
по трэс
.pdf
1. Классификация объектов производства, выбор заготовок, сортамента и т. д. Для детали важно определить соотношение длины и диаметра (L/d). Если L/d = 1, то детали равноразмерные (кодируются 1), если L/d > 1, то детали стержневые (кодируются 2).
соответствии с классификатором ЕСКД установлено 100 классов изделий. Каждый класс содержит сетку подклассов и групп, классификационные таблицы подгрупп и видов. Обозначение классификационного кода строится следующим образом:
|
. |
X X |
X X |
X |
Х. |
001 |
||||||
Шифр предприятия |
|
|
|
|
|
|
|
|
|
|
|
|
|
|
Класс |
|
|
|
|
|
Вид |
Порядковый номер разработки |
|||
|
|
|
|
|
|
|
Подгруппа |
|
|
|||
|
|
|
|
|
Группа |
|
|
|
|
|||
|
|
|
|
Подкласс |
|
|
|
|
|
|
Рис.1.8. Обозначение классификации кода
Технологическая классификация построена как многоаспектная и является продолжением и дополнением классификации деталей по конструктивным признакам. В технологическом классификаторе (ТК) устанавливается 14-значная структура технологического кода детали, составленного из двух частей: кода классификационных группировок основных признаков (постоянная часть) и кода классификационных группировок признаков, определяющих вид детали (переменная часть). Таким образом, структура полного конструкторскотехнологического кода детали, составленного из обозначения и технологического кода, имеет следующий вид:
. Х ХХХХХ. ХХХ. ХХХХХХ. ХХХХХХХХ
Обозначение |
Технологический код |
Рис.1.9. Структура полного конструкторско -технологического кода детали
2.Выбор технологических баз и способов фиксации деталей. Технологические базы используются в процессе изготовления для определения положения заготовки или детали при обработке относительно инструмента. При базировании соблюдают основные правила: единство конструкторских, технологических и измерительных баз; постоянство баз, т. е. использование одной и той же базы для обработки наибольшего числа поверхностей. При выборе схемы базирования детали прежде всего решают вопрос о том, каких степеней свободы должна лишиться деталь, соприкасаясь с установочными элементами приспособления, какие перемещения и повороты не отразятся на выдерживаемых размерах. Базой должна быть поверхность, от которой размер задается с наименьшим допуском.
3.Анализ типовых ТП и определение последовательности и содержания операций данного ТП (маршрут обработки или сборки). На основе анализа типовых ТП сборки блоков (ОСТ 4ГО.054.267) и перспективных
ТП по научно-технической литературе разрабатывают 2 — 3 варианта маршрутной технологии, руководствуясь следующим:
∙ в поточном производстве разбивка процесса на операции определяется тактом выпуска, причем время выполнения каждой операции должно быть равно или кратно такту;
4357

∙предшествующие операции не должны затруднять выполнение последующих;
∙на каждом рабочем месте должна выполняться однородная и технологически законченная работа;
∙после наиболее ответственных операций, а также после регулировки или наладки предусматривают контрольные операции.
4.Выбор технологического оборудования для двух либо трех вариантов ТП и расчет оптимального варианта по технико-экономическим показателям (см. § 1.5).
Рис.1.10. График загрузки оборудования
5.Выбор средств технологического оснащения или проектирование специализированной оснастки в соответствии с РТМ, банками данных (БД).
6.Расчет режимов обработки, нормирование операций ТП, определение среднего коэффициента загрузки оборудования:
Kз = tо / tшт ,
где tо, tшт — основное и штучное время работы.
Для наглядного представления о средней загрузке оборудования на линии или участке строят графики загрузки (рис. 1.7). По горизонтальной оси графика записывают модели технологического оборудования по операциям процесса, по вертикали откладывают значения коэффициента загрузки в процентах, а также указывают среднее значение коэффициента загрузки оборудования на линии, нормативные значения которого зави-
сят от типа производства: в массовом 0,65 < Кз.ср < 0,75, серийном 0,75 < Кз.ср < 0,85, мелкосерийном 0,8 < Кз.ср
< 0,9. При низких значениях коэффициента загрузки рекомендуется загружать оборудование сборочными единицами других партий блоков.
Коэффициент использования оборудования по основному (технологическому) времени определяется как отношение основного времени То к штучному Тшт для массового типа производства или штучнокалькуляционному Тшт.к для серийного производства:
Ко = То / Тшт. к .
7.Определение квалификации и профессий исполнителей по характеру выполняемой работы.
8.Выбор средств автоматизации ТП и внутрицехового транспортирования. В массовом и крупносерийном производстве применяют конвейеры различных типов, которые автоматически транспортируют изделия в места складирования. В серийном производстве используют робототехнологические комплексы (РТК) или линии (РТЛ).
9.Организация производственного участка и составление технологических планировок. В выбранном масштабе (1:50, 1:100) делают планировку будущего участка без оборудования. При этом обязательно указы-
4358
вают перегородки, окна, двери, колонны, вентиляционные шахты, силовые щиты энергоснабжения, противопожарные средства.
При определении места каждого производственного участка необходимо учитывать в первую очередь технологические, санитарно-гигиенические (отдаленность производственных участков от бытовых помещений), противопожарные требования и требования по взрывобезопасности (категорию помещений).
На отдельном листе в соответствии с масштабом рисуют (в плане) оборудование и рабочие места в рассчитанном количестве, затем вырезают и накладывают на планировку. Группируя оборудование и рабочие места, методом аппликаций подбирают подходящий вариант технологической планировки.
Планировку можно признать качественной, если учтены следующие требования:
∙технологический поток изготовления изделий последовательный;
∙все транспортно-погрузочные и складские работы входят в общий технологический поток;
∙транспортно-складские работы максимально механизированы и автоматизированы;
∙планировка обеспечивает сохранность материальных ценностей, а также возможность учета деталей, полуфабрикатов, готовых узлов и изделий;
∙использовано перспективное и технологическое оборудование;
∙капитальные затраты являются оптимальными, а окупаемость оборудования укладывается в нормативы.
10.Оформление ТД на разработанный ТП в виде комплекта документов. При серийном производстве и маршрутно-операционном типе ТП комплект ТД включает:
1) титульный лист (ГОСТ 3.1105—74);
2) |
ведомость технологических документов (ГОСТ 3.1122—84, формы 4 и 4а); |
|
3) |
комплектовочную карту (ГОСТ 3.1123—84, формы 6 и 6а); |
|
4) |
маршрутные карты (ГОСТ 3.1118—82, |
формы 1 и 1а); |
5) |
ведомость оснастки (ГОСТ 3.1122—84, |
формы 2 и 2а); |
6) |
ведомость операции контроля (ГОСТ 3.1105—74, форма 3). |
При крупносерийном или массовом производстве и операционном типе ТП комплект ТД включает:
1) |
титульный лист (ГОСТ 3.1104—81); |
|
2) |
ведомость технологических документов (ГОСТ 3.1122—84, формы 4 и 4а); |
|
3) |
комплектовочную карту (ГОСТ 3.1123—84, формы 6 и 6а); |
|
4) |
маршрутные карты (ГОСТ 3.1118—82, |
формы 2 и 2а); |
5) |
операционную карту сборки (ГОСТ 3.1407—82, формы 3 и 3а или 2 и 2а); |
|
6) |
карту эскизов (ГОСТ 3.1105—84, формы 7 и 7а); |
|
7) |
ведомость оснастки (ГОСТ 3.1122—84, |
формы 3 и 3а); |
8)операционную карту контроля (ГОСТ 3.1502—74).
1.5.ВЫБОР ОПТИМАЛЬНОГО ВАРИАНТА ТЕХНОЛОГИЧЕСКОГО ПРОЦЕССА
При выборе оптимального варианта ТП используют технико-экономические критерии — экономичность и производительность. Экономичным считается процесс, который при заданных условиях обеспечивает минимальную технологическую себестоимость. Производительность соответствует наименьшим затратам живого труда и обеспечивает быстрый выпуск продукции в плановые сроки.
Технологическая себестоимость изготовления партии изделии
C = A N + B , |
(1.1) |
4359
где А — текущие затраты на одно изделие; N — программа выпуска, шт.; В — единовременные затраты на программу.
Текущие затраты складываются из следующих составляющих:
А = М + З + П ,
где М — затраты на основные материалы; З — заработная плата производственных рабочих; П — расходы на эксплуатацию оснастки и оборудования.
Затраты на основные материалы рассчитываются с учетом возвратных отходов:
N |
N |
М = ∑mi qi |
− ∑m j q j , |
i =1 |
j =1 |
где N — программа выпуска; mi — масса i-го материала в изделии; qi — стоимость этого материала; mj — масса отходов j-го материала; qj — стоимость этих отходов.
Заработная плата производственных рабочих
M
З= ∑Кз.п Тшт i Si ,
i=1
где М — число операций; Кз.п — коэффициент к заработной плате; Тшт i — штучное время выполнения i-й операций, нормо-ч; Si — часовая тарифная ставка рабочего по данной операции.
Коэффициент к заработной плате определяется так:
K з.п = K1 K 2 K 3 ,
где K1 = P / m — коэффициент многостаночного обслуживания; Р — число рабочих; m — число станков, ко-
торые обслуживает один рабочий; К2 — коэффициент, учитывающий перевыполнение нормы (1,1—1,2); К3 — коэффициент, связанный с дополнительной оплатой, включающей отчисления на социальное страхование,
отпуска и т.д. (1,3—1,5).
Расходы на эксплуатацию оборудования П берутся в процентах к основной заработной плате рабочих и включают затраты на вспомогательные материалы, электроэнергию, амортизацию оборудования, текущий ремонт.
Единовременные затраты В складываются из двух статей: заработной платы наладчиков Зн и затрат на основное технологическое оборудование Со:
B = Зн + Со ,
k
Co = ∑Ci Ki ,
i =1
где k — количество единиц оборудования; Сi— стоимость единицы оборудования; Кi — коэффициент амортизации.
Коэффициент амортизации зависит от сложности технологического оснащения и составляет: 1,0 — 2,0 для простого, 0,7 — 0,8 для средней сложности, 0,4 — 0,5 для сложного оснащения.
Заработная плата наладчиков технологического оборудования
|
k |
|
Зн = ∑ K з.п Tп.з i Sн i H , |
|
i=1 |
где k — количество наладчиков; Тп.з i — |
подготовительно-заключительное время по данной операции; Sн i — |
часовая тарифная ставка наладчика; Н — |
число наладок оборудования. |
Уравнение технологической себестоимости единичной операции единицы продукции
Cоп = A + B / N .
4360
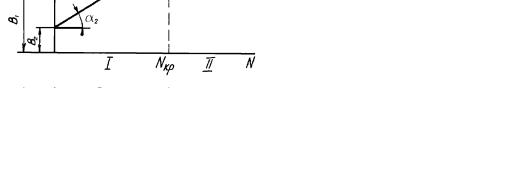
Эту зависимость можно представить в виде гиперболы, асимптотически приближающейся к оси N, и выделить в ней три участка (рис. 1.11): мелкосерийное, серийное, крупносерийное и массовое производство. Наиболее сильно программа выпуска влияет на технологическую себестоимость в мелкосерийном производстве.
Для выбора оптимального варианта ТП по себестоимости строят, используя уравнение (1.1), графические зависимости себестоимости годовой программы по двум вариантам (рис. 1.12):
C1 = А1 N + B1, |
(1.2) |
||||
C |
2 |
= А N + B , |
|
||
|
2 |
2 |
|
|
где A1 = tgα1 — постоянные текущие затраты, в данном случае А1>A2, В2>B1.
Для нахождения Nкр, при котором себестоимость по обоим вариантам равны: С1=С2, решим систему урав-
нений (1.2):
A1 Nкр + B1 = А2 Nкр + B2 ,
откуда Nкр = (B2 − B1) /( A1 − A2 ) .
Логический смысл сравнения вариантов заключается в том, что для варианта с большим уровнем автоматизации единовременные затраты будут выше по причине высокой стоимости оборудования, но текущие затраты меньше вследствие повышения производительности и снижения квалификации рабочих. Таким образом, если заданная программа меньше Nкр, то выбираем I вариант ТП, если программа выпуска больше Nкр, то выбираем II вариант.
Для выбора оптимального варианта ТП по производительности рассчитываем производительность труда по каждому из вариантов. Производительность — количество изделий, которое изготовлено за единицу времени (час, смену):
Q = |
|
Фд |
, |
n |
|
∑Tшт i i=1
где Фд — действительный фонд времени за плановый период; n — количество операций ТП; Тшт i — трудоемкость i-й операции.
Рис. 1.11. Зависимость технологической себестоимости |
Рис. 1.12. Сравнение двух вариантов ТП по себестоимости |
от программы выпуска
4361
При расчетах производительности труда необходимо различать штучно-калькуляционное и штучное время выполнения операции. Штучно-калькуляционное время
Тшт. к =Тшт + Тп.з / N ,
где Тп.з — подготовительно-заключительное время, которое затрачивается на ознакомление с чертежами, получение инструмента, на подготовку и наладку оборудования, оно затрачивается на всю программу выпуска.
Штучное время, затрачивается на каждое изделие,
Тшт = Тосн + Твсп + Тобсл + Тпер ,
где Тосн — основное время работы оборудования; Твсп — вспомогательное время на установку и снятие детали; Тобсл — время обслуживания и замены инструмента; Тпер — время регламентированных перерывов в работе.
Для сборочно-монтажного производства Тосн и Твсп объединяют в оперативное время Топ, а Тобсл+Тпер составляют дополнительное время, его задают в процентах от оперативного в виде коэффициентов. Согласно ОСТ 4ГО.050.012 "Нормирование сборочно-монтажных работ в производстве РЭА",
K |
2 |
+ K |
3 |
|
|
Тшт = Топ K1 |
|
|
+1 , |
||
|
100 |
|
|||
|
|
|
где К1 — коэффициент, зависящий от сложности аппаратуры и типа производства; К2 — коэффициент, учитывающий подготовительно-заключительное время и время обслуживания в процентах от оперативного; К3 — коэффициент, учитывающий долю времени на перерывы в работе в процентах к оперативному времени и зависящий от сложности выполняемой работы и условий труда.
Значения коэффициентов К1 и К2 выбирают по табл. 1.2 в зависимости от типа производства, К3 — по табл. 1.3.
Табл. 1.2. Значения коэффициентов К1 и К2 в зависимости от типа производства
Тип производства |
|
|
|
К1 для аппаратуры |
|
|
|
К2, % |
|
|
|
|
|
|
|
|
|
|
|
2-го поколения |
|
3-го поколения |
|
4-го поколения |
|
|
|
|
|
|
|
|
|
|
|
Индивидуальное |
1,3 |
|
1,8 |
2,0 |
|
10 |
||
Мелкосерийное |
1,2 |
|
1,5 |
1,8 |
|
9,6 |
||
Серийное |
1,0 |
|
1,2 |
1,5 |
|
7,6 |
||
Крупносерийное |
0,75 |
|
0,9 |
1,12 |
|
5,4 |
||
Массовое |
0,70 |
|
0,85 |
1,05 |
|
3,7 |
||
|
|
|
|
|
|
|
|
|
|
Табл. 1.3. Значения коэффициента К3 в зависимости от условий работы |
|
||||||
|
|
|
|
|
|
|
|
|
|
|
|
Характер работ |
|
К3, % |
|
||
|
|
|
|
|
|
|
|
|
|
|
Простые: |
|
|
|
|
|
|
|
|
Легкие |
|
|
|
3 |
|
|
|
|
Средние |
|
|
|
5 |
|
|
|
|
в неблагоприятных условиях |
|
6 |
|
|
||
|
|
в тяжелых условиях |
|
9 |
|
|
||
|
|
с большим зрительным напряжением |
|
12 |
|
|
||
|
|
Тяжелые или в особо неблагоприятных условиях |
|
16 |
|
|
||
|
|
Особо тяжелые и в неблагоприятных условиях |
|
20 |
|
|
||
|
|
|
|
|
|
|
|
|
Для выбора оптимального варианта ТП составляют два уравнения для вычисления суммарного штучнокалькуляционного времени сравниваемых вариантов в соответствии с технической нормой:
4362

m |
m |
m |
n |
n |
n |
∑ Тшт.к i |
= ∑ Тшт i |
+ ∑ Тп.з i / N , |
∑ Тшт.к i |
= ∑ Тшт i |
+ ∑ Тп.з i / N , |
i =1 |
i =1 |
i =1 |
i=1 |
i=1 |
i=1 |
где m, n — число операций по вариантам. Тогда критический размер партии изделий
|
m |
n |
|
|
∑ Тп.з i |
− ∑ Тп.з i |
|
Nкр = |
i =1 |
i =1 |
. |
n |
m |
||
|
∑ Тшт i |
− ∑ Тшт i |
|
|
i =1 |
i =1 |
|
Если вариант ТП отличается большим уровнем автоматизации, то ему соответствует большее суммарное подготовительно-заключительное время вследствие сложности подготовки оборудования и одновременно меньшее суммарное штучное время.
Ориентировочно подготовительно-заключительное время на всю годовую программу
Тп.з = Тп.з. см С Др ,
где Тп.з. см — сменная норма подготовительно-заключительного времени; С — количество смен; Др — количество рабочих дней в плановый период.
Сменная норма подготовительно-заключительного времени определяется инструкцией по эксплуатации и выражает готовность оборудования на начало ТП (табл.1.4).
Табл. 1.4. Укрупненные нормы подготовительно-заключительного времени
Тип оборудования |
ТП.З. СМ, мин |
|
|
Простая оснастка |
1—5 |
Оснастка средней сложности (с пневмоили электроприводом) |
10—15 |
Сложная технологическая и регулировочная оснастка |
15—30 |
Полуавтоматы |
15—25 |
Сложное автоматическое оборудование |
20—30 |
Микропроцессорное оборудование, управляемые роботы |
30—40 |
Установки волновой пайки |
50—60 |
|
|
Норму выработки рассчитывают для различных промежутков времени (час, смена и т.д.) в зависимости от типа производства. В серийном производстве сменная норма
H см = (Тсм − Тп.з ) / Тшт , |
(1.31) |
где Тсм — длительность смены (8 ч = 480 мин).
В массовом производстве при наличии наладчика и подаче деталей, сборочных единиц и материалов на рабочие места
Hсм = Тсм / Тшт .
При сборке на конвейерных линиях
|
|
= |
Ф |
= |
Тсм − (Тобс + Тпер ) |
|
H |
|
см |
|
. |
||
|
|
|
||||
|
см |
|
Топ |
|
То + Тв |
Пример. Определить сменную норму выработки на поточной линии сборки, если время выполнения всех сборочных операций 20
мин, обслуживание линии 12 мин, перерыв 8 мин. Р е ш е н и е . Находим: Hсм = 480 − (12 + 8) = 23 шт. 20
436
1.6. ПРОЕКТИРОВАНИЕ СБОРОЧНО-МОНТАЖНЫХ РАБОТ
Сборка представляет собой совокупность технологических операций механического соединения деталей, ЭРЭ и ИМС в изделии или его части, выполняемых в определенной последовательности для обеспечения заданного их расположения и взаимодействия. Выбор последовательности операций сборочного процесса зависит от конструкции изделия и организации процесса сборки.
Монтажом называется ТП электрического соединения ЭРЭ изделия в соответствии с принципиальной электрической или электромонтажной схемой. Монтаж выполняется с помощью печатных, проводных или тканых плат, одиночных проводников, жгутов и кабелей. Основу сборочно-монтажных работ составляют процессы формирования электрических и механических соединений.
Сборка по принципу концентрации операций заключается в том, что на одном рабочем месте производится весь комплекс работ по изготовлению изделия или его части. При этом повышается точность сборки, упрощается процесс нормирования. Однако большая длительность цикла сборки, трудоемкость механизации сложных сборочно-монтажных операций ограничивают применение такой формы рамками единичного и мелкосерийного производства.
Дифференцированная сборка предполагает расчленение сборочно-монтажных работ на ряд последовательных простых операций. Это позволяет легче механизировать и автоматизировать работы, использовать рабочих низкой квалификации. Сборка по принципу дифференциации операций эффективна в условиях серийного и массового производства. Однако чрезмерное дробление операций приводит к возрастанию потерь вспомогательного времени на транспортирование, увеличению производственных площадей, повышению утомляемости рабочих при выполнении несложных однообразных действий.
Параллельность сборки — одновременное выполнение частей или всего технологического процесса — приводит к сокращению производственного цикла. Использование этого принципа обусловлено конструкциями ЭА, степенью их расчленения на сборочные единицы. Наибольшими возможностями с технологической точки зрения обладают два вида обеспечения параллельности процессов: изготовление и сборка на многопредметных поточных линиях одновременно нескольких изделий; совмещение на автоматизированных поточных линиях изготовления деталей с их сборкой.
Непрерывность сборки предусматривает сокращение или полное устранение межили внутриоперационных перерывов, что достигается рациональным выбором ТП, соединением операций изготовления деталей с их сборкой, включением в ТП операций влагозащиты, контроля и регулировки.
Пропорциональность в организации ТП — это примерно одинаковая производительность на каждом рабочем месте, линии, участке, в цехе, что приводит к полному использованию имеющегося оборудования, производственных площадей и равномерному выпуску изделий, улучшает рациональное деление конструкции на сборочные единицы и унифицированность ее элементов.
Ритмичность предполагает выпуск в равные промежутки времени одинакового или возрастающего количества продукции за счет использования типовых и групповых процессов, их унификации и предварительной синхронизации операций.
Сборку ЭА проводят в три этапа. На п е р в о м э т а п е (механическая сборка):
∙выполняют неразъемные соединения деталей и сборочных единиц с шасси, рамой, платой (сваркой, пайкой, развальцовкой, склеиванием и т. д.);
∙устанавливают крепежные детали (угольники, кронштейны, лепестки и т. д.);
∙выполняют разъемные соединения частей блоков;
4364

∙закрепляют крупногабаритные (трансформаторы питания и т. д.) элементы собственным крепежом. На в т о р о м э т а п е (электрический монтаж):
∙выполняют заготовительные операции (подготовку проводов, жгутов, кабелей, выводов ЭРЭ);
∙устанавливают навесные ЭРЭ и микросхемы на платы;
∙выполняют электрические соединения (монтаж) в соответствии с электрической принципиальной или электромонтажной схемой;
∙ведут межблочные соединения (жгутами, разъемами);
∙контролируют качество монтажа.
На т р е т ь е м э т а п е (общая сборка изделия):
∙собирают шасси и переднюю панель;
∙устанавливают кожухи, закрепляют регулировочные элементы, ручки;
∙контролируют качество сборки и маркируют изделия;
∙выполняют регулировочно-настроечные работы.
По технологическим схемам сборки изделия выявляют число основных сборочных операций, определяют такт или ритм выпуска изделия:
Tв = 60 Фд (мин / шт.) .
N
Проектирование ТП сборочно-монтажных работ состоит из следующих этапов:
1)разработка технологической схемы сборки изделия, расчет коэффициента сборности и показателя расчлененности сборки;
2)выбор типа сборочного процесса, анализ типовых ТП и составление маршрута сборки;
3)выбор технологического оборудования, нормирование двух либо трех вариантов ТП и расчет оптимального варианта по технико-экономическим показателям;
4)выбор средств технологического оснащения и специализированной оснастки;
5)расчет режимов выполнения операций и коэффициентов загрузки оборудования;
6)определение квалификации и профессий исполнителей;
7)выбор средств автоматизации и механизации внутрицехового транспортирования;
8)организация производственного участка и составление планировки;
9)оформление комплекта ТД на разработанный ТП.
Сборка — это совокупность операций, в результате которых детали соединяются в сборочные единицы, блоки, стойки, системы и изделия. Простейшим сборочно-монтажным элементом является деталь, которая, согласно ГОСТ 2101—68, характеризуется отсутствием разъемных и неразъемных соединений.
Сборочная единица является более сложным сборочно-монтажным элементом, состоящим из двух или более деталей, соединенных разъемным либо неразъемным соединением. Характерным признаком сборочной единицы является возможность ее сборки отдельно от других сборочных единиц.
Технологическая схема сборки изделия является одним из основных документов, составляемых при разработке ТП сборки. Расчленение изделия на сборочные элементы проводят в соответствии со схемой сборочного состава, при разработке которой руководствуются следующими принципами:
∙схема составляется независимо от программы выпуска изделия на основе сборочных чертежей, электрической и кинематической схем изделия;
∙сборочные единицы образуются при условии независимости их сборки, транспортирования и контроля;
4365

∙минимальное число деталей, необходимое для образования сборочной единицы первой ступени сборки, должно быть равно двум;
∙минимальное число деталей, присоединяемых к сборочной единице данной группы для образования сборочного элемента следующей ступени, должно быть равно единице;
∙схема сборочного состава строится при условии образования наибольшего числа сборочных единиц;
∙схема должна обладать свойством непрерывности, т. е. каждая последующая ступень сборки не может быть осуществлена без предыдущей.
Включение в схему сборочного состава технологических указаний превращает ее в технологическую схему сборки. Для изделий широко применяются схемы сборки "веерного" типа (рис. 1.12, а), на которой стрелками показано направление сборки деталей и сборочных единиц. Достоинством схемы является ее простота и наглядность, но она не отражает последовательности сборки во времени.
Схема сборки с базовой деталью (рис. 1.12, б) устанавливает временную последовательность сборочного процесса. При такой сборке необходимо выделить базовый элемент, т. е. базовую деталь или сборочную единицу, в качестве которой обычно выбирают ту деталь, поверхности которой будут впоследствии использованы при установке в готовое изделие. В большинстве случаев базовой деталью служит плата, панель, шасси и другие элементы несущих конструкций изделия. Направление движения деталей и сборочных единиц на схеме показывается стрелками, а прямая линия, соединяющая базовую деталь и изделие, называется главной осью сборки. Точки пересечения осей сборки, в которые подаются детали или сборочные единицы, обозначаются, как элементы сборочных операций, например: Сб.1-1, Сб.1-2 и т. д., а точки пересечения вспомогательной оси
сглавной — как операции: Сб.1, Сб.2 и т. д.
При построении технологической схемы сборки каждую деталь или сборочную единицу изображают в виде прямоугольника (рис. 1.13, а), в котором указывают позицию детали по спецификации к сборочному чертежу (1), ее наименование (2) и обозначение (3) согласно КД, а также количество деталей (4), подаваемых на одну операцию сборки. Размеры прямоугольника рекомендуются 50×15 мм. Допускается изображение нормализованных или стандартных крепежных деталей в виде круга диаметром 15 мм, в котором указывают позицию по спецификации и количество деталей (рис. 1.13, б).
Рис.1.12. Схемы сборки: а – « веерного» тип; б – с базовой деталью
Технологические указания по выполнению сборочных операций или электрического монтажа помещают в прямоугольник, ограниченный штриховой линией, а место их выполнений указывают наклонной стрелкой, направленной в точку пересечения осей сборки. Так на технологических схемах сборки оговаривают характер
4366