
- •1. Рабочая программа
- •1.1. Пояснительная записка
- •1.2. Тематический план
- •2. Конспект лекций
- •Раздел 1. Производственные системы
- •Тема 1. Производство как объект управления
- •1.2. Понятие и содержание производственного менеджмента
- •1.3. Понятие и составные элементы производственной системы
- •1.4. Промышленное предприятие как объект управления
- •1.5. Общая характеристика и классификация промышленных предприятий
- •Тема 2. Рациональная организация производственного процесса
- •2.1. Понятие и составные элементы производственного процесса
- •2.2. Производственная структура предприятия
- •2.3. Типы производства
- •2.4. Основы организации гибких производственных систем (ГПС)
- •3.1. Организация процесса управления производством
- •3.2. Организационно-функциональная структура управления предприятием
- •3.3. Методологические основы производственного планирования
- •3.4. Содержание и взаимосвязь плановых расчетов
- •3.5. Методы эффективного управления материальным потоком
- •Раздел 2. Управление основным производством
- •Тема 4. Система управления основным производством
- •4.2. Организация производственного планирования
- •4.3. Состав и особенности расчета календарно-плановых нормативов (КПН)
- •4.5. Организация оперативного учета и контроля хода производства
- •Тема 5. Функции и задачи линейных руководителей производства
- •5.1. Требования к профессиональной компетенции менеджера производства
- •5.2. Функции и должностные обязанности руководителей производства
- •Тема 6. Обеспечение функционирования производственной системы
- •6.1. Организация управления сбытовой деятельностью
- •6.3. Характеристика систем складирования и размещения запасов
- •Тема 7. Организация обслуживания основного производства
- •7.1. Организация управления технической подготовкой производства (ТПП)
- •7.2. Организация управления ремонтным обслуживанием оборудования
- •7.3. Организация управления инструментальным хозяйством
- •7.4. Организация управления транспортным хозяйством
- •7.5. Организация управления энергетическим хозяйством
- •7.6. Организация управления техническим контролем качества продукции
- •3. Контроль знаний
- •3.1. Контрольные вопросы
- •3.2. Программированные задания
- •4. Глоссарий
- •5. Литература
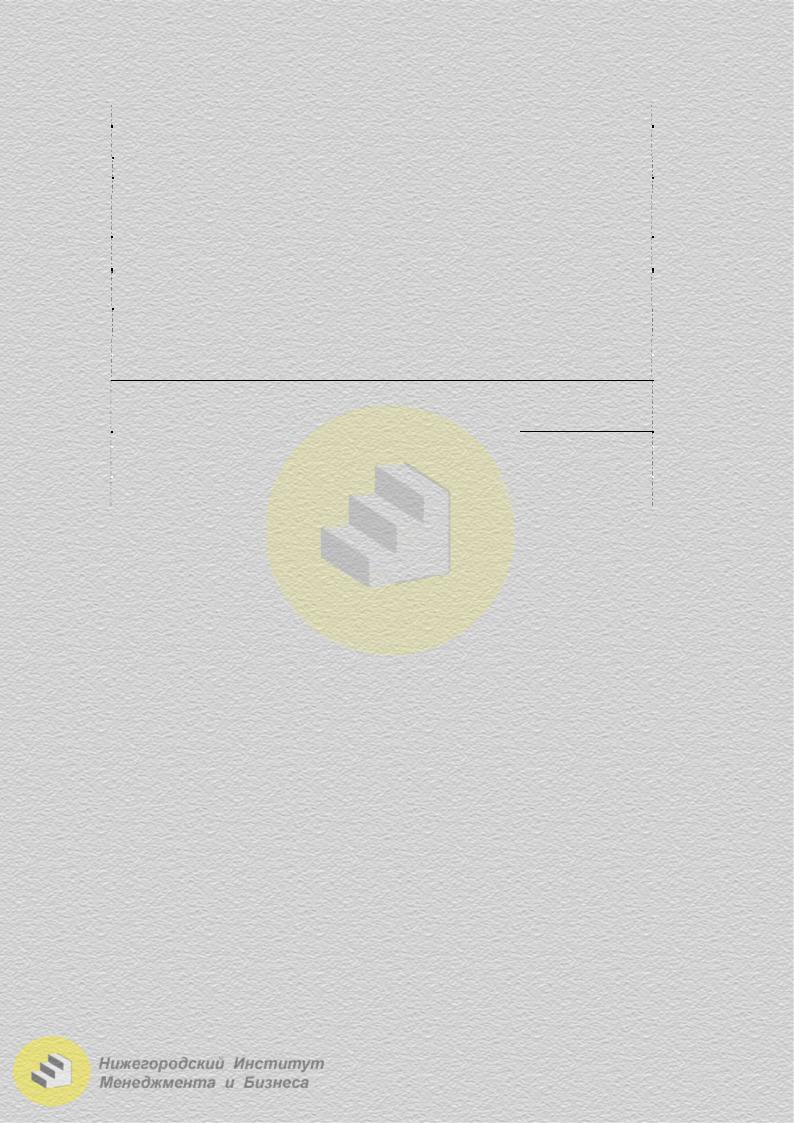
Испол- |
|
|
|
|
|
|
|
|
|
|
|
|
|
|
|
|
|
|
Период |
нитель |
|
|
|
|
|
|
|
|
|
|
|
|
|
|
|
|
|
|
управ- |
План производства товарной продукции по предприятию |
|
|
|||||||||||||||||
|
|
|
ления |
||||||||||||||||
ПЭО, |
Вид товар. |
Изделие |
Вид |
Вид измер. |
|
|
|
План производства |
|
|
|
||||||||
продукции |
|
|
исп. |
|
|
|
|
|
|
|
|
|
|
|
|
|
|
год |
|
ПДО |
|
|
|
|
|
|
|
|
|
|
|
|
|
|
|
|
|||
|
Наи- |
Обо- |
|
|
|
|
На год |
|
|
в т.ч. по кварталам |
|
||||||||
|
|
мен. |
знач. |
|
|
|
|
|
|
|
|
|
|
|
|
|
|
|
|
|
|
|
|
|
|
|
|
|
I |
|
|
II |
III |
|
IV |
|
|||
|
|
|
|
|
|
|
|
|
|
|
|
|
|
|
|||||
|
1 |
2 |
3 |
4 |
5 |
|
|
6 |
|
7 |
|
8 |
9 |
|
10 |
|
|
||
|
|
|
|
|
|
|
|
|
|
||||||||||
|
Подетальная производственная программа по цехам предприятия |
|
|
|
|||||||||||||||
|
цех-изготовитель |
|
|
|
|
|
|
|
|
|
|
|
|
|
|
|
|
|
|
ПДО |
Вид товар. |
Деталь, сбор. |
Вид |
Номер |
Ед. |
|
|
Потребность на план |
|
|
год, |
||||||||
продукции |
единица |
исп. |
захода |
изм. |
|
|
|
производства |
|
|
|||||||||
|
|
|
|
|
|
кварт. |
|||||||||||||
|
|
|
|
|
|
|
|
|
|
|
|
|
|
|
|
|
|
|
|
|
|
Наи- |
Обо- |
|
|
|
|
|
На |
|
|
в т.ч. по кварталам |
|
||||||
|
|
мен. |
знач. |
|
|
|
|
|
год |
|
I |
|
|
II |
III |
|
IV |
|
|
|
1 |
2 |
3 |
4 |
5 |
6 |
|
|
7 |
|
8 |
|
|
9 |
10 |
|
11 |
|
|
План сдачи-получения деталей, сборочных единиц по межцеховым передачам
ПДО, |
цех-изготовитель |
|
|
|
|
|
|
|
|
|
|||
ПДБ |
Цех- |
Вид |
Деталь |
Вид |
Номер |
Ед. |
Сред- |
План сдачи |
|
||||
цехов |
полу- |
плана |
Наи- |
Обо- |
исп. |
захода |
из- |
несут. |
На |
в т.ч. по |
|||
|
|
чат. |
|
мен. |
знач. |
|
|
мер. |
план |
квар- |
|
мес. |
|
|
|
|
|
|
|
|
|
|
|
тал |
1 |
2 |
3 |
|
|
1 |
2 |
3 |
4 |
5 |
6 |
7 |
8 |
9 |
10 |
11 |
12 |
кварт., месяц
Рис. 2.2.6. Виды форм производственных планов предприятия
4.3. Состав и особенности расчета календарно-плановых нормативов (КПН)
Основные КПН промышленного предприятия. Особенности расчета размера партии обрабатываемых деталей и ритма партии. Расчет длительности производственного цикла, нормативных заделов, опережений запуска-выпуска, нормативных запасов. КПН в единичном, серийном и массовом производстве.
Календарно-плановые нормативы (КПН) – это расчетные регламентирующие величины, которые используются для рациональной организации производственного процесса на машиностроительном предприятии (размер партии обработки, длительность цикла изготовления, нормы заделов незавершенного производства, нормативы опережения запуска-выпуска, нормы запасов и т.д.). Научно-обоснованная система КПН позволяет обеспечить согласованность в деятельности производственных подразделений, ритмичность и равномерность выпуска продукции, ускорить оборачиваемостьоборотныхсредств, снизитьзатратынапроизводствопродукции.
Внедрение КПН в практику управления производственной системой является необходимым условием:
–строгогоиобоснованногозакрепленияплановыхзаданийзарабочимиместами;
–изготовления каждой номенклатурной позиции в соответствии с установленной периодичностью;
–своевременной подачи деталей и узлов на последующие стадии производства;
–установления нормативных сроков запуска-выпуска партий деталей с учетом длительности производственных циклов и нормативных опережений;
69
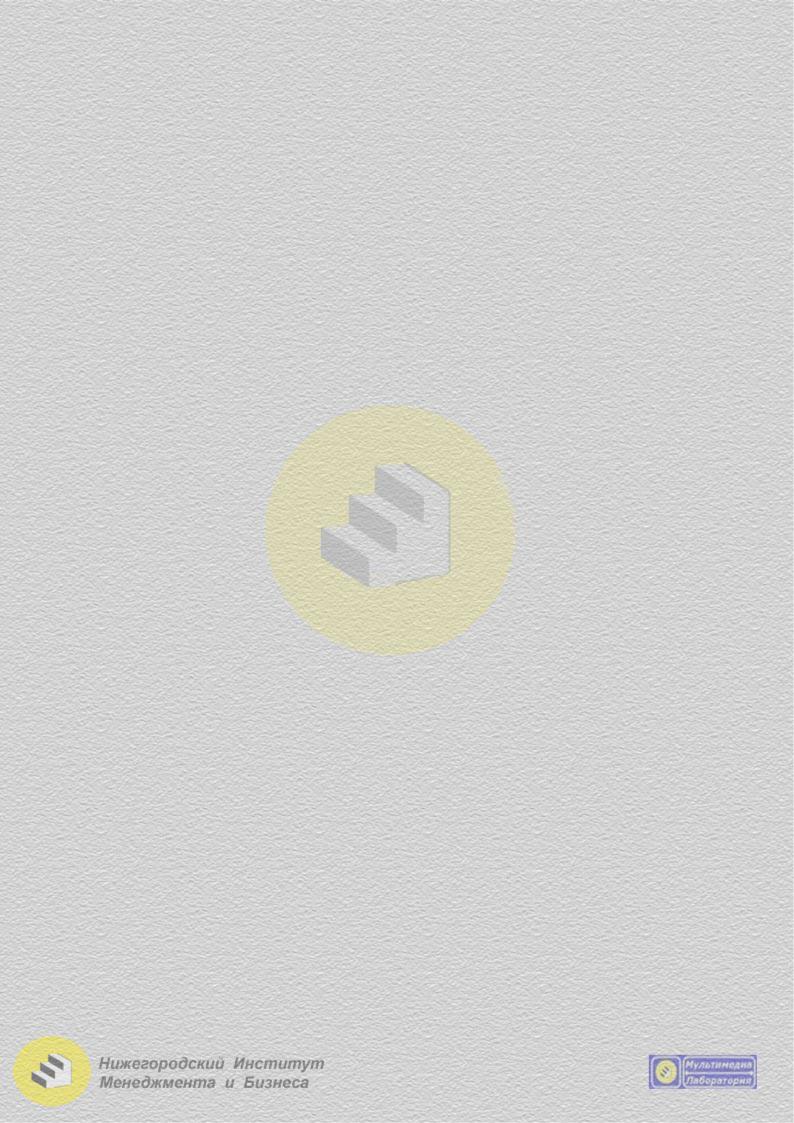
– своевременной и качественной подготовки производства.
Состав и методология расчетов КПН для различных типов производства и уровней управления существенно отличаются.
Наиболее характерными КПН для массового производства являются такт и темп работы поточной линии, нормативы заделов. Такт поточной линии устанавливается как средний промежуток времени между запуском или выпуском двух следующих друг за другом предметов труда. На разных стадиях производственного процесса находятся заделы заготовок, деталей, сборочных единиц, т.е. незавершенное производство. Независимо от типа организации производства заделы классифицируют по местоположению, выделяя внутрицеховые и межцеховые.
Вусловиях серийного производства принято рассчитывать следующую систему КПН:
–расчет партии запуска-выпуска деталей, сборочных единиц;
–периодичность запуска-выпуска партий предметов труда;
–длительность производственного цикла изготовления;
–календарныеопережениязапуска-выпускапартийдеталей, сборочныхединиц;
–нормативызаделовнезавершенногопроизводстваинормыскладскихзапасов.
Всерийном производстве особо выделяют цикловые и складские заделы. Цикловой задел состоит из деталей, находящихся на всех стадиях производственного процесса, на межоперационном транспорте и в ожидании очередной операции обработки. Складские заделы находятся на внутрицеховых и межцеховых складах.
Вединичном производстве основными календарно-плановыми нормативами являются:
–длительность производственного цикла изготовления деталей, сборочных единиц;
–опережения запуска-выпуска в работе смежных производственных подразделений;
–нормативная трудоемкость или стоимость работ по исполнителям;
–цикловой график выполнения заказа и др.
Основным КПН является нормативный размер партии обрабатываемых деталей, который необходим для:
–расчета нормативной длительности производственных циклов и календарных опережений в работе смежных цехов и участков;
–разработки календарных планов, определяющих сроки запуска партий деталей в обработку и их выпуска;
–определения нормативных уровней заделов;
–регламентации периодичности переналадок оборудования на изготовление одноименных деталей.
На длительность производственного цикла, кроме величины размера партии, влияют также количество рабочих мест, на которых выполняется данная работа, сменность и вид движения предметов труда по операциям, количество деталей, сборочных единиц, одновременно обрабатываемых на каждом рабочем месте и т.д.
При расчете КПН необходимо руководствоваться следующими основными методическими положениями:
–КПНрассчитываютсятолькопопредметамтрудасобственногопроизводства;
–расчеты КПН проводятся по каждому цеху с последующим формированием сводных КПН в целом по производству и предприятию;
70
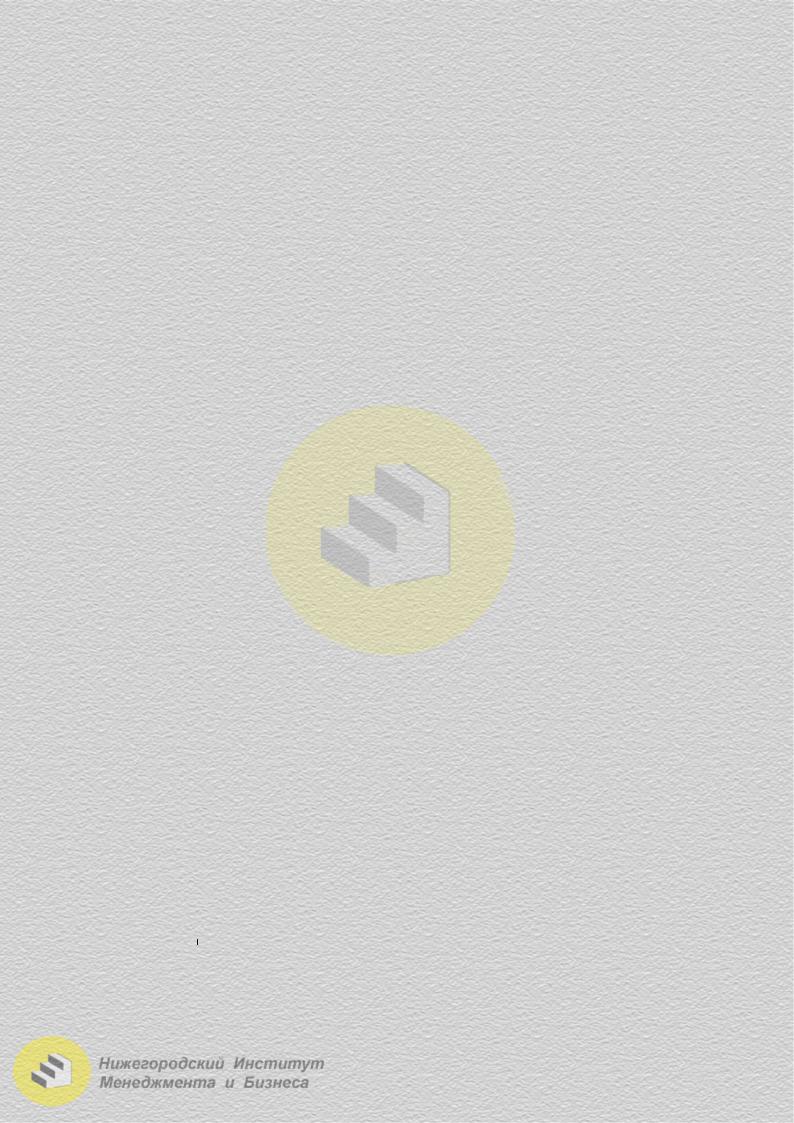
– КПН рассчитываются и устанавливаются сроком на год (корректировка или расчет КПН заново производится при существенном изменении производственной программы более чем на 10-15 %, а также при значительном изменении конструкции и технологии производства).
4.4. Оперативно-календарное планирование и регулирование производства (операционный менеджмент)
Методология календарного планирования и регулирования. Содержание и очередность выполняемых расчетов. Календарное планирование межцеховых передач. Внутрицеховое оперативно-календарное планирование. Моделирование управления цехом. Подход к формированию сменно-суточных заданий по участкам цеха. Образцы форм календарных графиков.
Календарное планирование заключается в том, чтобы при заданных последовательностях технологических операций и имеющихся ограничениях на материальные и трудовые ресурсы оптимально упорядочить во времени множество работ, выполняемых на имеющемся в наличии оборудовании. Календарное планирование является основной сферой практической реализации теории расписания, когда применяются методы, обеспечивающие рациональное использование оборудования для выполнения во времени множества разнообразных операций при изготовлении различных изделий. Трудности решения задач расписания связаны с большим числом разнообразных вариантов упорядочения по детали – операции – оборудованию, когда нахождение окончательного варианта основывается на применении эвристических правил предпочтения или на случайном поиске.
Основной задачей оперативно-календарного планирования на машиностроительном предприятии следует считать обеспечение бесперебойного хода производственного процесса, имеющего своей конечной целью выполнение принятых ранее договорных обязательств по изготовлению и поставке готовой продукции заказчикам в установленном количестве и заданные календарные сроки. При этом расчеты базируются на оперативных сведениях о реальном выполнении плановых заданий, выявленных отклонениях, обеспеченности заготовками, материалом, комплектующими и оборудованием.
Сложилась традиционная система оперативно-календарного планирования (межцехового и внутрицехового), при которой вначале задания по изготовлению конкретной продукции устанавливаются цехам, а затем они доводятся до участков, рабочих мест. Поскольку на каждой совокупности рабочих мест, как известно, может изготавливаться не один предмет, при календарном планировании встает проблема поиска такого рационального сочетания работ, рабочих мест и оборудования, которое обеспечивало бы выполнение установленного планового задания.
План-график, составляемый на месяц, считается базовым, так как он необходим для увязки производства и сбыта, материально-технического снабжения и подготовки производства, технико-экономических показателей и производственных возможностей по конкретным календарным датам (рабочим дням месяца). Однако в силу известных возмущающих внешних и внутренних факторов этот план по истечении определенного времени требует корректировки с суточной или сменной периодичностью. Построениепланов-графиковдолжнобазироватьсянаинформации:
–окалендарныхдатахотгрузкиготовойпродукции, установленныхдоговорами;
–о календарно-плановых нормативах основного производства;
71
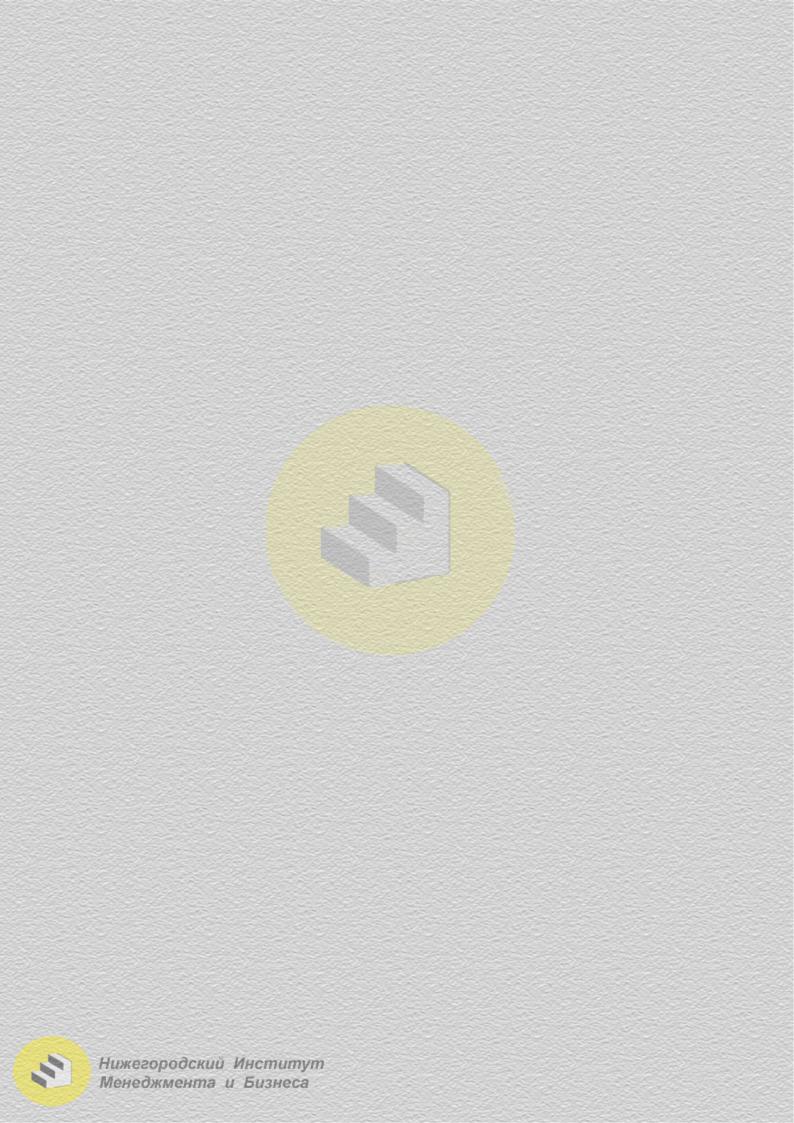
–о фактических сроках выполнения заданий плана-графика;
–об обеcпеченности производства необходимым оборудованием, инструментом, материалами, заготовками, рабочими, тарой, документацией и т.д.
Для этого по межцеховому оперативно-календарному планированию предлагается выделить следующие взаимоувязанные расчеты:
–сформировать месячные с разбивкой по суткам календарные графики выпуска конечной продукции сборочными цехами с учетом требований сбыта и особых указаний по отгрузке готовой продукции;
–составить календарный график межцеховых поставок на месяц с распределением по рабочим дням;
–выполнить оперативно-календарное планирование на каждые рабочие сутки межцеховых передач внутри предприятия, исходя из результатов фактического хода производства и особенностей применения системы ОПП;
–обеспечить оперативно-календарное планирование на сутки выпуска товарной продукции цехами основного производства предприятия.
Суточные планы-графики, рассчитываемые далее по каждому сборочному цеху, выпускающему конечную продукцию, должны быть не только увязаны с графиками отгрузки товарных изделий по заказам потребителей, но и учитывать поставку смежными цехами и, в том числе, по системе подвесных толкающих конвейеров. При этом особо контролируется наличие комплектующих на складах сборочных цехов и отдела внешней кооперации (ОВК), обеспечение техпроцесса необходимой оснасткой, приспособлениями, транспортными средствами и т.д. Плановые задания по сборке следует детализировать до сменного, а на большинстве предприятий – до часового интервала времени, указывая очередность закладки модификаций на конвейере и подачи основных узлов цехами, питающими сборку.
Важным и, несомненно, ответственным элементом функционирования системы оперативного управления следует считать внутрицеховое оперативно-кален- дарное планирование, целью которого является составление календарных плановграфиков запуска-выпуска партий деталей для участков, групп рабочих мест. План-график является основным оперативным документом, на основании которого осуществляется организация работ в цехе и на участке, технологическая подготовка производства, обеспечение его рабочими, необходимыми материалами, инструментом, комплектующими изделия и т.д.
Содержание и очередность ежедневно выполняемых вычислений в достаточно укрупненном виде можно представить следующим образом (рис. 2.2.7):
–календарный план-график межцеховых передач корректируется по фактическим результатам работы на дату расчета;
–определяется потребность в изготавливаемых цехом деталях, сборочных единицах на календарный график сборки и скорректированный график межцеховых передач;
–контролируется обеспеченность календарных графиков межцеховых передач деталями, имеющимися в наличии в незавершенном производстве цеха;
–устанавливаются приоритеты по запуску партии деталей в обработку, исходя из обеспеченности сборки, выполнения календарного плана межцеховых передач, выполнения месячного плана на дату расчета, дополнительных указаний и т.д.;
–корректируется суточное задание цеху с учетом фактической величины внутрицехового задела и определяется трудоемкость его изготовления;
72
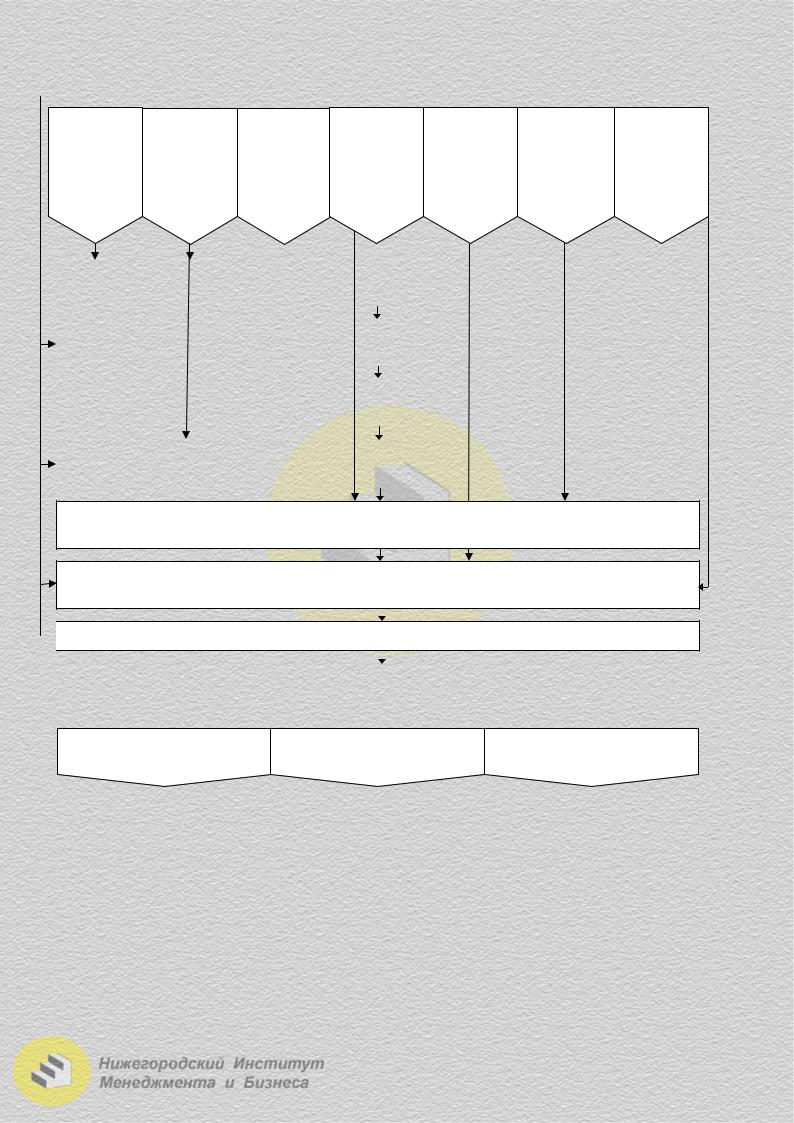
|
|
|
|
Исходная информация |
|
|
|
||
Календар- |
|
|
|
|
|
|
|||
Фактический КалендарноТехнологи- |
Наличный |
Состояние |
Обеспечен- |
||||||
ный план- |
результат |
плановые |
ческий мар- |
фонд време- |
внутрицехо- |
ность заго- |
|||
график |
работы на |
нормативы и |
шрут и тру- |
ни работы |
вых заделов |
товками, ин- |
|||
сборки и |
дату расчета |
нормы по |
доемкость |
оборудова- |
незавершен- |
струментом, |
|||
межцеховых |
|
|
цеху |
изготовле- |
ния цехов |
ного про- |
оснасткой |
||
передач |
|
|
|
|
ния ДСЕ |
|
|
изводства |
|
|
1 |
Корректировка календарного плана-графика межцеховых передач |
|
по фактическим результатам на дату расчета |
|
|
|
|
|
|
|
|
|
|
2 |
Определение потребности в изготовляемых цехом ДСЕ на календарный график |
|
|
|
сборки и скорректированный план-график межцеховых передач |
|
|
|
|
3 |
Корректировка календарного плана-графика межцеховых передач |
|
|
по фактическим результатам на дату расчета |
|
|
|
|
|
|
|
|
|
|
|
|
|
|
|
4 |
Установление приоритетов по запуску партии ДСЕ в обработку с учетом |
|
|
обеспеченности сборки, состояния заделов, выполнения плана |
|
|
|
|
|
|
|
|
|
|
Корректировка суточного задания с учетом фактического состояния заделов
5и определение трудоемкости изготовления
6Формирование календарного графика запуска выпуска по участкам цеха с учетом фонда времени работы оборудования, обеспеченности инструментом, оснасткой
7 Определение потребности в материальных ресурсах, комплектующих изделиях
8 |
Доведение календарных планов-графиков до исполнителей |
||||
|
|
|
|
|
|
|
|
|
|
|
|
|
|
|
Выходная информация |
|
|
|
Календарный план график |
Сменно-суточное задание по |
План график запуска-выпуска |
||
|
межцеховых передач |
|
участкам цеха |
на оборудовании участка |
|
|
|
|
|
||
9 |
Организация выполнения календарных план графиков участками, цехами |
||||
|
|
|
|
|
|
Рис. 2.2.7. Порядок расчета (алгоритм) оперативно-календарного планирования по участкам цеха
–формируются календарные графики запуска-выпуска по участкам, группам рабочих мест цеха с учетом наличия фонда времени работы оборудования, обеспеченности металлом, заготовками, комплектующими, инструментом и т.д.;
–определяется почасовая потребность сборки в основных узлах и отдельных видах ресурсов, составляется график синхронной работы подвесных толкающих конвейеров и, при необходимости, подготовки производства;
–плановые задания доводятся до исполнителей.
73
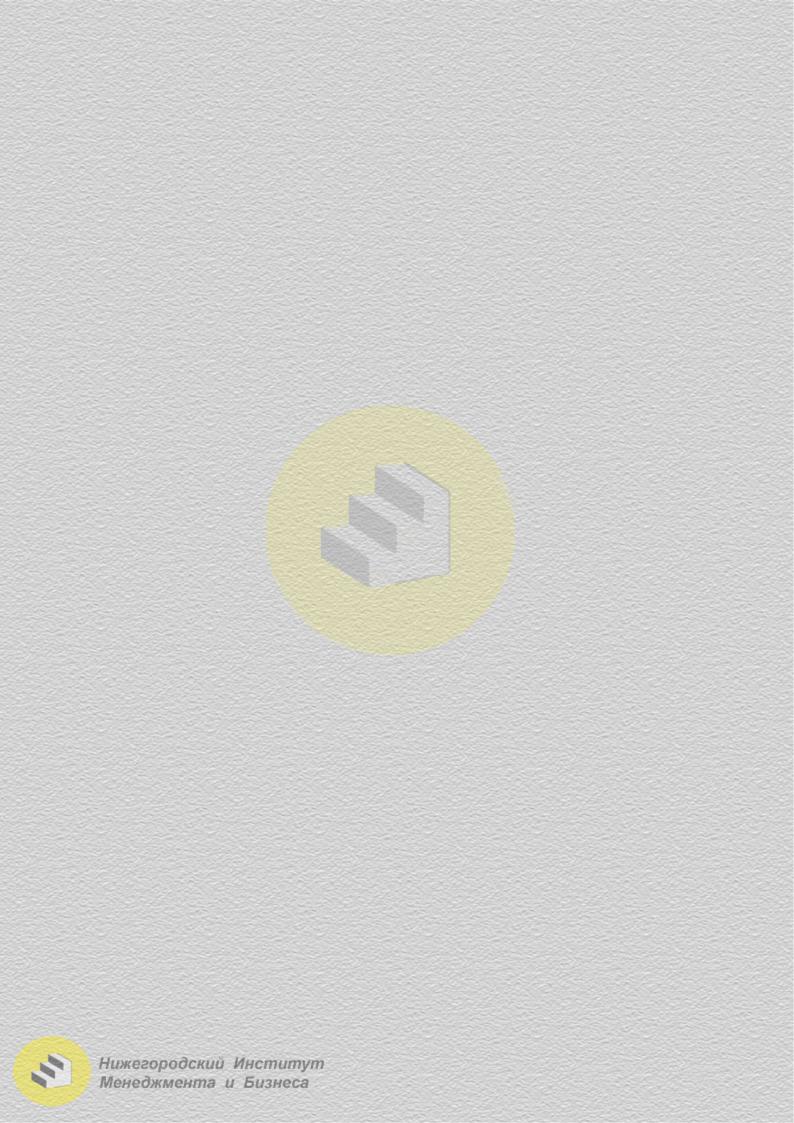
Подобной последовательностью действий в методологическом аспекте обеспечивается планомерная организация и взаимосвязанная деятельность всех производственных звеньев предприятия, гибкое маневрирование имеющимися ресурсами в условиях неопределенности, своевременная техническая подготовка и ма- териально-техническое обеспечение производства.
Формирование сменно-суточного плана и оперативное управление работой участка предполагает, в первую очередь, обоснованное установление функций предпочтения – приоритетов – для запуска партий деталей, находящихся в очереди для обработки перед оборудованием на участке.
При реализации задач оперативно-календарного планирования предлагается очередность запуска деталей по участкам цеха устанавливать с помощью взаимосвязанных функций предпочтения.
Первый приоритет следует присваивать деталям, фактическое наличие которых в сборочном цехе меньше плановой потребности в них на суточный план сборки. Внутри приоритета по каждой детали необходимо определять показатель обеспеченности сборки в часах.
Второй приоритет присваивается деталям, фактический задел на сборке по которым меньше нормативного. Также этот приоритет присваивается деталям, по которым фактическая их сдача с начала месяца меньше запланированной и требуется восполнить задел на участках-потребителях. Внутри приоритета по каждой детали определяется показатель относительного восполнения задела.
Третий приоритет присваивается всем остальным деталям из месячного плана, не имеющим второго или первого приоритета. Внутри приоритета по каждой детали делается расчет показателя обеспеченности в днях.
Детали, которые рассматриваются для изготовления на конкретные сутки, упорядочиваются по возрастанию величины присвоенного им приоритета, а внутри приоритета – по возрастанию показателей обеспеченности.
Моделирующий алгоритм формирования сменно-суточных планов по участкам цеха составлен таким образом, чтобы он мог настраиваться на определенный набор факторов. Так, в начале с учетом потребностей сборки, состояния заделов и фактического выполнения плана на дату расчета формируется очередь из деталей (с указанием количества) по приоритетам. Далее конкретный план на смену по рабочим местам участка формируется с учетом: наличия фонда времени работы групп оборудования; обеспеченности инструментом и оснасткой; наличия тары; обеспеченности комплектующими и поставками из смежных цехов. Начальник участка и начальник ПДБ вправе изменить приоритеты у деталей или снять с рассмотрения некоторые факторы.
Образцы форм документов по операционному менеджменту представлены на рис. 2.2.8.
Состав и очередность изготовления партий деталей разных наименований следует устанавливать, исходя из максимальной загрузки или минимального простоя оборудования, либо минимального пролеживания партий деталей, определенным наборомправили функцийпредпочтения, которые позволяют найтидопустимоерешение. При этом в сменно-суточное задание по участку предусматривается вначале включениеработ, непрошедшихокончательнойобработкинавсехоперацияхучастка. Далее, исходя из обеспеченности, определяются работы, сдерживающие сборку готовых изделий, и с учетомплана сдачи деталей на месяц формируется перечень работ впорядкеуменьшенияотклоненияфактическойсдачидеталейотпотребностивних.
74
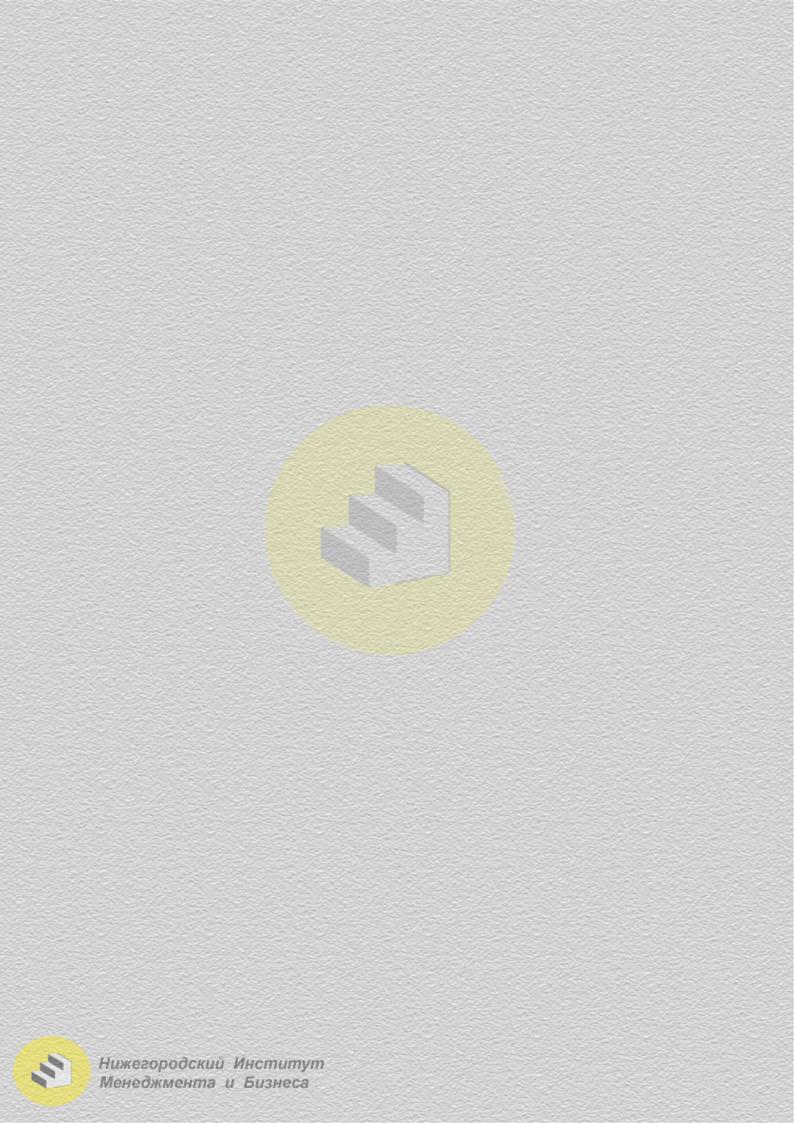
Расчет суточного задания участку цеха __ на дату __ _____
Код груп- |
Количество |
Обозначе- |
Код |
План |
План |
Загрузка |
пы обору- |
единиц обо- |
ние детали |
операции |
на сутки |
на месяц |
оборудова- |
дования |
рудования |
|
|
|
|
ния |
1 |
2 |
3 |
4 |
5 |
6 |
7 |
Сменно-суточное задание участку сборки цеха __ на дату, смену __ ___
При- |
Обозначение |
Направление |
Осталось до |
|
Задание на сутки |
|
|
оритет |
изделия |
реализации |
конца месяца |
Всего |
|
в том числе |
|
|
|
|
|
|
|
1 смена |
2 смена |
1 |
2 |
3 |
4 |
5 |
|
6 |
7 |
Сменно-суточное задание участку цеха __ на дату, смену __ ___
Обозначе- |
Код |
Код |
Плановое задание |
План |
Выполнено |
||
ние детали |
обору- |
операции |
на сутки |
1 смену |
2 смену |
на месяц |
с начала |
|
дования |
|
|
|
|
|
месяца |
1 |
2 |
3 |
4 |
5 |
6 |
7 |
8 |
Рис. 2.2.8. Образцы форм документов по операционному менеджменту
Предметная специализация производственных подразделений и их экономическая самостоятельность (бюджетный подход в управлении составными элементами производственной системы) вызывают необходимость рассмотрения вопросов моделирования управленческой деятельности в рамках конкретного цеха как экономически самостоятельной хозрасчетной бизнес-единицы.
Основной целью моделирования является повышение гибкости и оперативности управления всеми элементами производственной системы, обеспечение ритмичного производства и выпуска готовой продукции с учетом требований сбыта, выявление и снижение потерь материальных ресурсов и брака, поддержание заделов незавершенного производства на заданном уровне, улучшение качества и культуры производства. В имитационной модели, характеризующей производственный процесс в цехе, по каждому технологическому переходу (поставщик – изготовитель – потребитель) предусматривается установление определенного перечня контролируемых параметров, включающих:
–заданный маршрут движения и технологию изготовления;
–применяемость и варианты возможных замен;
–нормативные и плановые показатели деятельности (план получения, план сдачи, нормы складских запасов в кладовых цеха комплектующих, материалов, инструмента, нормы заделов, партии запуска и транспортировки, опережения запускавыпуска, календарныесроки приема-передачипоучасткам, группамоборудования);
–выделенные лимиты материальных ресурсов на программу цеха;
–виды оборудования, производительность, закрепление за операциями;
–график планово-предупредительного ремонта (ППР) и статистику возникновения внеплановых простоев оборудования;
–плановое количество рабочих по группам оборудования, взаимозаменяемость, статистику фактических выходов рабочих;
–режим работы;
–учетные данные о фактическом состоянии производства и его обеспеченности на любой момент времени.
75