
- •Рис. 9.2. К расчету теплообмена в реакторе вытеснения
- •Рис. 7.2. К примеру 10.1
- •Рис. 11.4. К примеру 11.1
- •Рис. 11.9. К расчету шпилек
- •Рис. 11.10. К примеру 11.3
- •Рис. 11.11. К примеру 11.5
- •Рис. 13.10. Рамные мешалки
- •Рис. 13.11. Якорные мешалки
- •Предисловие
- •Экологическое и технико-экономическое обоснование проектов химических производств.
- •Этапы проведения экологической экспертизы
- •Принципы экологической экспертизы
- •Рис. 1.1. Общая система организации проектирования
- •Рис. 1.2. Основные этапы и стадии разработки проектов для промышленного строительства
- •1.2. Задание на проектирование
- •Рис. 1.3. Пример построения розы повторяемости и силы ветров
- •Рис.1.4. Схема выпадения дымовых частиц при наличии зеленых защитных насаждений между застройкой и источником задымления и при отсутствии их:
- •Рис. 1.5. Совмещенная схема движения загрязненных нижнего и верхнего потоков
- •1.5. Разработка проектной документации по охране окружающей среды
- •1.5.2. Разработка прогноза загрязнения воздуха
- •1.5.4. Прогноз воздействия объекта при возможных авариях
- •1.6. Технологический процесс как основа промышленного проектирования
- •Рис. 1.6. Схема производства серной кислоты контактным способом:
- •Рис. 1.8. Процессы и аппараты химической технологии
- •Рис. 1.9. Виды оборудования химической технологии
- •Рис. 1.11. Уровни организации химического предприятия
- •1.7. Генеральный план химических предприятий
- •Рис. 1.12. Генеральный план предприятий химической промышленности
- •1.8. Типы промышленных зданий
- •1.8.1. Одноэтажные промышленные здания
- •Рис. 1.13. Одноэтажное здание павильонного типа:
- •Рис. 1.14. Многоэтажное производственное здание:
- •1.8.2. Многоэтажные здания
- •Рис. 1.15. Многоэтажное производственное здание:
- •Рис. 1.16. Поперечные разрезы зданий I и II очередей сернокислотного производства:
- •1.8.3. Вспомогательные здания и помещения химических предприятий
- •1.8.4. Склады промышленных предприятий
- •1.9. Инженерные сооружения
- •инженерных сооружений
- •1.10. Специальные вопросы проектирования химических предприятий
- •2.1. Основные стадии проектирования химических производств и оборудования
- •Рис. 2.1. Основные стадии проектирования
- •2.2. Виды конструкторских документов
- •2.4.1. Курсовое проектирование
- •2.4.2. Дипломное проектирование
- •2.4.3. Пример использования АвтоЛиспа
- •Рис. 2.2. Схема установки для ректификации трехкомпонентной смеси:
- •СИСТЕМЫ АВТОМАТИЗИРОВАННОГО ПРОЕКТИРОВАНИЯ
- •3.1. История развития САПР
- •3.2. Основные принципы создания САПР
- •Рис. 3.1. Модульная структура программного обеспечения
- •Рис. 3.2. Области использования ЭВМ в процессе проектирования
- •3.4. Автоматическое изготовление чертежей
- •3.5. Основные преимущества автоматизации проектирования
- •3.6. Основные требования к САПР
- •Рис. 3.3. Схема взаимодействия пользователя со средствами САПР:
- •3.7. Связь САПР с производством, расширение области применения
- •3.8. Система автоматизированного проектирования цементных заводов
- •3.8.1. Функционирование САПР
- •ВВЕДЕНИЕ В ПРОЕКТИРОВАНИЕ
- •4.1. Проектно-сметная документация
- •4.2.1. Исходные положения
- •4.2.2. Обоснование способа производства химической продукции
- •ВЫБОР И РАЗРАБОТКА ТЕХНОЛОГИЧЕСКОЙ СХЕМЫ ПРОИЗВОДСТВА
- •5.1. Общие положения
- •5.2. Последовательность разработки технологической схемы
- •Рис. 5.1. Примерная схема стадий технологического процесса:
- •Рис. 5.2. Блок-схема физико-химических процессов, протекающих в гетерофазном реакторе с мешалкой
- •5.3. Принципиальная технологическая схема
- •5.4. Размещение технологического оборудования
- •Выбор технологического оборудования химических производств
- •6.1. Основные типы химических реакторов
- •Рис. 6.1. Установка для непрерывного процесса:
- •Рис. 6.5. Изменение концентрации веществ в реакторах:
- •Рис. 6.6. Реакторы смешения:
- •6.2. Химические факторы, влияющие на выбор реактора
- •6.2.1. Реакции расщепления
- •Рис. 6.7. Относительный выход реакции расщепления:
- •Реактор
- •6.2.2. Реакции полимеризации
- •6.2.3. Параллельные реакции
- •Объем реактора
- •РВНД
- •6.3. Эскизная конструктивная разработка основной химической аппаратуры
- •6.3.1. Общие положения
- •6.3.2. Реакторы
- •6.4. Оптимизация процессов химической технологии
- •УРАВНЕНИЯ МАТЕРИАЛЬНОГО БАЛАНСА ТЕХНОЛОГИЧЕСКОГО ПРОЦЕССА
- •7.1. Стехиометрические расчеты
- •7.2. Термодинамический анализ процессов
- •7.2.1. Равновесие химической реакции
- •Рис. 1.1. Зависимость коэффициента активности газв от приведенных давления и температуры
- •7.2.2. Расчет состава равновесной смеси
- •7.3. Общее уравнение баланса массы
- •7.4. Практический материальный баланс
- •7.5. Физико-химические основы технологического процесса
- •8.1. Общие положения
- •8.2. Расчет объемов реакторов
- •8.2.1. Основные положения химической кинетики
- •8.2.2. Расчет идеальных реакторов
- •8.3. Определение объемов аппарата
- •Тепловой расчет основного оборудования
- •9.1. Общее уравнение баланса энергии
- •Рис. 9.1. К примеру 9.1
- •9.2. Практический тепловой баланс
- •9.3. Теплообмен в реакторах
- •9.4. Расчет энтальпий и теплоемкостей
- •9.6. Расчет реактора периодического действия
- •Рис. 9.3. К тепловому расчету реактора периодического действия
- •9.7. Степень термодинамического совершенства технологических процессов
- •Рис. 9.6. Технологическая схема 1:
- •Рис. 9.7. Технологическая схема 2
- •Рис. 9.8. Схемы использования тепла реакций:
- •Гидравлические расчеты
- •10.1. Расчет диаметра трубопровода
- •Пары, насыщенные при абсолютном давлении (МПа)
- •Рис. 10.1. Зависимость коэффициента трения от критерия Рейнольдса и степени шероховатости трубы
- •10.3. Гидравлическое сопротивление кожухотрубчатых теплообменников
- •10.4. Подбор насосов
- •МЕХАНИЧЕСКИЙ РАСЧЕТ
- •11.1. Расчет сварных химических аппаратов
- •11.1.1. Основные расчетные параметры
- •11.1.2. Расчет на механическую прочность
- •11.1.3. Требования к конструированию
- •11.1.4. Расчет цилиндрических обечаек
- •Рис. 11.1. Номограмма для определения толщины цилиндрических обечаек, работающих под наружным давлением
- •Рис.11.2. Схема пользования номограммой на рис. 11.1:
- •11.1.5. Расчет крышек и днищ
- •Рис. 11.3. Основные конструкции днищ сварных аппаратов:
- •11.1.6. Подбор стандартных элементов
- •11.2. Расчет толстостенных аппаратов
- •Рис. 11.7. Основные конструкции уплотнений затворов высокого давления:
- •Рис. 11.8. К расчету усилий, действующих на затворы высокого давления
- •КОНСТРУКционНЫЕ МАТЕРИАЛЫ В ХИМИЧЕСКОМ МАШИНОСТРОЕНИИ
- •12.1. Виды конструкционных материалов
- •12.2. Коррозия металлов и сплавов
- •12.2.1. Виды коррозии
- •12.2.2. Виды коррозионных разрушений
- •12.2.3. Способы борьбы с коррозией
- •12.3. Влияние материала на конструкцию аппарата и способ его изготовления
- •12.3.1. Конструкционные особенности аппаратов из высоколегированных сталей
- •Рис. 12.1. Сварка встык:
- •Рис. 12.2. Способы подготовки кромок под сварку
- •Рис. 12.4. Способы сварки легированной и углеродистой стали
- •12.3.2. Конструктивные особенности эмалированных аппаратов
- •Рис. 12.5. Элементы конструкции эмалированных аппаратов
- •Рис 12.6. Пайка элементов медных аппаратов
- •12.3.3. Конструктивные особенности аппаратов из цветных металлов
- •Рис. 12.7. Основные типы паяных соединений
- •12.3.4. Конструктивные особенности аппаратов из пластмасс
- •ОФОРМЛЕНИЕ ОТДЕЛЬНЫХ ЭЛЕМЕНТОВ ХИМИЧЕСКОЙ АППАРАТУРЫ
- •13.1. Оформление поверхности теплообмена
- •Рис. 13.5. Реактор со змеевиковой рубашкой
- •Рис. 13.6. Рубашка с вмятинами
- •Рис. 13.8. Вывод змеевика через крышку аппарата:
- •13.2. Перемешивающие устройства
- •Рис. 13.12. Листовая мешалка
- •Рис. 13.13. Пропеллерные мешалки
- •Рис. 13.14. Турбинные мешалки открытого (а) и (б) закрытого типа
- •Рис. 13.15. Крепление мешалок к ступице:
- •13.3. Уплотнения вращающихся деталей
- •Рис. 13.18. Одинарное торцовое уплотнение:
- •ТРУБОПРОВОДЫ И ТРУБОПРОВОДНАЯ АРМАТУРА
- •Рис 14.5. Фасонные части трубопроводов
- •Рис. 14.7. Крепление горизонтальных и вертикальных трубопроводов на подвесках
- •Рис. 14.8. Компенсаторы:
- •ВСПОМОГАТЕЛЬНОЕ ОБОРУДОВАНИЕ ХИМИЧЕСКИХ ЗАВОДОВ
- •15.1. Виды вспомогательного оборудования
- •Рис. 15.1. Схема многостадийного диспергирования твердой фазы с контрольной классификацией продукта
- •15.2. Транспортные средства
- •15.2.1. Классификация транспортных средств для твердых материалов
- •15.2.2. Машины для транспортировки жидкостей и газов
- •ТЕХНОЛОГИЧЕСКИЕ СХЕМЫ И ОБОРУДОВАНИЕ ДЛЯ ГРАНУЛИРОВАНИЯ ДИСПЕРСНЫХ МАТЕРИАЛОВ
- •16.1. Классификация методов гранулирования и особенности уплотнения гранул
- •Рис. 16.1. Тарельчатый гранулятор:
- •Рис. 16.2. Гранулятор барабанного типа конструкции НИИХиммаша
- •16.3. Основные закономерности и аппаратурное оформление метода экструзии
- •16.5. Гранулирование в псевдоожиженном слое
- •16.6. Технологические схемы процессов гранулирования дисперсных материалов
- •Рис. 16.11. Технологическая схема гранулирования шихты методом окатывания
- •Рис. 16.13. Схема уплотнения шихты в роторном грануляторе
- •Рис. 16.14. Схема гранулирования шихты методом экструзии
- •Рис. 16.15. Схема установки для компактирования шихты
- •ЛИТЕРАТУРА

−соединение должно обеспечить свободную усадку материала шва, для этого необходимо предусмотреть зазор между свариваемыми деталями;
−необходимо стремиться использовать соединение деталей встык, как наиболее надежное;
−продольные швы не должны прерываться отверстиями и штуцерами.
Рис. 12.4. Способы сварки легированной и углеродистой стали
Легированные стали являются весьма дорогостоящими конструкционными материалами и их следует использовать для изготовления деталей, поверхность которых контактирует с агрессивной средой. Все детали, вынесенные за пределы рабочего пространства, как, например, фланцы и лапы, необходимо изготавливать из обычной углеродистой стали.
Сварка легированной стали с углеродистой в принципе возможна, так как температуры плавления тех и других сталей отличаются незначительно. Однако различия в химическом составе и физических свойствах свариваемых сталей вызывают изменения в структуре и составе металла сварного шва. Сварной шов имеет достаточно высокую механическую прочность, но теряет коррозионную стойкость вследствие уменьшения в нем концентрации легирующих элементов.
Существуют специальные приемы, позволяющие вынести сварные швы за пределы поверхности, омываемой агрессивной средой, сохранив при этом коррозионную стойкость основного материала аппарата (рис. 12.4).
288
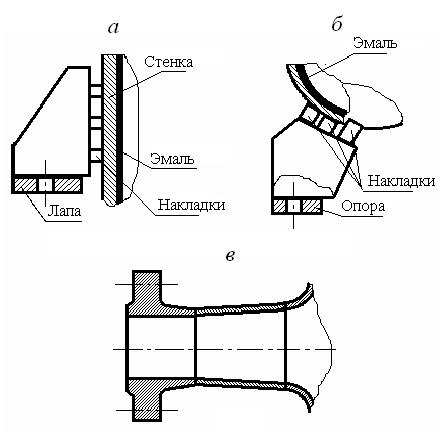
Как видно из рисунков, с целью сохранения коррозионной стойкости основных элементов аппарата из легированных сталей их сварку с деталями из углеродистых сталей следует осуществлять через дополнительную деталь (кольцо, прокладка из легированной стали).
После сварки изделий из легированных сталей швы тщательно зачищаются и протравливаются, что значительно повышает коррозионную стойкость сварной аппаратуры.
В процессе эксплуатации сварной аппаратуры необходимо регулярно осуществлять контроль за состоянием сварных соединений.
12.3.2. Конструктивные особенности эмалированных аппаратов
Эмалевые покрытия наносят на поверхность аппаратов, изготовленных из низкоуглеродистых сталей или чугуна.
Рис. 12.5. Элементы конструкции эмалированных аппаратов
Эмалевое покрытие, представляющее собой смесь песка, соды, поташа, пигментов и других элементов, равномерно наносится на предварительно обработанную поверхность аппарата и затем обжигается при температуре 700−900 °С.
Для получения качественного эмалевого покрытия необходимо соблюдать следующие условия:
289

−формы аппаратов должны иметь плавные очертания; должны отсутствовать острые углы, края и впадины;
−все части аппаратов перед эмалированием тщательно подготавливаются: швы зашлифовываются, острые углы и выступы закругляются;
−необходимо строго соблюдать температурный режим для равномерного прогрева, обжига и охлаждения эмалевого покрытия;
−узлы аппаратов должны быть равностенными, поэтому приварку лап и стоек следует проводить после эмалирования к специальным накладкам, которые привариваются к корпусу или днищу до эмалирования (рис. 12.5,а и 12.5,б).
Рис 12.6. Пайка элементов медных аппаратов
Штуцера выполняются с коническими патрубками, приваренными встык к краю отбортованного отверстия (рис. 12.5,в).
Эмалевое покрытие должно обладать хорошей адгезией (сцеплением) с поверхностью материала, из которого изготовлен аппарат.
12.3.3. Конструктивные особенности аппаратов из цветных металлов
В аппаратах, выполненных из цветных металлов и их сплавов, соединения отдельных деталей осуществляются сваркой и пайкой.
290

Медные аппараты часто используются в установках глубокого холода, их изготавливают из медного проката. Для увеличения жесткости медных тонкостенных аппаратов их изготавливают с гофрами (рис. 12.6,а).
Неразъемные соединения частей медных аппаратов получают пайкой, сваркой и реже клейкой. Медь и ее сплавы обладают хорошей паяемостью. Пайку мягкими припоями (ПОС−30, ПОС−40) выполняют внахлест (рис. 12.6,б), для увеличения прочности паяных соединений применяют замки (рис. 12.6,в).
Медные трубки к медным или латунным трубным решеткам крепятся заливкой припоем (рис. 12.6,г), бобышки огибают медью и припаивают (рис. 12.6,д).
Из паяных соединений более надежным считается соединение внахлест. Для стыковых соединений необходимо обрабатывать кромки спаиваемых деталей (рис. 12.6,е).
Рис. 12.7. Основные типы паяных соединений
Соединения встык применяются редко, так как они весьма чувствительны к вибрационным и ударным нагрузкам, плохо воспринимают крутящие и изгибающие моменты, несколько прочнее соединение вскос (рис. 12.7).
В аппаратах, выполненных из алюминия и его сплавов, соединение деталей осуществляется в основном сваркой встык. Сварное соединение может быть выполнено и внахлест, особенно в случае точечной сварки. Однако необходимо помнить, что при этом для достижения достаточной прочности соединения в 2 раза увеличивается число сварных швов и в целом трудоемкость изделия.
Пайка изделий из алюминия осложнена образованием на поверхности алюминия оксидной пленки, температура плавления которой – 2050 °С. Поэтому для пайки алюминия необходимо использовать специальные активные флюсы, содержащие хлориды, фториды или проводить пайку в парах магния, в вакууме.
291