
ЛАБОРАТОРНЫЙ ПРАКТИКУМ
.pdfВміст пиловидних, глинистих та мулистих частинок, що визначають відмучуванням, не повинен перевищувати значень, наведених у табл. 2.13.
Вміст органічних домішок у піску визначають, якщо пісок призначено для виготовлення цементних бетонів та будівельних розчинів. Метод визначення має назву «колориметрична проба» або «метод фарбування».
Випробування полягає в тому, що мірний циліндр ємністю 250 мл заповнюють піском з природною вологістю до рівня 130 мл і заливають 3 %-ним розчином їдкого натру до відмітки 200. Вміст циліндра перемішують і залишають на 24 години. Перемішування повторюють через кожні 4 години після початку випробування. Через 24 години офарблення розчину над піском (від світложовтого до темно-коричневого) порівнюють з еталоном. Якщо рідина, що відстоялась над піском, більш світла, ніж еталон, пісок вважають придатним для застосування у складі бетонних та розчинних сумішей. Якщо офарблення таке саме або темніше еталону, пісок без спеціальних досліджень використовувати для приготування бетонних та розчинних сумішей не допускається. Якщо офарблення рідини тільки незначно світліше еталону, вміст посудини підігрівають на водяній бані протягом 2–3 годин при температурі 60–70 °С і знов порівнюють з еталоном. Еталон готують з 2 %-ного розчину таніну у 1 %-ному розчині етилового спирту. Суміш з 5 мл одержаного розчину та 195 мл 3 %-ного гідрату оксиду натрію збовтують і залишають у спокої на 24 години. Еталон придатний до використання тільки у свіжоприготовленому стані.
Вологість піску визначають так само, як наведено раніш для визначення вологості гірських порід. Наважка для визначення вологості піску – 1000 г. Вологість піску значно впливає на його об’єм. При вологості піску 5–7 % його об’єм збільшується порівняно з сухим на 32–38 %. Зі збільшенням або зменшенням вологості відносно зазначених меж об’єм піску знижується. Це необхідно ураховувати при транспортуванні, зберіганні та об’ємному дозуванні піску.
Істинну густину піску визначають пікнометричним або прискореним методом з допомогою приладу Ле-Шательє-Кандло за методикою, що описана для визначення істинної щільності гірських порід, з використанням формул (2.1) та (2.2).
61
Для випробування готують наважку 200 г піску з середньої проби, висушеної та просіяної крізь сито № 5. Зерна піску не розмелюють до стану порошку, а обирають у початковому вигляді.
Насипну густину піску визначають у сухому неущільненому стані з допомогою мірного циліндра ємністю 1 л, як описано для визначення насипної густини сипких матеріалів, за формулою (2.6).
Питома площа поверхні піску – це сумарна площа поверхні зерен піску у одиниці його маси або об’єму. Розмірність питомої площі поверхні сипкого тіла – м2/кг або см2/г у одиниці маси або м2/м3 чи см2/см3 – у одиниці об’єму. Величина питомої площі поверхні сипкого матеріалу залежить від розміру його частинок, характеру поверхні зерен, зернового (гранулометричного складу): вона збільшується при зменшенні розмірів зерен, розвиненні їх поверхні, зростанні вмісту дрібних частинок у складі матеріалу.
62
РОЗДІЛ 3
ВИЗНАЧЕННЯ ЯКОСТІ ШТУЧНИХ КАМ’ЯНИХ МАТЕРІАЛІВ
3.1. Металургійні шлаки
Металургійні шлаки – це продукт остигання відносно легкоплавких мас, які утворюються як побічний продукт при виплавці чорних (шлаки чорної металургії) та кольорових (шлаки кольорової металургії) металів. Шлаки чорної металургії поділяють на доменні, що одержують під час виплавлення чавуну, та сталеплавильні (мартенівські, конвертерні, електроплавильні – залежно від технологічного процесу виплавлення сталі), шлаки кольорової металургії за видом металу, що виплавляється, – мідні, титанові, свинцеві та ін. Найбільш поширено використання доменних шлаків чорної металургії.
З доменних шлакових розплавів одержують литий шлаковий щебінь, литі вироби, шлакову пемзу, шлакоситал, гранульований шлак. При зливанні розплаву до відвалу утворюється відвальний шлак, неоднорідний за структурою та текстурою, а тому – за фізикомеханічними властивостями. Щебінь для дорожнього будівництва, як правило, одержують подрібненням та, при необхідності, розсіюванням відвальних доменних та сталеплавильних шлаків, шлаків поточного виробництва та ковшових залишків.
Вибір щебеню для улаштування різних видів покриттів, основ та підстеляючих шарів дорожніх одягів здійснюють залежно від його фізико-механічних властивостей за ДСТУ БВ.2.7-35 та ГОСТ 3344. Якість щебеню характеризують: крупністю та зерновим (гранулометричним) складом, формою та характером поверхні зерен, наявністю удруге зцементованих зерен, структурою та текстурою, стійкістю структури, активністю, показниками фізикомеханічних властивостей.
Шлаковий щебінь одержують партіями. Партія – це кількість шлакового щебеню, яку одночасно відвантажують споживачу у одному залізничному потязі, одній баржі або постачають автомобільним транспортом протягом однієї доби.
Підприємство-виготовлювач супроводжує кожну партію шлаку, що відвантажують споживачу, документом про якість, в якому
63
зазначені найменування та адреса підприємства-виготовлювача; найменування та адреса підприємства-споживача; номер документу про якість та дата його видавання; номер партії, найменування та кількість матеріалів в партії; активність та стійкість структури шлаку; зерновий склад шлакового щебеню; вміст пилуватих та глинистих частинок у щебені; марку щебеню за міцністю та здатністю до стирання; вміст слабких зерен; зерновий склад піску; вміст глини в піску; зерновий склад щебенево-піщаної суміші; результати радіаційного контролю; позначення діючого стандарту.
Для контрольної перевірки відбирають пробу з будь-якого вагону залізничного потягу (за вказівкою споживача) – не менш, ніж з п’яти місць вагону, з верхнього, середнього та нижнього шарів щебеню – у чотирьох кутах та у центрі, під час навантаження або розвантаження; під час навантаження та розвантаження судна або автомобілів також відбирають одну пробу від кожних 300 м3 щебеню.
Розмір проби шлакового щебеню для повного комплексу його випробувань – 400 кг. Розмір проби для окремих випробувань призначають у кожному конкретному випадку.
Гранулометричний (зерновий) склад шлакового щебеню, вміст у ньому зерен лещадної форми, мулистих, глинистих та інших сторонніх домішок, середню та насипну густину, стираність у поличному барабані, вологість, водовбирання та морозостійкість визначають згідно з ГОСТ 8269 з використанням тих же методів, що й при визначенні властивостей щебеню зі скельних гірських порід (див.гл.2). Вимоги до зернового складу кожної фракції шлакового щебеню або суміші фракцій щебеню наведено у табл. 3.1.
Границі зернового складу шлакового щебеню |
Таблиця 3.1 |
|||||
|
|
|||||
|
|
|
|
|
|
|
|
|
0,5 (d + D) |
|
|
|
|
|
|
|
|
|
|
|
Діаметр отворів |
D |
для кожної |
для |
|
D |
1,25 D |
контрольних сит, мм |
фракції |
суміші |
|
|||
|
|
|
|
|||
|
|
|
фракцій |
|
|
|
|
|
|
|
|
|
|
Повний залишок на |
|
|
|
|
|
|
контрольному ситі, |
|
|
|
|
|
|
% за масою |
0 – 10 |
20 – 70 |
30 – 60 |
90 – 100 |
95 – 100 |
64
За узгодженістю між споживачем та виготовлювачем допускається випускати щебінь у вигляді суміші двох або трьох суміжних фракцій, а також щебеню фракцій 5–15, 10–15 або 15–20 мм.Насипна густина щебеню має бути у таких межах: щебеню з доменних шлаків від 900 до 1300 кг/м3; щебеню з сталеплавильних шлаків – від 1100 до 1500 кг/м3. Вміст домішок пилуватих та глинистих частинок у щебені з неактивних шлаків не повинен перевищувати 3 % за масою, у щебені з активних шлаків – не нормується. Вміст глини у грудках має бути не більш 0,25 % за масою.
Щебінь за міцністю поділяють на марки. Марку щебеню визначають за результатами випробувань його стискуванням у циліндрі у водонасиченому стані. Марка щебеню за міцністю та вмістом у ньому слабких зерен повинна відповідати вимогам, наведеним у табл. 3.2. До слабких відносять зерна, що розламуються руками і руйнуються від легких ударів молотка.
Таблиця 3.2
Марки шлакового щебеню за показником дробильності
Марка щебеню |
Втрата маси при |
Вміст слабких зерен, в тому числі |
за міцністю |
випробуванні,% |
домішок,% за масою, не більш |
|
|
|
1200 |
до 15 |
5 |
100 |
15 – 25 |
5 |
800 |
25 – 35 |
10 |
600 |
35 – 45 |
20 |
300 |
45–55 |
30 |
За стираністю, що визначають у поличному барабані, щебінь поділяють на марки згідно з вимогами, що наведені у табл. 3.3.
Таблиця 3.3
Марки шлакового щебеню за зносом у поличному барабані
Марки щебеню за стираністю |
Втрати маси при випробуванні,% |
Р I |
до 25 включно |
P II |
25 – 35 |
P III |
35 – 45 |
P IV |
45 – 60 |
65
За морозостійкістю щебінь поділяють на марки Мрз15, Мрз25, Мрз50, Мрз100, Мрз150, Мрз200 та Мрз300. Втрата маси щебеню після навперемінного заморожування та відтавання проб щебеню марок Мрз15 та Мрз25 не повинна перевищувати 10 %, для інших марок – 5 %. Вимоги до морозостійкості щебеню з активних шлаків не пред’являють.
Таблиця 3.4
Класифікація шлакових пісків за крупністю
Група піску за |
Модуль |
Повний залишок |
Вміст частинок |
|
на ситі № 63 за |
менш 0,16 мм |
|||
крупністю |
крупності, Мк |
масою % |
за масою |
|
|
|
не більш % |
||
|
|
|
|
|
Підвищеної крупності |
3,0 – 3,5 включно |
65 – 75 |
включно |
10 |
Крупний |
2,5 – 3,0 |
45 |
– 65 |
10 |
Середній |
2,0 – 2,5 |
30 |
– 45 |
10 |
Дрібний |
1,5 – 2,0 |
10 |
– 30 |
15 |
Дуже дрібний |
1,0 – 1,5 |
до 10 включно |
25 |
Форму зерен щебеню характеризують вмістом зерен пластинчастої (лещадної) та голчастої форми (товщина та ширина або ширина яких менш довжини в три та більше рази). Вміст у щебеню таких зерен не повинен перевищувати 35 % за масою. Пісок з доменних та сталеплавильних шлаків поділяють на групи за крупністю (табл. 3.4).
Насипна щільність піску має бути у таких межах: пісок з доменних шлаків 950–1350 кг/м3, пісок зі сталеплавильних шлаків 1100–1600 кг/м3. Вміст глинистих частинок у піску для цементобетону, що визначають методом набрякання, має бути не більше 5 % за масою; у піску для асфальтобетону – не більше 1 % за масою.
Визначення стійкості шлакового щебеню проти розпаду
Для визначення стійкості структури шлакового щебеню проти усіх видів розпаду щебінь піддають дії насиченої водяної пари у автоклаві абокип’ятінню.
Підготовка щебеню до випробування полягає у промиванні проби випробуваної фракції від сипких частинок та пилу, сушінні до постійної маси та просіюванні крізь стандартні сита. Для випро-
66
бування беруть по дві проби щебеню об’ємом кожна не менше: для фракцій з максимальним розміром зерен до 20 мм – 1 л; до 40 мм – 2 л; більше 40 мм – 5 л. Визначають масу щебеню у кожній наважці m1 (кг). Кожну наважку щебеню випробовують окремо.
Пробу щебеню m1 (кг) поміщують до автоклава. Протягом 30 хв тиск у автоклаві поступово піднімають до 0,2 МПа. Під цим тиском щебінь витримують 6 годин, після чого тиск протягом 20 хв поступово знижують до атмосферного. Наважки щебеню витягують з автоклаву, кожну окремо промивають, висушують до постійної маси, просівають крізь сито з отворами діаметром, який відповідає діаметру випробуваної фракції щебеню. Визначають масу залишка на ситі m2 (кг). Допускається заміна випробування в автоклаві кип’ятінням у бачці протягом 10 годин згідно з ГОСТ 9758.
Втрату за масою Вм у відсотках з точністю до 0,1 % обчислюють за формулою
В = |
m1 −m2 |
100 ,% . |
(3.1) |
М m1
Втрату за масою щебеню, який складається з суміші кількох фракцій Всум, визначають за формулою
|
N |
B C |
|
||
B |
= ∑ |
i |
фi |
,%, |
(3.2) |
|
|
||||
СУМ |
100 |
|
|
||
|
N +1 |
|
|
де N – число фракцій, які входять до складу суміші; Ві – втрата даної фракції за масою, %; Сфі – вміст даної фракції за масою %.
За результат приймають середнє арифметичне значення результатів двох паралельних випробувань. Втрата маси не можна перевищувати 5 %.
Стійкість структури шлаків характеризують втратою маси при випробуванні їх в автоклаві або кіп’ятінням. Цей показник має бути не більше 5 % від маси шлаку.
Активність шлаків
Активність шлаків визначають у тонкоподрібненому стані шляхом визначення міцності стандартних зразків з суміші порошкоподібного шлаку та води після твердіння протягом 28 діб.
67
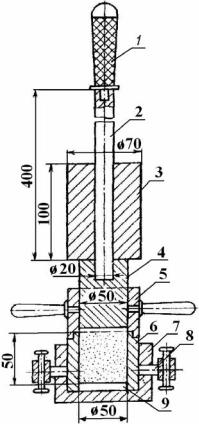
Для випробування середню пробу шлаку обсягом 5 кг висушують до постійної маси та розмелюють у кульковому млині, вібраційному млині або барабані з металічними кульками таким чином, щоб залишок на ситі з розміром отворів 0,071 мм складав 6–10 % або питома поверхня дорівню-вала (3000 ± 100) см2/г або (300 ± 10) м2/кг. Питому поверхню шлакового порошку визначають у приладі ПСХ-2 з уставленим до гільзи приладом з пустотілим вкладишем довжиною 120 мм. Розмелений шлак витримують у повітряно-сухих умовах протягом 1 доби.
Активність шлаку визначають на циліндричних зразках, виготовлених з суміші шлакового порошку та води з максимальним значенням середньої щільності скелетної частини. Максимальне значення середньої щільності скелетної частини визначають шляхом підбору оптимальної кількості води у складі суміші.
Рис. 3.1. Малий прилад СоюздорНДІ для стандартного ущільнення:
1– рукоятка; 2 – напрямний стержень; 3 – гиря; 4 – плунжер; 5 – напрямний насадний циліндр; 6 – розбірний циліндр;
7 – підстаканник; 8 – закріпні гвинти; 9 – металева пластинка
68
Для визначення оптимальної кількості води беруть наважку розмеленого шлаку масою 720–750 г, додають воду у кількості 6–8 % від маси шлаку і ретельно перемішують кельмою у сферичній чашці протягом 5 хв. Чашку попередньо протирають зволоженою тканиною. З приготованої суміші відбирають контрольну наважку і визначають її фактичну вологість, після чого з суміші формують 3 зразки діаметром та висотою 50 мм у розбірному малому приладі СоюздорНДІ для стандартного ущільнення (рис. 3.1). Суміш ущільнюють 40 ударами гирі масою 2,5 кг з висоти 300 мм. Після ущільнення ретельно зрізають надлишок суміші, зразок вивільняють з форми та зважують з точністю до 0,1 г. Підготовку шлакової суміші, виготовлення зразків та зважування повторюють кілька разів, зі збільшенням кожний раз кількості води на 2 %.
Воду припиняють додавати після одержання ряду показників середньої щільності скелету, значення яких закономірно знижуються з кожним наступним визначенням. Для визначення оптимальної вологості та максимальної середньої густини для кожної серії зразків (різної вологості) обчислюють середню щільність скелета зразка (без води) за формулою
ρСКM = |
|
ρm |
|
, г/см3, |
(3.3) |
||
|
|
|
|||||
1 |
+ |
|
W |
|
|
|
|
100 |
|
|
|
||||
|
|
|
|
|
|
де ρСКM – середня густина скелету зразка, г/см3;
ρm – середня густина матеріалу зразків, г/см3;
Середню густину матеріалу зразків визначають як для зразків гірських порід правильної геометричної форми (див.підрозділ 2.3): W-фактична вологість суміші, % від маси сухого меленого шлаку.
Середню густину зразків з суміші води та шлаку визначають за рівнянням
ρM = |
m |
, г/см3, |
(3.4) |
|
V |
||||
|
|
|
де m – маса зразка при даній вологості (середня з трьох зразків), г; V – об’єм зразка, см3.
69
За результатами визначення середньої густини скелета зразків будують графік, на осі абсцис якого відкладають вологість W, а на осі ординат – середню щільність скелетної частини ущільнених зразків. Найвища точка кривої відповідає оптимальній вологості та максимальній середній щільності зразків. Після цього 3 кг меленого шлаку перемішують з оптимальною кількістю води у лабораторній мішалці протягом 2,5 хв. При відсутності мішалки шлак з водою перемішують кельмою у сферичній металевій чашці протягом 10 хв.
3 суміші шлакового порошку та води готують зазначеним вище способом 10 зразків-циліндрів висотою та діаметром 50 мм. Допускається ущільнювати зразки із зазначеної суміші також на пресі під тиском 20 МПа, який забезпечує середню щільність зразка, що дорівнює середній щільності зразків, одержаних на приладі стандартного ущільнення, з витримкою протягом 3 хв.
При неможливості підібрати оптимальну вологість суміші за найбільшим ступенем ущільнення допускають для визначення активності шлаку готувати одним з двох наведених способів по 10 зразків з сумішей з водошлаковими відношеннями 0,12; 0,14; 0,16. Після витягання з води зразки випробовують на стиск на гідравлічному пресі, з поступовим підвищенням тиску на 0,3– 0,5 МПа у секунду до руйнування зразків.
Таблиця 3.5
Розподілення шлаків за активністю
Активність |
Міцність на стиск зразків з меленого шлаку, |
||
МПа |
|||
|
|||
|
|
|
|
Активний А |
Понад 2,5 |
до 5 |
|
Слабоактивний СА |
Понад 1,0 |
до 2,5 |
|
|
|
|
|
Неактивний НА |
Менш 1,0 |
|
|
|
|
|
Показник активності шлаку – середнє арифметичне значення границі міцності на стиск 10 зразків з суміші з оптимальним вмістом води та найбільший з середніх показників міцності на стиск 10 зразків з водошлаковим відношенням 0,12, 0,14 та 0,16. За активністю шлаки поділяють відповідно з табл. 3.5.
70