
Upravlenie_kachestvom_uchebnik
.pdfОсновная концепция «японского чуда» – совершенная технология, будь то технология производства, управления или обслуживания. На фирмах широко применяются вычислительная и микропроцессорная техника, новейшие материалы, автоматизированные системы проектирования, статистические методы (причем последние полностью компьютеризированы).
На японских предприятиях для персонала разработана программа участия в обеспечении качества, получившая название «Пять нулей». Она сформулирована в виде правил-заповедей:
•не создавать (условия для появления дефектов);
•не передавать (дефектную продукцию на следующую операцию);
•не принимать (дефектную продукцию с предыдущей операции);
•не изменять (технологические режимы);
•не повторять (ошибок).
Программу «пяти нулей» невозможно было реализовать без максимального использования человеческих ресурсов. И это первым доказал на практике вице-президент фирмы «Тойота» по производству Таичи Охно, создавший концепцию Just-In-Time (JIT) – «делать все вовремя», которая обеспечивает ноль запасов, ноль отказов, ноль дефектов. Система JIT ведет к эффективным действиям по доставке только требуемых товаров или услуг в «правильном» количестве, в «правильное» время и место. При этом под «правильным» понимаются характеристики, которые ожидают как внутренние, так и внешние потребители.
Практически все перечисленные выше принципы управления качеством были воплощены в микрологистической системе корпоративного управления производством и снабжением КАНБАН (KANBAN), внедренной в корпорации Toyota Motors и позволившей сократить производственные запасы на 50 %, а товарные – на 8 %.
Система КАНБАН начинает изготавливать конкретный образец продукции только тогда, когда на нее есть определенный заказчик (потребитель). Эта система базируется на следующих принципах:
•усиленный контроль качества;
•поставка продукции заказчику точно в срок;
•наладка оборудования, исключающая брак;
•сокращение числа поставщиков комплектующих;
•максимальное приближение смежников к головному (как правило, сборочному) заводу.
Третий этап начинается в 80-е гг. XX в. и характеризуется переходом от статистического к всестороннему контролю качества, стандартом ИСО серии 9000, принципам TQM. Идеи и концепции системного подхода к управлению качеством продукции нашли в Японии большее применение, чем на родине,
вСША. Утверждается, что качество нельзя обеспечить путем проверки, т. е. спомощью технического контроля. Оно должно быть заложено в изделии, причем с самых начальных этапов его концептуальной разработки. Подчеркивается, что 80–85 % проблем качества связано с несовершенством систем управления производством, ответственность за которую несет высшее руко-
101
водство. Важно отметить, что процесс формирования качества распространяется на всю производственно-хозяйственную деятельность, в которой принимают участие всефункциональные подразделения и персоналфирмы.
Японская концепция управления предусматривает четыре уровня качества.
1.Первый уровень (с 1950 г.) – «соответствие стандарту». Необходимо выяснить требования, утвердить стандарт, а также инструкции и процедуры проверки качества продукции. Инструментами при этом служат статистический контроль качества и организационная структура производства. Недостатками этой концепции являются необходимость проведения обязательного контроля качества и отсутствие учета требований потребителя (рынка).
2.Второй уровень (с 1960 г.) – «соответствие использованию». Чтобы соответствовать всем вариантам использования продукции, о ее качестве должны заботиться все подразделения, которые должны функционировать как единое целое. Но при этом требуется учитывать, что более высокое качество приводит к более высоким затратам, а значит, и к повышению цены на продукцию. Методы анализа рынка и межфункциональное управление были освоены в Японии в конце 1960-х – начале 70-х гг.
3.Третий уровень (с 1970 г.) – «соответствие фактическим требованиям рынка». В идеале это означает высокое качество при низкой цене. Единственным путем достижения этой цели является бездефектное производство. А это, прежде всего, зависит от сознательности рабочих и их постоянных усилий по обеспечению качества. Поэтому все рабочие должны постоянно определять дефекты или ошибки и сами их исправлять.
4.Четвертый уровень (с 1980 г.) – «соответствие скрытым потребностям». Преимущество при сбыте получает продукция, учитывающая скрытые потребности.
К основным особенностям японского опыта УК в настоящий период можно отнести:
1) воспитание у каждого изготовителя исключительно уважительного отношения к заказчикам и потребителям;
2) реальная мотивация персонала: пожизненный наем, отказ от идей наказания, увольнения, приоритет ценностей корпорации, поддержание чистоты и порядка, отчетности;
3) участие всех подразделений и работников в обеспечении и УК – навыки командной работы;
4) непрерывное систематическое обучение кадров вопросам обеспечения и УК;
5) эффективное функционирование широкой сети кружков качества на всех стадиях жизненного цикла продукции и сферы услуг;
6) использование развитой системы инспектирования всей деятельности по обеспечению и УК, постоянное присутствие руководителя на производстве;
7) широкое применение при обеспечении и УК передовых методов качества, включая статистические, при приоритетном контроле качества производственных процессов;
102
8)создание и реализация глубоко проработанных комплексных программ по контролю качества и оптимальных планов по их выполнению;
9)наличие в сфере производства высококачественных средств труда (с возрастным составом до трех – семи лет);
10)наличие исключительно развитой системы пропаганды значения высококачественной продукции и добросовестного труда.
11)сильное влияние со стороны государства на принципиальные направления повышения уровня качества и обеспечения конкурентоспособности продукции.
Развитие японской школы управления качеством связано с именами Каору Исикавы, Генити Тагути, Сигео Синго и др. Однако ее становление во многом обусловлено объективными факторами, а также американским и западноевропейским влиянием.
Ярким представителем японской школы управления качеством стал К. Исикава (1915–1989). В его работах подчеркивалась необходимость использования семи инструментов контроля качества: контрольные листы, диаграммы Парето, причинно-следственные диаграммы (диаграммы Исикавы), стратификация, гистограммы, корреляционные диаграммы, контрольные карты Шухарта.
К. Исикава в развитие теории управления качеством разработал концепцию движения «Управления качеством в рамках компании» (Company Wide – Quality Control), которое развернулось в Японии в 1955–1960 гг. по-
сле визитов У. Деминга и Дж. Джурана. Управление качеством в рамках компании есть не что иное, как комплексное управление качеством. К. Исикава подразумевал, что управление качеством должно характеризоваться участием в нем всех сотрудников компании.
К. Исикава известен и как пионер движения кружков качества в Японии. Он выделил общие задачи, стоящие перед кружками: содействие совершенствованию и развитию предприятия; создание здоровой, творческой и доброжелательной атмосферы на рабочем участке; всестороннее развитие способностей работников и использование этих возможностей винтересах фирмы.
Резюмируя основные идеи, предложенные К. Исикавой, необходимо выделить:
• повышение эффективной деятельности компании на основе комплексного управления качеством;
• перестройка мышления в области управления на основе превращения управления качеством в первостепенную задачу;
• ориентация на качество обеспечивает долгосрочное получение прибылей;
• ориентация всех без исключения подразделений на достижение конечной цели;
• управление качеством должно опираться на факты;
• человек в системе управления – основа комплексного управления качеством;
103

•управление качеством – это сочетание высокого профессионализма
иорганизации.
Идеи японского ученого Г. Тагути (род. в 1924 г.) получили распространение не только в Японии, но и в США, странах Западной Европы. Его методология ориентирована на целенаправленную оптимизацию продукции и процессов до начала производства.
В начале 1970-х гг. Г. Тагути разработал концепцию функции потерь качества (Quality Loss Function). Главным он считает экономический фактор (стоимость), а качество и стоимость рассматривает совместно. Он связывает их общей характеристикой, называемой функцией потерь, причем одновременно рассматривает потери как со стороны потребителя (вероятность аварий, травм, отказов, невыполнения своих функций, неудовлетворение требований заказчика и т. д.), так и со стороны производителя (затраты времени, энергии, сил, токсичность и др.) Проектирование осуществляется такимобразом, чтобы были удовлетворены обе стороны. Если параметр качества продукции совпадает с номинальным значением (рис. 26), то потери для общества равны нулю. При движении дальше по кривой они начинают возрастать.
LX
Поле допуска (Т)
|
Функция потерь |
|
Убывание |
(LX) |
|
Возрастание |
|
|
потерь |
потерь |
|
О |
Т |
Х |
Нижний предел |
Верхний предел |
|
Номинальное значение – m
Рис. 26. Функция потерь Г. Тагути
Поскольку финансовые потери связаны с функциональной характеристикой, разработчики получают надежный инструмент сопряжения техники и экономики:
L(X) = k (x – m)2,
где L(X) – потери; х – значение функциональной характеристики; m – номинальное значение; k – постоянная потерь, вычисляемая с учетом расходов, которые несет изготовитель при браковке изделия (затраты на ремонт или замену).
Если предложить, что допуск на показатель качества симметричен относительно номинала, а величина потерь на любой из границ допуска равна L0, то имеем:
104
К = 4L0/Т2
Вторым концептуальным новшеством Г. Тагути явилось введение понятия «робастности». Изделия или технологические процессы считаются «робастными», если они устойчивы к воздействию неконтролируемых факторов или шумов.
Соотношение сигнал/шум интерпретируется всегда одинаково: чем больше, тем лучше. Эта величина связана с коэффициентом вариации относительно x при фиксированных условиях эксперимента для управляемых факторов. Таким образом, разработчик призван больше заботиться о создании «робастных» изделий или производственных систем, чем о подавлении шумов, что часто дорого, трудно, а иногда и невозможно.
Г. Тагути впервые разделил учитываемые факторы на основные, оказывающие регулирующее действие на результат, и факторы второстепенные. Он ввел определение отклоняющего фактора (или шума), являющегося причиной разброса характеристик на рабочем месте. Поскольку на рабочем месте обычно велик разброс условий, Г. Тагути предложил характеризовать производимые изделия устойчивостью технических характеристик. Г. Тагути внес поправку также в понятие случайного отклонения. Он придерживается мнения, что все отклонения и ошибки имеют свои причины и что существуют не случайности, а факторы, которые иногда трудно учесть.
Основной вклад С. Синго (1909–1990) в решение проблемы качества связан с концепцией «Пока-Екэ» – «защищенность от ошибок», выдвинутой им в 1961–1964 гг. Главная идея состоит в остановке процесса, как только обнаруживается дефект, в определении причины и предотвращении возобновления источника дефекта. Поэтому не требуется никаких статистических выборок. Ключевая часть процедуры состоит в том, что инспектирование источника ошибки проводится как часть производственного процесса. При обнаружении ошибки либо останавливается производство до ее исправления, либо процесс корректируется с целью предотвращения появления дефекта. Это осуществляется на каждой стадии процесса путем мониторинга потенциальных источников ошибок и стало возможным с применением автоматической обратной связи.
Европейский опыт. В Европе в 50–70-е гг. XX в. реализуются программы повышения качества, проводится активная политика в вопросах качества, осуществляется долгосрочное планирование качества. В течение 80-х гг. повсюду в Европе наблюдалось движение к повышению качества продукции, работ и услуг на основе внедрения стандартов ИСО серии 9000. Это привело к более последовательной позиции по вопросам качества, более надежным поставкам и более стабильному уровню качества в целом.
Начиная с 1990-х гг. необходимо отметить целенаправленную деятельность стран Западной Европы по созданию единого европейского рынка, выработке общих требований и процедур, способных обеспечить эффективный обмен товарами и рабочей силой между странами.
105
ВЕвропе проводится активная работа по развитию унификации методов стандартизации качества.
Впроцессе подготовки к открытому общеевропейскому рынку, провозглашенному с 1 января 1993 г., были выработаны единые стандарты, единые подходы к технологическим регламентам, гармонизированы национальные стандарты на системы качества, созданные на основе стандартов ИСО серии 9000, введены в действие их европейские аналоги – EN серии 9000. Большое значение придается сертификации систем качества на соответствие этим стандартам, созданию авторитетного европейского органа по сертификации в соответствии стребованиями стандартов EN серии 45000.
Национальные организации входят в Западноевропейскую сеть род-
ственных национальных органов (European Network for Quality System Assessment and Certification – EQNET). Эта сеть создана в соответствии с мно-
госторонним Соглашением о сотрудничестве, подписанным в марте 1990 г. представителями восьми стран. К концу 1992 г. сеть практически сформировалась, в нее входят организации 16 стран, подтвердивших свои намерения. Главной целью сети EQNET является оказание организациям в странах ЕС, независимо от сферы их деятельности, разнообразных услуг, которые должны облегчить получение и признание сертификатов на системы качества; координация работы по оценке и сертификации систем в таких организациях, которые имеют представительства в нескольких странах Западной Европы; содействие подписанию двусторонних договоренностей между членами сети EQNET; развитие справочно-информационной службы. Каждая сторона, подписавшая соглашение, признает сертификаты, выданные членами сети EQNET.
Образованы Европейский координационный совет по испытаниям сертификации и Европейский комитет по оценке и сертификации систем качества.
Характерной особенностью деятельности по управлению качеством
вЕвропе является наличие авторитетной региональной организации, созданной еще в 1956 г., – Европейской организации по контролю качества (с 1989 г. – Европейская организация по качеству – EOQ).
ВЗападной Европе под эгидой Европейской организации по качеству (EOQ) развернута подготовка специалистов трех градаций: EQQ Quality Professional (профессионал по качеству); EOQ Quality System Manager (ме-
неджер по системам качества); EOQ Quality Auditor (аудитор по качеству). В феврале 1993 г. было создано Объединение по регистрации персонала по качеству (Unit for Registration of Quality Personnel – URQP), членами кото-
рого являются организации по качеству стран – членов Европейской организации по качеству. К 1997 г. национальные организации пятнадцати стран Западной и Центральной Европы получили аккредитацию в рамках Европейской гармонизированной схемы для квалификации и регистрации специалистов по качеству.
106
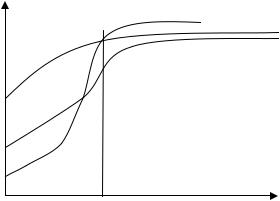
В сентябре 1988 г. президенты 14 крупнейших фирм Западной Европы подписали соглашение о создании Европейского фонда управления качеством (EFQM). Область деятельности Европейского фонда управления качеством:
1.Поддержка руководства западноевропейских компаний в ускорении процесса повышения качества для достижения преимуществ во всеобщей конкуренции.
2.Стимулирование и, где это необходимо, помощь всем сегментам западноевропейского сообщества принимать участие в деятельности по улучшению качества и укреплению культуры европейского качества.
EFQM совместно с Европейской организацией по качеству (EOQ) учредил Европейскую премию по качеству, которая начиная с 1992 г. присуждается лучшим фирмам. По инициативе Европейской организации по качеству и Европейского фонда управления качеством (ЕФУК) при поддержке Комиссии Европейских сообществ с 1995 г. стала проводиться Европейская неделя качества.
Отличительная особенность европейского подхода к решению проблем качества:
• единая законодательная основа для проведения всех работ, связанных с оценкой и подтверждением качества;
• гармонизация требований национальных стандартов, правил и процедур сертификации;
• создание региональной инфраструктуры к сети национальных организаций, уполномоченных производить работы по сертификации продукции и систем качества, аккредитацию лабораторий, регистрацию специалистов по качеству и т. д.
Обобщая зарубежный опыт управления качеством, следует отметить «сближение» уровня качества в ведущих странах мира (рис. 27).
Уровень |
2 |
качества |
1 |
продукции |
3 |
|
1950 1960 1970 |
1980 1990 2000 |
Годы |
Рис. 27. Уровни качества продукции: 1 – в США, 2 – в Японии, 3 – в Европе
107

Из рис. 27 видно, что в 1975 г. произошла смена лидерства в этой области. В лидеры по качеству продукции вышла Япония. К 1985 г. на долю Японии стало приходиться более половины продаваемых в мире товаров: фотокамеры (84 %), кассетные видеомагнитофоны (84 %), часы (82 %), калькуляторы (77 %), высокочастотные кухонные печи (71 %), телефонные аппараты (66 %), мотоциклы (55 %), цветные телевизоры (53 %) и др. Однако с 1991–1992 гг. Японию поразил экономический кризис, который привел к уменьшению объемов продаж и снижению конкурентоспособности товаров. На этом фоне произошло выравнивание уровней качества между продукцией Японии, США и стран Европы. Сближение уровней качества в различных странах мира стало следствием творческого обмена передовым опытом работы по улучшению качества, интеграции подходов и методов, к управлению качеством.
2.4. Создание системы менеджмента качества
Управление качеством продукции на предприятии предполагает создание систем менеджмента качества (СМК) и принятие всех необходимых мер по обеспечению их эффективного функционирования. СМК гарантирует предприятию стабильное, устойчивое качество изготавливаемой и поставляемой продукции.
Оценка опыта, накопленного в области управления качеством, показала, что создание СМК целесообразно осуществлять в пять этапов: 1) организация работ по созданию СМК; 2) проектирование СМК; 3) документирование СМК; 4) внедрение СМК; 5) контроль и сертификация СМК(рис. 28).
|
Этап 1 |
|
Этап 2 |
|
|
|
Этап 3 |
|
Этап 4 |
|
Этап 5 |
|
|
Организация |
|
Проектирова- |
|
|
Документиро- |
|
Внедрение |
|
Подготовка к |
||
|
работ |
|
ние |
|
|
|
вание |
|
|
|
сертификации |
|
|
Цель: |
|
Цель: |
|
|
Цель: |
|
Цель: |
|
Цель: |
||
|
создание ор- |
|
создание |
|
|
создание нор- |
|
обеспечение |
|
обеспечение |
||
|
ганизацион- |
|
структуры |
|
|
мативной |
|
функциониро- |
|
готовности |
||
|
ных предпо- |
|
СМК |
|
|
базы |
|
вания СМК в |
|
предприятия к |
||
|
сылок для |
|
|
|
|
|
|
|
|
соответствии |
|
проведению |
|
разработки и |
|
|
|
|
|
|
|
|
с установлен- |
|
сертификации |
|
внедрения |
|
|
|
|
|
|
|
|
ными требо- |
|
СМК |
|
СМК |
|
|
|
|
|
|
|
|
ваниями |
|
|
|
|
|
|
|
|
|
|
|
|
|
|
|
Рис. 28. Этапы создания СМК
Организация работ по созданию СМК включает следующие основные действия (в скобках указан результирующий документ соответствующей работы):
1)обоснование необходимости создания системы управления качеством (справка);
2)подготовка и издание приказа о разработке проекта СМК (приказ);
3) формирование рабочей группы по созданию СМК (положение о координационно-рабочей группе);
108

4)организация и проведение обучения в области качества (программы, учебные планы и справка о проведении обучения);
5)разработка программы и проведение предварительного анализа действующей СМК (отчет о проведенном анализе или аналитическая справка);
6)разработка технического задания (ТЗ) на проектирование СМК (утвержденное ТЗ).
Естественным продолжением первого этапа являются работы по проектированию СМК, направленные на выявление и описание процессов, которые обеспечивают создание потребительской ценности продукции.
При проектировании СМК, ориентированной на процессы, необходимо выполнять требования п. 4.1 стандарта ИСО 9001:2008, а именно:
a) выявить процессы, необходимые для реализации системы менеджмента качества, и их применение на предприятии;
b) определить последовательность и взаимодействие процессов;
c) определить критерии и методы, необходимые для обеспечения результативной работы и управления процессами;
d) обеспечить наличие ресурсов и информации, необходимой для поддержания деятельности и мониторинга процессов;
e) наблюдать, измерять и анализировать процессы;
f) принимать меры, необходимые для достижения запланированных результатов и постоянного улучшения процессов.
Требования пункта 4.1 стандарта ИСО 9001:2008 можно представить
ввиде схемы проектирования процессов системы качества (рис. 29).
Рис. 29. Схема проектирования СМК на предприятии
109

Фундамент процессного подхода составляет понятие «процесс». Общепринято под процессом (от лат. processus – прохождение, продвижение) понимается последовательное изменения каких-либо состояний во времени и в пространстве. Согласно ГОСТ Р ИСО 9000-2008 (п. 3.4.1) процесс –
совокупность взаимосвязанных и взаимодействующих видов деятельности, преобразующих входы в выходы. Общую модель процесса можно представить в виде риc. 30.
ВХОДЫ |
ПРОЦЕСС – со- |
ВЫХОДЫ |
|
Материалы |
вокупность взаи- |
|
|
Способы |
мосвязанных и |
Технические изделия |
|
Методы |
взаимодейст- |
Программное обеспечение |
|
Информация |
вующих видов |
Переработанные материалы |
|
Люди |
|||
деятельности |
Услуги |
||
Навыки |
|||
|
Информация |
||
Здания |
|
||
|
Документы |
||
Оборудование |
|
||
|
|
||
|
|
|
Рис. 30. Схема процесса
Строить процесс удобно графически. Можно предложить вариант такого графика (рис. 31).
КартаЛист1 |
|
Сводка |
|
|
|
из___ листов |
|
|
|
|
|
Продукция/ |
Действия |
Существует |
|
Предлагается |
Экономия |
Материал |
Обработка O |
|
|
|
|
Детали блока |
Транспортировка → |
|
|
|
|
Задержка ⌂ |
|
|
|
|
|
дегидратора |
Проверка □ |
|
|
|
|
(ND 250)/SS/34 |
Хранение ∆ |
|
|
|
|
Действие |
Расстояние, м |
|
|
|
|
|
|
|
|
|
|
Операция прес- |
|
|
|
|
|
сования |
|
|
|
|
|
Метод: |
|
|
|
|
|
Существующий |
|
|
|
|
|
Цех: Первый |
Время |
|
|
|
|
прессовый |
|
|
|
|
|
Отделение: |
|
|
|
|
|
Первая группа |
|
|
|
|
|
прессов |
|
|
|
|
|
Рабочие |
Затраты |
|
|
|
|
Смена № ___ |
Цена труда |
|
|
|
|
Подготовил |
Стоимость мате- |
|
|
|
|
___________ |
риалов |
|
|
|
|
Одобрил _____ |
Итого |
|
|
|
|
Дата ____ |
|
|
|
|
|
|
|
|
|
|
|
110 |
|
|
|
|
|