
- •Введение
- •Основные положения, понятия и определения
- •Жизненный цикл изделий машиностроения и его технологическая составляющая
- •Основные термины
- •Понятие о машине и ее служебном назначении
- •Качество и экономичность машины
- •Понятие о точности
- •Точность детали
- •Точность машины
- •Отклонения характеристик качества изделий от требуемых величин
- •Положение теории вероятностей и математической статистики, используемые в технологии машиностроения
- •Тема 3. Связи в машине и производственном процессе её изготовления
- •Связи в машине и производственном процессе её изготовления
- •Определение понятия "связь"
- •Свойства связей
- •Тема 4. Базирование и базы в машиностроении (2 часа лекции)
- •Базирование и размерные цепи
- •Основы базирования
- •Классификация баз
- •Рекомендации к решению задач по базированию
- •Тема 5. Теория размерных цепей (2 часа лекции)
- •Теория размерных цепей
- •Термины и определения
- •Основные понятия
- •Звенья размерных цепей
- •Виды размерных цепей
- •Размеры и отклонения
- •Расчетные коэффициенты
- •Методы достижения точности замыкающего звена
- •Задачи и способы расчета размерных цепей
- •Конструкторские и технологические размерные цепи
- •Тема 6. Порядок построения размерных цепей. (2 часа лекции)
- •Порядок построения размерных цепей
- •Последовательность построения размерной цепи
- •Нахождение замыкающего звена, его допуска, и координаты середины поля допуска
- •Выявление составляющих звеньев размерной цепи
- •Методы достижения точности замыкающего звена
- •Метод полной взаимозаменяемости
- •Метод неполной взаимозаменяемости
- •Метод групповой взаимозаменяемости
- •Метод пригонки.
- •Метод регулирования
- •Методика и примеры расчета размерных цепей
- •Основные расчетные формулы
- •Последовательность расчетов
- •Примеры расчетов допусков (прямая задача)
- •Тема 8. Формирование свойств материала детали. (2 часа лекции)
- •Формирование свойств материала и размерных связей в процессе изготовления детали
- •Формирование свойств материала детали
- •Свойства материала заготовок
- •Воздействия механической обработки на свойства материала заготовок
- •Влияние смазочно-охлаждающей жидкости (СОЖ).
- •Обработка методами поверхностно-пластического деформирования (ППД).
- •Воздействия на свойства материала заготовок термической и химико-термической обработок
- •Обеспечение требуемых свойств материала детали в процессе изготовления
- •Тема 9. Обеспечение точности детали (2 часа лекции)
- •Достижение требуемой точности формы, размеров и относительного положения поверхностей детали в процессе изготовления
- •Три этапа в выполнении операции
- •Сокращение погрешности установки Определенность и неопределенность базирования заготовки.
- •Тема 10. Точность технологической системы (2 часа лекции)
- •Настройка и поднастройка технологической системы
- •Сокращение погрешности динамической настройки технологической системы
- •Информационное обеспечение производственного процесса
- •Свойства технологической информации и информационные связи
- •Технологическая задача и информационное обеспечение ее решения
- •Структура информационных связей в производственном процессе
- •Задачи технологов в разработке информационных процессов
- •Тема 12. Временные связи в производственном процессе (2 часа лекция)
- •Компоненты временных связей
- •Виды и формы организации производственного процесса
- •Основы технического нормирования
- •Пути сокращения затрат времени на выполнение операции
- •Пути сокращения подготовительно-заключительного времени
- •Сокращения штучного времени
- •Вспомогательное время
- •Структуры временных связей в операциях технологического процесса
- •Тема 13. Разработка технологических процессов сборки (4 часа лекции)
- •Основы разработки технологического процесса изготовления машины
- •Последовательность разработки технологического процесса изготовления машины
- •Разработка технологического процесса сборки машины
- •Исходные данные для проектирования
- •Выбор вида и формы организации производственного процесса сборки машины
- •Изучение и анализ чертежей изделия
- •Размерный анализ изделия и выбор метода достижения точности замыкающего звена
- •Анализ технологичности конструкции изделия
- •Разработка последовательности сборки машины
- •Разработка технологических схем сборки
- •Составление перечня работ и их нормирование.
- •Уточнение типа и организационной формы производства.
- •Проектирование операций условий среднего производства
- •Построение циклограммы сборки
- •Разработка компоновки и планировки сборочного цеха (участка)
- •Тема 14. Разработка технологического процесса изготовления детали (8 часов лекции)
- •Разработка технологических процессов изготовления деталей
- •Выбор вида и формы организации производственного процесса изготовления деталей
- •Выбор полуфабриката и технологического процесса изготовления заготовок
- •Изучение служебного назначения детали. Анализ технических требований и норм точности
- •Переход от служебного назначения изделия к техническим условиям на отдельные детали
- •Выбор технологических баз
- •Выбор способов обработки и числа необходимых переходов.
- •Расчет припусков и межпереходных размеров
- •Выбор режимов обработки заготовки
- •Формирование операций из переходов, выбор оборудования и нормирование
- •Оформление документации
- •Тема 15. Современный этап развития технологии машиностроения. (2 часа лекции)
- •Заключение
Если зазор в подшипниках полностью использовать для компенсации погрешностей только в одной из координатных плоскостей, то допуски замыкающих звеньев размерных цепей К и µ составляют
ТХ = 10 мкм и ТµΔ = 100/45 мкм/мм.
Согласно допускам на размеры деталей, указанным на чертежах, образуются следующие значения погрешностей К и µ :
ТК Р = 50+70+150+50 = 320 мкм;
ТµΔР = (20+10+70+20)/45 = 210/45 мкм/мм. |
(11.8) |
Очевидно, что в этом случае для обеспечения требуемого зазора в подшипниках нельзя использовать ни один из методов взаимозаменяемости. Нельзя достичь этого и уменьшением допусков, поскольку это уменьшение должно быть очень значительным и сильно усложнит изготовление деталей.
Метод регулирования в данном случае также неприемлем.
Анализ технологичности конструкции изделия
Целью анализа технологичности конструкций и вносимых на его основе изменений является обеспечение возможности оптимальных затрат труда, средств, материалов и времени при технологической подготовке производства, изготовлении, эксплуатации и ремонте.
Основное внимание в проекте необходимо обратить на производственную технологичность, т.е. технологичность конструкции изделия с точки зрения его изготовления.
Анализ производится на основе ГОСТ 14.201-83 «Технологичность конструкции. Термины и определения», ГОСТ 2.116-84*, ГОСТ 14.205-83, «Правила обеспечения технологичности конструкции изделия», а также рекомендаций [2,4,5].
В первую очередь оцениваются качественные характеристик технологичности конструкции
(ГОСТ 14.004-83):
-взаимозаменяемость;
-регулируемость конструкции;
-контролепригодность конструкции;
-инструментальная доступность конструкции.
В проекте необходимо дать качественную оценку соответствия конструкции следующим требованиям:
– Требования к составу:
1.Сборочная единица расчленяется на рациональное число составных частей на основе принципа агрегатирования.
2.Конструкция сборочной единицы обеспечивает возможность ее компоновки из стандартных и унифицированных частей без применения сложной технологической оснастки.
3.Виды используемых соединений, их конструкции и месторасположение отвечают требованиям механизации и автоматизации сборочных работ.
4.В конструкции сборочной единицы и ее составных частей, имеющих массу более 20 кг, предусматриваются конструктивные элементы для удобного захвата грузоподъемными средствами, используемыми в процессе сборки, разборки и транспортирования.
5.Конструкция сборочной единицы предусматривает базовую составную часть, которая является основной для размещения остальных составных частей.
6.Базовую составную часть выбирают удобной для правильной установки на рабочем месте сборки (в приспособлении, на рабочем столе, сборочной площадке и пр.). Компоновка конструкции сборочной единицы должна позволять производить сборку при неизменном базировании составных частей.
В конструкции базовой составной части предусматривают возможность использования конструктивных сборочных баз в качестве технологических и измерительных.
Компоновка сборочной единицы обеспечивается:
1)общей сборкой без промежуточной разборки и повторных сборок составных частей;
2)удобным доступом к местам, требующим контроля, регулировки и проведения других
работ;
3)легкосъемностью составных частей с малым ресурсом;
4)рациональным расположением такелажных узлов, монтажных опор и других устройств для обеспечения транспортабельности изделия.
– Требования к конструкции соединений составных частей:
Наименьшее количество поверхностей и мест соединений составных частей в конструкции.
Доступность мест соединения составных частей при механизации сборочных работ и контроле качества соединения.
Отсутствие сложной и необоснованно точной обработки сопрягаемых поверхностей соединения составных частей.
Недопустимость дополнительной обработки составных соединений в процессе сборки конструкции.
Рациональность методов закрепления деталей (запрессовка, пластическая деформация, точечная сварка и др.).
Обоснованность посадок и ограничение их количества.
Наличие комплектов основных и вспомогательных конструкторских баз, обеспечивающих определенность базирования.
Наличие конструктивных элементов для ориентации деталей.
– Требования к точности и методу сборки:
Точность расположения составных частей обуславливается точностью изготовления составных частей. Выбирают метод сборки для данного объема выпуска и типа производства на основании расчета и анализа размерных цепей.
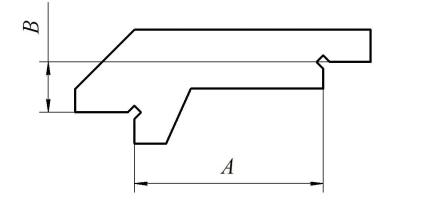
При выборе метода сборки следует учитывать трудоемкость сборочных работ и затраты на изготовление составных частей с точностью, необходимой для данного метода сборки.
Примечание. Методы сборки располагаются по убывающей производительности труда сборочных работ в следующем порядке:
-с полной взаимозаменяемостью;
-с неполной взаимозаменяемостью;
-с групповой взаимозаменяемостью;
-с регулировкой компенсаторами;
-с пригонкой.
В конструкции предусматриваются устройства, обеспечивающие заданную точность относительного расположения составных частей (центрирующие, фиксирующие, компенсирующие).
Пределы регулирования и параметры компенсаторов рассчитываются на основе теории размерных цепей.
Компенсирующие, центрирующие и фиксирующие устройства имеют простую конструкцию, свободный доступ для рабочего и контрольного инструмента.
На основе выполненного анализа технологичности конструкции определяют необходимые конструктивные изменения, упрощающие сборку. В пояснительной записке необходимо обосновать, что вносимые изменения не снижают качества изделия.
По согласованию с руководителем в проекте проводится оценка абсолютных и относительных показателей технологичности согласно работам [2,4,15].
Отработки изделий на технологичность. Снижение трудоемкости пригоночных работ
Применение метода пригонки позволяет снизить точность изготовления деталей, входящих в изделие, но приводит к необходимости выполнения пригоночных работ, требующих высокой квалификации сборщика.
Пригонка наиболее проста, если требуется пригонять только плотность прилегания детали по одной плоскости. Трудоемкость пригонки возрастает при прилегании деталей по одной плоскости. Трудоемкость пригонки возрастает при прилегании двух и более поверхностей, т.е., кроме плотности прилегания, обеспечивают точное взаимное расположение пригоняемой поверхности сопрягаемой детали. Пригонка наиболее сложна, когда, кроме плотности прилегания и взаимного расположения поверхностей, необходимо обеспечивать определенные размеры (рис. 11.6).

Рис.11.6.Пример нетехнологичности выполнения пригоночных работ
Значительное снижение трудоемкости пригоночных работ может быть достигнуто введением в конструкцию неподвижных компенсаторов(рис. 11.7).
Так, при общей сборке внутришлифовального станка совпадение по вертикали осей шпинделей шлифовальной бабки и передней бабки (рис. 11.7, а) достигалось шабрением основания корпуса шлифовальной бабки 1, а параллельность оси шлифовального шпинделя направляющим станины – шабрением его «ласточкина хвоста» по заранее обработанному «ласточкину хвосту» поперечного суппорта 2(рис. 11.7, б).
После введения в конструкцию неподвижного компенсатора 3, (рис. 17, в) выполненного в виде прокладки, и изменения формы поперечного суппорта (ликвидирован «ласточкин хвост» для корпуса шлифовальной бабки) совпадение осей шпинделей в вертикальной плоскости обеспечивается шлифованием компенсатора, а параллельность – поворотом шлифовальной бабки с фиксацией ее контрольными шпильками.
Рис.11.7.Пример отработки конструкции узла внутришлифовального станка на технологичность
Трудоемкость данного этапа сборки сокращается в данном случае на 75 %.
Снижение трудоемкости регулировки
Введение неподвижных компенсаторов при использовании метода регулировки требует разборки собранного узла после измерения замыкающего звена и снятия компенсатора с целью его замены.
После этого выполняется повторная сборка. Таких сборок и разборок может потребоваться несколько. Это резко увеличивает трудоемкость регулировочных и пригоночных работ и отрицательно сказывается на качестве деталей и выполняемых соединений.
Необходимо, чтобы конструкция обеспечивала возможность снятия компенсатора при минимальной разборке первоначального собранного узла (рис. 11.8). Так, при сборке узла с парой конических шестерен (рис. 11.8,а) необходимо:
-установить в корпус подшипник 1;
-надеть на шестерню 2 компенсатор К1 и запрессовать ее в подшипник;

Рис. 11.8. Пример отработки конструкции узла конических шестерен на технологичность
-поставить промежуточные кольца 3 и 4, предварительно совместно прошлифованные по
высоте;
-напрессовать подшипник 5 на шестерню, одновременно введя его наружное кольцо в
корпус;
-собрать остальные детали 6, 7, 8.
После сборки шестерни 2 можно приступить к сборке шестерни 9.
Для этого необходимо:
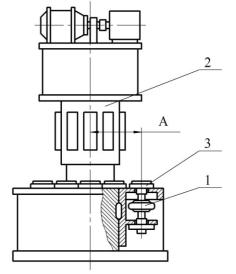
-установить в корпус подшипник 10;
-поставить компенсатор и шестерню 9;
-запрессовать в подшипник валик с установленной в него шпонкой;
-надеть промежуточную втулку (поз. 12);
-напрессовать подшипник 13 на валик, одновременно введя наружное кольцо подшипника в корпус;
-заложить в валик шпонку, надеть на шестерню 14 и закрепить ее винтом 16 через шайбу 15.
После измерения полученной величины замыкающего звена и определения требуемой величины размера компенсатора, необходимо провести полную разборку узла и, установив нужный компенсатор, выполнить вторичную сборку.
Значительно упрощает регулировочные работы изменение конструкции узла (рис. 11.8,б) и использование в качестве компенсатора К1 набора прокладок.
Для замены компенсатора К1 в измененной конструкции узла необходимо отвернуть винт 17 и снять подузел шестерни 2, а для замены компенсатора К2 – отвернуть гайку 18, сняв шайбу 19 и шестерню 9.
Кроме того, появляется возможность параллельной сборки подузлов шестерен 2 и 9.
Наиболее рациональными, с точки зрения трудоемкости сборки, являются конструкции с подвижным компенсатором.
Предпочтительны конструкции, в которых регулировка точности взаимного расположения деталей или узлов достигается без применения в качестве подвижных компенсаторов специальных деталей, т.е. когда подвижным компенсатором является сама рабочая деталь или узел. Этот принцип реализован в конструкции восьмишпиндельных вертикальных полуавтоматов (рис. 11.9).
Рис. 11.9. Схема регулировки токарного восьмишпиндельного полуавтомата
Установка шпинделей 3 на заданном расстоянии А от оси шпиндельного блока 1, установленного на корпусе колонны 2, а также на одинаковый угол по окружности относительно друг друга. Роль подвижных компенсаторов выполняют сами шпиндели в сборе.
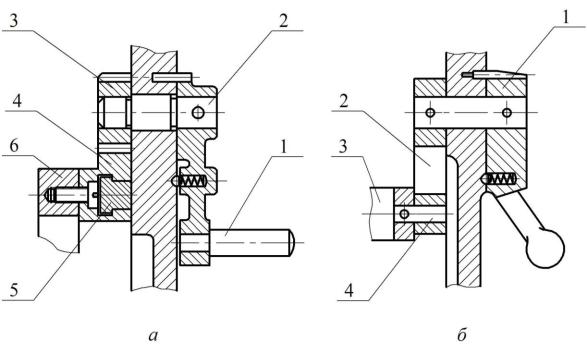
При регулировке они перемещаются по окружности и в радиальном направлении за счет боковых зазоров между фланцевыми втулками на шпинделе и стенками отверстий шпиндельного блока. По окончании регулировки и после контрольной проверки положение шпинделей фиксируется контрольными штифтами.
Снижение трудоемкости выполнения соединений деталей и узлов
Наиболее эффективным мероприятием в этом направлении является уменьшение числа деталей в узле. Пример удачного изменения конструкции механизма переключения шестерен токарного станка приведен на рис. 16. В исходной конструкции (рис. 11.10,а) этот механизм состоял из рукоятки 1, насаженной на ось 2. шестерни 3, сцепляющейся с рейкой 4. Рейка скользила по направляющей планке 5. Переводной сухарь 6 был привернут к рейке 4. В измененной конструкции (рис. 11.10,б) перевод шестерен производится рычагом 2, заштифтованным на оси рукоятки 1. Переводной сухарь 3 устанавливают по скользящей посадке на пальце 4 запрессованном в рычаге 2.
Соединяемые детали необходимо сопрягать по минимальному количеству поверхностей, обеспечивающему определенность заданного взаимного их расположения.
Рис. 11.10. Пример обработки конструкции узла на технологичность уменьшением числа деталей в узле.
Примеры необходимого и достаточного количества сопрягаемых поверхностей, определяющих взаимное расположение деталей, приведены на рис. 11.11.