
Wasserscheid P., Welton T. - Ionic Liquids in Synthesis (2002)(en)
.pdf
266 Hélène Olivier-Bourbigou, Alain Forestière
water is added in a mixer, followed by efficient phase separation in a settler. One advantage of this process is its flexibility and good performance with respect to the olefin carbon number.
The combination of ionic liquids with supercritical carbon dioxide is an attractive approach, as these solvents present complementary properties (volatility, polarity scale….). Compressed CO2 dissolves quite well in ionic liquid, but ionic liquids do not dissolve in CO2. It decreases the viscosity of ionic liquids, thus facilitating mass transfer during catalysis. The separation of the products in solvent-free form can be effective and the CO2 can be recycled by recompressing it back into the reactor. Continuous flow catalytic systems based on the combination of these two solvents have been reported [19]. This concept is developed in more detail in Section 5.4.
Membrane techniques have already been combined with two-phase liquid catalysis. The main function of this method is to perform fine separation of undesirable constituents from the catalytic system after phase decantation has already performed the coarse separation of the catalyst from the products. This technique can be applied to ionic liquid systems as a promising approach for the selective removal of volatile solutes from ionic liquids [20].
Ionic liquids have already been demonstrated to be effective membrane materials for gas separation when supported within a porous polymer support. However, supported ionic liquid membranes offer another versatile approach by which to perform two-phase catalysis. This technology combines some of the advantages of the ionic liquid as a catalyst solvent with the ruggedness of the ionic liquid-polymer gels. Transition metal complexes based on palladium or rhodium have been incorporated into gas-permeable polymer gels composed of [BMIM][PF6] and poly(vinylidene fluoride)-hexafluoropropylene copolymer and have been used to investigate the hydrogenation of propene [21].
5.3.5
Immobilization of Catalysts in Ionic Liquids
For the use of ionic liquids in catalytic or organic reactions, two main methodologies have been developed. In the first one, the ionic liquid is both the catalyst and the reaction solvent. This is the case in acid-catalyzed reactions in which Lewis acidic ionic liquids such as acidic chloroaluminates are both active catalytic species and solvents for carbenium ions. In this case, the dissolution of the inorganic Lewis acid (e.g., AlCl3) in the organic phase is not observed. The second approach, discussed in Section 5.2, is when the ionic liquid acts as a “liquid support” for the homogeneous catalyst. In this technology, the catalyst (in general a transition metal complex) is immobilized in the ionic phase and the products form the upper phase, as described in Section 5.3.4. To achieve the development of such an approach in a continuous process, the key point is to immobilize and stabilize the catalyst in the ionic liquid in the presence of an organic second phase with minimum loss of metal. Two approaches have been investigated:
1)the active species is known to be ionic in conventional organic solvents,
2)the active species is characterized as a non-charged complex.
5.3 Ionic Liquids in Multiphasic Reactions |
267 |
|
|
In the first case, one may expect that the catalyst should remain ionic and be retained without modification in the ionic liquid. Different successful examples have been reported, such as olefin and diolefin hydrogenation reactions catalyzed by the cationic [HRh(PPh3)2(diene)][PF6] complexes [22], and aromatic hydrocarbon hydrogenation catalyzed by the [H4Ru4(C6H6)4][BF4]2 cluster [23]. In the presence of hydrogen, this latter complex probably forms the [H6Ru4(C6H6)4][BF4]2 complex, which acts as the effective arene hydrogenation catalyst. Another example is olefin dimerization catalyzed by the cationic [HNi(olefin)][A] (A is a chloroaluminate anion) complexes. These species can be formed by in situ alkylation of a nickel(II) salt with an acidic alkylchloroaluminate ionic liquid acting both as the solvent and as the co-catalyst [24]. The cationic [(methallyl)Ni(Ph2PCH2PPh2(O))][SbF6] complex proved to be stable and active for ethene oligomerization in [PF6]–-based ionic liquids without the addition of Lewis acid. The high electrophilicity of the Ni center, which is responsible for the activity of the catalyst, is probably not altered by the ionic solvent [25]. In the Suzuki reaction, the active species in [BMIM][BF4] is believed to be the tricoordinated [Pd(PPh3)2(Ar)][X] complex that forms after oxidative addition of the aryl halide to [Pd(PPh3)4] [26]. Thanks, therefore, to their low nucleophilicity, ionic liquids do not compete with the unsaturated organic substrate for coordination to the electrophilic active metal center. The different recycling experiments demonstrate the stability of these organometallic complexes in ionic liquids.
Not only cationic, but also anionic, species can be retained without addition of specially designed ligands. The anionic active [HPt(SnCl3)4]3– complex has been isolated from the [NEt4][SnCl3] solvent after hydrogenation of ethylene [27]. The PtCl2 precursor used in this reaction is stabilized by the ionic salt (liquid at the reaction temperature) since no metal deposition occurs at 160 °C and 100 bar. The catalytic solution can be used repeatedly without apparent loss of catalytic activity.
In the second case, in which the active catalytic species is assumed to be uncharged, leaching of the transition metal in the organic phase can be limited by the use of functionalized ligands. As the triumph of aqueous biphasic catalysis follows the laborious work involved in the development of water-soluble ligands, recent investigations have focused on the synthesis of new ligands with “tailor made” structures for highly active and selective two-phase catalysts and for good solubility in the ionic liquid phase. These ligands are mainly phosphorus ligands with appropriate modifications (Scheme 5.3.1).
Polar groups such as the cationic phenylguanidinium groups 1–3 [28, 29], the imidazolium and pyridinium groups 4 and 5 [30], and the 2-imidazolyl groups 6 and 7 [31] have been reported. A cobaltocinium salt bearing phosphine donors (8) has also been described [32]. Phosphites are well known ligands in homogeneous Rh-catalyzed hydroformylation, affording enhanced reaction rates and regioselectivities. Since they are unstable towards hydrolysis, examples of their use in aqueous biphasic catalysis are rare. Ionic liquids offer suitable alternative solvents compatible with phosphites 9 [28].
To date, these functionalized ligands have been investigated on the laboratory scale, in batch operations to immobilize rhodium catalyst in hydroformylation.
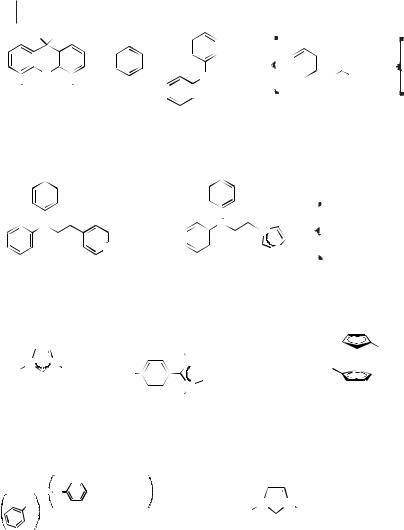

5.3 Ionic Liquids in Multiphasic Reactions |
269 |
|||
|
|
|
|
|
|
|
|
|
|
|
|
|
|
|
|
|
|
|
|
|
|
|
|
|
|
|
|
N |
|
|
|
|
N |
|
|
|
|
|
|
|
|
|
|
|
Br- |
|
|
Me |
|
|
|
|
Bu |
|
|
|
|
|
|
|
|
|
|
|
|
|
|
|
|
|
||||
|
|
|
|
|
|
|
|
|
|
Pd(OAc)2 |
|
|
|
|
|
|
Br |
||
|
|
|
|
|
|
|
|
|
|
|
|
|
|
||||||
|
|
|
|
|
|
|
|
|
|
|
|
|
|
||||||
N |
|
|
|
+ |
|
|
|
N |
|
|
Br |
Pd |
+ isomers |
||||||
Me |
|
|
|
|
|
|
|
|
|
Bu |
NaOAc |
|
|
|
|
|
|||
|
|
|
|
|
|
|
|
|
|
|
|
|
|
||||||
|
|
|
H |
|
|
Bu |
|
|
|
|
Me |
||||||||
|
|
|
|
|
|
|
|
|
|
|
|
|
N |
|
|
|
|
N |
|
|
|
|
|
|
|
|
|
|
|
|
|
|
|
|
|
|
|
|
|
|
|
|
|
|
|
|
|
|
|
|
|
|
|
|
|
|
|
|
|
Scheme 5.3-2: Formation of carbene complexes by dialkylimidazolium salt deprotonation.
|
|
|
|
|
|
|
|
|
|
|
|
|
|
|
+ |
|
|
|
|
B F - Pt(PPh3)4 |
|
|
N |
|
|
|
|
N |
|||
|
|
|
|
|
|
|
|
|
|
||||||
|
|
|
|
|
|
|
|
|
|
|
|||||
|
|
|
|
||||||||||||
N |
+ N |
|
Me |
|
|
|
|
Me |
[BF4]- |
||||||
|
|
|
4 |
|
|
|
|
|
|
|
|
|
|
||
Me |
|
|
|
Me |
|
|
|
|
|
Pt |
|
||||
|
|
|
|
|
|
|
|||||||||
|
|
|
|
|
|
|
|
H |
|
|
|
|
PPh3 |
|
|
|
|
|
|
|
|
|
|
|
|
|
|
PPh3 |
|
|
Scheme 5.3-3: Formation of carbene complexes by oxidative addition to Pt(0).
approach, however, the ligand/rhodium ratio, which influences the selectivity of the reaction, is difficult to control.
As well as phosphorus ligands, heterocyclic carbenes ligands 10 have proven to be interesting donor ligands for stabilization of transition metal complexes (especially palladium) in ionic liquids. The imidazolium cation is usually presumed to be a simple inert component of the solvent system. However, the proton on the carbon atom at position 2 in the imidazolium is acidic and this carbon atom can be deprotonated by, for example, basic ligands of the metal complex, to form carbenes (Scheme 5.3-2).
The ease of formation of the carbene depends on the nucleophilicity of the anion associated with the imidazolium. For example, when Pd(OAc)2 is heated in the presence of [BMIM][Br], the formation of a mixture of Pd imidazolylidene complexes occurs. Palladium complexes have been shown to be active and stable catalysts for Heck and other C–C coupling reactions [34]. The highest activity and stability of palladium is observed in the ionic liquid [BMIM][Br]. Carbene complexes can be formed not only by deprotonation of the imidazolium cation but also by direct oxidative addition to metal(0) (Scheme 5.3-3). These heterocyclic carbene ligands can be functionalized with polar groups in order to increase their affinity for ionic liquids. While their donor properties can be compared to those of donor phosphines, they have the advantage over phosphines of being stable toward oxidation.

270Hélène Olivier-Bourbigou, Alain Forestière
5.3.6
Scaling up Ionic Liquid Technology from Laboratory to Continuous Pilot Plant Operation
The increasing number of applications that make use of ionic liquids as solvents or catalysts for organic and catalytic reactions emphasizes their key advantages over organic solvents and their complementarity with respect to water or other “green” solvents. For scaling up to large-scale production, however, kinetic models are very often required and have to be developed for an optimum reactor design. In this type of multiphasic (biphasic) catalysis, one important parameter is the location of the reaction: does the reaction take place in the bulk of the liquid, at the interface, or simultaneously at both sites? For a reaction in the bulk of the liquid (e.g., in the ionic liquid), the liquid (and/or gaseous) reactants would first have to dissolve in the catalyst solution phase before the start of the chemical reaction. The reaction rate would therefore be determined by the concentration of the reactants in the catalyst phase. It is important to be able to identify mass transfer limitations that occur when the reaction rate is higher than the mass transfer velocity. In some cases the existence of mass transfer limitations can be used advantageously to control the exothermicity of reactions. For example, a reduction in stirring can be a means to decrease the reaction rate without having to destroy the catalyst. In single-phase
homogeneous reactions, catalyst poisons (such as CO or CO2) are sometimes deliberately injected into the reactor to stop the reaction.
In the aqueous biphasic hydroformylation reaction, the site of the reaction has been much discussed (and contested) and is dependent on reaction conditions (temperature, partial pressure of gas, stirring, use of additives) and reaction partners (type of alkene) [35, 36]. It has been suggested that the positive effects of cosolvents indicate that the bulk of the aqueous liquid phase is the reaction site. By contrast, the addition of surfactants or other surfaceor micelle-active compounds accelerates the reaction, which apparently indicates that the reaction occurs at the interfacial layer.
Therefore, important parameters such as phase transfer phenomena (i.e., the solubility of the reactants in the ionic liquid phase), volume ratio of the different phases, and efficiency of mixing so as to provide maximum liquid–liquid interfacial area are key factors in determining and controlling reaction rates and kinetics. Kinetic models have been developed for aqueous biphasic systems and are continuously refined to improve agreements with experimental results. These models might be transferable to biphasic catalysis with ionic liquids, but data concerning the solubilities of liquids (and gases) in these new solvents and the existence of phase equilibria in the presence of organic upper phases have still to be accumulated (see Section 3.4). Very few publications on these topics with respect to ionic liquids are available.
The influence of the concentration of hydrogen in [BMIM][PF6] and [BMIM][BF4] on the asymmetric hydrogenation of α-acetamidocinnamic acid catalyzed by rhodi-
um complexes bearing a chiral ligand has been investigated. Hydrogen was found to be four times more soluble in the [BF4]–-based salt than in the [PF6]–-based one,

5.3 Ionic Liquids in Multiphasic Reactions |
271 |
|
|
Turnover frequency [(mol of aldehydes produced)(mole Rh) -1 (min)-1]
70 |
|
|
|
|
|
|
|
|
|
|
|
|
|
|
|
|
|
|
|
|
|
|
|
|
|
|
|
|
|
|
|
|
|
|
|
|
|
|
|
|
|
|
|
|
|
|
|
|
|
|
|
|
HMI-CF |
CO |
] |
|
|
|
|
|
|||
|
|
|
|
|
|
|
|
|
|
|
|
|
|
|
|
|
|
|
|
|
|
|
|
|
|
|
|||||
|
|
|
|
|
|
|
|
|
|
|
|
|
|
|
|
|
|
|
|
|
|
|
3 |
2 |
|
|
|
|
|
||
60 |
|
|
|
|
|
|
|
|
|
|
|
|
|
|
|
|
|
|
|
|
|
[HMIM][CF3CO2 |
|
♦ |
|
|
|||||
|
|
|
|
|
|
|
|
|
|
|
|
|
|
|
|
|
|
|
|
|
|
|
|
|
|
|
|
|
|||
50 |
|
|
|
|
|
|
|
|
|
|
|
|
|
|
|
|
|
|
|
|
|
|
|
|
|
|
|
|
|
|
|
|
|
|
|
|
|
|
|
|
|
|
|
|
|
|
|
|
|
|
|
|
|
|
|
|
|
|
|
|
|
|
|
40 |
|
|
|
|
|
|
|
|
|
|
-CF |
O |
CO ] |
|
|
|
|
|
|
|
|
|
|
|
|
|
|
|
|
||
|
|
|
|
|
|
|
|
[BMIM][CF3 2 |
|
|
|
|
|
|
|
|
|
|
|
|
|
|
|
|
|||||||
|
|
|
|
|
|
|
|
|
|
|
|
|
|
3 |
2 |
|
|
|
|
|
|
|
|
|
|
|
|
|
|
|
|
|
|
|
|
|
|
|
- |
SO |
|
|
|
|
|
♦ |
|
|
|
|
|
|
|
|
|
|
|
|
|||||
30 |
|
|
|
|
|
[BMP][CF3 3 |
] |
|
|
|
|
|
|
|
|
|
|
|
|
|
|
|
|
||||||||
|
|
|
|
|
|
|
3SO3 |
♦ |
|
|
|
|
|
|
|
|
|
|
|
|
|
||||||||||
|
|
|
|
|
|
|
|
|
|
|
|
|
|
|
|
|
|
|
|
|
|
|
|
|
|
|
|
|
|||
|
|
|
|
-PF |
|
|
|
|
|
|
|
|
|
|
|
|
-N(CF |
SO ) |
SO |
|
) N] |
|
|
|
|||||||
|
|
|
|
|
|
|
|
|
|
|
|
|
|
|
|
|
|
|
|
|
|
|
|||||||||
20 |
|
|
|
[BMIM][PF ] |
|
|
|
|
|
|
|
|
|
|
|
|
|
|
[BMIM][(CF |
|
|
|
|
||||||||
|
- |
|
|
6 |
6 |
|
|
|
|
|
|
|
|
|
|
|
|
|
3 |
23 |
2 |
|
2 |
2 |
|
|
|
||||
|
|
|
|
|
|
|
|
|
|
|
|
|
|
|
|
|
|
|
|
|
|
|
|
|
|
|
|
|
|
|
|
|
|
|
|
|
|
|
|
|
|
|
|
|
|
|
|
|
|
|
|
|
|
|
|
|
|
|
|
|
|
|
|
|
|
[BMIM][BF ] |
|
♦ |
|
|
|
|
|
|
|
|
|
|
|
|
[BMP][(CF3SO2)2N] |
|
|
|
|
|
|
|
|||||||
10 |
|
4 |
4 |
|
|
|
|
|
|
|
|
|
|
|
|
|
|
|
|
|
|
|
|
|
|||||||
|
|
|
♦ |
|
|
|
|
|
|
|
|
|
|
|
|
|
|
|
|
|
|
|
|||||||||
|
|
|
|
|
|
|
|
|
|
|
|
|
|
|
|
|
|
|
|
|
|
|
|
|
|
|
|||||
0 |
|
|
|
|
|
|
|
|
|
|
|
|
[BMMIM][(CF3SO2)2N] |
|
|
|
|
|
|
|
|||||||||||
|
|
|
|
|
|
|
|
|
|
|
|
|
|
|
|
|
|
|
|
|
|
||||||||||
|
|
|
|
|
|
|
|
|
|
|
|
|
|
|
|
|
|
|
|
|
|
||||||||||
|
|
|
|
|
|
|
|
|
|
|
|
|
|
|
|
|
|
|
|
|
|
|
|
|
|
|
|
|
|
|
|
|
|
|
|
|
|
|
|
|
|
|
|
|
|
|
|
|
|
|
|
|
|
|
|
|
|
|
|
|
|
|
|
|
|
|
|
|
|
|
|
|
|
|
|
|
|
|
|
|
|
|
|
|
|
|
|
|
|
|
|
|
|
|
|
|
0 |
|
1 |
|
|
|
2 |
|
|
|
|
|
3 |
4 |
5 |
|
|
|
|
6 |
7 |
||||||||||
|
|
|
|
|
|
|
|
|
1-hexene solubility (10-2g of 1-hexene/g of ionic liquid) |
|
|
Figure 5.3-4: Turnover frequency of Rh-catalyzed hydroformylation as a function of 1-hexene solubility in ionic liquids. Reactions conditions: Rh(CO)2(acac) 0.075 mmol, 1-hexene/Rh = 800, TPPTS/Rh = 4, heptane as internal standard, CO/H2 = 1 (molar ratio), P = 2 MPa, T = 80 °C, TOF determined at 25 % conversion of 1-hexene ([BMP]= N,N-butylmethylpyrolidinium; [BMMIM] = 1-butyl-2,3-dimethylimidazolium)
at the same pressure. This difference in molecular hydrogen concentration in the ionic phase (rather than pressure in the gas phase) has been correlated with the remarkable effect on the conversion and enantioselectivity of the reaction [37].
In the rhodium-catalyzed hydroformylation of 1-hexene, it has been demonstrated that there is a correlation between the solubility of 1-hexene in ionic liquids and reaction rates (Figure 5.3-4) [28].
However, information concerning the characteristics of these systems under the conditions of a continuous process is still very limited. From a practical point of view, the concept of ionic liquid multiphasic catalysis can be applicable only if the resultant catalytic lifetimes and the elution losses of catalytic components into the organic or extractant layer containing products are within commercially acceptable ranges. To illustrate these points, two examples of applications run on continuous pilot operation are described: (i) biphasic dimerization of olefins catalyzed by nickel complexes in chloroaluminates, and (ii) biphasic alkylation of aromatic hydrocarbons with olefins and light olefin alkylation with isobutane, catalyzed by acidic chloroaluminates.
5.3.6.1Dimerization of alkenes catalyzed by Ni complexes
The Institut Français du Pétrole has developed and commercialized a process, named Dimersol X, based on a homogeneous catalyst, which selectively produces dimers from butenes. The low-branching octenes produced are good starting materials for isononanol production. This process is catalyzed by a system based on a nickel(II) salt, soluble in a paraffinic hydrocarbon, activated with an alkylaluminium chloride derivative directly inside the dimerization reactor. The reaction is sec-

272 Hélène Olivier-Bourbigou, Alain Forestière
Figure 5.3-5: Dimersol process.
ond order in monomer concentration and first order in catalyst concentration. The butene conversion level is highly dependent on its initial concentration. In its present commercial form, Dimersol X can achieve 80 % conversion of butenes (for 70–75 % butene concentration in the feed) with 85 % octene selectivity. A process flow diagram is shown in Figure 5.3-5.
The reaction takes place at low temperature (40–60 °C), without any solvent, in two (or more, up to four) well-mixed reactors in series. The pressure is sufficient to maintain the reactants in the liquid phase (no gas phase). Mixing and heat removal are ensured by an external circulation loop. The two components of the catalytic system are injected separately into this reaction loop with precise flow control. The residence time could be between 5 and 10 hours. At the output of the reaction section, the effluent containing the catalyst is chemically neutralized and the catalyst residue is separated from the products by aqueous washing. The catalyst components are not recycled. Unconverted olefin and inert hydrocarbons are separated from the octenes by distillation columns. The catalytic system is sensitive to impurities that can coordinate strongly to the nickel metal center or can react with the alkylaluminium derivative (polyunsaturated hydrocarbons and polar compounds such as water).
Despite all the advantages of this process, one main limitation is the continuous catalyst carry-over by the products, with the need to deactivate it and to dispose of wastes. One way to optimize catalyst consumption and waste disposal was to operate the reaction in a biphasic system. The first difficulty was to choose a “good” solvent. N,N’-Dialkylimidazolium chloroaluminate ionic liquids proved to be the best candidates. These can easily be prepared on an industrial scale, are liquid at the reaction temperature, and are very poorly miscible with the products. They play the roles both of the catalyst solvent and of the co-catalyst, and their Lewis acidities can be adjusted to obtain the best performances. The solubility of butene in these solvents is high enough to stabilize the active nickel species (Table 5.3-3), the nickel

