
Учебник по Технологии
.pdfляются связи параметров системы с критериями качества, т.е. величинами, однозначно связанными с качеством системы, которые образуют оптимизационную модель).
Объектом технологической оптимизации являются схемотехнические и топологические решения устройства, при синтезе которых оптимально удовлетворены требования обеспечения заданных эксплуатационных параметров, найдены допустимые отклонения электрических и конструкционных параметров от их номинальных значений и ТП их изготовления. При технологической оптимизации необходимы:
∙оценка вероятности выхода годных изделий, учитывающая, что оптимизируется единая система с взаимновлияющими параметрами (условной вероятностью);
∙поиск такого сочетания конструкционных параметров, чтобы вероятность выхода годных была максимальна.
Если решена первая задача, то на основе этого для решения второй можно использовать стандартные методы оптимизации. Основой алгоритма в этом случае является циклическое определение соответствия всех электрических параметров полям допусков при случайных выборах значений конструкционных параметров. Массив значений конструкционных параметров формируется так же, как в методе статистических испытаний с использованием датчика случайных чисел при учете корреляции между параметрами. Законы распределения конструкционных параметров принимаются гауссовскими.
Для каждой реализации массива значений конструкционных параметров последовательно рассчитываются значения электрических параметров и сравниваются с допустимыми отклонениями. При несоответствии значения параметра полю допуска расчет для данной реализации прекращается, и формируется следующая реализация. Та, при которой удовлетворены ограничения на все электрические параметры, регистрируется, после чего цикл повторяется для следующей реализации. Соотношение общего числа реализаций и реализаций, удовлетворяющих всем наложенным ограничениям, рассматривается как условная вероятность выхода годных.
При изменяемом ТП минимум технологической себестоимости годного изделия достигается взаимосвязанным выбором номинальных значений его конструкционных параметров, технологической точности и структуры ТП. Выделим три наиболее общих случая:
71
1)устойчивый и стабильный ТП целенаправленно изменяется по точности без изменения структуры за счет изменения точности операций;
2)ТП целенаправленно изменяется по структуре и точности, оставаясь устойчивым и стабильным;
3)ТП неустойчив за счет наличия систематических погрешностей и подлежит периодической корректировке.
Для отыскания условий оптимума во всех трех случаях приемлемы стандартные методы оптимизации. Для первых двух случаев задача оптимизации формулируется одинаково.
Пусть Y – вектор номинальных значений управляемых эксплуатационных параметров; s – вектор их среднеквадратичных отклонений. Минимизируемой (целевой) функцией является технологическая себестоимость годного изделия, критерием оптимальности – ее условный минимум min Ct(Y,s) при выполнении ограничений: Y YP, Y YD; s sP, где YP – область работоспособности; YD – допустимая область; sP – область реализуемых среднеквадратичных отклонений.
Для третьего случая в целевую функцию включается Tk – время до корректировки ТП, таким образом, целевая функция имеет вид Ct(Y,s,Tk) при неизменном критерии оптимальности – условном минимуме целевой функции в случае выполнения, помимо трех указанных и четвертого ограничения Tтп > Tk > 0 (Tтп – время, в течение которого функционирует ТП). Выбор точности ТП без изменения его структуры связан с выбором технологического оборудования по показателям точности, выбором точности поддержания режимов технологических операций и методов обеспечения этой точности. В результате точность ТП связана с величиной технологической себестоимости и определяет вероятность выхода годных изделий. Таким образом, целевая функция имеет вид
Ct = Ct(s)/Py(Y, s) → min, |
(18) |
где Ct(s) – себестоимость изготовления партии изделий; Py(Y, s) – вероятность выхода годных изделий.
В общем случае в процессе технологической оптимизации варьируется точность выполнения отдельных операций в зависимости от выбора технологического оборудования и методов обеспечения этой точности.
72
Все перечисленные выше изменения должны быть взаимосвязаны, т.е. решение задачи в рамках автономных систем автоматизированного проектирования конструкций (САПР К) и систем автоматизированного проектирования технологических процессов (САПРТ П) не представляется возможным.
Основными этапами разработки технологических процессов являются:
1. Изучение конструкции детали. По рабочему чертежу де-
тали и чертежам сборочных единиц, куда входит деталь, получают полное представление о форме детали, размерах и их точности, шероховатости обработанных поверхностей, физических и технологических свойствах материала, функциях детали в изделии и о специальных технических требованиях; выясняют, какие поверхности являются рабочими и какие элементы конструкции (поверхности, линии, точки) являются главными конструктивными базами.
Важнейшей задачей изучения чертежа является оценка технологичности конструкции детали и степени соответствия конструкции требованиям заданного объема производства. Анализ технологичности детали включает следующие основные проверки: целесообразность формы детали, степень ее пригодности для получения заготовки высокопроизводительными методами (литьем, штамповкой и др.); правильность выбора марки материала с учетом условий производства и назначения детали; соответствие номинальных размеров ГОСТ 6636–60; целесообразность допусков на размеры, указанные в чертеже, с точки зрения служебного назначения детали и условий производства; правильность основных размеров и увязку размерных цепей; правильность выбранных защитных покрытий; отсутствие ошибок и неточностей в выполнении графики чертежа; отсутствие ошибок в технических требованиях чертежа.
При оценке технологичности конструкции следует учитывать требования надежности работы детали в изделии в процессе эксплуатации и требования оптимальной стоимости ее изготовления.
Составление плана технологических операций обработки детали выполняют в зависимости от материала детали, точности размеров и параметров шероховатости поверхностей.
2. Расчет операционных размеров. Операционными назы-
ваются размеры, координирующие обрабатываемые поверхности в технологических операциях. Операционные размеры всех операций, предшествующих операции окончательной обработки, отли-
73
чаются от соответствующих чертежных размеров на величину припуска.
Припуском называется слой материала, прилегающий к поверхности заготовки и подлежащий удалению с целью получения заданного размера обработанной поверхности.
В промежуточных операциях обработки поверхностей следует различать два вида припуска: припуск, который удаляется с обрабатываемой поверхности в виде отхода (стружки), и припуск, который образуется в данной операции и подлежит удалению при обработке в следующей. Этот последний входит в состав операционного размера данной операции и определяется при проектировании технологического процесса. Припуск обусловлен необходимостью устранения в последующих операциях обработки погрешностей размеров, формы поверхности, шероховатости и дефектного слоя, возникающих в рассматриваемой операции. Вместе с тем размер припуска ограничивается экономическими факторами: трудоемкостью обработки, отходом материала в стружку, износом режущего инструмента, расходом энергии на обработку и др. Поэтому выбор оптимального припуска является весьма важной задачей в проектировании технологических операций обработки. На основании теоретических и экспериментальных исследований оптимальный припуск для обработки плоских поверхностей определяют по формуле
Zi = Rzi + Ti + δi + Ui + F , |
(19) |
где Zi – припуск, образующийся в данной операции; Rzi – |
параметр |
шероховатости поверхности, обработанной в данной |
операции; |
Ti – толщина дефектного слоя; δi – допуск операционного размера в данной операции; Ui – погрешность установки в i-й операции;
F – погрешность расположения поверхностей, вызываемая термической обработкой, учитывается в припусках операционных размеров операций, предшествующих термической обработке.
Для обработки поверхностей тел вращения припуск на диаметр определяется по формуле
Zi = (2Rzi + Ti ) + δi + Ui + F. |
(20) |
Допуск δi выбирают в соответствии с технологическими воз-
можностями проектируемой операции обработки.
В повседневной практике для типовых технологических операций припуски берутся по таблицам справочников или отраслевых нормалей.
74
Операционные размеры определяются следующим уравнением общего вида:
|
An = A + Zn+l + Zn+2 +… + Zn+m, |
(21) |
|
где |
Ап – операционный размер n-й |
технологической |
операции; |
А – |
номинальный размер по чертежу |
детали; Z – припуск на сле- |
дующую операцию; т – количество следующих операций обработки.
Размер исходной заготовки, координирующий поверхность, подлежащую обработке на основе уравнения (21), определяют по формуле
A0 = A + Z1 + Z2 + ... + Zm . |
(22) |
3. Выбор и обоснование способа получения исходной заго-
товки. В зависимости от размеров формы, материала и программы выпуска детали выбирается способ изготовления исходной заготовки. Рациональная форма заготовки должна быть максимально подобной форме готовой детали. Размеры заготовки отличаются от размеров готовой детали на сумму операционных припусков.
Для металлических деталей простой формы в качестве заготовок применяются отрезки стандартных профилей: круглых, квадратных, шестигранных, труб, уголков, листов, полос и т.д.
Для деталей сложной формы на заводах радиотехнических изделий применяют следующие основные способы изготовления заготовок: литье, горячая и холодная штамповка, прессование из пластмасс и металлокерамики. При разработке технологии выбирают наиболее экономически целесообразный способ получения заготовки, определяют ее конструкцию.
4. Выбор технологического оборудования. Выбор оборудо-
вания для выполнения операций технологического процесса основывается на выполнении требований: высокой производительности процесса формообразования; геометрической точности и оптимальной стоимости обработки. Производительность и точность обработки определяются типом и физическим состоянием оборудования, а стоимость обработки – его потребляемой мощностью, поэтому определенным массам и габаритам деталей соответствуют определенные типоразмеры технологического оборудования. Сведения об эксплуатационных данных технологического оборудования берут из технических характеристик, имеющихся в каталогах или паспортах.
75
5. Проектирование операций технологического процесса.
На основе перечня операций обработки отдельных поверхностей компонуют операции технологического процесса детали, реализуя возможности совмещения обработки двух и более различных поверхностей в одной операции. Контрольные операции вводят в общую последовательность операций обработки в тех местах, где это окажется целесообразным. Термическая обработка делит технологический процесс на два этапа: предшествующий термической обработке и последующий. На первом этапе выполняют операции предварительной обработки точных поверхностей и окончательной обработки поверхностей низких классов точности и шероховатости, на втором этапе (после термической обработки) − операции окончательной обработки точных поверхностей. Это обусловлено тем, что в процессе термической обработки происходит деформация изделий, сопровождаемая изменениями формы, размеров и относительного расположения поверхностей. На втором этапе обработки эти погрешности могут быть исправлены.
При определении объема работ, включаемых в отдельные операции, необходимо выполнить условие равенства или кратности нормы штучного времени на операцию такту производства изделий при заданной программе выпуска. Операциям технологического процесса присваиваются порядковые номера и названия. Предпочтительной является пятковая нумерация операций (5, 10, 15, 20...). Название операций, как правило, соответствует названию технологического оборудования, на котором выполняется операция.
После составления общего плана и определения ориентировочного состава операций приступают к техническому оформлению их в соответствии с Единой системой технологической документации.
Проектирование операции включает в себя:
∙вычерчивание операционных эскизов для формообразующих операций;
∙описание содержания операций в виде перечня переходов определенной последовательности;
∙выбор параметров режимов работы технологического оборудования;
∙расчет ожидаемой точности обработки;
∙техническое нормирование объема работ каждой операции; разработка технических заданий на проектирование специальной оснастки;
76
∙технико-экономическое обоснование выбранного варианта технологического процесса;
∙техническое оформление операционных карт и карты технологического маршрута.
6. Операционные эскизы. На операционном эскизе обрабатываемое изделие (заготовка или деталь) изображают в том виде, какой она приобретает после выполнения данной операции. Изображение детали (заготовки) на эскизе выполняется по методу прямоугольного проектирования, при этом ее располагают на эскизе в рабочем положении, т.е. так, как она установлена на станке при выполнении операции обработки. Эскиз выполняется с помощью чертежных инструментов с соблюдением всех требований ГОСТ, применяемых для Единой системы конструкторской документации, но в произвольном масштабе.
На операционном эскизе проставляют только те размеры, которые получаются в данной операции. Поверхности детали, выбранные как установочные базы в данной операции, обозначают условными знаками.
Содержание операции записывается в соответствующей графе операционной карты кратко в повелительном наклонении с указанием номера обработанной поверхности, например: «обточить поверхность 1 с подрезкой торца 2»; операционные размеры в тексте не пишутся. Одним из переходов каждой операции является контроль, что обязывает рабочего и контролера проверять исполнительные размеры и технические требования, указанные на операционном эскизе.
Для каждого основного перехода операции формообразования назначают параметры режима работы технологического оборудования. К числу таких параметров относятся: скорость резания, подача, глубина резания (для металлорежущих станков), усилие и температура прессования, время выдержки (для переработки пластмасс) и др.
Параметрами режима работы технологического оборудования во многом определяются такие показатели качества изделия, как точность размеров и шероховатость поверхностей, физикомеханические и электрические и другие свойства. Для большинства операций обработки параметры режима работы технологического оборудования выбираются по справочникам, отраслевым и заводским нормалям, а в некоторых случаях устанавливаются опытным путем и вписываются в соответствующие операционные карты.
77
7. Расчет ожидаемой точности обработки. По принятой схеме установки детали в каждой операции определяется наличие или отсутствие погрешности базирования. В тех случаях, когда в схеме установки измерительная база детали не совмещена с установочной, всегда имеет место погрешность базирования. Следовательно, необходимо расчетом проверить соблюдение условия обработки без брака по операционному (исполняемому) размеру.
Исходными данными, используемыми при проектировании ТП, являются:
∙конструкторская документация на изделие, включающая рабочие чертежи деталей;
∙технические условия (ТУ), которые содержат требования к наиболее ответственным и сложным деталям и составляется обычно в тех случаях, когда все требования невозможно изложить в чертежах (назначение детали, методы контроля, общие сведения о хранении, транспортировке, клеймении);
∙программа выпуска изделия, представляющая собой перечень наименований изготавливаемых или ремонтируемых изделий с указанием срока выполнения по каждому наименованию и объема выпуска, т.е. общего количества изделий определенного наименования и типоразмера;
∙руководящие технические материалы;
∙справочные данные об оборудовании, нормативы на припуски и операционные допуски;
∙нормативы для технико-экономических расчетов.
В разработку ТП входит следующий комплекс взаимосвязанных работ:
∙подбор оптимального варианта получения заготовки и разработка маршрутной технологии;
∙подбор возможных типовых ТП;
∙определение содержания вновь разрабатываемых технологических oпeраций с установлением технологических баз;
∙определение необходимого оборудования, оснастки, средств механизации и автоматизации производственного процесса;
∙назначение и расчет режимов обработки, техническое нормирование процесса и определение необходимых профессий и квалификации рабочих;
78
∙расчет и проектирование производственных участков, составление планировок и разработка операций перемещения изделий
иотходов производства;
∙выбор и назначение внутрицеховых подъемно-транспорт- ных средств;
∙оформление документации ТП на бланках, предусмотренных ЕСТД, и его утверждение.
Основными этапами проектирования полного ТП являются следующие:
∙анализ технологичности изделия;
∙проектирование ТП обработки деталей;
∙проектирование ТП сборки;
∙разработка технологии контроля;
∙оформление технологической документации. Основные этапы проектирования частного ТП:
∙определение структуры процесса;
∙выбор технологического оснащения процесса (оборудования, инструмента, оснастки, измерительной аппаратуры) с разработкой технического задания (ТЗ) и заказом нестандартного оснащения;
∙расчет режимов обработки;
∙расчет технических норм времени;
∙выбор оптимального варианта ТП;
∙оформление технологической документации;
Остановимся на анализе этапов проектирования частного ТП.
Проектирование ТП имеет целью дать подробное описание процессов изготовления изделий с необходимыми техникоэкономическими расчетами и обоснованием выбранного варианта, так как ТП характеризуются своей многовариантностью. Из нескольких возможных вариантов ТП изготовления одного и того же изделия, равноценных с точки зрения технического принципа проектирования, выбирают наиболее эффективный и рентабельный вариант. При равной производительности сопоставляемых вариантов выбирают наиболее рентабельный, а при равных рентабельностях – наиболее производительный. Эффективность и рентабельность проектируемого ТП выявляют по всем элементам, из которых они складываются.
79
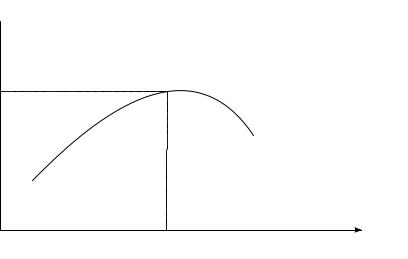
2.8.3. Этапы разработки частного технологического процесса
Первый этап проектирования частного ТП. Определение структуры процесса – это разбиение ТП на основные составляющие части (технологические операции).
Существует общее правило: чем больше годовая программа выпуска, тем на более мелкие операции следует «дробить» технологические процессы. Такие ТП называют дифференцированными в отличие от концентрированных, состоящих из малого числа крупных операций. Однако дробление, или дифференциация, не может быть чрезмерным, так как слишком простые операции (например, завинчивание одного винта) вызывают быструю утомляемость рабочего, потерю интереса к выполняемой работе и снижению производительности труда. Чрезмерная дифференциация требует значительного увеличения производственных площадей и вызывает значительные потери вспомогательного времени на транспортировку заготовок и т.п. (рис. 7).
П П
П Пvax max
Д |
Д Д |
Дслм |
|
Рис. 7. Зависимость производительности (П)
от степени дифференциации (Д) технологического процесса
Рассмотрим, например, структуру ТП при изготовлении трансформатора с ферритовым магнитопроводом. При индивидуальном или опытном производстве (всего несколько штук в год) целесообразно построить структуру ТП из малого числа максимально крупных операций:
80