлона. Суспензия разделя-
238