
Лабораторный практикум
.pdf
4. Рассчитать величину остаточной глубины резания tост по формуле
(8.10) для двух сечений заготовки х L 2 (середина заготовки) и х L у зад-
ней бабки.
5. Определить погрешность формы детали в продольном сечении, используя результаты расчета, полученные в п.4.
1 2 tост х L 2 tост x L .
6.Измерить микрометром диаметр обработанной заготовки в сечении
хL 2 и х L .
7.Определить фактическую погрешность формы детали по формуле:
1 dx L 2 dx L .
8. Сопоставить расчетную и фактическую погрешность формы детали и определить относительную неточность расчета, %:
1 1 100 % .1
В а р и а н т 2:
1. Установить заготовку в патроне токарного станка, как показано на схеме (рис. 8.3, б), предварительно проточив её для устранения погрешности формы.
2. Настроить станок на заданный режим резания: v – м/с;
S – 0,15–0,4 мм/об; t – 1–1,5 мм.
3.Проточить заготовку.
4.Рассчитать величину остаточной глубины резания tост для двух се-
чений х L (у свободного конца заготовки) и х 0 (у кулачков патрона) по формуле (8.10).
5.Определить погрешность формы детали в продольном сечении, используя результаты расчета, полученные в п.4:
2 2 tост х L tостx 0 .
6.Измерить микрометром диаметр обработанной заготовки в сечениях
хL и х 0 .
7.Определить фактическую погрешность формы детали по формуле
61
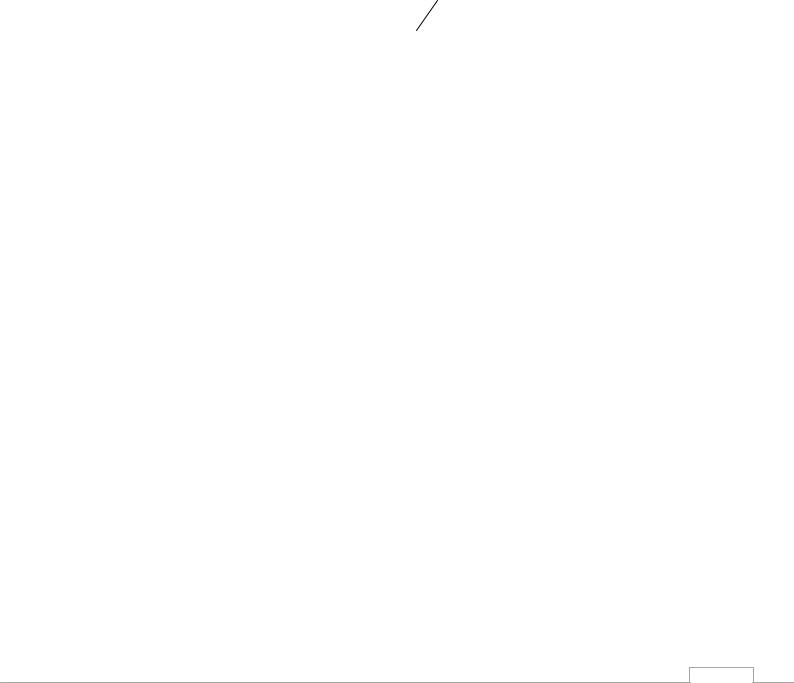
2 dx L dx 0 .
8.Сопоставить расчетную и фактическую погрешность формы детали и определись относительную неточность расчета, %.
Содержание отчета:
(для вариантов 1, 2)
1.Наименование работы.
2.Цель работы.
3.Эскиз обработки.
4.Характеристика обрабатываемого материала (табл. 8.1). 5, Условия обработки (табл. 8.2).
6.Характеристика жесткости технологической системы (табл. 8.3).
7. Расчет tост для сечений х L |
и х L |
|
(вариант 1); |
х L и х 0 |
|||||||||
|
|
|
|
|
2 |
|
|
|
|
|
|
|
|
(вариант 2); |
|
|
|
|
|
|
|
|
|
|
|
|
|
|
|
|
|
|
|
|
|
|
|
|
|
|
Таблица 8.1 |
|
|
|
|
|
|
|
|
|
|
||||
Марка ста- |
Твердость, |
|
Модуль упруго- |
Момент инерции поперечного |
|||||||||
ли |
|
НВ |
|
сти, Е, ГПа |
|
|
сечения, J 0, 05 d 4 , мм |
||||||
|
|
|
|
|
|
|
|
|
|
|
|
|
|
Таблица 8.2 |
|
|
|
|
|
|
|
|
|
|
|
|
|
|
|
|
|
|
|
|
|
|
|
||||
Глубина |
|
Подача |
|
Скорость резания, |
|
Ср |
|
K p |
|||||
t , мм |
|
S , мм/об |
|
v , м/с |
|
|
|
||||||
|
|
|
|
|
|
|
|||||||
|
|
|
|
|
|
|
|
|
|
|
|
|
|
Таблица 8.3 |
|
|
|
|
|
|
|
|
|
|
|
|
|
|
|
|
|
|
|
|
|||||||
Jп.б , Н/мм |
|
|
Jз.б , Н/мм |
|
|
Jсуп , Н/мм |
|||||||
|
|
|
|
|
|
|
|
|
|
|
|
|
|
|
|
|
|
|
|
|
|
|
|
|
|
|
|
8. Расчетные величины погрешности формы детали в продольном сече-
нии для варианта 1 – 1 ; варианта 2 – 2 .
9.Фактические величины погрешности формы детали в сечении для варианта 1 – 1 ; варианта 2 – 2 .
10.Относительная неточность расчета.
11.Выводы.
62

Лабораторная работа № 9
ОПРЕДЕЛЕНИЕ ПОГРЕШНОСТИ НАСТРОЙКИ СТАНКА
Цель работы: овладение методикой настройки технологической системы, экспериментальное и расчетное определение погрешностей настройки токарно-винторезного станка.
Краткие теоретические сведения
Для того чтобы изготовить с требуемой точностью одну деталь или партию деталей, необходимо, прежде всего, настроить технологическую систему (станок – приспособление – инструмент – заготовка) на заданный размер.
Под настройкой (наладкой) технологической системы (ГОСТ 3.1109–82) понимают приведение её в рабочее состояние, необходимое для выполнения технологической операции. Настройка включает согласованную установку режущего инструмента, рабочих органов станка и приспособления в положение, обеспечивающее достижение заданного размера с заданной точностью.
При настройке технологической системы решают две задачи:
1)обеспечение требуемой точности размеров, получаемых при обработке одной детали или партии;
2)обеспечение обработки максимального числа деталей до очередной поднастройки.
Настройка сводится к наладке технологической системы на размер ста-
тической настройки: |
|
Ас Ар Ад , |
(9.1) |
где Ар – рабочий настроенный размер – размер детали, который должен быть
получен при настройке; Ад – погрешность динамической настройки, вызван-
ная упругими и тепловыми деформациями технологической системы, износом инструмента, возникающими в процессе обработки.
Размер статической настройки Ас при обработке мелких партий изде-
лий определяется методом пробных проходов.
При обработке крупных партий изделий настройка, выполняется двумя основными методами:
1)по пробным деталям,
2)по эталону.
Сущность метода настройки по пробным деталям состоит в том, что обработка пробных групп деталей повторяется с внесением в настройку поправок до тех пор, пока групповой средний размер не попадет в установленные границы:
Агрнм.ср. Анм а К Т , |
(9.2) |
63
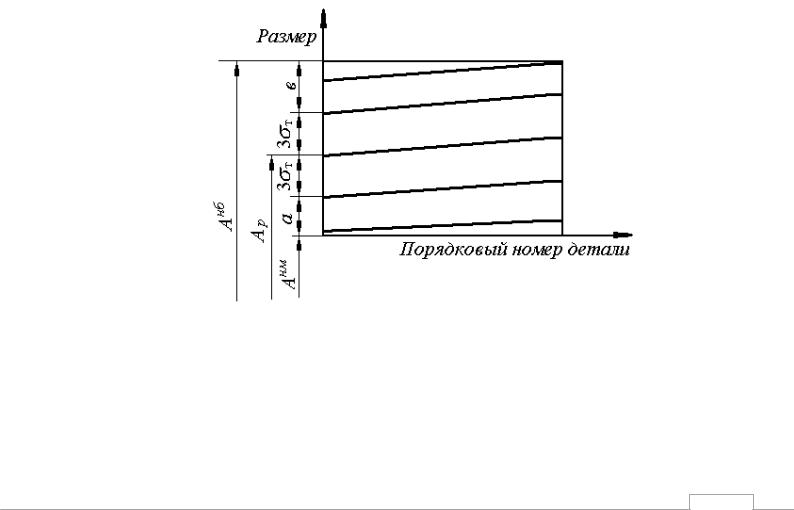
Агрнб.ср. Анб в К Т , |
(9.3) |
где Агрнм.ср. и Агрнб.ср. - наименьшее и наибольшее допустимые значения груп-
пового среднего размера; Анм и Анб – наименьшее и наибольшее значения заданного размера; а – часть поля допуска на заданный размер, предназначенная для компенсации постоянных систематических погрешностей; в – часть поля допуска, предназначенная для компенсации систематических за-
кономерно |
изменяющихся |
погрешностей; |
|||
К – коэффициент, К = t |
– 3, где t - коэффициент риска брака; |
t |
xпр |
, |
|
|
|||||
|
|
|
|
Т |
хпр – наименьшее значение отклонения Агр.ср от расчетного значения рабо-
чего настроечного размера А р , при котором ещё обеспечивается правильность настройки с принятым процентом риска; σТ – среднеквадратичное отклонение размеров. Величина 3σТ – половина расчетной части поля допуска, предназначенного для компенсации случайных погрешностей.
Для валов или вообще для охватываемых размеров настройка должна производиться в соответствии со схемой, приведенной на рис. 9.1.
Рис. 9.1. Схема настройки для охватываемых размеров
На рис. 9.2 приведена схема для определения необходимой точности настройки технологической системы на обработку валов.
64
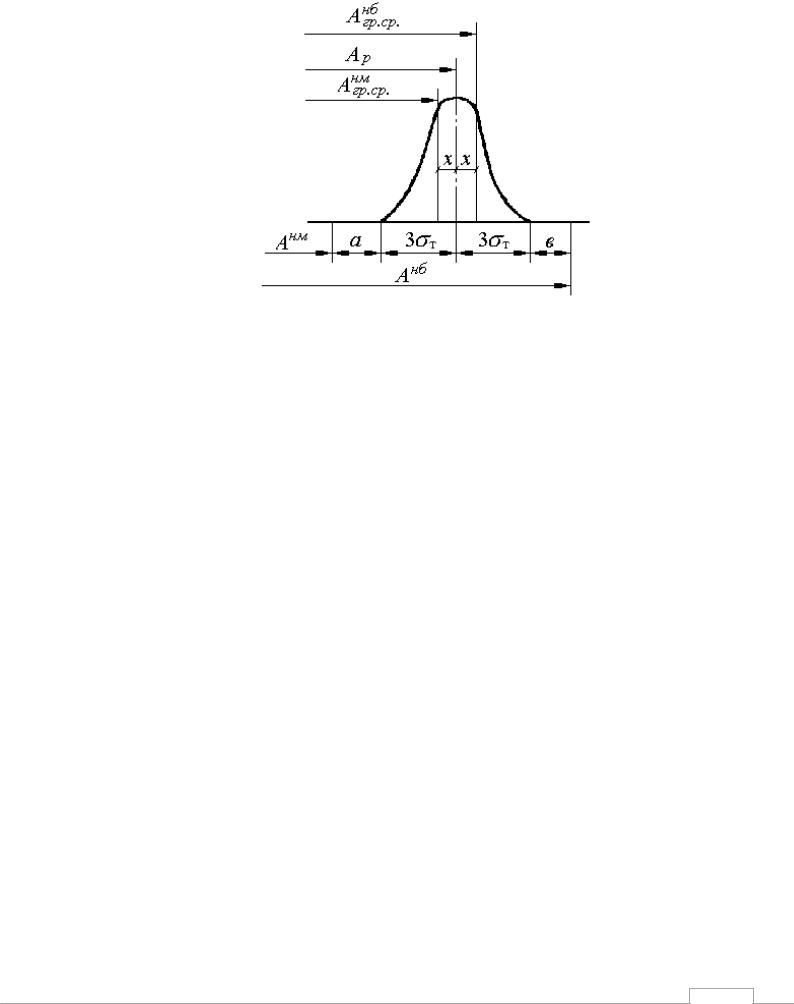
Рис. |
9.2. |
Схема |
определения |
необходимой |
точности |
настройки |
для охватываемых размеров |
|
|
|
|
Разность предельных значений Агрнб.ср определяет допуск на настройку:
Тн Агрнб.ср Агрнм.ср . |
(9.4) |
Поскольку в процессе обработки партии деталей при каждом регулировании технологической системы или смене инструмента невозможно обеспечить абсолютное постоянство положения его режущих кромок, то изменяются и значения размера статической настройки АС и рабочего настроечного размера Ар, получаемого на пробных деталях при настройке, т. е. возникает погрешность настройки ∆Н .
Погрешность настройки станка является случайной величиной и в зависимости от метода настройки, может включать в себя следующие составляющие погрешностей:
погрешность регулирования положения инструмента; погрешность измерения;
погрешность расчета положения центра группирования групповых средних размеров при настройке по пробным группам деталей.
Одной из доминирующих составляющих является погрешность установки (регулирования) инструмента на размер.
Существуют следующие основные способы установки инструмента на размер:
по лимбу; индикатору;
эталону с помощью щупа; жесткому упору.
65
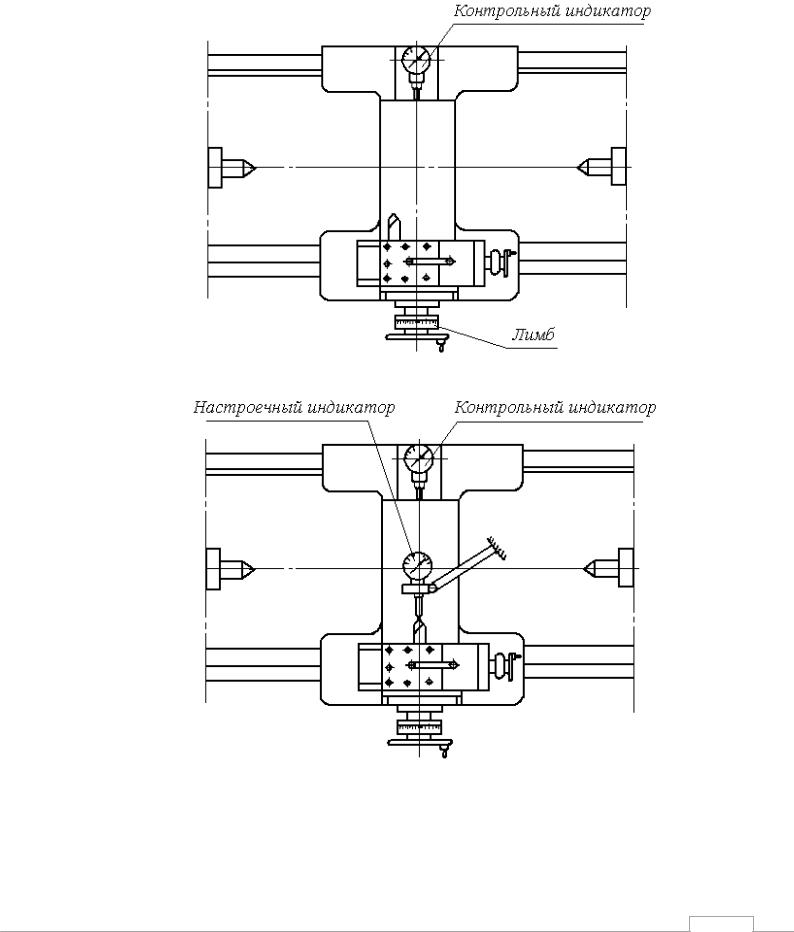
Погрешность установки по любому способу определяется с помощью контрольного индикатора (с ценой деления 0,001 мм), установленного на заднем торце суппорта (рис. 9.3, 9.4).
а
б
Рис. 9.3. Схема определения погрешности установки резца: а – по лимбу; б – по индикатору
66
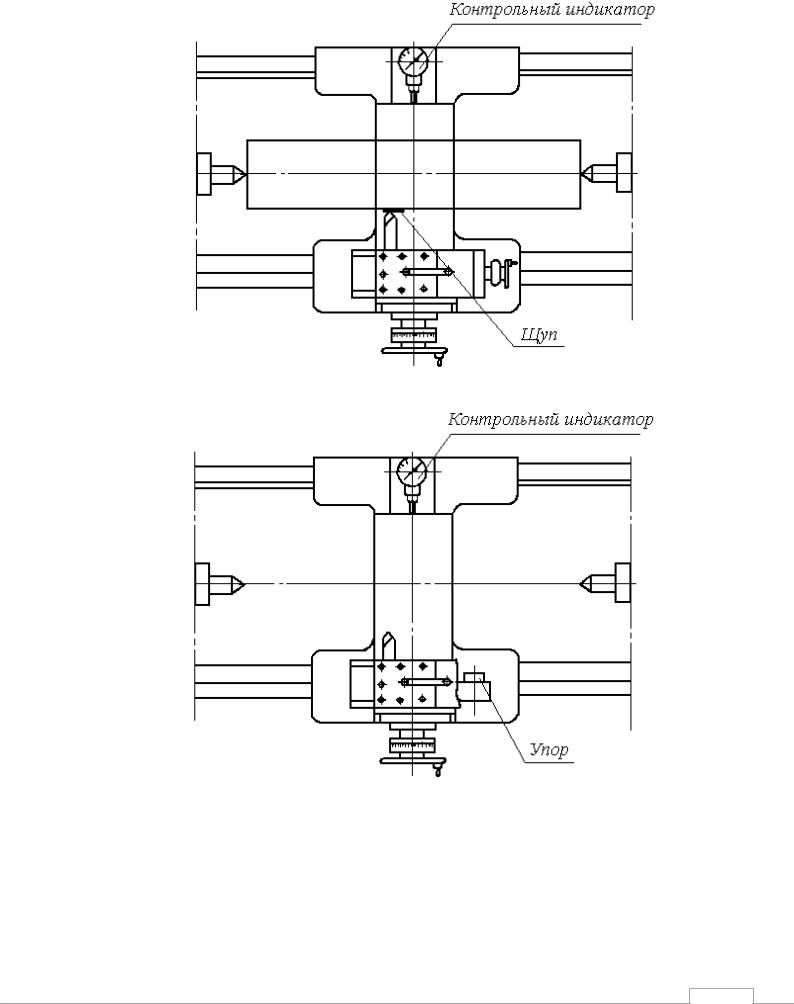
а
б
Рис. 9.4. Схема определения погрешности установки резца: а – по эталону с помощью щупа; б – по жесткому упору
Установка инструмента в заданное положение проводится 10 раз. При первом измерении шкала индикатора устанавливается на "0" . При последующих измерениях фиксируют, с учетом знака, отклонение от этого условного нулевого положения. Погрешность установки (регулирования) инструмента
67
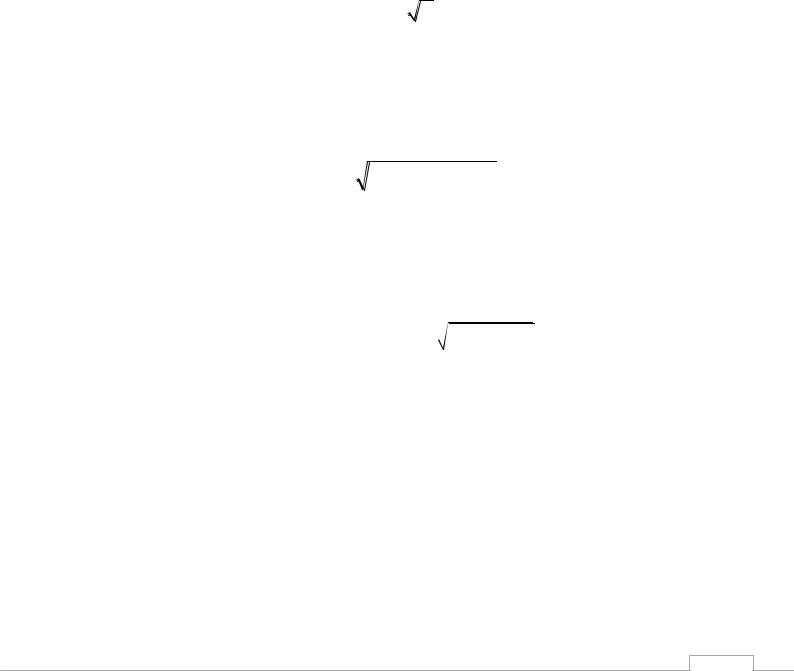
на размер при малом количестве замеров характеризуется размахом полученных величин:
|
|
рег max min , |
|
(9.5) |
|||||
где |
max – |
наибольшее |
положительное |
показание |
индикатора; |
||||
min – наименьшее отрицательное показание индикатора. |
|
||||||||
|
Погрешность измерения пробных деталей характеризуется точностью |
||||||||
применяемого |
измерительного |
средства (для |
микрометра |
1-го класса |
|||||
∆изм = 18 мкм). |
|
|
|
|
|
|
|
|
|
|
Погрешность расчета положения центра группирования групповых |
||||||||
средних размеров определяется формулой |
|
|
|||||||
|
|
расч |
6 |
|
|
, |
|
(9.6) |
|
|
|
|
|
|
|
||||
|
|
|
|
||||||
|
|
|
|
|
m |
|
|
где m – число пробных заготовок, по которым производят настройку станка, m = 5–10 шт.; σ - среднеквадратичное отклонение размеров.
Суммарная погрешность настройки при использовании метода пробных деталей определяется выражением
|
|
|
|
|
|
н 2К рег2 |
изм2 |
расч2 |
, |
(9.7) |
где K = 1–1,2 – коэффициент, учитывающий отклонение закона распределения элементарных погрешностей от нормального закона.
При использовании метода настройки по эталону погрешность настройки определяется по формуле
н 2К рег2 изг2 .эт , (9.8)
где изг.эт – погрешность изготовления эталона (10–20 мкм).
Основанием для выбора метода настройки и способа регулирования (установки) инструмента в каждом конкретном случае является выполнение
условия н Т н , где Tн – допуск на настройку.
Порядок выполнения работы
1. Определить погрешность установки резца по лимбу (рис. 9.3, а). Для этого необходимо:
1.1. Предварительно выбрать зазоры в винтовой паре и установить контрольный индикатор на станке.
68

1.2.Ввести в контакт с поперечным суппортом контрольный индикатор, при этом его шкалу установить на "0".
1.3.Отвести поперечный суппорт на себя и снова установить его по принятому делению лимба в заданное положение.
1.4.Зафиксировать смещение суппорта от заданного положения (по показанию контрольного индикатора), результат занести в табл. 9.1.
1.5.Рассчитать погрешность регулирования (установки) инструмента по формуле. (5).
1.6.Повторить пп. 1.3–1.5 столько раз, сколько указано в табл. 9.1.
2. Определить погрешность установки резца по индикатору (рис. 9.3, б). Для этого необходимо:
2.1.Установить настроечный и контрольный индикаторы на станке, как показано на рис. 9.3, б.
2.2.Установить шкалы индикаторов на "0".
2.3.Отвести суппорт на себя и снова вернуть в исходное положение контролируя установку рабочим индикатором.
2.4.Зафиксировать смещение суппорта от исходного положения с помощью контрольного индикатора, результат занести в табл. 9.1.
2.5.Рассчитать погрешность регулирования инструмента по формуле (9.5).
2.6.Повторить пп. 2.3–2.5 столько раз, сколько указано в табл. 9.1.
3.Определить погрешность установки резца по эталону с применением щупа (рис. 9.4, а). Для этого необходимо:
3.1.Установить эталонную деталь в центрах станка и контрольный индикатор на станке, шкалу – на "0".
3.2.Между эталонной деталью и резцом установить щуп толщиной
0,05–0,3 мм.
3.3.Подвести резцы к эталонной детали до его касания со щупом.
3.4.Зафиксировать смещение суппорта от исходного положения с помощью контрольного индикатора, результат занести в табл. 9.1.
3.5.Рассчитать погрешность регулирования инструмента по формуле (9.5). З.6. Повторить пп. 3.3–3.5 столько раз, сколько указано в табл. 9.1.
4.Определить погрешность установки резца по жёсткому упору (рис.9.4, б). Для этого необходимо:
4.1.Установить контрольный индикатор на сгонке и закрепить жесткий упор на каретке станка.
4.2.Установить шкалу контрольного индикатора на "0".
4.3.Подвести поперечный суппорт к упору, предварительно отведя его
на себя.
4.4.Зафиксировать смещение суппорта от исходного положения с помощью контрольного индикатора, результат занести в табл. 9.1.
4.5. Рассчитать погрешность регулирования инструмента по формуле (9.5)
69
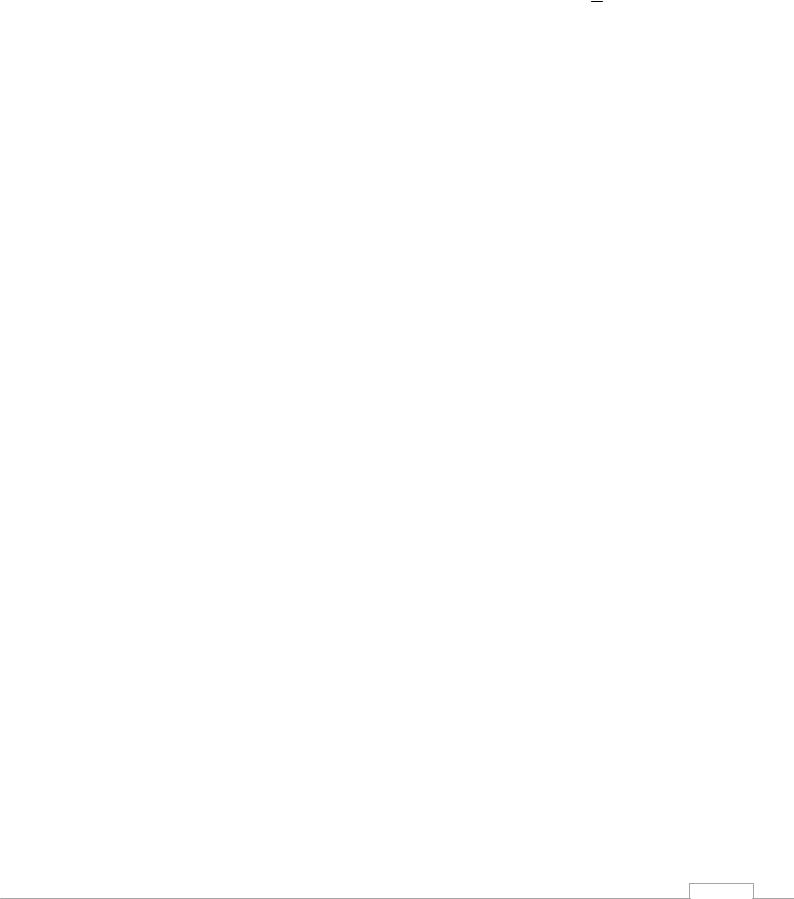
4.6. Повторить пункты 4.3–4.6 столько раз, сколько указано в табл. 9.1.
5. Рассчитать погрешность расчета положения центра группирования групповых средних размеров по формуле (9.6), приняв 16 Т , где Т- допуск на выполняемый размер.
6.Рассчитать погрешность настройки резца на размер по методу пробных деталей по формуле (9.7) отдельно для схем установки резца по лимбу, индикатору и упору.
7.Рассчитать погрешность настройки резца на размер по эталону по формуле (9.8).
8.Сравнить полученные величины погрешности настройки с допуском на настройку, приняв последний равным 0,1 от допуска на выполняемый размер.
Содержание отчета
1.Наименование работы.
2.Цель работы.
3.Схемы установки резца на размер: по лимбу.
по индикатору. по эталону.
по жесткому упору.
4.Табл. 9.1 с результатами экспериментов.
Таблица 9.1
Схема |
|
|
|
|
Замер |
|
|
|
|
Р, |
Н, |
|
установки |
1 |
2 |
3 |
4 |
5 |
6 |
7 |
8 |
9 |
10 |
мм |
мм |
По лимбу |
|
|
|
|
|
|
|
|
|
|
|
|
|
|
|
|
|
|
|
|
|
|
|
|
|
По индика- |
|
|
|
|
|
|
|
|
|
|
|
|
тору |
|
|
|
|
|
|
|
|
|
|
|
|
По эталону |
|
|
|
|
|
|
|
|
|
|
|
|
|
|
|
|
|
|
|
|
|
|
|
|
|
По жестко- |
|
|
|
|
|
|
|
|
|
|
|
|
му упору |
|
|
|
|
|
|
|
|
|
|
|
|
5.Определение погрешности расчета положения центра группирования групповых средних размеров.
6.Расчет погрешности установки резца на размер для схем установки по лимбу, индикатору, эталону и жесткому упору.
7.Выводы по результатам сравнения величин погрешностей настройки
сдопуском на настройку.
70