
Лабораторный практикум
.pdf
№ |
|
Параметр |
|
|
Время работы резца, мин |
|
||||
п/п |
|
|
|
|
|
|
|
|
|
|
|
|
|
|
0 |
|
2 |
5 |
10 |
|
20 |
|
|
|
|
|
|
|
|
|
||
|
Удлинение резца при обработ- |
|
|
|
|
|
|
|
||
|
ке, мм |
|
|
|
|
|
|
|
|
|
|
Размерный износ резца, мм |
|
|
|
|
|
|
|
||
|
|
|
|
|
|
|
|
|
|
|
|
Тепловые |
деформации |
резца |
|
|
|
|
|
|
|
|
при нагреве, мм |
|
|
|
|
|
|
|
|
|
|
Укорочение резца при нагреве, |
|
|
|
|
|
|
|
||
|
мм |
|
|
|
|
|
|
|
|
|
|
Тепловые |
деформации |
при |
|
|
|
|
|
|
|
|
охлаждении, мм |
|
|
|
|
|
|
|
|
7.Снять резец из приспособления, охладить его под водой, замерить величину размерного износа резца в приспособлении. Результат занести в табл.11.1.
8.Повторить пп. 3–7 для заданных в табл.11.1 интервалов времени, кроме последнего значения.
9.Для последнего, указанного в табл.11.1 интервала времени работы, повторить пп. 4–6; далее необходимо фиксировать величину укорочения резца через интервалы времени, указанные в табл.11.1. Результат измерений занести в табл.11.1.
10.Повторить п. 7.
11.Рассчитать тепловые деформации резца при нагревании как сумму между удлинением резца при обработке и размерным износом. Результаты занести в табл.11.1.
12.Рассчитать тепловые деформации резца при охлаждении как сумму между величиной ускорения резца при охлаждении и размерным износом после 20-минутной обработки. Результаты расчетов занести в табл.11.1.
13.Построить графики зависимости тепловых деформаций резца от времени обработки и охлаждения.
14.Рассчитать величину удлинения резца lр по формуле (11.1)
15.Сравнить расчетную величину удлинения резца при тепловом равновесии с фактической величиной удлинения резца. Сделать выводы.
Содержание отчета
1.Наименование работы.
2.Цель работы.
3.Наименование, модель станка.
4.Вылет резца, площадь поперечного сечения.
5.Марка обрабатываемого материала.
81

6.Режимы резания ( v, S, t ).
7.Схема измерения удлинения (укорочения резца).
8.Результаты опыта (табл.11.1).
9.Графики зависимостей тепловых деформаций резца от времени обработки и охлаждения.
10.Расчет величины удлинения резца в условиях теплового равновесия
lр, по формуле (11.1).
11. Сравнение расчетной lр с фактической. Выводы.
Контрольные вопросы
1.Факторы, влияющие на интенсивность тепловых деформаций режущего инструмента.
2.Закономерность изменения тепловых деформаций режущего инструмента во времени.
3.Влияние тепловых деформаций на точность.
4.Пути снижения влияния тепловых деформаций на точность обработ-
ки.
5.Методы экспериментальной оценки и расчета тепловых деформаций инструмента.
Литература: [4, 5].
82
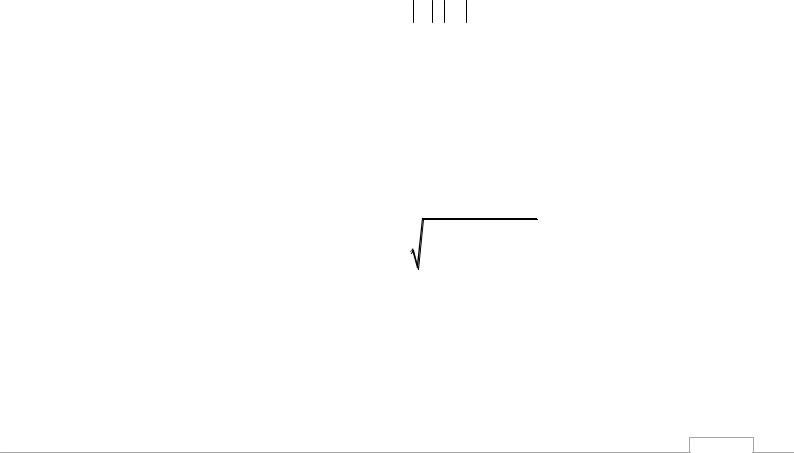
Лабораторная работа № 12
РАСЧЕТ ТОЧНОСТИ ОБРАБОТКИ
Цель работы: прогнозирование точности обработки валов на токарновинторезном станке.
Краткие теоретические сведения
Под точностью детали понимают её соответствие требованиям чертежа: по размерам, геометрической форме, правильности взаимного расположения обрабатываемых поверхностей и степени их шероховатости
Заданной точности обработки заготовки можно достичь одним из двух принципиально различных методов:
пробных проходов автоматического получения размеров на настроенных станках.
Каждый из этих методов неизбежно сопровождается погрешностями обработки, которые вызываются многими причинами систематического и случайного характера.
Соответственно различают систематические и случайные погрешности. Систематические погрешности подразделяют на постоянные и переменные. В совокупности все эти погрешности образуют суммарную погрешность обработки.
Расчет суммарной погрешности можно производить одним из двух методов:
1. Методом максимума-минимума:
n |
|
|
Si |
i , |
(12.1) |
i 1
где Si – передаточное отношение, показывающее абсолютную чувствительность к изменению параметра i ; i – элементарная погреш-
ность, i – индекс элементарной погрешности.
Данный метод не учитывает реальных комбинаций параметров, поэтому дает завышенные в 1,8–10 раз значения погрешности выходного параметра.
2. Вероятностным методом:
|
|
|
К |
|
|
|
|
|
|
|
1 |
n |
Ki |
Si Ti 2 , |
(12.2) |
|
|
i 1 |
|||||
|
|
|
|
|
|
|
где Ki - коэффициент относительного рассеяния, характеризующий отношение поля рассеяния погрешности при нормальном законе распределения к действительному полю рассеяния; Si – передаточное отношение; Ti – допуск; i – индекс элементарной погрешности.
83
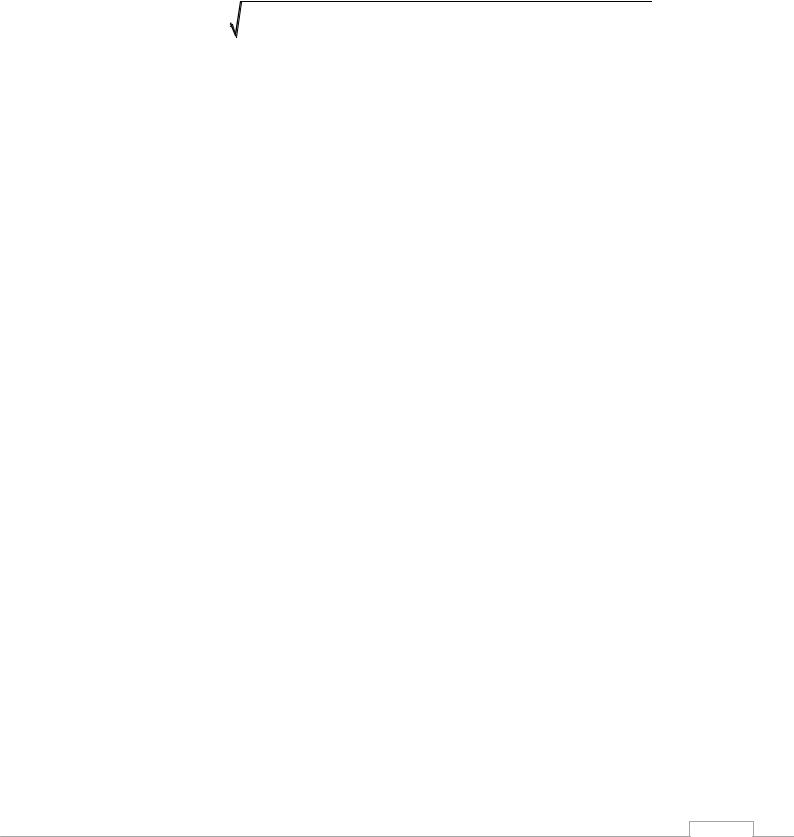
При данном методе расчета величина суммарной погрешности и величины элементарных погрешностей обработки определяются как случайные величины. Необходимо отметить, что зависимостью (12.2) следует пользо-
ваться, если элементарные погрешности независимы друг от друга.
Применительно к обработке на токарно-винторезных станках расчетная формула для определения суммарной погрешности обработки наружных цилиндрических поверхностей имеет вид
|
1 |
|
|
|
|
|
|
K2 y 2 K3 н 2 K4 изм 2 K5 ст 2 K6 Т 2 |
(12.3) |
||
К |
|||||
|
|
|
|
где y - погрешность, возникающая от колебания упругих деформаций технологической системы под влиянием нестабильности нагрузок (сил резания, сил инерции и др.), действующих в системе переменной жесткости; н – погрешность настройки технологической системы на выдерживаемый размер;
изм – погрешность вызванная размерным износом режущего инструмента;
ст – погрешность станка с учетом его износа за период эксплуатации; Т –
погрешность, вызванная колебанием, объемных и контактных деформаций элементов технологической системы вследствие их нагрева при резании, трения подвижных элементов системы, изменения температуры окружающей
среды; |
K2 , K3 , K4 , K5 , K6 – |
коэффициенты |
относительного |
рассеяния; при |
|||||||
расчетах можно принять K2 K3 |
1 и K4 |
K5 K6 1, 73 , а коэффициент |
|||||||||
1 |
следует выбирать с учетом выбранной гарантированной надежности Рr : |
||||||||||
|
К |
||||||||||
|
|
|
|
|
|
|
|
|
|
|
|
|
Рr |
|
… |
0,7 |
0,8 |
0,9 |
0,95 |
0,98 |
0,9977 |
0,9995 |
0,99999 |
1 |
|
… |
0,347 |
0,427 |
0,548 |
0,683 |
0,775 |
1,000 |
1,167 |
1,470 |
|
|
|
|
|||||||||
|
К |
|
|||||||||
|
|
|
|
|
|
|
|
|
|
|
В формуле (12.3) принято, что Si = 1.
Погрешность формы в продольном сечении учитывается отдельным слагаемым Ф путем суммирования его с погрешностью диаметрального разме-
ра, вычисленного для определенного поперечного сечения. Иногда определяют смешанным методом расчета. Принимают, что
некоторые параметры изменяются детерминированно, поэтому их суммирование выполняют по методу максимума-минимума, для других применяют вероятное суммирование.
Рассмотрим, как определяются элементарные погрешности, входящие в формулу (12.3).
Погрешность от колебания упругих деформаций технологической системы y возникает в результате смещения элементов технологиче-
ской система под действием сил. Её определяют как колебание упругих деформаций системы в различных сечениях обрабатываемой детали [5]:
84
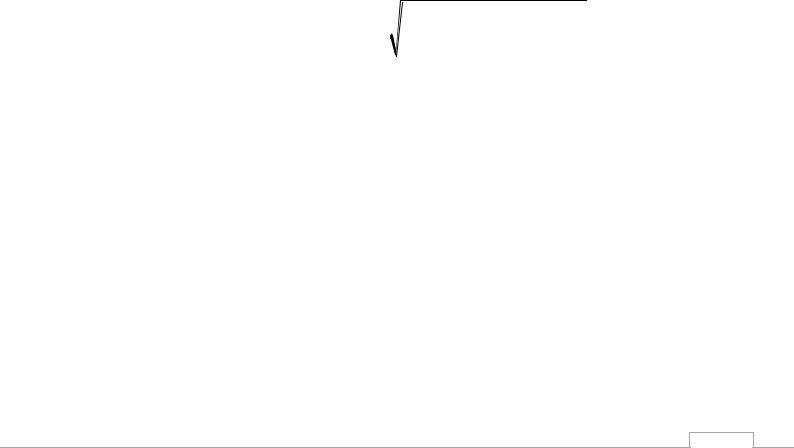
у уmax ymin Wmax Py max Wmin Py min , |
(12.4) |
где уmax , ymin – предельные смещения элементов технологической системы; Wmax , Wmin – предельные податливости системы; Py max – предельные
значения составляющей силы резания, совпадающей с направлением выдерживаемого размера.
Колебания силы Py при обработке партии деталей вызваны непостоян-
ством механических свойств материала и глубины резания. При обработке одной детали это колебание связано с неравномерным распределением припуска по противолежащим участкам обрабатываемой поверхности в поперечном и продольном сечениях.
Величины W приведены в [5], значение Py определяют из зависимо-
сти, приведенной в [6].
В данной работе значение у берется по данным лаб. работы № 7.
Погрешность настройки технологической системы возникает в результате того, что при каждом регулировании технологической системы или смене инструмента невозможно обеспечить постоянство положения его режущих кромок, а это приводит к колебанию рабочего настроечного размера.
Величина н зависит от погрешности регулирования p положения инструмента (по лимбу, эталону, жесткому упору, индикатору и т. п.) и по-
грешности измерения размера детали изм . |
|
|
|
|
|
|
|
|
Для поверхности вращения с учетом того, что н |
и p |
относятся к ра- |
||||||
диусу, а изм – к диаметру, н рассчитывается по формуле |
|
|||||||
|
|
|
|
|
|
|
|
|
н |
Kр р |
2 |
|
|
|
2 |
|
|
|
Kи |
|
изм |
(12.5) |
||||
|
|
|
|
2 |
|
|
где Kр = 1,14–1,73 и Kи = 1 (учитывают отклонение закона распределения величин р и изм от нормального закона распределения).
Значения р и изм приведены в [5]. В данной работе значение н бе-
рется по данным лаб. работы № 9.
Погрешность, получаемая в результате размерного износа инструмента и , рассчитывается по формуле
и |
|
L |
0 |
, |
(12.6) |
|
|
|
|||||
1000 |
||||||
|
|
|
|
где L – полная длина пути резания для партии деталей, 0 – относительный
размерный износ, мкм/км.
Полную длину пути резания рассчитывают по формуле
85

L LN Lн , |
(12.7) |
где LN - длина пути резания для партии деталей; Lн |
- длина начального пути |
резания, Lн = 1000 м. |
|
Величина LN определяется из выражения: |
|
LN LД N , |
(12.8) |
где LД - длина пути резания при точении одной заготовки, м; N - число заготовок в партии, шт.
Длина пути резания LД рассчитывается по любой из двух зависимо-
стей:
|
LД v t0 |
|
|
|
|
(12.9) |
||
или |
LД |
|
|
D |
|
lД |
||
|
|
|
|
|||||
1000 |
S |
|||||||
|
|
|
|
(12.10)
где v – скорость резания, м/мин; t0 – основное технологическое время, мин; D – диаметр обрабатываемой поверхности, мм; S – подача, мм/об, lД – длина
обрабатываемой поверхности.
Величину v0 можно принимать по [5] или по экспериментальным данным (лаб. работа № 10).
Погрешности станка ст вызывают образование конусности вследствие
отклонения от параллельности оси шпинделя относительно направляющих поверхностей станины в горизонтальной плоскости. Величина конусообразности рассчитывается по формуле [5]
кон |
Ст |
lД |
(12.11) |
|
l |
||
|
|
|
где: Ст - допустимое отклонение от параллельности оси шпинделя направляющим поверхностям станины в плоскости выдерживаемого размера на длине l, мм; lД – длина обрабатываемой поверхности, мм. Допустимые отклонения
приведены в [5].
В рассматриваемой работе допустимые отклонения можно выбрать из табл. 12.1.
|
|
Таблица 12.1 |
|
|
|
|
Постоянство диаметра |
|
Наибольший диаметр |
|
|
в поперечном сечении |
в продольном сечении |
|
обработки |
(допуск круглости), мкм |
(допуск цилиндричности), |
|
|
мкм |
86
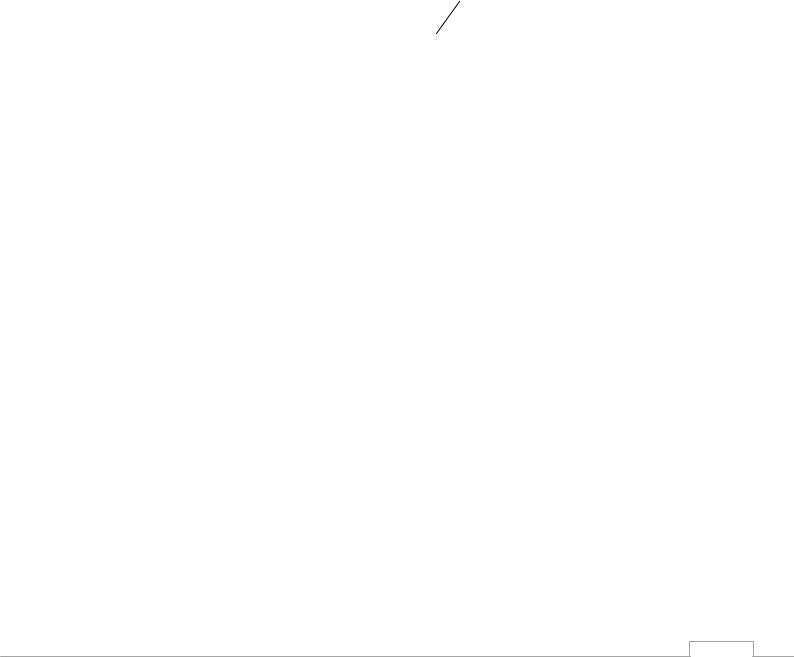
|
До 250 |
|
16 |
|
|
25 |
||
>250 < 400 |
|
20 на длине 100 км |
32 на длине 100 км |
|||||
> 400 < 600 |
|
25 |
|
|
40 |
|||
|
|
|
||||||
Погрешность от тепловых деформаций элементов технологической си- |
||||||||
стемы |
T |
для операции с жесткими допусками на обработку эта погреш- |
||||||
|
|
|
|
|
|
|
|
|
ность рассчитывается по формуле (12.5) |
|
|
|
|||||
|
|
|
|
T |
0,1 0, 4 |
|
. |
(12.12) |
|
|
|
|
|
|
|
В нашем случае величину погрешности T можно определить по экс-
периментальным данным лабораторной работы № 11.
Надежность обеспечения требуемой точности обработки заготовок характеризуется запасом точности данной операции, который определяется по формуле
T |
|
(12.13) |
|
где Т – допуск на обработку заготовки; – фактическое поле рассеяния размеров заготовок.
Величину поля рассеяния при различных законах распределения размеров обрабатываемых заготовок обычно берут как часть от величины среднеквадратичного отклонения , определённой на основе экспериментальных данных. Рекомендации по определению поля рассеяния даны в работе [4].
Поле рассеяния можно также приравнять к величине ожидаемой по-
грешности обработки, т. е. .
Если запас точности >1,0, то обработка заготовок может быть осуществлена без брака. При < 1,0 брак заготовок является весьма вероятным. При 1,2 процесс обработки считается надёжным.
Для всех законов распределения размеров условием обработки заготовок без брака является выражение
T или T |
(12.14) |
Вероятный процент брака в партии обработанных заготовок определяется суммой заштрихованных участков площади, ограниченной теоретической кривой распределения размеров при симметричном расположении её по отношению к полю допуска (рис.12.1).
87
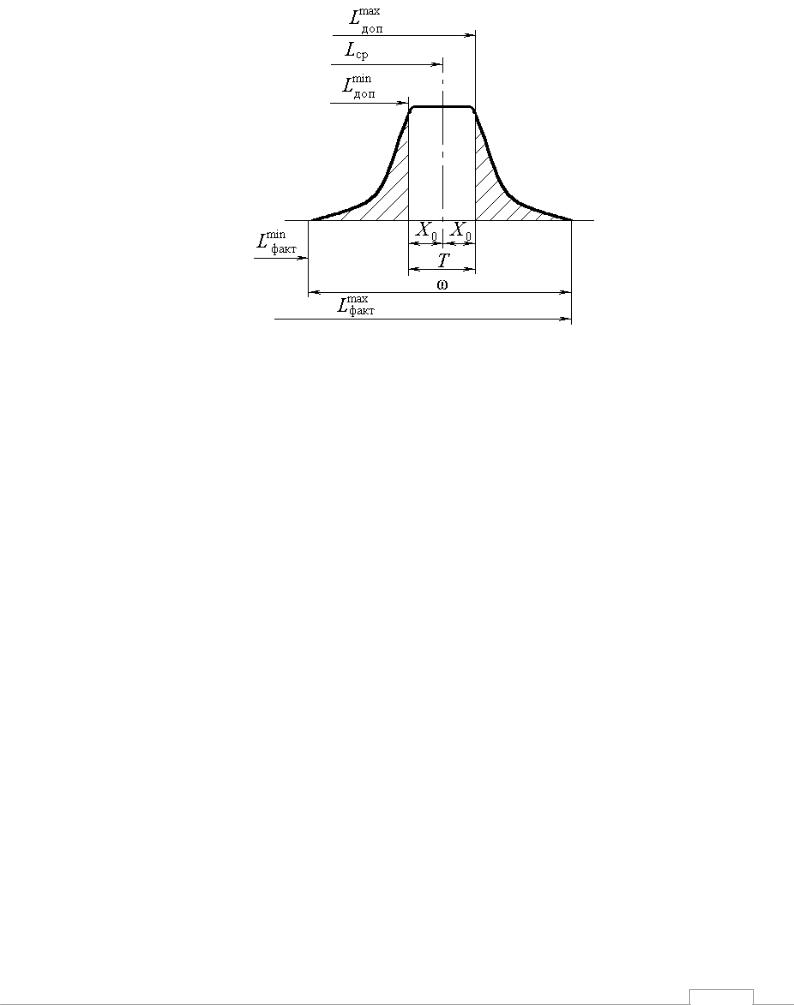
Рис. 12.1. Количество вероятного брака при симметричном расположении поля рассеяния, ограниченного кривой функции а(t) , относительно се-
редины поля допуска.
Lmaxдоп , Lminдоп – предельные допустимые размеры; Lmaxфакт , Lminфакт – предельные фактические размеры; X 0 – величина допустимого отклонения размеров, опре-
деляющая число годных заготовок; T – допуск на размер; – фактическое поле рассеяния размеров.
На рис. 12.2 изображена кривая функции а(t) . Эта функция характеризуется законом Гаусса с его параметрами и Lср , зависящими от точности вида обработки и технологической системы, и законом равной вероятности с параметром l (половина величины поля рассеяния).
Функцию можно рассматривать как результат равномерного смещения во времени вершины кривой Гаусса со средним квадратическим отклонением на величину параметра 2 l кривой распределения закона рав-
ной вероятности. Кривая функции а(t) приведена на рис. 12.2, где a0 – сред-
нее арифметическое значение размера в |
начальный момент времени; |
Lmax , Lmin – –предельные размеры деталей; |
Lср – средний размер детали; |
l – половина поля рассеяния для закона равной вероятности; на эту величину оказывают влияние продолжительность процесса обработки и систематические переменные погрешности, возникающие в ходе обработки.
Рассмотренный закон распределения характерен для механической обработки заготовок на настроенных станках.
88
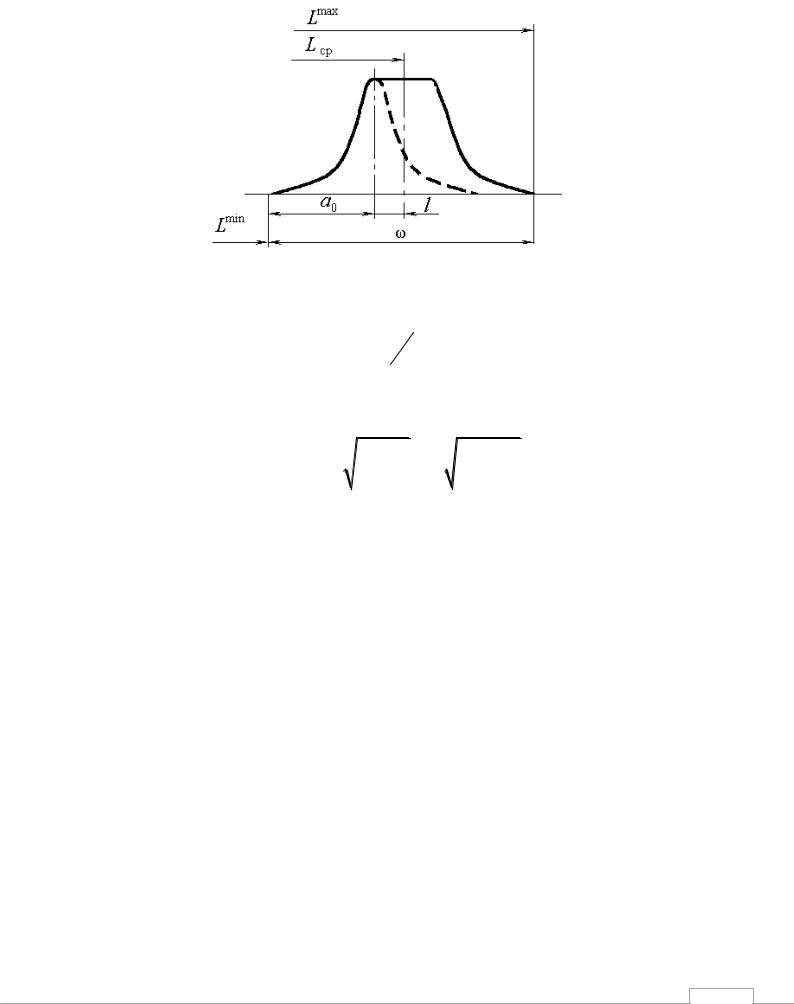
Рис. 12.2. Кривая функции а(t)
Форма кривой зависит от параметра a , определяемого из отношения
|
|
l |
. |
(12.15) |
a |
|
|
Среднеквадратичное отклонение функции
a |
2 |
l |
|
|
1 |
1 |
|
a2 |
(12.16) |
|
3 |
||||||||
|
3 |
|
|
|
|
Среднеарифметическое значение размера функции
Lср a0 l a0 a . |
(12.17) |
Функцию а(t) можно выразить в нормированном виде с помощью нормированного параметра распределения коэффициента риска, который определяется формулой
ta |
|
(L Lср ) |
|
Х |
0 |
, |
(12.18) |
||
|
ср |
|
а |
||||||
|
|
|
|||||||
|
|
|
|
|
|
|
где X 0 – допустимое отклонение размера, характеризующее число загото-
вок, размеры, которых находятся в пределах рассматриваемого поля допуска.
Возвращаясь к вопросу о нахождении количества годных заготовок, следует отметить, что число последних определяется площадью не заштрихованных областей, ограниченноых кривой и осью абсцисс на длине, равной
допуску T Lmaxдоп Lminдоп (рис 12.1). При симметричном расположении поля рассеяния относительно поля допуска (рис. 12.1) следует найти удвоенные
89
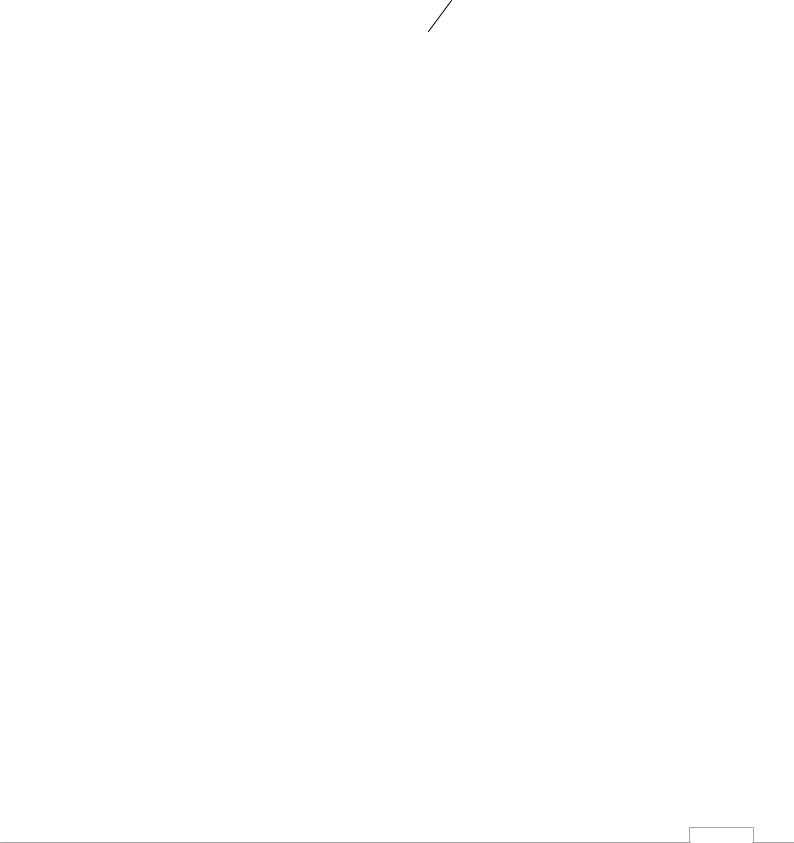
значения интеграла, определяющего половину площади, ограниченной кривой функции а(t) и абсциссой X 0 . Значение интеграла обозначается через Ф(ta , a ) . Значения функции табулированы в зависимости от величин ta и
a и приведены в табл. 12.2. Для случая, показанного на рис. 12.1. размеры
заштрихованных участков площади (а, следовательно, и долю брака) определяют последовательным расчетом ве-
личин: a – по формуле (12.15); X 0 T 2 и ta – по формуле (12.18).
По установленным значениям ta и a (табл. 12.2) находят выражаю-
щуюся в долях единицы половину общего числа годных заготовок (не заштрихованный участок площади на рис. 12.1, расположенный по одну сторону середины поля допуска), и рассчитывают общее количество бракованных заготовок в процентах по формуле
Qбр 100% 1 2Ф(ta , a ) . |
(12.19) |
Порядок выполнения работы
1.Для заданных условий, приведенных в табл. 12.2, и полученных результатов исследований размерного износа резца, его тепловых деформаций,
атакже результатов исследований жёсткости станка, влияния упругих деформаций станка на точность обработки и погрешности настройки выполнить следующее:
1.1.Определить погрешность y по формуле (12.4). Предельные сме-
щения элементов технологической системы берут из данных лаб. работы № 8
. Они равны половине диаметров детали после обработки, полученных вследствие явления копирования на участках заготовки с различной глубиной резания.
Таблица 12.2
|
Размеры обрабатываемой |
Поле до- |
Количество |
Среднеквадрати- |
||
Вариант |
детали, мм |
деталей в |
ческое отклоне- |
|||
пуска, мм |
||||||
|
Диаметр |
Длина |
партии, шт. |
ние, мм |
||
|
|
|||||
1 |
20 |
200 |
52 |
400 |
0,040 |
|
2 |
55 |
500 |
74 |
150 |
0,025 |
|
3 |
115 |
1000 |
37 |
50 |
0,010 |
|
4 |
30 |
300 |
62 |
300 |
0,025 |
|
5 |
85 |
700 |
87 |
80 |
0,010 |
90