
- •1. Рабочая программа
- •1.1. Пояснительная записка
- •1.2. Тематический план дисциплины “Менеджмент”
- •1.3. Содержание программы (основные дидактические единицы)
- •1.4. Рекомендуемая литература
- •2. Конспект лекций
- •Раздел 1. Общий менеджмент
- •Менеджмент как вид деятельности человека
- •История становления менеджмента
- •Место и роль менеджера в производстве
- •Закономерности управления
- •Контрольные вопросы
- •Принципы управления
- •Инфраструктура менеджмента
- •Техника и технология управления
- •Контрольные вопросы
- •Системный подход к анализу организации управления
- •Виды организационных структур
- •Состав функций управления
- •Делегирование полномочий
- •Контрольные вопросы
- •Лекция 4. Проектирование организационных структур
- •Управление социально-экономическими системами (организациями)
- •Последовательность построения организационной структуры
- •Разработка Положений о структурных подразделениях и Должностных инструкций
- •Контрольные вопросы
- •Структура и содержание “дерева целей”
- •Управление по целям и миссия организации
- •Контрольные вопросы
- •Общие сведения о решениях
- •Факторы, влияющие на процесс принятия решений
- •Научные подходы к принятию сложных решений
- •Контрольные вопросы
- •Графические модели для принятия решений
- •Экономико-математические модели принятия сложных решений
- •Методы экспертных оценок
- •Контрольные вопросы
- •Общие сведения о планах
- •Элементы и параметры сетевых моделей
- •Правила построения сетевой модели
- •Контрольные вопросы
- •Оптимизация сетевой модели
- •Контрольные вопросы
- •Время в деятельности менеджера
- •Теоретические основы ТМИ
- •Контрольные вопросы
- •Раздел 2. Инновационный менеджмент
- •Тема 7. Инновации как объект менеджмента
- •Классификация инновационных процессов и нововведений
- •Сочетание жизненных циклов спроса, технологии и товара
- •Процесс формирования инноваций
- •Контрольные вопросы
- •Структура бизнес-плана
- •Содержание бизнес-плана
- •Контрольные вопросы
- •Раздел 3. Стратегический менеджмент
- •Общие понятия
- •Анализ внешней и внутренней среды организации
- •Контрольные вопросы
- •Методы стратегического анализа
- •Разновидности стратегий организации
- •Структура стратегического плана
- •Состав основных разделов Project Expert
- •Процедуры в системе Project Expert-5
- •Контрольные вопросы
- •Раздел 4. Производственный менеджмент
- •Типы производств
- •Календарное планирование
- •Организация диспетчерской службы и контроля качества
- •Контрольные вопросы
- •Показатели для оценки трудовых процессов
- •Классификация затрат рабочего времени
- •Контрольные вопросы
- •Строительство как универсальный представитель производства
- •Этапы создания строительного объекта
- •Порядок разработки смет
- •Составление проекта производства работ
- •Контрольные вопросы
- •Раздел 5. Управление персоналом
- •Мотивация
- •Работа с кадрами
- •Процесс межличностных коммуникаций
- •Контрольные вопросы
- •Лидерство и влияние
- •Самоменеджмент
- •Контрольные вопросы
- •3. Методические указания по дисциплине
- •3.1. Общие требования
- •3.2. План прохождения дисциплины "Менеджмент" на третьем курсе очного отделения
- •4. Контроль знаний студентов
- •4.1. Вопросы к выходному контролю
- •4.3. Наименование и содержание практических занятий
- •4.5. Рекомендации по подготовке к зачету и экзамену
- •4.6. Контрольные вопросы при компьютерном тестировании
- •7. Глоссарий
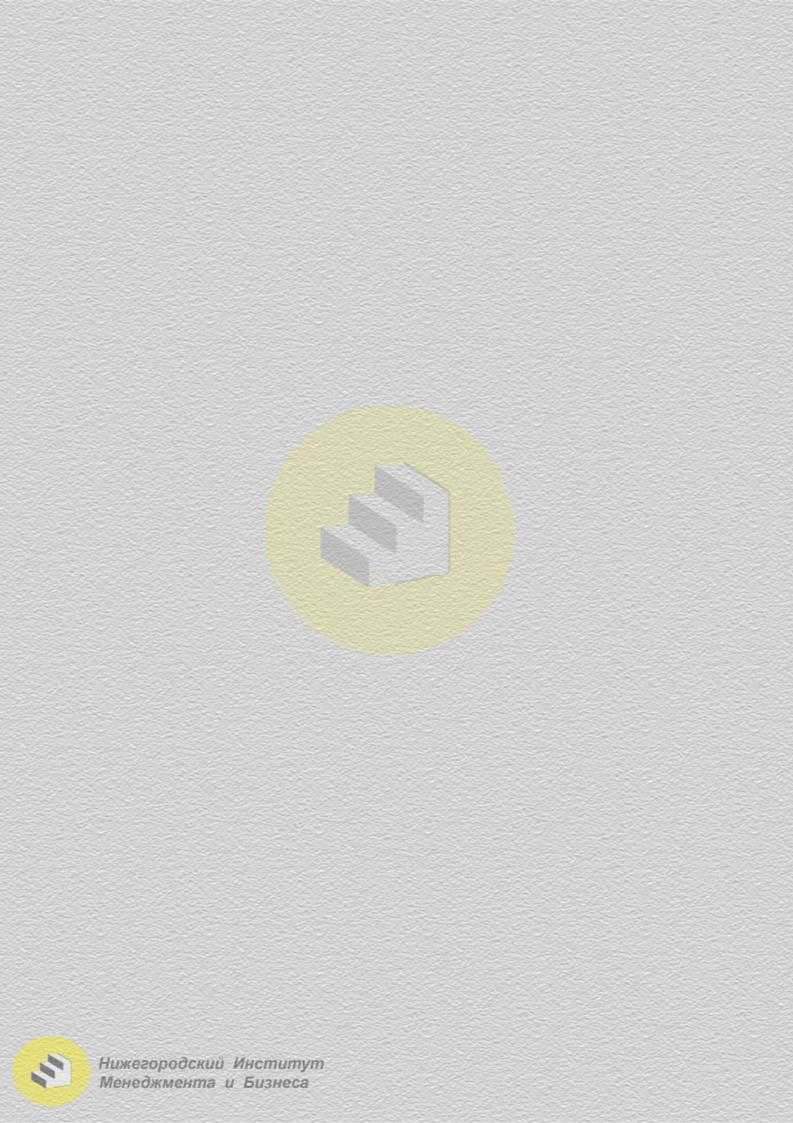
Вопрос 16.2. Календарное планирование
Данный вид планирования состоит в оптимальном упорядочении во времени множества работ, выполняемых на заданном оборудовании.
Календарное планирование является основной сферой практического приложения теории расписаний. Эта теория представляет собой систему качественных и количественных методов, позволяющих упорядочить во времени использование системы машин для обработки некоторого множества изделий. При этом должны быть упорядочены определенные технологические условия и обеспечено достижение оптимального значения заранее заданного критерия качества расписания.
Трудности решения задач теории расписаний обусловлены большим числом вариантов упорядочивания. Обычно используются методы, основанные на эвристических правилах предпочтения или на случайном поиске.
Задача календарного планирования работы участка единичного или мелкосерийного производства формулируется следующим образом: количество изделий (или серий) должны пройти обработку на одном или более типов станков.
Для каждого изделия (серии) задается технологический маршрут, т.е. последовательность номеров станков, на которых оно обрабатывается. Известны трудоемкости соответствующих операций. Предполагается, что одновременно на станке выполняется не более одной операции; операция, начавшись, не может быть прервана; последующая операция по обработке каждого изделия может начинаться лишь по окончании предыдущей; длительность операций не зависит от последовательности их выполнения; время на транспортировку и переналадку станков невелико.
Цель заключается в построении календарного графика обработки изделий, оптимального с точки зрения некоторого критерия.
Критериями могут быть: минимизация продолжительности календарного графика; минимизация простоев станков или неиспользования деталей; максимизация некоторого показателя использования оборудования; минимизация издержек и т.д.
Анализ отношений очередности операций удобно проводить на сетевых графиках, которые были ранее изучены. Известно, что кроме сетевых моделей инструментами календарного планирования могут стать: таблицы, линейные графики и циклограммы.
Календарные планы производства работ разрабатываются в рамках недели, месяца, квартала. Поэтому они могут называться оперативными планами. В состав календарных планов входят:
1) календарный план производства работ;
279

2)календарный график работы трудовых ресурсов;
3)календарный график использования основных машин и механизмов;
4)календарный график поступления материалов.
Все вышеперечисленные ресурсные документы увязаны с главным документом – “Календарным планом производства работ” по срокам и месту применения.
Данный документ представлен в табл. 2.4.1.
Таблица 2.4.1
Календарный план производства строительных работ (пример)
№ |
Наименования |
|
Характеристики работ |
|
Время работы (дн.) |
||||||||||||
п.п |
Ед. |
Объ- |
Трудоем- |
|
|
|
|
|
|
|
|
|
|
|
|||
. |
работ |
изм. |
ем |
кость (чел-ч) |
1 |
2 |
3 |
4 |
5 |
6 |
7 |
8 |
9 |
|
|||
1 |
Разработка грунта |
м3 |
10 |
320 |
|
|
|
|
|
|
10 |
чел |
. |
|
|
||
|
|
|
|
|
|
|
|
||||||||||
|
|
|
|
|
|
|
|
||||||||||
|
вручную |
|
|
|
|
|
|
|
|
|
|
|
|
|
|
|
|
2 |
Устройствофун- |
м |
3 |
126 |
170 |
|
|
|
|
|
|
|
|
|
5 |
чел. |
|
даментовизбетона |
|
|
|
|
|
|
|
|
|
|
|
|
|
||||
3 |
Кладка стен |
м3 |
128 |
46 |
|
|
|
|
2 чел. |
|
|
|
|
|
|
||
из кирпича |
|
|
|
|
|
|
|
|
|
|
|||||||
|
|
|
|
|
|
|
|
|
|
|
|
|
|
|
|
|
|
|
|
|
|
|
|
|
|
|
|
|
|
|
|
|
|
|
|
|
|
|
|
|
|
|
|
|
|
|
|
|
|
|
|
|
|
Как правило, к календарным планам, которые разрабатываются на квартал, месяц или неделю, дополнительно составляются календарные графики по следующим видам ресурсов: трудовым, материальным, техническим. Они имеют такую же, как и календарный план, конструкцию, но вместо наименования работ указывается соответствующий вид ресурсов со всеми характеристиками и временными параметрами потребления.
Таблицы отличаются от линейных графиков тем, что в них нет временных шкал.
Циклограммы строятся только для поточных процессов и имеют вид, представленный на рис. 2.4.3.
280
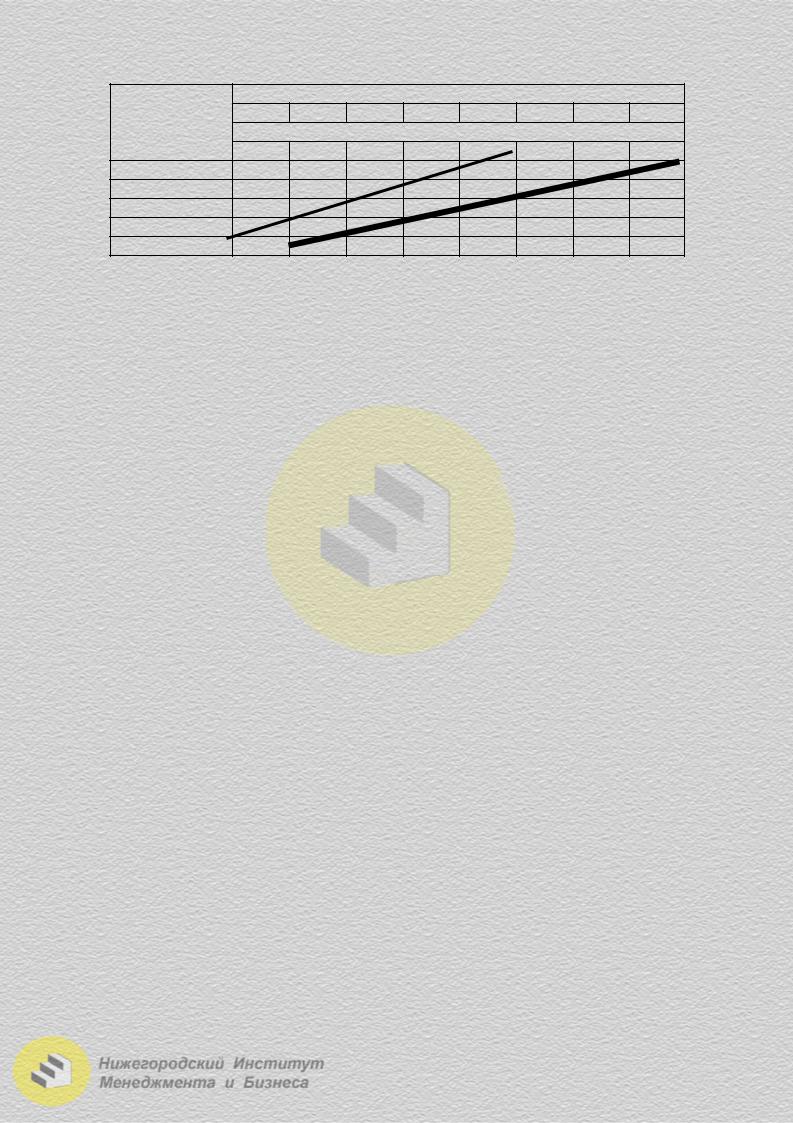
|
|
|
|
Календарное время |
|
|
|
|
Модули |
15 |
16 |
17 |
18 |
19 |
22 |
23 |
24 |
|
|
|
Рабочее время |
|
|
|
||
|
|
|
|
|
|
|
||
5 |
1 |
2 |
3 |
4 |
5 |
6 |
7 |
8 |
|
|
|
|
|
|
|
|
|
4 |
|
|
№1 |
|
№2 |
|
|
|
3 |
|
|
|
|
|
|
|
|
2 |
|
|
|
|
|
|
|
|
1 |
|
|
|
|
|
|
|
|
Примечание: модули – это одинаковые, повторяющиеся части будущего то- |
вара
Рис. 2.4.3. Общий вид циклограммы
Вопрос 16.3. Организация диспетчерской службы и контроля качества
Под диспетчерской службой, или диспетчеризацией, понимают систему централизованного контроля и управления производственными процессами, осуществляемую диспетчером из центрального пункта при помощи технических средств связи, сигнализации, телемеханики и автоматики.
Его цель состоит в обеспечении равномерного и комплектного выполнения плана. Особое значение для ритмичного хода производства имеют функции предупредительного контроля отклонений от установленного графика.
Диспетчеризация включает:
-непрерывный учет и текущую информацию о фактическом ходе работ по выполнению установленного графика;
-принятие оперативных мер по предупреждению и устранению отклонений от плана;
-выявление и анализ причин отклонений;
-координацию текущей работы взаимосвязанных звеньев производства в целях обеспечения ритмичного хода работы по установленному графику;
-организационное руководство оперативной подготовкой всего необходимого для выполнения сменно-суточных заданий и календарных графиков производства.
Вразных типах производства конкретное содержание диспетчерского руководства имеет ряд существенных особенностей.
Вединичном производстве основным объектом диспетчерского контроля за ходом производства являются сроки выполнения важнейших работ по отдельным заказам. Диспетчерский контроль осуществ-
281

ляется в этих условиях применительно к разработанным сетевым графикам выполненных заказов.
Вусловиях серийного производства главным объектом диспетчерского наблюдения являются: установленные по плану сроки запуска и выпуска партий заготовок и деталей на всех участках производства; состояние складских заделов заготовок и степень комплектной обеспеченности сборочных работ в соответствии с графиком.
Под контролем диспетчера также должны находится графики переналадки оборудования, учитывая, что серийное производство предусматривает эти работы.
Вусловиях массового производства диспетчерское наблюдение должно быть направлено на проверку соблюдения установленного такта работы поточных линий и норм заделов на всех стадиях производственного процесса.
Такой контроль осуществляется, как правило, с помощью суточных или почасовых линейных графиков работы или циклограмм.
Управление качеством – это действия, осуществляемые при создании, эксплуатации или потреблении продукции с целью установления, обеспечения и поддержания необходимого уровня ее качества.
Управление качеством продукции должно осуществляться системно, т.е. на предприятии должна оформиться и функционировать система управления качеством продукции.
При управлении качеством продукции используется ряд методов: - экономические методы, которые обеспечивают создание экономических условий, побуждающих коллективы предприятий улучшать
продукцию; - методы материального стимулирования, предусматривающие
поощрение работников; - организационно-распорядительные методы, осуществляемые по-
средством обязательного исполнения директив, приказов, требований нормативной документации;
- воспитательные методы, которые предполагают моральное поощрение.
Впоследние годы сформировалась новая стратегия в управлении качеством. Ее отличительные черты состоят в следующем:
- обеспечение качества понимается не как техническая функция, реализуемая определенным подразделением, а как систематический процесс, пронизывающий всю организационную структуру фирмы;
- новому понятию качества должна отвечать соответствующая структура предприятия;
282

-вопросы качества охватывают не только рамки производственного цикла, но и процесс разработок, конструирования, маркетинга, послепродажного обслуживания;
-качество должно быть ориентированно на удовлетворение требований потребителя, а не изготовителя;
-повышение качества продукции вызывает необходимость применения новой технологии производства, начиная с автоматизации проектирования и кончая автоматизированным измерением в процессе контроля качества;
-всеобъемлющее повышение качества достигается только заинтересованным участием всех работников.
Всеобъемлющий контроль качества (ТQМ – Тоtаl Quаlity Manаgеmеnt) предполагает наличие трех условий:
1. Качество как основная стратегическая цель деятельности признается высшим руководством фирм. Для этого устанавливаются конкретные задачи и выделяются средства для их решения. Поскольку требования к качеству определяет потребитель, уровень качества не может быть постоянным. Повышение качества должно идти по возрастающей, т.к. качество – постоянно меняющаяся цель.
2. Мероприятия по повышению качества должны затрагивать все подразделения.
3. Должен осуществляться непрекращающийся процесс обучения
иповышение мотивации персонала.
Первоначально, вопросы изучения качества продукции ограничивались только лишь регистрацией и заменой дефектных изделий. Первые серьезные исследования, связанные с качеством, появились после второй мировой войны. В 80-е годы требования к качеству стали главными в обеспечении конкурентоспособности.
По оценкам зарубежных ученых, объективно необходимо, чтобы расходы на качество составляли не менее 15-25% совокупных производственных затрат.
Первыми важность проблемы качества признали в Японии. При этом японцы основной акцент сделали на вовлечение всех работников в деятельность по улучшению качества.
Большое распространение в Японии получили кружки качества. Движение кружков качества поддерживается специальным общеяпонским штабом, имеющим свой журнал и проводящим ежегодные конференции. Таким образом, можно сказать, что работа по улучшению качества выходит за рамки отдельных фирм и приобретает общенациональный характер.
Часто японские кружки качества связывают с национальными особенностями японцев, что выражается в коллективизме и большом интересе к обучению (каждый рабочий хочет стать инженером).
283

Широкое распространение кружков качества требует от рабочих не только определенной психологии, но и достаточно глубоких знаний производства, а также методов контроля.
Одним из основных инструментов в обширном арсенале статистических методов контроля качества являются контрольные карты. Принято считать, что идея контрольной карты принадлежит известному американскому статистику Уолтеру Шухарту. Она была высказана в 1924 г. и обстоятельно описана в 1931 г. Первоначально карты использовались для регистрации результатов измерений требуемых свойств продукции. Выход параметра за границы поля допуска свидетельствовал о необходимости остановки производства и проведении корректировки процесса в соответствии со знаниями специалиста, управляющего производством.
Это давало информацию о том, когда, кто и на каком оборудовании получал брак в прошлом. Однако в этом случае решение о корректировке принималось тогда, когда брак уже был получен. Поэтому важно было найти процедуру, которая бы накапливала информацию не только для ретроспективного исследования, но и для использования при принятии решений. Это предложение опубликовал американский статистик И. Пейдж в 1954 г. Карты, которые используются при принятии решений, называются кумулятивными.
Контрольная карта (рис. 2.4.4) состоит из центральной линии, двух контрольных пределов (над и под центральной линией) и значений характеристики (показателя качества), нанесенных на карту для представления состояния процесса.
В определенные периоды времени отбирают (все подряд, выборочно или периодически из непрерывного потока) n изготовленных изделий и измеряют контролируемый параметр.
Результаты измерений наносят на контрольную карту, и в зависимости от этого значения принимают решение о корректировке процесса или о продолжении процесса без корректировок.
Сигналом о возможной неполадке технологического процесса могут служить:
•выход точки за контрольные пределы (точка 6) – процесс вышел из-под контроля;
•расположение группы последовательных точек около одной контрольной границы, но не выход за нее (11, 12, 13), что свидетельствует о нарушении уровня настройки оборудования;
•сильное рассеяние точек (15, 16, 17, 18, 19, 20) на контрольной карте относительно средней линии, что свидетельствует о снижении точности технологического процесса.
284

|
+ |
|
|
|
+ |
|
+ Верхний |
||
|
+++ |
|
|
++++ |
+ |
|
+ Централь- |
||
|
|
+ + |
+ |
|
+ |
+ |
|
ная линия |
|
|
|
|
|
Нижний пре- |
|||||
|
|
|
|
|
|
|
|
||
|
|
|
|
|
|
|
|
||
|
6 |
11 |
12 |
14 |
15 16 17 18 19 |
|
|||
|
|
|
|
|
|
|
|
|
|
Рис. 2.4.4. Контрольная карта
При наличии сигнала о нарушении производственного процесса должна быть выявлена и устранена причина нарушения.
Таким образом, контрольные карты используются для выявления определенной причины, но не случайной.
Под определенной причиной следует понимать существование факторов, которые допускают изучение.
Вариация же, обусловленная случайными причинами, необходима, она неизбежно встречается в любом процессе, даже если технологическая операция проводится с использованием стандартных методов
исырья. Исключение случайных причин вариации невозможно технически или экономически нецелесообразно.
Часто при определении факторов, влияющих на какой-либо результативный показатель, характеризующий качество, используют схемы Исикава. Они были предложены профессором Токийского университета Каору Исикава в 1953 г. при анализе различных мнений инженеров. Иначе схему Исикава называют диаграммой причин и результатов, диаграммой “рыбий скелет”, деревом и т. д.
Она состоит из показателя качества, характеризующего результат,
ифакторных показателей (рис. 2.4.5).
285

|
|
|
|
|
|
|
“Средняя |
|
|
|
“Мелкая |
|
|||||
|
|
“Большая кость” |
|
|
|
|
|
||||||||||
|
|
|
|
|
|
|
|
|
|
|
|
|
|
||||
|
|
|
|
|
|
|
|
|
|
|
|
|
|
||||
|
|
|
|
|
|
|
|
|
|
|
|
|
|
||||
|
|
|
|
|
|
|
|
|
|
|
|
|
|
|
|
|
|
|
|
|
|
|
|
|
|
|
|
|
|
|
|
|
|
|
|
|
|
|
|
|
|
|
|
|
|
|
|
|
|
|
|
|
|
|
|
|
|
|
|
|
|
|
|
|
|
|
|
|
|
Показатель каче- |
|
|
|
|
|
|
|
|
|
|
|
|
|
|
|
|
|
||
|
|
|
|
|
|
|
|
|
|
|
|
|
|
|
|
||
|
|
|
|
|
|
|
|
|
|
“Хребет” |
|
|
|
ства |
|||
|
|
|
|
|
|
|
|
|
|
|
|
|
|
|
|
|
|
|
|
|
|
|
|
|
|
|
|
|
|
|
|
|
|
|
|
|
|
|
|
|
|
|
|
|
|
|
|
|
|
|
|
|
|
Рис. 2.4.5. Структура диаграммы причин и результатов
Построение диаграмм включает следующие этапы:
−выбор результативного показателя, характеризующего качество изделия (“Хребта”);
−выбор главных причин, влияющих на показатель качества. Их необходимо поместить в прямоугольники (“большие кости”);
−выборвторичныхпричин(“средниекости”), влияющихнаглавные;
−выбор (описание) причин третичного порядка (“мелкие кости”), которые влияют на вторичные;
−ранжирование факторов по их значимости и выделение наиболее важных.
Диаграммы причин и результатов имеют универсальное применение. Так, они широко используются при выделении наиболее значимых факторов, влияющих, например, на производительность труда.
Отмечается, что число существенных дефектов незначительно и вызываются они, как правило, небольшим количеством причин. Таким образом, выяснив причины появления немногочисленных существенно важных дефектов, можно устранить почти все потери.
Эта проблема может решаться с помощью диаграмм Парето. Различают два вида диаграмм Парето:
1.По результатам деятельности. Они служат для выявления главной проблемы и отражают нежелательные результаты деятельности (дефекты, отказы и т.д.);
2.По причинам (факторам). Они отражают причины проблем, которые возникают в ходе производства.
Рекомендуется строить много диаграмм Парето, используя различные способы классификации как результатов, так и причин, приводящим к этим результатам. Лучшей следует считать такую диаграмму,
286

которая выявляет немногочисленные, существенно важные факторы, что и является целью анализа Парето.
Построение диаграмм Парето включает следующие этапы:
1.Выбор вида диаграммы (по результатам деятельности или по причинам (факторам);
2.Классификация результатов (причин). Разумеется, что любая классификация имеет элемент условности, однако большинство наблюдаемых единиц какой-либо совокупности не должны попадать в строку “прочие”.
3.Определение метода и периода сбора данных.
4.Разработка контрольного листка для регистрации данных с перечислением видов собираемой информации. В нем необходимо предусмотреть свободное место для графической регистрации данных.
5.Ранжирование данных, полученных по каждому проверяемому признаку в порядке значимости. Группу “прочие” следует приводить в последней строке вне зависимости от того, насколько большим получилось число.
6.Построение столбиковой диаграммы (рис. 2.4.6).
Число |
дефект- |
ных изде- |
Г |
Б В |
А |
про- |
Виды дефек- |
Рис. 2.4.6. Связь между видами дефектов и числом дефектных изделий
Значительный интерес представляет построение диаграмм Парето в сочетании с диаграммой причин и следствий. Выявление главных факторов, влияющих на качество продукции, позволяет увязать показатели производственного качества с каким-либо показателем, характеризующим потребительское качество.
Для такой увязки возможно применение регрессионного анализа. Например, в результате специально организованных наблюдений за результатами носки обуви и последующей статистической обработки полученных данных, было установлено, что срок службы обуви (y), зави-
287