
по трэс
.pdf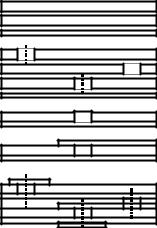
∙нанесение защитного рисунка схемы и травление меди;
∙гальваническое наращивание меди в отверстиях и химико-гальваническая металлизация наружной поверхности диэлектрика;
∙травление меди с пробельных мест;
∙получение многослойной структуры путем многократного повторения операций химико-гальванической металлизации и травления;
∙напрессовывание диэлектрика;
∙получение защитного рисунка печатного монтажа наружного слоя;
∙травление меди с пробельных мест и облуживание припоем;
∙механическая обработка;
∙контроль и маркировка.
1
2
3
4
5
Рис. 5.29. Стадии формирования МПП методом послойного наращивания
Послойным наращиванием получают МПП, на которых размещают только навесные элементы с планарными выводами. Недостатком данного метода является нетехнологичность конструкции, так как нельзя использовать фольгированные диэлектрики и необходимо вести последовательный цикл изготовления многослойной структуры. Стоимость изготовления МПП высокая. Достоинства метода — возможность получения большого числа слоев (5 и более) и самые надежные межслойные контактные соединения. Результаты качественного сравнения МПП, изготовленных различными методами, приведены в табл. 5.8.
К базовым технологическим процессам получения МПП относятся прессование пакета, механическая обработка и контроль. Прессование пакета МПП является одним из самых важных процессов изготовления МПП, так как от качества его выполнения зависят электрические и механические характеристики готовой МПП. Технологический процесс прессования состоит из следующих операций: подготовка поверхности слоев перед прессованием; совмещение отдельных слоев МПП по базовым отверстиям и сборка пакета; прессование пакета.
Табл. 5.8. Сравнительная характеристика методов при изготовлении МПП
|
|
|
Метод изготовления |
|
|
||
|
|
|
|
|
|
|
|
Показатель |
механическими |
попарным |
открытых кон- |
выступающих |
послойного |
металлизаци- |
|
деталями |
прессованием |
тактных пло- |
выводов |
наращивания |
ей сквозных |
||
|
|||||||
|
|
|
щадок |
|
|
отверстий |
|
|
|
|
|
|
|
|
|
Количество слоев |
6 |
4 |
12 |
5 |
15 |
20 |
|
Плотность печатного монтажа |
Н |
С |
Н |
С |
С |
В |
|
|
|
|
|
|
|
|
128
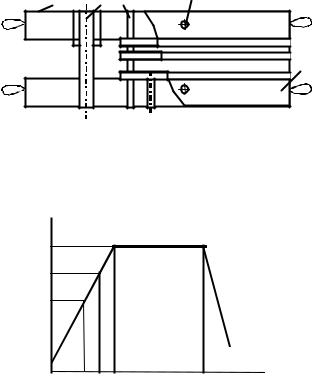
Надежность межслойных соединений |
|
Н |
С |
В |
В |
В |
С |
Стойкость к внешним воздействиям |
|
С |
С |
С |
В |
В |
С |
Ремонтопригодность |
|
Н |
Н |
В |
С |
С |
Н |
Технологическая себестоимость |
|
В |
С |
С |
В |
В |
С |
|
|
|
|
|
|
|
|
Примечание. Н — низкая; С — средняя; В — |
высокая. |
|
|
|
|
|
Для подготовки поверхности слоев к прессованию применяют механическую зачистку абразивами, обезжиривание поверхности органическими растворителями и легкое декапирование фольги. При прессовании экранов с большими участками фольги ее поверхность оксидируют для лучшей адгезии при склеивании. Текстура наполнителя (прокладок из стеклоткани) должна быть равномерно пропитана смолой, иначе при травлении химические растворы проникают в свободные полости и снижают тем самым сопротивление изоляции.
Совмещение отдельных слоев МПП по базовым отверстиям осуществляют в специальном приспособлении (рис. 5.30), состоящем из верхней 1 и нижней плит 5, изготовленных из стали. Толщина плит составляет 15—20 мм и зависит от габаритов изготавливаемой платы. Плиты шлифуют по обеим плоскостям, направляющие колонки 2 обеспечивают их полную параллельность. В торцах плит выполняют отверстия для термопар 4. Габаритные размеры нижней плиты должны быть больше прокладочных листов на 30—50 мм с каждой стороны по периметру, так как. при прессовании возможно вытекание значительного количества смолы. Фиксирующие штыри 3 располагают через 100—150 мм по периметру платы в пределах технологического поля.
1 |
2 |
3 |
4 |
|
|
|
5 |
Рис. 5.30. Приспособление для прессования пакета МПП: 1 – верхняя плита; 2 – отверстие для термопары; 3 – фиксирующий палец; 4 – направляющая колонка; 5 – нижняя плита
T,°C |
|
|
|
|
|
170 |
|
|
|
|
|
120 |
|
|
|
|
|
40 |
1 |
2 |
3 |
4 |
5 |
t
Рис. .5.31. Режим прессования пакета МПП:
1 – жидкость; 2 – гель; 3 – полимеризованная смола; 4 – давление; 5 – охлаждение
Для прессования МПП используют специализированные многоярусные гидравлические прессы, обору-
дованные системами нагрева, охлаждения плит и поддержания температуры с точностью ±3 °С, регуляторами подачи давления с точностью порядка 3 %. Нагрев плит пресса осуществляют либо перегретым паром, либо
129
электричеством. Для ускоренного охлаждения в плиты встраивают коллекторы для подачи проточной водопроводной воды.
На качество прессования существенно влияет текучесть смолы и время ее полимеризации. Основным фактором в процессе прессования является правильно выбранный момент приложения максимального давления. Если создать давление до начала полимеризации смолы, то значительное ее количество будет выдавлено, а если после полимеризации, то получается плохая проклейка слоев, что приводит к расслоению. При большой скорости возрастания температуры основные реакции отверждения проходят быстро, продукт получается хрупким, неоднородным, со значительными внутренними напряжениями. С уменьшением скорости нагрева механические свойства диэлектрика улучшаются.
Сборку пакета МПП осуществляют в режимах "холодного" и "горячего" прессования. При первом режиме пресс-форму с МПП помещают между холодными плитами пресса, в котором происходит ее последующий на-
грев до необходимой температуры со скоростью 15 °С/мин. На первой стадии прессования создают незначи-
тельное давление на пакет (0,15—0,2 МПа), а когда смола загустевает при температуре 130—140 °С, давление поднимают до 5—8 МПа. Окончательное отверждение продолжается в течение 40 мин, затем плиты пресса быстро охлаждают водой и, когда температура в пакете снизится до 40 С, пресс раскрывают и извлекают готовый пакет (рис. 5.31). При "горячем" прессовании плиты нагревают до 160—170 °С, это ускоряет процесс прессова-
ния, дальнейший нагрев ведут со скоростью 15—50 °С/мин.
Для снятия напряжений, возникающих в пакете в процессе прессования и вызывающих затем коробление платы, после обрезки облоя МПП подвергают дополнительной тепловой обработке. Для этого ее наглухо зажимают между двумя жесткими пластинами и помещают на 30—40 мин в термошкаф при температуре 120—130
°С, затем оставляют в печи до медленного остывания.
Установленные режимы прессования требуют постоянной корректировки в зависимости от изменения технологических свойств склеивающихся прокладок стеклоткани. Поэтому стеклоткань периодически проверяют на содержание связующей смолы, ее текучести, времени полимеризации. Для более точного контроля времени приложения максимального давления при прессовании пакета измеряют электрическое сопротивление связующей смолы с помощью датчика, представляющего собой электроды в форме гребенки, полученной на фольгированном диэлектрике. Электрическое сопротивление падает с 105 МОм до 1 МОм в момент полного расплавления смолы, а затем растет в процессе ее полимеризации.
Для прессования МПП применяют специализированные многоярусные гидравлические прессы, оборудованные системами нагрева и охлаждения плит, устройствами для регулирования технологических режимов. Прессы обеспечивают плоскостность и параллельность плит в пределах 0,1 мм, время нагрева плит до рабочей температуры 20 мин, точность поддержания температуры на их плоскости ±3 °С, давления ± 3 %. Повышение производительности прессования достигается на автоматических линиях (например, модель S75 MRT -372C-X- X-G фирмы Pasadena Hydraulies, США), в которых по заданной программе пресс-формы с обрабатываемыми пакетами МПП пневматическим автооператором перемещаются из позиции загрузки в нагретые плиты гидравлического пресса. Плиты сжимают пакеты в пресс-формах при низком давлении в течение заданного времени, а затем автоматически переключаются на высокое давление. В позицию загрузки устанавливается следующая партия пресс-форм. После выдержки заданного таймером времени полимеризации связующей смолы в пакетах МПП горячие и холодные плиты размыкаются, а автооператор перемещает прошедшие стадию полимеризации пакеты из горячих плит пресса в холодные для их остывания при заданном давлении. Одновременно на позицию прессования подается следующая пресс-форма из позиции загрузки, после чего плиты зажимаются и цикл повторяется.
130
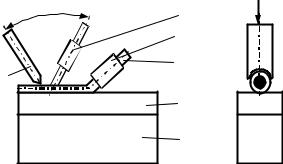
5.10. ТЕХНОЛОГИЯ ПРОВОДНЫХ ПЛАТ
Применение МПП экономически оправдано лишь в серийном и крупносерийном производстве ЭА. В мелкосерийном производстве на этапе разработки опытных образцов применяются другие методы, основанные на оптимальном сочетании печатного и объемного монтажа. Характерными особенностями таких комбинированных методов являются использование ДПП, имеющих шины земли и питания, контактные площадки под навесные ЭРЭ и ИМС, металлизированные переходные и монтажные отверстия. Монтаж остальных электрических цепей осуществляют путем раскладки проводов на одной из плоскостей платы и создания контактных соединений с элементами ДПП путем сварки или пайки.
Таким образом, имея стандартную конструкцию ДПП, изготовленную комбинированным позитивным методом, с помощью проводного монтажа получают конструкцию, аналогичную 8- или 9-слойной МПП. При этом отпадает необходимость изготовления большого числа фотошаблонов, применения прессования и других операций, характерных для МПП, что значительно сокращает цикл изготовления конструкции.
К комбинированным методам монтажа относятся: многопроводной упорядоченный фиксируемыми проводами, многопроводной неупорядоченный, стежковый неупорядоченный.
Многопроводной монтаж фиксируемыми проводами заключается в упорядоченном прокладывании изолированных проводов на поверхности ДПП, закреплении их в слое адгезива и соединении с печатным монтажом с помощью металлизированных монтажных отверстий. Метод разработан фирмой Kollmorgen Corporation (США) и называется Multiwire. Материалом для изготовления многопроводных плат служит фольгированный диэлектрик, на поверхности которого субтрактивным методом получают печатный монтаж. На обезжиренные поверхности плат наносят адгезионный слой, состоящий из прокладочной стеклоткани СПТ-3-0.025 и клея ВК-32-200. Для монтажа применяют провод диаметром 0,1—0,2 мм в высокопрочной полиимидной изоляции (ПНЭТ-
имид). Частичное отверждение адгезива осуществляется прессованием при температуре 90—100 °С и давлении
0,5 МПа.
Укладку монтажного провода осуществляют с помощью специальной головки, оснащенной ультразвуковым прижимом 1, ножом-отсекателем 2, трубкой 3 для подачи провода (рис. 5.32). Наконечник прижима спрофилирован таким образом, что в процессе укладки удерживает провод 4, утапливая его в адгезив 5, на поверхности
платы 6 на 0,5 диаметра. |
|
|
30° |
2 |
F |
|
|
|
|
3 |
|
|
4 |
|
1 |
|
|
|
5 |
|
|
6 |
|
Рис. |
5.32. Схема укладки монтажного провода |
Технологические режимы укладки |
провода: частота УЗК 44—45 кГц, амплитуда 10 мкм, давление |
16—18 кПа. УЗ-колебания обеспечивают размягчение адгезива и утапливание в него провода. После окончания трассировки провода головка останавливается и провод отрезается ножом. Полное погружение проводников в
131

слой адгезива и окончательное отвержение последнего происходит в результате прессования при температуре 180 С под давлением 1,0—1,5 МПа.
Плата с закрепленными в адгезиве монтажными проводами подается на операцию сверления. Монтажные отверстия сверлятся по программе таким образом, чтобы проводник в плате располагался по оси симметрии отверстия. Практически реализуется шаг координатной сетки 0,625 мм. В результате сверления возможно наволакивание диэлектрических материалов на торцы проводов. Поэтому необходима операция гидроабразивной очистки отверстий, которая проводится особо тщательно, так как вскрытая площадь при сверлении торцов монтажного провода достаточно мала.
Для укладки проводников в адгезив используется отечественная установка с программным управлением от перфоленты (рис. 5.33). Скорость координатных перемещений составляет 5,0 м/мин, точность позиционирова-
ния ±0,5 мм, потребляемая мощность 1,5 кВт. Максимальные размеры платы 500×600 мм, поворот расклады-
вающей головки до 90°, ультразвуковой генератор УЗГ-3-0.4 мощностью 400 Вт.
|
|
|
|
УЗГ |
|
Отрез- |
|
Привод |
|
|
Подача |
поворота |
|
|
МСП |
ное |
|
||
|
|
|||
прово- |
|
|
||
|
устрой- |
Привод |
Устройство |
|
|
ство |
локи |
программного |
|
|
|
перемещения |
||
|
|
|
управления |
|
|
|
|
|
|
|
|
Стол |
y |
|
|
|
х |
БП |
|
|
|
Привод |
|
|
|
перемещения |
|
|
|
Рис. 5.33. Схема установки для трассировки проводов |
Операцией, определяющей надежность электрического соединения проводного и печатного монтажа, является химико-гальваническая металлизация отверстий. Если на наружных слоях платы печатный монтаж не предусмотрен, то ее перед сверлением и металлизацией защищают технологическим лаком. Если печатный монтаж необходим, то применяют полуаддитивный метод (рис. 5.34).
Подготовка поверхности
Получение печатного монтажа
Нанесение
адгезива
Укладка проводов и их закрепление
Сверление и химикогальваническая металлизация отверстий
132
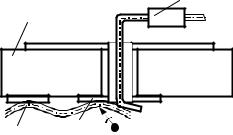
Рис. 5.34. Схема технологического процесса изготовления многопроводной платы
На одной стороне многопроводной платы можно разместить несколько слоев проводного монтажа, чередуя нанесение адгезива и раскладку проводов. Существенные недостатки метода — невысокая надежность монтажных соединений провода с металлизированными отверстиями, необходимость применения адгезива, высокая трудоемкость монтажа. Достоинства метода — высокая точность двустороннего монтажа с пересечением проводов, оперативное внесение изменений в монтаж, автоматизация трассировки проводов.
Для повышения надежности межслойных соединений разработан вариант многопроводного метода, отличающийся тем, что соединения объемных проводов и печатного монтажа осуществляются путем пайки проводов к монтажным площадкам, так как адгезионный слой наносится через трафарет и не закрывает отверстия и контактные площадки. Пайка выполняется монтажной головкой с программным управлением, ее производительность 300—400 точек в час. Метод экономичен при производстве плат в количестве 500—1000 шт/год.
Суть многопроводного неупорядоченного монтажа незакрепленными проводами заключается в произволь-
ном прокладывании изолированных монтажных проводов на поверхности ДПП и образовании контактных соединений с печатным монтажом путем пайки или сварки. К этим методам относятся методы Tiers (пайкой) и Stitch-Wire (сваркой соединений), разработанные фирмами США. В отличие от метода Multiwire провода 1 (рис. 5.35) не приклеиваются к основанию платы 2, а остаются свободными и соединяются с монтажными площадками 4 указанными выше методами. В отверстия плат могут монтироваться элементы 3.
3
2
1 4
Рис. 5.35. Схема проводного монтажа незакрепленными проводами
Достоинства метода — простота изготовления, ремонтопригодность, автоматизация трассировки и пайки проводников, высокая точность монтажа. Недостатки — односторонняя установка ЭРЭ и ИМС, необходимость дополнительных контактных площадок, большая степень свободы монтажных проводов.
Для изготовления специальной ЭА, устойчивой к ударам и вибрациям, применяется метод Stitch-Wire, в котором монтажные соединения выполняются сваркой. Это потребовало внесения в конструкцию платы некоторых специальных элементов. Так, для монтажа применяется одножильный никелевый провод диаметром 0,25 мм во фторопластовой изоляции, а контактные площадки выполнены из нержавеющей стали, что обеспечивает необходимую точность и коррозионную стойкость контактного соединения. С этой целью на диэлектрическую основу с обеих сторон наносят фольгу из нержавеющей стали толщиной 76 мкм, на которой с внутренней стороны нанесен слой меди толщиной 35—50 мкм, а с наружной — тонкий слой никеля. Медное покрытие под стальными монтажными площадками выполняет функции теплоотвода (рис. 5.36). Разводка соединений осуществляется методом параллельного электрода с подачей импульса тока длительностью 2,5 мс. В процессе сварки провод 2 подается через трубчатый электрод 3 и прижимается к монтажной площадке с некоторым усилием. Под давлением происходит удаление изоляции, сплющивание провода и образование контакта. Нижний элек-
133

трод 1 подводится к монтажной площадке с противоположной стороны. При кратковременном импульсе выделение теплоты невелико, что не оказывает влияния на прочность сцепления фольги с основанием платы.
3 |
4 |
5 |
2
~
1 |
Рис. 5.36. Схема сварки монтажных проводов:
1,3 – электроды; 2 – провод; 4 – монтажная площадка; 5 – плата
Стежковый монтаж заключается в прокладывании изолированных проводов по кратчайшим расстояниям по поверхности ДПП и в монтажных отверстиях с образованием петель и последующим подпаиванием их к контактным площадкам платы. Процесс осуществляется на станках с ЧПУ, а в качестве инструмента применяют иглу из нержавеющей стали, которая имеет внутренний диаметр, превышающий диаметр провода ПЭВТЛК
0,1—0,2 мм на 0,08—0,1 мм, а также скос с углом заточки 50—75 °, длину 25—35 мм.
Игла, проходя через монтажное отверстие, прокалывает пакет резиновых прокладок, которые задерживают провод при обратном ходе иглы (рис. 5.37, а). После трассировки резиновые прокладки стягивают с петель и проводят их лужение групповым методом в ванне припоя при температуре 350±10 °С в течение 5—6 с (рис. 5.37, б). Кабельная бумага предохраняет поверхность ДПП при лужении и удаляется после выполнения операции. Подгибку и пайку петель на контактные площадки (рис. 5.37, в) осуществляют вручную паяльником или на станках с ЧПУ.
1 |
2 |
3 |
|
|
4 |
а |
|
|
|
|
5 |
|
|
6 |
б |
|
|
в
Рис. 5.37. Схема стежкового монтажа:
1 – провод; 2 – игла; 3 – плата; 4 – кабельная бумага; 5 – пакет резиновых прокладок; 6 – защитная пластина
134
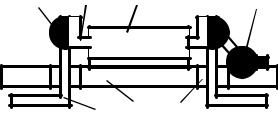
Установка "Аракс" имеет координатный стол, перемещающийся с шагом ±0,025 мм и максимальной скоро-
стью 10 мм/с. Она позволяет вести стежковый монтаж на платах размерами 350×450 мм. Достоинства метода — снижение трудоемкости в 2—3 раза по сравнению с методами изготовления МПП, сокращение времени выпуска конструкторской документации с 30 дней для 6—8- слойной МПП до 5—6 дней, брак не превышает 5 %.
Несмотря на то что отдельные операции стежкового монтажа автоматизированы, в целом производительность процесса невелика, так как каждая операция требует продолжительного ручного труда при сборке и разборке различных приспособлений.
Дальнейшим развитием проводного монтажа явилась разработка плат третьего поколения без печатного монтажа. Основанием таких плат является лист толщиной 0,5—2 мм из проводящего материала (стали, алюминиевого сплава и т. д.), который выполняет роль теплоотвода от микросхем и является шиной с нулевым потенциалом. В основании платы выполнены пазы, заполненные эластичным материалом, через который пропущены тонкие изолированные провода марки ПЭВТЛК (рис. 5.38). Между пазами установлены на теплопроводный клей микросхемы с планарными и штыревыми выводами с шагом 2,5; 1,25 и 1 мм, а также другие ЭРЭ.
1 |
2 |
3 |
4 |
|
7 |
6 |
5 |
Рис. 5.38. Фрагмент конструкции теплопроводящей платы проводного монтажа:
1 – паяное соединение; 2 – вывод; 3 – элемент; 4 – контактная площадка; 5 – диэлектрический материал; 6 – проводящее основание; 7 – провод
Преимущества плат с теплоотводом перед МПП:
∙ |
улучшение теплоотвода в 2—3 раза; |
∙ |
увеличение надежности работы, так как снижение температуры корпуса ИМС на 10 °С увеличивает на- |
дежность ее работы в 1,5—2 раза; |
|
∙ |
повышение быстродействия из-за высокой тактовой частоты (65—100 МГц) благодаря мощным шинам |
питания и хорошей электрической развязке ИМС по питанию;
∙отсутствие выброса химических стоков, содержащих тяжелые металлы (медь, никель, свинец, железо и др.), что в 20 раз экологически менее опасно;
∙снижение затрат на разработку плат в 2 раза, производственных площадей в 5 раз.
Новым направлением в технике монтажа является применение тканых коммутационных устройств (ТКУ), представляющих собой тканый материал, изготовленный из электропроводящих и диэлектрических нитей, с закрепленными на нем ЭРЭ и ИМС. В общем виде ТКУ (рис. 5.39) представляет собой однослойное или многослойное изоляционное поле 1, изготовленное из диэлектрических нитей. С двух сторон поля во взаимно перпендикулярных направлениях по координатам x и y проложены электропроводящие нити 2 и 3, которые на наружной поверхности в заданных точках образуют монтажные узлы 4, выполняющие электрические соединения между отдельными электропроводящими нитями. На наружной поверхности поля сформированы контактные площадки 6, петли 5, служащие для присоединения выводов ЭРЭ, и удлиненные выводы 7, необходимые для подсоединения к разъемам.
135
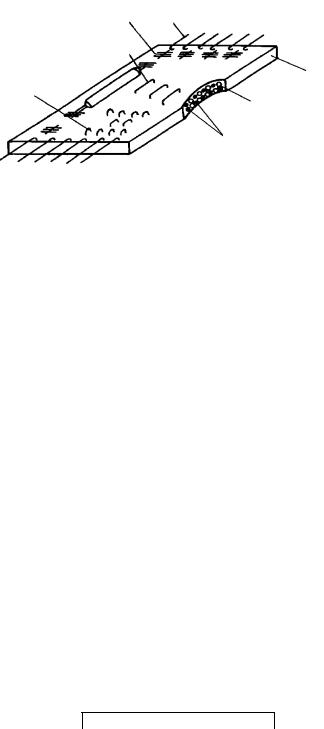
6 7
5
1
4
2
3
Рис. 5.39. Тканное коммутационное устройство
ТКУ изготавливаются на ткацких автоматах, дополнительно снабженных механизмами подачи и натяжения электропроводящих и диэлектрических нитей, а также петлеобразования. После изготовления ТКУ им придают жесткость. Применяются следующие способы фиксирования тканой структуры:
∙ тепловая обработка продувкой горячим воздухом или паром с температурой 180—220 °С для размягчения термопластичных тканей и последующей фиксации структуры;
∙оплавление исходного материала тканей для герметизации кромок, отверстий, контактных площадок;
∙компаундирование путем заливки сеточной структуры пластмассами с целью повышения механической жесткости и прочности ТКУ;
∙пластифицирование — заливка структуры составами на основе кремнийорганических каучуков для придания гибкости, эластичности, химической стойкости и повышения климатической стойкости;
∙формование — тепловой нагрев ткани с целью придания ей определенной пространственной формы и ее стабилизации.
Соединение электрических проводников в контактных узлах и присоединение навесных ЭРЭ осуществляются контактной микросваркой. ТКУ имеют электрическое сопротивление проводящих нитей не более 0,1 Ом,
прочность изоляции до 1000 В, электрическое сопротивление изоляции 10—12 МОм, температурный диапазон
–50…+65 °С, затухание 110—120 дБ, электрическую емкость между электропроводящими нитями 33—38 пФ. Функционально ТКУ подразделяются на четыре группы: конструктивы, платы, кабели и соединители
(рис. 5.40). Каждая структура может быть одноили многослойной с двухкоординатным, внутримодульным, внутриблочным или межблочным расположением нитей. Особенности технологии позволяют получать как гибкие и эластичные, так и жесткие коммутационные устройства плоской или объемной формы.
ТКУ
|
|
|
|
|
|
|
|
|
|
|
|
|
|
|
|
|
|
|
|
Платы |
|
Кабели |
|
Конструктивы |
|||||
|
|
|
|
|
|
|
|||
Пакетные |
|
Однослойные |
|
|
Страница |
||||
|
|
|
|
|
|
|
|||
Желобные |
|
Многослойные |
|
|
Модуль |
||||
|
|
|
|
|
|
|
|||
Комбинированные |
|
Сеточные |
|
|
Блок |
||||
|
|
|
|
|
|
|
|
||
Сеточные |
|
|
|
|
Конус, цилиндр |
Рис. 5.40. Классификация ТКУ
136
С экономической точки зрения производство ТКУ при существующем уровне развития текстильной промышленности в 5—6 раз дешевле по сравнению с печатным и проводным монтажом за счет того, что трудоемкость снижается в 5—6 раз, затраты на материалы — в 7, а на оборудование — в 5 раз. Экономятся цветные и дорогостоящие металлы, химреактивы и т. д. ТКУ имеют высокую гибкость формы, что позволяет формировать блоки заданной конфигурации и значительно меньшей массы. ТКУ имеют высокую надежность в условиях повышенных механических и климатических воздействий. К недостаткам метода относятся невысокая точность изготовления коммутационных полей, трудоемкость присоединения элементов и низкая ремонтопригодность.
5.11. ПЛАТЫ МИКРОЭЛЕКТРОННОЙ АППАРАТУРЫ
Дальнейшая микроминиатюризация электронной аппаратуры основана на широком использовании бескорпусных ИМС и микросборок частного применения, что ведет к существенному улучшению массогабаритных характеристик, теплообмена и повышению надежности изделий. Применение бескорпусных ИМС привело к созданию новых методов конструирования, потребовало дальнейшего совершенствования технологии коммутационных плат и внедрения методов микроэлектроники в производство ЭА. Современное конструктивнотехнологическое построение ЭА позволило выделить несколько уровней электрических соединений, каждый из которых имеет свои специфические особенности сборки и монтажа: соединение ИМС и БИС на пассивной подложке гибридных ИМС и БИС, соединение гибридных ИМС и БИС на коммутационных платах ячеек, соединения между ячейками в блоке, соединения между блоками в аппаратуре. Таким образом, выделилась новая кон- структивно-технологическая общность — микроэлектронная аппаратура (МЭА).
Наиболее распространенными методами коммутации функциональных модулей МЭА являются многослойные печатные платы, толстопленочная многослойная разводка, разводка на многослойной керамике, толстопленочная многослойная разводка на жестких и гибких платах. Для повышения плотности монтажа используют полуаддитивную и аддитивную технологию формирования слоев, а в субтрактивных процессах переходят на тонкую (9 мкм) и сверхтонкую (5 мкм) фольгу. Это позволяет исключать или уменьшать боковое подтравливание линий и изготавливать слои МПП с шириной токопроводящих дорожек 125—250 мкм.
Толстопленочная многослойная разводка выполняется путем последовательного нанесения на жесткую диэлектрическую подложку проводящих и диэлектрических паст методом трафаретной печати и последующего их вжигания. Коммутационные платы могут достигать размеров 100×120 мм, а изготавливают их на керамических основаниях из оксида алюминия (поликор, 22XC) или оксида бериллия (брокерит). Разработанные токопроводящие пасты на основе золота, серебра, никеля или сплавов платина— серебро— золото, палладий— золото, палладий— серебро, палладий— медь— серебро обеспечивают удельное сопротивление 0,005—0,1 Ом/мм2. Для межслойной изоляции применяют пасты пленочной технологии.
Необходимость улучшения теплоотвода от мощных радиоэлементов и ИМС при работе в условиях повышенных температур способствовала появлению МПП с разводкой слоев на жестких металлических основаниях. В качестве материала основы используется алюминий, сталь, ковар (сплав железа с никелем и кобальтом), титан, которые покрываются смолой, эмалью или легкоплавким стеклом. Самым экономичным материалом из этой группы является сталь с нанесенной пленкой эмали, в состав которой входят оксиды магния, кальция, кремния, бора, бериллия, алюминия или их смеси, связка (поливинилхлорид, поливинилацетат, метилметакрилат) и пластификатор. Пленка соединяется с основанием путем прокатки между вальцами с последующим спеканием. Таким образом можно создавать многослойные структуры с различными механическими и электрическими характеристиками.
137