
надежность машин и оборудования
.pdf201
Ð = Ð(g £ g £ |
|
), |
a |
|
= |
1 − Ðä |
= Ð(g < g ) = Ð(g > |
|
), |
|
|
g |
γ |
g |
(9.109) |
||||||||
|
|||||||||||
ä |
|
|
|
2 |
|
|
|
|
|||
|
|
|
|
|
|
|
|
|
ãäå αγ - уровень значимости симметричного доверительного интервала для γ.
Рассмотрим влияние коэффициента ускорения g на исход испытаний. Пусть для испытательного режима qè каким-либо образом назначен приемочный норматив T′ïð. Условия выбора гипотез запишутся в виде:
T′ ³ T′ïð - принимается гипотеза Í0; |
(9.110) |
T′ < T′ïð - принимается гипотеза H1. |
(9.111) |
Большие значения g снижают среднюю выборочную наработку T′ и тем самым способствуют выполнению условия браковки (9.111), малые значе-
ния g способствуют приемке по условию (9.110). Соответственно, в первом случае увеличивается вероятность ошибки первого рода, во втором случае - ошибки второго рода. Таким образом, кроме случайности выборки при ускоренных контрольных испытаниях приемка и браковка дополни-
тельно обусловлены случайностью значения коэффициента ускорения g изза недостоверности базовой зависимости. Следовательно, часть заданных рисков изготовителя и заказчика должна быть "выделена" на специфиче- скую для ускоренных испытаний возможность ошибок по недостоверности
коэффициента ускорения, и лишь оставшаяся их часть a0 è b0 использоваться для планирования по формуле (9.24).
План испытаний должен обеспечить требуемые риски a и b при всех значениях g, лежащих в доверительном интервале (9.109). Полная вероят-
ность браковки партии с Òô=Ò1 ïðè |
γ < γ определится по теореме умно- |
||||||||
жения вероятностей |
|
|
|
|
|
1 + Ðä |
|
||
Ð(g ³ g; T¢ < Tïð /Òô = Ò1) = (1 - b0 ) |
(9.112) |
||||||||
|
2 |
||||||||
и должна быть равна 1 – b, откуда |
|
|
|
|
|
|
|||
|
|
2(1 - b) |
|
|
|
|
|||
b0 |
= 1 - |
. |
|
|
(9.113) |
||||
|
|
|
|
||||||
|
1 + Ðä |
|
|
|
|
||||
Аналогично для Òô=Ò0 и g =`g можно получить |
|
|
|
||||||
a0 = 1 - |
|
2(1 - a) |
. |
|
|
(9.114) |
|||
1 +Ðä |
|
|
|||||||
|
|
|
|
|
|
Выражения (9.113) и (9.114) позволяют вычислить риски a0 è b0, которые нужно использовать при планировании объема выборки и приемоч- ного норматива ускоренных контрольных испытаний при заданных значе-
ниях a и b, если базовая зависимость определена с достоверностью Ðä. Из формул (9.113) и (9.114) также следует:
Ðä > 1 – 2a; Ðä > 1 – 2b, èëè Ðä > 1 – a – b . (9.115) Неравенства (9.115), определяющие достоверность базовой зависимо-
сти для обеспечения при ускоренных испытаниях заданных рисков a и b, используются для планирования исследовательской части испытаний.
Приемочно-браковочный норматив T′ïð в рабочем режиме испытаний qè должен устанавливаться также с учетом доверительных границ коэффици-
202
ента ускорения. Браковка партии производится при g < `g, а приемка - при
g > g, откуда с учетом выражений (9.113), (9.113) и (9.115): |
|
||||||||||||||||||||||||||||||||||
|
Òáð |
|
Ò |
0 |
|
|
c2 |
|
|
|
|
|
|
|
|
|
|
|
|
|
Òïð |
|
Ò |
|
c2 |
|
|
||||||||
T¢ = |
|
|
|
|
= |
|
|
|
|
|
|
|
(2n), |
|
|
T¢ |
= |
|
|
|
|
= |
1 |
|
(2n). |
(9.116) |
|||||||||
|
|
|
|
|
|
|
|
0 |
|
|
|
|
|
|
|
|
|||||||||||||||||||
|
|
|
|
|
|
|
|
|
|
|
|
|
|
|
|
||||||||||||||||||||
áð |
|
g |
|
g |
2n |
|
α |
|
|
|
|
|
|
|
|
ïð |
|
|
g |
|
g2n |
1−β0 |
|
|
|||||||||||
|
|
|
|
|
|
|
|
|
|
|
|
|
|
|
|
|
|
|
|
|
|
|
|
||||||||||||
Приравнивая T′ïð è T′áð, составим аналогичную систему уравнений для |
|||||||||||||||||||||||||||||||||||
планирования ускоренных контрольных испытаний: |
|
|
|
|
|||||||||||||||||||||||||||||||
|
|
|
|
|
|
ìÒ¢ |
|
|
|
= |
|
|
|
Ò0 |
c |
2 |
|
(2n) = |
Ò1 |
c2 |
(2n), |
|
|
||||||||||||
|
|
|
|
|
|
|
|
|
|
|
|
|
α |
0 |
|
|
|
||||||||||||||||||
|
|
|
|
|
|
ï |
|
ïð |
|
|
|
g2n |
|
|
|
|
|
|
|
g2n |
1−β0 |
|
|
|
|
||||||||||
|
|
|
|
|
|
ï |
|
|
|
|
|
|
|
|
|
|
|
|
|
|
|
|
|
|
|
|
|
|
|||||||
|
|
|
|
|
|
|
|
|
|
|
|
|
|
|
c2−β |
|
|
(2n) |
|
|
|
|
|
|
|
|
|
|
|
|
|||||
|
|
|
|
|
|
íT g |
|
|
|
|
|
|
|
|
|
|
|
|
|
|
|
|
|
(9.117) |
|||||||||||
|
|
|
|
|
|
ï |
|
0 |
|
|
|
= |
|
|
|
1 |
|
0 |
|
|
|
. |
|
|
|
|
|
|
|
|
|
|
|
||
|
|
|
|
|
|
ï |
T |
|
|
|
|
|
|
2 |
|
|
( |
|
|
) |
|
|
|
|
|
|
|
|
|
|
|
||||
|
|
|
|
|
|
g |
|
|
|
|
|
|
2n |
|
|
|
|
|
|
|
|
|
|
|
|||||||||||
|
|
|
|
|
|
î |
|
1 |
|
|
|
|
|
|
|
cα 0 |
|
|
|
|
|
|
|
|
|
|
|
|
|
|
В отличие от (9.116) в систему (9.117) входят значения a0 è b0, ìåíü-
шие заданных a и b в связи с недостоверностью базовой зависимости. Решение системы (9.117) аналогично решению уравнений (9.116): по из-
вестным значениям T0, T1, γ и`g вычисляется левая часть второго уравне-
ния, а затем по таблицам распределения c2 (прил.1) подбирается число степеней свободы k=2n, обеспечивающее равенство правой и левой частей. Затем из первого уравнения находится значение T′ïð.
Если уравнения (9.116) всегда имеют решение (так как T0/T1>1), то система (9.117) может быть решена только в случае, когда
T0 |
γ |
|
|
|
Ò0 |
|
|
|
. |
|
||
> 1, |
èëè |
|
> |
g |
(9.118) |
|||||||
|
|
|
|
|
|
|||||||
T g |
Ò |
|||||||||||
|
|
|
g |
|
||||||||
1 |
|
|
|
|
1 |
|
|
|
|
|
Невыполнение неравенств (9.118) означает, что неопределенность коэффициента ускорения превышает относительное различие проверяемых уровней наработки. В этом случае требуется либо изменение исходных
данных (T0 è T1), либо уточнение значения коэффициента g проведением дополнительных исследовательских испытаний.
Даже если неравенства (9.118) выполняются, объем выборки n для ускоренных испытаний получается больше, чем в нормальных условиях, что является своего рода платой за ускорение процесса.
Ускоренные контрольные испытания могут проводиться и по методу двукратной выборки. При этом планирование аналогично рассмотренному в разд.9.1, но с использованием уравнений (9.113), (9.114) и (9.117).
Проводятся рабочие контрольные испытания при выбранной темпера-
òóðå qè, подвергая испытаниям выборку объема n, найденного из уравнений (9.117). По значениям наработки всех экземпляров вычисляется их выборочное среднее. Выбор гипотез H0 èëè H1 (приемка или браковка партии) производятся проверкой неравенств (9.110) и (9.111).
9.3.3. Проведение ускоренных испытаний
Исходными данными для организации испытаний являются значения нормальной T0 и минимально допустимой T1 генеральной наработки, риски изготовителя a и заказчика b, значение температуры в нормальных усло-
203
âèÿõ θí. Разработка программы и проведение ускоренных форсированных контрольных испытаний при использовании в качестве ускоряющего фак-
тора температуры θ осуществляется в следующей последовательности:
1.По уравнениям (9.116) определяется достоверность базовой зависимости, необходимая для обеспечения заданных α è β.
2.Определяются элементы плана [N=n,U,r=n] исследовательских оп-
ределительных испытаний при α =`α = (1–Ðä)/2. Относительная точность
ε0 задается в пределах от 0,05 до 0,2. Малые значения ε0 в последующем облегчат проведение контрольных испытаний, но потребуют большего объ-
ема исследовательских испытаний. При больших ε0 ситуация обратная.
3. Выбираются значения температур θi, при которых будут проводиться исследовательские испытания, руководствуясь рекомендациями разд.9.3.1.
Желательно, чтобы одна из температур равнялась θí.
4.Проводится эксперимент и для каждой температуры θi вычисляется значение оценки средней наработки Ti*.
5.В координатах (1/θ, ln(1/T)) наносятся экспериментальные точки.
6.По формулам (9.99) вычисляются верхняя `ε и нижняя ε половины доверительного интервала в логарифмическом масштабе (ее можно для каждой экспериментальной точки отложить на графике).
7.Устанавливается возможность кусочно-линейной аппроксимации семейства точек (см.рис.9.13), определяются границы участков.
8.Для каждого участка методом наименьших квадратов (9.101) находится уравнение средней выравнивающей линии (9.100). Для проверки правильности расчетов эти линии строятся по найденным уравнениям, а затем уточняются границы участков аппроксимации.
9.Выбирается температурный режим для форсированных рабочих испытаний (см.разд.9.3.1).
10.По уравнениям (9.102) строятся линии доверительных границ базо-
вой зависимости (рис.9.14) участка, включающего температуры θí è θè, и вычисляются координаты угловых точек полученного параллелограмма. По
формулам (9.117) и (9.118) вычисляются доверительные границы γ è `γ .
11. По формулам (9.113) и (9.114) определяются скорректированные
значения рисков α0 è β0.
12. По уравнениям (9.117) находятся приемочно-браковочный норматив T′ïð для режима контрольных испытаний θè и необходимый объем выборки n. Если не выполняются условия (9.118), необходимо повысить точность испытаний, уменьшив величину ε0, и повторить действия, начиная с п.2.
13.Осуществляется экспериментальная часть контрольных испытаний
èпринимается решение о надежности партии.
При использовании в качестве ускоряющего фактора каких-либо других параметров последовательность планирования и проведения ускоренных испытаний примерно такая же.

204
Ëè ò å ð à ò ó ð à
1.Надежность и эффективность в технике: Справочник: В 10 т. Т.6. Экспериментальная отработка и испытания. - М.: Машиностроение, 1989.- 376 с.
2.Капур Е., Ламберсон Л. Надежность и проектирование систем.- М.: Мир, 1980.- 604 с.
3.Сотсков Б.С. Основы теории и расчета надежности элементов и устройств автоматики и вычислительной техники.- М.: Высш.шк., 1970.- 272 с.
4.ÃÎÑÒ 27.410-87. Надежность в технике. Методы и планы статистического контроля показателей надежности по альтернативному признаку.
5.Надежность технических систем. Справочник. Под ред. И.А.Ушакова.- М.: Радио
èсвязь, 1985. - 608 с.
6.ÃÎÑÒ 27.411-81. Надежность в технике. Одноступенчатые планы контроля по альтернативному признаку при распределении времени безотказной работы по закону Вейбулла.
7.Кугель Р.В. Испытания на надежность машин и их элементов.- М.: Машиностроение, 1982.- 181 с.
8.Труханов В.М. Методы обеспечения надежности изделий машиностроения.- М.: Машиностроение, 1995.- 304 с.
9.Справочник по надежности. Том 1.- Пер.с англ. под ред. Б.Р.Левина.- М.: Мир, 1969.- 340 с.
10.Волков Л.И., Шишкевич А.М. Надежность летательных аппаратов.- М.: Высш.школа, 1975.- 293 с.
11.Бессонов А.А., Мороз А.В. Надежность систем автоматического регулирования.- Л.: Энергоатомиздат, 1984.- 216 с.
12.Хазов Б.Ф., Дидусев Б.А. Справочник по расчету надежности машин на стадии проектирования.- М.: Машиностроение, 1986.- 224 с.
13.Надежность и эффективность в технике: Справочник: В 10 т. Т.7. Качество и надежность в производстве.- М.: Машиностроение, 1989.- 376 с.
14.Ллойд Д., Липов М. Надежность: организация, исследования, методы, математический аппарат.- М.: Сов.радио, 1964.- 686 с.
15.Судаков Р.С. Испытания технических систем. Выбор объемов и продолжительности.- М.: Машиностроение, 1988.- 271 с.
16.Комаров А.А. Надежность гидравлических устройств самолетов.- М.: Машиностроение, 1976.- 224 с.
17.Канарчук В.Е. Основы надежности машин.- Киев: Наукова думка, 1982.- 248 с.
18.Чернышев А.А. Основы надежности полупроводниковых приборов и интегральных микросхем.- М.: Радио и связь, 1988.- 256 с.
19.Проников А.С. Надежность машин.- М.: Машиностроение, 1978.- 592 с.
20.Наумов В.А. Основы надежности и долговечности в машиностроении.- Омск: Омский политехнический институт, 1972.- 332 с.
21.Бердичевский Б.Е. Вопросы обеспечения надежности радиоэлектронной аппаратуры при разработке.- М.: Сов.радио, 1977.- 384 с.
22.Перроте А.И., Карташов Г.Д., Цветаев К.Н. Основы ускоренных испытаний радиоэлементов на надежность.- М.: Сов.радио, 1968.- 224 с.
23.Пешес Л.Я., Степанова М.Д. Основы теории ускоренных испытаний на надежность.- Минск: Наука и техника, 1972.- 168 с.
24.Ускоренные испытания изделий машиностроения на надежность. Труды ВНИИНМАШ. Вып.4.- М.: Изд-во стандартов, 1969.- 25 с.
25.Кузнецов Н.Д., Цейтлин В.И. Эквивалентные испытания газотурбинных двигателей.- М.: Машиностроение, 1976.- 214 с.
26.ÐÄ 50-686-89. Надежность в технике. Методы ускоренных испытаний на усталость для оценки пределов выносливости материалов, элементов машин и конструкций. Методические указания.
205
ЗАКЛЮЧЕНИЕ
Современный уровень развития науки и техники позволяет создавать высоконадежные конструкции, машины, оборудование и приборы. Необходимым условием для этого является комплекс мер, принимаемых на стадиях проектирования, изготовления и эксплуатации:
-на стадии проектирования - выбор рациональных конструктивных и технологических схем, применение современных конструкционных и других материалов, использование научно обоснованных методик расчета с учетом всех возможных условий эксплуатации, внешних воздействий и внутренних процессов;
-на стадиях изготовления, сборки и монтажа - тщательный контроль используемых материалов и комплектующих изделий, высокий уровень организации и контроля технологических процессов, промежуточные контрольные испытания отдельных элементов (деталей, узлов, агрегатов и систем), отработанная система приемо-сдаточных мероприятий;
-в процессе эксплуатации - устранение скрытых дефектов на стадии пуска и приработки, разработка и применение системы технического обслуживания и ремонта, включающей комплекс диагностических и плановопрофилактических мероприятий.
Решение всех этих задач возможно только на базе теоретически обоснованных и экспериментально подтвержденных качественных и количественных закономерностей, определяющих надежность технических объектов, методов оценки влияния различных факторов, процессов и явлений на
количественные характеристики надежности. Разработка и использование методов теории надежности в различных областях техники открывает перспективу для научно обоснованного прогнозирования и расчета показателей качества и надежности технических объектов, анализа и синтеза высокоэффективных и высоконадежных технических систем, выбора оптимальных конструктивных и технологических решений, обеспечивающих высокие производственные и экономические показатели, длительные сроки эксплуатации.
Основные положения и методы теории надежности носят универсальный характер и в принципе применимы к объектам самой различной природы и структуры. Однако их практическое использование для расчета некоторых объектов связано с серьезными трудностями из-за сложного характера взаимодействия элементов и подсистем между собой и с окружающей средой, трудности или невозможности получения в необходимом объеме статистической информации об отказах, сложности, слабой изученности или непредсказуемости процессов и явлений, происходящих в элементах и т.д. Единственным путем преодоления этих трудностей является
развитие физической теории надежности ("физики отказов"), которая естественным образом включает описание физического взаимодейст-
206
вия объекта с окружающей средой и процессов перехода элементов и систем из работоспособного в неработоспособное состояние в структуру математических моделей надежности. При этом описание изменения надежности объекта становится органически связанным с описанием его функционирования. Однако если в настоящее время математические методы теории надежности развиты достаточно хорошо, то физическая теория надежности в отношении многих технических объектов находится на начальных стадиях развития.
Дальнейшее изучение процессов взаимодействия технических объектов со средой с учетом обратных связей, оценка взаимного влияния основных параметров и других особенностей потери работоспособности сложных систем позволит разработать более совершенные модели отказов, которые позволят с высокой точностью прогнозировать поведение объектов в различных условиях эксплуатации.
Прогнозирование надежности сложных систем является ключе- вым направлением для решения основных задач надежности, особенно на стадиях проектирования. С этой точки зрения существенным резервом теории надежности является широкое использование методов статистиче- ского моделирования надежности сложных технических систем, которые дают возможность существенно сократить или даже заменить длительные, сложные и дорогостоящие экспериментальные исследования. Современные ЭВМ позволяют производить расчеты надежности на основании алгоритмов практически любой сложности, максимально полно учитывающих реальные условия, в том числе большое количество случайных факторов.
Однако основным источником информации для прогнозирования надежности технических объектов являются их экспериментальные исследования. Уникальность многих сложных технических систем и их высокая безотказность часто исключают применение традиционных методов испытаний на надежность. Развитие методов испытаний в сочетании с методами прогнозирования и использования априорной информации, разработка алгоритмов оценки надежности с учетом информации о фактическом состоянии объектов, выявление возможностей экстремальных ситуаций при эксплуатации, сочетание испытаний со статистическим моделированием, расчет и прогнозирование основных процессов потери работоспособности являются основой для развития науки о надежности.
Особое место среди основных задач надежности занимает прогнозирование надежности на стадии эксплуатации. В отличие от стадии проектирования, когда, как правило, прогнозируются количественные характеристики надежности совокупности объектов (например, партии изделий), при эксплуатации оцениваются показатели конкретных работающих объектов. Индивидуальное прогнозирование открывает дополнительные возможности для увеличения экономического эффекта - оно не только позволяет предупреждать потенциальные отказы, но и более рационально и обоснованно планировать или корректировать режимы эксплуатации, профилактические мероприятия и систему снабжения запасными частями. Кроме того, индивидуальное прогнозирование надежности приводит к уве-
207
личению средних показателей, поскольку уменьшает вероятность преждевременного списания технических объектов или вывода из эксплуатации для ремонта. Особенно актуальна эта проблема для уникальных дорогостоящих технических объектов, надежность которых часто связана с безопасностью человека или окружающей среды и для которых, как правило, отсутствует достаточно полная информация об отказах (летательных и космических аппаратов, некоторых видов технологического оборудования, энергетических установок и т.д.).
Индивидуальное прогнозирование надежности связано, прежде всего, с дополнительными расходами на средства технической диагностики и приборы контроля, регистрирующие уровень нагрузок и состояние объектов, однако его внедрение является также серьезной задачей для теории надежности, поскольку требует фундаментального методического, математического и программного обеспечения, которое бы позволило получать обоснованные выводы на основании полученной информации.
Хотя при современных темпах развития техники моральное старение многих технических объектов происходит быстрее, чем раньше, во многих отраслях промышленности фактический ресурс оборудования еще не достигает оптимальных с экономической точки зрения значений. Поэтому увеличение сроков эксплуатации на базе совершенных моделей надежности и индивидуального прогнозирования может привести к существенной экономии материалов, снижению энергетических и трудовых затрат, которые идут на пополнение и ремонт парка оборудования. Увеличение сроков и повышение эффективности эксплуатации технических объектов невозможно также без оптимизации системы технического обслуживания и ремонта.
Необходимым условием для эффективного использования технических объектов и увеличения сроков их эксплуатации является также нормирование показателей надежности - разработка и обоснование нормативов для основных характеристик, регламентация процессов и предельных состояний элементов и систем, запасов надежности, скоростей изменения основных параметров и т.д. Базовым для решения этих вопросов является экономический фактор, оценивающий последствия отказов и выступающий в качестве основного критерия при оптимизации надежности. Поэтому одной из важных задач теории надежности является разработка экономи- ческих вопросов надежности. Экономические характеристики часто являются наиболее объективными при оценке эффективности функционирования многих технических объектов и их эксплуатации.
Все эти и многие другие задачи в настоящее время стоят перед теорией надежности и смежными техническими дисциплинами, причем решение некоторых из них требует лишь более квалифицированного подхода к расче- ту, проектированию, техническому обслуживанию и эксплуатации техниче- ских систем на базе научно обоснованных методов.
208
П Р И Л О ЖЕ Н И Я
Приложение IV.
Пример расчета надежности на стадии технического задания
В качестве примера для расчета показателей надежности взята полуавтоматическая линия для раскряжевки крупномерных хлыстов с обрезкой сучьев. Определение норм надежности при разработке технического задания на проектирование линий выполняется с целью обеспечения технических требований по уровню надежности согласно предъявляемым требованиям (табл.IV.1).
Принимаем: срок службы линии до списания при двухсменной работе Òà = 10 ëåò; количество капитальных ремонтов - один; срок службы до капитального ремонта - 5
ëåò; число межремонтных циклов: K = 5 ëåò/5 ëåò = 1.
Средний ресурс линии до капитального ремонта получим из выражения:
T |
= |
Òà × 365 × 24 × Êèã × Êèä × Êñ |
= |
10 × 365 × 24 × 0.7 × 0.67 × 0.83 |
= 17000, |
K |
|
||||
ð |
|
1+1 |
|
||
|
|
åÑ × K - 1 |
|
||
|
|
|
|
|
|
|
|
i=1 |
|
|
|
ãäå Êèã = 0,7 - коэффициент использования линии в течение года (численно равен от-
ношению числа рабочих дней в году к числу календарных дней); Êèã = 0,67 - коэффициент использования линии в течение суток (численно равен отношению часовой про-
должительности рабочего дня к числу часов в сутках); Êñ = 0.83 - коэффициент использования машины в течение смены (должен быть численно равен или близкой к коэффициенту технического использования, принят по ближайшему аналогу ПЛХ-З-АС).
Согласно "Временному положению об отраслевой системе повышения надежности
машин и оборудования" величина регламентированной вероятности g должна быть не менее 80%. Восьмидесяти-процентный ресурс линии до капитального ремонта
Tγ = T/Kγ ,
для нормального распределения ресурса можно также воспользоваться формулой
Tγ = T/Kγ = T(1 – uγvt),
ãäå Kγ - соотношение между средним и гамма-процентным ресурсами (прил.V); uγ- êâàí-
тиль нормального распределения, соответствующая уровню g (прил.I); vt - коэффициент вариации нормального распределения ресурса.
Выделим основные функциональные узлы и агрегаты линии: гидрооборудование 1, электрооборудование и автоматика 2, пила двухдисковая штанговая 3, транспортер для продольной шаговой подачи хлыстов 4, транспортер отходов 5, разгрузочно-расталкива- ющее устройство 6, сучкорезное устройство 7, манипулятор 8, приемный стол 9. Время на разборку и сборку основных агрегатов машин приведено в табл.IV.2.
Таблица IV.1
ТРЕБОВАНИЯ К НАДЕЖНОСТИ ЛЕСОЗАГОТОВИТЕЛЬНЫХ МАШИН НА 1990-2000 ГОДЫ.
Ï î ê à ç à ò å ë è |
|
|
Ì à ð ê è î á î ð ó ä î â à í è ÿ |
|
|
|||||
í à ä å æ í î ñ ò è |
ËÕÒ- |
ÒÒ- |
ËÒ- |
ËÏ- |
ÌÏ- |
ËÏ- |
ËÎ- |
ËÏ- |
ÏÒ- |
|
|
- 55 |
- 4Ì |
- 187 |
- 33À |
- 45 |
- 30Ã |
- 120 |
- 19Á |
- 188 |
|
80%-ный ресурс |
6000 |
6000 |
6000 |
6000 |
5000 |
4000 |
6000 |
5000 |
5000 |
|
до первого кап.ремонта |
||||||||||
8000 |
8000 |
8000 |
8000 |
7500 |
6500 |
8000 |
7000 |
7000 |
||
(ìàø.-÷àñû; êì) |
||||||||||
|
|
|
|
|
|
|
|
|
||
Ресурс после |
5000 |
5000 |
5000 |
5000 |
4000 |
3000 |
5000 |
4000 |
4000 |
|
первого кап.ремонта |
||||||||||
7000 |
7000 |
7000 |
7000 |
6000 |
5000 |
7000 |
6000 |
6000 |
||
(ìàø.-÷àñû; êì) |
||||||||||
|
|
|
|
|
|
|
|
|
||
Наработка на отказ |
80 |
80 |
75 |
75 |
70 |
70 |
70 |
70 |
70 |
|
(маш.-час; км/отказ) |
250 |
250 |
230 |
230 |
200 |
200 |
200 |
200 |
200 |
|
Удельная трудоемкость |
0,23 |
0,28 |
0,27 |
0,27 |
0,30 |
0,30 |
0,23 |
0,36 |
0,32 |
|
проф.обслуживания |
||||||||||
0,10 |
0,15 |
0,15 |
0,15 |
0,15 |
0,15 |
0,10 |
0,16 |
0,16 |
||
(÷åë.÷àñ/ìàø.÷àñ.) |
||||||||||
|
|
|
|
|
|
|
|
|
||
Удельная трудоемкость |
0,26 |
0,32 |
0,28 |
0,28 |
0,36 |
0,36 |
0,30 |
0,32 |
0,30 |
|
текущих ремонтов |
||||||||||
0,15 |
0,15 |
0,15 |
0,15 |
0,18 |
0,18 |
0,15 |
0,15 |
0,15 |
||
(÷åë.-÷àñ/ìàø.-÷àñ) |
||||||||||
|
|
|
|
|
|
|
|
|
||
Коэффициент расхода |
11 |
12 |
12 |
12 |
18 |
18 |
12 |
12 |
12 |
|
зап.частей на списочную |
||||||||||
6 |
6 |
17 |
7 |
9 |
9 |
7 |
7 |
7 |
||
машину (%%) |
||||||||||
|
|
|
|
|
|
|
|
|
209
Таблица IV.2
ОТНОСИТЕЛЬНЫЕ СУММАРНОЕ ВРЕМЯ НА РАЗБОРКУ И СБОРКУ ОСНОВНЫХ АГРЕГАТОВ МАШИН
|
Ë å ñ î ç à ã î ò î â è ò å ë ü í à ÿ ò å õ í è ê à |
Ï î ò î ÷ í û å ë è í è è |
||||||||
|
|
(классификация по мощности в л.с.) |
|
|||||||
|
|
|
|
|
|
|
||||
|
|
|
|
|
|
|
|
|
|
|
|
210 - |
150 - |
100 - |
ÒÄÒ-60 |
Автомобили |
ÒÑ-7 |
ËÏÕ- |
ÓÏÙ-Ç |
ÓÏÙ-6 |
|
|
|
|
|
|
|
|
|
|
|
|
|
- 150 |
- 100 |
- 50 |
|
100 - 70 |
70 - 50 |
ñ ÃÑÓ |
ÇÀÑ |
|
|
|
|
|
|
|
|
|
|
|
|
|
Машина (линия) в целом |
1 |
1 |
1 |
1 |
1 |
1 |
1 |
1 |
1 |
1 |
Двигатель |
0,2 |
0,3 |
0,25 |
0,45 |
0,3 |
0,3 |
- |
- |
- |
- |
Ходовая часть |
0,5 |
0,45 |
0,4 |
0,7 |
0,2 |
0,2 |
- |
- |
- |
- |
Бульдозер |
- |
0,35 |
0,5 |
- |
- |
- |
- |
- |
- |
- |
Электрооборудование |
0,1 |
0,05 |
0,05 |
0,05 |
0,15 |
0,15 |
0,85 |
0,5 |
0,25 |
0,35 |
Гидрооборудование |
0,2 |
0,1 |
0,05 |
0,1 |
0,05 |
- |
- |
0,3 |
- |
- |
Лебедка |
0,2 |
- |
- |
0,2 |
- |
- |
- |
- |
- |
0,1 |
Гидроскрепер |
- |
- |
0,05 |
- |
- |
- |
- |
- |
- |
- |
Скрепер прицепной |
- |
0,4 |
- |
- |
- |
- |
- |
- |
- |
- |
Циркулярная пила АЦ-ЗС |
- |
- |
0,3 |
- |
- |
- |
- |
0,1 |
- |
- |
Приемный стол |
- |
- |
- |
- |
- |
- |
- |
0,2 |
- |
- |
Транспортер отходов |
- |
- |
- |
- |
- |
- |
- |
0,1 |
0,05 |
0,05 |
Транспортер 20-30 м |
- |
- |
- |
- |
- |
- |
0,15 |
0,15 |
0,15 |
0,15 |
Транспортер 5-10 м |
- |
- |
- |
- |
- |
- |
- |
- |
0,05 |
0,05 |
Барабан корообдирочный |
- |
- |
- |
- |
- |
- |
- |
- |
0,3 |
0,4 |
Машина рубительная |
- |
- |
- |
- |
- |
- |
- |
- |
0,15 |
0,15 |
Пневмотранспорт 30 м |
- |
- |
- |
- |
- |
- |
- |
- |
- |
0,1 |
Загрузочное устройство |
- |
- |
- |
- |
- |
- |
0,1 |
0,1 |
0,1 |
0,1 |
Сбрасыватель бревен |
- |
- |
- |
- |
- |
- |
0,1 |
- |
- |
- |
Бревнотаска 100150 м |
- |
- |
- |
- |
- |
- |
- |
- |
0,1 |
0,1 |
Станок дровокольный КС-7 |
- |
- |
- |
- |
- |
- |
- |
- |
0,05 |
0,05 |
|
|
|
|
|
|
|
|
|
|
|
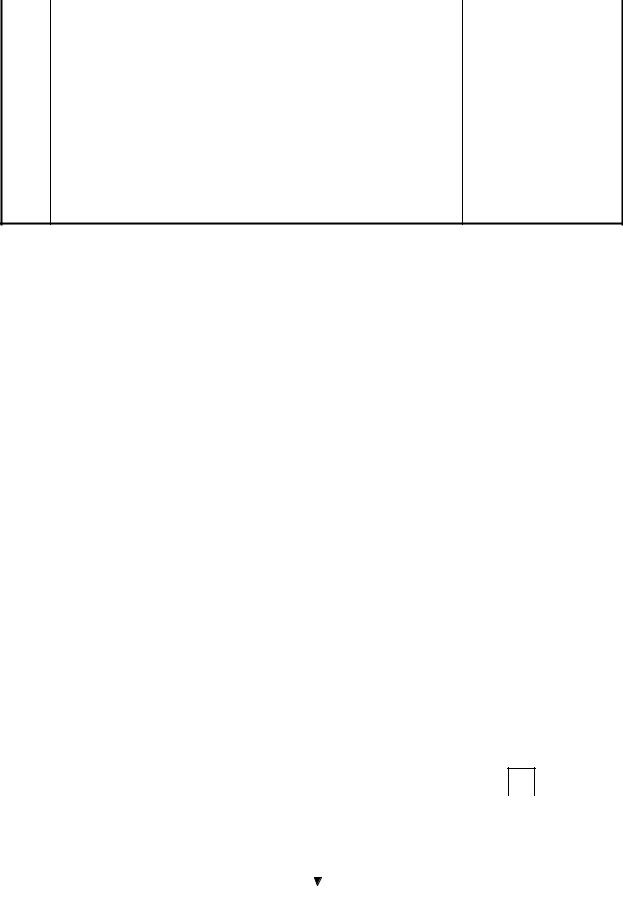
|
210 |
|
|
|
ЗАТРАТЫ ВРЕМЕНИ НА ОБОРУДОВАНИЕ |
Таблица IV.3 |
|
|
|
||
¹¹ |
Í à è ì å í î â à í è å ó ç ë î â |
Время на переборку |
|
ïï |
узлов линии |
||
|
|||
|
|
|
|
1. |
Гидрооборудование |
tp1 = 0,8 |
|
2. |
Электрооборудование и автоматика |
tp2 = 0,3 |
|
3. |
Пила двухдисковая штанговая |
tp3 = 0,3 |
|
4. |
Транспортер для продольной шаговой подачи хлыстов |
tp4 = 0,3 |
|
5. |
Транспортер отходов |
tp5 = 0,2 |
|
6. |
ÐÐÓ |
tp6 = 0,1 |
|
7. |
Сучкорезное устройство |
tp7 = 0,1 |
|
8. |
Манипулятор |
tp8 = 0,1 |
|
9. |
приемный стол |
tp9 = 0,1 |
После анализа конструктивных особенностей линии составляем табл.IV.3 затрат времени на переборку основных узлов и агрегатов относительно суммарного времени, которое требуется для демонтажа и монтажа всей линии в целом, это время принимаем
за единицу (tp = 1).
Описываем предельные состояния, при которых возникает необходимость проведения ремонтных работ, равноценных по продолжительности капитальному ремонту всей линии в целом. Капитальный ремонт линии определяется необходимостью в капитальном ремонте (полном демонтажа и монтажа) следующих групп узлов:
1 группа - гидрооборудование 1, транспортер отходов 5 и разгрузочно-растаскиваю- щее устройство 6.
2 группа - либо электрооборудование и автоматика 2, пила двухдисковая штанговая 3, транспортер для продольной шаговой подачи хлыстов 4, сучкорезное устройство 7, манипулятор 8 и приемный стол 9.
По данному описанию предельных состояний составляется структурная схема линии (рис.IV.1). Стрелка в структурной схеме указывает на узел или группу узлов, которые в расчете общей вероятности безремонтной работы не участвуют, ввиду малого
значения tpi. Двойные параллельные связи между некоторыми узлами говорят о том, что каждый из этих узлов может быть заменен или отремонтирован без замены другого узла.
В соответствии со структурной схемой и обозначениями отдельных звеньев записывается условие обеспечения вероятности работы линии без капитального ремонта на протяжении установленного гамма-ресурса.
Ð(Òê) = p1[1-(1-p2)(1-p3)(1-p4)] = 0,8[1-(1-0,9)(1-0,8)(1-0,8)] = 0,8×0,996=0,787.
Это значение вероятности практически совпадает с заданным.
При этом для расчетов на стадии проектирования классификация факторов, определяющих вид закона распределения ресурса и ориентировочные значения коэффициентов вариации ресурсов агрегатов и узлов, приняты в соответствии с табл.6.3 (см.гл.6).
Для агрегатов и узлов электрооборудования закон распределения ресурса следует считать экспоненциальным (Э) с коэффициентом вариации равным 1.0.
Показатели надежности комплектующих изделий и базовых машин согласовываться с соответствующими показателями надежности проектируемой машины и с принятой системой планово-предупредительных ремонтов. Показатели надежности комплектующих изделий содержатся в стандартах или в технических условиях на поставку.
Дальнейшее уточнение общей для линии вероятности работы без капитального ремонта производится на последую-
щих стадиях проектирования. |
|
|
|
|
|
|
|
|
|
|
|
|
|
2 |
|
|
|
|
|||
|
|
|
|
|
|
|
|
|
|
|
|
|
|
|
|
|
|||||
Èç |
структурной |
схемы |
|
|
|
|
1 |
|
|
|
|
|
|
|
|
|
|
|
|
|
|
|
|
|
|
|
|
|
|
|
|
|
|
|
|
|
|
|
|||||
видно, что ресурс гидрообо- |
|
|
|
|
|
|
|
|
|
|
|
|
|
|
|
|
|
|
|
||
|
|
|
|
|
|
|
|
|
|
|
|
|
|
3 |
|
|
|
|
|||
рудования является |
опреде- |
|
|
|
|
|
|
|
|
|
|
|
|
|
|
|
|
|
|
||
|
|
|
|
|
|
|
|
|
|
|
|
|
|
|
|
|
|||||
ляющим |
фактором |
ресурса |
|
|
|
|
|
|
|
|
|
|
|
|
|
|
|
|
|
|
|
|
|
|
|
|
|
|
|
|
|
|
|
|
|
|
|
|
|
|
|||
всей линии, поэтому прини- |
|
|
|
|
|
|
|
|
|
|
|
|
|
|
|
|
|
|
|||
|
|
|
|
|
|
|
|
|
|
|
|
|
4 |
|
|
|
|
||||
маем закон распределения и |
|
|
|
|
|
|
|
|
|
|
|
|
|
|
|
|
|
||||
коэффициент вариации ре- |
|
5 |
|
|
|
|
6 |
|
|
|
|
|
|
|
|
|
|
|
|||
|
|
|
|
|
|
|
|
|
|
|
|
|
|
||||||||
|
|
|
|
|
|
|
|
|
|
|
|
||||||||||
сурса линии и гидрообору- |
|
|
|
|
|
|
|
|
|
7 |
|
8 |
|
9 |
|
|
|||||
|
|
|
|
|
|
|
|
|
|
|
|
|
|||||||||
|
|
|
|
|
|
|
|
|
|
|
|
|
|
|
|||||||
|
|
|
|
|
|
|
|
|
|
||||||||||||
дования одинаковыми. |
|
|
|
|
|
|
|
|
|
|
|
|
|
|
|
|
|
|
|||
|
|
Рис.IV.1 Структурная схема линии |
|
|
|
||||||||||||||||
|
|
|
|
|
|
|
|
|