
по трэс
.pdf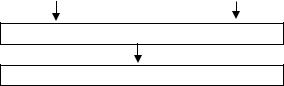

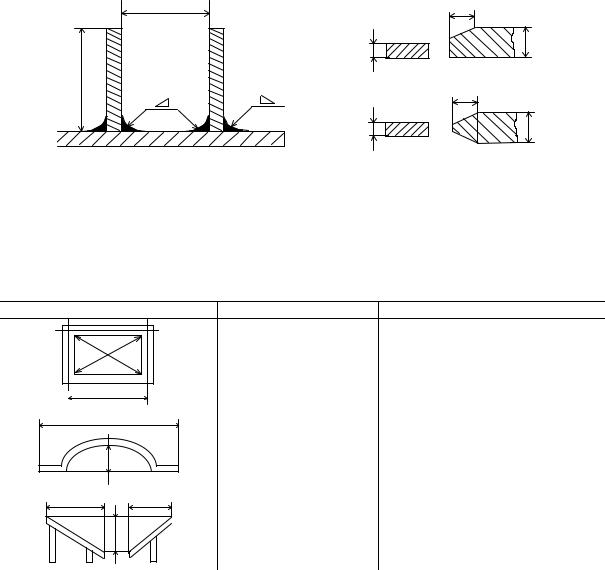
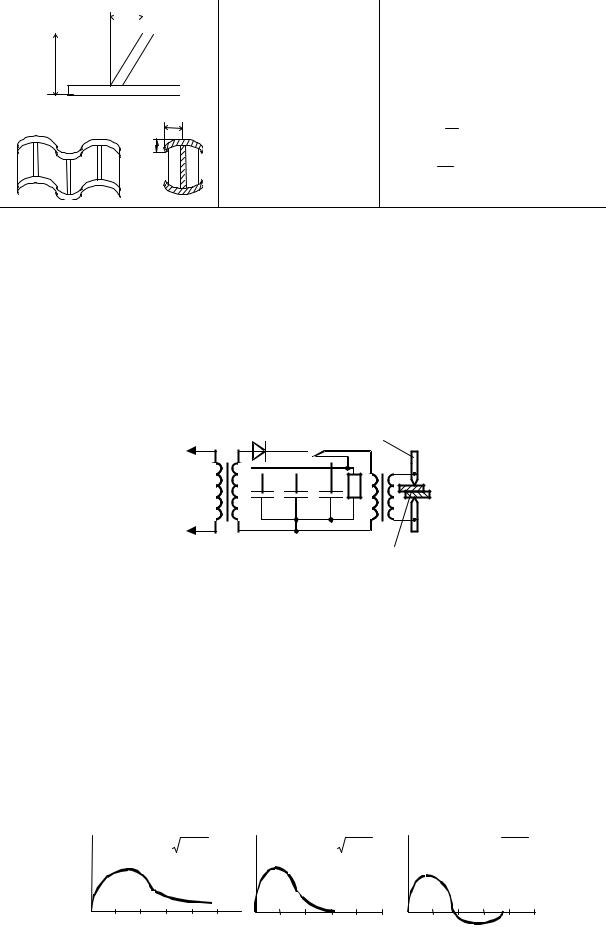
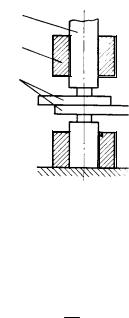
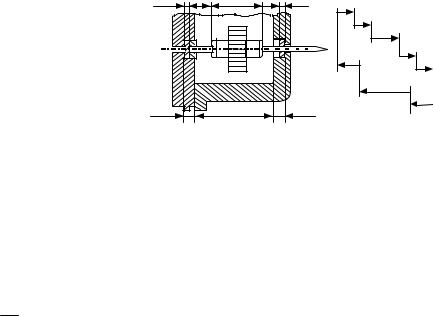

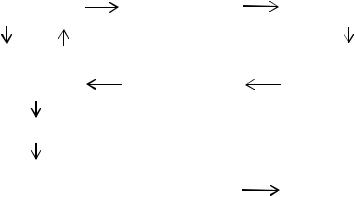
|
|
Подготовка навес- |
|
Установка навес- |
Входной кон- |
|
ных элементов к |
|
|
|
|
ных ЭРЭ на платы |
||
троль |
|
монтажу |
|
|
|
|
ОСТ4.ГО.054.265 |
||
|
|
ОСТ4.ГО.054.264 |
|
|
|
|
|
|
|
|
|
|
|
|
|
|
Установка и пайка |
|
|
Регулировка |
|
соединителей |
|
Пайка блоков |
|
ОСТ4.ГО.054.266- |
|
ОСТ4.ГО.054.267 |
|
|
|
|
||
|
|
267 |
|
|
|
|
|
|
|
Ремонт |
|
|
|
|
|
|
|
||
Контроль, стопорение резьбовых соедине- |
|
Влагозащита |
||
|
ний |
|
||
|
|
ОСТ4.ГО.054.205 |
||
ГОСТ 30133 – 95 |
|
|||
|
|
Рис. 9.1. Схема типового процесса сборки блоков на ПП
9.2.ВХОДНОЙ КОНТРОЛЬ И ЕГО ОПТИМИЗАЦИЯ
Впроизводстве ЭА применяют следующие виды контроля (ГОСТ 16504—70):
∙входной — дополнительная проверка элементов по параметрам, определяющим их работоспособность и надежность с целью исключения дефектных элементов вследствие ошибок поставщика, продолжительного хранения на складе, повреждений во время транспортирования и т. д.;
∙операционный — контроль продукции после завершения какой-либо операции;
∙приемочный — контроль готовой продукции после окончания всех технологических операций.
При входном контроле брак исправить легче, чем в готовом изделии, поэтому все комплектующие элементы подвергаются как визуальной, так и электрической проверке. При визуальной проверке обращают внимание на наличие на элементе отчетливо видимой надписи (тип, номинал, допуск, клеймо приемки ОТК), а также на отсутствие царапин, сколов, трещин, вмятин и коррозии. При электрической проверке проверяют соответствие электрических параметров элементов данным, указанным в ТУ или ГОСТах.
Входной контроль может быть сплошным (100 %) или выборочным. Объем выборки определяется по формуле
n = t P σ 2 / ε ;
где tР — коэффициент, зависящий от принятой вероятности Р и определяемый по табл. 9.1; σ — среднеквадра-
тичное отклонение; ε — заданная точность определения математического ожидания.
Табл. 9.1. Значения коэффициента tP
Р |
tР |
Р |
tР |
|
|
|
|
0,80 |
1,382 |
0,95 |
1,960 |
|
|
|
|
0,85 |
1,439 |
0,9973 |
3,000 |
|
|
|
|
0,90 |
1,643 |
0,999 |
4,200 |
|
|
|
|
226
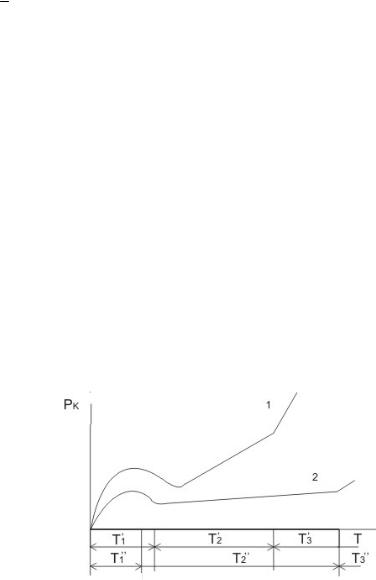