
Коррозия лабы
.pdf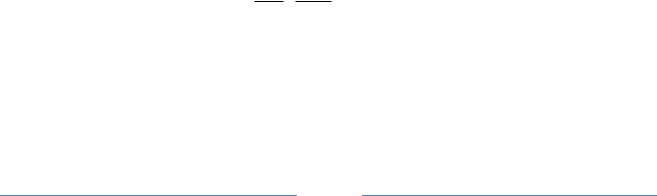
После окончания опыта электроды вынимают и измеряют рабочие (смоченные электролитом) размеры для расчета площади поверхности
электродов – Sан, Sкт, Sпр.
По полученным данным строят диаграмму коррозии.
2.Катодная защита от внешнего источника постоянного тока.
Проводят путем катодной поляризации коррозионного элемента от внешнего источника постоянного тока с помощью инертного анода
(рис.4).
Для более легкого установления постоянной величины катодного тока в цепь вспомогательного инертного электрода включает регулируемое высокоомное сопротивление (Rм3).
Используют ту же электрохимическую ячейку, но вместо протектора устанавливают инертный вспомогательный электрод Аз (графитовый или свинцовый).
Порядок выполнения работы.
Сначала устанавливают постоянную величину тока в коррозионном элементе. Для этого при полностью введенном сопротивлении магазина (Rм1) замыкают ключ (Кл1) и постоянно уменьшают сопротивление магазина (Rм1) до нуля. Ключ (Кл3) переключают в левое положение, (Кл2) замыкают вновь. Задавая определенную постоянную величину катодного тока от внешнего источника постоянного тока, замеряют установившуюся величину остаточного тока в коррозионном элементе с одновременным замером электродных потенциалов милливольтметром (V1) относительно
цинковых электродов сравнения Eанраб и Eктраб до тex пор, пока сила тока в
коррозионном элементе не станет равной нулю, всего не менее 5 ÷ 6 замеров. Равенство тока нулю свидетельствует о прекращении коррозии в короткозамкнутом макроэлементе.
При токе коррозии равном нулю замеряют силу внешнего тока катодной защиты и записывают напряжение по вольтметру (V2) на источнике постоянного тока. Экспериментальные данные заносят в табл. 1.
Расчет параметров катодной электрохимической защиты:
Скорость коррозии защищаемого металла или металла – протектора
K |
|
|
I |
|
|
A |
10 |
|
|
|
Ме |
|
|||||
|
|
|
|
|
4 |
, |
||
|
вес |
|
Sан |
|
z F |
|
||
|
|
|
|
|
|
|||
где I – сила тока в элементе Iкорo |
(на протекторе Iкорпр ), А; |
(5.3)
Sан – рабочая (смоченная электролитом с двух сторон) поверхность анода (протектора), см2;
AМе – атомный вес металла анода (протектора), г;
51

z – изменение валентности в анодной электрохимической реакции; F – число Фарадея, 26,8 А·час/г-экв.
Таблица 1
Исследование протекторной защиты на модели гальванического элемента
Коррозионный элемент (………… ). Протектор – …………. Электролит……..…; Sан = ………см2; Sкт =………см2; Межэлектродное расстояние……………………см.
Сила тока |
I , мА |
Потенциал (по цинку), |
B |
|
Параметры защиты |
|
|||||||
В корр. |
|
На про- |
Е |
|
Е |
|
Е |
пр |
P , |
Э , |
Е |
, B |
|
элементе |
|
текторе |
ан |
кт |
% |
% |
Эксп. |
Теор. |
|||||
|
|
|
|
||||||||||
|
|
|
|
|
|
|
|
||||||
0 |
|
0 |
|
|
|
|
|
|
|
|
|
|
|
I1 |
|
0 |
|
|
|
|
|
|
|
|
|
|
|
I2 |
|
0 |
|
|
|
|
|
|
|
|
|
|
|
и.т.д. |
|
0 |
|
|
|
|
|
|
|
|
|
|
|
In |
|
0 |
|
|
|
|
|
|
|
|
|
|
|
С протектором |
|
|
|
|
|
|
|
|
|
|
|
||
Iк1 |
|
IПр1 |
|
|
|
|
|
|
|
|
|
|
|
Iк2 |
|
IПр2 |
|
|
|
|
|
|
|
|
|
|
|
и.т.д. |
|
|
|
|
|
|
|
|
|
|
|
|
|
0 |
|
IПр |
|
|
|
|
|
|
|
|
|
|
|
Защита внешним |
|
|
|
|
|
|
|
|
|
|
|
||
током |
|
|
|
|
|
|
|
|
|
|
|
||
Iк1 |
|
Iвнеш1 |
|
|
|
|
|
|
|
|
|
|
|
Iк2 |
|
Iвнеш2 |
|
|
|
|
|
|
|
|
|
|
|
и.т.д. |
|
|
|
|
|
|
|
|
|
|
|
|
|
0 |
|
Iвнеш |
|
|
|
|
|
|
|
|
|
|
|
Глубинный показатель коррозии металла анода или протектора П ,
мм/год (проницаемость): |
|
|
|
П |
Kвес 8,76 |
, |
(5.4) |
|
|||
|
d Ме |
|
где d Ме – плотность металла анода (протектора), г/см3.
Степень протекторной защиты при каждой величине тока от протектора или от внешнего источника
где
I ост кор
Р% |
Iкорo |
Iкорост |
100% |
, |
(5.5) |
|
I o |
||||||
|
|
|
||||
|
|
кор |
|
|
|
Iкорo – сила тока коррозии при сопротивлении магазина Rм1 = 0;
– остаточная сила тока коррозии в коррозионном элементе при задан-
ном токе от протектора или внешнего источника тока по ( М А 1) . Электрохимическая эффективность катодной и протекторной защи-
ты рассчитывается по формуле
52
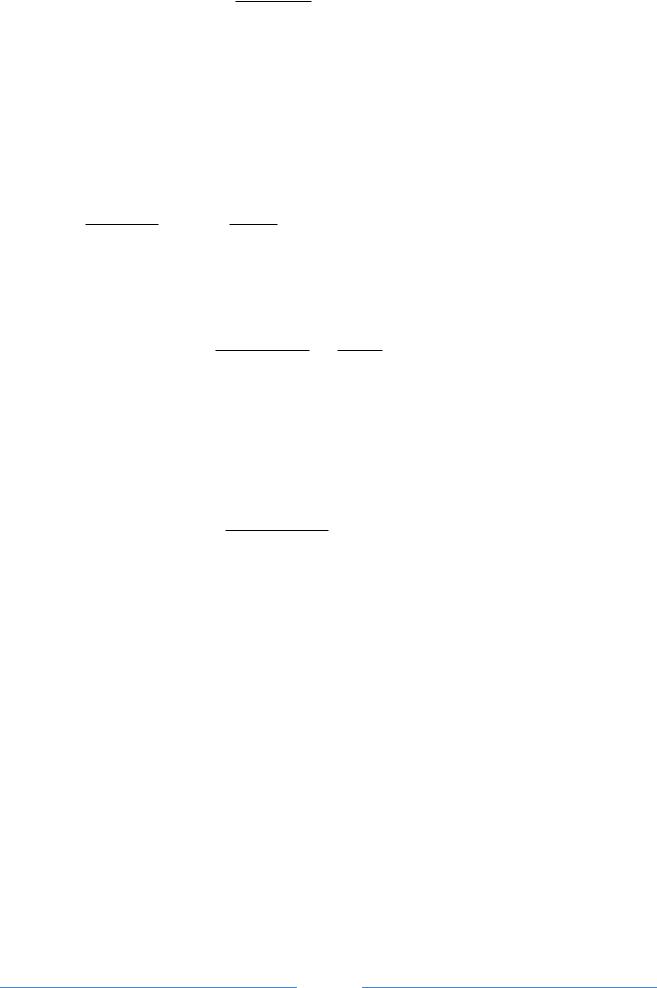
Э% |
I |
o |
I |
ост |
|
|
|||
|
кор |
|
кор |
|
|
|
|
||
|
|
Iвнешн |
100 %
,
(5.6)
где |
Iвнешн |
– ток, идущий от протектора или от внешнего источника тока. |
|
|
Эффективность электрохимической защиты есть отношение положительного защитного эффекта (+)ЗЭ (на сколько уменьшилась скорость
коррозии защищаемого металла |
Iкор Iкор |
) к величине затрат |
Iвнешн |
– |
|
|
o |
ост |
|
|
|
внешнего тока от протектора или источника постоянного тока. Электрохимическую эффективность катодной защиты можно выразить через ве-
личину коэффициента защитного эффекта |
К |
зэ . |
|
|
|
I |
o |
|
I |
ост |
|
( )ЗЭ |
|
|
|
|
Э% |
кор |
кор |
100 % |
100 % К |
|
100 % 1/(1 P |
/ P ) 100 % |
||||
|
|
|
|
||||||||
|
|
|
|
|
|
зэ |
|||||
|
|
|
Iвнешн |
|
Iвнешн |
|
a |
к |
|||
|
|
|
|
|
|
|
|
(5.7)
Теоретическое смещение потенциала конструкции Е Ey Ex под действием внешней катодной поляризации можно определить по формуле
(5.8)
Е |
2,303 R T. |
lg |
|
z F |
|||
|
|
j |
o |
|
|
кор |
|
jвнешн. |
,
(5.8)
где
jo кор
I o кор
/ San
– плотность тока коррозии в исследуемом макроэлементе и
плотность
jвнешн I |
пр |
/ |
|
кор |
|||
|
|
внешнего катодного тока (при использовании протектора
|
2 |
. |
пр ), А/см |
||
S |
|
|
Удельный расход электроэнергии (W , кВт·ч/м2·год) при катодной защите с наложением внешнего тока рассчитываем по формуле:
W
Iвнешн V 8,76
Sан.
104
,
(5.9)
где
А;
Iвнешн
– сила внешнего тока от протектора (источника постоянного тока),
V – напряжение на внешнем источнике постоянного тока, В (по показаниям вольтметра (V2) при токе коррозии анода равном нулю).
Экспериментальные и расчетные данные приводятся в сводных таблицах, примерная форма которых дается ниже.
|
|
|
|
|
Таблица 2 |
|
|
Параметры протекторной защиты |
|
|
|||
|
|
|
|
|
|
|
Максимальная сила тока, мА |
Скорость корро- |
Скорость |
Расход протек- |
|
||
в гальваниче- |
на протекторе |
зии анода, |
разрушения |
|
|
|
ском элементе |
|
Kвес |
ан, г/м2∙час |
анода, |
тора, Kвес пр, |
|
|
кг/м2 год |
|
||||
|
|
|
|
П , мм/год |
|
|
|
|
|
|
|
|
|
По данным измерений построить 2 коррозионные диаграммы: на од-
53

ной диаграмме отразить изменение потенциалов от силы тока при работе коррозионного элемента без присоединения протектора и при протекторной защите; на другой при работе коррозионного элемента без внешнего тока при защите внешним током).
Внимание! При построении диаграммы изменения потенциалов при наложении катодной защиты следует учесть, что катодный ток равен сумме остаточного анодного тока коррозии защищаемого металла и внешнего катодного тока, идущего от источника постоянного тока или от протектора.
|
|
|
|
|
Таблица 3 |
|
|
Параметры электрохимической катодной защиты |
|||||
|
|
|
|
|
|
|
Максимальная сила тока, I , |
Скорость кор- |
Напряжение |
Удельный рас- |
|
||
мА |
|
розии анода |
ход электро- |
|
||
|
V |
, |
|
|||
в гальваниче- |
на инертном |
Kвес ан, г/м2 час |
энергии W , |
|
||
В |
|
|
||||
ском элементе |
аноде |
|
|
|
кВт ч/м2·год |
|
|
|
|
|
|
|
|
Отчёт по работе должен состоять из введения, методики эксперимента, экспериментальных результатов в виде таблиц, расчетов и графиков, обсуждения результатов, рекомендации по выбору способа катодной защиты металла от коррозии, его экономическую целесообразность, выводов и списка использованной литературы.
Вариант «Б»– для студентов, обучающихся по направлениям: 22.03.02 – «Металлургия»; 22.03.01 – «Материаловедение и технология материалов».
Экспериментальная часть
Электроды коррозионного элемента и вспомогательный анод тщательно обработать наждачной бумагой, с тем, чтобы удалить с их поверхности оксидные пленки (замерить размеры для расчета рабочих поверхностей электродов). Затем электроды обезжирить протиркой влажной содой, промыть дистиллированной водой, установить в элемент, залитый заданным раствором. В первой части опыта в качестве вспомогательного анода использовать протектор – растворимый электрод с более отрицательным потенциалом, чем у анода элемента. Электрическая схема опыта приведена на рис.5.
Замыкают ключ (Кл1), ключ (Кл2) разомкнут. После 3÷5 минут выдержки замеряют и записывают силу тока, проходящего через миллиамперметр (мА1). Затем при полностью включенном магазине сопротивле-
54
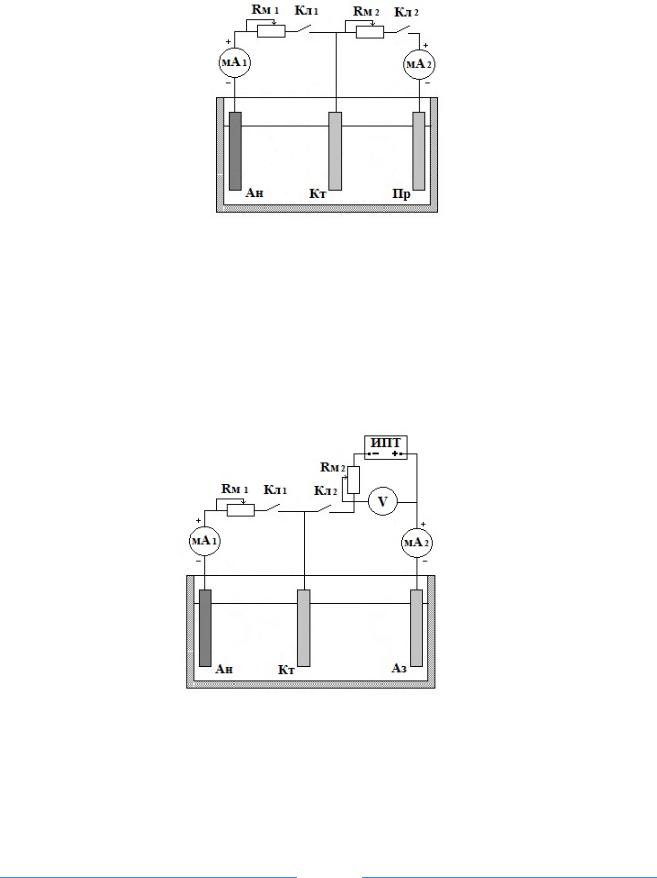
ний (Rм1) замыкают ключ (Кл2) и, уменьшая сопротивление магазина (Rм2), добиваются отсутствия тока в цепи элемента (или величину остаточного тока коррозии при сопротивлении магазина Rм2 = 0, при максимальном токе протектора). По достижении этого отмечают величину протекающего тока в цепи протектора (по миллиамперметру (мА2)).
Рис. 5. Электрическая схема протекторной защиты
Ан – анод, Кт – катод, Пр – протектор, Кл1– электрический ключ цепи микроэлемента, Кл2 – электрический ключ цепи протектора, Rм1 и Rм2 – магазины сопротивлений, мА1 и мА 2 – миллиамперметры
После окончания первого этапа опыта заменяют электрод – протектор на инертный электрод и изменяют схему опыта для проведения исследования катодной защиты с наложением внешнего тока (рис.6).
Рис. 6. Электрическая схема защиты с наложением внешнего катодного тока
Ан – анод, Кт – катод, Аз – анод внешней защиты (инертный электрод), Кл1– электрический ключ цепи макроэлемента, Кл2 – электрический ключ цепи протектора, Rм1 и Rм2 – магазины сопротивлений, мА1 и мА2 – миллиамперметры, ИПТ – источник постоянного тока, V – вольтметр
55
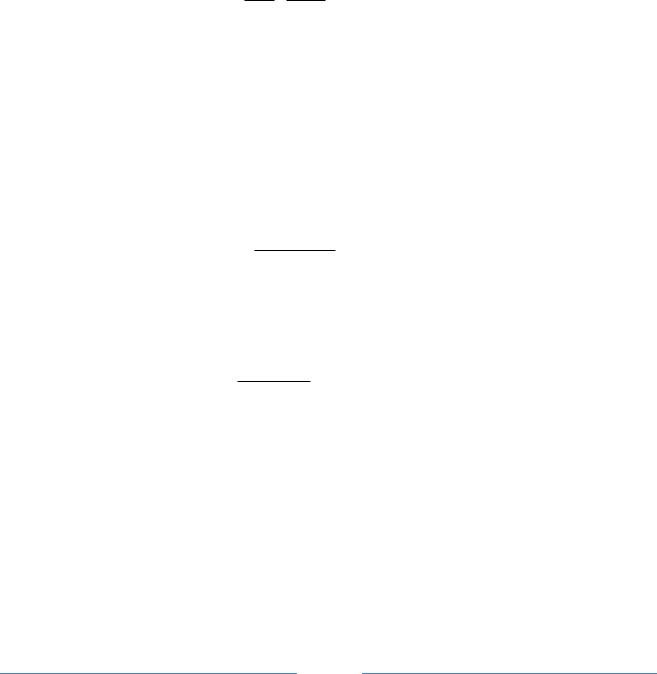
Первоначально определяют интенсивность работы гальванопары Ан
– Кт, замеряя ток при замкнутом ключе (Кл1) и сопротивлении магазина (Rм1 = 0). Затем замыкают ключ (Кл2) и включают внешний источник постоянного тока. Постепенно, увеличивая подаваемое напряжение, уменьшая сопротивление магазина (Rм2), добиваются отсутствия тока по миллиамперметру (мАl).
Записать протекающую при этом силу тока в цепи катодной защиты (по миллиамперметру (мА2)) и напряжения между электродами Кт – А З .
Равенство тока нулю в элементе свидетельствует о прекращении коррозии.
По величине силы тока в коррозионном элементе можно рассчитать скорость коррозии металла анода, Kвес ан, а по величине тока в цепи про-
тектора – скорость коррозии протектора |
|
Kвес пр, г/м2·час |
K |
|
|
|
вес |
|||
|
|
где I – сила тока в элементе
|
I |
|
Sан |
||
I |
o |
|
кор |
||
|
|
A |
10 |
|
Ме |
|
||
|
4 |
, |
|
|
z F |
|
|
|
|
|
(на протекторе
I |
пр |
|
кор |
||
|
), А;
(5.8)
Sан – рабочая (смоченная электролитом с 2-х сторон) поверхность анода (протектора), см2;
AМе – атомный вес металла анода (протектора), г;
z – изменение валентности в анодной электрохимической реакции; |
||||||
F |
– число Фарадея, 26,8 А·час/г-экв. |
|
|
|||
|
Глубинный показатель коррозии металла анода или протектора |
|||||
мм/год (проницаемость): |
|
|
|
|
|
|
|
|
K |
|
8,76 |
|
|
|
П |
вес |
, |
(5.9) |
||
|
|
|
||||
|
|
|
|
|||
|
|
|
d |
|||
|
|
|
|
|
||
|
|
|
|
Ме |
|
|
П
,
где
d Ме
– плотность металла анода (протектора), г/см3.
Степень протекторной защиты при каждой величине тока от протектора или от внешнего источника
Р% |
I |
o |
I |
ост |
|
|
|
|
|||
|
кор |
|
|
кор |
|
|
|
|
|
||
|
|
I |
o |
|
|
|
|
кор |
|
||
|
|
|
|
|
100%
,
(5.10)
где Iкорo – сила тока коррозии при сопротивлении магазина Rм1 = 0;
Iкорост – остаточная сила тока в коррозионном элементе при заданном токе от
протектора или внешнего источника тока по ( М А 1) .
Электрохимическая эффективность катодной и протекторной защиты рассчитывается по формуле
|
I o |
I ост |
|
|
|
Э% |
кор |
кор |
100 % , |
(5.11) |
|
Iвнешн. |
|||||
|
|
|
56

где |
Iвнешн |
– ток идущий от протектора или от внешнего источника тока. |
|||
|
|
|
|
|
|
|
Удельный расход электроэнергии (W , кВт·ч/м2·год) при катодной |
||||
защите с наложением внешнего тока рассчитываем по формуле: |
|
||||
|
|
W |
Iвнешн V 8,76 |
104 , |
(5.12) |
|
|
|
|||
где |
|
|
Sан. |
|
|
Iвнешн |
– сила внешнего тока от протектора (источника постоянного то- |
||||
|
|
|
|
|
|
ка), А; |
|
|
|
|
|
V – напряжение на внешнем источнике постоянного тока, В (по показани- |
ям вольтметра(V2) при токе коррозии анода равном нулю); Экспериментальные и расчетные данные приводятся в сводных таб-
лицах (табл. 2 и табл. 3)
Отчет по работе должен состоять из введения, методики эксперимента, экспериментальных результатов, обсуждения результатов, выводов и списка использованной литературы.
ВОПРОСЫ ДЛЯ САМОПРОВЕРКИ
1.Как изменится локальный ток коррозии двухэлектродной системы при подключении дополнительного макроанода? (Дать диаграмму коррозии).
2.При каких условиях достигается полная электрохимическая защита?
3.Докажите графически, что ток внешней катодной поляризации в большинстве случаев больше, иногда равен, но никогда не меньше тока коррозии.
4.Каким требованиям должен удовлетворять металл протектора?
5.Докажите графически, что коррозионный процесс, имеющий большую катодную поляризуемость, будет иметь больший защитный эффект при одинаковой величине катодного тока внешней поляризации?
6.В каких случаях полная электрохимическая защита становится экономически невыгодной и когда она практически недостижима?
7.Что такое перезащита и чем она вызвана и ее последствия?
8.Каков физический смысл коэффициента защитного эффекта?
9.Каков физический смысл понятия «радиус действия» протектора?
10.Сокращаются ли суммарные потери металлов в случае защиты протектором?
11.Напишите реакцию, протекающую на электродах в Вашем случае коррозионных испытаний.
12.Какие материалы могут использоваться в качестве анода – протектора при катодной электрохимической защите?
57

13. Дать сравнительную характеристику катодной электрохимической и протекторной защит?
ИСПЫТАНИЯ ХРОМОНИКЕЛЕВЫХ СПЛАВОВ НАСКЛОННОСТЬ К МЕЖКРИСТАЛЛИТНОЙ КОРРОЗИИ
Лабораторная работа № 6
Межкристаллитная коррозия (МКК), вызывающая избирательное разрушение по границам кристаллитов, приводит к снижению или полной потере прочности и пластичности металлов. Этот вид коррозии наблюдается в газовых средах и растворах электролитов. Появление межкристаллитной коррозии в электролитах чаще всего связано с электрохимической неоднородностью сплавов. Неоднородность сплавов является следствием распада некоторых твердых растворов в определенных условиях с выделением вторичных фаз, которые могут быть либо анодами, либо катодами по отношению к близлежащим участкам твердого раствора.
Особый интерес представляет межкристаллитная коррозия хромоникелевых сталей. Склонность к межкристаллитной коррозии хромоникелевых аустенитных сталей возникает в результате определенной термической обработки при неблагоприятном химическом и фазовом составе сплава. Склонность к межкристаллитной коррозии этих сталей объясняется обеднением хромом твердого раствора вблизи границ кристаллитов из– за выделения на поверхности кристаллитов карбидов хрома. Однако сам факт выделения карбидов хрома по границам кристаллитов не мог бы вызвать значительное обеднение поверхностного слоя сплава хромом, если бы скорости диффузии углерода и хрома были одинаковы.
Атомы углерода, имеющие меньший радиус, обладают гораздо более высокой подвижностью в кристаллической решетке твердого раствора, вследствие чего, в образовании карбидов участвует почти весь углерод сплава, а хром с большим атомным радиусом имеет низкую скорость диффузии, поэтому в образовании карбидов участвуют атомы хрома в основном из пограничной зоны. Стали с большим содержанием углерода должны быть более восприимчивы к появлению склонности к межкристаллитной коррозии.
58

На основе экспериментальных исследований в последние годы считают, что максимальное содержание углерода, не вызывающее появление у стали склонности к межкристаллитной коррозии, равно 0,007%.
Большое влияние на склонность хромоникелевых сталей к межкристаллитной коррозии оказывает длительность выдержки стали при температурах, вызывающих эту склонность (600÷6500С). При правильном режиме термической обработки хромоникелевых сталей, при температуре 1080÷11500С углерод и хром переходят из карбидной фазы в твердый раствор аустенита, содержание этих компонентов выравнивается по всему объему зерна. При достаточно быстром фиксировании этого состояния (охлаждении в воде) фиксируется однородность твердого раствора и исключается вероятность появления у стали склонности к межкристаллитной коррозии.
Существующие методы определения склонности сплавов к межкристаллитной коррозии можно подразделить на физические,химические и электрохимические.
Определить МКК можно следующими физическими методами:
Ультразвуковой метод контроля основан на принципе рассеивания ультразвуковых колебаний на участках металла, пораженных МКК;
Метод вихревых токов позволяет определить глубину межкристаллитной коррозии, что обусловлено зависимостью возбуждаемых вихревых токов на контролируемом участке материала изделия от его электрической проводимости. Разрушение границ зерен, нарушающее связь между кристаллами, приводит к снижению электрической проводимости.
Вэтих двух методах за количественные показатели МКК принимают изменение измеряемых характеристик образцов, выраженное в процентах по отношению к их значениям до коррозии.
Внастоящее время разработаны ускоренные химические методы
определения склонности к МКК коррозионностойких сталей. Среди них следует отметить следующие:
Взависимости от химического состава стали и сплава и их назначения ГОСТ 6032-2003 «СТАЛИ И СПЛАВЫ КОРРОЗИОННО-СТОЙКИЕ. Методы испытаний на стойкость к межкристаллитной коррозии» рекомендует один из следующих ускоренных методов:
Метод АМУ. Образцы сталей выдерживают в кипящем водном растворе сернокислой меди и серной кислоты в присутствии металлической меди (стружка). Продолжительность выдержки в кипящем растворе - (8,00
±0,25) ч
Метод применяют для контроля устойчивости к МКК сталей:
-ферритного класса марок 08Х17Т, 15Х25Т
-аустенитно-фсрритного класса марок 08Х22Н6Т, 08Х21Н6М2Т,
59

- аустенитного класса марок 12Х18Н9, 12Х18Н9Т, 12Х18Н10Т и др. Метод АМУФ. Образцы стали выдерживают при температуре 20 °С
- 30 °С в водном растворе сернокислой меди, серной кислоты, фтористого натрия или калия в присутствии металлической меди.
Продолжительность испытаний для сталей без молибдена – 2,0 ± 0,1 ч, содержащих молибден – 3,0 ± 0,1 ч.
Метод ВУ.Образцы стали или сплава выдерживают в кипящем водном растворе сернокислого оксидного железа и серной кислоты.
Метод применяют для контроля устойчивости к МКК стали марки 03Х21Н21М4ГБ и сплавов на железоникелевой основе марок: 06ХН28МДТ, 03ХН28МДТ и ХН30МДБ.
Продолжительность выдержки в кипящем растворе должна состав-
лять 48,0 ± 0,25 ч.
Метод ДУ. Образцы выдерживают в кипящем водном растворе 65 %-ной азотной кислоты. Метод применяют для контроля устойчивости к МКК сталей марок: 02Х18Н11, 03Х18Н11, 03Х18Н12, 03Х17Н14М3, 03Х24Н6АМ3, 02Х25Н22АМ2.
Продолжительность испытаний составляет 240 ч, пять циклов по 48,00 ± 0,25 ч каждый со сменой раствора после каждого цикла.
Оценка результатов испытаний на МКК 1. Определение наличия МКК с помощью изгиба образца
Осмотр изогнутых образцов проводят с помощью лупы при увеличении 7 - 12х.
Отсутствие трещин на образцах, изогнутых после испытания, за исключением продольных трещин и трещин непосредственно на кромках, свидетельствует о стойкости стали или сплава к МКК.
Наличие трещин на образцах, изогнутых после испытания, и отсутствие трещин на изогнутых таким же образом контрольных образцах свидетельствует о склонности стали к МКК.
2.Металлографический метод определения МКК
Для выявления МКК металлографическим методом из неизогнутого участка образца, прошедшего испытания, вырезают шлиф таким образом, чтобы плоскость реза была перпендикулярна к контролируемой поверхности образца. Наличие и глубину МКК устанавливают на протравленных шлифах при увеличении не менее х200.
Травление проводят лишь до слабого выявления границ зерен. Признаком стойкости к МКК при металлографическом контроле считают разрушение границ зерен на максимальную глубину до 30 мкм.
Электрохимические методы:
Потенциостатический метод – травление в 50%-м растворе серной кислотыпри контролируемом потенциале в течение 30 мин (или с исполь-
60