
по трэс
.pdf
где Дт. ПП — число типоразмеров печатных плат в изделии; ДПП — общее число ПП.
К электромеханическим устройствам относятся механизмы привода, отсчетные устройства, кодовые преобразователи и т. д. Состав показателей технологичности приведен в табл. 1.12.
Коэффициент точности обработки
K тч =1 − Дтч / Д ,
где Дтч — число деталей (без учета стандартных и крепежных), квалитет размеров которых не выше 10. Точность резьбовых поверхностей при расчете не учитывается.
Коэффициент сложности обработки
Kс.о =1 − Дм / Д ,
где Дм — число деталей, включая заимствованные и стандартные, требующих обработки снятием стружки; Д
—общее число деталей.
Табл. 1.12. Показатели технологичности электромеханических устройств
qi |
Коэффициенты |
Обозначение |
ϕi |
|
|
|
|
1 |
Точности обработки |
Ктч |
1,0 |
2 |
Прогрессивности формообразования деталей |
Кф |
1,0 |
3 |
Сложности обработки |
Кс.о |
0,8 |
4 |
Повторяемости деталей и сборочных единиц |
Кпов. ДСЕ |
0,5 |
5 |
Параллельности сборки |
Кп.сб |
0,3 |
6 |
Сложности сборки |
Кс.сб |
0,2 |
7 |
Использования материалов |
Ки.м |
0,1 |
|
|
|
|
Коэффициент повторяемости деталей и сборочных единиц
K пов. ДСЕ =1 − Дт − Ет ,
Д + Е
где Дт, Ет — общее число типоразмеров деталей и сборочных единиц без учета нормализованного крепежа; Д, Е — общее число типоразмеров деталей и сборочных единиц.
Коэффициент параллельности сборки Kп.сб = Еп.сб / Е ,
где Еп.сб — число сборочных единиц, допускающих параллельную сборку; Е — общее число сборочных единиц.
Коэффициент сложности сборки Kс.сб =1 − Ет.сл / Ет ,
где Ет.сл — число типоразмеров сборочных единиц, входящих в изделие и требующих регулировки и подгонки.
Коэффициент использования материалов Kи.м = М / Мк.м ,
где М — масса изделия без учета комплектующих изделий и тары: М = Мiе + Мiд ; Мiе — масса i-й сборочной единицы; Мiд — масса i-й детали, являющейся составной частью изделия; Мк.м — масса конструкционного материала.
К коммутационным устройствам относятся соединительные, распределительные блоки, коммутаторы и т.п. Состав показателей технологичности приведен в табл. 1.13.
Коэффициент повторяемости материалов Kпов. м =1 − Дм.м / Дт ,
где Дм.м — число маркосортаментов материалов, применяемых в изделий (под маркосортаментом понимается сочетание марки материала и профиля его поставки); Дт — количество типоразмеров оригинальных деталей.
4377
Табл. 1.13. Показатели технологичности коммутационных устройств
qi |
Коэффициенты |
Обозначение |
ϕi |
|
|
|
|
1 |
Повторяемости материалов |
Кпов. м |
1,0 |
2 |
Сложности сборки |
Кс.сб |
1,0 |
3 |
Точности обработки |
Ктч |
0,8 |
4 |
Прогрессивности формообразования деталей |
Кф |
0,5 |
5 |
Использования материалов |
Ки.м |
0,3 |
|
|
|
|
Нормативные значения комплексных показателей технологичности конструкций изделий ЭА зависят от стадии разработки рабочей документации (табл. 1.14).
Табл. 1.14. Нормативные значения показателей технологичности
|
Разработка |
Доработка рабочей документации |
|
|
|
|
|
Класс устройств |
рабочей документации |
установочной серии |
установившегося серийного |
|
|
|
производства |
|
|
|
|
Радиотехнические |
0,60 — 0,75 |
0,70 — 0,80 |
0,75 — 0,85 |
Электронные |
0,40 — 0,70 |
0,45 — 0,75 |
0,50 — 0,80 |
Коммутационные |
0,35 — 0,55 |
0,50 — 0,70 |
0,55 — 0,75 |
Электромеханические |
0,30 — 0,55 |
0,40 — 0,60 |
0,45 — 0,65 |
|
|
|
|
Для повышения технологичности конструкций необходимо выполнение следующих мероприятий:
∙повышение унификации, конструкторской и функциональной взаимозаменяемости деталей и сборочных единиц;
∙расширение использования ИМС, микросборок, функциональных элементов;
∙увеличение сборности конструкции за счет использования базовых несущих конструкций;
∙увеличение количества деталей, изготовленных прогрессивными способами формообразования, обоснование выбора квалитетов точности, шероховатости поверхности, установочных и технологических баз;
∙рациональная компоновка элементов, что обеспечивает автоматизированную установку и монтаж;
∙минимизация числа подстроечных и регулировочных элементов;
∙автоматизация подготовки элементов к монтажу;
∙совершенствование ТП монтажа;
∙механизация и автоматизация операций контроля и настройки;
∙применение прогрессивных методов формообразования деталей.
ВОПРОСЫ ДЛЯ САМОПРОВЕРКИ
1.Конструктивно-технологические особенности, характерные для поколений ЭА.
2.Основные задачи технологии ЭА на современном этапе.
3.Технологический процесс, его структура, виды и типы ТП.
4.Основные задачи, решаемые при проектировании ТП.
5.Как осуществить выбор оптимального варианта ТП?
6.Технологические схемы сборки, их разновидности и порядок проектирования.
7.Основные виды технологических документов и порядок их оформления.
8.Оценка технологичности конструкций блоков ЭА.
4378

2.ТОЧНОСТЬ И НАДЕЖНОСТЬ ТЕХНОЛОГИЧЕСКИХ ПРОЦЕССОВ
2.1.ПРОИЗВОДСТВЕННЫЕ ПОГРЕШНОСТИ И ЗАКОНЫ ИХ РАСПРЕДЕЛЕНИЯ
Производственные погрешности выходных параметров изделий следует рассматривать как следствие влияния нестабильности ТП изготовления деталей, ЭРЭ, а также технологических операций сборки и монтажа, герметизации, термотренировки и др. Под производственными погрешностями понимают отклонения параметров изделий от номинальных данных, указанных в ТУ на изделие.
Различают два вида производственных погрешностей: случайные и систематические. Погрешность называют случайной, если она принимает различные значения под влиянием случайных факторов, поэтому определить заранее точное значение для каждого момента времени невозможно. Систематической называется такая погрешность, которая в процессе исследований остается постоянной или же изменяется по определенному закону. Кроме случайных и систематических погрешностей на практике встречаются грубые ошибки ("промахи"), зависящие от грубых ошибок оператора, технолога и т. д. Влияние таких погрешностей не учитывается при построении модели, но принимаются меры по их предупреждению.
В производстве все погрешности проявляются в совокупности и вызываются в основном следующими факторами:
∙погрешностями в работе технологического оборудования, обусловленными дефектами электрических, механических и оптических систем;
∙износом рабочего инструмента, отклонениями его от требуемой конфигурации;
∙недостаточной жесткостью, нарушением конфигурации приспособлений и технологической оснастки, неправильной установкой в оборудовании;
∙неоднородностью электрофизических, механических и прочих свойств материалов и заготовок деталей;
∙субъективными ошибками оператора при настройке оборудования и поддержании режимов его работы;
∙метрологическими ошибками в результате неточности измерительных средств при контроле параметров изделия.
Как правило, в ТП изготовления изделий действует совокупность частных случайных погрешностей. В
том случае, если: число случайных факторов и параметры вызванных ими частных погрешностей не изменяются во времени; среди частных погрешностей нет доминирующих, т. е. все случайные факторы по своему влиянию на общую погрешность составляют величины одного порядка; все случайные факторы взаимно независимы, что имеет место при автоматически работающем оборудовании, погрешности подчиняются нормальному закону распределения Гаусса:
y(x) = |
|
1 |
|
−(x−M(x))2 |
|
||
|
|
e |
2σ2 |
, |
|||
|
|
|
|||||
2π σ |
|||||||
|
|
|
|
|
где y(x) — плотность распределения; x — отклонение от центра группирования; σ — среднеквадратичное отклонение.
Площадь под кривой Гаусса составляет 100 % всех значений случайной величины. При этом односигмовые границы соответствуют точкам перегиба кривой Гаусса с площадью 68,26 %, или 2/3 наблюдаемых значений, двухсигмовые — 95,44 %, трехсигмовые — 99,73 % всех площадей.
4379
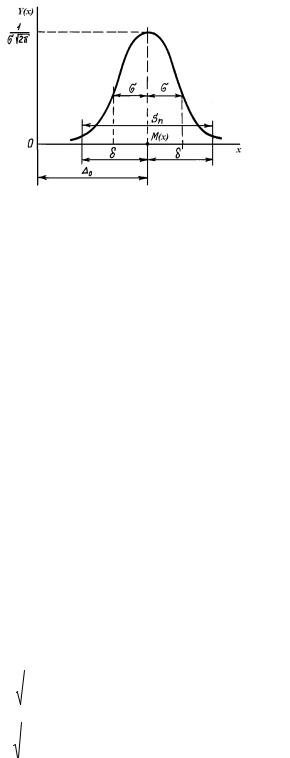
Кривая распределения имеет колоколообразную форму. Максимальная ордината кривой соответствует точке x=М(x). При x, стремящемся к бесконечности, кривая асимптотически приближается к оси абсцисс (рис. 2.1).
Рис. 2.1. Распределение нормального закона
Параметрами нормального закона распределения являются математическое ожидание, среднеквадратичное отклонение, половина поля допуска, поле рассеяния.
Математическое ожидание случайной величины для дискретных чисел
M (x) = |
k |
mi |
, |
|
∑ xi |
||||
|
||||
|
i =1 |
N |
||
где k — число интервалов ряда распределения; mi / N — |
частость значений. |
Для отображения дискретных изменений значений параметра x строится гистограмма и полигон распределения. Для этого по оси абсцисс откладывают отрезки, соответствующие ширине интервала c, а по оси ординат — частоту mi, т. е. число значений, попавших в данный интервал (рис. 2.2). Обычно принимают, что число интервалов
k = 5 lg N ,
где N — число значений, а ширина интервала
c = (xmax − xmin ) / k ,
где хmin, xmax — соответственно минимальное и максимальное значения параметра. Для непрерывных случайных чисел математическое ожидание
|
|
|
|
|
|
M (x) = |
+∞ |
||
|
|
|
|
|
|
∫ x y(x) dx . |
|||
|
|
|
|
|
|
|
−∞ |
||
Среднеквадратичное отклонение: |
|
|
|
|
|
|
|
|
|
|
|
|
|
|
|
|
|
|
|
для дискретных чисел |
σ (x) = |
|
k |
|
|
− M (x))2 |
m / N , |
||
|
∑(x |
i |
|||||||
|
|
|
i =1 |
|
i |
||||
|
|
|
|
|
|
|
|
||
|
|
|
|
|
|
||||
для непрерывных чисел |
σ(x) = |
+∞ |
(x − M (x))2 |
y(x) dx . |
|||||
|
|
|
∫ |
i |
|
|
|
|
|
|
|
−∞ |
|
|
|
|
|
|
|
Половина поля допуска на параметр |
|
|
δ = 3σ . Полное поле рассеяния при уровне вероятности 0,9973 |
Sn = 2δ = 6σ . Отношение среднеквадратичного отклонения к математическому ожиданию, выраженное в про-
центах, есть коэффициент вариации K в = σx / M (x). Будучи безразмерным, он удобен для сравнения.
4380
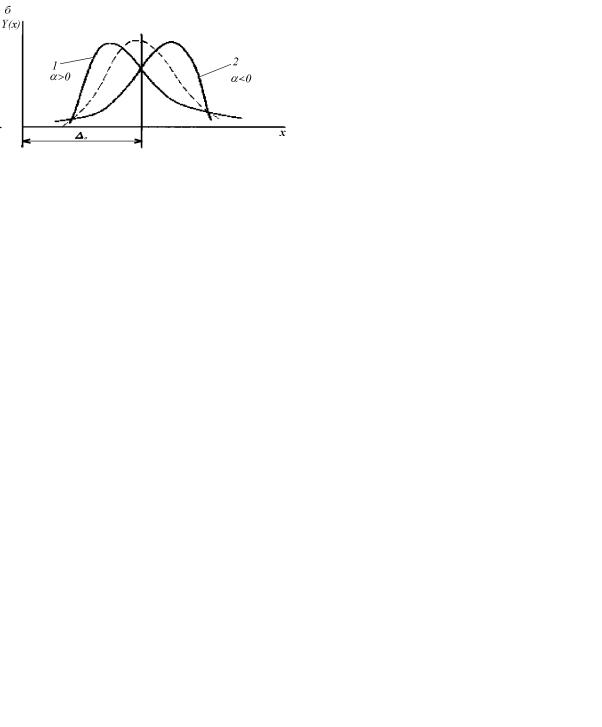
Для обеспечения заданного допуска в условиях производства необходимо, чтобы поле рассеяния производственных погрешностей не выходило за рамки поля допуска. Отсюда следует основное требование к настройке технологического оборудования: Sn ≤ 2δ (ТУ) .
Настроенность ТП определяют с помощью коэффициента технологической точности Т и коэффициента
смещения от середины поля допуска Е: |
|
|
|
|
|
|
|
|
T = |
2δ (ТУ) |
= |
δ (ТУ) |
|
E = |
M (x) − Bср |
(ТУ) |
|
|
|
, |
|
|
, |
|||
Sn |
δ |
δ(ТУ) |
|
|||||
|
|
|
|
|
|
где Вср(ТУ), δ(ТУ) — номинальное значение параметра и половина поля допуска по ТУ.
Рис. 2.2. Гистограмма и полигон распределения
Технологический процесс считается настроенным при Т > 0,95 и Е < 0,05, в этом случае брак не превысит 1 %. В электронике традиционная воспроизводимость на уровне допуска 3σ уже не удовлетворяет современным требованиям, т. е. область дефектности 0,27 % означает 2700 бракованных приборов на 1 млн. единиц продукции. Согласно стандарту по обеспечению качества Международной организации по стандартизации — ИСО
9000, воспроизводимость рекомендуется между границами 6σ, это 0,002 дефекта на 1 млн. изделий. Нормальному закону распределения в производстве ИМС подчиняются процессы нанесения резистивных и
диэлектрических слоев однотипных МОП-структур, толщина фоторезиста, наносимого центрифугированием на партию подложек, и др. При анализе производственных погрешностей неизбежно возникает расхождение между теоретической кривой распределения и статистическим распределением в виде полигона. Чтобы определить соответствие распределения статистических погрешностей нормальному закону, используют критерий согласия Пирсона (χ2), который представляет собой вероятность того, что случайная величина χ2 принимает значение, большее заданного:
k n′ − n |
i |
2 |
|
|
χ2 = ∑ |
i |
|
, |
|
n′ |
|
|||
|
|
|
|
|
i=1 |
i |
|
|
|
где ni, ni′ — практические и теоретические частоты распределения.
Рис. 2.3. Кривые распределения обобщенного закона типа А:
а – с положительной (τ>0) и отрицательной (τ<0) крутостью;
42

б – с положительной (α>0) и отрицательной (α<0) косостью;
Для распределения Р(χ2) составлены таблицы, дающие возможность по значению χ2 и числу степеней сво-
боды l найти вероятность того, что χ2 превзойдет заданное значение . Число степеней свободы равно:
l = k′ − f −1 ,
где k′— число объединенных (ni >5) интервалов; f — число параметров закона распределения.
Границей между случайным и существенным расхождениями является 5 %-й уровень значимости, т. е. при
Р(χ2)>0,05 расхождение является случайным и предполагаемый закон распределения достоверно описывает опытные данные. В противном случае расхождение признается существенным и для описания статистических данных выбирается другой закон распределения. При использовании критерия Р(χ2) число данных выборки должно быть больше 30.
При малом числе наблюдений точечная оценка статистических характеристик в значительной мере случайна и колеблется от выборки к выборке. Поэтому для каждой статистической характеристики следует указывать точность оценки, которая содержится в доверительном интервале. Доверительный интервал для математического ожидания
x − α σ ≤ M (x) ≤ x + α σ ,
N
N
где α — коэффициент, зависящий от принятой вероятности, при Р=0,95 α=1,96; N — объем выборки; М(х) — среднее арифметическое значение параметра.
Если распределение производственных погрешностей значительно отличается от нормального, то оно опи-
сывается обобщенным законом типа A |
|
|
|
|
|
YA |
(x) = y(x) − |
r3 |
yIII (x) + |
r4 −3 |
yIV (x) , |
|
|
||||
|
6 |
24 |
|
где y(х) — плотность распределения нормального закона; r3, r4 — основные моменты 3-го и 4-го порядка; yIII(x), yIV(x) — производные 3-го и 4-го порядка.
Обобщенный закон распределения типа A (рис. 2.3) наряду со средним значением М(х), среднеквадратич-
ным отклонением σ характеризуется мерой крутости τ и мерой косости α:
τ = r3 − 3 α= r3 .
Для обобщенного закона типа А
S n = t σ,
где t — безразмерная дробь, которая определяется по таблицам математической статистики в зависимости от значения и знака эксцесса τ.
Обобщенный закон типа A наиболее часто встречается в производстве гибридных пленочных ИМС. Так, погрешности параметров тонкопленочных резисторов и конденсаторов, измеренные за сравнительно большой период их производства, подчиняются этому закону. Примером может служить также смешивание изделий из разных партий, изменение настройки оборудования в технологическом процессе.
Для расчета параметров закона распределения используются понятия моментов, которые бывают начальными, центральными и основными. Начальным моментом ряда распределения порядка h называется сумма произведений отклонений случайной величины xi относительно условного начала a0 в степени h на соответствующую частость:
43
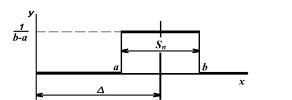
|
k |
(x − a |
0 |
)h |
||
|
∑ |
i |
|
ni |
||
|
c |
|
|
|||
γh = |
i =1 |
|
|
. |
||
|
N |
|
|
|||
|
|
|
|
|
|
Центральным моментом порядка h называется сумма произведений отклонений случайной величины xi относительно среднего значения М(х) в степени h на соответствующую частость:
k |
(x − M (x))h |
|
n |
|
μh = ∑ |
i |
|
i |
. |
c |
|
|||
i =1 |
|
N |
||
При с = 1 и h = 1 γ1= M(x), при h = 2 μ2 = σ2. |
|
|
|
|
Рис. 2.4. Равновероятностное распределение
Основным моментом порядка h называется частное от деления центрального момента соответствующего порядка на среднеквадратичное отклонение в степени h:
rh = μh / σh .
При резко доминирующей систематической погрешности, которая равномерно изменяется во времени (например, износ инструмента), для описания погрешностей применяют равновероятностный закон вероятно-
сти, который имеет вид |
|
|
|
0 |
при x < a, |
|
|
при a ≤ x ≤ b, |
y(x) = 1/(b − a) |
||
|
0 |
при x > b, |
|
где a, b — границы изменения значений систематической погрешности (рис. 2.4).
Математическое ожидание M (x) = (a + b) / 2 . Дисперсия D(x) = (b − a)2 /12 . Полное поле рассеяния по-
грешности Sn = 3,464σ .
2.2. МЕТОДЫ АНАЛИЗА ПРОИЗВОДСТВЕННЫХ ПОГРЕШНОСТЕЙ
Для анализа производственных погрешностей применяют два метода: статистический и аналитический. Статистический метод основан на обработке достаточно большого количества наблюдений с помощью правил математической статистики. Он позволяет определять суммарную технологическую погрешность, которая возникает в результате взаимодействия ряда факторов, но не дает возможности выявить причины ее возникновения.
Аналитический метод основан на выявлении функциональных зависимостей между производственными погрешностями и причинами их возникновения аналитическим или экспериментальным путем. Эти методы на практике сочетаются, дополняя друг друга. Так появились расчетно-статистический, корреляционный и другие методы анализа производственных погрешностей изготовления деталей и сборочных единиц.
44
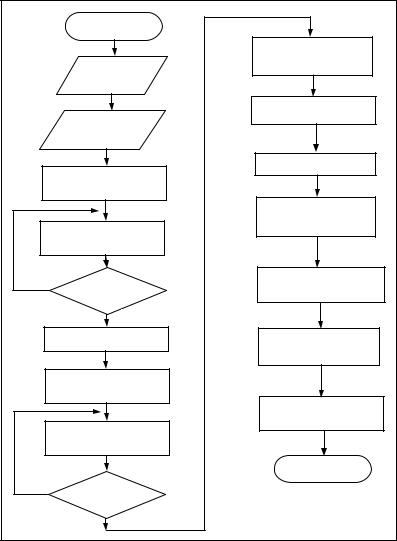
Вход |
|
Описание |
|
массива x |
|
Ввод N, |
M = V – M 2(x) |
δ(ТУ), В(ТУ) |
|
Подготовка цикла |
|
I = 0; S = 0 |
|
S = S + x2( I + 1) |
|
Да |
|
I – N < 0 |
|
Нет |
|
M(x) = S / N |
|
Подготовка цикла |
|
I = 0; D = 0 |
|
|
Печать |
D = D + x 2( I + 1) |
М(х), G, D, T, E |
|
|
Да |
Выход |
|
|
I – N < 0 |
|
Нет |
|
Рис. 2.5. Алгоритм расчета технологической точности изготовления |
Статистический метод проводится в три этапа.
На п е р в о м э т а п е выбирается объект исследования, определяется объем экспериментальных данных, назначаются средства технического контроля. Основным требованием, предъявляемым к объекту исследования, является однородность экспериментальных данных. Объем данных определяется в зависимости от допустимой ошибки при их анализе. Выборки могут быть малыми (10 ≤ n < 30), большими (30 ≤ n < 100) и представитель-
ными (100 ≤ n ≤ 300). Измерительные средства должны быть такими, чтобы полная предельная погрешность метода измерения не превышала 10 % от допуска на параметр.
На в т о р о м э т а п е проводится непосредственное наблюдение и измерение параметров и заполняются протоколы испытаний. Полученные данные для удобства вычисления характеристик ряда распределения разбивают на интервалы.
На т р е т ь е м э т а п е по известным формулам рассчитывают М(x), σx, δ, Sn, T, E и в конечном итоге определяют настроенность ТП.
Для автоматизации расчетно-статистического метода используют ПЭВМ, производя одновременную обработку массива чисел функции y(x) без разбивки его на интервалы. Алгоритм расчета технологической точности изготовления изделий приведен на рис. 2.5.
Аналитический метод анализа производственных погрешностей применяется в тех случаях, когда имеется аналитическое выражение, связывающее выходной параметр блока или устройства с параметрами входящих в
45
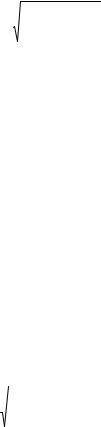
него элементов конструкции или параметрами ТП. Для оценки влияния погрешностей параметров отдельных деталей на величину производственной погрешности выходного параметра сборочных единиц используют выражение выходного параметра в общем виде:
П = q1, q2 , q3 ,..., qk , |
(2.1) |
где П — выходной параметр сборочной единицы; qi — параметры деталей.
После дифференцирования выражения (2.1) и замены дифференциалов конечными приращениями получим
k |
∂П |
|
|
П = ∑ |
|
q , |
(2.2) |
|
|||
|
|
i |
|
i =1 ∂qi |
|
где k — количество элементов, участвующих в сборке изделия.
Но на практике удобнее пользоваться не абсолютными значениями параметров, а относительными. Для этого уравнение (2.2) разделим на уравнение (2.1) и, произведя некоторые преобразования, получим
П |
k |
|
qi , |
|
|
= ∑ A |
(2.3) |
||||
|
|||||
П i =1 |
i |
qi |
|
где Аi — коэффициент влияния i-го параметра на погрешность выходного параметра:
A = |
∂П |
|
qi |
. |
|
|
|||
i |
∂qi П |
Используя уравнение (2.3), можно однозначно определить производственную погрешность выходного параметра при заданных погрешностях параметров элементов, если известны значения Аi. Для расчета коэффициентов влияния широко используют расчетный и статистические методы (малых приращений, корреляционный, планирования эксперимента и регрессионного анализа). Определив тем или иным способом значения коэффи-
циентов влияния, вычисляют средние значения М и δ относительной погрешности выходного параметра по формулам:
|
П |
k |
|
|
q |
|
|
П |
|
k |
|
|
q |
||
M |
|
|
= ∑ |
A M |
i |
|
, |
δ |
|
= |
∑ |
A2 |
δ2 |
i . |
|
|
|
||||||||||||||
П i =1 |
i |
|
|
|
|
П |
|
i =1 |
i |
|
|
||||
|
|
qi |
|
|
|
|
qi |
Эти уравнения справедливы в том случае, если распределение производственных погрешностей параметров отдельных элементов подчиняется нормальному закону и симметрично относительно среднего значения. Но в результате действия доминирующих факторов, смешивания партий, выборки практические кривые распределения отклоняются относительно значений, заложенных в ТУ на элементы. Количественно эти отклонения оцениваются коэффициентами относительной асимметрии bi и рассеяния Ki:
bi |
= |
M (xi ) − M (xi ) (ТУ) |
, Ki = |
|
S ni |
|
, |
δi (ТУ) |
|
|
|
||||
|
|
2 |
δ(ТУ) |
||||
где δi(ТУ) — половина поля допуска на параметр, определяемая по ТУ; |
Sni — величина поля рассеяния пара- |
||||||
метра, определяемая экспериментально. |
|
|
|
|
|
|
|
Для вычисления величин bi и Кi используют статистический метод анализа производственных погрешностей, основанный на обработке большого количества однородного экспериментального материала. В результате обработки определяют закон распределения производственных погрешностей (с помощью критерия Пирсона или Колмогорова ) и его параметры. Используя значения величин bi и Кi, вычисляют среднее значение и поле
рассеяния относительной погрешности выходного параметра: |
|
|
|
|
|
|
|
|
|
|
|
||||||||||
|
|
|
|
|
|
|
|
|
|
|
|
|
|
|
|
|
|
|
|
|
|
|
П |
k |
|
q |
i |
|
П |
|
|
k |
|
|
2 |
|
q |
i |
|
||||
M |
|
|
= ∑ |
A b M |
|
|
, |
δ |
|
= |
∑ |
A2 |
K |
δ2 |
|
. |
|||||
|
|
|
i |
|
|
||||||||||||||||
П i=1 |
i i |
|
qi |
|
|
|
П |
|
|
i =1 |
i |
|
|
qi |
|
|
|||||
|
|
|
|
|
|
|
|
|
|
|
|
46

Рис. 2.6. Номограмма для проверки достоверности коэффициентов корреляции:
А – незначимый; Б – значимый; В – весьма значимый
Если выходной параметр связан с влияющими параметрами дробной линейной рациональной или иррациональной функцией:
П = Q / H ,
где Q = Q(q1, q2, q3,...,qi), H = H(q1, q2, q3,...,qi) — многочлены, у которых показатель степени i-го параметра может быть больше единицы, то коэффициенты влияния могут быть определены по формуле
A = m Q(qi ) − n H (qi ) ,
Q H
где m — показатель степени параметра qi в числителе; n — показатель степени параметра qi в знаменателе; Q(qi), H(qi) — части многочленов, в которые входит параметр qi.
Анализ производственных погрешностей параметров элементов показывает, что между некоторыми из них на разных этапах изготовления существуют взаимные связи, которые могут быть статистическими. Более простым и практически важным случаем статистической зависимости является корреляционная зависимость, которая выражается в том, что при изменении одного параметра (x), второй (у) изменяет свое математическое ожидание.
Наличие корреляционных связей можно объяснить конструктивными факторами, а также особенностями ТП изготовления. Так, корреляционные связи имеют место между параметрами электронных ламп (S и ri), катушек индуктивности (L и R), подстроечных конденсаторов (Cmin и Cmax), транзисторов (h11, h21) и др. Корреляционная связь характеризуется формой и теснотой связи. Численными характеристиками тесноты связи являются следующие: при линейной зависимости — коэффициент корреляции r, при нелинейной — корреляцион-
ное отношение ξ. Значение коэффициента корреляции может изменяться от –1 до +1 и определяется как
r= γ11 − M (x) M ( y) ,
σx σ y
N
где γ11 — начальный момент связи: γ11 = ∑ xi yi / N .
i =1
Среднеквадратичное отклонение σr = (1 − r 2 ) / N .
Линейные уравнения регрессии:
x − M (x) = p x/y (M ( y) − y), y − M ( y) = p y / x (M (x) − x) ,
где коэффициенты регрессии px/y = r |
σ |
x |
, py/x |
= r |
σ y |
. |
|
|
σx |
||||
|
σ y |
|
|
47