
Учебник по Технологии
.pdfчений целевой функции. Технологический процесс можно рассматривать как систему, состоящую из управляемой и управляющей систем. При этом под управляемой системой понимают совокупность нескольких управляемых объектов, объединенных единством цели управления. Совокупность средств, стремящихся обеспечить выполнение управляемой системой определенной цели, является управляющей системой.
Поведение всякой системы управления определяется: целью управления, окружающей обстановкой или внешними и внутренними условиями, т.е. свойствами управляемой и управляющей систем.
Выходные переменные Хn, характеризующие РЭС после технологического процесса производства, могут представлять собой такие параметры прибора, как его стоимость, надежность работы, точность, простота конструкции, удобство эксплуатации и многие другие.
Логическая система управления технологическим процессом производства РЭС служит для создания таких управляющих сигналов rm, которые изменяют характеристики технологического процесса таким образом, что обеспечивается достижение некоторой целевой функции, являющейся комплексным показателем характеристик аппарата, выпускаемого при данном технологическом процессе.
Примерами логической системы управления могут служить человек, осуществляющий технологический процесс (самый простой случай), или система управления современного радиоэлектронного завода (директор, начальники цехов, технологи и т.д.). В более сложном случае автоматического технологического процесса логическое управление осуществляется логическим устройством или ЭВМ.
Управляющими сигналами rm могут быть конкретные значения параметров, характеризующих данный технологический процесс производства (состав специалистов, снабжение комплектующими изделиями, состояние и особенности транспортировки и т.п.).
Под целевой функцией понимается обобщенный показатель системы, всесторонне характеризующий объект производства.
Управляемые системы и объекты можно характеризовать следующими группами переменных: переменными состояния x1(t), x2 (t),..., xn (t) , представляющими собой их обобщенные коор-
динаты; управляющими переменными r1(t), r2 (t),..., rm (t) , представ-
ляющими собой воздействия на управляемый объект, создаваемые управляющей системой; внешними переменными или возмущающими воздействиями f1(t), f2 (t),..., fk (t) , создаваемыми окружаю-
51

щей средой (внешние условия); наблюдаемыми переменными z1(t), z2 (t),..., zl (t) , представляющими собой те из обобщенных ко-
ординат управляемой системы, сведения об изменении которых поступают на управляющую систему. Наблюдаемыми и переменными, в частности, могут быть переменные состояния xi (t) .
Если рассматривать эти переменные как компоненты многомерных векторов, то они выразятся так:
|
|
x1(t) |
|
|
|
r1(t) |
|
|
|||
x(t) = |
x2 (t) |
; r (t) = |
r2 (t) |
; |
|
||||||
|
... |
|
|
|
... |
|
|
|
|
||
|
|
xn (t) |
|
|
|
rm (t) |
|
|
|||
|
|
|
|
|
|
|
|
|
|
|
(1) |
|
|
|
f1(t) |
|
z1(t) |
|
|
|
|
||
|
|
|
|
|
|
|
|||||
|
|
|
f2 (t) |
|
z2 (t) |
|
|
|
|
||
f (t) = |
|
... |
|
; z (t) = |
... |
|
|
, |
|
||
|
|
|
|
|
|
|
|
|
|||
|
|
|
fk (t) |
|
zl (t) |
|
|
|
|
||
|
|
|
|
|
|
|
|
|
|
|
возмуще- |
где векторы: x(t) – состояния; r (t) – управления; f (t) – |
ния и z (t) – наблюдения.
Вдальнейшем для упрощения предполагается, что вектор состояния совпадает с вектором наблюдения.
Влюбой момент времени t состояние управляемой системы
является функцией начального состояния |
x(t0 ) , векторов |
r (t0 ) и |
|
|
|
f (t0 ) , т.е. |
|
|
|
|
|
x(t) = X{x(t); r (t,t0 ); |
f (t,t0 )}. |
(2) |
Уравнение (2) можно рассматривать как уравнение математической модели управляемой системы. Для систем, описываемых дифференциальными уравнениями, написанные выше уравнения можно привести к виду
dx = X |
{x(t); r (t); f (t)}. |
(3) |
|
|
|
dt
Часто на изменение вектора состояния x(t) (или на его производные) и вектора управления r (t) накладываются ограничения вида
52
|
|
|
|
|
|
|
|
|
x(t) A(t), |
||
|
|
, |
|
|
|
r (t) B(t)
которые означают, что изменения векторов x(t)
быть ограничены замкнутыми областями A(t) и
(4)
и r (t) должны
B(t) , соответст-
венно векторного пространства состояний и векторного пространства управлений.
Так как технологический процесс представляется как совокупность действий его звеньев, подчиненных решению единой цели, определяемой экстремумом некоторого функционала E , то справедливо уравнение
|
(5) |
E = E{x(t); r (t); f (t)}. |
Рассмотрим вопросы описания целей функционирования звеньев технологического процесса.
Существенное значение приобретают полнота, четкость описания цели функционирования сложной системы и перечень решаемых ею задач. Если цели и задачи системы определены, можно ставить вопрос об оценке качества ее функционирования. Качество функционирования сложной системы будем оценивать с помощью показателей эффективности. Под показателем эффективности технологического процесса будем понимать такую числовую характеристику системы, которая оценивает степень приспособленности системы к выполнению поставленных перед ней задач. По существу выбор показателя эффективности является заключительной стадией формулировки целей и задач процесса. Без указания показателя эффективности формулировка целей и задач не приобретает необходимой четкости. Вместе с тем целесообразно подчеркнуть, что выбор показателя эффективности оказывает существенное влияние на интерпретацию свойств технологического процесса и результатов его исследования.
Рассмотрим некоторый производственный процесс. При описании целей и задач необходимо указать перечень изделий, для выпуска которых он предназначен. Однако если мы ограничимся только упомянутым перечнем, то не получим нужных сведений для обоснованной оценки качества функционирования процесса. Пусть показателем эффективности рассматриваемого производственного процесса служит производительность, измеряемая количеством изделий, выпускаемых в течение фиксированного интервала времени. Оценивая качество производственного процесса с помощью этого критерия, будем придавать наиболее существенное значение факторам, способствующим достижению максимальной производи-
53
тельности. При одностороннем подходе обеспечение максимальной производительности будет неизбежно сочетаться с ухудшением других характеристик производственного процесса (расхода сырья, износа оборудования, расхода энергии, фонда зарплаты и т.п.).
Аналогичные рассуждения можно привести и для других показателей эффективности. Например, при использовании в качестве показателя эффективности величины себестоимости продукции такие факторы, как экономия сырья, износ оборудования, расход энергии и фонда зарплаты, будут иметь больший вес, в то время как факторы, связанные с производительностью оборудования, отойдут на второй план.
Очевидно, что для производственного процесса надо выбирать такие показатели эффективности, которые учитывают себестоимость продукции, производительность оборудования, величину прибыли, рентабельность и др.
Из рассмотренных примеров ясно, что только выбор показателя эффективности (целей функционирования) для динамического технологического процесса делает описание целей и задач вполне законченным.
Расчет показателей эффективности для технологического процесса представляет собой весьма сложную задачу, которая требует привлечения специальных математических методов и, как правило, решается с помощью быстродействующих вычислительных машин.
Для того чтобы показатель эффективности достаточно полно характеризовал качество процесса, он должен учитывать все основные особенности и свойства последнего, а также условия его функционирования и взаимодействие с внешней средой. Таким образом, показатель эффективности определяется функционированием технологического процесса. С этой точки зрения можно представить себе множество возможных процессов, элементы которого отличаются друг от друга за счет различных условий и режимов работы системы.
Каждому элементу этого множества можно поставить в соответствие элемент другого множества – значения показателя эффективности процесса, т.е. показатель эффективности является функционалом от характера осуществления технологического процесса.
В связи с тем, что на технологический процесс воздействуют случайные факторы, значения функционалов оказываются случайными величинами. Это создает известные неудобства при использовании их в качестве показателей эффективности. Поэтому при выборе показателей эффективности пользуются средними значениями соответствующих функционалов, например, средним количе-
54
ством изделий, выпускаемых за смену, себестоимостью продукции, прибылью и другими показателями, рассматриваемыми как средние величины. Следовательно, решение проблемы функционирования технологического процесса состоит в том, чтобы найти вектор управления r (t) , обеспечивающий экстремальные значения условия
|
(6) |
E{x(t); r (t); f (t)} |
и одновременно удовлетворяющий ограничениям и связям, налагаемым его внутренними свойствами.
Решение этой экстремальной проблемы ввиду ее трудности можно осуществить с помощью метода последовательных приближений, причем первое и второе приближения определяются в результате: а) этапа идеальной или первичной оптимизации, состоящей в нахождении идеального, но обычно нереализуемого вектора управления rид (t) ; б) этапа вторичной оптимизации (оптимизация
качества управления), в результате которой находится оптимальный и в то же время реализуемый вектор управления rопт (t) .
На первом этапе учитывается лишь важнейшее свойство технологического процесса. Этап вторичной оптимизации заключается в получении решения, наименее отличающегося от идеального и в то же время наиболее полно учитывающего ограничения и связи, налагаемые свойствами управления процессом.
Для количественной характеристики отклонение оптимального реализуемого решения E от идеального Eид вводится величина,
представляющая функционал Q1 , характеризующий эффективность
Q1 = Q{Eид − E}, |
(7) |
где Eид – экстремум показателя цели управления; E – |
значение по- |
казателя цели управления (эффективность), обеспечиваемое реальной системой.
Основная задача синтеза технологического процесса состоит в том, чтобы достигнуть наивыгоднейших условий компромисса между противоречивыми требованиями качества и реализуемости управления.
Показателем, характеризующим эффективность технологического процесса, можно назвать функционал
C1 = C{Q1, P}, |
(8) |
55

где P – величина, характеризующая условие реализуемости управляющей системы (например, меру ее точности, стоимости, сложности, надежности и др.).
В частном случае функционал (8) может иметь вид
C1 = Q1 + λP , |
(9) |
где λ – некоторый весовой коэффициент.
Для вторичной оптимизации характерна задача определения вектора управления r (t) , обеспечивающего минимум величины:
C1 = C{Q1, P}.
Оптимальный реализуемый алгоритм управления Rопт можно представить в виде
|
|
rопт (t) = Rопт{x(t),t}. |
(10) |
Следовательно, проблема синтеза технологического процесса состоит в определении и реализации вектора управления r (t) ,
обеспечивающего экстремум показателя эффективности управления (10) при достижении цели управления (8) и удовлетворяющего связям (2) и ограничениям (4).
В таком виде решение общей задачи управления сложно, и оно заменяется часто более простой задачей, когда показатель эффективности не зависит в явной форме от показателя цели. В этом случае чаще всего показателем эффективности может служить показатель точности изделия, т.е. функционирование системы определяется возможностью предсказания с достаточной степенью точности реакции системы на заданное входное воздействие. При этом вектор ошибки εид будет равен
εид (t) = xид (t) = x(t) , |
(11) |
где xид и x(t) – соответственно идеальный и реальный векторы со-
стояния производственного процесса. Показатель точности тогда выразится в виде функционала от ошибки
l(t) = Ф{εид (t)}. |
(12) |
Очевидно, что решение задачи минимизации |
функциона- |
ла (12) значительно проще минимизации функционала (10).
В качестве показателя точности можно выбрать функционал
вида
56
T |
|
l = ∫ ϕ{lид (t)}dt , |
(13) |
0 |
|
где ϕ{lид (t)} – некоторая непрерывная функция от εид (t) .
Функционал l является мерой отклонения в интервале (0,T ) действительного вектора состояния x(t) от идеального вектора состояния xид (t) совместно с имеющимися ограничениями на изменение вектора r (t).
Иногда интерес представляет мера полного отклонения на достаточно большом интервале времени, т.е. вместо функционала (13) с конечными пределами рассматривается функционал вида
∞ |
|
l = ∫ ϕ{lид (t)}dt |
(14) |
−∞
с бесконечными пределами.
Возможен также и другой случай, когда интерес представляет мера ошибки лишь в определенный момент времени t = T . В этом случае
l = ϕ{εид}, |
(15) |
при t = T .
Решение задачи на минимум функционала (14) при имеющихся ограничениях в связях позволяет найти оптимальный вектор состояния xопт (t) [вектор задания – q(t) ].
На рис. 4 изображена схема, поясняющая рассмотренный выше принцип управления технологическим процессом, когда показателем эффективности управления является показатель точности εид
изготовляемого прибора.
Пусть позиция I – идеальный производственный процесс изготовления РЭС или его модель, в результате которого получается прибор с характеристикой xид.
Позиция II – исследуемый реальный технологический процесс изготовления РЭС, в результате которого получается прибор с реальной точностной характеристикой x .
Позиция III – вычислитель идеального режима (функционирования) технологического процесса, служащий для построения идеального производственного процесса, в результате которого выходит прибор с характеристикой xид.
57
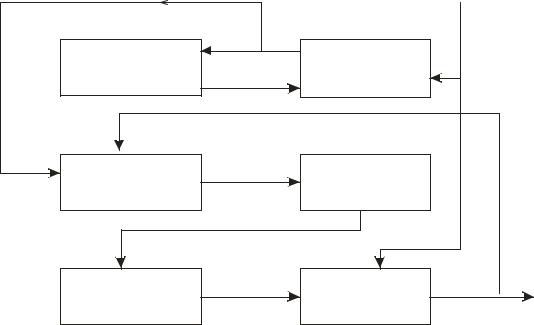
III |
Хид |
|
I |
|
|
|
|
||
Вычислитель |
|
|
Идеальная модель |
|
идеального режима |
|
|
|
|
Гид |
|
технологического |
|
|
технологического |
|
|
||
процесса |
г |
|
процесса |
|
|
|
|
|
|
Х |
|
|
|
|
ХХид |
|
|
|
|
Сравнивающее |
VI |
IV |
Оптимизатор |
|
|
|
|
||
|
|
точности технологи- |
|
|
устройство |
|
|
|
|
|
|
ческого процесса |
|
|
|
|
|
|
|
Линейный |
V |
II |
Исследуемый |
Х |
|
|
|||
|
|
|
||
преобразователь |
|
|
технологический |
|
сигнала управления |
|
|
процесс |
|
Рис. 4. Обобщенная функциональная схема оптимального управления технологическим процессом производства РЭС по точностному параметру
Позиция IV – оптимизатор точности управления технологическим процессом, служащий для создания такого воздействия через усилитель V, чтобы характеристика изготовляемой РЭС отвечала определенной заданной точности.
Работу системы, управляющей точностными технологическими (производственными) характеристиками изготовляемой РЭС, можно представить как работу следящей системы, где задающим входным воздействием принято считать значение точностного показателя идеального технологического процесса. Необходимо также устройство, реализующее (моделирующее) идеальный технологический процесс (цикл) и идеальную систему управления им (III) при воздействии на них реальных систематических и случайных факторов. Таким устройством может быть электронно-вычислительная машина.
Значение величины реальной точностной характеристики объекта производства x сравнивается в устройстве сравнения VI со значением идеальной характеристики объекта xид . Результат срав-
нения εид оптимизируется оптимизатором IV, и его значение явля-
ется управляющим сигналом для реального технологического процесса, т.е. воздействует на него, изменяя параметры процесса таким образом, чтобы получить минимальное отличие значений точност-
58
ных характеристик реального объекта производства от его идеальных значений. Как видно из рис. 4, оптимальный вектор состояния xопт или вектор задания q(t) сравнивается с действительным век-
тором состояния x(t) в сравнивающем устройстве, на выходе которого получается сигнал ошибки ε(t) :
ε(t) = xопт − x(t) . |
(16) |
В этом случае необходимо выполнение требования устойчивости технологического процесса.
2.5. Основные направления развития технологии радиоэлектронных средств
Основными направлениями развития РЭС являются микроминиатюризация, повышение степени интеграции и комплексный подход к разработке. Микроминиатюризация – это микромодульная компоновка элементов с применением интегральной и функциональной микроэлектроники. При микромодульной компоновке элементов осуществляют микроминиатюризацию дискретных ЭРЭ. В основе интегральной микроэлектроники лежит использование ИС и больших интегральных схем (БИС), применение групповых методов изготовления, машинных методов проектирования ТП, изготовления и контроля изделий.
Функциональная микроэлектроника основана на непосредственном использовании физических явлений, происходящих в твердом теле или вакууме (магнитные, плазменные и т.д.). Элементы создают, используя среды с распределенными параметрами. Основной задачей здесь является получение сред с заданными свойствами.
Трудоемкость производства сборочных единиц РЭС может быть представлена в таком соотношении: механообработка – 8–15 %, сборка – 15–20 %, электрический монтаж – 40–60 %, наладка –
20–25 %.
Следовательно, основными конструктивно-технологическими задачами производства РЭС являются разработка ИС на уровне ячеек и сборочных единиц и совершенствование технологии их изготовления, повышение плотности компоновки навесных элементов на ПП и плотности печатного монтажа; совершенствование методов электрических соединений модулей 1–4- го уровней, развитие авто-
59
матизированных и автоматических методов, средств наладки и регулировки аппаратуры сложных радиотехнических систем (РТС), создание гибких автоматизированных производств.
В технологии производства РЭС используются процессы, свойственные машино- и приборостроению: литье, холодная штамповка, механическая обработка, гальванические и лакокрасочные покрытия.
Формирование технологии РЭС можно условно характеризовать следующими этапами.
Первый этап: до 1950 г. – разработка и внедрение поточноконвейерных способов сборки и монтажа, прогрессивных способов выполнения отдельных операций при изготовлении деталей и узлов РЭС, изготовленных на электронных лампах и с навесным монтажом.
Второй этап: 1950–1965 гг. – разработка и внедрение механизированных и автоматизированных способов выполнения операций сборки, монтажа и регулировки РЭС, использующей печатный монтаж и работающей на полупроводниковых приборах; также внедрение автоматизированных и механизированных ТП изготовления деталей и узлов РЭС.
Третий этап: настоящее время – характерно для РЭС как переходный этап к следующему, высшему этапу совершенствования конструкции и технологии РЭС с использованием принципов микроэлектроники и проведением в связи с этим работ в области решения проблемы интегрирования различных технологических стадий. Решение этой проблемы позволит исключить большое количество схемных соединений и полностью автоматизировать операции, выполняемые взамен сборки.
Уровень технологии в настоящее время достаточно высок и обеспечивает создание малогабаритной и высоконадежной аппаратуры. Технология постоянно обновляется, ее совершенствование является важным условием технического прогресса.
К основным направлениям совершенствования современной технологии можно отнести:
∙ переход от прерывистых (дискретных, циклических) процессов к непрерывным поточным процессам, обеспечивающим увеличение масштаба производства и эффективное использование машин и оборудования; внедрение «замкнутой» (безотходной) технологии с целью наиболее полного использования сырья, энергии, топлива, ликвидации отходов производства, оздоровления окружающей среды;
60