
ЛАБОРАТОРНЫЙ ПРАКТИКУМ
.pdfБітуми з ІР менше мінус 1,0 умовно можуть бути віднесені до типу «золь», з ІР більше плюс 1,0 – до типу гель, а бітуму з ІР від мінус 1,0 до плюс 1,0 – до типу «золь-гель». Стандартом України ДСТУ 4044-2001 передбачена можливість використання бітумів з ІР від плюс 1,0 до мінус 2,0, оскільки малов’язкі бітуми наближуються до бітумів типу «золь». Об’єктивність цього критерію обумовлена відповідністю температури розм’якшеності температурі, при якій пенетрація рівна 800 × 0,1 мм.
Найбільш об’єктивними критеріями визначення структурного типу бітумів є критерії, що ґрунтуються на врахуванні їх групового складу. Найповніше особливості групового складу бітумів враховує індекс колоїдної нестабільності С. Гастеля, який визначається за виразом:
IКН = |
А+ ВП |
, |
(6.6) |
|
С + ВА |
||||
|
|
|
де А, ВП, ВА, С – відповідно процентний вміст асфальтенів, парафінових, ароматичних вуглеводнів та смол.
Використання цього коефіцієнту ускладнюються в зв’язку з необхідністю визначення групового складу.
На основі статистичних порівнянь було показано тісний кореляційний зв’язок між значеннями коефіцієнта колоїдної нестабільності та із запропонованим В.О. Золотарьовим коефіцієнтом, який враховує показники, що передбачені стандартом, температури розм’якшеності Тр, температури крихкості Ткр та розтяжності Д при 25 °С
КСТД = |
(Тр −Ткр) L |
, |
(6.7) |
|
25 Д |
||||
|
|
|
де L – довжина (3 см) шийки форми «вісімки» 25 – температура визначення розтяжності в °С
З врахуванням цього зв’язку запропоновано границі показника стандартних властивостей КСТД, які розмежовують бітуми різних структурних типів. Бітуми з КСТД > 0,13 відносяться до типу «гель», бітуми з КСТД < 0,08 є системами зі структурою «золь», а бітуми з проміжними значеннями цього показника є системами типу «зольгель». Накопичені до цього часу дані вказують на принципову
201
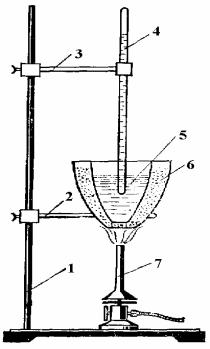
відміну реологічних властивостей бітумів, що характеризуються значеннями показників, які свідчать про їх належність до різних типів (табл. 6.2).
Визначення температури спалахнення. Всі основні техно-
логічні процеси підготовки бітумних в’яжучих та приготування матеріалів на їх основі виконують при високих температурах. Проте при перевищенні заданого температурного режиму бітум може загорітись, тому необхідно знати мінімальну критичну температуру (температуру спалаху), завдяки чому можна уникнути небезпеки.
Температурою спалахнення називають температуру, при якій газоподібні продукти, що виділяються з бітуму при нагріві, утворюють з повітрям суміш, яка спалахує на короткий час при контакті з відкритим полум’ям. Температура спалахнення свідчить про пожаробезпечні умови роботи з бітумом, його вогнестійкість. Її визначають у відкритому тиглі автоматичного приладу або приладу Бренкена (рис. 6.11). Прилад має штатив, на якому закріплено термометр та піщану баню із залізним тигелем діаметром (64 ± 1) мм, висотою (47 ± 1) мм, з товщиною стінок 1 мм. Тигель підігрівається газовою або спиртовою горілкою.
Рис. 6.11. Прилад для визначення температури спалахнення у відкритому тиглі: 1 – стійка; 2,3 – кронштейни, 4 – термометр; 5 – тигель з бітумом;
6 – піщана баня; 7 – пальник
202
Попередньо підготовлений бітум заливається в залізний тигель і встановлюється у піщаній бані. Рівень бітуму в тиглі має бути на 12 мм нижче його краю. Рівень піску в бані повинен знаходитись на одній висоті з рівнем бітуму в тиглі, а між дном тигля та банею має бути шар піску товщиною 5–8 мм. Замість піщаної бані може бути використаний прилад, який забезпечує підігрів бітуму струмом із заданою швидкістю. Термометр з межею вимірювання до 360 °С встановлюють у тиглі вертикально за допомогою затискача, закріпленого на штативі так, щоб ртутна куля термометра була в середині шару бітуму, що випробується. Починають розігрів бані на газовій горілці так, щоб швидкість нагріву бітуму складала 10 °С/хв. За 40 °С до очікуваної температури спалахнення зменшують швидкість нагріву бітуму до 4 °С хв.
Періодично через 2 °С, проносячи вогонь запалюючого пристрою над поверхнею бітуму, визначають момент появи синього полум’я. Температуру спалахнення бітуму, що відповідає цьому моменту, приймають як середнє арифметичне за результатами двох визначень, якщо вони розрізняються більше ніж на 3 °С.
Визначення розчинності. Показник розчинності характеризує однорідність бітуму, наявність в ньому інорідних включень та його склад. Для визначення розчинності використовують бензол або хлороформ чи трихлоретилен. Перед випробуванням бітум обезводнюють та проціджують через сито з отвором № 07 з металевою сіткою. Два складених разом фільтра промивають розчинником, вкладають у стаканчик для зважування з відкритою кришкою, висушують протягом 1 год у сушильній шафі при 105–110 °С. Потім стаканчик закривають кришкою, охолоджують в ексикаторі протягом 30 хв та зважують.
У попередньо зважену конічну колбу ємністю 250 мл розміщують біля 5 г бітуму, зваженного з точністю не менше 0,0002 г. Наважку бітуму розчиняють у 100 мл розчиннику, нагріваючи колби зі зворотним холодильником на водяній бані. Розчин бітуму фільтрують через доведений до постійної маси беззольний подвійний фільтр, покладений у скляну воронку, що закріплена на штативі. Розчин наливають на фільтр по скляній паличці. Залишок з колби змивають на фільтр чистим підігрітим розчинником.
203
Після закінчення фільтрації фільтр з осадком промивають нагрітим розчинником з допомогою промивалки. Промивання ведуть доти, доки на фільтрі не залишиться слідів бітуму і не стікатиме прозорий розчинник. Всі операції по розчиненню бітуму та фільтрації розчинувиконуютьу витяжній шафі.
Після закінчення промивання фільтр із залишком переносять в стаканчик для зважування, в якому сохнув чистий фільтр. Висушують фільтр, не закриваючи стаканчик кришкою, протягом 1 год у сушильній шафі при 105–110 °С. Потім стаканчик закривають кришкою, охолоджують в ексикаторі протягом 30 хв та зважують з похибкою не більше 0,0002 г. Операцію висушування та зважування повторюють до отримання розходження між двома послідовними зважуваннями не більше 0,0004 г.
Розчинність бітуму Х вираховують за формулою
Х = |
(m1 −m2 ) |
100, |
(6.8) |
|
m |
||||
|
|
|
||
|
1 |
|
|
де m1 – маса бітум, г;
m2 – маса залишку, що не розчинився на фільтрі, г.
За розчинність бітуму приймають середнє арифметичне значення двох паралельних визначень, допустиме розходження між якими не повинно перевищувати 0,04 %.
Визначення групового складу бітумів адсорбційно-хрома-
тографічним методом. Елементарний хімічний склад не є показовим для бітумів, оскільки він не пов’язаний безпосередньо з його властивостями. Тому склад бітумів визначають за вмістом в них найбільш характерних груп вуглеводнів: масел, смол, асфальтенів, карбенів та карбоїдів. Їх кількісне співвідношення визначає всі властивості бітумів. Вплив групового складу бітумів на їх властивості показано у табл. 6.3.
Виділення в бітумах груп вуглеводнів базується на їх селективній здатності розчинятися в різних розчинниках і на різній їх вибірній адсорбованості адсорбентами. Найбільше розповсюдження одержав метод адсорбційно-хромотографічного аналізу бітумів, який дозволяє виділити в маслах різні вуглеводні: парафіновонафтенові, моно-, біциклоароматичні, поліциклоароматичні, а також смоли петролейно- і спиртобензольні.
204
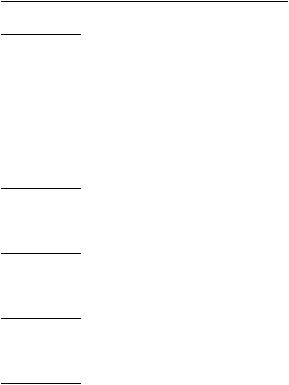
205
|
|
|
|
|
|
|
|
|
|
Таблиця 6.3 |
|
|
|
Взаємозв’язок властивостей та складу бітуму |
|
|
|
||||
|
|
|
|
|
|
|
Груповий склад, % |
|
|
|
|
|
|
|
|
|
|
|
|
||
Тип бітуму з |
|
Темпера- |
|
|
Коефіцієнт |
|
|
|
|
|
|
|
|
|
|
|
|
|
|||
глибиною |
|
Температура |
|
|
|
|
|
|
||
Розтяжність |
тура |
|
стандартних |
|
вуглеводні |
|
|
Коефіцієнт |
||
проникності |
Індекс |
вуглевод- |
|
|
||||||
голки при |
при 25 °С, |
розм’як- |
крихкості, |
пенетрацї |
властивос- |
парафі- |
смоли |
асфальтени |
колоїдної |
|
25 °С, |
см |
шеності, |
°С |
|
тей, |
ні аро- |
нонафте- |
нестабільності |
||
|
°С |
|
|
Кстд |
матичні |
|
|
|
||
80 × 0,1 мм |
|
|
|
нові |
|
|
|
|||
|
|
|
|
|
|
|
|
|
||
|
|
|
|
|
|
|
|
|
|
|
Гель |
4 |
63 |
-33 |
2,7 |
2,88 |
29,4 |
21,6 |
21,0 |
28,0 |
0,98 |
|
|
|
|
|
|
|
|
|
|
|
Гель-золь |
72 |
50 |
-24 |
0,1 |
0,12 |
21,9 |
26,8 |
30,3 |
21,0 |
0,92 |
|
|
|
|
|
|
|
|
|
|
|
Золь |
Більше 100 |
46 |
-14 |
-1,0 |
0,07 |
30,7 |
12,6 |
44,0 |
12,7 |
0,34 |
|
|
|
|
|
|
|
|
|
|
|
Для визначення групового складу бітумів за цим методом необхідні: адсорбційна скляна колонка діаметром 18–20 мм, довжиною 1300–1500 мм з кульовим резервуаром ємністю 250 мм у верхній частині та краном для регулювання швидкості проходження розріджувача у нижній частині, набір конічних колб об’ємом 50, 100 та 250 мм, холодильник Лібіха, рефрактометр типу РЛУ, сорбент-сілікагель марки АСК, фракції 0,25–0,5 мм.
Для розчинення та десорбції використовують набір розчинників: петролейний ефір (фракція з температурою кипіння до 45 °С, фракція з температурою кипіння 40–70 °С), в якому відсутні ароматичні вуглеводні; бензол ЧДА, спирт-ректифікат або гідролізний вищої очистки.
Перед випробуванням сілікагель промивають гарячою дистильованою водою, міняючи її до тих пір, поки вона не стане прозорою і на її поверхні не перестануть з’являтися пластівці або дрібні частинки. Потім воду зливають і відсмоктують її залишок на воронці Бюхнера за допомогою вакуумного насоса. Сілікатель поміщують у фарфорові чашки та витримують у сушильній шафі на протязі 6 год при температурі (150 ± 5) °С. Сілікагель після підготовки необхідно зберігати в герметично закритій посудині. На аналітичних терезах в колбу Ерленмейєра об’ємом 250 мм розміщують наважку 3–5 г випробованого бітуму з точністю до 0,0002 г. Добавляють до бітуму 6–10 мл бензолу, з’єднують колбу зі зворотним холодильником та розчиняють бітум на піщаній бані. Охолоджують вміст колби до кімнатної температури і невеликими порціями при постійному перемішуванні додають 40-кратну кількість (по відношенню до наважки) петролейного ефіру (фракція по температурі кипіння до 45 °С). Колбу ставлять на 24 год в темне місце для осідання асфальтенів. Потім асфальтени відфільтровують через подвійний фільтр, доведений попередньо до постійної маси. Змивають з фільтра асфальтени, розчиняючи їх гарячим бензолом в конічну колбу. Бензол з розчину асфальтенів відганяють на піщаній бані до об’єму 10 мл. Охолоджують колбу з асфальтенами і доливають в неї невеликими порціями, постійно перемішуючи, 150 мл петролейного ефіру (фракція з температурою кипіння до 45 °С) для повторного осадження асфальтенів. Необхідність повторного осадження асфальтенів викликана тим, що смоли та масла адсорбуються на поверхні асфальтенів і одноразове
206
осаджування не дає повного їх розділення. Через 24 год асфальтени відфільтровують через той же фільтр та промивають петролейним ефіром до повного видалення вуглеводнів та смол. Залишок асфальтенів на фільтрі розчиняють та змивають гарячим бензолом у колбу. Потім відганяють бензол та висушують асфальтени до постійної маси при температурі (105 ± 5) °С. Визначають вміст асфальтенів у відсотках до взятої наважки. Фільтр доводять нагрівом до постійної маси, приріст маси фільтру дає вміст карбенів, карбоїдів та механічних домішок.
В нижню частину адсорбційної колонки кладуть кусочок вати, поміщують біля 200 г сілікагелю, ущільнюючи сілікагель постукуванням по колонці двома гумовими грушами. В колонку доливають 250 мл петролейного ефіру (фракція з температурою кипіння 40– 70 °С), для того щоб змочити сілікагель по всій висоті колонки. Із розчину вуглеводнів та смол в петролейному ефірі відганяють майже досуха розчинник. Потім добавляють в колбу 25 мл петролейного ефіру (фракція з температурою кипіння 40–70 °С при повній відсутності ароматичних вуглеводнів). Після адсорбції чистого розчинника на сілікагелі розчин воглеводнів та масел переносять частинами в колонку.
Для десорбції масел та смол розчинники подають в колонку в такому порядку:
петролейний ефір (фракція 40–70 °С) – 200 мл; суміш петролейного ефіру (95 %) та бензолу (5 %) – 200 мл;
суміш петролейного ефіру (90 %) та бензолу (10 %) – 200 мл; суміш петролейного ефіру (85 %) та бензолу (15 %) – 200 мл; суміш петролейного ефіру (80 %) та бензолу (20 %) – 200 мл; суміш петролейного ефіру (75 %) та бензолу (25 %) – 200 мл; суміш петролейного ефіру (70 %) та бензолу (30 %) – 200 мл; бензол – 600 мл; спиртобензол у співвідношені 1:1 до стікання прозорих
крапель.
Швидкість проходження розчинників через силікагель регулюють за допомогою крана в нижній частині колонки так, щоб вона складала 300–350 мл (приблизно 1 крапля в 1 с.). По мірі проходження розчинників відбирають фракції в окремі таровані колби (об’ємом 50 та 150 мл).
207
Поява на силікагелі чорного кільця свідчить про проходження спирто-бензольних смол, а стікання з колонки безбарвних крапель спиртобензолу вказує на закінчення десорбції. Розчинник відганяють від вуглеводнів та смол на піщаній бані, а колбу з продуктами десорбції висушують до постійної маси в термостаті при температурі (105 ± 5) °С. Потім їх охолоджують в ексикаторі протягом 1 доби та зважують. Визначають коефіцієнт рефракції продукту в кожній колбі у відповідності з інструкцією до рефрактометра. За коефіцієнтом рефракції, що характеризує ступінь заломлення проміння світла у речовині, яка досліджується (у даному випадку в різних вуглеводнях), визначають приналежність кожної фракції до тієї чи іншої групи вуглеводнів.
Отримані при адсорбційному розділенні фракції складають в окремі групи залежно від значення коефіцієнту рефракції у такому порядку: парафінонафтенові вуглеводні – коефіцієнтів рефракції до 1,49; ароматичні вуглеводні – вище 1,49. Значно забарвлені фракції, для яких неможливо визначити коефіцієнт рефракції, відносять до смолистих речовин. Визначають сумарний вміст кожної групи у відсотках.
6.2. Бітуми, модифіковані полімерами
Підвищення інтенсивності руху та зростання питомої ваги важких автомобілів у транспортному потоці вимагає посилення несучої здатності дорожнього одягу в цілому і асфальтобетонного покриття особливо. Традиційні матеріали не можуть забезпечити такі показники властивостей асфальтобетону, що задовольняли б вимогам сучасного дорожнього руху. В цих умовах використання бітумів, модифікованих полімерами, дозволяє значно збільшити міцність асфальтобетону при високих температурах та забезпечити одночасно достатньо високу його стійкість проти тріщиноутворення взимку.
Полімери – це органічні речовини, молекули яких складаються з великої кількості атомів (десятків та сотень тисяч), що можуть мати різноманітні форми і по-різному розміщуватись одна відносно одної. Завдяки своєму складу та структурі, багато полімерів мають значну міцність при високих температурах та низьку температуру переходу до крихкого стану.
208
У дорожньому будівництві для отримання модифікованих бітумів використовують головним чином два види полімерів: термопласти та термоеластопласти. До перших відносять поліетілен, поліпропілен, поліізобутилен та сополімери типу етиленвінілацетата, етилен-метилакрилата, етилен-бутилакрилата та інші. До других належать сополімери типу стирол-бутадиєн-стирол (СБС), стирол-ізопрен-стирол (СІС) та ін.
Термоеластопласти типу СБС на відміну від термопластів, крім підвищення температури розм’якшеності, зниження величини пенетрації та температури крихкості, надають бітумополімерам еластичність, тобто здатність до значних зворотних деформацій.
Вміст добавки полімеру в бітумі призначають з врахуванням декількох факторів: необхідності отримання в’яжучого із завданими пенетрацією та температурою крихкості; забезпечення стабільності складу та властивостей модифікованого в’яжучого при технологічному зберіганні; вартості кінцевого продукту. Як правило, для забезпечення необхідної якості модифікованого в’яжучого до бітуму додають близько 2,5–3,5 % термоеластопласту або 4–6 % термопласту. Збільшення вмісту полімеру у бітумополімерному в’я- жучому покращує технічні властивості в’яжучого (зростає його міцність, когезія, знижується температура крихкості), але одночасно погіршуються технологічні властивості в’яжучого (погіршується стабільність при зберіганні, підвищуються температури його використання), зростає його вартість.
В’яжучі з вмістом термоеластопластів типу СБС у межах 2,5– 3,5 %, а термопластів 4–6 % називаються бітумополімерами. При вмісті цих полімерів відповідно більше 5–6 % та 8–9 % модифіковані в’яжучі називаються полімербітумними. Останні використовуються здебільшого в покрівельному та гідроізоля-ційному виробництві.
Механізм покращення якості в’яжучого за рахунок введення 2,5–3,5 % полімеру полягає в тому, що відносно малов’язкий вихідний бітум під впливом полімеру переходить у більш в’язкий (знижується його пенетраця та підвищується температура розм’якшеності). При цьому отриманий модифікований бітум має температуру крихкості, яка була притаманна вихідному мало- в’язкому бітуму. Таким чином, за рахунок модифікації досягається збільшення інтервалу пластичності.
209
Система оцінки якості бітумів, модифікованих полімерами, для дорожнього будівництва включає такі показники: однорідність; глибину проникності голки при 0 та 25 °С; температуру розм’якшеності; розтяжність при 0 та 25 °С; еластичність при 0 та 25 °С; температуру крихкості; зміну властивостей після прогрівання (температури розм’якшеності та пенетрації при 25 °С); зчеплюваність з кам’яним матеріалом та склом; розшарування при зберіганні (за температурою розм’якшеності та пенетрацією), інтервал пластичності; індекс пенетрації; температуру спалахнення. Технічні вимоги до бітумополімерних в’яжучих, що вміщують термопласти типу СБС наведені в табл. 6.4. Ці вимоги включені в перші в Україні технічні умови ТУ УВ.2.7-24.1-0340778-198-2002 «Бітуми, модифіковані полімерами», що розроблені ДерждорНДІ та ХНАДУ. Серед перерахованих показників абсолютна більшість тих, що визначаються для в’язких бітумів (табл. 6.4).
Таблиця 6.4
Технічні властивості бітумів, модифікованих термоеластопластами
|
|
Норми модифікованого бітуму |
||||
|
Найменування показників |
|
|
за марками |
|
|
|
БМТЕ |
|
БМТЕ |
БМТЕ |
БМТЕ |
|
|
|
|
||||
|
|
40/60-56 |
60/90-52 |
90/130-49 |
130/200-47 |
|
|
1 |
2 |
|
3 |
4 |
5 |
1. |
Однорідність |
не повинно бути згустків та частинок |
||||
|
нерозчиненого полімеру |
|||||
|
|
|
||||
2. |
Глибина проникності голки (0,1 |
40–60 |
|
61–90 |
91–130 |
131–200 |
|
° |
|
||||
мм): при 25 С |
15 |
|
22 |
30 |
38 |
|
при 0 °С не менше |
|
|||||
3. |
Температура розм’якшеності за |
56,0 |
|
52,0 |
49,0 |
47,0 |
кільцем і кулею, °С не нижче |
|
|||||
4. |
Розтяжність (см), не менше: |
25,0 |
|
30,0 |
30,0 |
30,0 |
|
° |
|
||||
при 25 С |
8,0 |
|
10,0 |
12,0 |
15,0 |
|
при 0 °С |
|
|||||
5. |
° |
60 |
|
60 |
65 |
65 |
Еластичністьпри25 С,% неменше |
|
|
|
|
|
|
6. |
° |
–15 |
|
–18 |
–21 |
–24 |
Температуракрихкості Сневище |
|
|
|
|
|
|
7. |
Температура спалахнення °С не |
|
|
|
|
|
нижче |
230 |
|
230 |
230 |
220 |
210