
gusakov_v_g_ekonomika_organizatsiy_i_otrasley_agropromyshlen
.pdfются производства и производственные участки. Схема производственной структуры большинства льнозаводов республики представлена на рис. 3.12.
В настоящее время на льнозаводах выделяют следующие производства: основное, вспомогательное, обслуживающее, побочное и подсобное. До недавнего времени основное производство было представлено производством приготовления длинного и короткого волокна из льнотресты и производством приготовления тресты из льносоломки. В связи с изменившимися экономическими условиями на льнозаводах перерабатывают только льнотресту, поступающую от сельскохозяйственных производителей. Поэтому основная деятельность коллектива предприятия направлена на приготовление длинного и короткого волокна. В основном производстве выделяют следующие производственные участки: подсушки сырья; механической обработки; сортировки волокна; прессовки волокна. Вспомогательное производство включает в свой состав ремонтно-механический участок, энергетическое и паросиловое хозяйство. Обслуживающее производство представлено складским и транспортным хозяйством. На отдельных льнозаводах производят переработку отходов от основной деятельности. Поэтому здесь возможно производство кастроплит, нетканых материалов, смоляной пакли, которые образуют побочное производство. Отличительной особенностью деятельности льнозаводов в последние годы является наличие подсобного производства. В связи с нехваткой сырья для полной загрузки производственных мощностей льнозаводы вынуждены самостоятельно заниматься возделыванием и уборкой льна. Исходя из этого, на льнозаводах создается материально-техническая база для этого нехарактерного до последнего времени (1998 г.) вида деятельности.
Эффективность производственного процесса зависит не только от типа производства, но и от особенностей технологического процесса изготовления продукции, способов обработки сырья. На характер технологического процесса, а следовательно и на его эффективность, большое влияние оказывает качество сырья, поступающего на предприятие. В зависимости от качества сырья и принятого способа его обработки разрабатывают план технологического процесса получения готовой продукции, в котором предусматривают содержание и последовательность технологических операций, определяют цепочку технологического оборудования, устанавливают параметры протекания процесса на каждой технологической операции.
При заготовке и переработке стланцевой тресты технологический процесс изготовления волокна на льнозаводе состоит из 10–11 технологических операций: сортировка сырья; подсушивание; слоеформирование; механическая обработка тресты; съем длинного волокна; сортировка длинного волокна; механическая обработка отходов трепания (включая подсушивание и трясение); сортировка короткого волокна; увлажнение волокна; прессование короткого волокна.
Параметры технологического процесса обработки сырья должны устанавливаться и регулироваться в зависимости от номера перерабатываемой тресты, с учетом ее физико-механических свойств и степени вылежки (вымочки). От того, насколько выдерживаются параметры технологического процесса обработки сырья, зависят технико-экономические показатели работы льнозавода (количество и качество вырабатываемого волокна, степень использования
521
технологического оборудования, уровень производительности труда, себестоимость продукции и рентабельность производства).
Втехнологии необходимо предусматривать возможное упрощение процесса обработки, широкое применение поточных методов работы, использование совершенного высокопроизводительного оборудования и механизмов, заменяющих ручной труд.
Длительность производственного цикла на льнозаводах, где не имеют места естественные процессы сушки, невелика — 1–2 дня.
Если проводится естественная сушка тресты на воздухе и отлежка длинного волокна, то длительность производственного цикла увеличивается в несколько раз. Например, процесс отлеживания длинного волокна длится по условиям технологии 10–12 дней, следовательно, общая длительность производственного цикла получения волокна будет составлять 11–14 дней.
На льнозаводах поточные линии имеют черты как непрерывно поточного, так и прямопоточного производства.
Агрегирование мяльных и трепальных машин, с целью очистки волокна от древесины, позволило ликвидировать перерывы при механической обработке тресты. Установление перед мяльно-трепальными агрегатами слоеформирующих механизмов и сушильных машин позволило создать поточную линию получения длинного волокна.
Впоточные линии для получения короткого волокна (из отходов трепания, путанины и тресты низкого сорта) наряду с куделеприготовительными агрегатами, которые производят очистку от костры и паремхимных тканей, установлены трясильные и сушильные машины. Передача отходов трепания от мяльно-тре- пального агрегата на линии приготовления короткого волокна с помощью пневмотранспортера объединяет обе линии в единый поток. Это увеличивает непрерывность процесса и сокращает длительность производственного цикла.
На многих льнозаводах сортировка и прессовка длинного и короткого волокна осуществляется в потоке, что позволяет сократить затраты ручного труда на сортировку и производственные площади.
Синхронизация операций, включенных в поточную линию, достигается изменением параметров технологического процесса, регулировкой скоростей рабочих органов машин, перераспределением рабочей силы и т. д.
Поточные формы организации производства, особенно непрерывно-по- точные, имеют ряд преимуществ перед непоточными:
сокращается длительность производственного цикла; появляется возможность увеличения объемов производства на действую-
щих предприятиях без капитальных вложений на расширение производства; уменьшается объем незавершенного производства, вследствие чего сокра-
щается потребность предприятия в собственных оборотных средствах; уменьшаются производственные площади, необходимые для хранения по-
луфабрикатов во время их межоперационного пролеживания; высвобождаются рабочие, занимавшиеся внутризаводским перемещением
полуфабрикатов.
Врезультате этого повышается производительность труда, снижается себестоимость продукции, увеличиваются фондоотдача, прибыль, рентабельность, т. е. повышается эффективность производства.
522
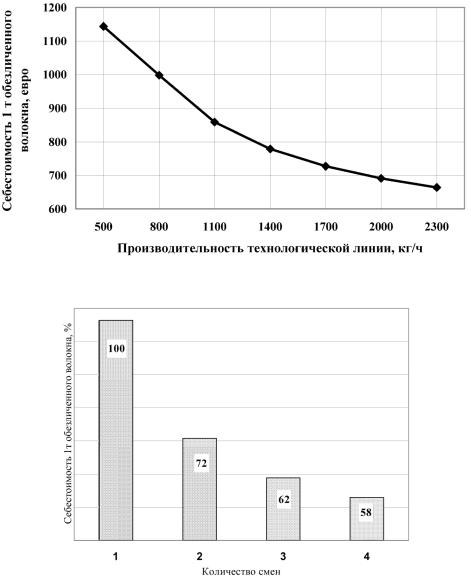
Рисунок 3.13. Зависимость себестоимости волокна от производительности технологической линии
Рисунок 3.14. Зависимость себестоимости 1 т обезличенного льноволокна от сменности работы технологической линии (работа в 4 смены осуществляется по скользящему графику)
Проведены расчеты по влиянию на эффективность производства льноволокна увеличения производительности технологической линии и сменности ее работы (при этом было сделано допущение, что во всех случаях выход длинного волокна остается величиной постоянной).
Полученные результаты, приведенные на рис. 3.13, 3.14. показывают, что с увеличением сменности работы предприятия и производительности технологической линии по пропуску льнотресты себестоимость волокна снижает-
523
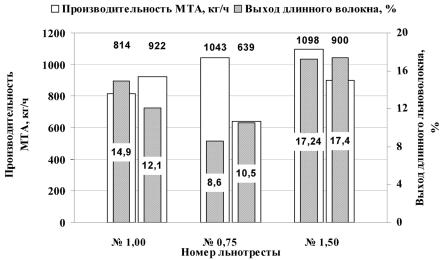
Рис. 3.15. Результаты контрольных разработок льнотресты по определению зависимости между выходом длинного льноволокна и производительностью МТА
ся. Однако увеличение сменности работы оборудования ограничено и не представляется в сложившихся условиях эффективным. Ограничение же производительности оборудования обусловлено его физическим состоянием и кон струкцией, т. е. имеет возможность для совершенствования.
Еще одним из путей повышения эффективности работы льноперерабатывающего предприятия является увеличение выхода длинного волокна. В этом случае затраты на производство 1 т обезличенного волокна примерно остаются величиной постоянной, а стоимость волокна возрастает за счет увеличения удельного веса длинного волокна в общем объеме волокна, выработанного предприятием.
Замечено, что на практике, как правило, повышение производительности по пропуску льнотресты сорто-номером выше 1,0 приводит к некоторому снижению выхода длинного волокна. На рис. 3.15 приведены данные контрольных производственных разработок в 2003—2004 гг. однородной льнотресты на мяльно-трепальном агрегате МТА-2Л.
На наш взгляд, такая тенденция объясняется тем, что повышение производительности на существующих линиях достигается увеличением линейной плотности слоя льна, скоростных режимов транспортирующих органов МТА и повышением интенсивности обработки сырья. Однако это влечет за собой больший выход недоработки или потери волокна с отходами трепания.
Оценка опыта зарубежных льноперерабатывающих предприятий показывает, что ведущие фирмы идут по пути снижения интенсивности обработки сырья, но не в ущерб производительности по пропуску льнотресты. Произ водительность современных линий бельгийского производства (Depoortere, Vanhauwaert) составляет примерно 2000 кг/ч льнотресты при соотношении выхода длинного и короткого льноволокна 70 : 30%. Это достигается за счет высокого качества исходного льносырья и применения смягчающей конст
524
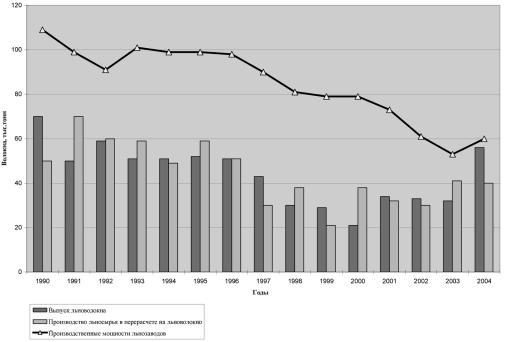
Рис. 3.16. Производственные мощности, производство и выпуск льноволокна
руктивно-технологической схемы МТА, предусматривающей по две секции на обработку комлевой и верхушечной части слоя стеблей в мяльной и трепальной машинах, что и позволяет сохранять высокую скорость транспортирования обрабатываемого сырья (скорость зажимного транспортера 70—
120м/мин).
Впоследние годы в республике наблюдается тенденция снижения производства льносырья, выпуска льноволокна и использования ресурсного потенциала льнозаводов. За анализируемый период (1990—2004 гг.) льнозаводы уменьшили выработку льноволокна в 1,3 раза, на 55% сократили производственные мощности, причем использование их составляет 60—80% (рис. 3.16).
Таблица 3.20. Экономические показатели эффективности выработки льноволокна, млн руб.
|
Выручка от реализации |
Себестоимость |
Прибыль (+), |
|
|
|||
|
льнопродукции |
реализованной |
Рентабельность, % |
|||||
|
убыток (–) |
|||||||
|
без НДС |
льнопродукции |
|
|
||||
Область |
|
|
|
|
||||
|
|
|
|
|
|
|
|
|
|
2003 |
2004 |
2003 |
2004 |
2003 |
2004 |
2003 |
2004 |
|
|
|
|
|
|
|
|
|
Брестская |
5656 |
7711 |
6229 |
8158 |
–571 |
–447 |
–9,2 |
–5,5 |
Витебская |
10822 |
17349 |
13865 |
21650 |
–3043 |
–4301 |
–21,9 |
–19,9 |
Гомельская |
2312 |
2905 |
3118 |
4246 |
–806 |
–1341 |
–25,8 |
–31,6 |
Гродненская |
10220 |
12955 |
10992 |
15226 |
–772 |
–2271 |
–7,0 |
–14,9 |
Минская |
7014 |
9877 |
8571 |
12046 |
–1557 |
–2169 |
–18,2 |
–18,0 |
Могилевская |
4261 |
7294 |
5039 |
7759 |
–778 |
–465 |
–15,4 |
–6,0 |
Всего по республике |
40287 |
58091 |
47814 |
69085 |
–7527 |
–10994 |
–15,7 |
–15,9 |
525

Рис. 3.17. Структура себестоимости 1 т льноволокна: 1 — стоимость льносырья; 2 — материалы; 3 — электроэнергия; 4 — заработная плата основных производственных рабочих с начислениями; 5 — содержание и эксплуатация оборудования; 6 — общезаводские расходы; 7 — прочие расходы; 8 — внепроизводственные расходы
Финансовое положение льноперерабатывающих предприятий остается сложным. Отпускные цены на льноволокно, поставляемое за счет госзаказа, покрывают затраты льнозаводов на выпуск льноволокна на 84,1%. Рента бельность производства в целом по республике в течение ряда лет остается на уровне ниже –15%, а в Гомельской области снизилась до –31,6% (табл. 3.20).
Применяемые в настоящее время технологии производства льноволокна и выработки другой продукции несовершенны. Большинство льнозаводов построено в послевоенные годы и оснащено в основном устаревшим оборудованием, которое в сравнении с зарубежными аналогами более материалоемкое и энергоемкое. Коэффициент износа активной части основных производственных фондов достигает 90—95%, а коэффициент их обновления не превышает 5%.
Из анализа сложившейся на практике структуры себестоимости льноволокна видно, что стоимость заготавливаемой льнотресты занимает около 38% (рис. 3.17).
Поэтому снижение затрат на льносырье остается первоочередной задачей во всей технологической цепи производства льноволокна.
Качественные параметры конечной продукции закладываются на протяжении всего технологического процесса, но наиболее важной является стадия производства сырья, т. е. льнотресты, и его первичная переработка.
В нашей стране почти вся треста получается биологическими способами: росяной мочкой при расстиле и мочкой в воде. При этом свыше 98% тресты, приготовленной сельскохозяйственными производителями, получают способом росяной мочки.
Способ приготовления тресты росяной мочкой известен давно. Одним из крупных недостатков его является трудность регулирования режима, так как он полностью зависит от внешних условий. Опыт сельскохозяйственных пред
526
приятий показывает, что расстил льносоломки, проведенный в августе, дает возможность своевременно получить тресту высокого качества. Кроме того, этот способ не требует никаких капитальных затрат.
Росяную мочку тресты проводят на луговых стлищах, на льнище. В основу росяной мочки положена жизнедеятельность микроорганизмов и их воздействие на основные ткани льняного стебля.
В процессе расстила и мочки разрушаются пектиновые вещества и освобождается волокно от окружающих тканей.
Основными факторами росяной мочки являются тепло, влага и свет. Стебли после обмолота (соломка) расстилают льноуборочным комбайном на поле равными рядами, где они вылеживаются 15–25 суток. Под действием плесневых грибков, тепла, света и влаги пектин и другие вещества стеблей разлагаются и освобождается волокно от окружающих тканей.
При приготовлении тресты в сельхозпредприятиях часто наблюдаются большие потери волокна, снижение его качества вследствие несвоевременного выполнения таких операций, как подъем тресты со стлищ, ее подсушивание.
Получить льняную тресту можно и путем мочки ее в воде. Правильно проведенная мочка льна, в сравнении с расстилом, может обеспечить получение волокна лучшего качества. Однако следует отметить, что мочка льна требует больших затрат труда на единицу продукции, чем расстил. Она может применяться в тех хозяйствах, где имеются удобные водоемы. При холодноводной мочке соломку в снопах, тюках, контейнерах погружают в водоем на 10–15 суток. В результате жизнедеятельности пектиносбраживающих бактерий лубяные волокна отделяются от тканей.
Используемые в практике способы первичной подработки льна-долгунца имеют тот недостаток, что после биологической обработки приходится высушивать большие массы сырья, затрачивая на это много ручного труда. Кроме того, мокрая льнотреста имеет невысокую прочность волокнистой ткани, которая легко расползается под действием натяжений, возникающих при механической обработке. Это обстоятельство существенно влияет на качество льноволокна.
4.2. Заготовка, хранение и подготовка сырья к подработке
Успех процесса заготовки льнотресты обусловлен двумя аспектами. В первую очередь, с целью обеспечения максимальной загрузки производственных мощностей льнозаводы для привлечения поставщиков сырья должны заключить с ними взаимовыгодные договоры контрактации. Во-вторых, подготовить техническую базу к началу заготовительного сезона.
Заводы и заготовительные пункты (отделения) в срок до 1 января соответствующего года заключают с поставщиками сырья контрактационный договор, в котором указываются вид, качество, количество, цена, стоимость, сроки и пункты сдачи продукции. Заводы при этом обязаны принимать
иоплачивать сырье в строгом соответствии с действующими стандартами
иценниками. Договор контрактации сдатчиком должен быть выполнен в отношении как качества, так и количества продукции. Если договор оказыва-
527
ется невыполненным в отношении качества сырья, то сельскохозяйственное предприятие обязано сдать большее его количество.
Льнозаводы выделяют средства до 30% стоимости сырья в порядке авансирования на приобретение сельскохозяйственными предприятиями, входящими в его сырьевую зону, семян, удобрений, средств защиты под лен и т. д. Кроме того, представители льнозавода систематически инструктируют сельхозпроизводителей по вопросам посева, ухода, уборки, обмолота, расстила и подготовки к сдаче льнопродукции. Они обеспечивают производителей сырья действующими инструкциями, стандартами и другой документацией, регламентирующей закупку льнотресты.
С целью стимулирования сельскохозяйственных предприятий, производящих льнотресту, установлены специальные правила оплаты этого сырья: за тресту № 1 и выше производится оплата по закупочной цене с надбавкой за стандартную льнотресту районированных сортов в размере 8%.
При засоренности льнотресты свыше 10% производится скидка с веса в размере 1% и скидка с закупочной цены 0,8% за каждый процент засоренности свыше 10%.
Доставка сырья оплачивается поставщику по тарифам от места погрузки (бригады сельскохозяйственных предприятий) до льнозавода заготовителем.
Невыполнение обязательств по договорам контрактации является грубым нарушением и влечет за собой ответственность.
До начала приемки сырья льнозаводы и заготовительные пункты проводят ряд мероприятий, связанных с заготовкой льнотресты, ее хранением и подготовкой к обработке. В первую очередь разрабатывается план рационального размещения сырья на территории завода или заготовительного пункта с учетом отдельных мест хранения в соответствии с ожидаемым объемом заготовок и графиком поступления сырья. План размещения сырья согласовывается с органами пожарного надзора и утверждается директором льнозавода.
В период подготовки к приемке сырья на льнозаводе или заготовительном пункте производят ремонт шох, складов, подъездных путей, подготавливают площадки для осмотра и оценки сырья, весовое хозяйство, средства механизации и прочий инвентарь. Штат работников укомплектовывают лаборантами, контрольными мастерами, весовщиками и необходимым количеством рабочих для обеспечения бесперебойной разгрузки транспорта и укладки сырья в местах хранения. Кроме того, подготавливают и вывешивают на видном месте стандартные образцы принимаемого сырья, закупочные цены, а также положение о порядке разрешения спорных вопросов по качеству сдаваемого сырья.
Сырье на льнозаводах хранится в шохах и скирдах. Льнотреста поступает на завод обычно осенью и хранится в течение нескольких месяцев на сырьевом складе.
Шоха представляет собой большой, открытый по бокам навес из сборного железобетона. Размеры и вместимость шох различны. Шоха размерами 144 × 24 × 8,4 м имеет вместимость 2500 т, а размерами 90 × 30 × 6,5 м — 1500 т. В шохи укладывают сырье наиболее высоких номеров. Укладка производится в штабеля, при этом стенки штабелей должны быть строго вертикальны.
528
Скирды на льнозаводах имеют в плане размеры (18–20) × (8–9) м; их высота 8–9 м, вместимость — до 100 т. На некоторых льнозаводах вместимость скирд увеличивают до 200 т (32 × 10 × 10 м).
Наилучшая сохранность сырья обеспечивается в шохах. Поэтому окупаемость их составляет менее 5 лет. Использование шох уменьшает площадь сырьевых складов, облегчает механизацию трудоемких работ.
Для механизированной подачи сырья при его укладке в местах хранения используют передвижные ленточные конвейеры ТЛПГ-2УМ и ТЛХ-18. Их производительность составляет 4 т/ч.
После окончания укладки сырья места хранения маркируют, т. е. указывают порядковый номер хранения, номер тресты, дату начала и окончания укладки, массу уложенного сырья, влажность, засоренность, селекционный сорт и фамилию ответственного за укладку лица.
Качество укладки сырья после завершения скирды или штабеля проверяет комиссия в составе директора, старшего контрольного мастера и лаборанта. Результаты проверки оформляются актом и заносятся в паспорт учета сырья. Комиссия проверяет состояние всех мест хранения на заводе (заготовительном пункте) не реже двух раз в месяц, а в весеннее время — не реже двух раз в декаду. Сырье с повышенной влажностью направляют на переработку в первую очередь до наступления теплой погоды.
Перед отправкой сырья на переработку на льнозаводах проводят сортировку стеблей и снопов. При сортировке отбраковывают сырье с повышенной влажностью, подгнившее и пораженное болезнями. Эту часть тресты перерабатывают отдельно.
4.3. Государственная поддержка отрасли
Определяющим приоритетом развития льноводства в республике является уровень государственной поддержки отрасли. Постановлением Совета Ми нистров Республики Беларусь «О дополнительных мерах по развитию льноводства в республике на 2004—2006 годы» утверждены мероприятия, которыми предусматривается выделение финансовых средств за счет республиканского и местного бюджетов в течение трех лет в объеме 114216 млн руб. Из них на приобретение минеральных удобрений и средств защиты растений — 58%, на ремонт и приобретение техники для льносеющих хозяйств — 32% и на научное обеспечение отрасли — 2%. В среднем на 1 га посевов льна планируется инвестировать 230 долл. бюджетных средств, что позволит повысить урожайность льна до10—12 ц/га, довести ежегодное производство льноволокна до
60 тыс. т.
Таким образом, дополнительное инвестирование в льняной подкомплекс как со стороны государства, так и за счет использования собственных средств позволит повысить эффективность использования ресурсного потенциала льнозаводов
Ксожалению, пока в республике не сложилось ясного представления
отребуемых объемах производства волокна. Государственный заказ сформирован под потребность Оршанского льнокомбината в объеме примерно 10,0 тыс т длинного и почти 5,0 тыс. т короткого волокна. Потребности пред-
529
приятий легкой промышленности и самих переработчиков составляет не более 15,0 тыс т короткого льноволокна. Следовательно, объем производства в настоящее время превышает как минимум в два раза потребность. Воз можности и коммерческий опыт экспортно-сортировочных баз, которым доверено право монопольной реализации волокна за пределы республики, до настоящего времени можно характеризовать как очень скромные. Это обстоятельство порождает намерения руководства подотрасли сократить количество предприятий по первичной обработке льна. Однако подходы к решению таких задач неизвестны.
4.4. Производство котонизированного льноволокна
Производство котонизированного льноволокна в республике организовано в основном на двух предприятиях: ОАО «Несвижский льнозавод» и ГРУПП «Гронитекс», суммарная производственная мощность которых по выпуску такой продукции составляет 2700 т/год. Смонтированная на ОАО «Несвижский льнозавод» линия переработки короткого льноволокна фирмы «Ля Рош» (Франция) мощностью 1100 т/год работает по принципу штапелирования, т. е. резки исходного сырья на определенную длину. Продукция хорошо используется в прядении шерсти, химических волокон и их смесей в разных сочетаниях. Ткани из такой пряжи в первую очередь предназначены как отделочный материал для мебельной, автомобильной и авиационной промышленности. Установленная на ГРУПП «Гронитекс» технологическая линия фирмы «Темафа» (Германия) мощностью 1600 т/год работает по принципу расщепления волокон и обеспечивает более высокое качество сырья, имеющего толщину (текс), более близкую к хлопку, а поэтому котолен, полученный на линии «Темафа», используется преимущественно в хлопкопрядении для производства бытовых тканей и трикотажных изделий.
В то же время за последние пять лет (1999—2004 гг.) производственный потенциал ОАО «Несвижский льнозавод» в среднем использовался на 36,7%, ГРУПП «Гронитекс» — на 55,0%. Суммарный коэффициент использования мощностей составил в 2004 г. только 34,6% (табл. 3.21).
Таблица 3.21. Производственные мощности по выпуску котонизированного льноволокна
и уровень их использования в 2004 году
Предприятие |
Среднегодовая |
Выпуск продукции, т |
Коэффициент использо- |
|
мощность, т |
вания мощности, % |
|||
|
|
|||
|
|
|
|
|
ОАО «Несвижский льнозавод» |
1100 |
77,5 |
7,0 |
|
ГРУПП «Гронитекс» |
1600 |
856 |
53,5 |
|
Итого |
2700 |
933,5 |
34,6 |
Столь низкая загрузка производственных мощностей по выпуску котольна обусловлена его неконкурентоспособностью из-за несовершенства технологического процесса, незначительного ассортимента изделий, ограниченностью сферы применения, в результате производственный потенциал функционирует крайне неэффективно. Согласно проведенным расчетам, при минимальных затратах на заработную плату 4%, электроэнергию 8,8% цена 1 т котони-
530