
по трэс
.pdf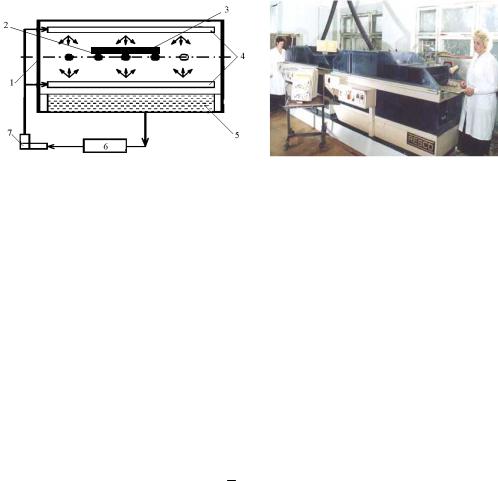
произвольному разложению со взрывом, поэтому необходимо тщательно контролировать состав ванн и обеспечивать надежную вытяжную вентиляцию на рабочем месте. Окислитель не поддается регенерации.
Процесс травления организуется таким образом, чтобы химическое воздействие травителя на травящийся материал осуществлялось в оптимальном режиме. Травильные установки должны обеспечивать: температурную стабильность процесса; перемещение заготовки и подачу травителя в зону обработки; аэрацию (разбрызгивание) травителя; удаление травителя, промывку, нейтрализацию и сушку плат; непрерывный процесс при массовом производстве. Различают травильные установки, работающие по принципу погружения, центрифугирования и разбрызгивания. Более производительны установки с разбрызгиванием травильного раствора на одну или обе стороны плат (рис. 5.12). Платы с помощью транспортного устройства перемещаются из одной технологической зоны в другую.
а б Рис. 5.12. Схема (а) и внешний вид установки струйного травления:
1 – ванна; 2 – |
транспортер; 3 – заготовка, 4 – |
разбрызгиватель; |
5 – |
травитель; 6 – регенератор; 7 – |
насос |
Давление в форсунках находится в пределах 0,1— 0,5 МПа, а струя подается либо перпендикулярно к по-
верхности платы, либо под небольшим углом. Постоянное обновление окислителя в зоне обработки и удаление продуктов реакции обеспечивают высокую производительность, а соответствующая траектория струи — незначительное боковое подтравливание. Линии компонуются из модулей травления, промывки, сушки и регенерации. Автоматические модульные линии оснащаются устройствами для контроля кислотности раствора, температуры и давления в форсунках.
Скорость травления возрастает в два раза по сравнению с персульфатными растворами. Недостаток — высокая летучесть аммиака из раствора. В травильных установках струйного типа, в которых струи раствора постоянно соприкасаются с воздухом, происходит саморегенерация раствора при его достаточной кислотности:
2FeCl2 + 2HCl + 1 O2 → 2FeCl3 + H2O.
2
Это позволяет поддерживать коэффициент использования хлорного железа в пределах 50—55 %. Полуавтоматическая линия травления “ Печать-1” имеет следующие характеристики: производительность —
16 м2/ч, размеры обрабатываемых плат — 500 ×500 мм, температура травильного раствора — 35—50 |
°С, число |
|
качаний коллекторов с форсунками — 27 в минуту, скорость конвейера — 0,2—2 |
м/мин, мощность источников |
питания — 10 кВт, габаритные размеры — 4230 ×1160×1330 мм.
Линия травления рисунка печатных плат КПМ 1.240.000 состоит из трех модулей: травления, промывки и сушки с регулируемой скоростью транспортного конвейера 0,2—2 м/мин. Травление меди осуществляется раствором, подаваемым через форсунки, совершающие 27—30 качаний в минуту. Травящий раствор работает в замкнутом цикле и очищается фильтром. Производительность до 16 м2/ч.
108
Во Франции в 1970 г. запатентован электрохимический способ травления, который осуществляется в струе электролита, причем анодом служит медная фольга платы. Скорость травления возрастает в 2—3 раза, однако широкое применение электрохимического травления сдерживается неравномерностью удаления металла с поверхности платы, что приводит к образованию невытравленных островков. Индивидуальный токоподвод и совмещение электрохимического процесса с химическим не обеспечивают его эффективность. Полностью реализовать преимущества электрохимического метода позволяют подвижные носители заряда, которые принимают заряд с анода и переносят его на поверхность меди, переводя последнюю в ионную форму. В качестве подвижных носителей используют взвешенный активированный уголь с содержанием в растворе 15—30 % и размером частиц 10—50 мкм. Электрохимическое травление сводит к минимуму боковое подтравливание токопроводя-
щих дорожек и контактных площадок, обеспечивает разрешающую способность, равную 70— 100 мкм.
5.6. ХИМИЧЕСКАЯ И ЭЛЕКТРОХИМИЧЕСКАЯ МЕТАЛЛИЗАЦИЯ
Химическая металлизация ПП используется в качестве подслоя для нанесения основного слоя токопроводящего рисунка гальваническим способом при субтрактивном полуаддитивном методе или основного слоя при изготовлении плат аддитивным методом. Толщина слоя химической меди должна составлять 0,25—1,0 мкм, покрытие должно быть однородным, пластичным, хорошо сцепленным с диэлектриком.
Для придания диэлектрику способности к металлизации проводят такие подготовительные операции, как сенсибилизация и активация поверхности.
Сенсибилизация (от лат. sensibilis — чуствительный) поверхности имеет целью формирование на поверхности диэлектрика пленки ионов двухвалентного олова Sn2+, являющихся восстановителем для ионов активатора металлизации. Платы обрабатывают в растворе двуххлористого олова и соляной кислоты с соотношением 1:4 в течение 5—7 мин и промывают в деионизованной воде. Образование гидрооксида олова происходит по реакциям:
SnCl2 + H2O = Sn(OH)Cl + HCl , Sn(OH)Cl + H2O = Sn(OH)2 + HCl .
Электронно-микроскопические исследования показали, что гидрооксид двухвалентного олова адсорбируется в виде отдельных участков размером порядка 10 нм, на расстоянии 20—30 мм друг от друга, так, что ею покрывается вся поверхность диэлектрика. Гидрооксид двухвалентного олова обладает сильными восстановительными свойствами. Активация поверхности диэлектрика проводится в растворах солей благородных металлов, преимущественно палладия, и способствует последующему осаждению меди. Активирующий раствор имеет следующий состав: 3,5—4,0 г/л PdCl2, 10— 20 мл/л HCl, остальное — вода, а процесс осуществляют при температуре 40—50 °С (pH = 3,5—0,5) в течение 5—7 мин.
Реакция восстановления палладия на диэлектрике
Sn(OH)2 + PdCl2 = Pd +SnO2 + 2HCl ,
в ионном виде
Sn 2+ + Pb2+ = Sn 4+ + Pb0 ,
на торцах контактных площадок
Cu + PbCl2 = Pb + CuCl2 .
На поверхности изоляционного материала вследствие адсорбции и восстановления палладия образуется тонкая сетка частиц размером порядка 10 нм. Связь частиц палладия с подложкой определяется их внедрением в поры диэлектрика, а также образованием ковалентных связей между металлом и материалом подложки. Для
109
хорошего сцепления необходимо, чтобы на поверхности диэлектрика было не менее 1×10–6 кг/см2 палладия. Пленка палладия, образующаяся на торцах контактных площадок, является нежелательной, так как приводит к снижению прочности химически осажденной меди в результате образования гидридов палладия при захватывании палладием водорода. Кроме того, это приводит к образованию высокого и неравномерного переходного электрического сопротивления.
Для устранения контактного выделения палладия применяют либо предварительное оксидирование медных торцов контактных площадок, либо совмещенные растворы для активации диэлектрика следующего состава
(г/л): 0,8—1,0 PbCl 2, 40—70 SnCl 2×2H2O, 150—200 HCl, 140—150 KCl.
Совмещенный активатор содержит коллоидные растворы, в которые входят соли палладия и олова. При обработке плат в этом растворе в течение 5—10 мин выделение палладия на торцах контактных площадок значительно меньше.
Химическое осаждение меди — окислительно-восстановительный процесс, который происходит вследствие восстановления ионов двухвалентной меди на активированных поверхностях из ее комплексных солей. Основными компонентами раствора химического меднения являются:
·15—20 г/л сернокислой меди CuSO4 — источника катионов Cu2+ ;
·2—4 г/л солей никеля NiCl2 для большей прочности сцепления меди с диэлектриком;
·10—15 г/л щелочи NaOH для создания pH = 10—13;
·2—4 г/л Na2CO3 для увеличения скорости химического меднения и как буферная добавка;
·4—16 г/л восстановителя ¾ 33 %-го раствора формалина (CHOH);
· комплексообразователь ¾ калий виннокислый как стабилизатор раствора — 50—60 г/л.
При введении формалина в раствор реакция восстановления меди при комнатной температуре становится автокаталитической. Процесс химического меднения представляет собой сумму электрохимических реакций катодного восстановления металла и анодного окисления восстановителя. Основная катодная реакция восстановления меди выражается уравнением
Cu2+ + 2HCOH + 4OH− ® Cu + H2 + 2HCOO− + 2H2O .
Анодная реакция заключается в окислении формалина при pH = 12—13 и потенциале + 0,80 В. Время осаж-
дения подслоя меди толщиной 0,5 мкм при температуре 20 °С составляет 15—20 мин. Для облегчения удаления водорода и лучшего омывания раствором отверстий малого диаметра процесс ведется с плавным покачиванием плат (8—10 качаний в минуту при амплитуде 50—100 мм).
Для повышения качеств металлизации ПП в серийном производстве применяют специальное технологиче-
ское оборудование, которое обеспечивает поддержание температуры с точностью ±1 °С и состава растворов, повышает производительность труда в 10 раз, снижает стоимость металлизации на 20—30 % по сравнению с ручным трудом.
Для химической металлизации ПП используют автоматические линии типа АГ-38, АГ-42, оснащенные набором ванн необходимого размера и автооператором (рис. 5.13). В соответствии с заданной программой подвески с платами перемещаются автооператорами, управляемым командоаппаратом. Длина линии по ходу авто-
операторов — 10 м, габаритные размеры плат — 250 ´250 мм, производительность составляет 30 шт/ч.
Линия химической металлизации МЦ 104.131 имеет гибкую систему управления автооператором, механизм покачивания подвесок грузоподъемностью до 500 кг. Количество одновременно загружаемых заготовок в ванне
— 132, темп выхода подвесок с линии — 12 шт/мин, из автооператоров — 3 шт/мин, производительность линии 660 плат в час, что в 2 раза выше производительности линии АГ-42.
110
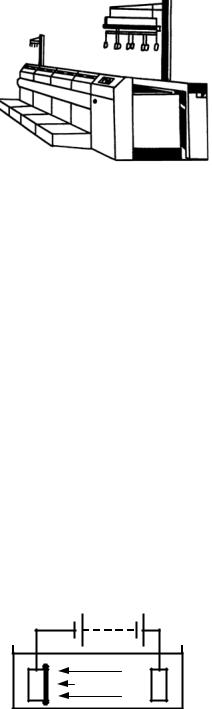
Рис. 5.13. Автоматическая линия АГ-38
Основными проблемами химической металлизации являются низкая производительность, сложность процесса, использование драгоценных металлов. Поэтому разрабатываются процессы термохимической беспалладиевой металлизации в растворе следующего состава: 130—170 г/л кальция фосфорноватисто-кислого, 200— 250 г/л меди сернокислой пятиводной, 6—10 г/л гипофосфита аммония, 200—300 мл/л аммиака (25%-го). После обработки платы выдерживают в термошкафу при температуре 100—150 °С в течение 8—10 мин, в результате чего происходит термическое разложение комплексной соли гипофосфита меди на поверхности платы и в отверстиях, приводящая к образованию электропроводящего покрытия.
Гальваническую металлизацию в производстве ПП применяют: для образования проводящего рисунка схемы с толщиной меди в отверстиях не менее 25 мкм; для предварительного увеличения тонкого слоя химической меди до толщины 5—8 мкм с целью последующего формирования рисунка схемы; для нанесения металлического резиста, например олово— свинец, толщиной 10—20 мкм либо специальных покрытий золотом, серебром толщиной 2—5 мкм.
Гальванический метод нанесения металлических покрытий был изобретен в 1837 г. в России электротехником Б.С.Якоби и заключается в том, что деталь, подлежащая покрытию, помещается в электролитно-водный раствор солей металла в качестве катода, а анодом является осаждаемый металл (медь). Необходимые для восстановления электроны поступают от внешнего источника постоянного тока. Под действием напряжения ионы металла движутся к катоду, присоединяют электроны и осаждаются на нем как нейтральные атомы (рис. 5.14).
K |
Men+ |
A |
Рис. 5.14. Cхема гальванической металлизации
Понятия "анод" (от греч. anodos — движение вверх, восхождение) и "катод" (от греч. kathodos — ход вниз, возвращение) были введены М. Фарадеем для обозначения направлений движения частиц, выделенных на электродах. Реакция восстановления меди
Cu 2+ + 2e = Cu .
Количественно процессы гальванической металлизации описываются первым законом Фарадея, согласно которому, масса выделяемого вещества при электролизе пропорциональна прошедшему количеству электричества I t:
m = k I t ,
111

где k — теоретический электрохимический эквивалент, пропорциональный молярной массе М и обратно про-
порциональный химической валентности металла n (второй закон Фарадея): k = M /(F n) ; F — постоянная Фа-
радея: F » 96 500 г/А×с.
Для двухвалентной меди k = 1,186 г/(А×с), однако на практике теоретическое значение электрохимического эквивалента не достигается из-за побочных процессов, например осаждения водорода. Поэтому второй, не менее важной, характеристикой процесса гальванической металлизации является выход металла по току:
h = M ×100 % .
M р
Время для нанесения покрытия заданной толщиной d, считая, что масса
M = rм Sк d
(где rм — плотность металла; Sк — площадь катода), определяется так:
t = rм Sк d . k I hк
Для предварительной металлизации (затяжки) отраслевыми стандартами рекомендуются борфтористоводородные и сернокислые электролиты меднения. Первый состоит из: 230—250 г/л борфтористой меди Cu(BF4)2
¾ источника ионов; 5—15 г/л борфтористоводородной кислоты HBF4, вводимой для повышения злектропроводности электролита; 15—40 г/л борной кислоты H3BO3, необходимой для стабилизации электролита. Процесс ведут при температуре (20±5) °С, катодной плотности тока 3—4 А/дм2, скорости осаждения 20—30 мкм/ч.
Достоинства электролита — большая концентрация меди, высокая скорость ее осаждения, покрытие получается более мелкокристаллическое, чем из сернокислого электролита. Недостаток — высокая агрессивность электролита.
Лучшей рассеивающей способностью характеризуется сернокислый электролит с комплексной добавкой следующего состава: 60—70 г/л сернокислой меди; 150—180 г/л серной кислоты; 0,03—0,06 г/л хлористого натрия; 1—3 мл/л комплексной добавки (трилон Б).
Электролитический сплав олово— свинец должен иметь состав, приближающийся к эвтектическому, что обеспечивает в дальнейшем его оплавление при минимальной температуре и хорошую паяемость ПП. Это достигается определенным процентным содержанием олова и свинца в электролите, строгим поддержанием режима осаждения.
Осаждение покрытия олово— свинец ведут в борфтористоводородном электролите следующего состава:
13—15 г/л Sn2+, 8—10 г/л Pb2+, 250—300 г/л HBF4, 20—30 г/л H3BO3, 3—5 г/л комплексных добавок. Аноды из-
готавливают из сплава, содержащего 61 % олова и 39 % свинца. Процесс осаждения ведут при температуре
(20±5) °С, плотности тока 1—2 А/дм2, скорость осаждения при этом составляет 1 мкм/мин.
В качестве оборудования используют автооператорную и управляемую ЭВМ линию АГ-44 или универсальные лабораторные установки типа УПУГ-1, УПУГ-2, имеющие ванны с автоматическими регуляторами температуры и пневматическими механизмами для покачивания штанг.
Для улучшения паяемости гальваническое покрытие сплавом олово— свинец оплавляют, используя установки с ИК-нагревом НПО "Ратон". Установка состоит из верхнего и нижнего блоков отражателей, между которыми проходит конвейер. ИК-лампы, установленные в фокусе эллиптического отражателя, фокусируют световой поток на поверхность плат, в результате сплав олово— свинец оплавляется и приобретает структуру металлур-
гического сплава. Температура зоны предварительного нагрева составляет 200 °С, а зоны оплавления — 500 °С
±5 %. Скорость движения конвейера 0,05—0,5 м/мин, потребляемая мощность 51,5 кВт.
112
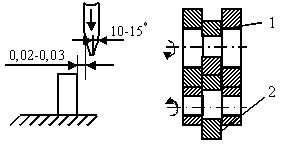
5.7.МЕХАНИЧЕСКАЯ ОБРАБОТКА ПЛАТ
Впроизводстве ПП до 60 % трудозатрат приходится на механическую обработку, которая включает: ∙ получение заготовок путем резки листового материала и раскроя листа либо штамповкой; ∙ формирование контура платы фрезерованием; ∙ выполнение отверстий в плате сверлением либо штамповкой.
Всерийном и мелкосерийном производстве для резки листового материала применяют гильотинные нож- ницы, которые состоят из подвижного и неподвижного ножей, изготовленных из инструментальной стали У8А, прижима разрезаемых материалов и упора, регулирующего ширину заготовок. Геометрические параметры ре-
жущей части подвижного ножа: передний угол 0—5 °, задний 10—15 ° , для неподвижного ножа задний и перед-
ний углы равны 0°. Параллельные ножи устанавливаются с минимальным зазором 0,02—0,03 мм по всей длине (рис. 5.15, а). Недостатки оборудования — низкая производительность, возможность образования сколов на краях заготовок.
В серийном и крупносерийном производстве материал разрезают с помощью одно- и многоножевых ролико- вых ножниц, в которых ножи изготовлены из металлокерамического твердого сплава ВК8М. Ножи устанавливают с зазором 0,01—0,03 мм и вращают навстречу друг другу со скоростью 2—10 м/мин (рис. 5.15, б). Для получения заданной ширины заготовки ножницы снабжены регулируемыми упорами. Образующуюся пыль отсасывают с помощью промышленных пылесосов. Кинематическая скорость резания достигает 24 м/мин, максимальная ширина разрезаемого материала 1300 мм, потребляемая мощность 3 кВт.
Размеры заготовок из слоистых пластиков определяют по формулам:
Аз = Ап + 2 H , Bз = Bп + 2 H ,
где Аз, Вз — длина и ширина заготовки; Ап, Вп — длина и ширина платы по рабочему чертежу; Н — ширина технического поля.
Рис. 5.15. Схема резания гильотинными (а) и роликовыми (б) ножницами Платы малых габаритных размеров изготавливают из групповой заготовки, площадь которой
n
Sз = ∑ ( Апi + 2 H ) (Bпi + 2 H ) ,
i =1
где n — количество плат; Апi, Впi — длина и ширина i-й платы.
Ширина технологического поля для ОПП и ДПП не должна превышать 10 мм, для МПП — 30 мм.
В крупносерийном и массовом производстве раскрой стандартных листов фольгированного диэлектрика
(обычно 500×700 мм) выполняют штамповкой в специальных штампах на эксцентриковых прессах с одновременной пробивкой базовых отверстий на технологическом поле. Вырубные детали оснастки (матрицу и пуансон) изготавливают из металлокерамических твердых сплавов типа ВК-15 и ВК-20.
Усилие штамповки определяют по формуле
113
|
Pшт = Pпроб + Pприж + Pпрот + Pсъем , |
|
|
|
где Рпроб — усилие вырубки-пробивки; Рприж — усилие прижима; Рпрот — усилие проталкивания; Рсъем — |
усилие |
|||
съема детали с пуансона. |
|
|
|
|
Усилие вырубки-пробивки |
|
|
|
|
|
Pпроб = K1 L δ τср , |
|
|
|
где К1 — |
коэффициент, зависящий от состояния режущих кромок пуансона (1,1—1,3); |
L — |
периметр среза; δ — |
|
толщина материала; τср — сопротивление материала срезу, Па. |
|
|
|
|
|
Усилие прижима сосредоточивается как можно ближе к поверхности среза для исключения сколов: |
|||
|
Pприж = 4 p δ , |
|
|
|
где p — |
удельное давление прижима; при δ до 1,5 мм p = (10—15) МПа, при δ до 3 мм p = (15—20) МПа. |
|||
Усилие проталкивания детали |
|
|
|
|
|
Pпрот = K2 Pпроб h / S , |
|
|
|
где К2 — |
коэффициент, зависящий от зазора между матрицей и пуансоном (0,05—0,08); |
h — |
высота матрицы. |
|
Усилие съема детали |
|
|
|
|
|
Pсъем = K3 Pпроб , |
|
|
|
где К3 — |
коэффициент, зависящий от толщины материала и типа штампа; при δ=1,0 мм К3=0,02—0,04, |
при |
||
δ=3,0 мм К3=0,06—0,12. |
|
|
|
Пример. Для СФ-2-35-1.0 τср =90 МПа, для платы размером 100×50 мм усилие пробивки 50 кН, усилие прижима 5 кН. Суммарное усилие штамповки 50+5+3+1,5 ≈ 60 кН. Выбираем однокривошипный пресс простого действия модели К2122 с усилием 100 кН.
Исполнительные размеры матрицы Dм и пуасона Dп определяют по уравнениям:
Dм = (Dн − δ1) + δм , Dп = (Dн − δ1 − 1) − δп ,
где Dм, Dп — диаметры матрицы и пуансона соответственно; Dн — номинальный диаметр пробиваемого отвер-
стия; δ1 — допуск на размер отверстия; |
1 — зазор между матрицей и пуансоном; при δ до 1,5 мм 1 = 0,02— |
0,05 мм, при δ до 3,0 мм 1 = 0,06—0,09 |
мм; δм, δп — допуски на изготовление режущей части матрицы и пуан- |
сона, которые соответствуют 10-му квалитету точности.
Обработка плат по контуру (снятие технологического припуска) осуществляется фрезерованием на специализированных фрезерных станках, работающих по контуру, или на многошпиндельных станках с программным управлением. Такой способ отличается высокой производительностью, допускает обработку плат в пакете по 6—10 шт., дает хорошее качество кромок и точность размеров в пределах ±0,025 мм. В качестве инструмента используются алмазные дисковые фрезы или твердосплавные фрезы диаметром 3—8 мм.
Фрезерные станки с программным управлением имеют 2—5 шпинделей, вращающихся со скоростью до 60 000 об/мин, устройство для автоматической смены фрез, защитные скафандры для ограждения оператора от пыли и стружки (табл. 5.6).
Табл. 5.6. Технические характеристики фрезерных станков
Параметры |
Модель 6720П (СССР) |
Модель 7Б (Poul Dasier, США) |
|
|
|
Производительность, плат/ч |
1000 |
1800 |
Размеры поля фрезерования, мм |
500×300 |
362×620 |
Скорость резания, м/мин |
200—600 |
500—1000 |
Подача, мм на зуб фрезы |
0,05—0,16 |
0,05—0,08 |
|
|
|
114
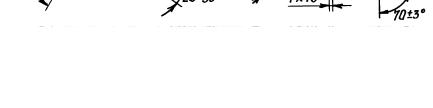
Для получения монтажных отверстий в ПП применяют пробивку на специальных штампах и сверление. Пробивку используют в тех случаях, если отверстия в дальнейшем не подвергаются металлизации. Для
улучшения качества отверстий применяют прижим заготовки с помощью прокладки из картона, которая предохраняет пуансоны от налипания на них стружки. Уменьшению усилия пробивки и повышению чистоты среза способствует предварительный подогрев заготовок до 80—100 °С со скоростью подогрева 5—8 °С/мин.
Недостатки: возможны разрывы фольги, затягивание проводников внутренних слоев МПП в отверстия, расплющивание торцов контактных площадок.
Сверление отверстий обеспечивает необходимое качество операции и ее высокую точность. Сверление в платах из гетинакса и текстолита обычно производят сверлами из быстрорежущей стали Р18. Для стеклотекстолита вследствие его высокого абразивного воздействия и низкой теплопроводности стойкость сверл из стали Р18 оказывается низкой, поэтому применяют сверла из твердых сплавов ВК6М.
Ксверлам для обработки отверстий ПП предъявляют следующие требования:
∙диаметр сверл должен быть на 0,1—0,15 мм больше диаметра металлизированного отверстия для компенсации некоторой упругости диэлектрика и толщины металлизации в отверстии;
∙ рабочая часть сверл должна иметь обратную конусность в пределах 0,02—0,03 мм для уменьшения трения
впроцессе обработки;
∙радиальное биение рабочей части относительно хвостовика не должно превышать 0,02 мм;
∙несимметричность режущих кромок относительно оси сверла должно составлять не более 0,02 мм, а осе-
вое биение кромок, проверяемое на их середине, — не более 0,01—0,02 мм; |
|
|||
∙ |
поверхности стенок и спиральных канавок должны быть полированными для предотвращения налипания |
|||
смолы в процессе сверления; |
|
|
|
|
∙ |
оптимальный угол при вершине сверл должен составлять 122—130 |
° , угол спинки зуба — 30—35 , |
угол- |
|
крутизны спирали — 25—30 ° (рис. 5.16); |
|
|
||
∙ |
оптимальная скорость резания твердосплавными сверлами составляет 25—50 м/мин; |
|
||
∙ |
стойкость сверла — 2000 — 4000 |
отверстий, после чего оно перетачивается и очищается от налипших свя- |
||
зующих веществ материала платы; твердосплавные сверла допускают 5—6 |
переточек. |
|
Рис. 5.16. Сверло для печатных плат
Диаметр сверла рассчитывается по уравнению
Dc = Dо + 0,7 ( 1 + 2 ) ,
где Dо — диаметр отверстия; 1 — предельно допустимое отклонение диаметра отверстия, (±0,05 мм); 2 — допустимое уменьшение диаметра после охлаждения заготовки (5 % от толщины платы), мм.
В качестве оборудования для сверления отверстий в ПП применяются многошпиндельные станки с программным управлением, имеющие автоматизированный привод по двум координатам. К таким станкам предъ-
115
являются следующие требования: жесткость конструкции; точность и высокая скорость позиционирования; максимальное число оборотов шпинделя; высокие скорости хода шпинделя.
Применение в сверлильных станках вместо традиционных чугунных станин гранитных обеспечивает вибропоглощение, снижает температурные деформации. Оптимальное число оборотов шпинделя лежит в диапозоне 45 000—120 000 об/мин. Скорость обратного хода достигает 25 м/мин. В станках современного типа применяют автоматическую смену сверл по программе, управление от мини-ЭВМ или микропроцессора (табл. 5.7).
Основные проблемы при сверлении отверстий в платах — повышение долговечности сверл, борьба с наволакиванием размягченной смолы на сверла и на медные кромки отверстий, препятствующим последующей металлизации отверстий. Для борьбы с этим явлением предложены: применение охлаждающих сред (воды, водяного тумана, сжатого воздуха) в зоне сверления; сверление под водой (технически трудно осуществимо); гидроабразивная очистка поверхности отверстий после сверления.
Табл. 5.7. Технические характеристики сверлильных станков с программным управлением
Параметр |
СФ-4 |
Alpha-Z |
ABL-2м |
AFIG |
|
(СССР) |
(США) |
(Schmoll, Германия) |
(Micromat, Швейцария) |
|
|
|
|
|
Число шпинделей |
4 |
5 |
2—6 |
1—2 |
Поле сверления, мм |
500×300 |
630×630 |
500×500 |
470×610 |
Частота вращения шпинделя, 103 об/мин |
60 |
90 |
60 |
90 |
Максимальное число двойных ходов в минуту |
100 |
200 |
300 |
350 |
Точность позиционирования, мм |
±0,01 |
±0,005 |
±0,005 |
±0,01 |
|
|
|
|
|
Гидроабразивная обработка с использованием шлифовальных микропорошков используется при подготовке поверхности платы к проведению технологического процесса (для зачистки поверхности фольгированного диэлектрика). Механизированную механическую подготовку проводят также крацеванием вращающимися капроновыми или нейлоновыми щетками, на которые подаются струи абразивной суспензии. Заготовка при этом перемещается с помощью конвейера со скоростью 0,5 — 1,0 м/мин. Обрабатываются заготовки с минимальны-
ми размерами 100×100 мм и максимальными 500×500 мм. Расход воздуха при полной нагрузке 13 м3/мин, потребляемая мощность 1,6 кВт.
Установка гидроабразивной зачистки поверхности фольгированного диэлектрика от оксидной пленки и отверстий от заусенцев, наволакиваемой смолы и стружки типа АРСМ 3.190.000 облегчает последующую операцию подтравливания диэлектрика, позволяет исключить ручной труд. Абразивный материал — микропорошок М40 — подается с помощью 21 форсунки под давлением сжатого воздуха. Для повышения равномерности фор-
сунки покачиваются на угол 20—40 ° с числом качаний 35 — 60 в минуту.
Для формирования переходных отверстий, вырезки пазов, разделения керамических коммутационных плат используется автоматизированная лазерная установка СТ-403 НПО "Спектр" (Беларусь), имеющая рабочее поле координатного стола 150×150 мм, погрешность позиционирования ±10 мкм. Размеры отверстий составляют
130±20 мкм, производительность 600 тыс. отверстий в час. Длина волны лазерного излучения 1,06 мкм, длительность импульса 200—1000 мкс, максимальная энергия 10 Дж.
5.8. ТЕХНОЛОГИЯ ОДНОСТОРОННИХ И ДВУСТОРОННИХ ПЕЧАТНЫХ ПЛАТ
116
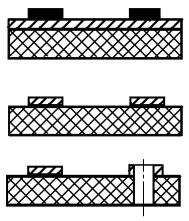
Односторонние ПП изготавливают как негативным, так и позитивным методом, используя односторонний фольгированный диэлектрик. Технологический процесс по негативному методу включает следующие операции
(рис. 5.17): |
|
|
∙ |
подготовка поверхности заготовки: механическая и химическая очистка поверхности от оксидов, остатков |
|
смазки и других загрязнений; |
|
|
∙ |
обезжиривание при 45—60 |
°С в растворах следующего состава: 30—35 г/л тринатрийфосфата (Na3PO4), |
30—35 |
г/л кальцинированной соды (Na2CO3), 3—5 г/л моющего средства "Прогресс"; |
|
∙ |
промывка в проточной холодной воде; |
|
∙ |
активирование в 20—25 %- |
м растворе HCl при температуре 20 °С в течение 0,2—0,3 мин; |
∙промывка в холодной и горячей воде;
∙сушка поверхности заготовки;
∙нанесение защитного рисунка схемы сеткографическим или фотоспособом;
∙травление незащищенных участков металлической фольги;
∙удаление резиста химическим путем;
∙пробивка или сверление отверстий; 1
∙нанесение защитного покрытия на плату.
Для облегчения монтажа навесных элементов со стороны их установки на плату наносят маркировку, для ограничения растекания припоя по печатным проводникам — защитные маски для пайки. Для защиты от влияния окружающей среды после изготовления платы покрывают защитным лаком.
2
3
Рис. 5.17. Схема технологического процесса изготовления ОПП:
1 – нанесение защитного рисунка; 2 – получение проводников; 3 – выполнение отверстий
При позитивном методе после нанесения защитного рисунка гальванически осаждают покрытие, устойчивое к травлению (сплав олово— свинец, серебро), затем сверлят отверстия и осуществляют травление рисунка. Процесс получения ПП субтрактивным химическим методом наименее трудоемок, легко механизируется, обеспечивает высокую разрешающую способность при производительности до 1000 плат/ч. Недостаток — наличие бокового подтравливания элементов проводящего рисунка. Область применения — бытовая РЭА, техника связи, блоки питания.
Двусторонние ПП с переходными электрическими соединениями изготавливают комбинированными негативным или позитивным методами. При комбинированном негативном методе экспонирование осуществляют с фотонегатива, проводящий рисунок схемы получают травлением меди с пробельных мест, сверлят отверстия, затем выполняют металлизацию отверстий электрохимическим методом (рис. 5.18).
117