
Лабораторный практикум
.pdf
E |
2 A |
A x |
y |
2 A |
A x |
y |
|
... 2 A |
A x |
y |
|
; |
||
|
|
2 |
n |
|||||||||||
0 |
1 1 |
1 |
0 |
1 2 |
|
0 |
1 |
n |
|
|
||||
A0 |
|
|
|
|
|
|
|
|
|
|
|
|
||
E |
2 A0 |
A1 x1 |
y1 x1 2 A0 A1 x2 y2 x2 ... 2 A0 |
A1 xn yn xn . |
||||||||||
|
||||||||||||||
A1 |
|
|
|
|
|
|
|
|
|
|
|
|
Приравнивая полученные выражения к нулю и проведя преобразования, получаем:
nA0 (x1 x2 ... xn ) A1 y1 y2 ... yn ,
или
(x1 x2 ... xn ) A0 (x12 x22 ... xn2 ) A1 x1 y1 x2 y2 ... xn yn ,
|
n |
n |
|
n A0 A1 xi |
yi ; |
|
|
|
i 1 |
i 1 |
(3) |
n |
n |
n |
|
A0 xi |
A1 xi2 xi yi . |
|
|
i 1 |
i 1 |
i 1 |
|
Линейные уравнения (3) называют нормальными уравнениями. Число таких уравнений равно количеству определяемых параметров (коэффициентов А).
Решая систему линейных уравнений (3), определяют параметры A0 , A1 , т. е.
положение аппроксимирующей прямой на плоскости ХУ. На экспериментальном графике прямую удобно проводить по двум наиболее удаленным точкам, найденным
из основного уравнения с экспериментально определенными параметрами A0 , A1 .
Например, для графика "нагрузка – перемещение" суппорта токарного станка (рис. 6.1) нагрузочная ветвь графика может быть аппроксимирована функцией вида
y A0 A1 x или в принятых на графике обозначениях зависимости Py A0 A1 y . Нормальные уравнения будут иметь вид
|
10 |
10 |
|
|
|
|
10 A0 A1 yi |
Pyi |
; |
|
|
|
|
|
i 1 |
i 1 |
|
|
|
|
10 A0 |
A1 1754 1792; |
|
|
|
|
|
10 |
10 |
10 |
|
|
|
|
A0 yi A1 yi2 yi Pyi ; |
|
|
|
|||
i 1 |
i 1 |
i 1 |
|
|
|
|
A0 1754 A1 413792 412144. |
|
|
|
|||
Решая полученные уравнения, находим |
A P 178 |
(Н); |
A |
=0,92, откуда |
||
|
|
0 |
0 |
|
1 |
|
уравнение аппроксимирующей прямой будет
Py 17,8 0,92 y .
На основании этого уравнения на рис. 6.1 проводим прямую 3, аппроксимирующую нагрузочную ветвь 1 графика "нагрузка – перемещение", 2– разгрузочную ветвь.
51

Лабораторная работа № 7
ОПРЕДЕЛЕНИЕ ЖЕСТКОСТИ ТОКАРНОГО СТАНКА ПРОИЗВОДСТВЕННЫМ МЕТОДОМ
Цель работы: освоение методики определения жесткости токарного станка производственным методом.
Краткие теоретические сведения
Статическая жесткость не совпадает с действительной жесткостью станка в процессе работы (см. лаб. раб. № 6).
Используя разработанные методики, можно вычислить упругие деформации и жесткость работающего станка под нагрузкой при определенном режиме работы. Одна из таких методик, названная производственным методом испытания жесткости станков, основана на явлении копирования в процессе обработки исходных размеров и форм заготовки. При использовании производственного метода жесткость (Н/м) определяется как отношение приращения силы Ру к вызванному им приращению упругих перемещений в
технологической системе у :
jст |
|
Ру |
. |
(7.1) |
|
||||
|
|
у |
|
Приращение силы резания Ру задается путем изменения глубины ре-
зания при обработке напроход ступенчатой заготовки (рис.1). Увеличение глубины резания
t tmax tmin |
|
Dзаг |
|
min |
Dзаг min |
, |
(7.2) |
|
2 |
|
1 |
||||
|
|
|
|
|
2 |
|
|
где Dзаг2 min , Dзаг1 min – диаметры ступеней исходной заготовки.
Радиальная составляющая силы резания Py может быть выражена формулой
Py 10Cp t0,9 S 0,6v 0,3 K p , |
(7.3) |
где Cp – коэффициент, зависящий от механических свойств обрабатываемо-
го материала и угла резания (при наружном продольном точении заготовок из конструкционной стали резцами, у которых материал рабочей части –
твердый сплав Cp = 243; быстрорежущая сталь Cp = 125); t – глубина реза-
ния; S – подача, v – скорость |
резания; |
K p – поправочный |
коэффициент, |
|||||||
определяется по формуле |
|
|
|
|
|
|
|
|
|
|
K |
p |
K |
p |
K |
p |
K |
p |
K |
rp |
(7.4) |
|
|
|
|
|
|
52
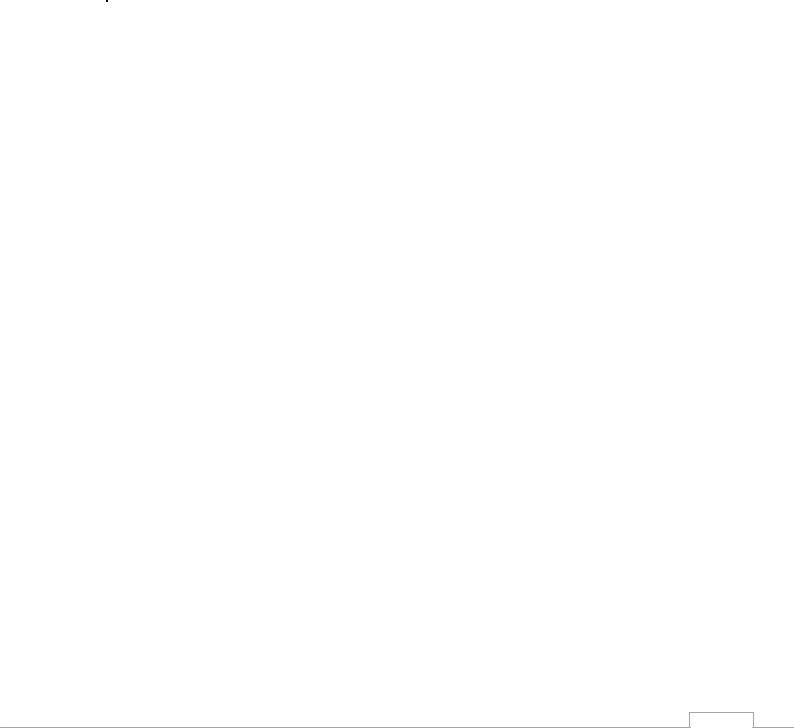
где К р – коэффициент, зависящий от угла в плане ; К р – коэффициент, зависящий от главного переднего угла ; К р – коэффициент, зависящий от угла
наклона кромки ; |
Кrp – коэффициент, зависящий от радиуса при вершине r . |
|||||||
Значения коэффициентов приведены в табл. 7.1. |
|
|
|
|||||
Таблица 7.1 |
|
|
|
|
|
|
|
|
|
|
|
|
|
|
|
||
|
Параметр |
|
Материал режу- |
Поправочный коэффициент |
||||
|
|
|
|
|
Обозна- |
Величина коэф- |
||
Наименование |
|
Величина |
щей части кромки |
|||||
|
чение |
фициента |
||||||
|
|
|
|
|
|
|||
|
|
|
|
30 |
|
|
|
1,30 |
|
|
|
|
45 |
Твердый сплав |
|
|
1,00 |
|
|
|
|
60 |
|
|
0,77 |
|
|
|
|
|
|
|
|
||
Главный |
угол |
в |
|
90 |
|
К р |
0,50 |
|
плане |
|
|
|
30 |
|
1,63 |
||
|
|
|
|
|
|
|||
|
|
|
|
45 |
Быстрорежущая |
|
|
1,00 |
|
|
|
|
60 |
сталь |
|
|
0,71 |
|
|
|
|
90 |
|
|
|
0,44 |
|
|
|
|
-15 |
|
|
|
2,0 |
Передний угол |
|
0 |
Твердый сплав |
|
|
1,4 |
||
|
10 |
|
К |
р |
1,0 |
|||
|
|
|
|
12–15 |
Быстрорежущая |
|
|
1,6 |
|
|
|
|
20–25 |
сталь |
|
|
1,0 |
|
|
|
|
-5 |
|
|
|
0,75 |
Угол |
наклона |
|
0 |
Твердый сплав |
К р |
1,0 |
||
кромки |
|
|
|
5 |
1,25 |
|||
|
|
|
|
|
|
|||
|
|
|
|
15 |
|
|
|
1,7 |
|
|
|
|
0,5 |
|
|
|
0,66 |
Радиус при вер- |
|
1,0 |
Быстрорежущая |
|
|
0,82 |
||
|
2,0 |
Кrp |
1,0 |
|||||
шине r |
|
|
|
сталь |
||||
|
|
|
3,0 |
|
|
1,14 |
||
|
|
|
|
|
|
|
||
|
|
|
|
4,0 |
|
|
|
1,33 |
Приращение силы резания Py , вызванное изменением глубины резания от tmin до tmax , находят по формуле:
Ру 10 Ср S 0,6 v 0,3 К р tmax0,9 tmin0,9 . (7.5)
Упругие деформации узлов станка Уст в данном случае складываются из перемещений передней бабки Уп.б. , задней бабки Уз.б. и суппорта Усуп :
Уст Уп.б. Уз.б. Усуп. . |
(7.6) |
Собственной деформацией детали можно пренебречь в связи с большой её жесткостью.
53
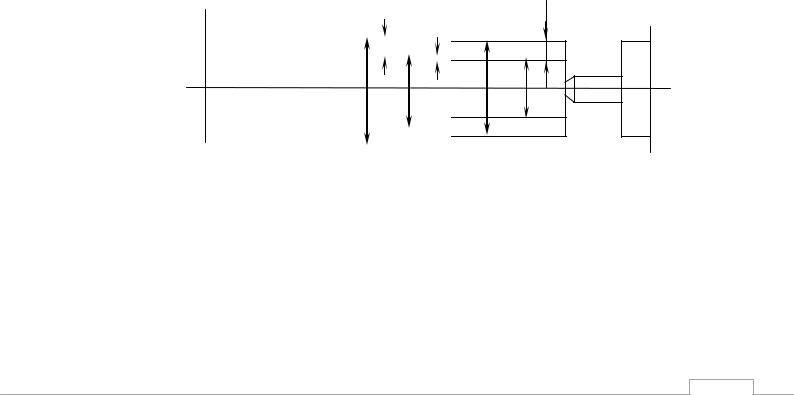
С увеличением силы резания Ру при изменении глубины резания от tmin до tmax суммарная величина упругих деформаций узлов станка также изменяется от
Уст min до Уст max .
Приращение упругих деформаций Уст Уст max Уст min равно полуразности диаметров детали после обработки d 2 и d 1 , полученных вследствие явления копирования на участках заготовки с глубиной резания tmax и tmin :
|
|
|
Уст |
d 2 |
d 1 |
, |
|
|
|
||||||||||
|
|
|
|
2 |
|
|
|
|
|||||||||||
|
|
|
|
|
|
|
|
|
|
|
|
|
|
|
|
|
|
||
|
|
|
где Уст |
д |
dд 2 dд1 |
. |
|
||||||||||||
|
|
|
|
|
|||||||||||||||
|
|
|
|
|
|
|
|
|
|
|
|
|
|
2 |
|
|
|
||
Подставляя значения Ру |
и Уст |
в формулу (7.1), получаем: |
|||||||||||||||||
|
P |
|
20C |
|
S |
0,6 v 0,3 |
K |
|
|
(t |
0,9 |
t0,9 ) |
|||||||
jст |
y |
|
|
p |
|
|
|
|
|
|
p |
|
max |
min |
. |
||||
y |
|
|
|
|
d 2 d 1 |
|
|
|
|
|
|||||||||
|
|
|
|
|
|
|
|
|
|
|
|
|
|||||||
|
|
|
|
|
|
Отношение |
|
|
|
||||||||||
|
|
|
|
t |
|
2(t0,9 |
t0,9 |
) |
|
|
|
|
|||||||
|
|
|
|
max |
|
|
min |
|
|
|
|
|
|
||||||
|
|
|
|
|
|
|
|
|
|
|
|
|
|
|
|||||
|
|
|
|
|
|
|
d 2 |
d 1 |
|
|
|
|
|
|
называется уточнением.
Подставляя ε в формулу (7.8), получаем окончательно: jст 10 Cp S 0,6 v 0,3 K p
Порядок выполнения работы
(7.7)
(7.8)
(7.9)
(7.10)
1. Установить ступенчатую заготовку на станке, как показано на рис 7.1. Перепад ступеней заготовки для токарных станков с наибольшим диаметром обрабатываемого изделия 160–320 мм должен составлять 4–6 мм.
|
|
|
max |
|
|
||
|
|
|
У |
|
|
||
|
|
|
|
с |
|
|
|
|
|
|
t |
|
|
|
|
|
|
|
|
|
|
|
|
|
|
|
|
|
|
|
|
|
|
|
|
|
|
|
|
|
|
|
заг 2 |
|
|
|
|
|
|
|
|
|
|
|
|
|
|
|
д2 |
|
|||
|
|
|
D |
d |
|
||
|
|
|
|
|
|
|
|
|
|
|
|
|
|
|
|
|
|
|
|
|
|
|
|
|
min |
|
t |
заг1 |
1 |
D |
d |
|
д |
Рис. 7.1. Схема обработки
2.Установить вылет пиноли в соответствии с данными табл. 7.2.
3.Измерить диаметры ступеней исходной заготовки Dзаг1 и Dзаг2.
4.Назначить режим обработки, установить выбранную подачу и число оборотов.
Таблица 7.2
54

|
|
|
Наибольший диаметр изделия, |
|
|
||||
Параметр |
|
|
обрабатываемого на станке, мм |
|
|||||
100 |
125 |
160 |
200 |
250 |
320 |
|
400 |
500 |
|
|
|
||||||||
|
|
|
|
|
|
|
|
|
|
Вылет пиноли с |
50 |
60 |
70 |
80 |
95 |
115 |
|
140 |
170 |
центром, мм |
|
||||||||
|
|
|
|
|
|
|
|
|
5.Измерить геометрию резца с помощью угломера и данные занести в табл. 7.3, определить коэффициент K p по формуле (7.4).
6.Установить резец таким образом, чтобы со ступени меньшего диаметра Dзаг1 снять припуск 0,2–0,5 мм на сторону.
7.Обработать ступенчатую заготовку за один проход.
8.Измерить микрометром диаметры d 2 и d 1 , полученные в результате
обработки. Ввести результаты измерений в табл. 7.4.
9. Рассчитать уточнение и жесткость станка по формулам (7.9) и (7.10).
Содержание отчета
1.Наименование работы.
2.Цель работы.
3.Наименование, модель и характеристика станка.
4.Схема установки для определения жесткости токарного станка производственным методом.
5.Характеристика измерительных приборов (наименование, цена деле-
ния).
6.Материалы обрабатываемой детали и режущего инструмента.
7.Режим обработки (tmin, S, v), геометрия инструментов, значения ко-
|
эффициентов K p |
и Сp . Результаты занести в табл. 7.3. |
|
|
|
|
|
|
|||||||||||
|
Таблица 7.3 |
|
|
|
|
|
|
|
|
|
|
|
|
|
|
|
|
|
|
|
|
|
|
|
|
|
|
|
|
|
|
|
|
|
|
|
|
||
|
Заготовка |
Коэффициент |
Геометрия инструмента |
|
|
Режим резания |
|||||||||||||
|
|
|
|
|
|
|
|
|
|
|
|
|
|
|
|
|
|
|
|
Марка стали |
K p |
|
|
Сp |
|
|
|
|
|
1 |
|
r |
n, об/с |
v, |
S, |
||||
|
|
|
|
|
|
|
|
|
|
|
|
|
|
|
|
|
м/с |
мм/об |
|
|
|
|
|
|
|
|
|
|
|
|
|
|
|
|
|
|
|
|
|
|
8. Результаты измерений образца. |
|
|
|
|
|
|
|
|
|
|||||||||
|
|
|
|
|
|
|
|
|
|
|
|
|
|
|
|
|
Таблица 7.4 |
||
|
|
|
|
|
|
|
|
|
|
|
|
|
|
|
|
|
|
||
|
Dзаг1 |
|
|
|
|
Dзаг2 |
|
|
|
|
d 2 |
|
|
|
d 1 |
|
|
||
|
|
|
|
|
|
|
|
|
|
|
|
|
|
|
|
|
|
|
|
9.Расчет уточнения .
10.Расчет суммарной жесткости станка jст .
Контрольные вопросы
55

1.Сущность производственного метода измерения жесткости станка.
2.Сущность явления копирования.
3.Смысл показателя уточнения.
4.Расчетные формулы для определения жесткости производственным методом.
Литература: [2, 5, 6].
56
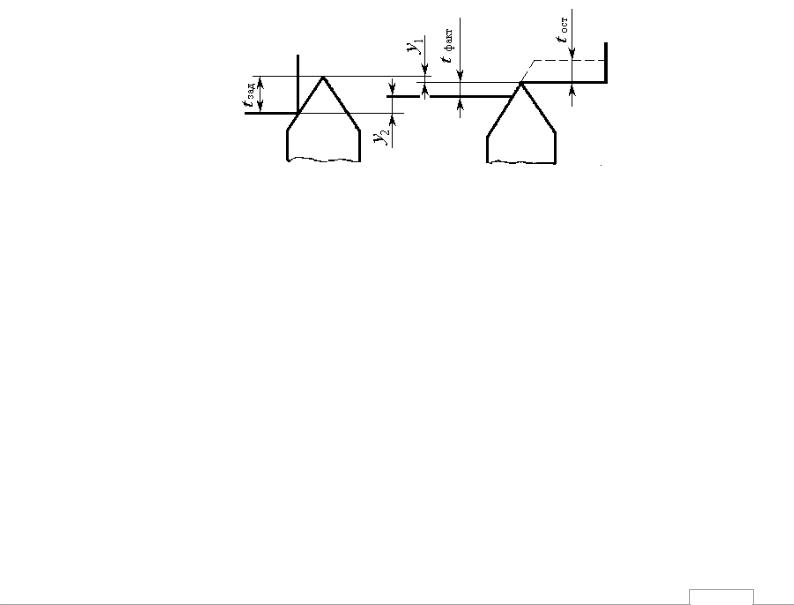
Лабораторная работа № 8
ИССЛЕДОВНИЕ ВЛИЯНИЯ УПРУГИХ ДЕФОРМАЦИЙ ТЕХНОЛОГИЧЕСКОЙ СИСТЕМЫ НА ТОЧНОСТЬ ОБРАБОТКИ
Цель работы: определение расчетом и экспериментально погрешность выполняемого размера в двух сечениях обрабатываемой заготовки, возникающую в результате деформации технологической системы от усилий резания.
Работа выполняется в двух вариантах: для обтачивания цилиндрической заготовки в центрах и для заготовки, закрепленной в трехкулачковом патроне.
Краткие теоретические сведения
В результате упругих перемещений элементов технологической системы под воздействием силы резания фактическая глубина резания оказывается
меньше заданной ( tзад ), рис. 8.1.
Рис. 8.1. Остаточная глубина резания:
tост tзад |
tфакт у1 у2 |
(8.1) |
где: tост – остаточная глубина |
резания; tзад – |
заданная глубина резания; |
tфакт – фактическая глубина резания; у1 – отжим резца; у2 – отжим заготовки.
Разность максимального и минимального значений tост при обработке
партии деталей определяет поле рассеяния достигаемых размеров, вызванное упругими деформациями технологической системы:
у tост |
tост |
min |
(8.2) |
|
max |
|
57
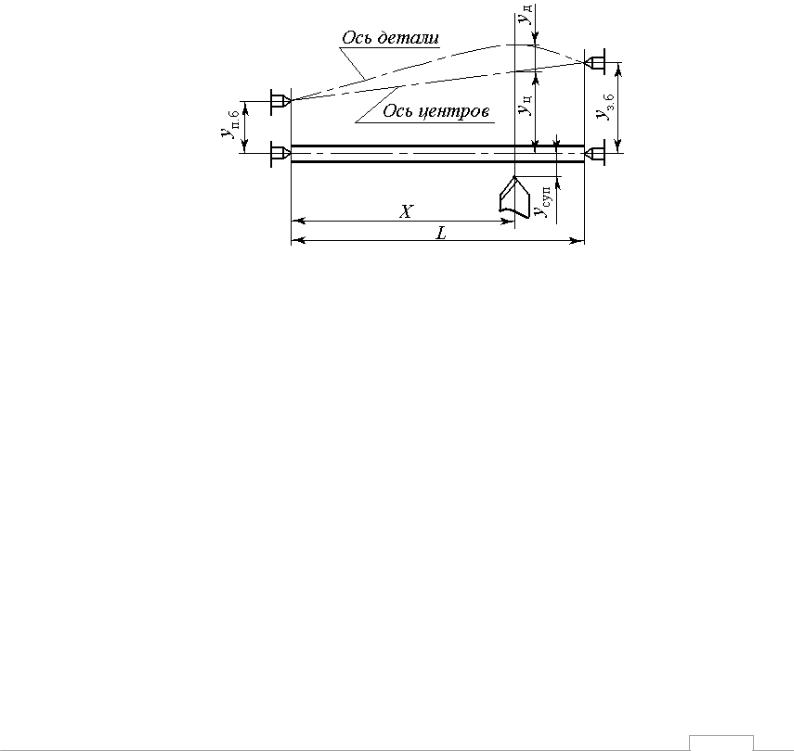
где: у – поле рассеяния размеров, вызванное упругими деформациями элементов технологической системы; tост max , tост min – максимальное и минимальное значения остаточной глубины резания в партии деталей.
При обработке одной детали разность значений tост max , tост min в раз-
личных ее сечениях определяет погрешность формы детали.
Упругие деформации элементов технологической системы являются переменными по координате перемещения режущего инструмента, так как по мере передвижения инструмента изменяется удельное влияние жесткости узлов технологической системы и жесткости обрабатываемой детали. Схема упругих деформаций элементов технологической системы приведена на рис. 8.2.
|
Рис. 8.2. |
Схема деформаций |
элементов |
технологической |
системы: |
||
уп.б – |
смещение |
передней |
бабки; |
уз.б – |
смещение |
задней |
бабки; |
уц – смещение заготовки, вызванное суммарным смещением центров станка в рассмат-
риваемом сечении; усуп. – упругий отжим суппорта; уд – упругий прогиб детали
Для случая, изображенного на рис. 8.2;
tост tзад tфакт уц уд усуп , |
(8.3) |
где уц – смещение заготовки, вызванное упругими смещениями передней и задней бабок станка; уд – прогиб заготовки в месте приложения силы; усуп – упругий отжим суппорта.
По аналогии со случаем жесткой балки на двух опорах |
|
||||||||||||
|
|
|
х 2 |
|
Py |
|
x 2 |
|
Py |
|
|||
уц |
1 |
|
|
|
|
|
|
|
|
|
|
, |
(8.4) |
|
Jп.б. |
|
|
||||||||||
|
|
|
L |
|
|
L |
|
Jз.б. |
|
58

где Jп.б – жесткость передней бабки м/мм; Jз.б – жесткость задней бабки, м/мм; L – длина заготовки, мм; x – расстояние от переднего центра до рассматриваемого сечения заготовки, мм; Py – составляющая силы резания,
нормальная к обрабатываемой поверхности, Н. Прогиб детали
|
|
уд |
|
Py |
|
|
х2 L x |
, |
(8.5) |
||
|
|
|
|
|
L |
||||||
|
|
|
|
3Е J |
|
|
|
||||
где Е |
– модуль |
упругости материала заготовки, Па (для |
сталей |
||||||||
Е = 0,2 |
Па); J – |
момент |
инерции |
поперечного сечения заготовки, мм; |
|||||||
J 0, 05 d 4 , где d – диаметр заготовки, км, до обтачивания. |
|
||||||||||
Упругое смещение суппорта: |
|
|
|
|
|
|
|
||||
|
|
|
|
усуп |
|
|
Py |
|
|
||
|
|
|
|
|
|
, |
|
(8.6) |
|||
|
|
|
|
|
|
|
|||||
|
|
|
|
|
|
|
|
Jсуп |
|
|
где: Jсуп - жесткость суппорта, Н/мм.
Радиальная составляющая силы резания
Р 10С |
р |
t0,9 S0,6 v 0,3 K |
p |
, |
(8.7) |
у |
|
где Ср – коэффициент, зависящий от механических свойств обрабатываемого материала и угла резания. (для резцов с материалом рабочей части из: твердого сплава Ср = 243; быстрорежущей стали Ср = 125; t – глубина реза-
ния; S – подача; v – скорость резания; K p – поправочный коэффициент, определяется по формуле:
K p K p K p K p Kr p ,
где К р – коэффициент, зависящий от угла в плане ; К р – коэффициент, зависящий от главного переднего угла ; К р – коэффициент, зависящий от угла наклона кромки ; Кrp – коэффициент, зависящий от радиуса при вер-
шине r .
Введя обозначение
C 10P С |
р |
S0,6 v 0,3 K |
p , |
(8.8) |
y |
|
получим:
59
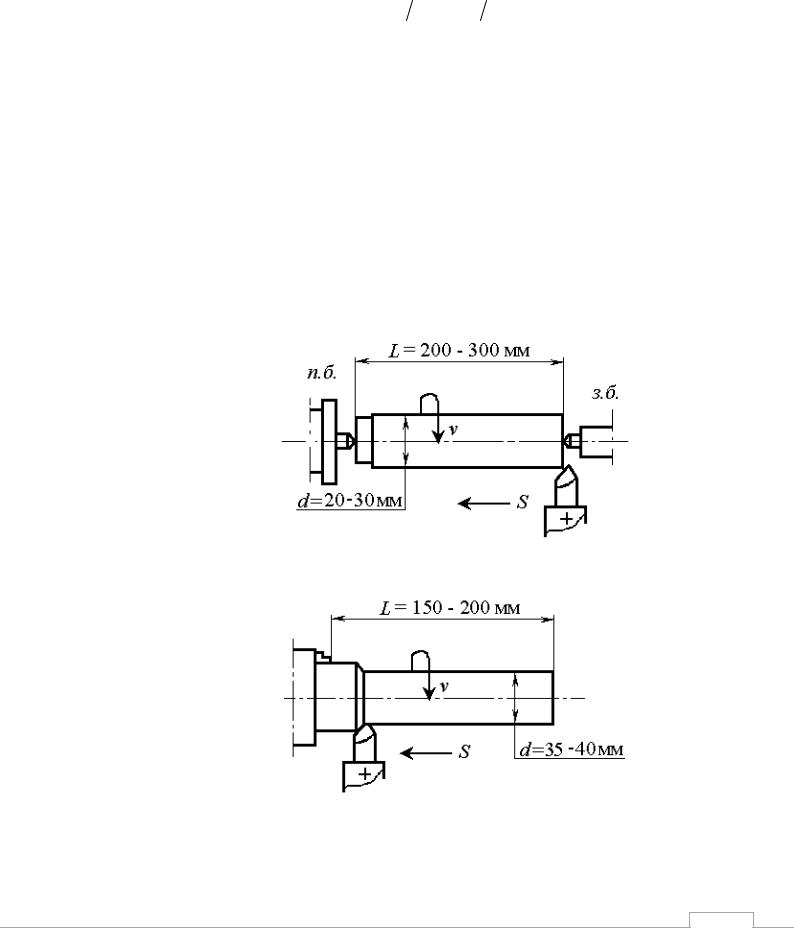
Ру С tзад0,9 . |
(8.9) |
Используя выражения (8.3), (8.4), (8.5), (8.6), (8.9) получаем:
|
|
|
|
|
|
|
|
|
|
|
|
|
|
t |
С t0,9 1 x L |
2 |
x L |
2 |
|
х |
2 |
L x |
2 |
|
1 |
||
|
|
|
|||||||||||
|
|
|
|
|
|
|
|
|
|
|
|
|
|
ост |
зад J |
|
|
|
|
|
|
|
|
|
(8.10) |
||
п.б |
|
Jз.б |
|
|
3E J L |
|
|
Jсуп |
|||||
|
|
|
|
|
|
|
|
|
|
|
|
|
|
Величины Jп.б , Jз.б , Jсуп – определяются экспериментально. Допустимо использование значений Jп.б , Jз.б Jсуп , полученных в лаб. работе № 7.
Порядок выполнения работы:
В а р и а н т 1:
1. Установить заготовку в центрах токарного станка, как показано на схеме (рис. 8.3, а), предварительно проточив её для устранения погрешности формы.
2. Настроить станок на заданный режим резания: v – м/с; S – 0,15–0,4 мм/об; t – 1–1,5 мм.
а
б
Рис. 8.3. Схемы обработки; а – в центрах; б – в патроне
3. Проточить заготовку.
60