
Детали машин и основы конструирования
.pdf
ка D или стакана.
Рис. 12.10. Основные размеры крышек:
а) накладная (торцевая): б) закладная (врезная)
Размеры накладных (торцевых) (рис.12.10, а) и закладных (рис.12.10, б) крышек определяют по табл. 12.1.
ширина кольца l=6–8 мм (при D≤100 мм), l=8–10 мм (при D> 100 мм); высота кольца с=0,5l; l1≥l.
Таблица 12.1
Основные размеры накладных крышек подшипников
Основные размеры, мм |
Наружный диаметр подшипника D, мм |
|||
|
40-62 |
62-95 |
95-145 |
145-220 |
1 |
2 |
3 |
4 |
5 |
Диаметр болтов d3 |
М6 |
М8 |
М10 |
М12 |
Количество болтов Z |
4 |
4 |
6 |
6 |
Толщина фланца крышки h1 |
6 |
8 |
10 |
12 |
Толщина крышки δ2 |
5 |
6 |
7 |
8 |

Окончание табл. 12.1
|
1 |
2 |
|
3 |
4 |
5 |
Диаметр оси установки бол- |
|
|
D1=D+2,5d3 |
|
||
тов |
|
|
|
|
||
|
|
|
|
|
|
|
Наружный диаметр фланца |
|
|
D2=D1+2,0d3 |
|
||
Толщина |
цилиндрической |
|
|
δ3=(0,9–1,0)h1 |
|
|
части крышки |
|
|
|
|||
|
|
|
|
|
||
Размеры проточек: |
|
|
|
|
|
|
D3 |
|
D-0,5 |
|
D-1,0 |
D-1,5 |
D-1,5 |
b |
|
3 |
|
4 |
5 |
5 |
R3 |
|
1,0 |
|
1,6 |
2,0 |
2,0 |
Длина цилиндрической час- |
|
|
B1=(1,2–2,0)b |
|
||
ти |
|
|
|
|
||
|
|
|
|
|
|
|
Диаметр под манжетное уп- |
dу см. |
приложение 6 табл. 5 |
||||
лотнение |
|
|||||
|
|
|
|
|
|
|
Ширина под манжетное уп- |
bу см. |
приложение 6 табл. 5 |
||||
лотнение |
|
|||||
|
|
|
|
|
|
|
Фаска |
|
|
|
f см. табл. |
|
|
Диаметр отверстия под вы- |
d4=d2+(1,0-1,5), где d2 – диаметр вала |
|||||
ходной конец вала |
|
|
под уплотнение |
|
||
Отверстие |
для выпресовки |
|
|
d5=(2,0-3,0) мм |
|
|
манжетного уплотнения |
|
|
|
|||
|
|
|
|
|
Примечания. 1. Размер L принимают конструктивно. Размер H – в зависимости от толщины наружного кольца подшипника.
12.4. Конструирование стаканов
Применение стаканов при конструировании подшипниковых узлов обусловлено облегчением их сборки и разборки вне корпуса редуктора и удобством регулировки радиальных зазоров в подшипниках
изубчатых зацеплениях (рис. 12.5, рис. 12.6, рис. 12.7), с конструктивных соображений и в случаях установки вала в неразъемный корпус (рис. 12.3). Стаканы изготовляют обычно из чугуна СЧ-15, реже из стали.
Конструкция стакана и его размеры представлены на рис.12.11
итабл. 12.2.

Рис. 12.11. Стакан для установки двух подшипников
|
|
|
|
|
Таблица 12.2 |
||
Основные размеры стакана |
|
|
|
||||
|
|
|
|
|
|||
Основные размеры, мм |
Наружный диаметр подшипника D, мм |
||||||
<52 |
|
52÷80 |
|
80÷120 |
|
120÷170 |
|
|
|
|
|
||||
Толщина стакана h3 |
6 |
|
8 |
|
10 |
|
12 |
Диаметр установки болтов |
|
|
D1=Da+2,5d3 |
|
|||
Наружный диаметр фланца |
|
|
D2=D1+2,0d3 |
|
|||
Толщина фланца |
|
|
h2≥h3 |
|
|||
Толщина заплечика H |
|
по толщине наружного |
|
||||
|
|
|
кольца подшипника |
|
|||
Диаметр болтов d3 и их ко- |
определяют по табл. 12.1 приняв за D |
||||||
личество Z5 |
|
|
значение Da |
|
12.5. Уплотнения подшипниковых узлов
Уплотнения применяют для предотвращения вытекания смазочного материала из подшипниковых узлов, а также защиты их от

попадания пыли, грязи и влаги в полость редуктора. В зависимости от места установки в подшипниковом узле уплотнения делят па две группы: наружные – устанавливают в крышках подшипников и внутренние – устанавливают с внутренней стороны подшипниковых узлов.
Наружные уплотнения. Выбор типа уплотнения зависит от способа смазывания подшипников, окружной скорости вала, рабочей температуры и характера внешней среды.
Манжетные уплотнения. Их используют при смазывании подшипников как пластичным, так и жидким материалом при низких и средних скоростях V ≤10 м/с. Резиновые армированные манжеты состоят (рис. 12.12) из корпуса 1, изготовленного из бензомаслостойкой резины, стального Г–образного каркаса 2 и браслетной пружины 3, которая стягивает уплотняющую часть манжеты и образует рабочую кромку. Манжеты, работающие в засоренной среде, снабжены «пыльником» (тип 2).
Рис. 12.12. Типы и конструкция резиновых манжет
Для предохранения смазочного материала от вытекания манжету обычно устанавливают рабочей кромкой внутрь корпуса, что обеспечивает к кромке доступ масла, уменьшающего износ ре-
зины. Для удобства выемки манжеты в крышке подшипника иногда предусматривают 2–3 отверстия диаметром 3–4 мм.
Размеры манжет выбирают в зависимости от диаметра участка вала под манжетное уплотнение по таблице 5 (приложение 6).
Щелевые (рис.12.13), лабиринтные (рис.12.14, а) и комбинированные(рис. 12.14, б) уплотнения эффективно работают при любом
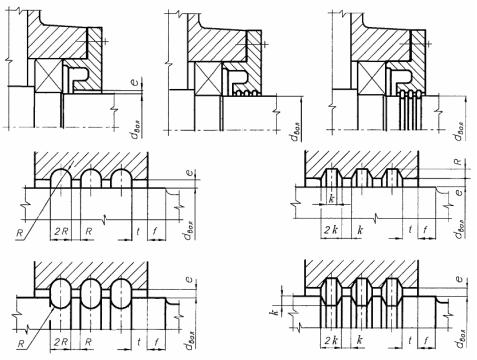
способе смазывания подшипников, практически при любой скорости, так как не оказывают сопротивления вращению вала. Такие уплотнения надежно удерживают смазочный материал от вытекания под действием центробежной силы. Формы проточек щелевых уплотнении см. на рис. 12.13. Зазоры щелевых и лабиринтных уплотнений целесообразно заполнять пластичным смазочным материалом, создающим дополнительный жировой заслон для попадания извне пыли и влаги.
Рис. 12.13. Формы щелевых канавок
Рекомендуемые размеры канавок щелевых уплотнений выбирают по табл. 12.3.
На рис. 12.14 представлены лабиринтные и комбинированные уплотнения. Размеры зазоров в лабиринтах выбирают по табл. 12.4.
Внутренние уплотнения. Установка и конструкция внутренних уплотнений зависят от способа смазывания подшипников и конструкции подшипникового узла.
а) При смазывание разбрызгиванием подшипников картерной смазкой при нижнем или боковом расположении червяка в червячных редукторах и шестерни в цилиндрических и конических редукторах масло, выжимаемое из зацепления, обильным потоком
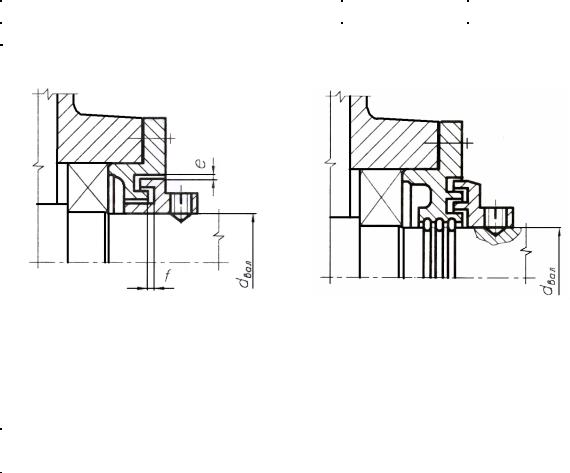
выбрасывается в рядом расположенные подшипники. Во избежание попадания в подшипники продуктов износа червячных и зубчатых колес, а также излишнего полива маслом подшипниковые узлы закрывают с внутренней стороны корпуса маслозащитными шайбами (рис. 12.15). Толщина шайб 1,2-2,0 мм; зазор между корпусом и наружным диаметром шайбы – 0,2-0,6 мм (на чертежах этот зазор не показывается).
|
|
|
|
Таблица 12.3 |
Размеры канавок щелевых уплотнений, мм |
|
|||
|
|
|
|
|
dвал |
10≤ dвал≤50 |
50≤ dвал≤85 |
|
85≤ dвал≤100 |
e |
0,2 |
0,3 |
|
0,4 |
R, f, k |
1,5 |
2,0 |
|
2,0 |
t |
5 |
5 |
|
2 |
минимальное число щелей |
3 |
4 |
|
5 |
а) |
б) |
|
|
|
Рис. 12.14. Уплотнения: а) лабиринтное; б) комбинированное
Таблица 12.4
Рекомендуемые размеры зазора в лабиринтах, мм
dвал |
10≤ dвал≤48 |
|
50≤ dвал≤84 |
85≤ dвал≤110 |
e |
0,2 |
|
0,3 |
0,4 |
|
|
f=5e |
|

Рис. 12.15. Маслозащитные шайбы:
а, 6 – со ступицей; в, г – с центрирующим кольцом
б) При смазывание подшипников пластичным материалом. При этом способе смазывания подшипниковые узлы должны
быть изолированы от внутренней полости редуктора во избежание вымывания пластичного смазочного материала жидким, применяемым для смазывания зацепления.
Уплотнение мазеудерживаюшим кольцом (рис. 12.16, а). Такое уплотнение является комбинированным – центробежным и щелевым одновременно. Кольцо вращается вместе с валом и имеет две – четыре круговые канавки треугольного сечения и зазор между кольцом и корпусом (стаканом) 0,1–0,3 мм (на чертежах зазор не показывают); выход за торец корпуса стакана С=1–2 мм. Выступающий за пределы корпуса участок кольца отбрасывает жидкое масло, остальная цилиндрическая поверхность с проточками удерживает пластичный смазочный материал от вымывания.
Рекомендуемые размеры мазеудерживающих колец приведены на рис. 12.16, б.
Торцовое уплотнение стальной шайбой (рис. 12.17). Оно относится к типу контактных и весьма эффективно предохраняет подшипник от вытекания смазочного материала и попадания воды и грязи.

Кольцо между шайбой и буртиком вала создает ее точное центрирование.
а) |
б) |
Рис. 12.16 Уплотнение мазеудерживаюшим кольцом:
а – конструкция подшипникового узла; б – рекомендуемые размеры колец
Рис. 12.17. Уплотнение стальной шайбой с прижимным кольцом

13. ВЫБОР СПОСОБА СМАЗКИ И СМАЗОЧНЫХ МАТЕРИАЛОВ ПЕРЕДАЧ И ПОДШИПНИКОВ
Смазка зубчатых и червячных зацеплений и подшипников уменьшает потери на трение, износ и нагрев деталей.
По способу подачи смазки к зацеплению различают картерную и циркуляционную смазки.
Картерная смазка осуществляется окунанием венцов зубчатых и червячных колес (или червяков) в масло, заливаемое внутрь корпуса. Эту смазку применяют при окружных скоростях в зацеплении зубчатых передач V<12 – 15 м/с, в зацеплении червячных передач при скорости скольжения V<10 м/с. При большей скорости масло сбрасывается центробежной силой. При смазывании окунанием объем масла заливаемого в картер, определяется из расчета (0,4-0,8) л масла на 1 кВт передаваемой мощности.
Глубина погружения в масло hт зубьев колеса в цилиндрических редукторах 2т<hт<0,25d2 (где т – модуль зацепления); при расположении шестерни ниже колеса hт=(0,1–0,5)d1, при этом hтim=0,2m. Рекомендуется, чтобы уровень масла был не выше центра нижнего тела качения подшипника (шарика или ролика) (рис.13.1).
Вконических редукторах должны быть полностью погружены в масляную ванну зубья конического колеса или шестерни.
Вчервячных редукторах при окунании в масляную ванну чер-
вячного колеса 2т< hт<0,25d2; при нижнем или боковом расположении червяка hт=(0,1–0,5)d1, причем hтin≥2,2m. Одновременно рекомендуется, чтобы уровень масла был не выше центра нижнего тела
качения подшипника. Если при этом hтin<2,2m, то на валу червяка размещают брызговики (рис. 13.1), забрасывающие масло па червячное колесо.
1 вариант |
2 вариант |
Рис. 13.l. Брызговики на валу червяка.
В двухступенчатом цилиндрическом редукторе при окружной скорости колес тихоходной ступени Vокр>1 м/с достаточно погружать в масло только колесо тихоходной ступени. При Vокр<1 м/с рекомендуется погружать колеса обеих ступеней. В соосных редукторах также рекомендуется погружать в масло колеса обеих ступеней. В косозубых и червячных передачах масло увлекается зубьями колеса или витками червяка в сторону одного из подшипников, вызывая в нем дополнительные гидравлические потери и снижая качество уплотнения подшипникового узла. В этом и другом случаях для предотвращения обильного забрасывания масла в подшипники устанавливают мазеудерживающие кольца и шайбы (рис.12.16, 12.17).
При окружной скорости зубчатых колес Vокр>12 м/с применяют циркуляционную смазку зацепления, при которой масло из картера или бака подается насосом по трубопроводу через фильтр и холодильник к месту зацепления.
Для открытых передач, работающих при окружных скоростях Vокр<4 м/с, обычно применяют периодическое смазывание зацепления вязкими маслами или пластичными мазями, которые наносят на зубья через определенные промежутки времени. В некоторых случаях (при Vокр<1,5 м/с) применяют капельное смазывание или смазывание погружением в ванну, наполненную вязким маслом.
Смазывание подшипников качения редукторов общего назначения осуществляют жидкими маслами или пластичными мазями. Наиболее благоприятные условия для работы подшипников обеспечивают жидкие масла. Преимущества их заключаются в высокой стабильности смазывания, меньшем сопротивлении вращению, способности отводить теплоту и очищать подшипник от продуктов износа. Жидкое масло легче заменить без разборки узла. Недостаток жидких масел связан с необходимостью применения сложных уплотнений.
На практике подшипники стремятся смазывать тем же маслом, которым осуществляется смазывание деталей передач механизма. При этом смазывание подшипников обычно осуществляется за счет разбрызгивания масла зубчатыми колесами, в результате чего масло попадает в подшипниковые узлы. Однако такое смазывание эффективно при окружной скорости колес Vокр>2-3 м/с. При меньших скоростях смазывание подшипников производят индивидуально пластичными мазями.
Пластичные мази лучше, чем жидкие масла, защищают подшипник от коррозии, особенно при длительных перерывах в работе.