
по трэс
.pdf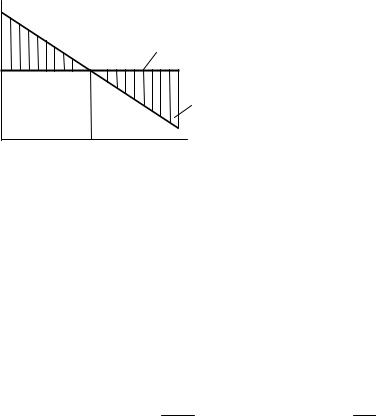
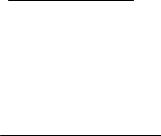

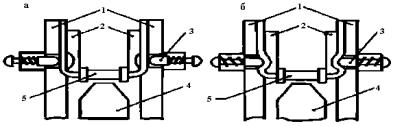
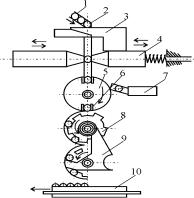
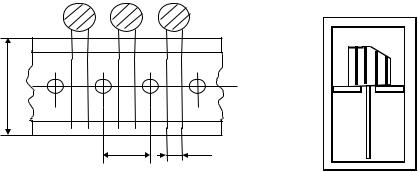
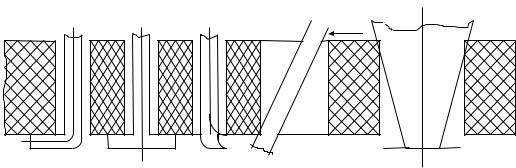
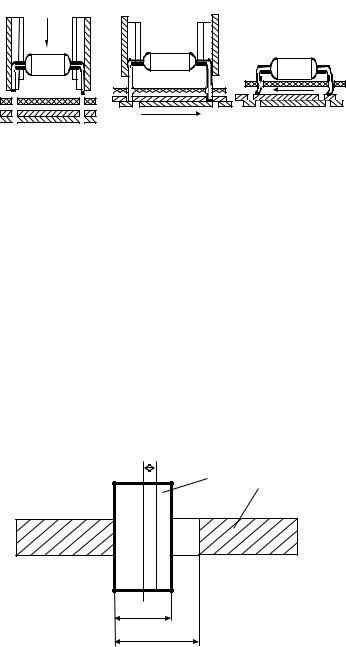
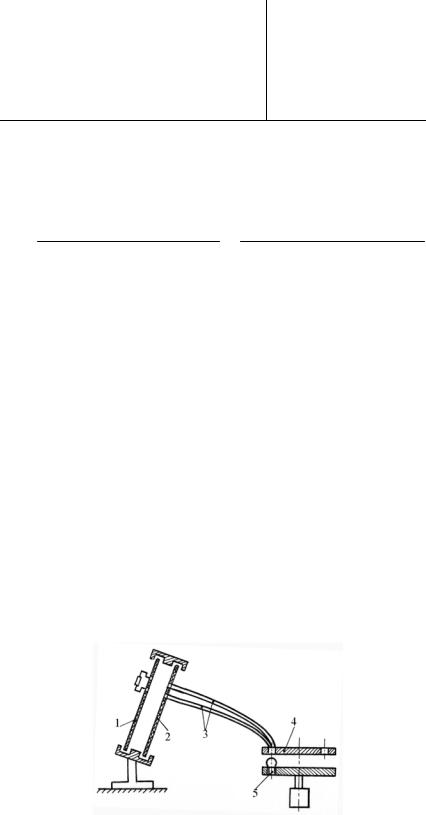
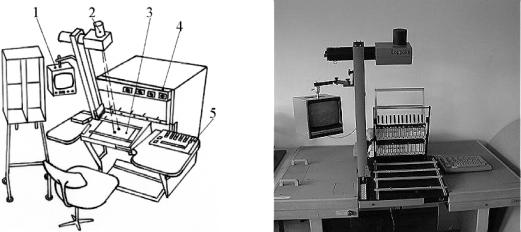
Рис. 9.15. Стол с гибкой программой сборки: 1 – дисплей; 2 – проектор; 3 – панель; 4 – накопитель; 5 – микроЭВМ; 6 – кассетница
для нестандартных элементов и плат
В первых светомонтажных столах модели УПСП-904 (СССР) и фирмы Streckfuss (Германия ) указание посадочных мест осуществлялось проецированием со слайдов в диапроекторе, закрепленном под столом. Число и расположение пятен света на ПП зависели от расположения отверстий в носителе информации — латунной фольге или кинопленке толщиной 0,1 мм, вставленной в рамку слайда. Недостатками являлись высокая трудоемкость подготовки программ, низкий темп сборки.
Указание с помощью световодов путем подсветки отверстий в ПП снизу использовалось в установках "Свет" и "Цвет". Полярность элементов указывалась миганием. Недостатками являлись значительная трудоемкость подготовки программ (до 2 ч на 50 ЭРЭ), ограниченные возможности передачи дополнительных символов.
Более гибкая система с использованием "световой указки", в которой пятно светового луча от проектора перемещается по ПП со скоростью 300 — 400 мм/с с разрешением 0,15 — 0,3 мм. Луч может формировать разные символы, указывать место установки. Характеристики столов приведены в табл. 9.5.
Табл. 9.5. Светомонтажные столы программной сборки
Модель |
Устройство |
Производитель- |
Средства отобра- |
Тип внешних |
|
управления |
ность, шт/ч |
жения |
ОЗУ |
|
|
|
|
|
ПМПП-902 (СССР) |
МП-901 |
200-300 |
Табло 3-знаковое |
НМЛ |
ТС-1409 (СССР) |
"Электроника-60" |
500-600 |
То же |
НМЛ |
3D-TS Polytronik |
Z-80 |
650 |
Табло 32знако- |
НГМД 64 К |
|
|
|
вое |
|
6235 Logpoint |
Z-80 |
1000 |
Дисплей |
НГМД 64 К |
(Англия) |
|
|
|
|
V-T-AS |
Микропроцессор |
1000 |
То же |
НМЛ |
|
|
|
|
|
Светомонтажный стол модели Logpoint (рис. 9.15) состоит из светолучевой головки, рабочего стола, микроЭВМ, дисплея, клавиатуры и элеваторного накопителя. Программирование осуществляется в пошаговом режиме, и все данные выводятся на экран дисплея.
237