
Лабораторный практикум
.pdf
где TM .K . – погрешность метода компенсации, учитывает допуск на ком-
пенсирующее звено. TM .K . T , поэтому примем TM .K . = 0,1.
Величина необходимой компенсации координаты середины поля рассея-
ния погрешности замыкающего звена: 0 К 0 0 ,
где – координата середины поля рассеяния погрешности замыкающего звена при расширенных допусках на составляющие звенья, определяется по формуле:
n |
|
k |
|
|
|
|
|
|
|
0 0 j 0q 0 ( 0, 2 2 0 0, 05 2) 0,3 |
|||||||||
j 1 |
|
q 1 |
|
|
мм. |
||||
Знак “+” при расчете 0 К |
ставится, если компенсатор является увели- |
||||||||
чивающим звеном, а знак “–”, если компенсатор – уменьшающее звено. |
|||||||||
|
|
0К 0,1 0,3 0, 2 |
мм. |
||||||
|
|
|
|
|
|
|
|
|
|
Вычислим предельные значения величины необходимой компенсации раз- |
|||||||||
мера замыкающего звена: |
|
|
|
|
|
|
|
|
|
|
|
|
|
|
TK |
|
0, 2 0, 49 0, 29 0,3 |
||
BK |
0K |
|
|
||||||
|
|
2 |
|
|
мм; |
||||
|
|
|
|
|
|
||||
|
|
|
|
|
TK |
|
0, 2 0, 49 0, 69 0, 7 |
||
HK |
0K |
|
|
||||||
|
|
2 |
|
|
мм. |
||||
|
|
|
|
|
|
При расчетах необходимо исключить возможность случая, когда HK 0. Для этого нужно изменить либо номинальный размер Аi, либо координату сере-
дины поля допуска любого составляющего звена на величину HK .
Для увеличивающих звеньев: |
A |
A |
|
|
; |
|
|
|
|
|
|
HK . |
|||||||
j |
j |
|
|
HK |
|
|
|
0 j |
|
|
|
0 j |
|
|
|||||
Для уменьшающих звеньев: |
A |
A |
HK ; |
|
|
|
|
|
|
|
|
|
|
HK . |
|||||
q |
q |
|
|
|
|
0q |
|
|
0q |
|
|
||||||||
Толщина одной прокладки: S = T =0,1 мм |
|
|
|
|
|
|
|
|
|
|
|
|
|||||||
|
|
|
Z |
TK |
|
|
|
0,98 |
|
10 |
|||||||||
|
|
|
|
|
0,1 |
|
|||||||||||||
Необходимое количество прокладок: |
|
|
|
|
S |
|
|
|
|
|
|
шт. |
|||||||
|
|
|
|
|
|
|
|
|
|
|
|
|
|
|
Если число прокладок окажется большим, то их делают разной толщины:
S |
|
|
TK BK |
|
|
n |
|
|
|||
Si 2 Si 1 , где S1 T . Толщина последней прокладки: |
2 |
. |
|||
|
41

Лабораторная работа № 6
ОПРЕДЕЛЕНИЕ ЖЕСТКОСТИ ТОКАРНОГО СТАНКА МЕТОДОМ СТАТИЧЕСКОГО НАГРУЖЕНИЯ
Цель работы: освоение методики определения жесткости токарного станка методом статического нагружения и обработки результатов эксперимента методом наименьших квадратов.
Краткие теоретические сведения
Упругие деформации технологической системы, возникающие под воздействием сил резания, закрепления, а также инерционных сил, являются одним из существенных факторов, определяющих точность обработки. Погрешности, обусловленные ими, в зависимости от условий, могут составлять 20–80 % суммарной погрешности обработки.
В связи с этим одной из важнейших характеристик физического состояния технологической системы является жесткость.
Под жесткостью упругой системы понимают ее способность оказывать сопротивление перемещению выбранной точки в направлении действия силы, порождающей это перемещение.
Относительные перемещения выбранных точек двух деталей упругой системы представляют собой сумму перемещений, происходящих из-за наличия зазоров в стыках, контактных и собственных деформаций и поворотов деталей. Поэтому жесткость технологической системы является переменной величиной, зависящей от изменения ряда характеристик:
состояния станка, степени его износа; конструктивных особенностей; материала деталей технологической системы; вязкости смазки и ее количества в стыках;
погрешности формы и шероховатости сопряженных поверхностей; величины и направления предварительных натягов; температуры.
Определение жесткости или зависимости "нагрузка – перемещение" производится при строгой регламентации всех факторов, оказывающих влияние на изменение этой зависимости. Условия определения жесткости (в частности положение узлов и деталей токарных станков и точек приложения сил) указаны в ГОСТ 7895–56.
Наиболее существенное влияние на достигаемый размер обрабатываемой детали оказывают перемещения элементов технологической системы в направлении, нормальном к обрабатываемой поверхности. Эти перемещения обусловлены в основном действием соответствующей составляющей силы резания.
Поэтому жесткость технологической системы определяется как отношение составляющей силы резания, направленной по нормали к обрабатываемой
42
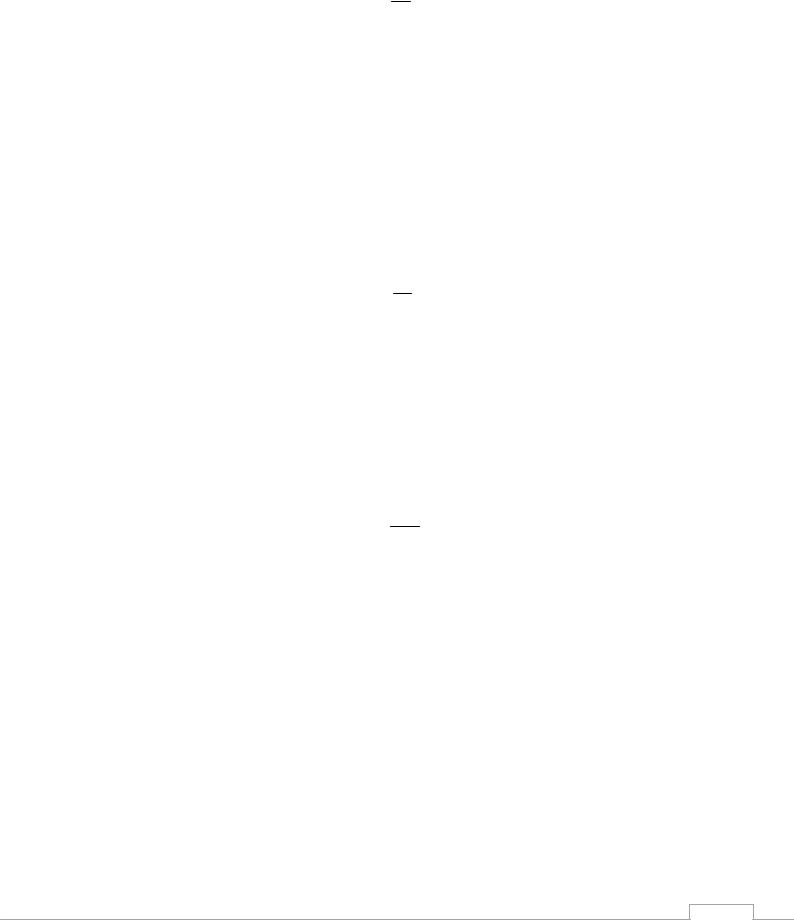
поверхности Py , к смещению лезвия инструмента y относительно детали, отсчитываемому в том же направлении (кН/м, Н/мм):
|
P |
|
j |
yy . |
(6.1) |
Для точных расчетов жесткости, с целью учета воздействия составляющих силы резания Рх и Рz, введено понятие эквивалентной силы Рэ:
Рэ Рz Py Px |
(6.2) |
где , , – коэффициенты, показывающие влияние каждой из составля-
ющих силы резания на эквивалентную силу.
Под эквивалентной силой понимают силу, направленную при токарной обработке вдоль резца по нормали к обрабатываемой поверхности. Момент эквивалентной силы равен сумме моментов всех действующих сил. Поэтому в [3] предложено под жесткостью технологической системы понимать отношение эквивалентной силы Рэ к смещению y в направлении действия этой силы (по нормали к обрабатываемой поверхности):
j |
Pэ |
|
y . |
(6.3) |
При экспериментальном определении жесткости учитывается действие составляющих Рх и Рz. Нагружение системы производят силой, совпадающей по направлению с суммарной силой резания, хотя приближенный расчет жесткости ведут только по составляющей Ру. Упругие свойства технологической системы обычно невозможно определить одним коэффициентом жесткости, так как зависимость между силой и отжатием (упругая характеристика) – нелинейная. Но при расчетах точности обычно нелинейную характеристику в рабочем диапазоне резания заменяют линейной и принимают:
j Py , (6.4)
y
где Py – приращение составляющей силы резания Ру; y – действующее
приращение перемещения в направлении Ру.
В технологических расчетах часто пользуются величиной податливости, характеризующей способность технологической системы изменять относительное положение выбранных точек двух ее деталей под влиянием приложенной силы в направлении ее действия. Податливость является величиной, обратной жесткости:
|
1 |
|
y |
|
|
|
|
. |
(6.5) |
||
j |
P |
||||
|
|
|
y |
|
Существует несколько методов определения жесткости металлорежущих станков или их отдельных узлов:
1)статический (испытания на неработающем станке);
2)производственный (испытания в процессе обработки заготовки);
43

3) динамический (испытания в процессе колебаний).
Сущность статического метода заключается в том, что узлы станка с помощью специальных приспособлений и динамометра нагружают силой, воспроизводящей действие силы резания, и одновременно измеряют перемещение отдельных узлов станка. Сила прикладывается в направлении действия одной (Ру), двух (Ру, Рz) и трех (Рх, Ру, Рz) составляющих силы резания. Перемещение узлов станка измеряются в направлении нормальном к обрабатываемой поверхности, так как эти перемещения имеют наибольшее значение в формировании погрешностей обработки, обусловленных деформациями технологической системы.
По принятой терминологии, при нагружении узлов станка силой в направлении одной составляющей силы резания Ру определяется коэффициент жесткости Y (а не жесткость) и соответственно коэффициент податливости W, а при приложении двух или трех составляющих силы резания определяется жесткость j и податливость .
При определении жесткости станков на заводах (статическим методом) обычно узлы станка нагружают максимальной эксплуатационной нагрузкой (в направлении Ру) и фиксируют вызванные ею перемещения узлов станка.
Жесткость узла станка в этом случае определяется по формуле
j |
Py max |
, |
(6.6) |
|
|||
|
ymax |
||
|
|
|
где Ру max – максимальная эксплуатационная величина составляющей нагрузки, действующей в направлении, нормальном к обработанной поверхности, кН; ymax – максимальное значение перемещения узла станка в том же направлении, м.
При лабораторных испытаниях узлы станка нагружают ступенчато возрастающей нагрузкой и одновременно регистрируют соответствующее приращение перемещения. Аналогично производят разгрузку.
По результатам испытания строят графики "нагрузка – перемещение" (рис. 6.1). Как правило, нагрузочная ветвь графика 1 не совпадает с разгрузочной ветвью 2; они образуют петлю гистерезиса. Площадь петли гистерезиса, образованной кривыми, характеризует работу, затраченную на преодоление силы трения в стыках, контактные деформации и силы собственного веса деталей. Полученная характеристика позволяет достаточно объективно оценить качество изготовления данного узла и его состояние. Так, при высокой точности изготовления узла ветви 1, 2 характеристики располагаются ближе одна к другой, чем при низкой. Несовпадение ветвей 1, 2 на оси X и нелинейный характер кривых говорит о том, что узлы станков являются не вполне упругими звеньями технологической системы. Нагрузочная ветвь графика "нагрузка – перемещение" может иметь один или несколько резко выраженных перегибов. Это говорит о том, что жесткость данного узла имеет различные значения в разных диапазонах нагрузки. В этом случае жесткость узла определяют на отдельных участках (до точек перегиба) и получают несколько значений жесткости для различных диапазонов нагрузки.
Для определения средней жесткости узла нагрузочную ветвь графика спрямляют, т. е. экспериментальную ломаную линию аппроксимируют линейной зависимостью вида
44
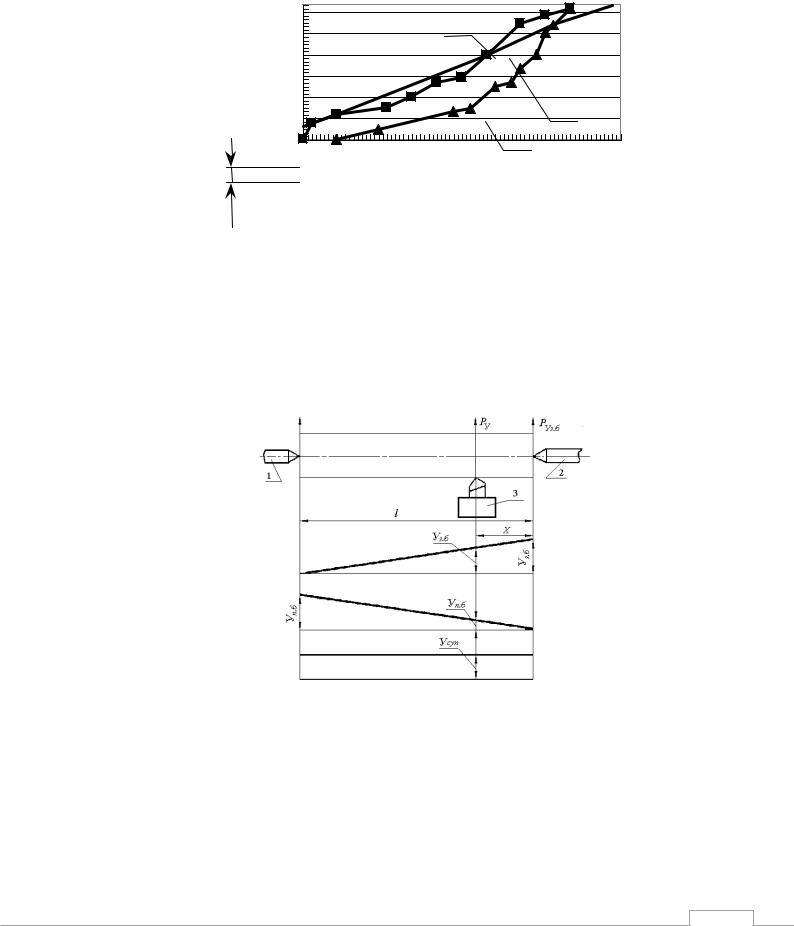
|
|
|
Py A0 A1 y , |
(6.7) |
где А0 |
и А1 – постоянные коэффициенты, подлежащие определению. |
|||
|
|
Р, Н |
|
|
|
|
3600 |
|
1 |
|
|
3000 |
|
|
|
|
|
|
|
|
|
2400 |
|
|
|
|
1800 |
|
|
|
|
1200 |
|
3 |
|
|
600 |
|
|
|
|
|
2 |
|
|
у0 |
0 |
|
|
|
|
|
|
|
|
Р |
0 |
0,05 0,1 0,15 |
0,2 0,25 0,3 0,35у , м |
|
|
|||
|
|
Рис. 6.1. График “нагрузка – перемещение” |
Наиболее точным методом оценки коэффициентов А0 и А1 является метод наименьших квадратов. Получив значения жесткости отдельных узлов, определяют суммарную жесткость станка, исходя из схемы действия сил резания на узлы станка и суммируя перемещения отдельных узлов, приведенные к лезвию режущего инструмента (зоне обработки). Наиболее общий случай определения жесткости станка имеет место, когда жесткость его узлов, а следовательно, и станка в целом зависит от координаты перемещения инструмента (рис. 6.2).
Рис. 6.2. Схема нагрузки и упругих перемещений узлов токарного станка: 1 – передняя бабка; 2 – задняя бабка; 3 – суппорт
На токарном станке суммарное перемещение инструмента относительно обрабатываемой детали, установленной в центрах, складывается из перемещений передней бабки, суппорта и задней бабки (рис. 6.2).
При изменении координаты зоны резания, т.е. при перемещении точки приложения нагрузки по длине обрабатываемой детали, величина суммарной податливости и жесткости станка имеет вид:
45
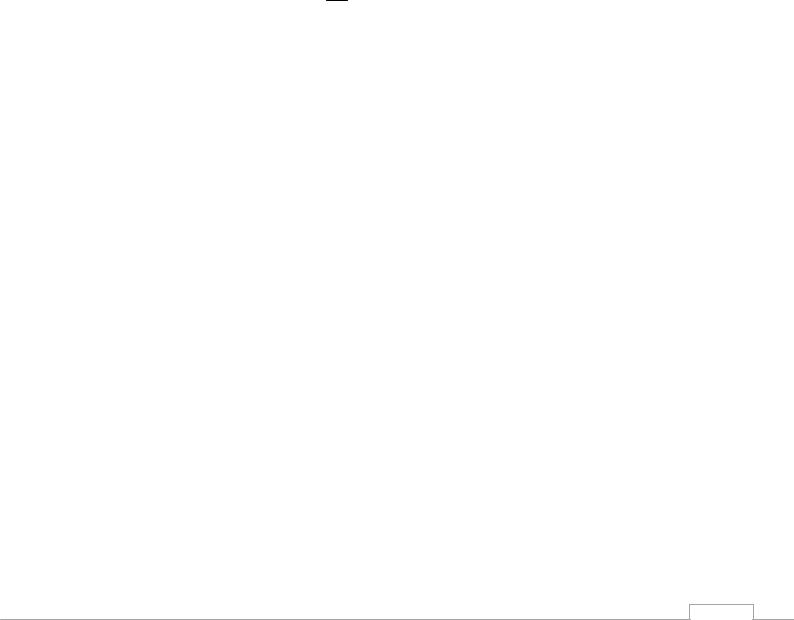
где
усуп
|
|
|
|
|
у |
у у |
у |
|
, |
|
|
|
|
|
|
|
||||||
|
|
|
|
|
ст |
суп |
|
з.б. |
|
п.б. |
|
|
|
|
|
|
|
|
||||
|
е х |
|
|
|
|
е х |
|
|
|
|
|
|
|
Р |
|
|
|
|
|
|
||
|
|
|
|
|
|
|
|
|
у |
|
|
|
|
|
|
Ру |
||||||
|
е |
|
; |
|
уп.б. |
|
е |
; |
|
|
|
|
|
|
|
|
з.б. ; |
|
уп.б. |
|||
уз.б. уз.б. |
|
|
уп.б. |
|
|
|
з.б. |
у |
|
|
||||||||||||
|
|
|
|
|
|
|
|
|
|
|
|
|
|
|
|
з.б. |
|
|
|
|
п.б. |
|
Ру суп ; Ру |
|
Ру |
|
е х |
; |
Ру |
Ру |
х |
. |
|
|
|
|
|
|
|
|
|
||||
|
|
|
|
|
|
|
|
|
|
|
|
|||||||||||
|
|
з.б. |
|
е |
|
п.б. |
|
|
е |
|
|
|
|
|
|
|
|
|
||||
|
|
|
|
|
|
|
|
|
|
|
|
|
|
|
|
|
|
|
||||
Подставляя полученные значения в формулу (6.8), получаем |
|
|||||||||||||||||||||
|
|
|
|
|
|
|
|
|
|
|
е х 2 |
|
|
|
х 2 |
|
||||||
|
уст |
Ру суп Ру з.б. |
|
|
|
|
|
Ру |
п.б. |
|
|
. |
|
|||||||||
|
|
е |
|
|
||||||||||||||||||
|
|
|
|
|
|
|
|
|
|
|
|
|
|
|
|
|
е |
|
(6.8)
п.б. ;
(6.9)
Подставляя вместо уст его значение и производя сокращения, получа-
ем выражения для определения податливости и жесткости токарного станка в зависимости от координаты обработки:
ст
1
jст
|
|
|
|
|
|
|
|
е х 2 |
|
|
|
||
суп |
з.б. |
|
|
|
|
|
п.б. |
||||||
|
е |
||||||||||||
|
|
|
|
|
|
|
|
|
|
|
|
||
|
1 |
|
1 |
|
|
|
е х 2 |
|
1 |
|
|||
|
|
|
|
|
|
|
|
|
|
||||
jсуп |
jз.б. |
|
|
|
jп.б. |
||||||||
|
|
|
|
|
е |
|
|
|
|
х |
2 |
|
|
|||
|
|
|
|
|
|
|
|
|
|
|
|
|
|
||||
|
|
е |
|
|
|
|||
|
х |
2 |
|
(6.10) |
||||
|
|
|
|
|||||
|
|
|
|
|
|
|
|
|
|
|
|
|
|
||||
|
|
|
|
|
|
|||
|
е |
|
|
|
|
|||
|
|
|
|
|
|
|
|
Чтобы сравнить токарные станки по жесткости, иногда определяют среднюю жесткость (или податливость) станка, то есть жесткость зоны обработки (положение резца в середине обрабатываемой детали) х l2 .
В этом случае
ст |
суп |
|
1 |
з.б. |
п.б. |
|
|
|||||||
|
|
|
|
|
||||||||||
4 |
|
|||||||||||||
|
|
|
|
|
|
|
|
|
|
|
(6.11) |
|||
1 |
1 |
|
|
1 |
|
|
1 |
1 |
|
|
||||
|
|
|
|
|
||||||||||
|
|
|
|
|
|
|
|
|
|
|
|
|
|
|
j |
j |
4 |
|
j |
j |
|
|
|||||||
ст |
|
суп |
|
|
|
|
|
з.б. |
|
п.б. |
|
Порядок выполнения работы
1.Установить по линии центров и закрепить в резцедержателе станка поджимной винт 3 с шаровым наконечником (рис. 6.3)
2.Установить в центрах станка вал 5. Расстояние l от корпуса задней бабки до торца вала, установленного в центрах станка, должно соответствовать величине, указанной в табл. 6.1.
3.Установить между валом и шаровой поверхностью державки динамометр 2 так, чтобы передаваемая на узлы нагрузка совпадала с направлением действия радиальной составляющей силы резания Ру.
4.Установить индикаторы 1 так, чтобы их измерительные наконечники соответственно касались (рис. 6.3) центра передней бабки, торца резцедержателя и центра задней бабки.
Таблица 6.1
46
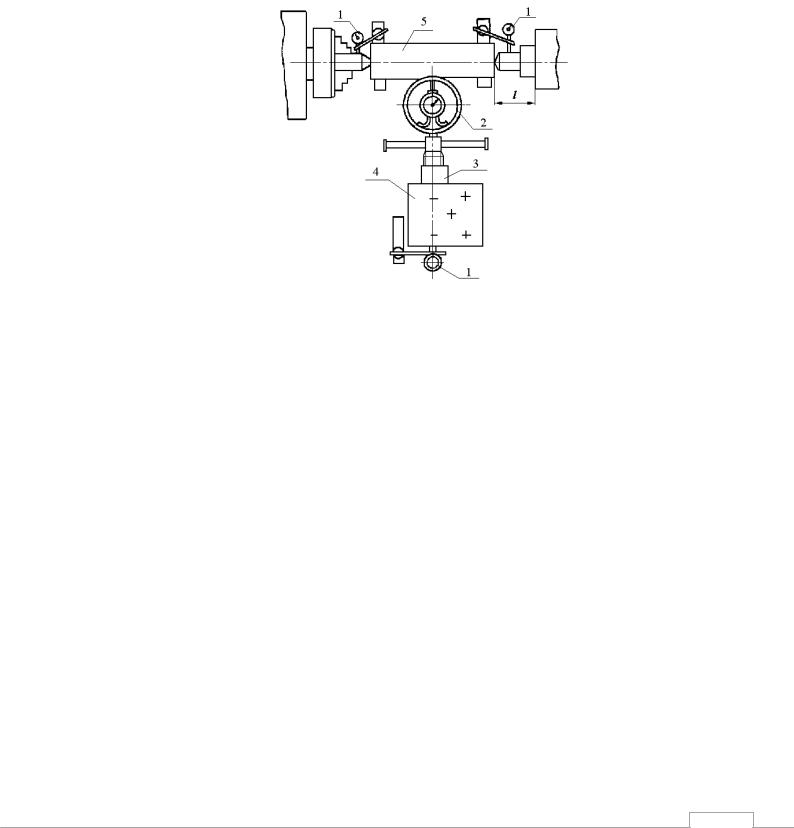
Наибольший |
диаметр |
|
|
|
|
|
|
|
|
|
обрабатываемого |
из- |
100 |
125 |
160 |
200 |
250 |
320 |
400 |
500 |
|
делия, мм |
|
|
|
|
|
|
|
|
|
|
Расстояние |
от |
торца |
|
|
|
|
|
|
|
|
корпуса задней |
бабки |
50 |
60 |
70 |
80 |
95 |
115 |
140 |
170 |
|
до торца вала, мм |
|
|
|
|
|
|
|
|
5. Выбрать предельную нагрузку (табл. 6.2) для чего предварительно нагрузить технологическую систему 1–2 раза до предельной нагрузки, а затем снять ее.
Рис. 6.3. Схема установки для измерения жёсткости токарного станка методом статического нагружения
Таблица 6.2
Наибольший диаметр |
|
|
|
|
|
|
|
|
обрабатываемого изде- |
100 |
125 |
160 |
200 |
250 |
320 |
400 |
500 |
лия, мм |
|
|
|
|
|
|
|
|
Предельная нагрузка, Н |
300 |
500 |
700 |
1000 |
1400 |
2000 |
2800 |
4000 |
6.Установить все индикаторы на нуль с предварительным натягом (натяг индикаторов должен быть 0,5–1 мм).
7.Ступенчато, через 2–3 деления индикатора динамометра нагружать систему до предельной нагрузки при помощи поджимного винта 3, фиксируя деформации узлов станка.
8.В обратной последовательности произвести полную разгрузку станка.
9.Результаты опытов записать в табл. 6.3.
|
|
|
|
|
Таблица 6.3 |
|
|
|
|
|
|
№ |
Показа- |
Нагрузка по |
Деформация |
Деформация |
Деформация |
п/п |
ния ин- |
динамометру, |
передней баб- |
суппорта, |
задней бабки, |
|
дикато- |
Н |
ки, м |
м |
м |
47

|
ра дина- |
Наг- |
Раз- |
Наг- |
Раз- |
Наг- |
Раз- |
Наг- |
Раз- |
|
мометра, |
рузка |
грузка |
рузка |
грузка |
рузка |
груз- |
рузка |
грузка |
|
мм |
|
|
|
|
|
ка |
|
|
1 |
|
|
|
|
|
|
|
|
|
2 |
|
|
|
|
|
|
|
|
|
… |
|
|
|
|
|
|
|
|
|
10. Построить диаграммы "нагрузка – перемещение" для передней бабки, суппорта и задней бабки (рис. 6.1).
11. Пользуясь построенными диаграммами, по формуле (6.6) определить жесткость передней бабки, суппорта и задней бабки.
12. Подсчитать суммарную жесткость станка при положении резца в середине детали, пользуясь формулой (6.11).
Содержание отчета
1.Наименование работы.
2.Цель работы.
3.Характеристика применяемого оборудования и измерительных приборов.
4.Схема установки для определения жёсткости токарного станка.
5.Результаты опытов (табл. 6.3).
6.Диаграммы "нагрузка – перемещение" для передней бабки, суппорта и задней бабки.
7.Расчет жесткости передней бабки, суппорта и задней бабки.
8.Расчет суммарной жесткости станка.
9.Пользуясь нормами жесткости на токарные станки общего назначения, сравнить полученные значения жесткости отдельных узлов станка с табличными
(табл. 6.4)
Таблица 6.4
Высота центров, |
Жесткость, Н/мм |
|
|
мм |
передней бабки |
задней бабки |
суппорта |
200 |
5000 |
3300 |
4000 |
300 |
7600 |
5000 |
5900 |
400 |
10000 |
6200 |
8300 |
Примечание. Данные взяты из ГОСТ 18097–72.
10. Для математической обработки экспериментальных данных (методом
наименьших квадратов) и нахождения параметров функции |
P P |
j y , |
|
|
y |
y0 |
|
где Py0 – определяется на основании экспериментальных данных (рис. 6.1). Со-
ставить систему нормальных уравнений, коэффициенты которых для удобства расчета свести в таблицу 6.5.
Таблица 6.5
48

у |
у2 |
Py |
Py |
yi |
||
|
|
|
i |
i |
|
|
у1 |
y |
2 |
P |
Py |
y1 |
|
|
1 |
y |
1 |
|
||
… |
|
|
1 |
|
|
|
… |
… |
… |
||||
yn |
||||||
y |
2 |
P |
P |
y |
||
|
n |
yn |
n |
|||
n |
|
yn |
|
|
||
|
|
|
n |
|
||
yi |
n |
|
n |
|
||
|
Pyi yi |
|||||
yi2 |
Pyi |
|||||
i 1 |
i 1 |
|
i 1 |
i 1 |
|
|
|
|
|
||||
|
|
|
|
Примечание. n – количество опытных точек нагрузочной ветви
Методика оценки параметров функции Py Py0 j y приведена на стр. 50. Решая систему нормальных уравнений (6.12), определить жесткость узла j:
n Py |
|
n |
n |
|
|
|
j yi Py |
|
|||||
|
|
0 |
|
|
i |
|
|
|
|
i 1 |
i 1 |
|
|
|
|
n |
n |
|
n |
(6.12) |
|
yi |
|
2 |
Pyi |
yi |
|
Py0 |
j yi |
|||||
|
|
i 1 |
i 1 |
|
i 1 |
|
Значение нагрузки Py0 найти для прямой y f (Py ) (рис. 6.1).
11. Выводы. Объяснить результаты сопоставления полученных значений жесткости с табличными.
Контрольные вопросы
1.Определение понятия жесткости технологической системы.
2.Факторы, определяющие жесткость технологической системы.
3.Формула для определения жесткости узла станка по диаграмме “нагруз- ка–перемещение”.
4.Понятие эквивалентной силы.
5.Жесткость и коэффициент жесткости,
6.Методы определения жесткости технологической системы.
7.Схема упругих перемещений токарного станка при обработке вала в
центрах.
8.Формулы для расчета средней жесткости станка в зависимости от координаты положения резца.
9.Податливость технологической системы, ее определение.
10.Пути повышения жесткости технологической системы.
11.Пути снижения погрешностей, вызываемых упругими деформациями технологической системы.
Литература [1, 3, 5, 9] П р и м е р р а с ч е т а
Определение параметров линейной функции
При обработке экспериментальных данных, полученных, во время опыта, необходимо найти функцию y f (х, z ...) , значение которой возможно ближе соответствовало бы результатам эксперимента. Общий вид функции
49

обычно известен и поэтому задача математической обработки экспериментальных данных сводится к определению параметров этой функции, полученных на основании экспериментальных данных.
Для обработки экспериментальных данных применяются различные методы: графический, интерполяционных формул, средних значений, наименьших квадратов. Из перечисленных наиболее точным является метод наименьших квадратов. При вычислении этим методом необходимо, чтобы точки y
располагались по обе стороны от кривой функции y f (х) , но как можно ближе к последней, чтобы сумма квадратов отклонений i , измеренных значений yi от функции y f (х) была минимальной
i2 min . |
(1) |
Линейная функция |
|
y A0 A1 x , |
(2) |
где A0 , A1 – искомые коэффициенты, которые аппроксимируют многие экс-
периментальные зависимости, в частности, линейной зависимостью аппроксимируется нагрузочная ветвь графика "нагрузка-перемещение" при определении жесткости узлов металлорежущих станков. Обработка экспериментальных данных в этом случае производится следующим образом:
В формулу (2) подставляют все найденные экспериментальные значения xi , yi и получают систему
A0 A1 x1 y1 1 , A0 A1 x2 y2 2 ,
..............................
A0 A1 xn yn n ,
где n – количество экспериментальных точек. Из условия (1) следует:
A0 A1 x1 y12 A0 A1 x2 y22 ... A0 A1 xn yn2 min .
Так как переменными величинами в этом выражении являются коэффициенты A0 , A1 , то для них необходимо найти такие значения, при которых
указанное выражение имеет минимум. Для этого определяют частные производные по коэффициентам A0 , A1 и приравнивают их нулю. Обозначая через Е левую часть приведенного выше выражения, находим частные производные:
50