
Детали машин и основы конструирования
.pdf
Для их удержания в подшипнике и корпусе не требуются сложные уплотнения. При выборе пластичной мази учитывают рабочую температуру подшипникового узла и наличие в окружающей среде влаги. В узлах с интенсивным тепловыделением пластичные мази не применяют из-за недостаточного отвода теплоты трущихся поверхностей. Наиболее распространенной для подшипников качения редукторов общего назначения является мазь марки 1-13 (табл.13.1).
|
|
|
|
|
|
Таблица 13.1 |
|
Характеристика пластичных смазок, применяемых |
|||||
|
|
|
для механизмов общего назначения |
|||
|
|
|
|
|||
Наименование и марка |
ГОСТ |
Температура |
Водостойкость |
|||
смазки |
|
примен., 0С |
||||
Солидол |
|
синтетиче- |
|
|
|
|
ский общего назначе- |
4366−76 |
–20–+65 |
Хорошая |
|||
ния |
|
|
|
|
|
|
Мазь |
универсальная |
|
|
|
||
среднеплавкая |
УС |
|
|
|
||
(жировой солидол) ма- |
1033−73 |
|
Удовлетворительная |
|||
рок УС−1 |
и |
УС−2 |
|
|
|
|
(пресс-солидол) |
|
|
|
|
||
Смазка ЦИАТИМ−201 |
6267−73 |
–60–+90 |
Гигроскопична |
|||
Смазка ЦИАТИМ− 202 |
1170−75 |
–50–+120 |
Гигроскопична |
|||
Смазка ЦИАТИМ−203 |
|
|
|
|||
(с улучшенными про- |
|
|
|
|||
тивозадирными |
свой- |
|
|
|
||
ствами, |
эффективна в |
|
|
|
||
тяжелонагруженных |
8773−73 |
–50–+90 |
Хорошая |
|||
винтовых и червячных |
|
|
|
|||
передачах, а также в |
|
|
|
|||
подшипниковых |
опо- |
|
|
|
||
рах) |
|
|
|
|
|
|
Мазь |
универсальная |
|
|
|
||
тугоплавкая |
жировая |
1631−61 |
–60–+110 |
Хорошая |
||
1 − 13 |
|
|
|
|
|
|
Для защиты от загрязнений извне и предупреждения вытекания
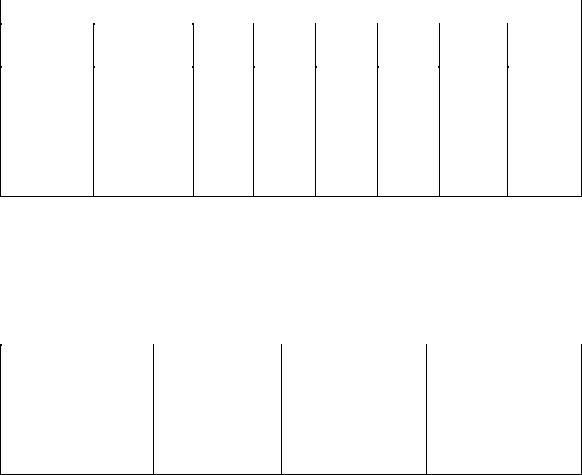
смазки подшипниковые узлы снабжают уплотняющими устройствами
(п. 12.5).
Для отделения узлов подшипника от общей системы смазки при их смазывании пластичными мазями (окружная скорость поверхности вала V< 2−3 м/с) применяют мазеудерживающие кольца (рис. 12.16). Выбор сорта масла начинают с определения необходимой кинематической вязкости масла: для зубчатых передач − в зависимости от окружной скорости (табл. 13.2), для червячных передач − от скорости скольжения (табл. 13.3). Затем по найденному значению вязкости выбирают соответствующее масло (табл. 13.4).
Таблица 13.2
Рекомендуемые значения кинематической вязкости масел для смазывания зубчатых передач, 10-6 м2/с
Материал |
|
|
Окружная скорость V,м2/с |
|
|||
зубчатых |
σв, МПа |
до |
0,5−1 |
1−2,5 |
2,5−5 |
5−12,5 |
12,5−25 |
колес |
|
0,5 |
|||||
|
|
|
|
|
|
||
Сталь |
< 1000 |
266 |
177 |
118 |
81,5 |
59 |
44 |
|
|
(20,5) |
(20,5) |
(11,4) |
− |
− |
− |
|
1000−1250 |
266 |
266 |
177 |
118 |
81,5 |
59 |
|
|
(32,4) |
(32,4) |
(20,5) |
(11,5) |
− |
− |
|
|
444 |
266 |
266 |
117 |
118 |
81,5 |
|
|
(52) |
(32,4) |
(32,4) |
(20,5) |
(11,4) |
− |
Примечание: числа без скобок обозначают кинематическую вязкость при 50ºС, в скобках − при 100ºС.
Таблица 13.3
Рекомендуемые значения кинематической вязкости масел для смазки червячных передач
Скорость сколь- |
Условия ра- |
Смазка |
Кинематическая |
|
жения V, м/с |
боты |
вязкость, м²/с |
||
|
||||
Менее 1 |
Тяжелые |
Окунанием |
444 (52,0) |
|
1 − 2,5 |
− // − |
− // − |
266 (32,4) |
|
Менее 5 |
Средние |
Струйная |
177 (20,5) |
|
5 − 10 |
− // − |
Окунанием |
118 (11,4) |
Примечание: числа без скобок означают кинематическую вязкость при 50ºС, а в скобках − при 100ºС.

Таблица 13.4
Кинематическая вязкость некоторых сортов масел, 10-6 м2/с
Наименование и марка |
|
При температуре |
Температура |
||
ГОСТ |
|
|
застывания, |
||
масла |
50ºС |
100ºС |
|||
|
ºС (не выше) |
||||
|
|
|
|
||
Индустриальное 20А |
20799 |
17−23 |
– |
–20 |
|
Индустриальное 30А |
20799 |
28−33 |
− |
–15 |
|
Индустриальное 40А |
20799 |
35−45 |
− |
–10 |
|
Индустриальное 50А |
20799 |
47−55 |
− |
–20 |
|
Индустриальное 70А |
20799 |
65−75 |
− |
− |
|
Турбинное 30 |
9972 |
28−32 |
− |
–10 |
|
Турбинное 57 |
9972 |
55−59 |
− |
− |
|
Авиационное МО−14 |
21743 |
≥92 |
≥14 |
–30 |
|
Авиационное МО−20 |
21743 |
≥157 |
≥20 |
–18 |
|
Авиационное МО−22 |
21743 |
≥192 |
>≥22 |
–14 |
|
Уровень масла, находящегося в корпусе редуктора, контроли- |
руют различными маслоуказателями (рис. 13.2 – 13.3). |
|
а) |
б) |
Рис. 13.2. Жезловые маслоуказатели:
а – маслоуказатель в корпусе; б – основные размеры
Наибольшее распространение имеют жезловые маслоуказатели,

так как они удобны для осмотра, конструкция их проста и достаточно надежна (рис. 13.2).
Круглые маслоуказатели (рис. 13.3) просты по конструкции и удобны для корпусов, расположенных достаточно высоко над уровнем пола. В них через нижнее отверстие масло проходит в полость маслоуказателя; через верхнее отверстие маслоуказатель сообщается с воздухом в корпусе редуктора.
Рис. 13.3. Круглый маслоуказатель
Таблица 13.5
Основные размеры пробок с цилиндрической резьбой, мм
d1 |
D |
D1 |
L |
l |
b |
S |
t |
d2 |
D2 |
b2 |
М16×1,5 |
25 |
21,9 |
24 |
13 |
3 |
19 |
1,9 |
16 |
38 |
3 |
М20×1,5 |
30 |
25,4 |
28 |
15 |
4 |
22 |
2,5 |
20 |
32 |
3 |
Для слива масла из корпуса редуктора предусматривается маслосливное отверстие, размещаемое в нижней части корпуса и закрываемое резьбовой пробкой. Разновидности и основные размеры пробок с цилиндрической резьбой и маслосливных отверстий приведены на рис. 13.4. Размеры пробок выбирают из табл. 13.5.Разновидности пробок с конической резьбой приведены на рис.13.5. Их размеры при-

ведены в табл. 13.6.
Рис. 13.4. Пробки с цилиндрической резьбой
Рис. 13.5. Пробки с конической резьбой
Таблица 13.6.
Размеры пробок с конической резьбой
d |
H |
h |
b |
D |
S |
S1 |
Ктруб 1/2˝ (21,0 мм) |
15 |
7 |
4 |
16,2 |
14 |
8 |
Ктруб 3/4˝ (26,4 мм) |
16 |
9 |
5 |
19,6 |
17 |
12 |
Ктруб 1˝ (33,2 мм) |
19 |
10 |
5 |
25,4 |
22 |
14 |
Ктруб 1/5˝ (47,8 мм) |
24 |
16 |
6 |
41,6 |
36 |
24 |
Во время работы редукторов повышается давление внутри корпуса в связи с нагревом масла и воздуха. Это приводит к выдавливанию масла из корпуса через уплотнения. Чтобы избежать этого, внут-

реннюю полость корпуса соединяют с внешней средой путем установки отдушин (обычно в крышке смотрового окна). Разновидности и размеры отдушин приведены на рис. 13.6–13.8 табл. 13.7.
Рис.13.6. Пробка-отдушина |
Рис.13.7. Ручка отдушина |
Рис.13.8. Колпачковая отдушина
Таблица 13.6
Основные размеры колпачковых отдушин, мм
А |
Б |
В |
Г |
Д |
Е |
Ж |
З |
И |
М27×2 |
15 |
30 |
15 |
45 |
36 |
32 |
6 |
4 |
М48×3 |
35 |
45 |
25 |
70 |
62 |
52 |
10 |
5 |
|
К |
Л |
М |
Н |
О |
П |
Р |
С |
М27×2 |
10 |
8 |
22 |
6 |
32 |
18 |
36 |
32 |
М48×3 |
15 |
13 |
52 |
10 |
56 |
36 |
52 |
55 |
14. НОРМИРОВАНИЕ ГЕОМЕТРИЧЕСКИХ ПАРАМЕТРОВ ДЕТАЛЕЙ
Одним из принципов конструирования и производства, независимо изготовленных деталей и узлов, обеспечивающих правильную сборку, работоспособность и замену их при ремонте без дополнительной обработки с соблюдением требований качества и экономичности является взаимозаменяемость.
Для обеспечения взаимозаменяемости деталей и узлов и упорядочения их производства должны выполняться определенные требования, предъявляемые к точности геометрических, механических и других параметров качества, устанавливаемых соответствующими стандартами.
Точность геометрических параметров оценивается точностью размеров, форм, взаимным расположением и шероховатостью поверхностей и должна быть соответствующим образом задана в технической документации (на чертежах).
14.1.Нормирование размеров деталей, некоторые сведения
одопусках и посадках и обозначение их на чертежах
Для изготовления деталей на чертежах необходимо проставить все ее номинальные размеры. Номинальный размер – это размер полученный в результате расчета на прочность, жесткость или принятый из конструктивных соображений, округленный до стандартного и поставленный на чертеже. Так как в реальных условиях абсолютно точно получить действительный размер невозможно (погрешность станка, приспособления, инструмента и т. д.) вводятся понятие предель-
ных размеров (dmax, Dmax, dmin, Dmin), между которыми должно находиться значение действительного размера годной детали. Действи-
тельный размер – это размер полученный в результате изготовления и замеренный с определенной точностью.
Принято обозначать dmax, dmin для вала Dmax, Dmin для отверстия. Для изготовления и контроля детали информация о предельных
(допускаемых) размерах должна быть известна из чертежа. Однако для упрощения чертежей на них обозначают не предельные размеры, а предельные отклонения размера от номинального значения (верхнее и нижнее), которые представляют собой алгебраическую разность

между соответствующим предельным размером и номинальным. Величины отклонений могут быть как положительными, так и
отрицательными. Разность между наибольшим и наименьшим предельными размерами или алгебраическая разность между верхним и нижним предельными отклонениями называется допуском размера.
Зона (область значений), ограниченная нижним и верхним предельными отклонениями или наименьшим и наибольшим предельными размерами, называется полем допуска (рис. 14.1).
Расположение полей допусков относительно номинального размера (нулевой линии) определяется одним из предельных отклонений, называемым основным, и обозначается одной (или двумя) буквами латинского алфавита – прописной для отверстий и строчной для валов (например, H, N, Ys, h, n, js и т.д.)
Основным всегда является предельное отклонение, ближайшее к номинальному размеру (нулевой линии). Его величина зависит от номинального размера и буквенного обозначения.
Рис. 14.1. Размерные параметры вала и отверстия, схемы полей допусков
Второе предельное отклонение (не основное) зависит от величины допуска.
При увеличении допуска на размер требования к точности снижаются, и деталь в изготовлении будет простой и дешевой. При одном и том же допуске деталь большего размера изготовить сложней, чем деталь меньшего размера. Поэтому величину допуска (IT) определяют по формуле
I T = a·i
где i – единица допуска, которая зависит от размера и определяется по формуле

l = 0,453d + 0,001d , мкм (здесь d мм)
а – число единиц допуска (коэффициент точности) и зависит от принятой точности изготовления.
Стандартом установлено 19 квалитетов точности: 01, 0, 1, 2, …17. При этом в среднем машиностроении квалитеты 5–11 используют для назначения допусков на сопрягаемые размеры деталей, а квалитеты 12–17 для несопрягаемых (свободных) размеров.
Числовые значения предельных отклонений и допуски размеров деталей определяются единой системой допусков и посадок (ЕСДП, установленной ГОСТ 25347 и ГОСТ 25346), и указываются на рабочих чертежах деталей для всех размеров.
Величины верхнего и нижнего предельных отклонений сопрягаемых размеров указывают на чертежах непосредственно после номинального размера одним из трех способов:
1) числовыми значениями предельных отклонений в миллиметрах (более мелкими цифрами: верхнее – вверху, нижнее – внизу; каждое со своим знаком; отклонение, равное нулю, не проставляется; если верхнее и нижнее отклонения равны по абсолютной величине, но имеют разные знаки, то они записываются один раз со знаком “+” цифрами одинаковой высоты с цифрами номинального размера), например
35−−0,0200,072 |
75++0,0760,030 |
100−+0,0060,048 |
|
20 |
−0,033 |
75(± 0,023) |
75+0,076 |
|
|
|
2)в виде условного обозначения поля допуска, состоящего из буквы и цифры, например 20h8; 35f9; 50Н7; 40К6.
3)одновременным указанием условного обозначения поля допуска и соответствующих ему цифровых значений предельных отклонений (в скобках), например
20h8(− 0,033) 35 f 9(+−00,,020072 )
Выбор способа простановки зависит от типа производства. Предельные отклонения размеров неуказанных на чертежах обо-
значаются в технических требованиях в виде записи:
«неуказанные предельные отклонения размеров: отверстий H14,
валов h14, остальных ± IT14 ». 2
В отдельных случаях в указанных вариантах записи допускается опускать поясняющие слова, например

H14, h14, ± IT14 . 2
В любом варианте записей для всех размеров ссылка должна быть на один квалитет точности.
Числовые значения стандартных допусков и предельных отклонений приведены в ГОСТ 25346 или технической литературе.
Отклонения угловых размеров указывают на изображениях непосредственно после их номинального значения, числовыми значениями в градусах, минутах, секундах, например 900±10´.Характер соединения двух деталей (охватываемой – вала и охватывающей – отверстия) называется посадкой. Если диаметр отверстия больше диаметра вала (поле допуска отверстия находится над полем допуска вала), то в соединении между ними образуется зазор (Smax и Smin), обеспечивающий свободное перемещение одной детали относительно другой (рис. 14.2, а). Если размер отверстия меньше размера вала (поле допуска вала находится над полем допуска отверстия), то в соединении образует-
ся натяг (Nmax и Nmin) (рис. 14.2, б). В том случае когда поля допусков перекрываются образуется переходная посадка (Smax = -
Smin) (рис. 14.2, в).
|
|
|
а) |
б) |
в) |
Рис. 14.2. Схемы полей допусков посадок с зазором (а), с натягом (б) и переходных (в).
Для того чтобы на сборочном чертеже указать характер двух сопрягаемых деталей (посадку), необходимо и достаточно после номинального размера сопрягаемых поверхностей обозначить их поля допусков. Обозначения выполняют в виде дроби: в числителе обозначают поле допуска отверстия, а в знаменателе – поле допуска вала одним из указанных выше способов, например
90 H 7 ; |
|
+0.035 |
; |
90 H 7 |
( |
+0.035 |
). |
90 |
|
|
|||||
|
+0.093 |
||||||
|
|||||||
s6 |
|
+0.093 |
|
s6 |
|
|
|
|
|
|
|
|
|
||
|
|
+0.071 |
|
|
|
+0.071 |
|