
Лабораторный практикум
.pdf
Контрольные вопросы
1.Задачи, решаемые при настройке технологической системы.
2.Сущность метода настройки по пробным деталям.
3.Как определяется допуск на настройку?
4.Как обосновать выбор метода настройки?
5.По каким зависимостям определяют погрешность настройки по пробным деталям и эталону?
Литература: [1, 4].
71
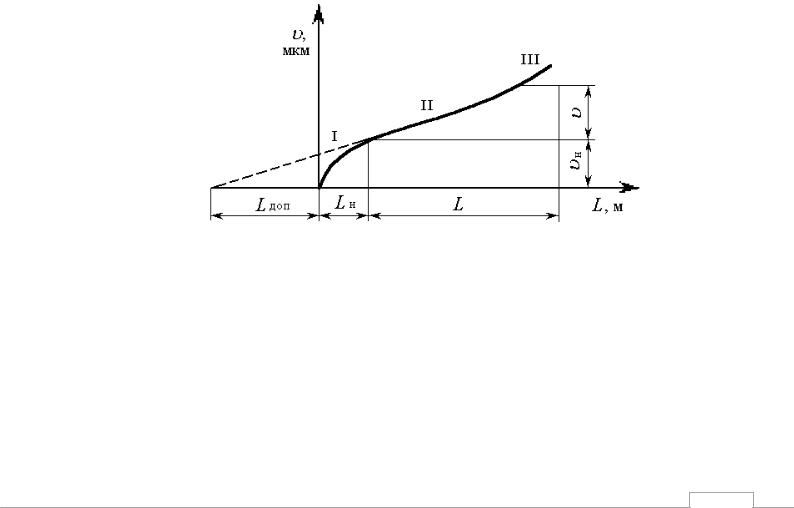
Лабораторная работа № 10
ИССЛЕДОВАНИЕ РАЗМЕРНОГО ИЗНОСА РЕЖУЩЕГО ИНСТРУМЕНТА
Цель работы: экспериментальное исследование зависимости размерного износа токарного резца от пути резания и вывод эмпирической формулы для расчета величины размерного износа резца с использованием метода наименьших квадратов.
Краткие теоретические сведения
Износ режущей кромки инструмента при обработке деталей на станке приводит к возникновению переменной погрешности обработки.
Вследствие износа режущая кромка как бы отдаляется от обрабатываемой поверхности на расстояние, равное величине радиального износа инструмента. Данная погрешность приводит к увеличению диаметра обтачиваемого вала или уменьшению размера диаметра растачиваемого отверстия.
При ориентировочных расчетах точности механической обработки размерный износ инструмента рассматривают в зависимости от пути резания L (м), т. е. Пути, пройденного лезвием инструмента в металле. График зависимости величины размерного износа инструмента от пути резания приведен на рис. 10.1.
Рис. 10.1. Зависимость размерного износа инструмента от длины пути резания
Различают три зоны износа инструмента: I – начального износа инструмента;
II – нормального износа инструмента;
III– катастрофического износа инструмента.
Впериод начального износа происходит приработка режущего лезвия инструмента, сопровождающаяся выкрашиванием отдельных неровностей и
72

заглаживанием следов заточки режущих граней. В этот период шероховатость обрабатываемой поверхности обычно постепенно уменьшается.
Начальный износ Н и его продолжительность LН зависят от материа-
ла режущего инструмента и режима резания. Обычно LН находится в преде-
лах 500–2000 м. Второй период износа (зона II) характеризуется нормальным износом инструмента, прямо пропорциональным пути резания.
Интенсивность износа инструмента в этот период, оценивают величиной относительного износа 0 (мкм/км), которая рассчитывается по формуле:
|
0 |
|
, |
(10.1) |
|
L |
|||
где |
|
|
|
|
– размерный износ на пути резания L , мкм; |
L – путь резания в зоне |
нормального износа, км.
Третий период (зона III) характеризуется интенсивным износом инструмента, сопровождающимся выкрашиванием режущей кромки инструмента и его поломкой.
Из всех рассмотренных зон на точность обработки наибольшее влияние оказывает зона II, т. е. износ инструмента в период нормального износа, который определяется выражением:
|
0 L |
|
1000 , |
(10.2) |
|
где – размерный износ инструмента, мкм; |
L – длина пути резания, м; |
0 – относительный износ инструмента, мкм/км.
Применительно к точению длина пути резания может быть рассчитана по одной из двух зависимостей:
|
|
D l |
|
||
|
L |
1000 |
|
, |
(10.3) |
|
S |
||||
|
L v t0 , |
(10.4) |
|||
где |
D – диаметр обрабатываемой поверхности, мм; l – длина обрабатывае- |
||||
мой |
поверхности, мм; S |
– подача, мм/об; v |
– скорость |
резания м/мин; t0 – основное технологическое время, мин.
Однако при определении износа нового или вновь заточенного инструмента расчет по формуле (10.2) дает заниженный результат, так как не учи-
тывается повышенный износ инструмента в зоне I, т. е. на длине LН .
Для учета величины начального износа Н принято расчетную L длину пути резания, определенную по формуле (10.3) или (10.4), увеличивать на некоторую дополнительную величину Lдоп (рис. 10.1). В этом случае выражение (10.2) получает вид
73
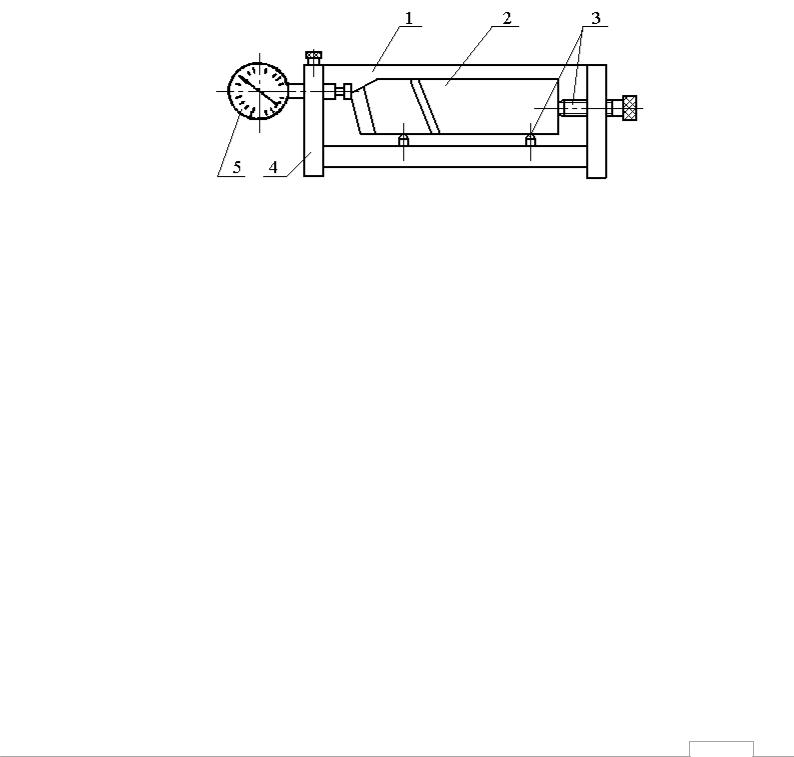
|
0 L Lдоп |
. |
(10.5) |
|
1000 |
||||
|
|
|
||
Для доведенных инструментов |
Lдоп =500 м, для заточенных |
Lдоп = 1500 м. В среднем принимают Lдоп =1000 м.
Экспериментально размерный износ определяется путем последовательного измерения расстояния от вершины резца до выбранной измерительной базы. Эскиз приспособления для измерения размерного износа токарного резца приведен на рис. 10.2.
Рис. 10.2. Приспособление для измерения размерного износа токарного резца: 1 – корпус; 2 – резец, 3 – опоры, 4 – стойка, 5 – инди-
катор.
Следует отметить, что для исключения влияния температурных деформаций резца его необходимо охлаждать до постоянной температуры перед каждым измерением.
Построенную по результатам измерений кривую зависимости от L
аппроксимируют линейной зависимостью |
|
А0 А1 L1 , |
(10.6) |
где А0 и А1 – постоянные координаты, подлежащие определению.
Наиболее точным методом оценки коэффициентов А0 и А1 является метод наименьших квадратов (см. лаб. работу № 7). Следует иметь в виду, что при такой обработке не принимаются во внимание точки кривой, лежащие на участке начального износа.
Коэффициенты А0 и А1 определяют из известных уравнений:
n |
|
n |
|
n A0 A1 Xi |
Yi , |
(10.7) |
|
i 1 |
|
i 1 |
|
n |
n |
n |
|
A0 Xi A1 |
Xi2 XiYi . |
(10.8) |
|
i 1 |
i 1 |
i 1 |
|
74

По известным значениям А0 и А1 можно определить величину 0 от Lдоп , так как
0 А1 , |
(10.9) |
||
Lдоп |
А0 |
. |
(10.10) |
|
|||
|
А |
|
|
|
1 |
|
|
В табл. 10.1 приведены значения относительного износа резцов при чистовом точении и растачивании с глубиной резания t = 0,1–0,3 мм, при достижении шероховатости Rz = 10 мкм.
Приведенные в табл. 10.1 данные могут быть использованы для сравнительных оценок износа и расчетов погрешностей обработки.
Таблица 10.1
Обрабатываемый ма- |
|
Материал |
Режим резания |
Стойкость по |
Относи- |
|||
|
териал |
|
инстру- |
|
|
шероховато- |
тельный |
|
|
|
|
мента |
скорость |
Подача, |
сти, |
выра- |
износ |
|
|
|
|
v , м/мин |
S , мм/об |
женная |
в |
0 , |
|
|
|
|
|
|
метрах |
пути |
мкм/км |
|
|
|
|
|
|
резания |
|
|
|
|
|
|
|
|
|
|
|
Стали |
углеродистые, |
|
|
|
|
|
|
|
конструкционные, ка- |
Т30К4 |
100–180 |
0,04–0,08 |
12500 |
6,5 |
|||
чественные |
|
|
|
|
|
|
|
|
Стали |
конструкцион- |
|
Т30К4 |
120–180 |
0,04–0,08 |
20000 |
4,7 |
|
ные, легированные |
|
|
|
|
|
|
|
|
Стали |
высоколегиро- |
|
|
|
|
|
|
|
ванные, |
коррозионно- |
|
Т30К4 |
80–120 |
0,02–0,04 |
11000 |
6,5 |
|
стойкие, жаростойкие, |
|
|||||||
жаропрочные |
|
|
|
|
|
|
|
|
Стальное литье |
|
Т30К4 |
100–160 |
0,04–0,06 |
7000 |
8,5 |
||
|
|
|
|
|
|
|
|
|
Чугун серый |
|
|
|
|
|
|
|
|
СЧ 15-32 |
|
ВК3М |
100–160 |
0,04–0,08 |
21000 |
6,0 |
||
СЧ 18-36 |
|
|
|
|
|
|
|
|
Чугун серый |
|
|
|
|
|
|
|
|
СЧ 21-40 |
|
ВК3М |
120–160 |
0,04–0,08 |
23000 |
6,5 |
||
СЧ 28-48 |
|
|
|
|
|
|
|
|
Чугун ковкий |
|
|
|
|
|
|
|
|
КЧ 30-6 |
|
|
ВК3М |
80–140 |
0,03–0,06 |
19000 |
6,0 |
|
КЧ 37-12 |
|
|
|
|
|
|
|
|
|
|
Порядок выполнения работы |
|
|
|
1.Установить и закрепить заготовку на станке.
2.Охладить резец в проточной воде.
75

3.Установить резец в приспособлении (рис. 10.2) так, чтобы измерительная поверхность наконечника индикатора касалась вершины резца с натягом 1–2 деления. Индикатор установить на нуль и снять резец.
4.Установить и закрепить резец на станке.
5.Настроить станок на указанный режим обработки.
6. .Включить станок, проточить заготовку в течение двух минут, отвести резец от заготовки и выключить станок. Снять резец со станка, охладить под проточной водой, установить в приспособление и измерить величину износа как разность двух показателей индикатора. Результат занести в табл. 10.2.
7.Повторить пп. 4–6 для всех указанных в табл. 10.2 значений времени работы резца.
8.Подсчитать путь резания для всех заданных в табл. 10.2 интервалов времени по формуле (10.4). Результаты работы занести в табл. 10.2.
9.Построить график зависимости f (L)
10.Заполнить табл. 10.3 и рассчитать параметры А0 и А1 зависимости
(10.6) по уравнениям (10.7), (10.8).
11.Определить величины 0 и Lдоп .
Таблица 10.2
Номер |
|
Параметр |
|
Время работы резца от начала опыта, мин |
|||||||||
|
|
0 |
|
2 |
|
5 |
|
10 |
|
20 |
|||
|
|
|
|
|
|
|
|
|
|||||
1 |
|
Путь резания |
от |
|
|
|
|
|
|
|
|
|
|
|
|
начала опыта L , км |
|
|
|
|
|
|
|
|
|
||
2 |
|
Размерный |
износ |
|
|
|
|
|
|
|
|
|
|
|
|
резца 0 , мкм |
|
|
|
|
|
|
|
|
|
|
|
|
|
|
|
|
|
|
|
|
|
|
|
|
|
Таблица 10.3 |
|
|
|
|
|
|
|
|
|
|
|||
|
|
|
|
|
|
|
|
|
|
||||
|
|
L |
|
|
|
L2 |
|
|
L |
||||
|
L |
|
|
|
L2 |
|
|
L |
|||||
|
1 |
|
1 |
|
|
1 |
|
|
|
1 |
|
1 |
|
|
… |
|
… |
|
… |
|
|
… |
|
||||
|
Ln |
|
n |
|
L2n |
|
|
Ln n |
|||||
|
n |
|
n |
|
n |
|
|
n |
|
||||
Li |
|
i |
|
L2i |
|
|
Li i |
||||||
|
i 1 |
|
i 1 |
|
i 1 |
|
|
i 1 |
|
Содержание отчета
1. Наименование работы.
2. . Цель работы.
3.Наименование и модель станка.
4.Марка пластинки твердого сплава.
76

5.Марка обрабатываемого материала.
6.Размеры заготовки.
7.Режимы резания( v, S, t ).
8.Схема измерения размерного износа резца.
9.Результаты опытов и расчетов (табл. 10.2 и 10.3).
10.График зависимости f (L) ;
11.Решение уравнений (10.7) и (10.8) и расчет величин 0 и Lдоп .
Контрольные вопросы
1.Характеристика трех зон размерного износа.
2.Какой величиной оценивается износ инструмента в период нормального износа?
3.Каким образом учитывается начальный износ при расчете износа инструмента?
4.Каким образом можно определить величины H , 0 и Lдоп по экспериментальным данным?
Литература: [1, 4. 6].
77

|
Лабораторная работа № 11 |
|
ИССЛЕДОВАНИЕ |
ТЕПЛОВЫХ |
ДЕФОРМАЦИЙ |
РЕЖУЩЕГО ИНСТРУМЕНТА |
|
Цель работы: экспериментальное исследование зависимости тепловых деформаций токарного резца от пути резания при обработке валов.
Краткие теоретические сведения
При непрерывной работе станка возникает переменная систематическая погрешность обработки заготовок, связанная с нагревом технологической системы “станок – приспособление – инструмент – заготовка”. Эта погрешность складывается из следующих составляющих:
тепловых деформаций станка; тепловых деформаций заготовки; тепловых деформаций инструмента.
Тепловые деформации станка возникают вследствие нагрева его составных элементов в результате потерь на трение в подвижных механизмах, а также от охлаждающей жидкости, которая отводит теплоту из зоны резания и нагрева от внешних источников (батарей, солнечных лучей).
Для устранения данной погрешности обработки необходимо произвести предварительный прогрев станка путем его обкатки на холостом ходу в течение 2–3 часов для достижения стабилизации температуры нагрева [4]. Последующую обработку следует производить без значительных перерывов в работе, чтобы избежать охлаждения станков и обратной деформации его составных частей.
Тепловые деформации заготовки возникают из-за того, что часть тепла, образующегося в зоне резания, переходит в обрабатываемое изделие, вызывая изменение его размеров. Причем при равномерном нагреве заготовки возникают погрешности размеров, а при местном нагреве заготовки – погрешности формы, обусловленные короблением поверхности.
Нагрев заготовки зависит, прежде всего, от режимов обработки.
При токарной обработке с увеличением скорости резания и подачи температура нагрева заготовки уменьшается из-за уменьшения продолжительности теплового воздействия на заготовку.
Увеличение глубины резания, наоборот, приводит к возрастанию температуры нагрева заготовки в результате увеличения площади контакта инструмента с заготовкой и увеличения количества тепла, образующегося в зоне резания.
Следует отметить, что тепловые деформации заготовки имеют существенное влияние лишь при изготовлении тонкостенных деталей, а при обработке сплошных, массивных изделий их влияние на точность обработки не велико.
Одним из средств уменьшения тепловых деформаций заготовки является применение обильного охлаждения.
78

Тепловые деформации в инструментах возникают из-за перехода части теплоты из зоны резания в режущий инструмент, что вызывает его нагрев и изменение размеров.
При токарной обработке наибольшая часть погрешностей, вызванная тепловыми деформациями, обусловлена удлинением размеров.
Характер процесса, возникающего в резце при обработке, показан на рис. 11.1. Наибольший рост тепловых деформаций резца (кривая 1) наблюдается в начальный период, затем интенсивность роста уменьшается и наступает состояние теплового равновесия, при котором рост тепловых деформаций невелик. Аналогичная картина наблюдается при охлаждении резца (кривая
2).
При точении легированной стали с = 1080 МПа (110 кг/мм2) резцами, снабженными пластинками Т15К6, с вылетом 40 мм и сечением 20x30 мм тепловое равновесие, при котором прекращается удлинение резца наступает примерно через 20–24 мин непрерывной работы (рис. 11.1) [4].
В процессе обработки мягкой стали, тепловое равновесие резца восстанавливается через 12 мин непрерывной работы при сохранении общего характера закономерностей, показанных на рис. 11.1.
Рис. 11.1. Зависимости тепловых деформаций резца от времени обработки и охлаждения: 1– нагревание резца; 2– охлаждение резца
Среди факторов, наиболее сильно влияющих на интенсивность нагрева резца, можно отметить:
режим резания ( v, S, t ), увеличение скорости резания;
подача и глубина резания (влияет на интенсификацию нагрева резца и рост его удлинения);
вылет резца (при уменьшении вылета резца сокращается его удлине-
ние);
площадь поперечного сечения стержня резца; толщина пластинки из твердого сплава (при увеличении толщины пла-
стинки удлинение резца уменьшается);
79
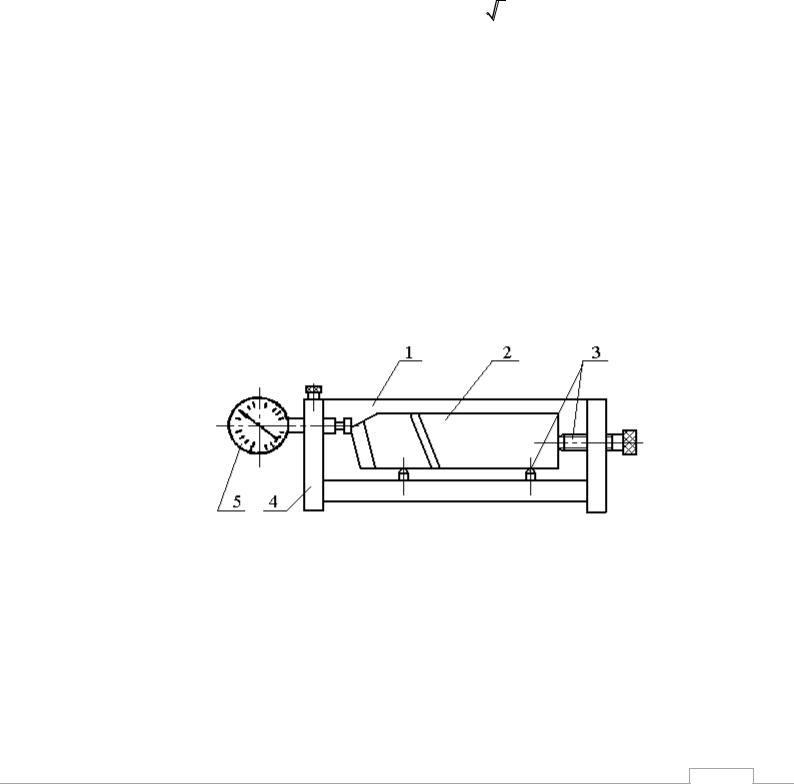
твердость обрабатываемого материала (увеличение твердости ведет к интенсификации нагрева резца и росту его удлинения).
При токарной обработке в стружку уходит 50–85% тепла, а при высоких скоростях резания до 90%; 10–40% тепла переходит в резец; 3–9% остаётся в заготовке и около 1 % рассеивается в окружающей среде. При обработке без охлаждения удлинение резца может достигать 30–50 мкм [4]. Обильным охлаждением удлинение резцов уменьшается в 3–3,5 раза.
Удлинение резца lр, мкм, в условиях теплового равновесия можно приближенно подсчитать по формуле:
lp |
C |
lp |
в t S 0,75 |
|
, |
|
|
v |
(11.1) |
||||||
F |
|||||||
|
|
|
|
|
|
||
где С – постоянная (при v |
=100–200 м/мин, t 1 |
мм, S 0,2 мм/об |
С = 4,5 [5]); lр – вылет резца; F – поперечное сечение резца, мм2; в - предел прочности (для деталей из стали в =700 МПа); t – глубина резания; S – подача, мм/об; v – скорость резания м/мин.
Порядок выполнения работы
1.Установить и закрепить заготовку на станке.
2.Охладить резец водой.
3.Установить резец в приспособление (рис. 11.2) так, чтобы измерительная поверхность наконечника индикатора касалась вершины резца с натягом 1–2 деления, индикатор установить на нуль и снять резец.
Рис. 11.2. Приспособление для измерения удлинения (укорочения) резца: 1 – корпус; 2 – резец, 3 – опоры, 4 – стойка, 5 – индикатор
4.Установить и закрепить резец на станке.
5.Настроить станок на заданный режим работы.
6.Включить станок, проточить заготовку в течение двух минут, отвести резец от заготовки и, быстро сняв его со станка, замерить величину удлинения резца в приспособлении. Результат измерения занести в табл. 11.1.
Таблица 11.1
80