
по трэс
.pdf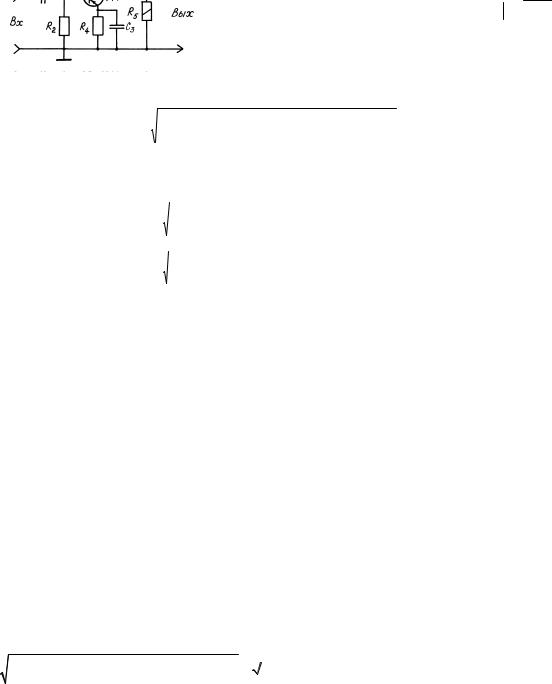
Проверка надежности найденной корреляционной зависимости осуществляется по условию r N −1 > 3
или по номограмме (рис. 2.6). При наличии корреляционной связи между параметрами отдельных элементов (индуктивностей, транзисторов, микросхем и т. д.) ее учитывают введением поправочных коэффициентов в
общее уравнение погрешности выходного параметра сборочной единицы:
σ
П |
= |
k |
2 |
|
|
|
∑ Ai |
||
|
||||
П |
|
i =1 |
|
2 |
σ |
2 |
|
qi |
Ki |
|
|
qi |
|
|
|
|
|
|
|
|
|
|
qi |
|
|
|
|
q j |
. |
|
+ ∑ 2rij |
Ai |
Ki |
σ |
|
|
Aj |
K j |
σ |
|
|
|
|
||||||||||
|
|
|
|
|
qi |
|
|
|
|
q j |
|
i ¹ j |
|
|
|
|
|
|
|
|
Если сборочную единицу характеризует не один выходной параметр, а l, то точность ее определяется системой из l уравнений:
|
|
|
|
|
|
|
|
|
|
DП |
1 |
|
|
k |
|
|
|
|
|
|
|
Dq |
i |
|
|
|
|
|
|
Dq |
i |
|
|
|
|
|
|
|
Dq j |
|
|
|
|||||||||||||
|
|
|
|
|
|
|
|
|
|
d |
|
|
|
|
= |
∑ Ai2 Ki2 d2 |
|
|
|
|
+ ∑ |
2rij Ai Ki |
d |
|
|
|
|
A j |
K j |
d |
|
|
|
|
|
||||||||||||||||||||
|
|
|
|
|
|
|
|
|
|
|
П |
|
q |
|
|
q |
|
|
|
q |
|
||||||||||||||||||||||||||||||||||
|
|
|
|
|
|
|
|
|
|
|
|
|
|
i=1 |
|
|
|
|
|
|
i |
|
|
|
|
|
|
|
i |
|
|
|
|
|
|
|
|
|
j |
|
|
||||||||||||||
|
|
|
|
|
|
|
|
|
|
|
|
1 |
|
|
|
|
|
|
|
|
|
|
|
i¹ j |
|
|
|
|
|
|
|
|
|
|
|
|
|
|
|
|
|||||||||||||||
|
|
|
|
|
|
|
|
|
|
................................................................................................................ |
|
|
|
|
|||||||||||||||||||||||||||||||||||||||||
|
|
|
|
|
|
|
|
|
|
|
|
|
|
|
|||||||||||||||||||||||||||||||||||||||||
|
|
|
|
|
|
|
|
|
|
|
|
|
|
|
|
|
|
|
|
|
|
|
|
|
|
|
|
|
|
|
|
|
|
|
|
|
|
|
|
|
|
|
|
|
|
|
|
|
|
|
|
|
|
|
|
|
|
|
|
|
|
|
|
|
|
|
|
DПl |
|
|
k |
|
|
|
|
|
|
|
Dqi |
|
|
|
|
|
Dqi |
|
|
|
|
|
|
|
|
Dq j |
|
|
|||||||||||||||
|
|
|
|
|
|
|
|
|
|
|
|
|
2 |
|
2 |
|
2 |
|
|
|
|
|
|
|
|
|
|
|
|
||||||||||||||||||||||||||
|
|
|
|
|
|
|
|
|
|
s |
|
|
|
|
|
|
= |
∑ |
A |
|
K |
|
d |
|
|
|
|
|
|
|
|
+ |
∑ |
2r A K |
|
s |
|
|
|
|
|
A |
|
K |
|
s |
|
|
|
|
|
|
|||
|
|
|
|
|
|
|
|
|
|
|
|
|
П |
l |
|
|
|
i |
|
i |
|
|
|
q |
i |
|
|
|
ij i |
i |
|
q |
i |
|
|
|
|
j |
|
j |
|
|
q |
j |
|
|
|||||||||
|
|
|
|
|
|
|
|
|
|
|
|
|
|
|
|
|
i=1 |
|
|
|
|
|
|
|
|
|
|
i¹ j |
|
|
|
|
|
|
|
|
|
|
|
|
|
|
|
|
|
||||||||||
|
|
|
|
|
|
|
|
|
|
|
|
|
|
|
|
|
|
|
|
|
|
|
|
|
|
|
|
|
|
|
|
|
|
|
|
|
|
|
|
|
|
|
|
|
|
|
|
|
|
|
|
|
|
|
|
|
|
Пример. Определить допуск на коэффициент усиления блока УНЧ (рис. 2.7) при следующих условиях: коэффициент усиления |
|||||||||||||||||||||||||||||||||||||||||||||||||||||
K |
y |
= |
h21 Rн |
|
, эквивалентное сопротивление нагрузки |
|
R |
|
= |
|
|
R3 R5 |
, R3 = 3 кОм, R5 = 6 кОм, h21 = 100, h11 = 4,5 кОм, h = 0,5, |
||||||||||||||||||||||||||||||||||||||||||
|
|
|
|
|
|
|
|
|
|
||||||||||||||||||||||||||||||||||||||||||||||
|
|
h11 + hRн |
|
|
|
|
|
|
|
|
|
|
|
|
|
|
|
|
|
|
|
н |
|
|
|
R3 + R5 |
|
|
|
|
|
|
|
|
|
|
|
|
|
|
|
|
|
|
|
|
|||||||||
|
|
|
|
|
|
|
|
|
|
|
|
|
|
|
|
|
|
|
|
|
|
|
|
|
|
|
|
|
|
|
|
|
|
|
|
|
|
|
|
|
|
|
|
|
|
|
|||||||||
r |
|
|
= 0,9 , |
|
|
|
R |
|
|
R |
|
|
|
|
|
|
|
h |
|
|
|
|
|
|
|
|
|
|
|
|
|
|
|
|
|
|
|
|
|
|
|
|
|
|
|
|
|
|
|
|
|
||||
|
|
RН = 2 кОм, |
|
3 |
|
= |
5 |
|
|
=10 %, |
|
|
21 |
|
= 20 % . |
|
|
|
|
|
|
|
|
|
|
|
|
|
|
|
|
|
|
|
|
|
|
||||||||||||||||||
|
|
R |
R |
|
h |
|
|
|
|
|
|
|
|
|
|
|
|
|
|
|
|
|
|
|
|
|
|
|
|||||||||||||||||||||||||||
h21h11 |
|
|
|
|
|
|
|
|
|
|
|
|
|
|
|
|
|
|
|
|
|
|
|
|
|
|
|
|
|
|
|
|
|
|
|
|
|
|
|
|
|
|
|
|
|
|
|||||||||
|
|
|
|
|
|
|
3 |
|
|
5 |
|
|
|
|
|
|
|
|
|
21 |
|
|
|
|
|
|
|
|
|
|
|
|
|
|
|
|
|
|
|
|
|
|
|
|
|
|
|
|
|
|
|
|
Р е ш е н и е . |
Рассчитываем коэффициенты влияния параметров h21, RН, h11: |
A h21 |
= |
k |
|
h21 |
= |
|
Rн |
|
|
h21 (h11 + h Rн ) |
= 1, |
|||||||||||||||||
h21 |
|
|
|
|
|
|
|
|||||||||||||||||||||||
|
|
|
|
|
|
|
|
|
|
|
|
|
|
|
|
|
|
k |
h11 + h Rн |
h21 Rн |
||||||||||
A R = |
h21(h11 |
+ h Rн) − h21 Rн h |
|
R (h11 + h Rн) |
= |
|
h11 |
= 0,8 |
, A h = |
−h21 Rн |
|
|
h11(h11 + h Rн ) |
= |
|
−h11 |
|
= − 0,8 . |
||||||||||||
н |
(h + h R ) |
|
h R |
(h + hR ) |
|
11 |
(h + h R |
) |
|
|
h R |
|
|
h |
+ h R |
|||||||||||||||
|
|
11 |
н |
21 |
н |
11 |
н |
|
|
11 |
н |
|
|
|
21 |
н |
11 |
|
|
|
н |
Рис. 2.7. Схема усилителя низкой частоты
Допуск на коэффициент усиления
D К y |
|
k |
2 |
2 |
D q i |
|
D q i |
|
||||||
δ |
|
|
= |
∑ A |
|
i δ |
|
|
+ 2 ri j |
A i |
A jδ |
|
|
δ |
K |
|
|
q |
|
q |
|
||||||||
|
y |
|
i = 1 |
|
|
i |
|
|
|
i |
|
|||
|
|
|
|
|
|
|
|
D q j |
|
|
|
|
|
q j |
|
|
|
|
|
= ( 0 , 8 ) 2 ( 0 , 1 + 0 , 1 ) 2 + 1 2 × 0 , 2 2 + 2 × 0 , 9 × 1 × 0 , 8 ( 0 , 2 + 0 , 2 ) 2 |
= 0 , 3 8 6 |
|
|
|
|
|
|
|
|
|
2.3. ТОЧНОСТЬ И УСТОЙЧИВОСТЬ ТЕХНОЛОГИЧЕСКИХ ПРОЦЕССОВ
Все технологические операции производства ЭА по влиянию на выходные параметры изделий условно разбиваются на три основные группы:
1)активные формирующие, в процессе которых образуются выходные параметры блока (сборочномонтажные операции);
2)активные преобразующие, в результате которых изменяются значения выходных параметров блока (настройка, заливка, пропитка, обволакивание, термотренировка и др.);
3)пассивные, которые не влияют на количественные показатели выходных параметров (покраска, маркировка, контроль и др.).
48
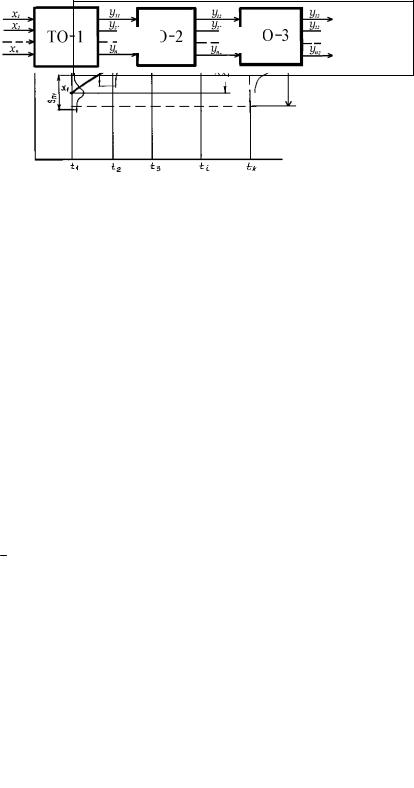
Технологический процесс производства функциональных блоков и изделий можно представить в виде структурной схемы, состоящей из ряда технологических операций (ТО): формирующих, преобразующих и пассивных (рис. 2.8). На вход первого формирующего звена поступают серии компонентов и деталей со своими параметрами х1, х2,...,хn.
Рис. 2.8. Схема многооперационного технологического процесса
На выходе его из совокупности этих параметров образуются новые показатели y11, y21,...,yj1, которые после преобразующего звена принимают значения y12, y22,...,yin и т. д.
Основная задача анализа точности ТП состоит в том, чтобы определить количественные показатели влияния технологических операций по результатам изменения входных и выходных характеристик блоков. Различают функциональную и технологическую точность выходных параметров блоков и изделий.
Функциональная точность определяется как требуемая точность, обеспечивающая нормальное функционирование изделия согласно ТУ, и задается допуском. Обычно функциональная точность аппаратуры задана, а функциональная точность блоков и сборочных единиц рассчитывается исходя из соотношения
δ N (ТУ) ≤ f (δ1, δ2 ,..., δi ,...),
где δ N (ТУ) — половина поля допуска на выходной параметр изделия по ТУ; δi — половина поля допуска на выходной параметр i-го блока.
Полная устойчивость ТП означает, что все изменения параметров изделия укладываются в поле допуска по ТУ. Но так как ТП не могут быть абсолютно устойчивыми, то кривые распределения параметров могут иметь вид, отличный от нормального закона распределения.
Для оценки устойчивости ТП применяют метод точностных диаграмм, основанный на построении кривых распределения производственных погрешностей изучаемого параметра во времени. По оси абсцисс откладывают равные промежутки времени, по истечении которых небольшие партии изделий (25 — 30 шт.) подвергают статистическому анализу. По оси ординат откладывают вычисленные для каждой группы значения среднего арифметического xi , среднеквадратичного отклонения σi и предельных отклонений Sni. Соединяя последова-
тельно точки, получают временную функцию изменения параметра изделия (рис. 2.9).
Рис. 2.9. Точностная диаграмма ТП
По точностной диаграмме можно выявить влияние систематических погрешностей на точность изготовления изделия и определить устойчивость ТП. Степень устойчивости процесса определяется коэффициентом Tу:
49

Ту = σi / σ S ,
где σi — среднеквадратичное отклонение в данный момент t1, t2, ..., ti; σs — общее среднеквадратичное отклоне-
ние. Процесс остается устойчивым, если Tу > 0,95, а xi → 0.
Дополнительными характеристиками устойчивости процесса являются число наладок H за наблюдаемый период времени t и коэффициент длительности периода между наладками, который характеризует способность процесса длительно сохранять нормальное функционирование без наладок: Tн = t / Н .
Технологическая точность — это реально существующая точность выходных параметров функциональных блоков в процессе их изготовления при выбранном варианте технологии. Для определения технологической точности используют статистические методы. Однако в этом случае трудно получить полностью изоморфную модель процесса, поскольку увеличение объема испытаний связано с увеличением затрат времени, средств и материальных ресурсов. Поэтому для правильного расчета технологической точности необходимо математическое описание каждой из рассматриваемых операций, т. е. математическая модель каждой технологической операции.
2.4. РАСЧЕТ ТЕХНОЛОГИЧЕСКОЙ ТОЧНОСТИ С ПРИМЕНЕНИЕМ ТЕОРИИ СЛУЧАЙНЫХ ФУНКЦИЙ
Теория случайных функций позволяет установить функциональную зависимость между двумя величинами, одна из которых — независимая переменная величина, другая — зависимая случайная. Случайной называется функция, которая в результате опыта может принять тот или иной вид (реализацию), заранее неизвестный. Случайная функция совмещает в себе черты случайной величины и функции. Если зафиксировать значение аргумента t, функция превращается в обычную случайную величину. В результате каждого опыта она превращается
вобычную функцию. В качестве аргумента в теории случайных функций используют чаще всего время t.
Вотличие от числовых характеристик случайных величин, представляющих собой определенные числа, характеристики случайных функций представляют собой не числа, а функции, основными из которых являются математическое ожидание, дисперсия и корреляционная функция.
Предположим, что в результате опытов получено n реализаций независимой функции (рис. 2.10). Выходной параметр в этом случае также является случайной величиной. Математическое ожидание выходного параметра
влюбой момент времени t следует представить как некоторую функцию в сечениях t1, t2, ..., tk:
|
|
|
n |
|
|
|
|
|
|
|
|||
X (t1 ) = ∑ xi (t1 ) / n, |
||||||
|
|
|
i=1 |
|
|
|
|
|
|
|
|
|
|
|
|
|
n |
|
|
|
|
|
|
||||
X (t2 ) = ∑ xi t |
2 |
/ n, |
||||
|
|
|
i=1 |
|
|
|
|
|
|
n |
|
|
|
|
|
|
||||
X(t3 ) = ∑ xi t3 / n, |
||||||
|
|
|
i=1 |
|
|
|
где n — общее число функциональных блоков; хi — выходной параметр функционального блока.
50
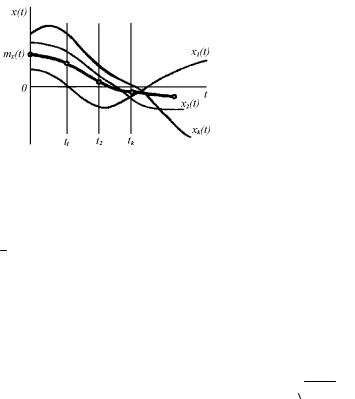
Рис. 2.10. Реализация случайных функций x(t) и mx(t)
Следовательно, математическое ожидание случайной величины в общем случае зависит от выбранного се-
чения и представляет собой функцию: M (x(t)) = mx (t) . Для фиксированного сечения tk математическое ожида-
n
ние mx (tk ) = x(tk ) = ∑ xi (tk ) / n .
i =1
Таким образом, математическое ожидание случайной функции есть некоторая функция, около которой различным образом варьируются конкретные реализации случайной функции. Дисперсией случайной функции х(t) называется функция Dx(t), значение которой для каждого t равно дисперсии соответствующего сечения случай-
ной функции: Dx (t) = D(x(t)) .
Среднеквадратичное отклонение случайной функции σx (t) = Dx (t) .
Корреляционной функцией случайной функции х(t) называется неслучайная функция двух аргументов Кх(tk, tl), которая при каждой паре значений tk и tl равна:
|
n |
|
|
|
∑ (xi (tk ) − mx (tk )) (xi (tl ) − mx (tl )) |
|
|
K (t , t ) = |
i=1 |
, |
|
n − 1 |
|||
x k l |
|
||
|
|
где tk, tl — независимые переменные, определяющие сечения, для которых вычисляется корреляционная функция.
Во многих случаях вместо корреляционной функции Кx(tk, tl) пользуются нормированной корреляционной функцией
rx (tk |
, tl ) = |
K x (tk |
, tl ) |
||
|
|
|
, |
||
σx (tk ) |
|
|
|||
|
|
σx (tl ) |
которая представляет собой коэффициент корреляции величин х(tk), х(tl). В этом случае дисперсия является ча-
стным случаем корреляционной функции при tk= tl: K x (tk , tl ) = Dx (t) .
Метод случайных функций используется для определения выходных параметров функциональных блоков (коэффициент усиления — для УНЧ, длительности импульса — для формирователя импульсов) в дискретные моменты времени t1,t2,..., tn (например, после пайки, заливки, термотренировки, при воздействии отрицательных и положительных температур и т. д.). При этом определяются коэффициенты корреляции между операциями, а также математические ожидания и дисперсии выходной функции.
2.5. МЕТОДЫ ОБЕСПЕЧЕНИЯ ЗАДАННОЙ ТОЧНОСТИ ТЕХНОЛОГИЧЕСКИХ ПРОЦЕССОВ
В технологии применяются следующие методы обеспечения заданной точности выходных параметров функциональных блоков: полной, неполной, групповой взаимозаменяемости, подгонки, регулировки.
51
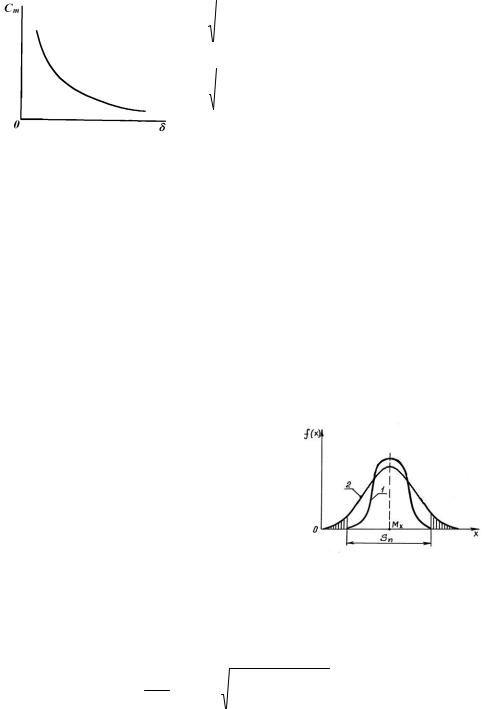
Суть метода полной взаимозаменяемости заключается в том, что требуемая точность выходных параметров функциональных блоков достигается включением в схему элементов с достаточно узкими допусками на их параметры без какого-либо дополнительного подбора или подгонки. Допуски на параметры элементов рассчитывают путем решения системы уравнений, в которых известными величинами являются производственные допуски на выходные параметры:
|
DП1 |
|
|
|
l |
2 |
|
2 |
|
2 |
|
|
Dqi |
|
|
|
|
|
|
|
|
|
|
|
|
||||||||||
|
|
|
³ |
∑ A |
K |
d |
|
|
|
|
|
||||||
|
|
|
|
|
|
|
|||||||||||
d |
|
|
|
|
i |
|
|
|
|
, |
|
||||||
|
П1 |
|
|
|
i |
|
|
|
|
qi |
|
|
|
|
|||
|
|
ТУ |
|
i=1 |
|
|
|
|
|
|
|
|
|
|
|||
× × × × × × × × × × × × × × × × × × × × × × × × × × × × × × × × × × × × × |
|
||||||||||||||||
|
|||||||||||||||||
|
|
|
|
|
|
|
|
|
|
|
|
|
|
|
|
|
|
|
DПl |
|
|
|
|
|
|
|
|
|
|
|
Dqi |
|
|
||
|
|
l |
2 |
|
2 |
|
2 |
|
|
|
|||||||
|
|
|
³ |
∑ A |
K |
d |
|
|
|
. |
|||||||
|
|
|
|
|
|
|
|||||||||||
d |
|
|
|
|
i |
|
|
|
|
|
|
|
|||||
|
Пl |
|
|
|
i |
|
|
|
|
qi |
|
|
|||||
|
|
ТУ |
|
i=1 |
|
|
|
|
|
|
|
|
|
|
|
Практическим критерием обеспечения полной взаимозаменяемости считается условие, когда в пределах поля допуска на выходной параметр содержится 99,73 % всех отклонений параметров элементов. Достоинства метода: простота достижения требуемой точности, отсутствие подгоночных и регулировочных операций, замена вышедших из строя элементов без подгоночных операций, широкое кооперирование предприятий по изготовлению отдельных взаимозаменяемых (унифицированных) элементов и сборочных единиц.
Границы применения метода полной взаимозаменяемости определяются экономическими показателями, в частности себестоимостью изготовления изделия (рис. 2.11). По мере ужесточения допуска ТП усложняется, требуется дополнительное и дорогостоящее оборудование, что снижает рентабельность метода.
Суть метода неполной взаимозаменяемости заключается в том, что требуемая точность выходных параметров достигается путем установки более широких допусков на параметры схемных элементов. В результате погрешность выходных параметров может выйти за пределы заданного допуска, однако при этом процент брака невелик и дополнительные затраты на его исправление меньше, чем затраты на изготовление деталей с более жесткими допусками на их параметры (рис. 2.12).
Рис. 2.11. Зависимость себестоимости изготовления |
Рис. 2.12. Распределение погрешностей в пределах поля допуска при |
изделия от допуска на параметр |
полной (1) и неполной (2) взаимозаменяемости |
Расчет допусков выходных параметров проводится по формуле
d DП1П1 ТУ
|
1 |
l |
|
2 |
|
Dq |
i |
|
|
³ |
|
∑ A2 |
K |
d2 |
|
|
, |
||
|
i |
|
|
||||||
|
ks |
i |
|
|
qi |
|
|
|
|
|
i=1 |
|
|
|
|
|
|
где ks — коэффициент относительного рассеяния выходных параметров, который для нормального закона распределения погрешностей зависит от допустимого брака (табл. 2.1).
Табл. 2.1. Значения коэффициента относительного рассеяния
52
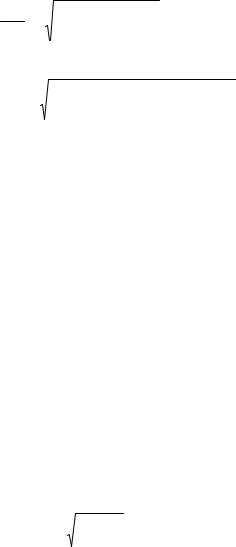
Процент |
0,27 |
0,5 |
1,0 |
1,5 |
2,0 |
5 |
10 |
брака |
|
|
|
|
|
|
|
|
|
|
|
|
|
|
|
kS |
1,0 |
1,05 |
1,11 |
1,17 |
1,21 |
1,33 |
1,44 |
|
|
|
|
|
|
|
|
Основным преимуществом метода является использование более широких, экономически выгодных допусков на параметры деталей. Недостаток — необходимость дополнительных рабочих мест на исправление брака.
Метод групповой взаимозаменяемости заключается в том, что требуемая точность выходных параметров блоков достигается включением в изделие деталей с узкими допусками на их параметры, полученных в результате отбора из одной партии. Отбору подвергаются те элементы, погрешности которых сильнее всего влияют на производственные погрешности выходных параметров изделий. Расчет допусков на производственные погрешности параметров элементов проводится в два этапа. Вначале полагают, что погрешности сильно влияющих элементов равны нулю:
|
Dq1 |
|
|
Dq2 |
|
|
|
|
|
|
= 0 , |
||
d |
q1 |
|
= d |
q2 |
|
|
|
|
|
|
|
и определяют допуск на выходной параметр без учета этих элементов, который будет меньше заданного при широких, экономически оправданных допусках на параметры остальных элементов:
d¢ DП ³i
Пi
k − 2
∑
i =1
|
|
2 |
|
Dq |
i |
|
A2 |
K |
d2 |
|
. |
||
i |
|
|
||||
i |
|
|
qi |
|
|
|
|
|
|
|
|
|
Затем методом подбора определяют допуски на параметры сильно влияющих элементов:
|
DП |
i |
|
|
DП |
i |
|
|
|
|
2 |
|
Dq |
|
|
|
2 |
|
Dq |
2 |
|
d |
|
|
- d¢ |
|
|
³ |
A2 |
K |
d2 |
1 |
|
+ A2 |
K |
d2 |
|
. |
|||||
|
|
|
|
1 |
|
2 |
|
|
|||||||||||||
|
Пi |
|
|
|
Пi |
|
|
|
1 |
|
|
|
|
2 |
|
|
q2 |
|
|
||
|
|
ТУ |
|
|
|
|
|
|
|
|
q1 |
|
|
|
|
|
|
Преимуществом метода является возможность получения повышенной точности параметров блоков ЭА при достаточно широких допусках на основную массу элементов. Дополнительные расходы, связанные с селекцией нескольких элементов, окупаются за счет экономии при изготовлении элементов с более широкими допусками.
Метод подгонки состоит в том, что требуемая точность выходных параметров блоков достигается подгонкой параметров одного или нескольких элементов. Введением такого элемента в схему обеспечивают частичную или полную компенсацию производственных погрешностей выходного параметра. В качестве компенсирующего выбирают элемент, погрешность параметра которого оказывает наиболее сильное влияние на выходные параметры изделия, так называемое "замыкающее" звено.
При расчете размерной сборочной цепи уравнение для замыкающего звена цепи имеет вид
Z = Y ( A1, A2 ,..., Ai ,..., Ak ) ,
где Ai — составляющие размеры.
Учитывая, что допуск равен разнице между наибольшим и наименьшим значениями размера, и используя дифференциальное исчисление, получаем уравнение для допуска замыкающего звена:
n |
¶Z |
|
|
dZ = ∑ |
|
= dAi . |
|
¶Ai |
|||
i=1 |
|
Среднеквадратичное отклонение размера замыкающего звена
|
|
1 |
n |
|
|
sS |
= |
∑ Ki2 |
di2 , |
||
ks |
|||||
|
|
i =1 |
|
где ks — коэффициент относительного рассеяния замыкающего звена; di — допуск на i-е звено.
53

Из условия компенсации излишнего отклонения выходного параметра при широких допусках на элементы схемы определяют предельные отклонения значений параметров замыкающего (компенсирующего) звена:
|
|
П |
|
|
|
П |
|
|
|
П |
i |
|
|
||||
2δ |
|
|
i |
= 2δ |
|
|
i |
− 2δ |
|
|
|
|
, |
||||
|
|
|
|
|
|
|
|||||||||||
|
к |
Пi |
|
|
|
Пi |
|
|
|
Пi |
|
|
|
||||
|
|
|
|
|
|
расч |
|
|
ТУ |
|
|||||||
|
|
|
|
|
|
|
|
|
|
|
|
|
|
|
|||
|
|
|
|
q |
|
|
δ2 |
( П |
/ П |
) |
|
|
|
|
|||
|
|
δ |
к |
= |
|
|
к |
i |
i |
|
. |
|
|
|
|||
|
|
|
|
|
2 |
|
|
|
|
|
|||||||
|
|
|
|
qк |
|
|
|
|
|
|
|
|
|
|
|
|
|
|
|
|
|
|
|
|
|
Bк |
|
|
|
|
|
|
|
|
При групповых методах подгонки точность составляет ±5 %, при индивидуальных ±1 %. Групповую подгонку осуществляют перерезанием коммутационных проводников в секциях тонкопленочных резисторов, индивидуальную — изменением толщины резистора (механическим путем, электрохимическим анодированием, лазерным или ионным лучом).
Основным преимуществом метода подгонки является возможность получения высокой точности изделий при экономически оправданных допусках на параметры влияющих элементов. Недостаток — необходимость дополнительных работ, связанных с измерением и подгонкой компенсирующего элемента.
Метода регулировки заключается в том, что требуемая точность выходных параметров изделий достигается путем изменения значения параметра специального регулировочного элемента. Наличие элемента с переменным параметром позволяет получать необходимую точность не только в период изготовления, но и при эксплуатации прибора, а также дает возможность достижения требуемой точности выходных параметров изделий при широких допусках на параметры влияющих элементов.
К недостаткам метода регулировки следует отнести снижение надежности аппаратуры, так как надежность регулировочных элементов значительно ниже надежности элементов с постоянными параметрами вследствие необходимости фиксации положения, трудностей влагозащиты и т. д., а также усложнения ТП регулировочными операциями.
2.6. НАДЕЖНОСТЬ ТЕХНОЛОГИЧЕСКИХ ПРОЦЕССОВ
Под надежностью ТП понимают его способность обеспечивать изготовление изделий в полном соответствии с технической документацией.
Надежность ТП — это вероятность того, что изготовляемое изделие будет годным:
H = Nг/Nобщ ,
где Nг — число годных изделий; Nобщ — общее число изделий: Nобщ = Nг +Nг / д +Nд / г +Nд ; Nг/д, Nд/г — число
годных изделий, признанных дефектными, и наоборот, из-за несовершенства выходного контроля; Nд — число дефектные изделий.
Если изготовление изделия состоит из трех фаз (входного контроля, ТП и выходного контроля), то надежность производственного процесса состоит из трех составляющих:
Hпр = H1 H 2 H3 ,
где Н1, Н2, Н3 — надежность входного контроля, ТП и выходного контроля соответственно.
Технологический процесс состоит из ряда технологических операций, поэтому его надежность равна произведению надежностей операций:
k
H 2 = ∏ Hi ,
i =1
где k — число операций; Hi — надежность i-й операции.
54
Показателем надежности является вероятность появления на выходе процесса, состоящего из k операций, m дефектных изделий:
P1,...,k (m) = λm e −λ ,
m!
где λ — математическое ожидание числа дефектных изделий.
Нормально организованный процесс характеризуется малым количеством дефектных изделий, т. е. m мало. При m = 1
P1,...,k (1) = λe−λ .
Разложением функции e в ряд Маклорена можно получить, ограничиваясь первым членом разложения P(1)
≈ λ. Среднее количество дефектных изделий на выходе ТП определяют по эмпирической формуле:
λ = ak z ,
где а — коэффициент, зависящий от ритма производства; k — количество операций; z — экспериментально определяемый параметр.
Кроме того, значение λ может быть определено статистическим путем. Так, например, при сборке блока УПЧ λ = 0,0023k1,425 .
Вероятность появления брака на одном рабочем месте сборщика или монтажника
Pоп = λ / k ,
где λ — среднее число дефектов, допускаемых оператором на рабочем месте; k — число операций. Тогда вероятность выхода годных изделий с этого рабочего места, т. е. вероятность данной технологической операции,
H оп =1 − Pоп .
Даже при хорошо организованном контроле ТП всегда остается вероятность попадания дефектных изделий в готовую продукцию, что снижает показатели надежности процесса. Одним из путей повышения количественных показателей надежности выпускаемых изделий, широко применяемых при изготовлении ЭА, является отбраковка потенциально ненадежных изделий путем их технологической тренировки.
ВОПРОСЫ ДЛЯ САМОПРОВЕРКИ
1.Законы распределения производственных погрешностей и их параметры.
2.Какой ТП считается настроенным?
3.Методика анализа производственных погрешностей.
4.Как построить точностную диаграмму и оценить устойчивость многооперационного ТП?
5.Методы обеспечения заданной точности ТП.
55
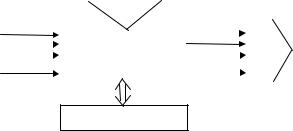
3 ОСНОВЫ ФУНКЦИОНИРОВАНИЯ ОПТИМАЛЬНЫХ ТЕХНОЛОГИЧЕСКИХ СИСТЕМ
3.1. МОДЕЛИ ТЕХНОЛОГИЧЕСКИХ СИСТЕМ И ИХ ОСНОВНЫЕ ПОКАЗАТЕЛИ
Для современных ТП производства ЭА характерно:
∙наличие значительного числа разнообразных факторов, влияющих на ТП;
∙большое число внутренних связей между параметрами ТП и их сложное взаимное влияние;
∙наличие нескольких конкурирующих направлений процессов, имеющих различные выходные данные;
∙воздействие на ТП большого числа внешних неконтролируемых и неуправляемых факторов, играющих роль возмущений.
Изучение и оптимизация таких сложных ТП невозможны без применения современных методик моделирования процессов на ЭВМ.
Современная технологическая система (ТС) — это совокупность взаимосвязанных потоков энергии, материалов и информации, действующая как единое целое, в которой осуществляется определенная последовательность ТП. Совокупность физико-химических процессов внутри ТС можно рассматривать как преобразование вводимых потоков энергии и вещества (рис. 3.1). Для обеспечения требуемых физико-химических превращений
входе выполнения ТП этими потоками необходимо управлять.
|
|
|
Возмущения |
|
|
|
|
|
|
|
Материал Х1 |
|
|
|
|
|
|
|
|
|
|
|
|
|
|
|
|
|
Y1 |
|
|
|
Энергия Х2 |
|
|
Технологическая |
|
|
|
|
Y2 |
|
Изделия |
|
|
система |
|
|
|
|
|
|||
Комплектующие Х3 |
|
|
|
|
|
|
Y3 |
|
||
∙ ∙ ∙ |
∙ ∙ ∙ |
|
|
|
||||||
|
|
|
|
|
|
|||||
Информация Хn |
|
|
|
|
Yn |
|
|
|||
|
|
|
|
|
|
|
|
|
||
|
|
|
|
|
|
Система управления
Рис. 3.1. Схема сложной технологической системы Технологическим системам свойственны признаки больших систем:
∙наличие общей цели функционирования (выпуск продукции);
∙большое количество элементов системы и параметров, характеризующих ее функционирование;
∙сложность поведения ввиду большого числа взаимосвязей ее составляющих;
∙воздействие внешних неконтролируемых и неуправляемых факторов.
Всвязи с этим изучение технологических систем, их анализ и синтез проводятся на моделях.
Модель — упрощенная система, отражающая отдельные наиболее важные стороны и ограничения изучаемого процесса. Процесс моделирования должен удовлетворять следующим требованиям:
∙эксперимент на модели должен быть проще, экономичнее и оперативнее, чем на объекте;
∙по результатам испытания модели должно быть получено аналитическое выражение для расчета параметров объекта.
Применяют два вида моделирования: физический и математический.
Физическое моделирование предполагает воспроизведение объекта в ином, уменьшенном, масштабе и сопровождается анализом особенностей и линейных размеров. Для него характерно постоянство критериев подобия модели и объекта. Подобие — это условие, при котором возможен количественный перенос результатов
56
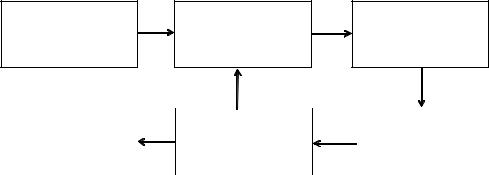
эксперимента с модели на оригинал. Физическое моделирование широко применяется при конструировании, а для анализа сложных ТП производства ЭА его применение затруднительно.
Математическое моделирование — метод качественного и (или) количественного описания процесса с помощью математических моделей, которые в зависимости от характера изучаемых явлений делятся на детерминированные и стохастические. Детерминированными называются такие модели, которые однозначно предсказывают поведение системы в данных условиях. Они обычно строятся без использования статистических вероятностных распределений. Стохастические, или вероятностные, модели строятся с использованием теории вероятности и математической статистики и однозначно описывают поведение системы. В зависимости от сложности процессов при их изучении могут использоваться изоморфные или гомоморфные модели. Первые характеризуются полным поэлементным соответствием между ней и реальной системой или процессом, вторые соответствуют лишь крупным частям реальной системы.
Математические модели могут быть аналитическими и имитационными. При составлении аналитических моделей процессы функционирования элементов сложной системы записываются в виде функциональных соотношений. Аналитическая модель может быть использована одним из следующих способов:
1)аналитически, когда получают в общем виде явные зависимости для искомых величин;
2)численно, когда для решения уравнений применяют методы вычислительной техники, чтобы получить числовые результаты при конкретных начальных данных;
3)качественно, когда, не имея решений в явном виде, можно определить некоторые свойства системы, например устойчивость и т.д.
При использовании имитационных моделей, в отличии от аналитических, в ЭВМ воспроизводится текущее функционирование ТС в некотором масштабе времени. Эксперимент позволяет учитывать влияние большого числа случайных и детерминированных факторов, дает возможность проводить активный эксперимент с помощью целенаправленных изменений параметров модели на некотором множестве реализации. Одно из основных достоинств имитационных моделей — возможность моделирования в тех случаях, когда аналитические модели либо отсутствуют, либо не дают практически надежных результатов.
Стратегия построения математической модели включает следующие этапы (рис. 3.2):
∙формулирование целей оптимизации параметров ТП, что включает выбор количественных и качественных критериев оптимизации (целевых функций) и их ограничений;
∙выбор вида математической модели с учетом особенностей процесса (детерминированный, стохастический) и создание алгоритма дискретного или нелинейного программирования на ЭВМ;
∙математическое моделирование с обработкой данных на ЭВМ;
∙проверка адекватности математической модели исследуемому процессу с целью определения того, насколько правомерны принятые допущения.
Выбор |
Выбор модели, |
Математическое |
целевой |
создание |
моделирование |
функции |
алгоритма |
процесса |
|
|
|
|
|
ИспользованиеРис. 3.2. |
Стратегия построенияПроверкаматематической |
моделиОбработка результа- |
||
модели для |
|
адекватности |
тов моделирования |
|
оптимизации ТП |
|
модели |
на ЭВМ |
|
|
|
|
|
|
Рис. 3.2. Стратегия построения математической модели
57