
- •Химический состав нефтей
- •Классификация нефтей
- •Химические классификации.
- •Геохимические и генетические классификации.
- •Технологические классификации.
- •СВОЙСТВА НЕФТЕЙ
- •Физико-химические свойства нефтей
- •Плотность.
- •Молекулярная масса.
- •Вязкость*.
- •Теплопроводность.
- •Теплоемкость.
- •Теплота испарения.
- •Энтальпия (теплосодержание).
- •Оптическая активность.
- •Электрические свойства.
- •Коллоидные свойства нефтей
- •Коллоидно-дисперсное строение нефтяных систем.
- •ПРОИСХОЖДЕНИЕ НЕФТИ
- •ЛИТЕРАТУРА
- •Перегонка и ректификация
- •Азеотропная ректификация.
- •Экстракция и экстрактивная ректификация.
- •Адсорбционная хроматография
- •Термодиффузия
- •Диффузия через мембраны
- •Кристаллизация и экстрактивная кристаллизация
- •Образование аддуктов и комплексов
- •МЕТОДЫ ВЫДЕЛЕНИЯ И РАЗДЕЛЕНИЯ НЕУГЛЕВОДОРОДНЫХ КОМПОНЕНТОВ
- •Экологические и технологические аспекты выделения
- •Выделение гетероатомных соединений средних фракций
- •Серусодержащие соединения.
- •Образование солей и комплексов.
- •Азотсодержащие соединения.
- •Нейтральные кислородсодержащие соединения.
- •Выделение смолисто-асфальтеновых веществ
- •Разделение смолисто-асфальтеновых веществ
- •ЛИТЕРАТУРА
- •СПОСОБЫ ВЫРАЖЕНИЯ СОСТАВА НЕФТЯНЫХ ФРАКЦИЙ
- •МЕТОДЫ АНАЛИЗА ИНДИВИДУАЛЬНОГО СОСТАВА
- •Газовая хроматография
- •МЕТОДЫ АНАЛИЗА ГРУППОВОГО СОСТАВА
- •Масс-спектрометрия и хромато-масс-спектрометрия
- •Спектральный анализ
- •МЕТОДЫ АНАЛИЗА МИКРОЭЛЕМЕНТОВ
- •МЕТОДЫ СТРУКТУРНО-ГРУППОВОГО АНАЛИЗА
- •Анализ легких и средних фракций
- •Анализ смолисто-асфальтеновых веществ
- •Определение молекулярной массы асфальтенов и смол.
- •Рентгеноструктурный анализ.
- •Структура ароматических фрагментов.
- •Структура циклоалкановых фрагментов.
- •Структура алифатических фрагментов.
- •Структура фрагментов, содержащих гетеро атомы и микроэлементы.
- •Интегральный структурный анализ.
- •ЛИТЕРАТУРА
- •АЛКАНЫ
- •Физические свойства
- •Теплофизические свойства.
- •Фазовые превращения.
- •Физико-химические свойства
- •Химические превращения
- •ЦИКЛОАЛКАНЫ
- •Физические свойства
- •Химические превращения
- •АРЕНЫ
- •Состав аренов нефтей различных месторождений
- •Физико-химические свойства
- •Химические превращения
- •ГЕТЕРОАТОМНЫЕ СОЕДИНЕНИЯ СРЕДНИХ ФРАКЦИИ
- •Серусодержащие соединения
- •СМОЛИСТО-АСФАЛЬТЕНОВЫЕ ВЕЩЕСТВА
- •Физические свойства .
- •Физико-химические свойства
- •Химические превращения
- •МИКРОЭЛЕМЕНТЫ
- •ЛИТЕРАТУРА
- •АЛКАНЫ
- •Природные горючие газы.
- •Жидкие алканы.
- •Твердые алканы.
- •Белки биологического синтеза.
- •ЦИКЛОАЛКАНЫ
- •Циклогексан и продукты его химических превращений.
- •Другие циклоалканы и продукты их химических превращений.
- •АРЕНЫ
- •ГЕТЕРОАТОМНЫЕ СОЕДИНЕНИЯ СРЕДНИХ ФРАКЦИИ
- •Серусодержащие соединения.
- •Азотсодержащие соединения.
- •СМОЛИСТО-АСФАЛЬТЕНОВЫЕ ВЕЩЕСТВА
- •ЛИТЕРАТУРА
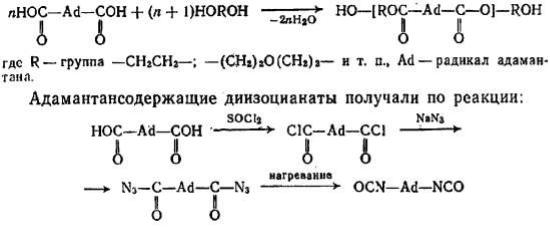
Адамантан и продукты его химических превращений. Адамантан используют как модификатор полимеров, повышающий их прочность, химическую и термическую стойкость. Термической поликонденсацией адамантансодержащих силанов и их сополимеризацией с бифункциональными алкил(арил)хлорсиланами были получены полиорганосилоксаны с адамантановым ядром в боковой цепи макромолекул, обладающие повышенной термической устойчивостью и инертностью в среде кислот и щелочей [38].
Осуществлен синтез полиуретанов на основе производных адамантана по схеме [39]:
Адамантан-1,3-диизоцианат, 1,3-бис (метиленизоцианат) адамантан получают с выходом 90%. При взаимодействии адамантансодержащих диизоцианатов с полиэфирами получены каучуки, отличающиеся высокой прочностью, термоустойчивостью до 220— 240 °С, стойкостью к УФ-облучению, гидролитическому воздействию и к действию растворителей. Адамантансодержащие полимеры пригодны для производства специальных эластомеров, искусственных кож, пенопластов, синтетических полимерных покрытий.
Производные адамантана обладают антивирусным действием, в частности 1-аминоадамантан, салицилаты аминоадамантана применяются для профилактики и лечения гриппа и некоторых вирусных заболеваний [38].
Возможности использования циклоалканов в качестве химического сырья далеко не исчерпаны. Их потенциальные возможности огромны. Продолжение их изучения, выделения и исследование химических превращений даст народному хозяйству много ценных продуктов.
АРЕНЫ
Получение и использование аренов освещены в обзорах и монографиях [42—49].
Нефтеперерабатывающая и нефтехимическая промышленность является основным поставщиком аренов (табл. 117) [50]. Большая часть бензола, толуола и ксилолов в мире производится в процессе каталитического риформинга бензиновых фракций нефти с последующим их выделением экстракцией селективными растворителями [43].
317
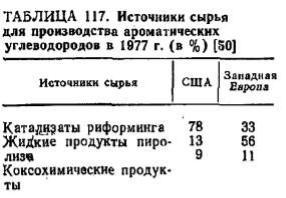
Применение полиметаллических катализаторов серии KP на промышленных установках каталитического риформинга позволило повысить относительный суммарный отбор бензола и толуола на 12—15 %.
С целью увеличения ресурсов бензола и ксилолов разработаны процессы переработки толуола и аренов С9—С10, также образующихся при
риформинге, основанные на реакциях деалкилирования, диспропорционироваиия и трансалкилирования [52]. Комбинированием каталитического риформинга и деалформинга при переработке 1 млн. т фракции 70—180 °C можно получить около 150 тыс. т бензола и 300—350 тыс. т ксилолов. Получающиеся суммарные ксилолы характеризуются очень низким содержанием этилбензола (0,5—2 %), что должно облегчить процесс изомеризации и выделения n- и о-ксилола.
В последние годы отмечается тенденция к увеличению доли аренов, получаемых при пиролизе, что связано с утяжелением сырья пиролиза. При пиролизе остаточных нефтяных фракций и сырой нефти получаются жидкие продукты с высоким содержанием аренов. Например, фракция C5 (200 °С), полученная пиролизом мазута, содержит 90,5 % аренов, в том числе 25,2 % бензола и 27,7 % толуола [53].
Один из наиболее крупнотоннажных продуктов основного органического синтеза — бензол. Данные о мощности действующих и проектирующихся установок для производства бензола по всем странам и регионам мира на 1979 г. приведены в работе [54]. Мощность всех действующих установок составляет около 23 млн. т/год, а проектируемых — около 5 млн. т/год. Основные направления использования бензола — производство этилбензола и далее стирола (45%), фенола (20%), циклогексана (15%), анилина (5%), алкилбензолов (5%). На долю прочих остается около 10 % от потребляемого бензола. Таким образом, главные области применения бензола — производство пластмасс и волокон — например в США — получение полистирола (25%), найлона (20%), других полимеров (10%), синтетических каучуков (5%) [55].
Большую часть этилбензола в промышленности получают алкилированием бензола этиленом, и лишь незначительное количество выделяют сверхчеткой ректификацией из смеси с ксилолами. Алкилирование осуществляется как гомогенное в присутствии хлорида алюминия, так и на твердых гетерогенных катализаторах, в частности на цеолитах, фториде бора [42, 48].
Стирол получают в основном каталитическим дегидрированием этилбензола, например в США около 90% стирола производится по способу [56]. По процессу Оксирейн этилбензол окисляют до гидропероксида, при взаимодействии которого с пропиленом в результате реакции эпоксидирования получается оксид пропилена и метилфенилкарбинол. Последний дегидратацией переводят в стирол. Несмотря на многостадийность, этот процесс оказался достаточно экономичным.
Разработан ряд вариантов окислительного дегидрирования этилбензола в присутствии различных катализаторов [57]. Более мягким окислителем по сравнению с кислородом
318
воздуха является оксид серы (IV), при использовании которого селективность повышается с 86 до 98 % и выход стирола — с 53 до 86 % на этилбензол [58]. Однако недостаток процесса с оксидом серы (IV) — более сильное зауглероживание катализатора и быстрая потеря его активности.
По прогнозам ежегодный прирост мирового потребления стирола будет 6,8 % и к 1983 г. его производство составило 15,5 млн. т/год [59]. Около 94% производимого в мире фенола получается из бензола, в том числе приблизительно 90 % промышленных мощностей приходится на кумольный метод и 4 % — на процессы щелочного плавления бензолсульфокислоты и окислительного хлорирования бензола [60]. Остальное количество фенола получается из толуола через бензойную кислоту.
Реакции, протекающие при окислении кумола и разложении гидропероксида с образованием фенола и ацетона, а также побочных продуктов, рассмотрены в [61]. Направления использования фенола (получение фенолоформальдегидных смол, циклогексана и далее капролактама, дифенилолпропана, о-крезола и 2,6-ксиленола, анилина и т. д.) рассмотрены в работах [42, 62]. Гидрированием бензола получают циклогексан, окислением последнего — циклогексанон и далее оксимированием и бекмановской перегруппировкой — капролактам [63].
Анилин до настоящего времени продолжают получать в основном нитрованием бензола с последующим парофазным гидрированием нитробензола [64]. Расширение производства анилина обусловлено главным образом увеличением спроса на полиуретановые пенопласты, которые могут получаться из анилина через дифенилметандиизоцианат.
Так, в 1979 г. свыше 55 % анилина потреблялось для производства изоцианатов, около 27 % — для получения химикатов, использующихся при переработке каучуков, всего 3,6 % — для производства красителей и небольшие количества анилина — для получения гидрохинона, лекарственных препаратов и гербицидов [65].
В Японии освоено производство анилина аммонолизом фенола. Этот процесс оказался рентабельным, несмотря на более высокую стоимость сырья, вследствие более простой стадии очистки анилина, отсутствия кислотных паров, выбрасываемых в атмосферу и меньших капитальных затрат [66].
Малеиновый ангидрид получают как из бензола, так и из бутана. Производство из бензола продолжает конкурировать с бутановым вариантом, так как в последнем случае, несмотря на относительно низкую стоимость бутана, оказывается более сложной очистка продукта от примесей и требуются реакторы большей вместимости, что приводит к высоким капиталовложениям [67, 68]. В связи с этим основное количество малеинового ангидрида (82%) в развитых капиталистических странах получают окислением бензола [69].
Японскими исследователями разработан процесс одновременного получения резорцина и гидрохинона из бензола и пропилена. В 1980 г. построена установка производительностью 5 тыс. т/год резорцина и 2 тыс. т/год гидрохинона [70, 71].
319

Толуол лишь в незначительной степени сейчас используется для синтеза неуглеводородных органических соединений. Так, в 1977 г, в США 44 % толуола деалкилировалось в бензол, 20 % использовалось как растворитель, 19 % — как добавка к бензину для повышения октанового числа, 2,5 % диспропорционировалось в бензол и ксилолы и только 14,5 % служило сырьем для органического синтеза [72].
Бензол из толуола получают каталитическим гидродеалкилированием в присутствий никелевого катализатора при 680—720 °C с выходом свыше 96% [73]. Деалкилирование может проводиться также с использованием водяного пара:
C6H6CH3 + 2Н2О → C6H6 + CO2+ 3Н2
Реакция протекает либо при 600—800 °C в присутствии катализаторов иттрия, лантана, церия, празеодима, неодима, самария или тория [74], либо при 320—630 °C в случае использования катализаторов никеля — оксида хрома (III) или никеля — оксида алюминия. Выход бензола составляет около 90%. В присутствии платины или палладия на активном оксиде алюминия селективность повышается до 96—98 % [75].
Каталитическим диспропорционированием толуола в присутствии водорода получают смесь бензола и изомеров ксилола [76]. Реакция протекает при 450—530 °C, в качестве катализатора служит оксид кобальта — оксид молибдена (VI) на алюмосиликате или оксиде алюминия, выход составляет 97 % при степени превращения 40 %.
Как отмечалось выше, около 6 % фенола производится из толуола через бензойную кислоту.
Технология производства бензойной кислоты окислением толуола кислородом воздуха с использованием жидкофазного катализатора рассмотрена в работе [76]. Мольный выход бензойной кислоты составляет 90—95 %. Далее получение фенола проводится по процессу компании «Дау кемикл» в расплавленной бензойной кислоте, содержащей соли меди и различные промоторы, при подаче воздуха и водяного пара. Окислителем является медь (II), восстанавливающаяся до меди (I). Из бензоата меди образуется бензоилсалициловая кислота, дальнейшее превращение которой в фенол протекает через фенилбензоат или через салициловую кислоту [60].
320

Основной недостаток метода — образование до 0,1 кг остаточных продуктов на 1 кг фенола, которые нельзя сжигать из-за содержащихся в них солей меди.
Фирмой «Луммус» разработан процесс окисления бензойной кислоты в паровой фазе над новым катализатором, содержащим медь. Процесс проводится с высокой объемной скоростью, и благодаря быстрому удалению фенола из зоны реакции не образуются нелетучие побочные продукты. Процесс более экономичен по сравнению с жидкофазным вариантом и не уступает кумольному методу [60].
Из бензойной кислоты можно получить циклогексанкарбоновую кислоту и далее реакцией с нитрозилсерной кислотой — капролактам [77]. Выход капролактама составляет 85 % от теоретического при расчете на толуол. Важное преимущество этого метода состоит в отсутствии побочного продукта — сульфата аммония.
Диспропорционированием бензоата калия в присутствии оксида углерода (IV) может быть получена терефталевая кислота через ее дикалиевую соль [78]:
Реакция проводится в жидкой фазе при 400 °C в присутствии цинковых или кадмиевых катализаторов.
Японской фирмой «Мицубиси гэс кемикл» разработан процесс производства n-толуилового альдегида из толуола и оксида углерода (II) [79]. Карбонилирование толуола протекает селективно при использовании системы HF - ВF3. Получается n-толуиловый альдегид чистотой 99,3% с выходом 95%, который далее может быть превращен в терефталевую или в надтолуиловую кислоту, из последней можно получать n-крезол, а также различные эпоксиды — оксид пропилена, глицидол, эпихлоргидрин.
Нитрованием толуола получают о- и n-иитротолуол [80], продукты восстановления которых — толуидины — применяются в производстве красителей. n-Нитротолуол используется также для получения n-аминобензойной кислоты, 4-карбоксифенилгидразина аминостильбена [45].
Нитрованием толуола производится 2,4-динитротолуол, из которого получают толуилендиизоцианат по одной из следующих схем [81]:
321

Толуилендиизоцианат — важный мономер для производства полиуретанов [82].
Прямым окислением толуола или гидролизом бензальхлорида может быть получен бензальдегид [45]. Хлорированием толуола получают также бензилхлорид и бензотрихлорид. Из толуола можно получать стильбен, при взаимодействии которого с этиленом образуется стирол [45]:
Предложен способ получения стильбена из толуола и водяного пара в присутствии' катализаторов: оксидов таллия(III), сурьмы (III) и др. при 570 0C. Описано получение из толуола диарилметан- и диарилкетондикарбоновых кислот, которые могут использоваться для производства поликонденсационных смол [84].
Окислительным аммонолизом толуола в Японии получают бепзонитрил [85]. Щелочным плавлением сульфокислот толуола получают смесь крезолов, содержащую 80—85 % n-крезола, а из цимолов по аналогии с кумольным методом — дикрезольную фракцию, представляющую в основном смесь м- и n-крезола [49].
Мощности действующих и проектирующихся установок по производству о- и л-ксилола во всех странах и регионах мира на 1981 г. приведены в работе [86]. Общие мировые мощности действующих установок составляли 2522 тыс. т/год о-ксилола и 5987 тыс. т/год n-ксилола, а проектирующихся — соответственно 587 и 1190 тыс. т/год.
Средний состав ксилольной фракции в зависимости от метода получения приведен в табл. 118 [87].
322

Около 16 % выделенных ксилолов смешивается с бензином, 17 % используется в качестве растворителя и 67 % разделяется на индивидуальные изомеры [71]. о-Ксилол выделяют из ксилольной фракции ректификацией как наиболее высококипящий изомер, а n-ксилол — кристаллизацией [43] или адсорбцией [88]. Выход n-ксилола повышается при использовании процесса изомеризации остающейся фракции [89].
Парофазным окислением о-ксилола в присутствии оксида ванадия (V) при 375—435 °C получают фталевый ангидрид [90]. Селективность процесса возрастает при замене оксида кремния(IV) на оксид титана (IV) [91]. К 1980 г. около 75% фталевого ангидрида производилось из о-ксилола и лишь 25 % — из нафталина [92].
Окислительным аммонолизом о-ксилола получают фталонитрил [93], использующийся в производстве пигментов.
м-Ксилол до настоящего времени в основном изомеризуется в о- и n-изомеры. Окислением м-ксилола сульфитом аммония может быть получена изофталевая кислота
[46]:
Окисление может проводиться также кислородом воздуха в среде уксусной кислоты в присутствии кобальт-бромидного катализатора. Изофталевая кислота применяется для производства ненасыщенных полиэфиров, алкидных смол и пластификаторов [94].
Окислительным аммонолизом м-ксилола получают изофталонитрил, а гидрированием последнего — ксилилендиамин [45]. Сополимеризацией адипиновой кислоты с м-ксилилеидиамином в Японии производят найлон-6,8. м-Ксилилендиамин используется также в качестве исходного продукта для производства м-ксили- лендиизоцианата и полиуретанов на его основе.
Алкилирование м-ксилола пропиленом приводит к 2,4-диметилизопропилбензолу, из которого по аналогии с кумольным методом получают 2,4-ксиленол [94], применяющийся в производстве пластмасс, ядохимикатов, фармацевтических препаратов.
n-Ксилол практически полностью потребляется для производства терефталевой кислоты и диметилтерефталата, из которых получают полиэфирные волокна [42, 45,
323
78]. Направления использования полиметилбензолов рассмотрены в работах [42, 45,
95].
Из фракции C9 катализата риформинга ректификацией выделяют псевдокумол [96]. Разработан и метод выделения мезитилена, включающий следующие стадии: гидрирование мезитиленовой фракции, ректификация гидрогенизата с выделением 1,3,5-три- метилциклогексанов, дегидрированием которых получают мезитилен [97].
Окислением псевдокумола получают тримеллитовую кислоту и тримеллитовый ангидрид [70], которые применяются для производства пластификаторов, полиэфироимидных и полиамидимидных лакокрасочных покрытий, в качестве отвердителя эпоксидных смол [98].
Нитрованием псевдокумола с последующим восстановлением получают 2,4,5-триметиланилин (псевдокумидин) — полупродукт для синтеза красителей и витамина E [99]. Алкилированием псевдокумола пропиленом можно получать триметилизопропилбензол, а при алкилировании метилхлоридом в присутствии хлорида алюминия — тетраметилбензолы, содержащие 48 % (по массе) дурола.
При алкилировании мезитилена метанолом в присутствии алюмосиликатов, получается фракция тетраметилбензолов, содержащая 85—95 % изодурола [100].
Мезитилен применяется для производства тримезиновой кислоты, мезидина (2,4,6-триметиланилина) — полупродукта для промышленности красителей [46]. Перспективно получение из мезитилена антиокислителей, некрасящих стабилизаторов для пластмасс.
Хлорированием мезитилена можно получать смесь продуктов, обогащенную 1,3,5-трис(трихлорметил) бензолом, которая может использоваться в качестве противоизносной присадки к смазочным маслам [101].
Среди тетраметилбензолов наиболее важный изомер — дурол, окислением которого производится пиромеллитовый диангидрид [48, 102]. Из пиромеллитового диангидрида и ароматических диаминов получают полипиромеллитимиды, сохраняющие рабочие свойства в интервале от —270 до 500 °С.
Нафталин и поликонденсированные арены в настоящее время получают при переработке коксохимической смолы. Перспективно выделение нафталина из жидких продуктов пиролиза на мощных этиленовых установках при использовании газойля в качестве сырья. Так, на установке ЭП-300 при пиролизе бензина может быть выделено всего 6—6,5 тыс. т/год нафталина, а при пиролизе дизельного топлива 18—24 тыс. т/год нафталина [103]. Получающийся нафталин, в отличие от коксохимического, почти не содержит бензотиофена, а примеси алкенов легко могут быть удалены с помощью гидрогенизационного метода.
Разработаны также процессы производства нафталина гидродеалкилированием алкилнафталинов, содержащихся в тяжелых фракциях катализатов риформинга и в каталитических крекинг-газойлях [104].
324