
- •Предисловие
- •1.2. КРАТКИЕ ИСТОРИЧЕСКИЕ СВЕДЕНИЯ О РАЗВИТИИ ПРОМЫШЛЕННОГО ПРОИЗВОДСТВА ЛЕКАРСТВ
- •1.3. ОСНОВНЫЕ ТЕРМИНЫ И ПОНЯТИЯ
- •1.4. ПРИНЦИПЫ КЛАССИФИКАЦИИ ЛЕКАРСТВЕННЫХ ФОРМ
- •1.5. ЭФФЕКТИВНОСТЬ ЛЕКАРСТВ И БИОФАРМАЦИЯ
- •1.6. ПРОБЛЕМЫ И ПУТИ СОВЕРШЕНСТВОВАНИЯ ФАРМАЦЕВТИЧЕСКОЙ ТЕХНОЛОГИИ
- •2.1. ОСНОВНЫЕ ПОНЯТИЯ О ТАРЕ И УПАКОВКЕ
- •2.2. МАТЕРИАЛЫ И МЕТОДЫ ИЗГОТОВЛЕНИЯ УПАКОВКИ
- •2.2.1. Полимерные материалы
- •2.2.2. Медицинское стекло
- •2.2.3. Картон и бумага
- •2.2.4. Металлическая тара
- •2.2.5. Эластомеры и резина
- •2.2.6. Комбинированная тара
- •2.3. ТЕХНОЛОГИЯ УПАКОВКИ ЛЕКАРСТВЕННЫХ ФОРМ
- •2.3.1. Упаковка твердых лекарственных форм
- •2.3.2. Упаковка мягких лекарственных форм
- •2.3.3. Упаковка жидких лекарственных средств
- •2.3.4. Упаковывание в групповую упаковку
- •2.4. МАРКИРОВКА УПАКОВОК
- •2.4.1. Современные технологии маркировки продукции
- •2.5. НОВЫЕ ВИДЫ УПАКОВКИ ЛС
- •2.6. ПРОБЛЕМА ФАЛЬСИФИКАЦИИ ЛЕКАРСТВЕННЫХ СРЕДСТВ
- •2.6.1. Факторы, способствующие распространению фальсификатов
- •2.6.2. Технологии предупреждения фальсификации ЛС
- •3.1. ПРОМЫШЛЕННОЕ ПРОИЗВОДСТВО СБОРОВ
- •3.1.1. Классификация сборов
- •3.1.2. Первичная обработка сырья
- •3.1.3 Сушка лекарственного растительного сырья
- •3.1.4. Доведение растительного сырья до стандартного состояния
- •3.1.5 Приготовление сборов
- •3.1.6. Частная технология сборов
- •3.2. ПРОМЫШЛЕННОЕ ПРОИЗВОДСТВО ПОРОШКОВ
- •3.2.1 Технология порошков
- •3.2.2 Частная технология и номенклатура порошков
- •4.1. ХАРАКТЕРИСТИКА И КЛАССИФИКАЦИЯ ТАБЛЕТОК
- •4.2. СВОЙСТВА ПОРОШКООБРАЗНЫХ ЛЕКАРСТВЕННЫХ СУБСТАНЦИЙ
- •4.2.2. Технологические свойства
- •4.3. ОСНОВНЫЕ ГРУППЫ ВСПОМОГАТЕЛЬНЫХ ВЕЩЕСТВ В ПРОИЗВОДСТВЕ ТАБЛЕТОК
- •4.4. ТЕХНОЛОГИЧЕСКИЙ ПРОЦЕСС ПРОИЗВОДСТВА ТАБЛЕТОК
- •4.4.1. Прямое прессование
- •4.5. ФАКТОРЫ, ВЛИЯЮЩИЕ НА БИОДОСТУПНОСТЬ ЛЕКАРСТВЕННЫХ ВЕЩЕСТВ ИЗ ТАБЛЕТОК
- •4.6. ТИПЫ ТАБЛЕТОЧНЫХ МАШИН
- •4.7. ФАКТОРЫ, ВЛИЯЮЩИЕ НА ОСНОВНЫЕ КАЧЕСТВА ТАБЛЕТОК
- •4.8. ПОКРЫТИЕ ТАБЛЕТОК ОБОЛОЧКАМИ
- •4.8.1. Дражированные покрытия
- •4.8.2. Пленочные покрытия
- •4.8.3. Прессованные покрытия
- •4.9. КОНТРОЛЬ КАЧЕСТВА ТАБЛЕТОК
- •4.11. УСЛОВИЯ ХРАНЕНИЯ ТАБЛЕТОК
- •4.12. ПУТИ СОВЕРШЕНСТВОВАНИЯ ТАБЛЕТОК
- •4.13. ГРАНУЛЫ. ПЕЛЛЕТЫ. ДРАЖЕ. ЛЕДЕНЦЫ. РЕЗИНКИ ЖЕВАТЕЛЬНЫЕ ЛЕКАРСТВЕННЫЕ. ПЛИТКИ
- •4.14. КОНДИТЕРСКИЕ ЛЕКАРСТВЕННЫЕ ФОРМЫ
- •5.1. ОБЩАЯ ХАРАКТЕРИСТИКА МИКРОКАПСУЛ
- •5.2. СТРОЕНИЕ МИКРОКАПСУЛ
- •5.3. ХАРАКТЕРИСТИКА ОБОЛОЧЕК МИКРОКАПСУЛ
- •5.4. МЕТОДЫ МИКРОКАПСУЛИРОВАНИЯ
- •5.4.1. Характеристика физических методов
- •5.4.3. Химические методы
- •5.5. СТАНДАРТИЗАЦИЯ МИКРОКАПСУЛ
- •5.7. ПЕРСПЕКТИВЫ РАЗВИТИЯ ТЕХНОЛОГИИ МИКРОКАПСУЛИРОВАНИЯ
- •6.1. СОВРЕМЕННАЯ КЛАССИФИКАЦИЯ И ОБЩАЯ ХАРАКТЕРИСТИКА
- •6.2. ХАРАКТЕРИСТИКА ОСНОВНЫХ И ВСПОМОГАТЕЛЬНЫХ ВЕЩЕСТВ
- •6.3. ПРОИЗВОДСТВО ЖЕЛАТИНОВЫХ КАПСУЛ
- •6.4. МЯГКИЕ ЖЕЛАТИНОВЫЕ КАПСУЛЫ
- •6.5. ТВЕРДЫЕ ЖЕЛАТИНОВЫЕ КАПСУЛЫ
- •6.6. АВТОМАТЫ ДЛЯ НАПОЛНЕНИЯ КАПСУЛ
- •6.6.1. Методы инкапсулирования
- •6.7. КОНТРОЛЬ КАЧЕСТВА И УПАКОВКА КАПСУЛ
- •6.8. РЕКТАЛЬНЫЕ ЖЕЛАТИНОВЫЕ КАПСУЛЫ
- •6.9. ФАКТОРЫ, ВЛИЯЮЩИЕ НА БИОДОСТУПНОСТЬ ЛЕКАРСТВЕННЫХ ВЕЩЕСТВ В ЖЕЛАТИНОВЫХ КАПСУЛАХ
- •7.1. ТЕОРЕТИЧЕСКИЕ ОСНОВЫ ПРОЦЕССА РАСТВОРЕНИЯ
- •7.1.1. Механизмы и типы растворения
- •7.1.2. Теория гидратации
- •7.1.3. Способы обтекания частиц жидкостью
- •7.1.4. Растворы твердых веществ
- •7.1.5. Растворы жидких веществ
- •7.2. ХАРАКТЕРИСТИКА РАСТВОРИТЕЛЕЙ
- •7.2.1. Водные растворители
- •7.2.2. Водоподготовка
- •7.2.3. Неводные растворители
- •7.3. ТЕХНОЛОГИЯ ЖИДКИХ ЛЕКАРСТВЕННЫХ ФОРМ
- •7.3.1. Растворение веществ
- •7.3.2. Очистка растворов
- •7.3.3. Устройство и принцип действия аппаратов для фильтрования
- •7.3.4. Центрифугирование
- •7.3.5. Фасовка и упаковка растворов
- •7.4. ФАРМАЦЕВТИЧЕСКИЕ РАСТВОРЫ
- •7.4.1. Водные растворы
- •7.4.2. Спиртовые растворы
- •7.4.3. Глицериновые растворы
- •7.4.4. Масляные растворы
- •7.5. КАПЛИ
- •7.5.1. Назальные капли и жидкие аэрозоли
- •7.5.2. Ушные капли и аэрозоли
- •7.6. СИРОПЫ
- •7.6.1. Вкусовые сиропы
- •7.6.2. Лекарственные сиропы
- •8.1. ТЕОРЕТИЧЕСКИЕ ОСНОВЫ ЭКСТРАГИРОВАНИЯ
- •8.1.2. Стадии процесса экстрагирования
- •8.1.3. Основные факторы, влияющие на полноту и скорость экстрагирования
- •8.2. ТРЕБОВАНИЯ К ЭКСТРАГЕНТАМ
- •8.3. МЕТОДЫ ЭКСТРАГИРОВАНИЯ
- •8.3.1. Классификация методов экстрагирования
- •8.3.3. Перколяция
- •8.3.6. Циркуляционное экстрагирование
- •8.3.7. Интенсивные методы экстракции
- •8.5. НАСТОЙКИ
- •8.6. ЭКСТРАКТЫ
- •8.6.4. Комбинированные фитопрепараты
- •8.6.5. Масляные экстракты
- •8.7. КОМПЛЕКСНАЯ ПЕРЕРАБОТКА ЛРС
- •8.7.1. Препараты облепихи
- •8.7.2. Препараты шиповника
- •8.8. НОВЫЕ ТЕХНОЛОГИИ ПРОИЗВОДСТВА ФИТОПРЕПАРАТОВ
- •8.8.1. Полиэкстракты
- •9.1. ХАРАКТЕРИСТИКА НОВОГАЛЕНОВЫХ ПРЕПАРАТОВ
- •9.2. ОСОБЕННОСТИ ПРОИЗВОДСТВА
- •9.3.1. Осаждение БАВ из растворов
- •9.3.2. Разделение БАВ с помощью мембран
- •9.3.3. Сорбция
- •9.3.4. Адсорбционно-хроматографические методы
- •9.3.5. Афинная хроматография
- •9.3.6. Электрофорез
- •9.4. ПРЕПАРАТЫ ИНДИВИДУАЛЬНЫХ ВЕЩЕСТВ
- •9.4.1. Алкалоиды
- •9.4.2. Флавоноиды
- •9.4.4. Сердечные гликозиды
- •9.4.5. Стероидные сапонины
- •10.1. ХАРАКТЕРИСТИКА ЭФИРНЫХ МАСЕЛ
- •10.2. МЕТОДЫ ПОЛУЧЕНИЯ ЭФИРНЫХ МАСЕЛ
- •10.3. ОПРЕДЕЛЕНИЕ КАЧЕСТВА ЭФИРНЫХ МАСЕЛ
- •10.4. ХРАНЕНИЕ ЭФИРНЫХ МАСЕЛ
- •10.5. ПРИМЕНЕНИЕ ЭФИРНЫХ МАСЕЛ
- •10.6. АРОМАТНЫЕ ВОДЫ
- •10.7. БАЛЬЗАМЫ
- •11.1. ПРЕПАРАТЫ ИЗ СВЕЖИХ РАСТЕНИЙ
- •11.2. СПОСОБЫ ПОЛУЧЕНИЯ СОКОВ ИЗ СВЕЖЕГО РАСТИТЕЛЬНОГО СЫРЬЯ
- •11.3. НЕСГУЩЕННЫЕ (НАТУРАЛЬНЫЕ) СОКИ РАСТЕНИЙ
- •11.4. СГУЩЕННЫЕ СОКИ
- •11.5. СУХИЕ СОКИ
- •11.8. СОВРЕМЕННЫЕ СВЕДЕНИЯ О ХИМИЧЕСКОЙ ПРИРОДЕ БИОГЕННЫХ СТИМУЛЯТОРОВ
- •11.9. БИОГЕННЫЕ ПРЕПАРАТЫ РАСТИТЕЛЬНОГО ПРОИСХОЖДЕНИЯ
- •11.10. БИОСТИМУЛЯТОРЫ ЖИВОТНОГО ПРОИСХОЖДЕНИЯ
- •11.11. ПРЕПАРАТЫ ИЗ ИЛОВОЙ ЛЕЧЕБНОЙ ГРЯЗИ (МИНЕРАЛЬНОГО ПРОИСХОЖДЕНИЯ)
- •11.12. СТАНДАРТИЗАЦИЯ ПРЕПАРАТОВ БИОГЕННЫХ СТИМУЛЯТОРОВ
ТАБЛЕТКИ. ГРАНУЛЫ. ДРАЖЕ. ПЕЛЛЕТЫ. ЛЕДЕНЦЫ. РЕЗИНКИ ЖЕВАТЕЛЬНЫЕ …
4.4.1. Прямое прессование
Метод прямого прессования обладает рядом преимуществ. Он позволяет достичь высокой производительности труда, значительно сократить время технологического цикла за счет упразднения ряда операций и стадий, исключить использование нескольких позиций оборудования, уменьшить производственные площади, сократить энерго- и трудозатраты, значительно снижая себестоимость таблеток. Прямое прессование дает возможность получать таблетки из влаго-, термолабильных и несовместимых веществ. На сегодняшний день, однако, этим методом получают незначительное количество наименований таблеток. Это объясняется тем, что большинство лекарственных веществ не обладают свойствами, обеспечивающими непосредственное их прессование. К этим свойствам относятся: изодиаметрическая форма кристаллов, хорошая текучесть и прессуемость, низкая адгезионная способность к пресс-инструменту таблеточной машины.
Прямое прессование – это совокупность различных технологических приемов, позволяющих улучшить основные технологические свойства таблетируемого материала (текучесть и прессуемость) и получить из него таблетки, минуя стадию грануляции.
В настоящее время прямое прессование осуществляется:
1)путем непосредственного таблетирования сыпучих лекарственных веществ с хорошей прессуемостью;
2)с добавлением вспомогательных веществ, улучшающих технологические свойства материала;
3)принудительной подачей таблетируемого материала из загрузочной воронки таблеточной машины в матрицу;
4)с предварительной направленной кристаллизацией прессуемого веще-
ства.
Большое значение для прямого прессования имеют величина, прочность частиц, прессуемость, текучесть, влажность и другие свойства веществ. Так, для получения таблеток натрия хлорида приемлемой является продолговатая форма частиц, а круглая форма этого вещества почти не поддается прессованию. Наиболее хорошая текучесть отмечается у крупнодисперсных порошков с равноосной формой частиц и малой пористостью – таких, как лактоза, фенилсалицилат, гексаметилентетрамин и другие подобные препараты, входящие в
ТАБЛЕТКИ. ГРАНУЛЫ. ДРАЖЕ. ПЕЛЛЕТЫ. ЛЕДЕНЦЫ. РЕЗИНКИ ЖЕВАТЕЛЬНЫЕ …
эту группу. Поэтому такие препараты могут быть спрессованы без предварительного гранулирования. Наилучшим образом зарекомендовали себя лекарственные порошки с размером частиц 0,5-1,0 мм, углом естественного откоса менее 42º, плотностью после усадки более 330 кг/м3, пористостью менее 37%. Они состоят из достаточного количества изодиаметрических частиц приблизительно одинакового фракционного состава и, как правило, не содержат большого количества мелких фракций. Их объединяет способность равномерно высыпаться из воронки под действием собственной массы, т.е. способность самопроизвольного объемного дозирования, а также достаточно хорошая прессуемость.
Однако подавляющее большинство лекарственных веществ не способно к самопроизвольному дозированию вследствие значительного (более 70%) содержания мелких фракций и неравномерностей поверхности частиц, вызывающих сильное межчастичное трение. В этих случаях добавляют скользящие вспомогательные вещества. Таким методом получают таблетки витаминов, алкалоидов, гликозидов, кислоты ацетилсалициловой, бромкамфоры, фенолфталеина, сульфадимезина, фенобарбитала, эфедрина гидрохлорида, кислоты аскорбиновой, натрия гидрокарбоната, кальция лактата, стрептоцида и другие.
Предварительная направленная кристаллизация – один из наиболее сложных способов получения лекарственных веществ, пригодных для непосредственного прессования. Этот способ осуществляется двумя методами:
–перекристаллизацией готового продукта в необходимых условиях;
–подбором определенных условий кристаллизации синтезируемого
продукта.
Применяя эти методы, получают кристаллическое лекарственное вещество с кристаллами достаточно изодиаметрической (равноосной) структуры, которая свободно высыпается из воронки и вследствие этого легко подвергается самопроизвольному объемному дозированию, что является непременным условием прямого прессования. Данный метод используется для получения таблеток кислот ацетилсалициловой и аскорбиновой.
Для повышения прессуемости лекарственных веществ при прямом прессовании в состав порошковой смеси вводят сухие связывающие вещества: МКЦ, макрогол, Плаздон S -630 и др. Благодаря своей способности поглощать воду и гидратировать отдельные слои таблеток, МКЦ оказывает благоприятное воздействие на процесс высвобождения лекарственных веществ. С МКЦ можно изгото-

ТАБЛЕТКИ. ГРАНУЛЫ. ДРАЖЕ. ПЕЛЛЕТЫ. ЛЕДЕНЦЫ. РЕЗИНКИ ЖЕВАТЕЛЬНЫЕ …
вить прочные, но не всегда хорошо распадающиеся таблетки. Для улучшения распадаемости таблеток с МКЦ рекомендуют добавлять ультраамилопектин.
При прямом прессовании показано применение модифицированных крахмалов. Последние вступают в химическое взаимодействие с лекарственными веществами, значительно влияя на высвобождение и их биологическую активность.
Часто используют молочный сахар, как вещество, улучшающее сыпучесть порошков, а также гранулированный кальция сульфат, обладающий хорошей текучестью и обеспечивающий получение таблеток с достаточной механической прочностью. Комбинация α-лактозы моногидрата (100 меш1) с МКЦ дает эффект синергизма при распадаемости таблеток. С повышением содержания МКЦ в смеси с тойкость таблеток к раздавливанию увеличивается. Применяют также циклодекстрин, способствующий увеличению механической прочности таблеток и их распадаемости.
При прямом таблетировании рекомендована мальтоза, обеспечивающая равномерную скорость засыпки и как вещество, обладающее незначительной гигроскопичностью. Также применяют гранулят «Лудипресс» – смесь лактозы моногидрата и двух полимеров: Коллидона 30 и Коллидона СL. Лудипресс может использоваться как наполнитель, как связующее, скользящее и разрыхляющее средство.
Технология приготовления таблеток заключается в том, что лекарственные препараты тщательно смешивают с необходимым количеством вспомогательных веществ и прессуют на таблеточных машинах. Недостатком этого способа является возможность расслаивания таблетируемой массы, изменения дозировки при прессовании с незначительным количеством действующих веществ и используемое высокое давление. Некоторые из этих недостатков сводятся к минимуму при таблетировании путем принудительной подачи прессуемых веществ в матрицу. Это достигается некоторыми конструктивными изменениями деталей машины, то есть вибрацией питателей-дозаторов, поворотом матрицы в определенный угол в процессе прессования, установлением в загрузочную воронку звездообразных мешалок разных конструкций, засасыванием материала в матричное отверстие при помощи самосоздаваемого вакуума или специальным соединением с вакуум-линией.
1 Меш – число отверстий на 1 погонный дюйм (25,4 мм) сита. 100 меш соответствует размеру отверстий сита
0,147 мм

ТАБЛЕТКИ. ГРАНУЛЫ. ДРАЖЕ. ПЕЛЛЕТЫ. ЛЕДЕНЦЫ. РЕЗИНКИ ЖЕВАТЕЛЬНЫЕ …
Наиболее перспективной является принудительная подача прессуемых веществ на основе вибрации загрузочных воронок в сочетании с приемлемой конструкцией ворошителей.
Благодаря появлению высокоэффективных вспомогательных веществ и новых конструкций таблеточных машин, прямое прессование находит все большее применение в производстве таблеток. Но пока основное количество таблеток получают по технологии с предварительной грануляцией.
4.4.2. Грануляция Грануляция – направленное укрупнение частиц, т.е. – это процесс пре-
вращения порошкообразного материала в агрегаты определенной величины. Грануляция необходима для улучшения текучести таблетируемой массы,
что происходит в результате значительного уменьшения суммарной поверхности частиц при их слипании в гранулы и, следовательно, соответствующего уменьшения трения, возникающего между этими частицами при движении. Расслоение многокомпонентной порошкообразной смеси обычно происходит за счет разницы в размерах частиц и значениях удельной плотности входящих в ее состав лекарственных и вспомогательных компонентов. Такое расслоение воз-

ТАБЛЕТКИ. ГРАНУЛЫ. ДРАЖЕ. ПЕЛЛЕТЫ. ЛЕДЕНЦЫ. РЕЗИНКИ ЖЕВАТЕЛЬНЫЕ …
можно при различного рода вибрациях таблеточной машины или ее воронки. Расслоение таблетируемой массы – это опасный и недопустимый процесс, вызывающий в ряде случаев почти полное выделение компонента с наибольшей удельной плотностью из смеси и нарушение ее дозировки. Грануляция предотвращает эту опасность, поскольку в ее процессе происходит слипание частиц различной величины и удельной плотности. Образующийся при этом гранулят, при условии равенства размеров получаемых гранул, приобретает достаточно постоянную насыпную плотность. Большую роль играет также прочность гранул: прочные гранулы меньше подвержены истиранию и обладают лучшей сыпучестью.
В настоящее время в фармацевтической промышленности используют следующие методы грануляции: 1) сухая грануляция; 2) влажная грануляция; 3) смешанная грануляция; 4) структурная грануляция.
Метод сухой грануляции заключается в перемешивании лекарственных и вспомогательных веществ, первоначальном их уплотнении с последующим размолом в крупный порошок или гранулы. Полученные гранулы фракционируют с помощью сит, опудривают антифрикционными веществами, и затем прессуют на таблеточных машинах таблетки заданной массы и диаметра, то есть проводят вторичное уплотнение.
Первоначальное уплотнение порошков осуществляют двумя способами: брикетированием и компактированием. По первому способу из порошка прессуют брикеты на специальных брикетировочных прессах с матрицами большого размера (25-50 мм) под высоким давлением. Полученные брикеты измельчают на валковой дробилке или дисковой мельнице. Также разламывание брикетов проводят в горизонтальном грануляторе, рабочий орган которого состоит из двух шнеков, снабженных протирочными стержнями, что позволяет перемещать гранулируемый материал в осевом направлении. Шнеки продавливают брикеты через перфорированную пластину, образующую дно рабочей камеры.
Производительность установки
– 150-1000 кг/ч.
Второй способ заключается в уплотнении смеси порошков под давлением при ее прохождении между двумя вра-
Привод валка
Рис. 4.8. Принцип давления на валки ролл-компактора
ТАБЛЕТКИ. ГРАНУЛЫ. ДРАЖЕ. ПЕЛЛЕТЫ. ЛЕДЕНЦЫ. РЕЗИНКИ ЖЕВАТЕЛЬНЫЕ …
щающимися навстречу друг другу горизонтальными валками в валковом компакторе или ролл-компакторе (рис. 4.8). Сформированный в пластины материал разбивается на гранулы в измельчителе, находящемся в нижней части установки. Размер готовых гранул определяется отверстиями сита, расположенного под измельчителем.
Качественные гранулы одинаковой чечевидной формы могут быть получены в пресс-грануляторе фирмы «ХУТТ» (Германия), рабочим органом которого являются прессующие валки в виде полых цилиндров с зубцами на поверхности, между которыми в стенках расположены радиальные отверстия для продавливания порошковой массы. Внутри валков установлен нож, срезающий гранулы.
Сухая грануляция используется в тех случаях, когда лекарственные вещества в присутствии воды или в процессе сушки при повышенной температуре разлагаются, вступают в химические реакции взаимодействия или подвергаются физическим изменениям (плавление, размягчение, изменение цвета). Грануляцию брикетированием можно применять также для лекарственных веществ с хорошей прессуемостью, но недостаточной текучестью.
При сухом методе грануляции в состав таблетируемой массы порошков могут вводить сухие связывающие вещества (например, МКЦ, макрогол, Плаздон S-630), обеспечивающие под давлением сцепление частиц, как гидрофильных, так и гидрофобных веществ. Но этот прием не всегда приводит к получению прочных таблеток.
Метод влажной грануляции. Данному методу грануляции подвергаются порошки, имеющие плохую текучесть и недостаточную способность к сцеплению между частицами. В обоих случаях в массу добавляют растворы связывающих веществ, которые улучшают сцепление между частицами. Влажная грануляция является распространенным видом грануляции в производстве таблеток и проводится такими способами, как: грануляция продавливанием и грануляция в высокоскоростном смесителе-грануляторе.
Получение массы для таблетирования с использованием метода влажной грануляции продавливанием включает следующие операции: смешивание и увлажнение порошков; грануляция влажной массы; сушка влажных гранул; получение сухих гранул; опудривание сухих гранул.
ТАБЛЕТКИ. ГРАНУЛЫ. ДРАЖЕ. ПЕЛЛЕТЫ. ЛЕДЕНЦЫ. РЕЗИНКИ ЖЕВАТЕЛЬНЫЕ …
Смешивание и увлажнение порошков. Смешивание сухих лекарствен-
ных порошков со вспомогательными веществами с последующим увлажнением смеси раствором связывающих веществ проводится в смесителях с вращающимися лопастями. Увлажнитель добавляют в массу отдельными порциями с непрерывным перемешиванием, что необходимо для предотвращения ее комкования.
При влажном смешивании порошков равномерность их распределения в значительной степени улучшается, не наблюдается разделения частиц и расслоения массы, улучшается ее пластичность. Перемешивание смоченных порошков сопровождается некоторым уплотнением массы вследствие вытеснения воздуха, что позволяет получать более плотные твердые гранулы. Время перемешивания влажной массы: для простых смесей 7-10 минут, для сложных – 1520 минут. Оптимальное количество увлажнителя определяется экспериментально (исходя из физико-химических свойств порошков) и указывается в регламенте. Ошибка может привести к браку: если увлажнителя ввести мало, то гранулы после сушки будут рассыпаться, если много – масса будет вязкой, липкой и плохо гранулируемой. Масса с оптимальной влажностью представляет собой влажную, компактную смесь, не прилипающую к руке, но рассыпающуюся при сдавливании на отдельные комочки.
Действующие вещества вводят в виде тритураций как в процессе подготовки массы к таблетированию, так и при опудривании готового гранулята.
Небольшие количества препарата в состав таблеток могут вводиться и следующим способом. Лекарственное вещество растворяют в подходящем растворителе или растворе гранулирующего агента. Затем полученным раствором увлажняют смесь компонентов рецептуры в смесителе с последующей сушкой. Одновременно с растворением препарата можно растворять вспомогательные вещества, обеспечивающие получение твердодисперсных систем. Введение препарата данным методом обеспечивает однородность дозирования в процессе производства таблеток.
Грануляция влажной массы. Влажная масса гранулируется на специальных машинах-грануляторах, принцип работы которых состоит в том, что материал протирается лопастями, пружинящими валиками или другими приспособ-

ТАБЛЕТКИ. ГРАНУЛЫ. ДРАЖЕ. ПЕЛЛЕТЫ. ЛЕДЕНЦЫ. РЕЗИНКИ ЖЕВАТЕЛЬНЫЕ …
лениями через перфорированный цилиндр или сетку. Грануляторы бывают
вертикальные (рис. 4.9) и горизонтальные.
1
2
3
4
5
Рис. 4.9. Гранулятор вертикальный:
1 – цилиндр с отверстиями; 2 – протирающие лопасти; 3 – электродвигатель; 4 – коническая передача; 5 – приемник гранул.
Для обеспечения процесса протирания машина должна работать на оптимальном режиме без перегрузки так, чтобы влажная масса свободно проходила через отверстия цилиндра или сетки. Если масса достаточно увлажнена и в меру пластична, то она не заклеивает отверстия и процесс проходит без затруднений. Если же масса вязкая и заклеивает отверстия, машина работает с перегрузкой и необходимо периодически выключать мотор, промывать лопасти барабана.
Выбор сит для гранулирования имеет очень большое значение. Установлено, что влажную массу необходимо пропускать через сито с диаметром отверстий 3–5 мм, а уже сухие гранулы– через сито с диаметром отверстий 1–2 мм.
Несмотря на улучшение технологических свойств таблетируемых материалов, влажная грануляция продавливанием имеет ряд недостатков:
–длительное воздействие влаги на лекарственные и вспомогательные вещества;
–ухудшение распадаемости и растворимости таблеток;
–использование ряда специальных машин и аппаратов для каждой опе-
рации;
ТАБЛЕТКИ. ГРАНУЛЫ. ДРАЖЕ. ПЕЛЛЕТЫ. ЛЕДЕНЦЫ. РЕЗИНКИ ЖЕВАТЕЛЬНЫЕ …
–длительность и трудоемкость процесса, поскольку перегрузка продукта из одной единицы оборудования в другую, как правило, выполняется вручную;
–большие потери обрабатываемых материалов.
Сушка влажных гранул. Для этой цели су ществуют различные типы сушилок. Наибольшее распространение получили сушилки псевдоожиженного («кипящего») слоя. Принцип действия сушилок заключается в разрыхлении продукта воздушным потоком и приведении его во взвешенное состояние. Сушильные аппараты фирм «Глатт» (Германия), «ИMA» (Италия), «Мюнстер», «Аэроматик-Филдер» (Швейцария), «Ниро» (США) имеют подобную конструкцию (рис. 4.10) и работают следующим образом. Приточный поток воздуха поступает в блок подготовки, где проходит вначале через фильтр грубой очистки, затем омывает внешнюю поверхность трубчатого змеевика-охладителя, который установлен для снижения влагосодержания воздуха. Часть потока осушенного воздуха отводится через заслонки на нагрев в паровой калорифер и далее смешивается с потоком холодного воздуха. Заслонки, перекрывающие потоки воздуха, механически связаны и, когда несколько заслонок открыты и пропускают воздух, то другие в это время закрыты. Для регулирования температуры сушки между температурой потока воздуха Твх и положением заслонок устанавливается контур обратной связи. Если температура сушки снижается ниже заданного значения, заслонки переводятся в положение, позволяющее отводить большую часть входящего потока воздуха в калорифер для увеличения температуры смешанного потока воздуха. Если температура сушки отклоняется в сторону значения выше заданного, часть заслонок закрывается для снижения потока через калорифер. Преимуществом такой системы регулирования температуры является короткое время ответа. Нагретый сухой воздух затем проходит через фильтр тонкой очистки, фильтр с высокой эффективностью очистки типа НЕРА и направляется в сушильную камеру.

ТАБЛЕТКИ. ГРАНУЛЫ. ДРАЖЕ. ПЕЛЛЕТЫ. ЛЕДЕНЦЫ. РЕЗИНКИ ЖЕВАТЕЛЬНЫЕ …
9 |
10 |
11 |
Твых
Отработанный
воздух
8
7
5 4
6 |
L |
|
Свежий
воздух
Твх
3 |
2 |
1 |
Рис. 4.10. Схема сушильной установки с псевдоожиженным слоем:
1 – фильтр грубой очистки воздуха; 2 – змеевик охладитель; 3 – заслонки; 4 – калорифер; 5 – фильтр тонкой очистки воздуха и НЕРА-фильтр; 6 – продуктовый резервуар; 7 – сушильная камера; 8 – рукавные фильтры; 9 – клапан регулирования потока воздуха; 10 – вентилятор; 11 – фильтры очистки отработанного воздуха
Продукт, подлежащий высушиванию, помещается в резервуар сушильной камеры, снабженный перфорированным днищем, которое имеет отверстия специальной изогнутой формы или покрывается мелкоячеистой металлической сеткой из нержавеющей стали. Поток воздуха проходит через резервуар снизу вверх, псевдоожижая слой продукта. Продуктовый резервуар имеет форму перевернутого усеченного конуса. Увеличивающееся кверху сечение резервуара способствует снижению скорости потока воздуха, что уменьшает вынос частиц из псевдоожиженного слоя. Обычно скорость воздуха возле сетки составляет 1,5-2,5 м/с и снижается после расширения резервуара до 0,6-1,0 м/с. Во время процесса сушки соответственно с уменьшением плотности гранул скорость воздуха может быть снижена.
Далее увлажненный воздух проходит через рукавные фильтры, которые предупреждают унос частиц из сушильной камеры. Фильтры периодически встряхиваются без прерывания процесса сушки для удаления накопленного порошка. Рукавные фильтры могут располагаться в двух отделах. В этом случае поток воздуха через один отдел прекращается, и фильтровальная ткань прохо-
ТАБЛЕТКИ. ГРАНУЛЫ. ДРАЖЕ. ПЕЛЛЕТЫ. ЛЕДЕНЦЫ. РЕЗИНКИ ЖЕВАТЕЛЬНЫЕ …
дит дополнительную очистку продувкой чистым воздухом в направлении, обратном движению ожижающего воздуха. Затем поток возобновляется, и операция очистки проводится в другом отделе. Вместо полипропиленовых, полиэфирных или нейлоновых рукавных фильтров могут использоваться плиссированные патронные фильтры, изготовленные из трех слоев стальной сетки, и очищаемые продувкой.
Ожижающий воздух всасывается вентилятором, расположенным в установке после сушильной камеры. Расход воздуха L регулируется клапаном. При этом в камере создается небольшое разрежение, что препятствует попаданию частиц продукта и паров органических растворителей в окружающую среду. Перед выбросом в атмосферу используемый воздух пропускается через фильтр тонкой очистки и НЕРА-фильтр для удаления биологически активных и потенциально опасных частиц продукта, которые могут пройти через рукавные фильтры. При использовании органических растворителей перед выбросом в атмосферу из отработанного воздуха должны быть удалены их пары. Сушильная установка полностью автоматизирована и изготавливается во взрывобезопасном исполнении.
Основное преимущество сушилок псевдоожиженного слоя – высокая производительность: время сушки материала в зависимости от его физических свойств и формы длится от 20 до 50 мин; они потребляют мало энергии и зан и- мают небольшую рабочую площадь. Но к недостаткам следует отнести возможность излишнего истирания некоторых высушиваемых гранулятов с образованием порошковой фракции.
В отличие от сушил ьных установок, приведенных выше, эксплуатируемые в производстве таблеток аппараты псевдоожиженного слоя СП-30, СП-60 (НПО «Прогресс», Cанкт-Петербург) представляют собой цельносварной корпус, состоящий из отсека по подготовке воздуха и сушильной камеры. То есть отсек фильтрации и нагрева воздуха, а также вентилятор располагаются не в техническом, а в рабочем помещении, что нецелесообразно согласно требованиям GMP. Поэтому в настоящее время на предприятиях проводится замена таких сушилок сушильными установками новых конструкций.
Полочные сушилки с принудительной циркуляцией воздуха (воздушные су-
шилки) представляют собой камеру, внутри которой размещена этажерка с полками. Материал загружается на противни и устанавливается на полки. Высуши-
ТАБЛЕТКИ. ГРАНУЛЫ. ДРАЖЕ. ПЕЛЛЕТЫ. ЛЕДЕНЦЫ. РЕЗИНКИ ЖЕВАТЕЛЬНЫЕ …
ваемый продукт периодически перемешивают вручную или он остается неподвижным в течение всего процесса сушки, продолжающегося несколько часов.
Сушилки с силикагельной колонкой. В случае необходимости регенерировать жидкости, содержащиеся в высушиваемых материалах, применяют сушилки, в которых воздух пропускается через силикагель. При этом ценные пары адсорбируются, а теплый воздух вновь используется для сушки материала.
Инфракрасные сушилки. В качестве термоизлучателей в таких сушилках применяются специальные зеркальные лампы, нихромовые спирали накаливания, помещенные в фокусе параболических отражателей, металлические и керамические панельные излучатели с электрическим, паровым или газовым обогревом. Тепловое действие инфракрасных лучей вызывает быстрое испарение влаги из тонких слоев материала. Однако сушилки отличаются высоким расходом энергии, поэтому применяются редко.
Высушенные гранулы перед прессованием должны иметь некоторую влажность, которая называется остаточной. Остаточная влажность для каждого таблетируемого препарата индивидуальна и должна быть оптимальной, т.е. такой, при которой процесс прессования протекает наилучшим образом, качество таблеток соответствует требованиям ГФУ, а прочность их наивысшая по сравнению с таблетками, получаемыми из гранул этого же препарата с другой степенью влажности. Недосушенные гранулы прилипают к пуансонам, неравномерно заполняют матрицу и требуют повышенного количества антифрикционных веществ. Пересушенные гранулы трудно прессуются и таблетки могут получаться с нарушенными краями.
Получение сухих гранул и их опудривание. В процессе сушки гранул возможно их слипание в отдельные комки. С целью обеспечения равномерного фракционного состава, высушенные гранулы пропускают через грануляторы с размером отверстий сеток 1,5 мм, что в значительной степени обеспечивает постоянную массу таблеток. После этого гранулы опудривают в смесителях с вращающимся корпусом, добавляя антифрикционные вещества, и передают на стадию таблетирования.
Грануляция в высокоскоростном смесителе-грануляторе. В фарма-
цевтической промышленности широкое распространение получили машины и аппараты, в которых совмещаются несколько технологических операций.

ТАБЛЕТКИ. ГРАНУЛЫ. ДРАЖЕ. ПЕЛЛЕТЫ. ЛЕДЕНЦЫ. РЕЗИНКИ ЖЕВАТЕЛЬНЫЕ …
При использовании полифункционального оборудования достигается ускорение и увеличение механизации процесса влажной грануляции. Так смешивание, увлажнение и грануляция проводятся в одной рабочей емкости высокоскоростного смесителя-гранулятора. Вначале порошки смешиваются при помощи импеллера – горизонтальной трехлопастной мешалки, расположенной внизу по центру полированной емкости с закругленным днищем. При быстром вращении импеллера, лопасти которого расположены под углом 35° к поверхности днища, создается интенсивная циркуляция материала, который переходит
всостояние близкое к псевдоожижению и перемешивается за 3-5 мин. Затем на смесь порошков с помощью перистальтического дозирующего насоса или сжатого воздуха через форсунку распыляется увлажнитель. Одновременно включается боковая ножевая мешалка или чоппер – винт, оборудованный несколькими рядами ножей, частота вращения у которого выше, чем у импеллера, примерно
в10 раз. Равномерно увлажненные частицы порошка соединяются между собой
иобразуют циркулирующие агломераты. Чоппер разбивает большие комки. Пока гранулы непрочные, непрерывно проходят процессы соединения и отделения частиц, что способствует равномерному распределению веществ в гранулах. Скопления частиц быстро уплотняются и на образованные ядра наслаиваются новые частицы. Под действием центробежной, центростремительной, сре-
ТАБЛЕТКИ. ГРАНУЛЫ. ДРАЖЕ. ПЕЛЛЕТЫ. ЛЕДЕНЦЫ. РЕЗИНКИ ЖЕВАТЕЛЬНЫЕ …
зывающей силы и силы трения за 3-8 мин формируются гранулы округлой формы, компактной структуры, с высокой насыпной плотностью и узким интервалом распределения по размерам. Размер получаемых гранул зависит от вязкости увлажнителя, размера и характера поверхности исходных частиц, смачиваемости веществ, скорости импеллера и чоппера и времени грануляции. Плотность гранул определяется скоростью добавления увлажнителя. На качество гранул также влияют тип распылительной форсунки и состав смеси. Как и в процессе грануляции продавливанием, недопустимо переувлажнение массы.
Высокоскоростные смесители-грануляторы типа MGT выпускаются фирмами: «Лёдиге» (Германия), «ИСиАй Лимитед» (США). В таких смесителяхгрануляторах, как вертикальный гранулятор типа VG фирмы «Глатт», гранулятор Roto фирмы «Занкетта» (Италия), грануляторы моделей Грануматор GMA и Вагуматор VMA фирмы «Боле» (Германия) помимо смешивания и грануляции может осуществляться также сушка влажных гранул. Загрузка сырья из вспомогательного сборника в емкость аппаратов осуществляется через трубопровод самотеком или при помощи вакуума. Импеллер и чоппер работают с регулируемой частотой вращения.
В конструкции вертикального гранулятора VG (рис. 4.11) предусмотрено расположение вала и привода импеллера под днищем рабочей емкости. Чоппер находится в нижней боковой части резервуара и приводится в действие через горизонтальный вал. Для предотвращения загрязнения сырьем валов мешалок через их уплотнения в емкость подается воздух. Продуктовый резервуар герметично закрывается крышкой при помощи откидных болтов. На крышке располагается фильтр для сбрасывания давления, создаваемого внутри емкости подачей воздуха и для очистки воздуха, отводимого вакуумной системой. Также на крышке имеется отверстие для загрузки порошков, мерник для увлажнителя, и люк с чистящим устройством для наблюдения за процессом. Сушка влажных гранул в емкости аппарата проводится с помощью вакуума 18–22 мм. рт. ст. (2,4–2,7 кПа) при циркуляции горячей воды с температурой 60–80°C в рубашке. Во время сушки импеллер перемешивает материал с более низкой скоростью, чем при смешивании и грануляции. Подаваемый возле валов мешалок воздух или инертный газ ускоряет удаление влаги из емкости. Расход воздуха составляет 3–30 м3/ч (в зависимости от объема резервуара). При этом эффект псевдоожижения не создается. Увеличение расхода воздуха выше

ТАБЛЕТКИ. ГРАНУЛЫ. ДРАЖЕ. ПЕЛЛЕТЫ. ЛЕДЕНЦЫ. РЕЗИНКИ ЖЕВАТЕЛЬНЫЕ …
оптимального уровня снижает эффективность сушки из-за повышения давления в рабочей емкости.
|
|
|
|
|
|
|
|
|
|
|
|
|
|
5 |
6 |
|
|
|
|
|
|
|||||
|
|
|
|
|
|
|
|
|
|
4 |
|
|
|
|
|
|
||||||||||
|
|
|
|
|
|
|
|
|
|
|
|
|
|
|
|
|
|
|
|
|
|
|
|
|
|
|
|
|
|
|
|
|
|
|
|
|
|
|
|
|
|
|
|
|
|
|
|
|
|
|
|
|
|
|
|
|
|
К вакуум-линии |
|
|
|
|
|
|
|
|
|
|
|
|
|
|
|
|
|
|||||
|
|
|
|
|
|
|
|
|
|
|
|
|
|
|
|
|
|
|
Циркуляция |
|
|
|||||
Вода для мойки |
|
|
|
|
|
|
|
|
|
|
||||||||||||||||
|
|
|
|
|
|
|
|
|
|
|
теплоносителя |
|
|
|||||||||||||
|
|
|
|
|
|
|
|
|
|
|
Сырье |
|
|
|
|
|
|
|
|
|||||||
|
|
|
|
|
|
|
|
|
|
|
|
|
|
|
|
|||||||||||
|
|
|
|
|
|
|
|
|
|
|
|
|
|
|
|
|
|
|
|
|
|
|
|
|
||
|
|
|
|
|
|
|
|
|
|
|
|
|
|
|
|
|
Сжатый воздух |
|
|
|
||||||
|
Вода для мойки |
|
|
|
|
|
|
|
|
|
|
|
|
|
|
|
|
|
|
|||||||
|
|
|
|
|
|
|
|
|
|
|
|
|
|
|
|
|
|
|
||||||||
|
|
|
|
|
|
|
|
|
|
Увлажнитель |
|
|
|
|
||||||||||||
|
|
|
|
|
|
|
|
|
|
|
|
|
|
|
|
|
|
|
|
|
||||||
|
3 |
|
|
|
|
|
|
|
|
|
|
|
|
|
|
|
|
|
|
|
|
|||||
|
|
|
|
|
|
|
|
|
|
|
|
|
7 |
|
|
|
|
|
|
|||||||
|
|
|
|
|
|
|
|
|
|
|
|
|
|
|
|
|
|
|
|
|
|
|
|
|
|
|
|
|
2 |
|
|
|
|
|
|
|
|
|
|
|
|
|
|
|
|
|
|
|
|||||
|
|
|
|
|
|
|
|
|
|
|
|
|
|
8 |
|
|
|
|
|
|
||||||
|
|
|
|
|
|
|
|
|
|
|
|
|
|
|
|
|
|
|
|
|
|
|
|
|
|
|
|
|
|
|
|
|
|
Движение |
|
|
|
|
|
|
|
|
|
|
|
|
|||||||
|
|
|
|
|
|
|
|
|
|
|
|
|
|
|
|
|
|
|
||||||||
|
|
|
1 |
|
|
|
|
|
|
|
Вода для мойки |
|
|
|||||||||||||
|
|
|
продукта |
|
|
|
|
|
|
|
||||||||||||||||
|
|
|
|
|
|
|
|
|
|
|
|
|
|
|
|
|
|
|
||||||||
|
|
|
|
|
|
|
|
|
|
|
|
|
|
|
|
|
|
|
||||||||
|
|
|
|
|
|
|
|
|
|
|
|
|
|
|
|
|
|
|
|
|
|
|
|
|||
|
|
|
|
|
|
|
|
|
|
|
|
|
|
|
|
9 |
|
|
|
|
||||||
|
|
|
|
|
|
|
|
|
|
|
|
|
|
|
|
|
|
|
|
|
|
|
|
|
|
|
|
|
|
|
|
|
|
|
|
11 |
10 |
|
Воздух для |
|||||
|
очистки |
|
|
|
|
|
|
|
|
|
|
|
|
|
|
|
|
Гранулы
Теплоноситель
Рис. 4.11. Схема вертикального гранулятора VG:
1 – чоппер; 2 – рабочая емкость; 3, 4, 9 – форсунки для мойки; 5 – фильтр; 6 – мерник для увлажнителя; 7 – форсунка для увлажнителя; 8 – рубашка; 10 – разгрузочный клапан; 11 – импеллерная мешалка
К преимуществам вакуумной сушки следует отнести сохранение качества термолабильных и окисляющихся на воздухе веществ, снижение остаточного количества растворителя в гранулах до минимального уровня, возможность восстановления растворителя, уменьшение риска взрыва от пыли в аппарате.
Для интенсификации передачи тепла грануляту в смесителе-грануляторе могут подключаться микроволновые генераторы. Микроволновая сушка основана на воздействии на высушиваемый продукт интенсивного электромагнитного поля сверхвысоких частот (СВЧ). Микроволны частотой 915 МГц или 2,45 ГГц генерируются магнетронами и через полый волновод направляются в слой гранул. Диэлектрики, такие как вода и растворители с растворенными солями, содержащиеся во влажных гранулах, поглощают микроволновую энергию, которая увеличивает колебания молекул. Это


ТАБЛЕТКИ. ГРАНУЛЫ. ДРАЖЕ. ПЕЛЛЕТЫ. ЛЕДЕНЦЫ. РЕЗИНКИ ЖЕВАТЕЛЬНЫЕ …
лученных в установке модели VG, целесообразно проводить в сушилке псевдоожиженного слоя, которая подсоединяется посредством трубопровода к смеси- телю-гранулятору через калибратор.
Гранулятор-сушилка типа Roto отличается от вертикального гранулятора VG расположением чоппера, который находится сбоку крышки и приводится в действие через вертикальный вал.
Высокоскоростные грануляторы фирмы «Боле» (рис. 4.13) имеют эллип-
тическое днище. Приводы мешалок располагаются над крышкой рабочей емкости. Такая конструкция позволяет наиболее полно выгружать готовые гранулы через центральный разгрузочный патрубок. Гранулы при выгрузке проходят через сито. Для сушки гранул, помимо рубашки для обогрева емкости, вакуумной линии и микроволнового генератора, аппарат оснащен ВАГАЗ-системой, включающей несколько патронов распределения подаваемого воздуха или инертного газа и ускоряющей процесс сушки. Фильтр для очистки отводимого
воздуха изготовлен из нержавеющей стали, что предотвращает его быстрое из-
нашивание. За процессами,
происходящими внутри ре-
зервуара, проводится видеоконтроль. Установка имеет
систему СIP для очистки. Смесители-
грануляторы управляются при помощи компьютера, на котором задаются параметры: время операций, температура грануляции и сушки, частоты вращения мешалок, давление на подаче увлажнителя через форсунку, давление и интервалы подачи воздуха в массу, расход воздуха, величина вакуума, ус-
ТАБЛЕТКИ. ГРАНУЛЫ. ДРАЖЕ. ПЕЛЛЕТЫ. ЛЕДЕНЦЫ. РЕЗИНКИ ЖЕВАТЕЛЬНЫЕ …
ловия аварийной остановки.
Сухие гранулы, полученные в смесителе-грануляторе, опудривают смазывающими веществами в смесителе с вращающимся корпусом.
Смешанная грануляция. В производстве таблеток для некоторых гидрофобных материалов, образующих после увлажнения и высушивания хрупкую массу, часто применяют смешанную грануляцию, которая заключается в перемешивании порошков, их увлажнении раствором связывающего вещества в смесителях, высушивании до комковатой массы в воздушных сушилках с последующим протиранием через перфорированную пластину гранулятора. Полученные сухие гранулы опудривают и отправляют на таблетирование.
Структурная грануляция. При использовании этого метода грануляции происходит характерное воздействие на увлажненный материал, которое приводит к образованию округлых, а при соблюдении определенных условий и достаточно однородных по размеру гранул.
В настоящее время в фармацевтическом производстве применяют три вида грануляции данного типа: в дражировочном котле; распылительным высушиванием и в псевдоожиженном слое.
Дражировочный котел представляет собой вращающуюся емкость эллипсоидной формы, укрепленную на наклонном валу, или емкость цилиндрической формы с двумя усеченными конусами по бокам. Для грануляции в дражировочном котле загружают смесь порошков и при вращении его со скоростью 30 об/мин производят увлажнение подачей раствора связывающего вещества через форсунку. Частицы порошков слипаются между собой, высушиваются теплым воздухом и в результате трения приобретают приблизительно одинаковую сферическую форму. В конце процесса к высушиваемому грануляту добавляют скользящие вещества.
Грануляцию распылительным высушиванием целесообразно использо-
вать в случаях нежелательного длительного контактирования гранулируемого продукта с воздухом (например, в производстве антибиотиков, ферментов, продуктов из сырья животного и растительного происхождения).
Готовят раствор или суспензию из вспомогательного вещества и увлажнителя и подают их через форсунки в виде мелких капель в камеру распылительной сушилки. Сушка осуществляется воздухом при температуре 150ºС.
ТАБЛЕТКИ. ГРАНУЛЫ. ДРАЖЕ. ПЕЛЛЕТЫ. ЛЕДЕНЦЫ. РЕЗИНКИ ЖЕВАТЕЛЬНЫЕ …
Распыленные частицы имеют большую поверхность, вследствие чего происходит интенсивный массо- и теплообмен. Они быстро теряют влагу и образуют всего за несколько секунд сферические пористые гранулы размером 10–70 мкм. Полученные гранулы смешивают с лекарственными веществами и, если необходимо, добавляют вспомогательные вещества, не введенные ранее в состав суспензии. Гранулы имеют хорошую текучесть и прессуемость, поэтому таблетки, полученные из такого гранулята, обладают высокой прочностью и прессуются при низких давлениях.
Если в удельных весах гранулята и лекарственного вещества наблюдается значительная разница, то возможно расслоение таблетируемой массы. В результате чрезмерного высушивания суспензии также возможно отслоение верхней части таблетки («кэппинг») при прессовании.
Грануляция в псевдоожиженном слое. Для гранулирования таблеточ-
ных смесей с целью подготовки их к таблетированию в фармацевтической промышленности широко применяется псевдоожижение материала, при котором обрабатываемый порошок, а затем и образующийся гранулят непрерывно находятся в движении. Основные процессы – смешивание компонентов, увлажнение смеси раствором связывающего вещества, грануляция и сушка гранулята – протекают в одном аппарате. Грануляция в псевдоожиженном слое осуществляется двумя способами:
–распылением раствора или суспензии, содержащих вспомогательные и лекарственные вещества, в псевдоожиженной системе на мелкие сферические ядра;
–распылением раствора связывающих веществ на порошкообразные вещества, находящиеся в псевдоожиженном состоянии.
При применении первого способа, гранулы образуются при нанесении гранулирующего раствора или суспензии распылением с последующей сушкой на поверхность первоначально введенных в камеру ядер, приведенных в состояние псевдоожижения и являющихся искусственными «зародышами» будущих гранул. Ядром может быть лекарственное вещество или индифферентное вещество, например, сахар. Таким путем получают твердые и плотные гранулы, имеющие близкие размеры, округлую форму, высокую насыпную плотность и текучесть.
ТАБЛЕТКИ. ГРАНУЛЫ. ДРАЖЕ. ПЕЛЛЕТЫ. ЛЕДЕНЦЫ. РЕЗИНКИ ЖЕВАТЕЛЬНЫЕ …
Другой способ получения гранул – непосредственная грануляция порошков в псевдоожиженном слое. Порошок помещается в рабочую камеру аппарата, где поддерживается во взвешенном состоянии потоком воздуха, и на него через форсунку распыляется гранулирующая жидкость. В псевдоожиженном слое обеспечивается кратковременное взаимодействие лекарственных веществ с жидкостью и нагретым воздухом, что благоприятно для нестабильных препаратов. Полученные гранулы отличаются большой прочностью и хорошей текучестью, являющейся следствием почти правильной геометрической формы гранул, приближающейся к шарообразной. При этом образуются более мягкие и пористые агломераты со сбалансированным фракционным составом, чем при получении гранул влажной грануляцией продавливанием, где образуются крупные агломераты, подлежащие последующему измельчению.
Качество гранул и их фракционный состав зависят от многих факторов, определяющих ход процесса, основными из которых являются скорость ожижающего газа, состав и скорость подачи гранулирующей жидкости, расположение форсунки, температура в слое.
При гранулировании таблеточных смесей в псевдоожиженном слое смешивание порошков является первой технологической операцией, влияющей на качество гранул. Равномерность смешивания зависит от аэродинамического режима работы аппарата, отношения компонентов в смеси, формы и плотности частиц. Для повышения гомогенности массы создаются условия для встряхивания или продувки рукавных фильтров без прекращения псевдоожижения.
При смешивании частиц, близких друг к другу по форме и имеющих соотношение по массе не более 1:10, перемешивание практически происходит без сепарации, при больших соотношениях характер перемешивания во многом зависит от формы и плотности частиц, а также от аэродинамических параметров процесса и требует конкретного изучения с целью выбора оптимального режима. При необходимости некоторые вещества могут вноситься в таблеточную смесь в виде суспензии, смешанной с раствором связывающих веществ. Смешивание порошков длится около 5 мин.
При добавлении гранулирующей жидкости происходит комкование частичек гранулируемой массы за счет склеивающих сил, как самой жидкости, так и раствора, образующегося при смачивании этой жидкостью поверхностного слоя обрабатываемого материала. Частицы связываются между собой мостами
ТАБЛЕТКИ. ГРАНУЛЫ. ДРАЖЕ. ПЕЛЛЕТЫ. ЛЕДЕНЦЫ. РЕЗИНКИ ЖЕВАТЕЛЬНЫЕ …
из раствора связывающего вещества. В процессе сушки жидкость испаряется, а соединение частиц остается благодаря затвердевшему связывающему веществу. При этом комки превращаются в твердые агломераты, частично разрушающиеся в результате трения между собой и со стенками аппарата.
Для распыления раствора связывающих веществ в форсунку вместе с раствором подается воздух. Размер гранул определяется размером капель жидкости, который варьируется выбором диаметра отверстий форсунки и давлением распыления: чем выше давление, тем меньше капельки, и соответственно, меньше гранулы. Более крупные гранулы получаются при подаче большего относительного количества гранулирующей жидкости. При этом снижается содержание негранулированного порошка в грануляте. Также диаметр и износостойкость гранул зависят от применяемых связывающих веществ и концентраций их растворов. Концентрация раствора связывающих веществ ограничивается возможностью распыливания через форсунку. С повышением концентрации увеличивается вязкость жидкости, но даже при использовании небольших концентраций получают качественные гранулы, что не всегда достигается в технологии грануляции продавливанием. Так применяется 3 % крахмальный клейстер, раствор метилцеллюлозы до 5 %.
Одним из факторов, влияющих на пористость гранул, является форма частиц материала. Высокая пористость характерна для гранул из кристаллов в виде иголок и пластин, а низкая – для гранул из частиц сферической формы.
Процесс роста гранул длится около 15-30 мин. Грануляция в псевдоожиженном слое проходит быстрее с образованием слабопористых гранул, если вещества хорошо смачиваются гранулирующей жидкостью и растворяются в ней.
Процесс грануляции в псевдоожиженном слое происходит одновременно с сушкой получаемых гранул горячим воздухом. Сушка готового гранулята является фактически дополнительной операцией до требуемого значения остаточной влажности и длится 3-5 мин. Если после прекращения гранулирования таблеточная смесь имеет необходимую для прессования остаточную влажность, то дополнительная сушка не требуется.
В зависимости от физических свойств гранул опудривание высушенного гранулята производится в этом же аппарате добавлением антифрикционных веществ в гранулят и вторичного перемешивания в псевдоожиженном слое или в смесителе с вращающимся корпусом.
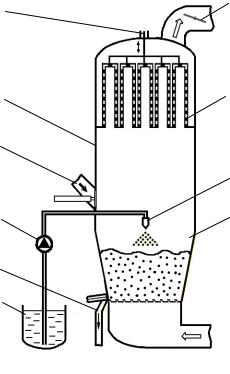
ТАБЛЕТКИ. ГРАНУЛЫ. ДРАЖЕ. ПЕЛЛЕТЫ. ЛЕДЕНЦЫ. РЕЗИНКИ ЖЕВАТЕЛЬНЫЕ …
Грануляция в псевдоожиженном слое на производстве осуществляется в аппаратах фирм «Глатт», «Хюттлин» (Германия), «Мюнстер», «АэроматикФилдер» (Швейцария), «Ниро», «ИСиАй Лимитед» (США), установке модели «Гибли» фирмы «IMA» (Италия). До недавнего времени использовались аппараты СГ-30 и СГ-60 (НПО «Прогресс», Cанкт-Петербург).
Сушилки-грануляторы псевдоожиженного слоя имеют те же составные части, что и сушилки, и дополнительно – устройства для распыления раствора связывающих веществ. Принципиальная схема аппарата представлена на рис. 4.14. Корпус аппарата 5 выполнен из нескольких цельносварных секций, после-
|
|
|
|
|
|
|
|
|
довательно смонтированных друг с |
||||||
6 |
|
7 |
|
|
|||||||||||
|
|
|
|
|
|
|
|
другом. |
В |
местах |
присоединения |
||||
|
|
|
|
|
|
|
|
||||||||
Отработанный |
|||||||||||||||
|
|
||||||||||||||
|
|
|
|
|
|
воздух |
продуктового резервуара 10 к дру- |
||||||||
|
|
|
|
|
|
|
|
|
|||||||
|
|
|
|
|
|
|
|
|
|||||||
5 |
|
|
|
|
|
|
|
|
гим секциям происходит герметиза- |
||||||
|
|
8 |
|
|
ция |
с |
помощью |
пневматических |
|||||||
|
|
|
|
|
|
|
|
|
|||||||
|
|
|
|
|
|
|
|
|
|||||||
|
|
|
|
|
|
|
|
|
прокладок. В средней части рабочей |
||||||
4 |
|
|
|
|
|
|
|
|
|||||||
|
|
|
|
|
|
|
|
камеры |
аппарата, |
стенки которой |
|||||
|
|
|
|
|
|
|
|
|
|||||||
|
|
|
|
|
|
|
|
|
|||||||
|
|
|
|
|
9 |
|
|
||||||||
|
|
|
|
|
отполированы до зеркальной по- |
||||||||||
|
|
|
|
|
|
|
|
|
|||||||
|
|
|
|
|
|
|
|
|
|||||||
|
|
|
|
|
|
|
|||||||||
3 |
|
10 |
|
|
верхности, расположена переме- |
||||||||||
|
|
|
|
|
|
|
|
|
щающаяся |
|
в вертикальной плоско- |
||||
2 |
|
|
|
|
|
|
|
|
сти форсунка 9. Жидкость, предна- |
||||||
|
|
|
|
|
|
|
|
|
|||||||
|
|
|
|
|
|
|
|
|
|||||||
|
|
|
|
|
|
|
|
|
значенная |
для гранулирования, по- |
|||||
1 |
|
|
|
|
|
|
|
|
|||||||
|
|
|
|
|
|
Горячий |
дается |
к |
форсунке |
перистальтиче- |
|||||
|
|
||||||||||||||
|
|
фильтрованный |
|||||||||||||
|
|
|
|
|
|
воздух |
ским насосом высокого давления 3 |
||||||||
|
|
|
|
|
|
|
|
|
|||||||
|
из реактора 1. Также к распылителю |
||||||||||||||
Рис. 4.14. Принципиальная схема ап- |
|||||||||||||||
парата с псевдоожиженным слоем для |
по |
специальной системе подается |
|||||||||||||
гранулирования таблеточных смесей: |
сжатый воздух. В процессе работы |
||||||||||||||
1 – емкость для гранулирующей жидкости; 2 |
|||||||||||||||
– разгрузочный патрубок; 3 – насос дози- |
аппарата рукавные фильтры 8 очи- |
||||||||||||||
рующий; 4 – загрузочный патрубок; 5 – кор- |
щаются |
от |
пылевидного продукта, |
||||||||||||
пус аппарата; 6 – встряхивающее устройст- |
который затем гранулируется. Такая |
||||||||||||||
во; 7 – клапан регулирования потока возду- |
|||||||||||||||
ха; 8 – рукавные фильтры; 9 – распылитель- |
работа |
установки позволяет умень- |
|||||||||||||
ная форсунка; 10 – продуктовый резервуар |
шить долю негранулированного ма- |
||||||||||||||
|
|
|
|
|
|
|
|
|
териала и нагрузку на фильтры в грануляторе. Для каждого препарата экспериментально устанавливаются и задаются на пульте управления температура, расход гранулирующей жидкости, воздуха, продолжительность каждой технологи-

ТАБЛЕТКИ. ГРАНУЛЫ. ДРАЖЕ. ПЕЛЛЕТЫ. ЛЕДЕНЦЫ. РЕЗИНКИ ЖЕВАТЕЛЬНЫЕ …
ческой операции. Также на пульте управления задается цикличность и периодичность встряхивания фильтров. Недостатком такого способа грануляции является возможность возникновения высоких зарядов статического электричества, которые могут вызвать взрыв. Для защиты аппаратов от накопления зарядов предусмотрено заземление, а от взрыва – предохранительный клапан, автоматически открывающийся при повышении давлениябольше заданной величины.
В отличие от других грануляторов-сушилок псевдоожиженного слоя аппарат фирмы «Хюттлин» имеет продуктовый контейнер, над днищем которого находится воздухораспределительное устройство «турбоджет», представляющее собой тонкие стальные пластины, расположенные по окружности под углом 60° к горизонтальной поверхности на расстоянии 1 мм друг от друга (рис. 4.15). Рабочий воздух выходит из отверстий «турбоджета» горизонтальным по-
током. |
Такое техническое решение позволяет создавать во время грануляции |
||||||
|
|
|
|
|
|
|
вихреобразные движения порошка. Три форсун- |
|
|
|
|
|
|
|
ки располагаются близко к днищу по периметру |
|
|
|
|
|
|
|
контейнера или непосредственно на устройстве |
|
|
|
|
|
|
|
«турбоджет». Подобный монтаж форсунок дает |
|
|
|
|
|
|
||
4 |
|
|
|
ряд преимуществ: гранулирующая жидкость по- |
|||
|
|
|
|
||||
|
3 |
|
|
|
дается в зону, где псевдоожижаемый продукт |
||
|
|
|
|
|
|
|
|
|
2 |
|
|
|
имеет максимальную скорость; исключается ло- |
||
|
|
|
|
|
|
|
|
|
|
|
|
|
|
|
кальное переувлажнение с образованием круп- |
|
|
|
|
|
|
|
|
1 |
|
|
|
ных агломератов; расстояние между форсунками |
|||
|
|
|
|
|
|||
|
|
|
|
|
|
|
и продуктом во время процесса остается посто- |
|
|
|
|
|
|
|
янным; распыляемая жидкость не нагружает ру- |
|
|
|
Рис. |
4.15 |
Продуктовый |
кавные фильтры. Благодаря подаче воздуха через |
|
|
|
|
контейнер |
гранулятора- |
отверстие вокруг распыляемой жидкости, так на- |
||
|
|
|
сушилки «Хюттлин» в |
зываемому «микроклимату», форсунка не заби- |
|||
|
|
|
разрезе: |
|
|||
|
|
|
1 – тележка; 2 – трубопровод |
вается порошком или увлажнителем, и таким об- |
|||
|
|
|
подачи воздуха; 3 – устройст- |
разом, выдерживается заданная величина капель. |
|||
|
|
|
во «турбоджет»; 4 – форсунка |
Аппараты для гранулирования таблеточных смесей в псевдоожиженном слое работают следующим образом. В продуктовый резервуар в соответствии с рецептурой по трубопроводу самотеком или при помощи вакуума загружается таблеточная смесь или вещества, подлежащие грануляции. На пульте задаются необходимые параметры. В калорифер

ТАБЛЕТКИ. ГРАНУЛЫ. ДРАЖЕ. ПЕЛЛЕТЫ. ЛЕДЕНЦЫ. РЕЗИНКИ ЖЕВАТЕЛЬНЫЕ …
подается пар и включается вентилятор. Через заданные промежутки времени автоматически включаются привод, встряхивающий рукавные фильтры, форсунка и насос, подающий гранулирующую жидкость. Происходит грануляция таблеточной смеси, затем система распыливания отключается и начинается сушка гранулята. По окончании всего цикла грануляции автоматически выключается вентилятор и прекращается подача пара в калориферную установку. Готовый гранулят выгружается через боковое отверстие продуктового резервуара пневмоподачей или поворотом перфорированного днища через калибратор во вспомогательный сборник «бин».
Также резервуар с гранулами может отделяться от аппарата и при помощи тележки подвозиться к кантователю емкостей или колонному подъемнику,
|
|
|
|
представляющему собой стойку, на которой |
|
|
|
|
|
4 |
|
5 |
смонтирована каретка для подъема и поворота |
|
|
|
|
||
|
|
|
6 |
емкостей (рис. 4.16). Каретка имеет бункер с обе- |
|
|
|
|
чайкой. Продуктовый резервуар подается под |
|
3 |
|
|
|
|
|
7 |
бункер с обечайкой кантователя, крепится к ней |
|
|
|
|
||
|
|
|
||
|
|
|
8 |
герметично захватами, поднимается и механиз- |
|
|
|
|
мом поворота переворачивается. При этом про- |
|
2 |
|
|
дукт высыпается в бункер. Под бункер подают |
1 |
|
9 |
сборник или при необходимости калибратор с |
|
|
|
|
|
ситом и, открывая ручной затвор бункера, загру- |
|
|
Рис. |
4.16. Схема |
|
|
|
жают гранулы в сборник или производят их ка- |
||
|
кантователя емкостей: |
|||
|
|
1 – привод; 2 – меха- |
либровку. |
|
|
низм подъема; 3 – каретка; 4 |
Далее гранулят поступает на опудривание |
||
|
– стойка; 5 – затвор; 6 – |
|||
|
бункер с обечайкой; 7 – ме- |
или сразу на таблетирование (при условии со- |
||
|
ханизм поворота; 8 – про- |
держания смазывающих веществ). При подсое- |
||
|
дуктовый резервуар; 9 – те- |
|||
|
лежка |
|
динении бинов к механизму вращения, опудри- |
вание гранул осуществляют в них. С использованием в таблеточном производстве системы трубопроводов для загрузки и выгрузки материалов из технологического оборудования, передвижных сборников с герметичными клапанами и кантователей обеспечивается защита от загрязнения продукции и пылеобразования в цехе.