
по трэс
.pdf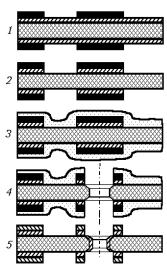
Технологический процесс включает следующие операции:
∙получение контура заготовки (штамповка, резка роликовыми ножницами);
∙подготовка поверхности заготовки;
∙нанесение негативного рисунка схемы, ретуширование;
∙травление металлической фольги с пробельных мест;
∙нанесение защитной пленки лака для защиты всей поверхности платы от химического меднения краско-
распылителем и подсушивание при температуре 50—60 °С (цапонлак, бакелитовый лак, клей АК-20);
∙сверление отверстий;
∙химическое меднение;
∙снятие защитного слоя лака;
∙гальваническое меднение отверстий;
∙снятие фоторезиста;
∙покрытие проводников припоем ПОСВ 33 для обеспечения их паяемости.
К преимуществам метода относятся освоенность процесса производства и широкая номенклатура травителей. Недостатки — возможность срыва контактных площадок при сверлении, необходимость специальных контактирующих приспособлений при металлизации отверстий, вредное воздействие химических растворов на платы, большая величина подтравливания.
Рис. 5.18. Схема процесса изготовления ДПП комбинированным негативным методом: 1 – нанесение защитного рельефа; 2 – травление меди; 3 – нанесение лака;
4 – сверление и зенкование отверстий; 5 – металлизация отверстий
При комбинированном позитивном методе выполняются следующие операции (рис. 5.19):
∙получение контура заготовки и подготовка ее поверхности;
∙нанесение позитивного рисунка схемы;
∙нанесение защитного слоя лака (нитроклей АК-20, эмаль ХСЭ, ХСЛ и др.) для предохранения от воздей-
ствия химически активных растворов при химической металлизации (количество слоев 2—3, нанесение окунанием, поливом или с помощью краскораспылителей, сушка в сушильных печах в течение 20—40 мин при температуре 60—80 С);
∙ сверление отверстий в плате;
118

∙ |
химическое меднение отверстий слоем толщиной 1—2 мкм со скоростью 20—30 мкм/ч; |
∙ |
гальваническое меднение толщиной 25—30 мкм; |
∙удаление защитного слоя лака;
∙нанесение металлического резиста для защиты проводников и отверстий от травления (серебрение тол-
щиной 10—12 мкм, гальваническое покрытие сплавами Sn—Pb, Sn—Bi, |
ПОСВ33 толщиной 20—25 мкм); |
∙удаление фоторезиста;
∙травление пробельных мест;
∙оплавление металлического резиста (необходимо для удаления припоя из отверстий и улучшения паяемости покрытия);
∙контроль платы, маркировка.
Гальванически нанесенный металлический резист из сплава Sn—Pb имеет пористую структуру, быстро окисляется, теряет способность к пайке. Для устранения этих недостатков проводят оплавление резиста либо с помощью ИК-излучения, либо в нагретой жидкости (глицерине) или газе. В результате покрытие приобретает структуру металлургического сплава и хорошую паяемость.
Рис. 5.19. Схема процесса изготовления ДПП комбинированным позитивным методом:
1 – нанесение защитного рельефа; 2 – нанесение лака; 3 – сверление и металлизация отверстий; 4 – нанесение металлического резиста; 5 – травление и оплавление резиста
В связи с повышением требований к качеству плат используют аддитивные методы, которые устраняют такие недостатки субтрактивных, как подтравливание проводников, неравномерная толщина металлизации отверстий, большой расход медной фольги и травильных растворов.
При аддитивном методе изготовления ДПП используют нефольгированный диэлектрик с введенным в него катализатором Pd:Sn = 1:3. Технологический процесс включает следующие операции (рис. 5.20):
∙подготовка поверхности диэлектрика (очистка);
∙нанесение адгезива путем погружения платы в композицию на основе нитрильного каучука толщиной
20—30 |
мкм либо полимера АБС-2 и вытягивания из раствора полимера со скоростью 20—100 мм/мин с после- |
дующей сушкой при температуре 130—140 °С в течение 1,5—2 ч; |
|
∙ |
сверление и очистка отверстий в плате; |
119
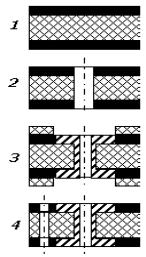
∙нанесение защитного негативного рисунка схемы, обладающего повышенной стойкостью к высокощелочному составу ванны химического меднения;
∙подтравливание поверхностей диэлектрика, открытых для нанесения меди, в растворе фторборатной или хромовой кислоты для улучшения адгезии проводников к подложке;
∙ химическое меднение в течение 8—16 ч;
∙удаление защитного резиста;
∙создание неметаллизированных отверстий;
∙нанесение маски для пайки трафаретной печатью;
∙лужение проводников и металлизированных отверстий в плате.
Процесс нанесения толстослойной (25—35 мкм) химической меди требует специального оборудования, оснащенного системами дозирования добавок в ванну, непрерывной фильтрации раствора. Во время меднения выделяется водород, поэтому необходимо непрерывное покачивание плат со скоростью 5—10 качаний в минуту при длине хода до 50—100 мм, а также применение ЭВМ для автоматического поддержания концентрации растворов, pH, температуры и уровня раствора в ваннах.
Рис. 5.20. Схема процесса изготовления ДПП аддитивным методом: 1 – нанесение адгезива; 2 – сверление отверстий; 3 – химическое меднение;
4 – сверление металлизированных отверстий
Применение аддитивного метода ограничено его невысокой производительностью, трудностью получения хорошей адгезии проводников с основой, интенсивным воздействием растворов на диэлектрик.
При полуаддитивном методе изготовления ДПП используется нефольгированный диэлектрик без введенного катализатора, поэтому обязательными являются операции сенсибилизации и активации. Процесс включает следующие операции (рис. 5.21):
∙подготовка поверхности диэлектрика и нанесение адгезива;
∙сверление и очистка отверстий;
∙сенсибилизация и активация всей поверхности;
∙ химическое меднение слоем толщиной 2—3 мкм для трафаретной печати и 4—6 мкм для фотопечати;
∙создание защитного рисунка схемы;
∙гальваническое меднение (усиление меди);
∙удаление резиста и травление;
∙создание неметаллизированных отверстий;
120
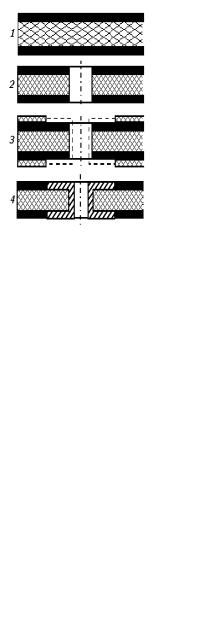
∙ нанесение маски для пайки и лужение печатных проводников.
В настоящее время химическое меднение ведут на периодических токах: импульсных, реверсных и произвольной формы, что улучшает микрорельеф покрытий, снижает внутренние напряжения и сокращает время осаждения.
При изготовлении ДПП методом травления фольгированного диэлектрика требуется до 40 операций с использованием драгоценных металлов (хлористого палладия) и токсичных травящих растворов. Ширина проводников и расстояние между ними — около 0,2—0,3 мм, причем уменьшение размеров снижает прочность сцепления с подложкой. Разработана технология рельефных ПП, свободная от перечисленных выше недостатков. Подложка платы изготавливается путем литья или прямого прессования из реактопласта типа ДСВ2-Р-2Н, при этом формируются переходные отверстия, конструктивные элементы, а также углубления для проводников (рис. 5.22). Матрицу для пресс-формы получают путем глубокого химического травления. Для создания платы больших размеров и малой толщины необходима терморихтовка. Затем поверхности придается шероховатость с одновременным удалением облоя и притуплением острых кромок отверстий.
Рис. 5.21. Схема процесса изготовления печатных плат полуаддитивным методом:
1 – нанесение адгезива; 2 – сверление отверстий; 3 – подготовка поверхности и нанесение защитного рельефа; 4 – гавальническая металлизация
На установке магнетронного распыления на обе стороны подложки наносится медный слой с соответствующим подслоем, покрывающий внутренние поверхности отверстия. Далее слой наращивается гальванически до 25 мкм. Затем подложка шлифуется на глубину, превышающую толщину нанесенного слоя. Несошлифованная медь в рельефе и образует рисунок проводников, которые облуживаются сплавом олово— свинец.
а
б
в
Рис. 5.22. Схема технологического процесса получения рельефных плат: а – штамповка; б – напыление; в – шлифование
121
Преимущества метода: минимальная ширина проводников 0—1 мм; прочность сцепления с подложкой в 2 раза выше по сравнению с аддитивным методом; сокращение производственных площадей в 3 раза; улучшение условий труда, уменьшение загрязнения окружающей среды. Недостаток — сложность внесения изменений в рисунок платы.
5.9. ТЕХНОЛОГИЯ МНОГОСЛОЙНЫХ ПЕЧАТНЫХ ПЛАТ
Развитие современной радиоэлектроники характеризуется широким применением микросхем различной сложности (ИМС, БИС и СБИС) в качестве основных компонентов ЭА. Сложность и большая функциональная плотность современной аппаратуры потребовала огромного числа коммутационных соединений, которые возможно осуществить, только используя многослойный печатный монтаж.
С 60-х гг. для всей электроники характерно обращение к цифровой обработке сигналов. Как следствие прогресса в этой области, постоянно растет скорость обработки электрических сигналов в единицу времени и плотность компоновки элементов в единице объема. Это предъявляет в качестве основных требования к системе монтажа максимальные помехозащищенность и плотность проводников.
Проблема помехозащищенности давно являлась наиболее важной в технике передачи информации. Собственные помехи системы обусловлены взаимным воздействием внутренних проводников путем емкостной и (или) индуктивной связи. Внешние помехи возникают за счет электромагнитного воздействия системы электропитания, цепей ввода и вывода сигналов. Использование МПП позволяет в 10 раз уменьшить электромагнитные помехи за счет печатных экранов.
Многослойная печатная плата состоит из ряда склеенных печатных слоев, в которых находятся сигнальные проводники, переходные отверстия, экраны, шины питания, контактные площадки или выступы для присоединения выводов элементов. Сохраняя все достоинства печатного монтажа, МПП имеют дополнительные преимущества:
∙более высокая удельная плотность печатных проводников и контактных площадок (20 и более слоев);
∙уменьшение длины проводников, что обеспечивает значительное повышение быстродействия (например, скорость обработки данных в ЭВМ);
∙возможность экранирования цепей переменного тока;
∙более высокая стабильность параметров печатных проводников под воздействием внешних условий. Недостатки МПП:
∙более жесткие допуски на размеры по сравнению с ОПП и ДПП;
∙большая трудоемкость проектирования и изготовления;
∙применение специального технологического оборудования;
∙тщательный контроль всех операций;
∙высокая стоимость и низкая ремонтопригодность.
Внастоящее время МПП нашли применение для изготовления панелей ЭВМ, объединяющих конструктивно ИМС, ЭРЭ и коммутационные элементы, а также в космической и авиационной аппаратуре. Основные способы получения МПП классифицируют по методу создания электрических межслойных соединений (рис. 5.23).
Впервой группе методов электрическая связь между проводниками, расположенными на различных слоях платы, осуществляется с помощью механических деталей: штифтов, заклепок, пистонов, упругих лепестков.
МПП изготавливается из нескольких ДПП путем прессования, в отверстия вставляются предварительно облу-
122

женные штифты, которые затем под действием электрического тока, проходящего через штифт, разогреваются, образуя с помощью припоя электрическое соединение с печатными проводниками (рис. 5.24, а). В отверстия могут вставляться также заклепки, пистоны, которые облуживаются по торцам и развальцовываются (рис. 5.24, б). Соединения могут осуществляться по соприкасающимся фланцам пистонов, а также путем соединения предварительно отбортованных контактных площадок пистоном, что уменьшает размеры пакета (рис. 5.24, в). Эти методы весьма трудоемки, плохо поддаются автоматизации и не обеспечивают высокого качества межслойных соединений.
Метод выступающих выводов характеризуется тем, что при его осуществлении межслойные соединения образуются за счет выводов, выполненных из полосок медной фольги, выступающих с каждого печатного слоя и проходящих через перфорированные отверстия в диэлектрических межслойных прокладках. Выводы отгибаются на наружную сторону МПП и закрепляются пайкой в специальных колодках. Метод включает следующие операции (рис. 5.25):
Способы изготовления МПП
|
|
|
|
|
|
|
|
|
|
|
|
|
|
|
|
|
|
|
|
|
|
|
|
|
|
|
|
|
|
|
|
|
|
Механичес- |
|
|
Печатными |
|
Химико- |
|
|
Выводами |
||||||||
кими |
|
|
|
гавальнической |
|
|
||||||||||
|
|
проводниками |
|
|
|
ЭРЭ |
||||||||||
деталями |
|
|
|
металлизацией |
|
|
||||||||||
|
|
|
|
|
|
|
|
|
|
|
|
|||||
|
|
|
|
|
|
|
|
|
|
|
|
|
|
|||
|
|
|
|
Выступающими |
|
Металлизацией |
|
|
Открытых |
|||||||
Штифтами |
|
|
|
сквозных |
|
|
контактных |
|||||||||
|
|
|
|
|
||||||||||||
|
|
выводами |
|
|
|
|||||||||||
|
|
|
|
|
отверстий |
|
|
площадок |
||||||||
|
|
|
|
|
|
|
|
|
|
|
||||||
|
|
|
|
|
|
|
|
|
|
|
|
|
|
|
||
Пистонами |
|
|
|
|
|
|
|
Попарного |
|
|
|
|
|
|||
|
|
|
|
|
|
|
пресования |
|
|
|
|
|
||||
|
|
|
|
|
|
|
|
|
|
|
|
|
|
|||
|
|
|
|
|
|
|
|
|
|
|
|
|
|
|
|
|
Отгибкой |
|
|
|
|
|
|
|
Послойного |
|
|
|
|
|
|||
боковых |
|
|
|
|
|
|
|
|
|
|
|
|
||||
|
|
|
|
|
|
|
наращивания |
|
|
|
|
|
||||
лепестков |
|
|
|
|
|
|
|
|
|
|
|
|||||
|
|
|
|
|
|
|
|
|
|
|
|
|
|
|
||
|
|
|
|
Рис.5.23. Основные способы получения МПП |
|
|
|
Рис. 5.24. Соединения с помощью штифта (а), пистонов, соприкасающихся по фланцам (б) и предварительно отбортованных контактных площадок (в)
Рис. 5.25. Стадии формирования МПП методом выступающих выводов:
1 – нарезка заготовок; 2 – перфорирование диэлектрика; 3 – нанесение рисунка на слой; 4 – травление меди; 5 – прессование пакета
123
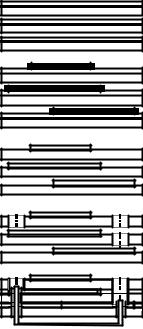
∙изготовление заготовок из стеклоткани и медной фольги (нарезка в размер);
∙перфорирование стеклоткани;
∙склеивание заготовок перфорированного диэлектрика с медной фольгой;
∙получение защитного рисунка схемы отдельных слоев;
∙травление меди с пробельных мест;
∙прессование пакета МПП;
∙отгибка выводов на колодки и закрепление их;
∙облуживание поверхности выводов, механическая обработка платы по контуру;
∙контроль, маркировка.
При данном методе используется более толстая медная фольга (до 80 мкм), платы допускают установку только ИМС с планарными выводами. Количество слоев не превышает 20. Преимущества метода — высокая жесткость и надежность межслойных соединений, недостатки — сложность механизации процесса разводки выступающих выводов и их закрепления на плате, а также установки навесных элементов.
Метод открытых контактных площадок основан на создании электрических межслойных соединений с помощью выводов навесных элементов или перемычек через технологические отверстия, обеспечивающие доступ к контактным площадкам, и включает следующие операции (рис. 5.26):
∙получение заготовок фольгированного материала;
∙нанесение защитного рисунка схемы на каждый слой;
∙травление меди с пробельных мест и удаление резиста;
∙пробивка отверстий в слоях;
∙прессование пакета МПП;
∙облуживание контактных площадок, выполнение электрических соединений.
1
2
3
4
5 |
Рис. 5.26. Стадии формирования МПП методом открытых контактных площадок:
1 – получение заготовок; 2 – нанесение защитного рельефа на слой; 3 – травление меди; 4 – пробивка отверстий; 5 – прессование пакета и выполнение соединений
124

В слоях вырубаются отверстия: для штыревых выводов круглые, для планарных прямоугольные. Для увеличения площади контакта диаметр площадок делают больше диаметра отверстий. МПП являются ремонтопригодными, так как допускается перепайка выводов ЭРЭ. Количество слоев — до 12.
Недостатки метода: возможность попадания клея на контактные площадки при склеивании слоев и трудоемкость его удаления скальпелем; трудность автоматизации процесса пайки выводов в углублениях; отсутствие электрической связи между слоями; низкая плотность монтажных соединений.
Метод металлизации сквозных отверстий характеризуется тем, что собирают пакет из отдельных слоев фольгированного диэлектрика (внешних — одностороннего, внутренних — с готовыми печатными схемами) и межслойных склеивающихся прокладок, пакет прессуют, а межслойные соединения выполняют путем металлизации сквозных отверстий. Технологический процесс включает следующие операции (рис. 5.27):
∙получение заготовок фольгированного диэлектрика и межслойных склеивающихся прокладок;
∙получение рисунка печатной схемы внутренних слоев фотохимическим способом аналогично ДПП;
∙ пресование пакета МПП при температуре 160—180 °С и давлении 2—5 МПа;
∙сверление отверстий в пакете;
∙получение защитного рисунка схемы наружных слоев фотоспособом;
∙нанесение слоя лака;
∙подтравливание диэлектрика в отверстиях в смеси серной и плавиковой кислот в соотношении 4:1 при температуре (60±5) °С в течение 10—30 с. При этом растворяется смола стеклопластиков и стеклоткань склеивающих прокладок устранения следов наволакивания смолы, обнажения контактных площадок и увеличения площади контактирования;
1
2
3
4
5
Рис. 5.27. Стадии формирования МПП методом металлизации сквозных отверстий:
1 – получение заготовок; 2 – нанесение рисунка на внутренних слоях; 3 – прессование пакета; 4 – сверление отверстий; 5 – подтравливание диэлектрика
∙ химическое меднение сквозных отверстий;
125
∙ |
удаление слоя лака; |
∙ |
гальваническое меднение отверстий и контактных площадок до толщины 25—30 мкм в отверстиях; |
∙нанесение металлического резиста гальваническим путем (сплавы Sn—Pb, Sn—Ni);
∙удаление защитного слоя рисунка и травление меди с пробельных мест;
∙осветление (оплавление) металлического резиста;
∙механическая обработка МПП (снятие технологического припуска);
∙контроль и маркировка.
Качество МПП, изготовленных методом металлизации сквозных отверстий, в значительной мере зависит от надежности межслойных соединений — торцов контактных площадок с металлизированными отверстиями. Надежное соединение образуется при удалении со стенок отверстий пленки эпоксидной смолы, наволакиваемой при сверлении. Наиболее распространенный способ очистки отверстий перед металлизацией — химическое подтравливание диэлектрика стенок отверстий. Для этого используются растворы кислот или их смеси, однако смеси кислот склонны проявлять продукты травления в порах диэлектрика. За рубежом наибольшее распространение получил способ травления диэлектрика не в смеси кислот, а сначала в серной, а затем в плави-
ковой. При повышении температуры раствора с 30 до 60 °С глубина подтравливания диэлектрика увеличивается от 2—5 до 40—50 мкм, а при увеличении времени воздействия травящего раствора с 1 до 5 мин глубина подтравливания растет от 25—50 до 100—120 мкм.
В связи с тем, что для подтравливания используются агрессивные растворы (смесь горячих концентрированных кислот), требующие постоянного контроля и последующей нейтрализации обработанных заготовок, был предложен способ сухого плазменного травления. Он обеспечивает хорошую адгезию меди в отверстиях, короткий цикл обработки и отсутствие побочных эффектов. В качестве реагента используется низкотемпера-
турная плазма из смеси газов, например кислорода и фреона при температуре 50—350 °С и давлении 0,13—260 ГПа. Плазма содержит свободные радикалы (до 90) и ионы (1 %). Рекомендуется перед травлением предвари-
тельный подогрев плат до 50—70 °С. Плазма превращает эпоксидную смолу в летучее вещество, легко удаляемое из отверстий. Никаких промывок и сушки при плазменном методе не требуется. Этот процесс сухой и полностью автоматизирован. При обработке каждая МПП помещается в пространство между двумя параллельно расположенными алюминиевыми пластинами— электродами. Электроды имеют отверстия, совпадающие с отверстиями в МПП.
Метод металлизации сквозных отверстий является основным и наиболее перспективным в производстве МПП, так как не имеет ограничения количества слоев, легко поддается автоматизации и обеспечивает наибольшую плотность печатного монтажа. Он позволяет изготавливать МПП, пригодные для размещения на них элементов с планарными и штыревыми выводами. Более 80 % всех МПП, производимых в мире, изготавливается этим методом.
Метод попарного прессования характеризуется тем, что внутренние слои МПП изготавливаются на одной стороне заготовки из двустороннего фольгированного диэлектрика, межслойные соединения — путем химикогальванической металлизации отверстий в заготовках, полученные слои прессуются, а рисунок на наружных сторонах платы выполняется комбинированным позитивным методом.
В конструкции МПП нет прямой электрической связи между внутренними слоями многослойной структуры, она осуществляется через внешние слои. Сложность переходов не дает возможности получить высокую плотность печатного монтажа. Число слоев МПП — не более четырех. Технологический процесс включает следующие операции (рис. 5.28):
126
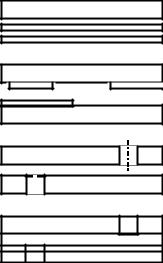
∙получение заготовок;
∙нанесение защитного рисунка схемы внутренних слоев;
∙травление меди с пробельных мест и удаление защитного рисунка;
∙выполнение межслойных электрических соединений между внутренними и наружными слоями химикогальванической металлизацией;
∙прессование пакета МПП (металлизированные отверстия переходов заполняются смолой во избежание их разрушения при травлении);
∙сверление отверстий и нанесение защитного рисунка схемы наружных слоев;
∙химическое меднение сквозных отверстий;
∙гальваническое меднение и нанесение металлического резиста;
∙травление меди на наружных слоях;
∙осветление металлического резиста;
∙механическая обработка;
∙контроль, маркировка.
∙ 1
∙
∙
2
∙
∙
3∙
∙
∙
4 |
∙ |
|
∙ |
|
∙ |
|
∙ |
5∙
∙
∙
∙
∙
Рис. 5.28. Стадии формирования МПП методом попарного прессования: 1 – получение заготовок; 2 – получение рисунка на внутренних слоях; 3 – выполнение межслойных переходов; 4– прессование пакета
Попарным прессованием изготавливаются МПП, на которых размещаются навесные элементы с планарными и штыревыми выводами. Недостатки метода — низкая производительность, невозможность получения большого числа слоев и высокой плотности печатного монтажа.
Метод послойного наращивания характеризуется тем, что при его осуществлении межслойные соединения выполняют сплошными медными переходами (столбиками меди), расположенными в местах контактных площадок. Технологический процесс включает следующие операции (рис. 5.29):
∙получение заготовок стеклоткани и фольги;
∙перфорирование диэлектрика;
∙наклеивание перфорированной заготовки диэлектрика на фольгу;
∙гальваническая металлизация отверстия и химико-гальваническая металлизация второй наружной поверхности заготовки;
127