
Коррозия лабы
.pdf
зависимости
h
lg(
)
вычисляем степень параболы, и
К вес
h
– изменение
скорости коррозии с ростом толщины пленки.
В отчете дается краткое описание теории коррозионного процесса, методики эксперимента, приводятся полученные результаты. Приводятся расчеты и сводные таблицы, дается подробный анализ полученных данных в обсуждении результатов.
Графические зависимости и данные последней таблицы анализируются, при этом должен быть дан ответ на следующие вопросы:
1. Как связаны полученные цифровые данные с внешним видом прокорродировавших образцов и почему эта связь имеет место?
2.Является ли пленка образовавшихся оксидов сплошной? 3.Почему кривая имеет тот вид, который получился на рисунке? 4.Каков механизм коррозии?
5.В каком участке, считая от поверхности корродирующего материала, может быть зона роста пленки оксидов?
Даются выводы, в которых указывается:
1.Что изучалось в работе в заданных конкретных условиях;
2.Что конкретно установили или определили в результате изучения;
3.Даются практические рекомендации по способам защиты данного металла, пути повышения окалиностойкости.
Часть 2. Защита металлов от высокотемпературной газовой коррозии легированием или нанесением коррозионностойких тонкопленочных металлических или неметаллических покрытий
Металлические покрытия могут сами обеспечивать свойства стойкости к газовой коррозии на основе критериев теории жаростойкого легирования или же стать термостойким за счет введения в свой состав легирующих добавок, например бора, обеспечивающих термостойкость.
Для защиты металлов от термоокисления широко применяют гальванические покрытия хромом, которые наносят из электролитов, содержащих ионы хрома. Также наносят никелевые покрытия, но в электролиты дополнительно вводят борсодержащие добавки, обеспечивающие получение сплавов никель-бор, устойчивых к газовой коррозии при высоких температурах.
Электроосаждение термостойких металлических покрытий имеет ряд преимуществ перед другими способами защиты, так как позволяет регулировать толщину слоя покрытия , экономно расходовать цветной металл, получать металлические сплавы заданного состава и свойств. Но может использоваться и бестоковый (химический) способ получения термостойких покрытий, основанный на обработке защищаемых деталей в
11

растворах, содержащих ионы металла (никеля, кобальта, железа) и добавку борсодержащего восстановителя (борогидрида или аминоборана). В результате химической реакции восстановления осаждается сплав металлбор, например никель-бор, по следующим реакциям:
1) осаждение никеля:
2NiCl2 + NaBH4+4 NaOH 2Ni + NaBO2 +2H2 + 2H2O +4NaCl 2) включение бора:
NaBH4 + H2O kat B + 2,5H2+ NaOH
Наличие бора в сплаве (1÷7%) обеспечивает его термостойкость в условиях газовой коррозии. Полученные покрытия отличаются высокой равномерностью толщины, являются твердыми, износостойкими и коррозионностойкими. Однако данный метод является весьма дорогостоящим.
Для защиты черных металлов от газовой коррозии может использоваться метод фосфатирования, когда на поверхности металла формируется неметаллическая солевая фосфатная пленка, состоящая из малорастворимых фосфатов и гидрофосфатов железа и других металлов.
Основан метод на свойствах солей фосфорной кислоты.
В воде растворяются только фосфаты аммония и щелочных металлов. Двух – FeНРO4и трехзамещенные – Fe3(РO4)2 фосфаты железа малорастворимые. Следовательно, если создать условия для их образования, то они будут оставаться на поверхности металла основы.
При взаимодействии металла с фосфорной кислотой первоначально образуются дигидрофосфаты:
Me 2 H |
PO |
Me(H PO ) |
2 |
H |
. |
|
3 |
4 |
2 |
4 |
2 |
|
При снижении концентрации фосфорной кислоты получают вторичные и третичные соли:
Me(H2PO4 )2 MeHPO4 |
H3PO4; |
|
||||||||||
3 Me(H |
PO |
4 |
) |
2 |
Me |
(PO |
4 |
) |
2 |
4 H |
PO |
. |
2 |
|
|
3 |
|
|
3 |
4 |
|
Выпадающие в осадок ди- и трифосфаты на поверхности металла образуют плотную кристаллическую пленку.
Фосфатные пленки обладают хорошей адгезией, имеют высокоразвитую шероховатую поверхность. Они обеспечивают термостойкость сталей до температур 200÷2500 С и являются хорошим грунтом для нанесения лакокрасочных покрытий.
Неметаллические лакокрасочные покрытия являются одними из самых распространенных и надежных способов защиты от коррозии. Они дешевы и доступны, имеют простую технологию нанесения на поверхность, легко восстанавливаются в случае повреждения, отличаются разнообразием внешнего вида и цвета.
12

Защитные действия лакокрасочного покрытия (ЛКП) заключаются в создании на поверхности металлического изделия сплошной пленки, которая препятствует агрессивному воздействию окружающей среды и предохраняет металл от разрушения, в том числе при высоких температурах.
Термостойкие лакокрасочные покрытия для защиты от газовой коррозии получают на основе кремнийорганических соединений. Для защиты от газовой коррозии при сравнительно низких температурах могут найти применение силоксановые лаки, в которых пленкообразующим являются соединения на основе полимерных продуктов кислородных соединений кремния, имеющих структуру: –O–Si–O–Si–. Они могут длительно работать при температуре до 300 0С, а с пигментом из алюминиевой пудры – даже до 600° С. Эти составы обеспечивают хорошую, но кратковременную защиту поверхности металлов при 500÷800 0С. Такие покрытия используют для окрашивания вентиляционных и сушильных установок, теплообменников, элементов печей, газового оборудования.
Экспериментальная часть
Испытания коррозионной стойкости защитных покрытий проводят на деталях аналогичных, используемых в части 1 (марка металла (сплава), размеры). Вид защитного покрытия и режимы нанесения задаются преподавателем.
Для подготовки деталей к нанесению защитных покрытий проводят операции в следующей последовательности:
1. Химическое обезжиривание.
Деталь завешивается в щелочной раствор обезжиривания соответствующий для каждого конкретного металла или сплава (температура 50 ÷ 70 0С) и обрабатывается в течение 5 мин. Возможно обезжиривание и влажным порошком оксида магния.
2.Промывка в теплой и холодной дистиллированной воде.
3.Травление в растворе: НСl 100 ÷ 150 г/л + 1 ÷ 5 г/л уротропина 1÷3 минуты.
4.Промывка в дистиллированной проточной воде.
После операции промывки деталь завешивается в ванну гальванопокрытия или ячейку химической металлизации (фосфатирования).
5.Промывка в дистиллированной воде.
6.Сушка в термошкафу при температуре 80 0Св течение 5 мин. Лакокрасочные покрытия наносятся только после тщательной предвари-
тельной подготовки поверхности (согласно инструкции по применению полимерного материала) и сушки образцов в термошкафу. Затем, после окрашивания, детали с лакокрасочными покрытиями вновь помещают в сушильный
13

шкаф и выдерживают 30 минут при температуре +2000 С для полной полимеризации пленки.
Коррозионные испытания образцов с тонкопленочными покрытиями проводят по методике, приведенной в части 1 данной лабораторной работы при той же температуре на установке рис.2.
Из полученных данных по формулам (1.1÷1.3) рассчитываются весовые и глубинный показатели коррозии, которые для сравнения заносятся в табл.2.
ВОПРОСЫ ДЛЯ САМОПРОВЕРКИ
1.Как определить термодинамическую возможность газовой корро-
зии?
2.Как меняется термодинамическая возможность газовой коррозии с изменением температуры среды и почему?
3.Каков механизм газовой коррозии в случае образования защитных и незащитных коррозионных пленок?
4.Каков механизм диффузии в защитных оксидных пленках
5.По какому закону растет толщина оксидной защитной пленки в случае лимитирующей стадии – диффузии в пленке?
6.По какому закону растет толщина оксидной защитной пленки в случае соизмеримости лимитирующих стадий – диффузии и химической реакции компонентов в пленке?
7.Как рассчитывается положительный и отрицательный весовые показатели для газовой коррозии? Каков физический смысл этих показателей?
8.Как рассчитать отрицательный весовой показатель газовой коррозии, зная её положительный весовой показатель?
9.Как меняется скорость газовой коррозии с изменением температу-
ры?
10.Как меняется состав образующихся при коррозии оксидов черных металлов при изменении температуры?
11.Безокислительный нагрев в защитных атмосферах. Принцип выбора состава защитной атмосферы для данного температурного режима обработки металла.
12.На чем основан способ защиты металлов от газовой коррозии с помощью тонкослойных металлических или неметаллических покрытий?
13.Жаростойкое легирование – как метод защиты от газовой коррозии; требования к легирующему компоненту. Основные компоненты жаростойких сталей.
14.Как зависит скорость газовой коррозии металлов от класса обработки поверхности, местных напряжений, скорости движения газовой среды, наличия наклепа и др. факторов?
14

Дополнительные вопросы для самопроверки студентов, обучающихся по направлениям:22.03.02 – «Металлургия»; 22.03.01 – «Материаловедение и технология материалов»:
1.Как классифицируются коррозионные процессы по характеру коррозионных разрушений?
2.Качественные и количественные показатели коррозионной стойко-
сти?
3.Взаимосвязь показателей коррозионной стойкости и характера коррозионного разрушения металла?
4.Глубинный показатель коррозионной стойкости, его определение и расчет по весовым показателям коррозионной стойкости.
5.Десятибалльная шкала коррозионной стойкости и её применимость для оценки различных по характеру разрушения коррозионных процессов.
6.Стадийность процесса химического окисления металлов при газовой коррозии.
7.Лимитирующая стадия процесса и законы роста толщины оксидных пленок.
8.Лимитирующая стадия при линейном законе роста толщины пленок и принцип определения ряда металлов, окисляющихся по этому закону.
9.Почему при линейном законе роста толщины оксидной пленки температурная зависимость скорости окисления соответствует температурной зависимости константы скорости диффузии, а не константы скорости химической реакции?
10.Какова лимитирующая стадия при логарифмическом законе роста толщины оксидных пленок?
11.Как идентифицировать параболический закон роста толщины пленок по опытной кривой окисления металлов?
12.Физический смысл объединенной кривой окисления металлов.
13.Внутренние и внешние факторы, влияющие на скорость газовой коррозии.
14.Особые случаи газовой коррозии.
15.Обезуглероживание сталей при высоких температурах, его химизм и методы его предупреждения.
16.Водородная хрупкость сталей, её сущность, предупреждение и устранение этого вида коррозионного разрушения.
17.Термохромирование, термосилицирование и термоалитирование – как методы защиты от газовой коррозии; их практическое осуществление и применимость.
15
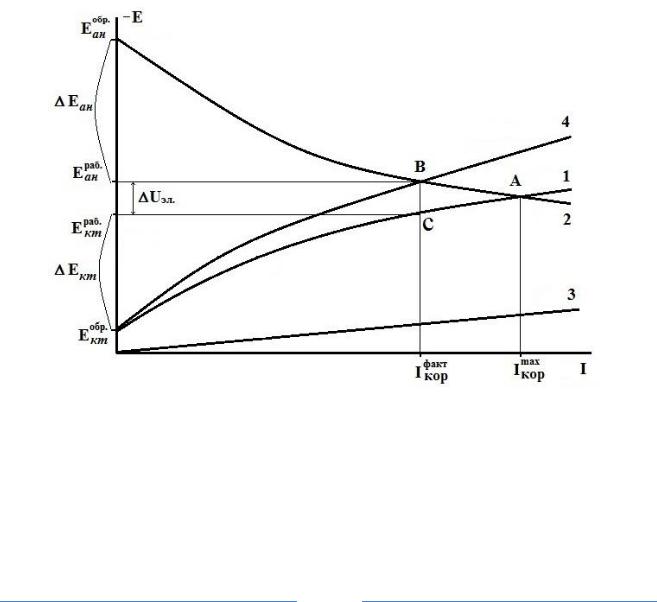
ГРАФИЧЕСКИЙ АНАЛИЗ ЭЛЕКТРОХИМИЧЕСКОГО КОРРОЗИОННОГО ПРОЦЕССА
Лабораторная работа № 2
Физической моделью электрохимической коррозии является короткозамкнутый коррозионный гальванический элемент. Для графического определения скорости и характеристик электрохимического коррозионного процесса используют полученные опытным путем анодные и катодные поляризационные кривые процессов (так называемые идеальные поляризационные кривые). Подобные кривые имеют приближенный характер, так как парциальные площади анодных и катодных участков в общих случаях не равны, в то время как сила коррозионного тока одна и та же для анодного и катодного процессов.
Учитывая сопряженность процессов по току, поляризационную коррозионную диаграмму (диаграмму Эванса) строят в координатах: коррозионный ток – потенциал электродов (рис. 1.).
Рис. 1. Поляризационная коррозионная диаграмма:
1 и 2 – катодная и анодная поляризационные кривы; 3 – падение напряжения в электролите; 4 – суммарная кривая катодной поляризации и падения напряжения в элек-
тролите, Eанобр и Eктобр – обратимые потенциалы для анодной реакции окисления металла и для катодной реакции восстановления окислителя); Eанраб и Eктраб – рабочие потенциалы (под фактическим током коррозии) анода и катода
16

Для построения диаграммы в таких координатах идеальные поляризационные кривые пересчитываются с учетом соотношения поверхностей анодных и катодных участков. Если это соотношение заранее известно, то пересчета можно избежать, снимая поляризационные кривые на электродах соответствующих поверхностей не при одинаковых плотностях тока, а при равных силах тока. Такой метод используется в данной работе.
Обратимые потенциалы
E |
обр |
|
ан |
||
|
и
E |
обр |
|
кт |
||
|
для анодной реакции окисления
металла и для катодной реакции восстановления окислителя рассчитываются по уравнению Нернста или определяются по диаграмме Пурбэ для данного металла (значения переводятся в единую шкалу потенциалов).
Точка (А) пересечения анодной 2 и катодной 1 кривых соответствует значению максимального коррозионного тока Iкорmax , который будет иметь
место у элемента при отсутствии омического сопротивления(R= 0) в данной системе.
Если сопротивление не равно нулю, то разность равновесных потенциалов электродов (движущая сила коррозионного процесса) расходуется не только на поляризацию, но и на преодоление сопротивления – на падение напряжения в электролите (падением напряжения на других омических составляющих в виду малости величин обычно пренебрегают).
На коррозионной диаграмме омическое падение напряжения в электролите выражается прямой 3. Для определения величины фактического коррозионного тока с учетом омических потерь напряжения катодную поляризационную кривую 1 и прямую 3 графически суммируют по потенциалам (складывают величины рабочих потенциалов электрохимического процесса и падения напряжения в электролите при данном токе коррозии)
– суммарная кривая 4. Затем находят точку пересечения (В), полученной суммарной кривой 4 с анодной поляризационной кривой 2. При этом точке (В) при экстраполяции на ось токов соответствует фактический проте-
кающий в коррозионной системе ток
I факт кор
, а при экстраполяции на ось
потенциалов
циала катода
E |
раб |
|
ан |
||
|
||
E |
раб |
|
|
кт |
– рабочий потенциал анода. Величину рабочего потен-
определяют экстраполяцией точки (С) (находящейся на
катодной поляризационной кривой при фактическом токе коррозии) на ось потенциалов.
Из поляризационной коррозионной диаграммы (рис. 1) можно найти графически значения анодной поляризации Eан = Eанраб Eанобр и катодной
17
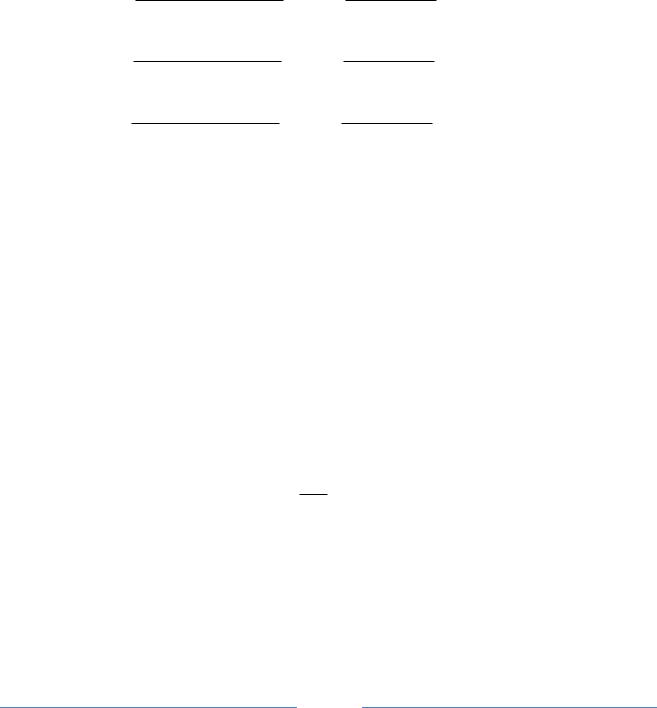
E кт
=
E |
раб |
|
кт |
||
|
Eобр
кт
поляризации, а также падения напряжения в электроли-
те
U |
эл |
|
=
E |
раб |
|
кт |
||
|
E |
раб |
|
ан |
||
|
.
Общий процесс электрохимической коррозии металла состоит из последовательно соединенных более простых процессов (ступеней): анодного, катодного, а также процесса протекания электрического тока через электролит и внешнюю цепь. При этом установившееся значение коррозионного тока определяется суммой торможений его протекания на отдельных ступенях.
Долю сопротивления данной ступени в общем сопротивлении всего процесса называют степенью контроля Ci ступени по данной, которую можно рассчитать по формулам (2.1) – (2.3):
|
|
|
|
|
E |
|
|
|
|
|
|
|
E |
|
|
|
|
|
||||
С |
|
|
|
|
|
кт |
100% |
|
|
|
|
|
кт |
100% |
, |
|||||||
кт |
|
E |
|
U |
эл |
E |
E |
обр |
E |
обр |
|
|
||||||||||
|
|
|
кт |
|
|
|
|
ан |
кт |
|
|
|
|
|||||||||
|
|
|
|
|
|
|
|
|
|
|
|
|
|
|
|
|
|
ан |
|
|
||
|
|
|
|
|
|
|
|
|
|
|
|
|
|
E |
|
|
|
|
|
|||
C |
|
|
|
|
|
|
|
|
|
|
100% |
|
|
|
|
|
ан |
|
|
100% |
, |
|
ан |
|
E |
|
U |
эл |
E |
E |
обр |
|
E |
обр |
|
|
|||||||||
|
|
|
кт |
|
|
|
|
ан |
кт |
|
|
|
|
|
||||||||
|
|
|
|
|
|
|
|
|
|
|
|
|
|
|
|
ан |
|
|
||||
|
|
|
|
|
U |
эл |
|
|
|
|
U |
эл |
|
|
|
100% . |
||||||
C |
|
|
|
|
|
|
100% |
|
|
|
|
|
|
|
|
|||||||
R |
E |
U |
|
|
|
E |
обр |
|
|
|
обр |
|||||||||||
|
|
эл |
E |
E |
|
|
||||||||||||||||
|
|
|
кт |
|
|
|
ан |
кт |
|
|
|
|
|
|||||||||
|
|
|
|
|
|
|
|
|
|
|
|
|
|
ан |
|
|
(2.1)
(2.2)
(2.3)
Контролирующим называется тот процесс, который имеет наибольшее сопротивление. Значение контролирующего процесса необходимо знать при выборе способа коррозионной защиты. Наиболее значительный эффект всегда будет давать то мероприятие, которое затрудняет именно контролирующий процесс.
В водных растворах электролитов во многих случаях коррозии металлов в качестве окислителей, участвующих в катодных реакциях, выступают протоны водорода (например, в кислых средах) и молекулы кислорода, растворенные в электролите.
В данном случае обратимый потенциал катода определяется обратимым потенциалом реакции с наиболее положительным потенциалом – ре-
акции ионизации кислорода |
|
|
|
|
|
|
|
|
|
|
|
|||||||||||
|
|
|
|
|
|
|
|
|
|
|
|
|
|
|
0 |
|
|
|
|
|
|
|
O |
|
4H |
4e |
2H |
|
O , |
=+1,23 B |
|
|
|
||||||||||||
2 |
|
2 |
EO |
|
|
(2.4) |
||||||||||||||||
|
|
|
|
|
|
|
|
|
|
|
|
|
|
|
|
2 |
|
|
|
|
|
|
|
|
E |
обр |
E |
обр |
1,23 |
RT |
2,303lg a |
|
|
1,23 0,059pH. |
|||||||||||
|
|
|
|
|
||||||||||||||||||
|
|
кт |
|
|
|
|
|
|
||||||||||||||
|
|
|
|
O |
2 |
|
|
|
|
|
|
|
F |
|
|
|
H |
|
||||
|
|
|
|
|
|
|
|
|
|
|
|
|
|
|
|
|
|
|
|
|||
|
|
|
|
|
|
|
|
|
|
|
|
|
|
|
|
|
|
|
|
|
||
Катодная реакция выделения водорода |
|
|
|
|||||||||||||||||||
|
|
|
|
|
|
2H |
|
|
|
|
|
H , E0 |
0,0B. |
|
||||||||
|
|
|
|
|
|
2e |
|
(2.5) |
||||||||||||||
|
|
|
|
|
|
|
|
|
|
|
|
|
|
|
|
|
2 |
|
|
|
|
|
|
|
|
|
|
|
|
|
|
|
|
|
|
|
|
|
|
|
|
|
|
|
|
|
|
|
|
|
|
EHобр |
|
RT |
|
2,303lg a |
0,059pH . |
|||||||||||
|
|
|
|
|
|
|
F |
|||||||||||||||
|
|
|
|
|
|
|
|
2 |
|
|
|
|
|
|
H |
|
|
|
|
|||
|
|
|
|
|
|
|
|
|
|
|
|
|
|
|
|
|
|
|
|
|
18
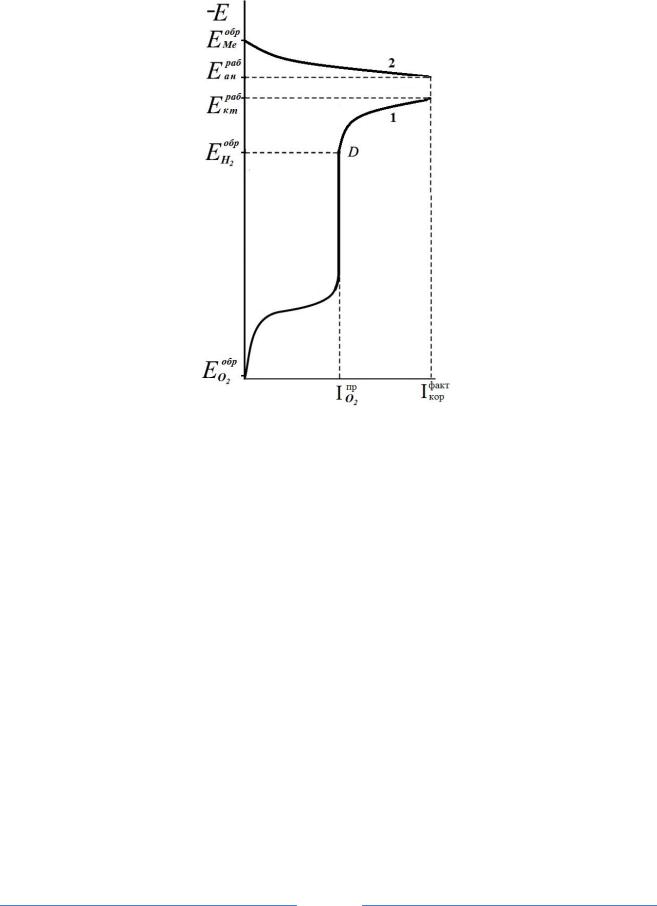
Данная реакция будет реализоваться на катоде, если рабочий по-
тенциал катода |
E |
|
раб |
будет отрицательнее обратимого потенциала водо- |
|||
кт |
|||||||
|
|||||||
родного электрода |
E |
обр |
. |
||||
H |
2 |
||||||
|
|||||||
|
|
|
|
|
|
Рис. 2. Поляризационная коррозионная диаграмма:
1 и 2 – катодная и анодная поляризационные кривы;
E обр Ме
и
E обр О 2
– обратимые потен-
циалы анодной реакции окисления металла и катодной реакции восстановления моле-
кулярного кислорода); |
E |
раб |
и |
E |
раб |
– рабочие потенциалы (под фактическим током |
ан |
кт |
|||||
|
|
|
|
|
коррозии) анода и катода
В этом случае на катоде будут одновременно протекать обе реакции
(ионизации кислорода на предельном токе диффузии
I пр о2
и выделение во-
дорода), то есть процесс коррозии металла протекает с водороднокислородной деполяризацией. Ток, идущий на реакцию ионизации кислорода, можно определить из коррозионной диаграммы экстраполяцией на ось токов точки (D) на катодной поляризационной кривой при потенциале
EHобр2 (при этом потенциале нет выделения водорода на катоде). Тогда ток для процесса выделения водорода можно определить как разницу между
I факт
фактическим током коррозии кор и током процесса ионизации кислоро-
да I пр .
о2
19
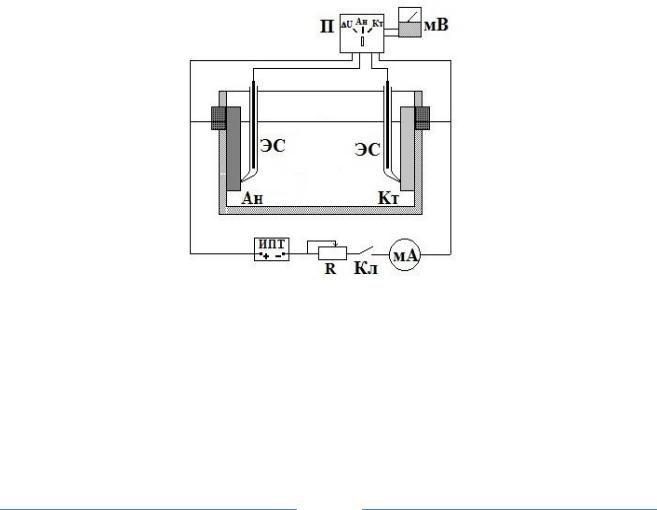
Цель работы: – построение поляризационной диаграммы коррозии металла на основе экспериментально снятых поляризационных кривых для гальванопары в электролите (при определенном соотношении анодной
икатодной поверхностей), заданным преподавателем;
–определение скорости коррозии металла, контролирующего процесса (по степеням контроля) и вида деполяризующих процессов (исследование влияния ингибиторов на ход поляризационных диаграмм по особому заданию).
Экспериментальная часть
Работа проводится в ячейке, оборудованной устройством для опускания электродов в раствор на определенную глубину в соответствии с заданным соотношением рабочих поверхностей анода и катода. Потенциалы электродов и падение напряжения в электролите замеряются милливольтметром.
Электродами сравнения (ЭС) служат цинковые стержни, которые помещают во встроенные стеклянные геберы вблизи рабочих электродов.
Все электроды зачистить наждачной бумагой, промыть дистиллированной водой и высушить фильтровальной бумагой. Для поляризации собирается схема (рис. 3).
Рис. 3. Электрическая схема для снятия поляризационных диаграмм коррозии:
Ан – анод, Кт – катод, ЭС – цинковый электрод сравнения, Кл – ключ замыкания, П – переключатель измерения потенциалов, мА – миллиамперметр, мВ – милливольтметр, ИПТ – источник постоянного тока, R – магазин сопротивлений
До включения тока измеряются потенциалы анода и катода. Затем, изменяя сопротивление (R), устанавливают последовательно следующие
20