
u-lectures сопромат
.pdf71
Влияние радиоактивного облучения
Влияние этого фактора на материал конструкции приводит к увеличению прочности и уменьшению характеристик их пластичности.
Ползучесть материалов и релаксация напряжений
Способность материалов деформироваться во времени при действии постоянных нагрузок называется ползучестью.
Явление ползучести присуще таким материалам, как бетон, кирпич, полимеры и т.п. Металлы также обнаруживают это свойство, которое становится особенно заметным при высокой температуре, а в цветных металлах (свинце, меди и т. п.) – даже при комнатной.
Фактор ползучести имеет существенное значение для работы конструкций. Например, напряжения в арматуре железобетонных изделий могут в процессе ползучести увеличиться в 2 – 2,5 раза, а перемещения в 3 – 4. Известны случаи, когда стальные котельные трубы разрушались под действием внутреннего давления вследствие ползучести материала.
Частным проявлением ползучести является рост необратимых деформаций
при постоянном напряжении. Это явление носит название последействия. На-
глядной иллюстрацией последействия может служить наблюдаемое увеличе-
ние размеров диска и лопаток газовой турбины, находящихся под воздействи-
ем больших центробежных сил и высоких температур. Это увеличение размеров необратимо и проявляется обычно после многих часов работы двигателя. Другим частным проявлением свойств ползучести является релаксация – самопроизвольное изменение во времени напряжений при неизменной деформации. Релаксацию можно наблюдать, в частности, на примере ослабления затяжки болтовых соединений, работающих в условиях высоких температур.
Ослабление плотности болтового соединения фланцев газопровода или ци-
линдра высокого давления паровой турбины может привести к утечке газа или пара, если периодически не возобновлять затяжку болтового соединения.
Предел длительной прочности и предел ползучести
Основными механическими характеристиками материала в условиях ползучести являются предел длительной прочности и предел ползучести.
Пределом длительной прочности называется отношение нагрузки, при кото-
рой происходит разрушение растянутого образца через заданный промежуток времени, к первоначальной площади сечения.
Таким образом, предел длительной прочности зависит от заданного проме-
жутка времени до момента разрушения. Последний выбирается равным сроку службы детали и изменяется в пределах от десятков часов до сотен тысяч часов. Соответственно столь широкому диапазону изменения времени меняется
72
и предел длительной прочности. С увеличением времени он, естественно, па-
дает.
Пределом ползучести называется напряжение, при котором пластическая деформация за заданный промежуток времени достигает заданной величины. Как видим, для определения предела ползучести необходимо задать интервал времени (который определяется сроком службы детали) и интервал допустимых деформаций (который определяется условиями эксплуатации детали). Пределы длительной прочности и ползучести сильно зависят от температуры. С увеличением температуры они, очевидно, уменьшаются.
Среди различных типов статических нагрузок особое место занимают периодически изменяющиеся, или циклические, нагрузки. Вопросы прочности ма-
териалов в условиях таких нагрузок составляют содержание специального
раздела сопротивления материалов и связываются с понятиями выносливо-
сти, или усталости, материала.
Анизотропные материалы
В практике наряду с изотропными материалами, которые являются основным объектом рассмотрения сопротивления материалов, имеют место и анизотропные материалы, т. е. материалы, свойства которых в различных направлениях различны. Это относится как к характеристикам упругости (модулям
упругости первого E и второго G рода), так и характеристикам предельного
состояния (предел текучести σТ , предел прочности σВ ).
Анизотропия может быть начальной (исходной), существующей до процесса
нагружения, или вторичной (деформационной), т. е. изменившейся, или зано-
во возникшей в процессе деформации. Можно выделить три типа анизотропии механических свойств: кристаллографическая, технологическая и компо-
зиционная.
Кристаллографическая анизотропия обусловлена кристаллическим строени-
ем металлов, что приводит к различию свойств, определяемых при разных углах между кристаллографическими плоскостями монокристаллов и направле-
нием действия нагрузки. Кристаллографическая анизотропия наиболее явно выражена в монокристаллах. Строго говоря, все металлы на микроскопическом уровне являются анизотропными и то, что эта анизотропия не проявля-
ется, как правило, при испытании образцов больших размеров, – результат осреднения свойств микрообъемов материала. Технологическая анизотропия обусловлена текстурой материалов, вызванной обработкой металлов и сплавов в процессе производства деталей или полуфабрикатов, такими, например, как прессование, волочение, пропитка и т. п. Композиционная анизотропия обусловлена строением композиционных материалов (сочетанием материалов матрицы и наполнителя), закладываемым в структуру в процессе их разработки и производства.
Изучая напряженное и деформированное состояния анизотропных тел, вы-
73
званные какой-либо внешней нагрузкой, принимается ряд предположений и
ограничений. Важнейшие из них сводятся к следующему:
Тело является сплошным (сплошной средой), причем напряжения на любой площадке, внутри и на поверхности являются силами, отнесенными к единице площади. Иначе говоря, моментными напряжениями, пренебрегаем, как это делается в классической теории упругости.
Связь между компонентами деформации и проекциями перемещения и их
первыми производными по координатам является линейной, т.е. рассматриваются только малые деформации.
Между компонентами напряжений и деформаций существуют линейные зависимости, т.е. материал следует обобщенному закону Гука, причем коэф-
фициенты этих линейных зависимостей могут быть как постоянными (одно-
родное тело), так и переменными функциями координат, непрерывными или прерывными (в случае неоднородного тела).
4. Начальные, т. е. существующие без внешней нагрузки, напряжения, в том
числе и температурные, не учитываются.
Таким образом, к изучению анизотропного тела подходят с позиций классиче-
ской линейной теории упругости однородного или неоднородного тела.
Изотропным в отношении упругих свойств называется тело, у которого эти
свойства (упругое сопротивление) одинаковы для всех направлений, прове-
денных через данную точку; анизотропным называется тело с упругими свойствами, вообще различными для разных направлений, проведенных через данную точку. Направления, для которых упругие свойства (упругое сопротивление) одинаковы, называют упруго-эквивалентными. У изотропного тела упруго-эквивалентными являются все направления, проведенные через данную точку, а у анизотропного — не все, а только некоторые.
В зависимости от структуры тело может быть изотропным или анизотропным
иодновременно однородным или неоднородным. Заметим еще, что в разных
средах можно различить два основных типа анизотропии: 1) прямолинейную
и2) криволинейную.
Анизотропия свойств характерна для композиционных или гетерогенных материалов.
Композиционные материалы
Анизотропия композита является конструкционной, она закладывается специально для изготовления конструкций, в которых наиболее рационально ее использовать. Возможность управления свойствами вновь создаваемых материалов, особенно хорошо реализуемая при проектировании гибридных (армированных несколькими типами наполнителей) композитов, оказывает существенное влияние на совершенствование технологического проектирования.
74
Композит представляет собой неоднородный сплошной материал, состоящий
из двух или более компонентов, среди которых можно выделить армирующие элементы, обеспечивающие необходимые механические характеристики материала, и матрицу (связующее), обеспечивающую совместную работу армирующих элементов. Механическое поведение композита определяется соотношением свойств армирующих элементов и матрицы, а также прочностью связи между ними. Эффективность и работоспособность материала зависят от
правильного выбора исходных компонентов и технологии их совмещения,
призванной обеспечить прочную связь между компонентами при сохранении их первоначальных характеристик.
В результате совмещения армирующих элементов и матрицы образуется комплекс свойств композита, не только отражающий исходные характеристики его компонентов, но и включающий свойства, которыми изолированные компоненты не обладают. Например, наличие границ раздела между армирующими элементами и матрицей существенно повышает трещиностойкость материала, и в композитах, в отличие от металлов, повышение статической прочности приводит не к снижению, а, как правило, к повышению характери-
стик вязкости разрушения. Совместная работа разнородных материалов дает
эффект, равносильный созданию нового материала, свойства которого и количественно и качественно отличаются от свойств каждого из его состав-
ляющих.
Для композиционных конструкционных материалов характерны следующие признаки:
-состав и форма компонентов материала определены заранее;
-компоненты присутствуют в количествах, обеспечивающих заданные свойства материала;
-материал является однородным в макромасштабе и неоднородным в микромасштабе (компоненты различаются по свойствам, между ними существует
явная граница раздела).
Композиционный материал состоит из матрицы и армирующего вещества.
Матрицей могут быть металлы и их сплавы, органические и неорганические полимеры, керамика и другие материалы.
Усиливающими или армирующими компонентами чаще всего являются тонкодисперсные порошкообразные частицы или волокнистые материалы раз-
личной природы: две группы композитов по армирующим компонентам: дис-
персно-упрочненные и волокнистые. Они отличаются структурой и механиз-
мом образования высокой прочности.
Композиционные материалы нашли широкое применение в конструкциях и
изделиях, когда требования по удельной прочности, жесткости и надежности довольно высоки, а их способность иметь заданные свойства в определенных направлениях дает выигрыш не только в весе, но и в технологии изготовления.
Из композитов изготавливают различные резервуары и сосуды давления, обо-
75
лочки несущих конструкций самолетов, малотоннажных судов, ракет и ваго-
нов, трубопроводы и стержни различного профиля, бытовые приборы и элементы к ним, и т.д.
В машиностроении к конструкционным композиционным материалам относятся материалы, из которых изготавливаются конструкции и детали машин, воспринимающие механические нагрузки.
Восприятие нагрузки делится по виду (растяжение, сжатие и т.д.), по характе-
ру нагружения (статическое, динамическое), по действию окружающей сре-
ды. Перечисленные факторы определяют комплекс конструктивноэксплуатационных требований, предъявляемых к конструкционным композиционным материалам. Наиболее полное представление о материале в конструкции дают показатели механических свойств.
Механические свойства оцениваются по нескольким видам показателей:
показатели свойств материалов, определяющихся вне зависимости от конструктивных особенностей и характера службы изделия - стандартные испыта-
ния образцов на растяжение, сжатие и т.д. Характеристики эти используются
для расчетов деталей машин при статических нагрузках в нормальных условиях;
показатели конструкционной прочности, характеризующие их работу в усло-
виях эксплуатации конкретного изделия - характеристики долговечности (усталостная прочность, износоустойчивость, коррозионная стойкость) и надеж-
ность материала в изделии (вязкость разрушения, энергия трещинообразования, живучесть при циклическом нагружении);
требования по технологичности - возможность обеспечивать меньшую трудоемкость при изготовлении деталей и конструкций.
Технологичность характеризуется способностью материала приобретать заданную форму при действии различных факторов (температуры, давления и
др.), подвергаться механической обработке, соединяться различными метода-
ми (сварка, склеивание и т. д.).
Различия в упругих, прочностных и других свойствах, присущие различным материалам, тесно связаны с их составом и структурой. Изменения в них отражаются на свойствах материала. Знание закономерностей, определяющих в
материале наличие тех или иных физических, механических, теплофизиче-
ских, технологических и иных свойств, позволяет рационально использовать существующие и создавать новые материалы.
Армирующими элементами композиционных материалов являются тонкие
непрерывные или короткие волокна (диаметром от 5 до 200 мкм). Армирование осуществляется либо этими волокнами, либо составленными из них нитями, жгутами, лентами и тканями с различным типом плетения.
Волокна должны удовлетворять комплексу эксплуатационных и технологических требований. К первым относятся условия по прочности, жесткости, плотности и стабильности свойств в процессе эксплуатации. Технологичность
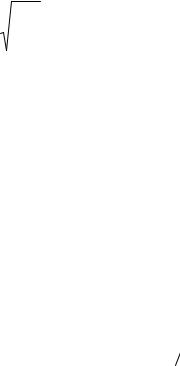
76
волокон определяет возможность создания высокопроизводительных про-
цессов изготовления изделий на их основе. Одним из важнейших требований является совместимость материала волокон с материалом матицы. Пpи этом, совместимыми считаются компоненты, на границе котоpых возможно достижение пpочной связи, близкой к пpочности матpицы при условиях, обеспечивающих сохранение исходных свойств компонентов.
Теоретическая прочность материалов σТеор возрастает с увеличением модуля
упругости Е и поверхностной энергии γ вещества и падает с увеличением расстояния между соседними атомными плоскостями а0:
σТеор = |
γE |
. |
(2.51) |
|
|||
|
a0 |
|
Следовательно, высокопрочные тела должны иметь высокие модули упруго-
сти и поверхностную энергию, и возможно большее число атомов в единице
объема. Этим требованиям удовлетворяют бериллий, бор, углерод, кремний,
азот, кислород и алюминий. Наиболее прочные материалы всегда содержат один из этих элементов, а зачастую состоят только из них.
Пи создании волокнистых композитов применяются высокопрочные стеклян-
ные, углеводные, бойные и органические волокна, металлические поволоки, а также волокна и нитевидные кристаллы ряда каpбидов, оксидов, нитpидов и
дpугих соединений. Свойства различных армирующих волокон приведены в
таблице 2.1
|
|
|
|
|
|
|
|
Таблица 2.1 |
|
Материал волокна |
|
Прочность, |
|
Модуль |
|
Плотность, |
|
Диаметр, |
|
|
|
|
|
||||||
|
|
упругости, |
|
|
|||||
|
ГПа |
|
|
г см3 |
|
мкм |
|||
|
|
|
|
ГПа |
|
|
|
|
|
Сталь |
|
2…3 |
|
200 |
|
7,8 |
|
- |
|
Стекло |
|
3,5…4,6 |
|
72…110 |
|
2,5…2,9 |
|
3…25,80 |
|
Ароматический |
|
3,8…5,5 |
|
120…185 |
|
1,43…1,47 |
|
10…12 |
|
полиамид |
|
|
|
|
|||||
|
|
|
|
|
|
|
|
|
|
Полиэтилен |
|
2…3,5 |
|
50…125 |
|
меньше 1 |
|
30…35 |
|
Углеродное |
|
3,6…7,2 |
|
300 |
|
1,8 |
|
5…10 |
|
высокопрочное |
|
|
|
|
|||||
|
|
|
|
|
|
|
|
|
|
Углеродное |
|
2,5-3,25 |
|
500-800 |
|
1,8…2,2 |
|
5…10 |
|
высокомодульное |
|
|
|
|
|||||
|
|
|
|
|
|
|
|
|
|
Оксид алюминия |
|
2,2…2,4 |
|
385…420 |
|
3,95 |
|
10…25 |
|
Карбид кремния |
|
3,1…4,0 |
|
410…450 |
|
2,7…3,4 |
|
100…140 |
|
Бор |
|
3,45 |
|
400 |
|
2,6 |
|
100…200 |
|
Матрица обеспечивает монолитность композита, фиксирует форму изделия и взаимное расположение армирующих волокон, распределяет действующие напряжения по объему материала, обеспечивая равномерную нагрузку на ее

77
волокна и перераспределение при разрушении части волокон. Материал ма-
тицы определяет метод изготовления изделий из композитов, возможность выполнения конструкций заданных габаритов и формы, параметров технологического процесса. В табл. 2.2 для примера приведены физико-механические свойства полимерных матриц, используемых при создании углепластиков.
|
|
|
|
|
|
|
|
|
|
Таблица 2.2 |
|
Параметр |
|
Полиэфир- |
|
Фенол- |
|
Эпок- |
|
Кремний- |
|
Поламид- |
|
|
|
|
|
|
|||||||
|
|
формаль- |
|
|
органичес- |
|
|||||
|
|
ные |
|
дегидные |
|
сидные |
|
кие |
|
ные |
|
|
|
|
|
|
|
|
|
|
|
||
Предел |
|
|
|
|
|
|
|
|
|
|
|
прочности |
|
30…70 |
|
40…70 |
|
50…100 |
|
25…50 |
|
90…95 |
|
при растяжении, |
|
|
|
|
|
||||||
|
|
|
|
|
|
|
|
|
|
|
|
МПа |
|
|
|
|
|
|
|
|
|
|
|
Предел |
|
|
|
|
|
|
|
|
|
|
|
прочности |
|
80…150 |
|
100…125 |
|
90…160 |
|
60…100 |
|
250…280 |
|
при сжатии, |
|
|
|
|
|
||||||
|
|
|
|
|
|
|
|
|
|
|
|
МПа |
|
|
|
|
|
|
|
|
|
|
|
Модуль упруго- |
|
2,8…3,8 |
|
7…11 |
|
2,4…4,2 |
|
6,8…10 |
|
3,2…5 |
|
сти, ГПа |
|
|
|
|
|
||||||
|
|
|
|
|
|
|
|
|
|
|
|
Плотность |
|
1,2…1,35 |
|
1,2…1,3 |
|
1,3 |
|
1,35…1,40 |
|
1,41…1,4 |
|
10−3 , кг м3 |
|
|
|
|
|
||||||
|
|
|
|
|
3 |
|
|||||
Теплостойкость, |
|
50…80 |
|
140…180 |
|
130…150 |
|
250…280 |
|
250…320 |
|
oC |
|
|
|
|
|
||||||
|
|
|
|
|
|
|
|
|
|
|
|
Относительное |
|
1,0…5,0 |
|
0,4…0,5 |
|
2…9 |
|
0,3…0,5 |
|
1…2,5 |
|
удлинение, % |
|
|
|
|
|
||||||
|
|
|
|
|
|
|
|
|
|
|
|
Объемная |
|
5…10 |
|
15…25 |
|
1…5 |
|
15…20 |
|
15…20 |
|
усадка, % |
|
|
|
|
|
||||||
|
|
|
|
|
|
|
|
|
|
|
Требования, предъявляемые к матицам разделяются на эксплуатационные и технологические. К эксплуатационным относятся требования, связанные с механическими и физико-химическими свойствами, обеспечивающими работоспособность композиции при действии различных эксплуатационных факторов.
Контрольные вопросы к разделу 2
1.Дайте определение равновесного состояния стержня, называемого простым
растяжением или сжатием.
2.Что такое принцип Сен-Венана? Дайте пояснение на конкретном примере.
3.Сформулируйте гипотезу плоских сечений Я. Бернулли.
4.Запишите дифференциальную и интегральную зависимости, связывающие нормальную силу с интенсивностью продольной распределенной нагрузки.
78
5.Как определяются напряжения в поперечных и наклонных сечениях бруса
при растяжении (сжатии)?
6.Что такое продольная и поперечная деформации стержня (определения).
7.Поясните физический смысл модуля первого рода.
8.Сформулируйте закон Гука при растяжении (сжатии), выражающий связь между напряжением и деформацией, а также закон Гука для абсолютной про-
дольной деформации.
9.Что называется коэффициентом поперечной деформации (коэффициентом Пуассона) и какие он может принимать предельные значения для конструкционных материалов?
10.Что называется допускаемым напряжением? Как оно выбирается для
хрупких и пластичных материалов?
11.Как записываются условия прочности и жесткости при растяжении (сжа-
тии) стержня?
12.Дайте определение статически определимых и неопределимых систем.
13.Что такое брус равного сопротивления?
14.Назовите характерные участки диаграммы растяжения образца из малоуглеродистой стали. Какие характерные точки различают на диаграмме растя-
жения.
15.Каким образом определяется предел текучести материала, если его диа-
грамма растяжения не имеет явно выраженной площадки текучести?
16.Как определяются характеристики пластичности материала при испыта-
ниях на растяжение?
17.Как определяется потенциальная энергия при растяжении?
18.Что такое хрупкость? Перечислите хрупкие материалы.
19.В чем состоит особенность разрушения хрупких материалов при растя-
жении? Какой вид имеет диаграмма растяжения хрупких материалов?
20.Какой вид имеют диаграммы сжатия пластичных и хрупких материалов?
21.Каков характер разрушения при испытании на сжатие образцов из мало-
углеродистой стали, чугуна?
22.Указать различие между диаграммами сжатия древесины вдоль и поперек волокон.
23.Какой материал называется анизотропным? Приведите примеры анизотропных материалов.
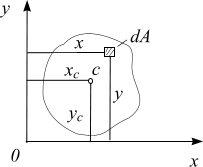
79
Раздел 3 Геометрические характеристики плоских сечений
Тема 3.1 Основные определения и общие свойства геометрических характеристик
Центр тяжести сечения. Статические моменты сечения
При расчетах на прочность, жесткость и устойчивость используются геометрические характеристики поперечного сечения бруса: площадь, осевые и по-
лярный моменты инерции, осевые и полярный моменты сопротивления. Кро-
ме того, при расчетах касательных напряжений при изгибе используются
статические моменты сечения. Статические моменты и центробежные мо-
менты инерции играют также вспомогательную роль при определении перечисленных выше геометрических характеристик.
Рассмотрим произвольную фигуру (поперечное сечение бруса), связанную с координатными осями Оx и Оy (рис. 3.1).
Рис. 3.1.
Выделим элемент площади dA с координатами х, у. Площадь сечения равна
сумме элементарных площадок
A = ∫dA |
(3.1) |
A |
|
Статическим моментом сечения относительно данной оси называется взя-
тая по всей его площади A сумма (интеграл) произведений элементарных площадок dA на их расстояния до этой оси.
Статические моменты площади сечения относительно осей x и y определяются по формулам:
S y = ∫xdA, |
Sx = ∫ ydA. |
(3.2) |
A |
A |
|
Статические моменты выражаются в см3, м3. В зависимости от знаков коор-
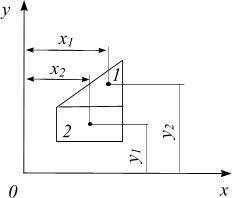
80
динат они могут принимать положительные значения, отрицательные и рав-
ные нулю.
Пусть xc и yc – координаты центра тяжести фигуры (рис.3.1). На основании теоремы Вариньона (из курса теоретической механики) можно записать:
S y = Axc , Sx = Ayc , |
(3.3) |
где А – площадь фигуры.
Оси, проходящие через центр тяжести, называется центральными. В этом случае xc = 0 и yc = 0, тогда Sx = Sy = 0 . Следовательно, статические мо-
менты относительно центральных осей равны нулю.
Если сечение имеет сложную форму и его можно разбить на простейшие составные части (прямоугольники, треугольники и т.п.), площади и положение центров тяжести которых известны, то статический момент площади всего
сечения относительно любой оси (рис. 3.2) равен алгебраической сумме ста-
тических моментов сечения составляющих фигур относительно той же оси:
Sx = A1 y1 + A2 y2 |
+...An yn = ∑Sxi ; |
(3.4) |
|
S y = A1x1 + A2 x2 +...An xn = ∑S yi ; |
|||
|
Рис.3.2
По формулам (3.3) и (3.4) легко найти координаты центра тяжести сложной фигуры:
yc = |
S |
x |
|
∑S x |
|
|
||
|
= |
i , |
|
|||||
A |
(3.5) |
|||||||
|
|
|
∑ Ai |
|||||
xc = |
|
S y |
= |
∑S y |
i . |
|
||
|
A |
|
|
|||||
|
|
|
∑ Ai |
|
Для симметричных сечений определение положения центра тяжести значительно упрощается. При наличии двух или более осей симметрии (прямо-