
u-lectures сопромат
.pdf211
Для получения объективных характеристик материала необходимо соблюдать условие однородности напряженного состояния, т. е. необходимо обеспе-
чить постоянство напряженного состояния для всех точек испытуемого образца. Это условие соблюдается, например, при растяжении, частично при сжатии короткого образца и при кручении тонкостенной трубки. Изменение свойств материала в этих испытаниях происходит одновременно во всем объеме образца и легко поддается количественной оценке. При кручении сплошных образцов, а также и при изгибе напряженное состояние является неоднородным. Качественные изменения свойств материала в отдельных точках не влекут за собой заметных изменений в характеристиках образца.
Требование однородности напряженного состояния накладывает серьезные ограничения на результаты многих видов испытаний. В частности, до сих пор не удается провести объективные испытания в условиях однородного всестороннего растяжения. Это напряженное состояние можно создать пока только в отдельных точках образца, например в центре сплошного шара, быстро нагреваемого извне.
Одним из видов механических испытаний являются технологические пробы, дающие не объективные, а только сравнительные характеристики свойств материала при строго регламентированных условиях испытания. Сюда относятся испытания на твердость, на ударную вязкость и некоторые другие. В некоторой мере к технологическим пробам могут быть отнесены также испытания на усталостную прочность.
Кроме статических испытаний часто возникает необходимость проведения и динамических испытаний. Например, весьма распространены испытания приборов, работающих в условиях вибраций. Эти испытания проводят на специальных вибрационных столах при различных значениях частот и амплитуд. При таких испытаниях деформации и напряжения в вибрирующих деталях прибора обычно не замеряют. О прочности отдельных узлов судят только в случае их разрушения. В ряде случаев динамические испытания ведут с осциллографированием (записью) быстро изменяющихся деформаций, возникающих в наиболее опасных узлах.
Существующие в настоящее время способы экспериментального исследования напряженных конструкций сводятся, так или иначе, к прямому определению деформаций, возникающих в испытуемом объекте. Напряжения определяют косвенно через деформации на основе закона Гука. В случае пластических деформаций напряжения при испытаниях конструкций обычно не определяют, а устанавливают только разрушающую нагрузку или то значение силы, при котором наблюдаются признаки возникновения пластических деформаций.
Для замера деформаций применяют различные методы: определение деформаций при помощи приборов (тензометров) с механическим и электрическим

212
принципами замера; оптический и рентгенографический методы, метод муаровых полос, метод лаковых покрытий.
Подробно остановимся на определении деформаций при помощи механических и электрических тензометров.
Определение деформаций при помощи механических тензометров
Принцип работы механического тензометра основан на замере расстояния между какими-либо двумя точками образца до и после нагружения. Первоначальное расстояние между двумя точками носит название базы тензометра l . Отношение приращения базы l к l дает значение среднего удлинения по направлению установки тензометра. Если деформированное состояние однородно, то в результате замера определяют точное значение искомой деформации, как это имеет место, например, при растяжении стержня (рис. 6.9, а). В случае, если деформация вдоль базы изменяется, то замеренное среднее значение ее будет тем ближе к местному истинному, чем меньше база тензомет-
ра (рис. 6.9, б).
Рис. 6.9
При испытании материалов на растяжение, когда однородность деформации обеспечена, база ограничивается размерами образца. Обычно в этом случае база l имеет значения 50, 100, 150 и 200 мм.
При испытании конструкций увеличение базы ограничено погрешностью, связанной с неоднородностью деформаций, а ее уменьшение определяется потерей точности вследствие инструментальных погрешностей. Как правило, база механических тензометров, применяемых при испытании конструкций, лежит в пределах 2–20 мм.
Для точных замеров упругих удлинений при определении модуля упругости материала широко используется тензометр Мартенса с оптическим рычагом.

213
Тензометр состоит из жесткой планки, прижимаемой к образцу при помощи струбцины. Верхний нож остается планки неподвижным. В качестве второго ножа используется каленая призма, имеющая ромбовидное сечение. Длина диагонали призмы равна a . С призмой жестко связано зеркальце. На расстоянии L от зеркальца неподвижно устанавливается шкала. При удлинении образца зеркальце поворачивается, и наблюдатель через трубу производит отсчет по отраженной шкале. Увеличение, даваемое прибором, определяется отношением разности показаний по шкале в миллиметрах к значению l , измеренному также в миллиметрах.
Угол поворота зеркальца α = la . Разность отсчетов по шкале до и после на-
гружения в силу малости α равна h = L 2α. Исключая угол α, находим коэффициент увеличения прибора
i = hl = 2aL .
Обычно у тензометра Мартенса шкалу (размер L ) выбирают так, что i ≈ 500 . Для исключения погрешностей, связанных с внецентренным растяжением образца и возможным его изгибом, практикуют установку сразу двух тензометров. Осреднение показаний двух приборов исключает влияние изгиба.
Сдвоенный тензометр Мартенса неудобен тем, что требует сравнительно кропотливой работы при установке. Менее точными, но более удобными в употреблении являются хорошо зарекомендовавшие себя большебазные тензометры МИЛ и Бояршинова.
Тензометр МИЛ имеет базу 100 мм и является шарнирно-рычажным. Это – сдвоенный тензометр, устанавливаемый на образце при помощи пружинного зажима. Нижняя опора является неподвижной, верхняя же представляет одно целое с рычагом. Перемещение нижнего конца этого рычага передается планке, а от нее – стрелке. При помощи винта имеется возможность приводить стрелку перед экспериментом в нулевое положение. Если деформации образца велики настолько, что стрелка выходит за пределы шкалы, тем же винтом можно вернуть ее в исходное положение и во время опыта. Увеличение тензометра МИЛ равно 500.
В тензометре Бояршинова вместо механических шарниров применен упругий шарнир, состоящий из двух плоских пружин. Алюминиевые детали поворачиваются при растяжении образца относительно точки пересечения пружин. Упругий шарнир обладает тем преимуществом, что не имеет зоны застоя, которая характерна для обычных механических шарниров вследствие наличия сухого трения. Тензометр имеет два стальных каленых ножа, которыми он прижимается к образцу при помощи винтов. В момент установки прибор арретируется (запирается) при помощи штифта, соединяющего наглухо детали. Отсчет деформаций ведется при помощи индикаторов.
214
Тензометром Бояршинова можно производить отсчеты без перестановки шкалы в пределах деформаций, достигающих 4 %. Таким широким диапазоном измерения другие тензометры не обладают. База тензометра l = 50 мм, увеличение около 500.
При замере деформации образцов, испытываемых на растяжение и сжатие, отлично зарекомендовал себя тензометр Лихарева с «гидравлическим рычагом». Основными частями этого тензометра являются металлические гофрированные коробки (сильфоны), образующие замкнутую полость, сообщающуюся с капилляром. Полость между сильфонами заполнена жидкостью. При удлинении образца объем полости увеличивается и уровень жидкости в капилляре понижается на h .
Из условия неизменности объема жидкости, очевидно,
(πR2 − πr2 ) l = hF ,
где R , r – средний радиус большого и малого сильфона, соответственно; F – площадь сечения капилляра. Таким образом, увеличение тензометра равно
π(R2 − r2 )F и зависит от размеров выбранных сильфонов и капилляра.
Обычно коэффициент увеличения прибора около 2000.
Тензометр на образце устанавливают с помощью винтов. Для изменения уровня жидкости в капилляре и для установки прибора на нуль служит винт. Наименьшая база прибора около 20 мм.
Среди механических тензометров, применяемых не только при механических испытаниях материалов, но и при испытаниях конструкций, имеющих сравнительно малую базу, наиболее широкое распространенно в лабораторной практике получил шарнирнорычажный тензометр Гугенбергера с базой 20 мм и увеличением около 1000.
Механические тензометры с меньшей базой не имеют широкого распространения и являются уникальными. Попытки отдельных исследователей внедрить такие тензометры в лабораторную практику успеха не имели, поскольку при испытании материалов более предпочтительными являются тензометры с большой базой, а при испытании конструкций тензометры заменяют проволочными датчиками сопротивления.
Применение датчиков сопротивления
При экспериментальных исследованиях напряженного состояния конструкций, а также в качестве преобразователей деформаций в различных измерительных устройствах широко применяются тензорезисторы.
215
Широкое распространение тензорезисторов объясняется тем, что они малоинерционны, позволяют дистанционно и во многих точках проводить измерения; способ установки их на исследуемую деталь не требует сложных приспособлений и не искажает поле деформаций исследуемой детали. Малые размеры и масса тензорезисторов позволяют размещать их в малодоступных местах и устанавливать на детали в период сборки конструкции. Тензорезисторы используют с современными многоканальными измерительноинформационными системами.
Научно-технический прогресс в машиностроении и других областях промышленности привел к существенному усложнению задач и условий измерения деформаций конструкций: рабочие температуры от -269 до 1100 °С; длительные статические, динамические и ударные нагружения; измерение упругопластических деформаций в концентраторах напряжения и др. Тензометрирование натурных конструкций привело к необходимости повышения надежности и простоты установки тензорезисторов. Развитие динамометров и датчиков давления тензорезисторного типа потребовало создания тензорезисторов и методов их применения, обеспечивающих измерительным устройствам погрешность измерения до сотых долей процента.
Для решения перечисленных задач разрабатываются и применяются различные типы приклеиваемых и привариваемых тензорезисторов (проволочные, фольговые и полупроводниковые).
Принцип измерения деформаций с помощью тензорезисторов состоит в том, что при деформации изменяется его активное сопротивление. Эффект изменения удельного сопротивления металлического проводника под действием всестороннего сжатия (гидростатического давления) был обнаружен в 1856 г. лордом Кельвином и в 1881 г. О. Д. Хвольсоном. Однако пионерами применения этого эффекта для измерения деформаций являются Е. Е. Симмонс (Калифорнийский технологический институт) и Л. С. Руже (Массачусетский технологический институт), которые в 1938 г. изготовили и применили первые образцы приклеиваемого тензорезистора, являющегося прототипом широко распространенных во всем мире тензорезисторов различного назначения.
Внашей стране тензорезисторы начали применяться в 40-х годах нашего столетия. Они практически полностью заменили механические тензометры, открыли новые возможности в исследовании прочности различных машиностроительных конструкций. Применение тензорезисторов в качестве вторичных преобразователей различных измерительных устройств обеспечивало последним необходимую точность и надежность при длительных испытаниях.
Всовременном виде тензорезистор конструктивно представляет собой чувствительный элемент из тензочувствительного материала (проволоки, фольги и др.), закрепленный с помощью связующего (клея, цемента) на исследуемой детали. Для присоединения чувствительного элемента в электрическую цепь в тензорезисторе имеются выводные проводники.
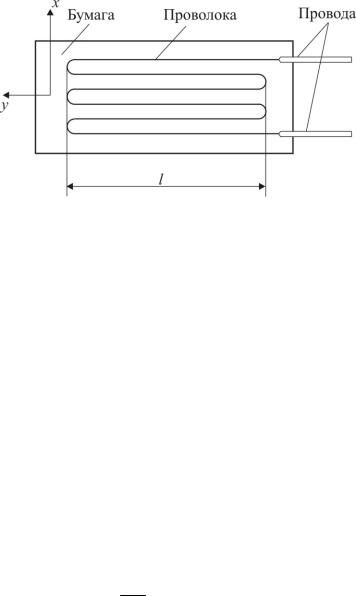
216
Некоторые конструкции тензорезисторов для удобства установки имеют подложку, расположенную между чувствительным элементом и исследуемой деталью, а также защитный элемент, расположенный поверх чувствительного элемента.
В технике испытания конструкций широкое распространение получили проволочные датчики сопротивления.
Проволочный датчик представляет собой наклеенную на полоску бумаги тонкую зигзагообразно уложенную проволочку (рис. 6.10) толщиной 0,015– 0,030 мм. К концам проволочки сваркой либо пайкой присоединяются провода.
Рис. 6.10
Датчик наклеивают на поверхность исследуемой детали так, чтобы размер базы l совпадал с направлением, в котором желательно замерить деформацию. При деформации объекта проволочка удлиняется (укорачивается) и сопротивление изменяется.
Опыт показывает, что относительное изменение омического сопротивления проволоки RR пропорционально ее удлинению, R
R = γ0ε где γ0 – коэф-
фициент тензочувствительности – безразмерная величина, зависящая от физических свойств материала. Для материалов, применяемых в датчиках сопротивления, значение γ0 колеблется в пределах 2–3,5. Для константана, на-
пример, γ0 =2,0–2,1, для нихрома 2,1–2,3, для элинвара 3,2–3,5.
У проволочного датчика вследствие закруглений на концах петель обнаруживается чувствительность не только к продольным, но и к поперечным деформациям, и
RR = γεx + δεy ,
217
где εx , εy – удлинения в направлениях осей x и y (рис. 6.10), γ и δ – коэф-
фициенты продольной и поперечной тензочувствительности датчика, определяемые путем тарировки.
Значение γ вследствие наличия закруглений на концах петель оказывается несколько меньше коэффициента тензочувствительности проволоки γ0 . По мере увеличения базы l разница между γ и γ0 уменьшается и для обычно
применяемых датчиков с базой l = 20 мм оказывается ничтожно малой. Того же порядка малую величину представляет собой и коэффициент δ. Для датчиков, имеющих малую базу (l < 5 мм), значение δ соизмеримо с γ, и при
подсчете напряжений коэффициент поперечной тензочувствительности следует принимать во внимание.
При исследовании напряженного состояния в элементах сложной конструкции часто возникает необходимость делить не только значение, но и направление главных напряжений. В таком случае практикуют установку в исследуемой области сразу трех датчиков в направлениях, составляющих углы 45° (рис. 6.11), так называемой розетки датчиков. По трем замеренным удлинениям могут быть без труда определены главные удлинения и угол, определяющий положение главных осей. Делают это следующим образом: положим, заданы деформации по главным осям x и y . Абсолютное приращение длины AB , равно
∂∂us ds cosϕ + ∂∂vs ds sin ϕ,
где u и v – перемещения по осям x и y . Относительное удлинение вдоль оси I составляет
εI = ∂∂us cosϕ + ∂∂vs sin ϕ
или
εI = ∂∂ux cos2 ϕ + ∂∂yv sin2 ϕ,
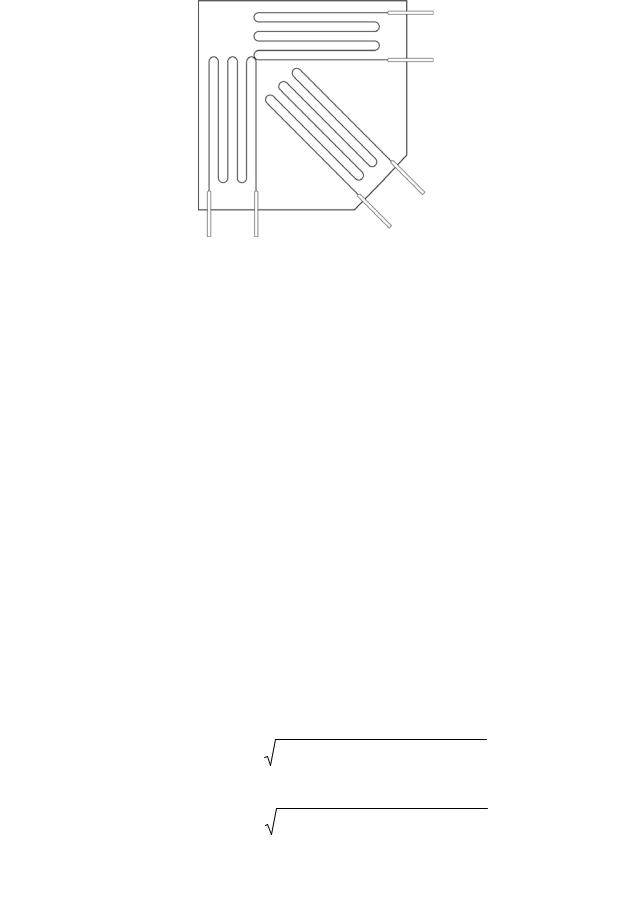
218
Рис. 6.11
откуда
εI = εx cos2 ϕ + εy sin2 ϕ.
Для трех осей, совпадающих с осями датчиков в розетке, получим соответственно
εI = εx cos2 ϕ + εy sin2 ϕ;
εII = εx cos2 (ϕ + 450 )+ εy sin2 (ϕ + 450 );
εIII = εx cos2 (ϕ + 900 )+ εy sin2 (ϕ + 900 ),
Откуда после несложных преобразований находим
|
|
|
tg2ϕ = εI − 2εII + εIII ; |
|||||||
|
|
|
|
|
ε |
I |
− ε |
III |
||
|
|
|
|
|
|
|
|
|||
εx = |
εI + εIII |
+ |
1 |
(εI − εIII )2 |
+ (εI − 2εII + εIII )2 ; |
|||||
2 |
2 |
|||||||||
|
|
|
|
|
|
|
|
|||
εy = |
εI − εIII |
+ |
1 |
(εI − εIII )2 |
+ (εI − 2εII + εIII )2 . |
|||||
|
2 |
|||||||||
|
2 |
|
|
|
|
|
|
|
Таким образом, в общем случае получены выражения для определения значения и направления главных деформаций.
219
Главные деформации с равным успехом могут быть найдены и при помощи трех механических тензометров. В некоторых случаях практикуется определение главных осей при помощи лаковых покрытий с последующей установкой тензометров по главным направлениям.
В современной технике эксперимента датчики сопротивления используют не только для замера деформаций. Во многих силоизмерительных устройствах их используют как чувствительные элементы, реагирующие на изменение внешних нагрузок. Для замера усилий датчики сопротивления наклеивают на деформируемый упругий элемент (стержень, вал), и по изменению сопротивления датчика судят о действующем усилии. Такой способ удобен тем, что позволяет весьма просто осуществить дистанционный замер, без введения сложных дополнительных устройств.
При статических испытаниях датчик, наклеенный на поверхность исследуемой детали, включают в измерительный прибор по мостовой схеме с отсчетом показаний по гальванометру. Одно из четырех сопротивлений моста, например R1 , представляет собой сопротивление датчика. Остальные сопротив-
ления подбираю так, чтобы при отсутствии удлинений детали (до начала опыта) мост был сбалансирован и сила тока в гальванометре iГ равнялась бы
нулю. Протекающий через гальванометр ток будет пропорционален изменению сопротивления датчика и, следовательно, замеряемой деформации. Основной погрешностью датчиков сопротивления является температурная погрешность. При изменении температуры сопротивление датчика меняется весьма заметно. Например, для константанового датчика, наклеенного на поверхность стальной детали, при изменении температуры на 1° омическое сопротивление меняется так же, как при изменении напряжения в стальном образце, на 0,7 МПа. С тем чтобы компенсировать температурную погрешность, датчик R4 в мостовой схеме помещают без приклейки на датчике R1 и закры-
вают сверху теплоизолирующим материалом, например тонкой фетровой полоской. Температура обоих датчиков оказывается при этом одинаковой. Тогда одинаковым будет и температурное изменение сопротивлений указанных датчиков. Балансировка моста, следовательно, меняться не будет.
Когда ведется исследование напряженного состояния сложной конструкции, имеется большое количество датчиков, с которых необходимо снять показания. Гальванометр и сопротивления R2 и R3 остаются при этом общими, а
пары сопротивлений R1 , R4 каждой исследуемой точки включают в схему
поочередно для снятия показаний. Чтобы избежать погрешностей из-за изменения напряжения питания непосредственно перед каждым отсчетом проводить балансировку моста при помощи переменного сопротивления.
Описанный способ замера пригоден, только при статическом изменении нагрузки. При быстро протекающих процессах вводят специальную регистрирующую аппаратуру. Для записи деформаций применяют осциллографы, а в схему включают усилитель.
220
Тема 6.3 Теории прочности
Хрупкое и пластичное разрушение
В зависимости от величины характеристик прочности ( σт , σв ) и пластичности
δ, ψ, определяющих механические свойства, материалы делятся на пластичные и хрупкие. В зависимости от условий нагружения и испытаний один и тот же материал может находиться в различных механических состояниях: упругом, упруго-пластическом, пластическом и в состоянии разрушения. Предельное состояние материала как состояние разрушения может реализоваться как в пластичных материалах, так и в хрупких. Для пластичных материалов характерна следующая последовательность смены механических состояний:
-упругая стадия деформирования;
-пластическая стадия (накопление повреждений, пластическое
течение);
-стадия разрушения (накопление повреждений и образование микротрещин; развитие магистральной трещины до разрушения по механизму среза).
Для материалов, находящихся в хрупких состояниях, вторая стадия исключается, т.к. пластические деформации ограничены по величине и существенно локализованы, а разрушение происходит хрупко после развития магистраль-
ной трещины по механизму отрыва.
Переход материала от упругой стадии деформирования к пластической опи-
сывается критериями пластичности, а от упругого деформирования к разрушению - критериями разрушения.
Понятие о предельном состоянии материала
В общем случае при объемном напряженном состоянии (σ1 ≥ σ2 ≥ σ3 ) опасное предельное состояние материала возникает, когда некоторая функция глав-
ных напряжений F (σ1,σ2 ,σ3 ) достигнет своего предельного значения: |
|
F (σ1,σ2 ,σ3 ) = C , |
(6.30) |
где C - критерий предельного состояния.
Уравнение (6.30) в зависимости от природы материала (пластичный, хрупкий) характеризует:
-начало пластического течения, тогда C является критерием пластичности (текучести);
-момент разрушения и C являются критерием разрушения.